SMT技术Word文档格式.docx
《SMT技术Word文档格式.docx》由会员分享,可在线阅读,更多相关《SMT技术Word文档格式.docx(70页珍藏版)》请在冰豆网上搜索。
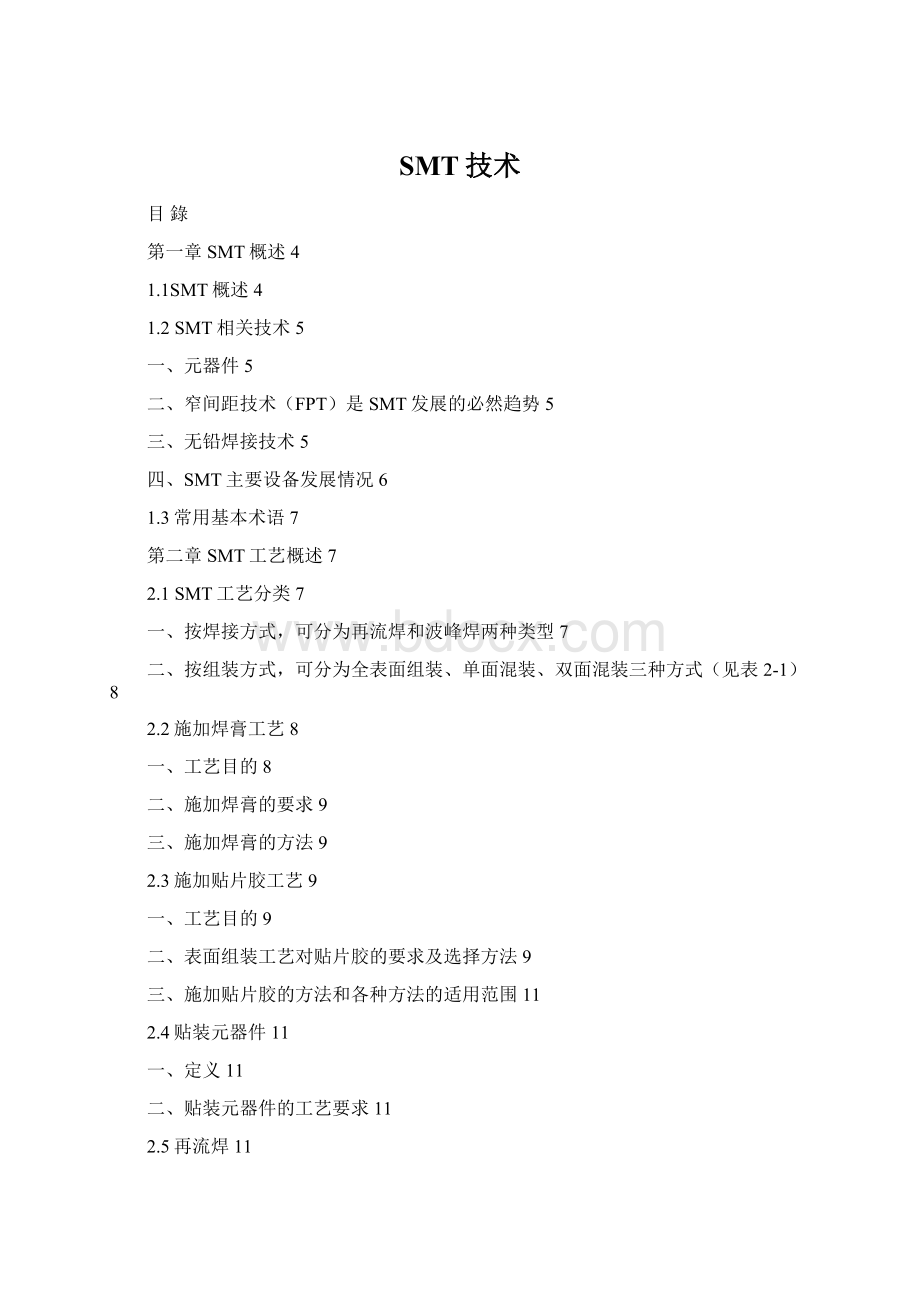
4.2表面组装元件(SMC)的外形封装、尺寸主要参数及包装方式(见表4-1)21
4.3表面组装器件(SMD)的外表封装、引脚参数及包装方式(见表4-2)22
4.4表面组装元器件的焊端结构22
4.5表面组装电阻、电容型号和规格的表示方法;
23
4.6表面组装元器件(SMC/SMD)的包装类型24
4.7表面组装元器件使人用注意事项25
第五章表面组装工艺材料介绍――焊膏25
5.1焊膏的分类、组成25
5.2焊膏的选择依据及管理使用27
5.3焊膏的发展动态28
5.4无铅焊料简介28
第六章SMT生产线及其主要设备30
6.1SMT生产线30
6.2SMT生产线主要设备31
第七章SMT印制电路板设计技术33
7.1PCB设计包含的内容:
33
7.2如何对SMT电子产品进行PCB设计33
第八章SMT印制电路板的设计要求36
8.1几种常用元器件的焊盘设计36
8.2焊盘与印制导线连接,导通孔.测试点.阻焊和丝网的设置41
8.3元器件布局设置43
8.4基准标志46
第九章SMT工艺(可生产性)设计----贴装机对PCB设计的要求48
9.1可实现机器自动贴装的元器件尺寸和种类48
9.2PCB外形和尺寸49
9.3PCB允许翘曲尺寸49
9.4PCB定位方式49
第十章SMT不锈钢激光模板制作、外协程序及制作要求50
10.1向模板加工厂发送技术文件50
10.2模板制作外协程序及制作要求51
第十一章SMT贴装机离线编程55
11.1PCB程序数据编辑56
11.2自动编程优化编辑57
11.3在贴装机上对优化好的产品程序进行编辑57
11.4校对并备份贴片程序58
第十二章后附(手工焊)修板及返修工艺介绍58
12.1后附(手工焊)、修板及返修工艺目的58
12.2后附(手工焊)、修板及返修工艺要求58
12.3后附(手工焊)、修板及返修技术要求59
12.4后附(手工焊)、修板及返修方法59
第十三章BGA返修工艺61
13.1BGA返修系统的原理61
13.2BGA的返修步骤61
13.3BGA植球工艺介绍63
第十四章表面组装检验(测)工艺64
14.1表面组装检验(测)工艺介绍64
14.2组装前检验(来料检验)65
14.3工序检验67
14.4表面组装板检验71
14.5AOl检测与X光检测简介74
第十五章SMT回流焊接质量分析77
15.1PCB焊盘设计77
15.2焊膏质量及焊膏的正确使用79
15.4贴装元器件.80
15.5回流焊温度曲线80
15.6回流焊设备的质量81
第十六章波峰焊接质量分析81
16.1设备要求82
16.2材料要求82
16.3印制电路板84
16.4元器件84
16.5工艺84
16.6设备维护85
第十七章中小型SMT生产线设备选型86
17.1中小型SMT生产线设备选型依据87
17.2中小型SMT生产线设备选型步骤88
17.3SMT生产线设备选型注意事项93
附录SMT在焊接中不良故障96
一.再流焊的工艺特点97
二.影响再流焊质量的原因分析99
三、SMT再流焊接中常见的焊接缺陷分析与预防对策103
SMT實用工藝基礎
第一章SMT概述
SMT(表面組裝技術)是新一代電子組裝技術。
經過20世紀80年代和90年代的迅速發展,已進入成熟期。
SMT已經成為一個涉及面廣,內容豐富,跨多學科的綜合性高新技術。
最新幾年,SMT又進入一個新的發展高潮,已經成為電子組裝技術的主流。
1.1SMT概述
SMT是無需對印製板鑽插裝孔,直接將處式元器件或適合於表面組裝的微型元件器貼、焊到印製或其他基板表面規定位置上的裝聯技術。
由於各種片式元器件的幾何尺寸和占空間體積比插裝元器件小得多,這種組裝形式具有結構緊湊、體積小、耐振動、抗衝擊、高頻特性好和生產效率高等優點。
採用雙面貼裝時,組裝密度的5倍以左右,從而使印製板面積節約了60%-70%,重量減輕90%以上。
SMT在投資類電子產品、軍事裝備領域、電腦、通信設備、彩電調諧器、錄影機、攝像機及袖珍式高檔多波段收音機、隨身聽、傳呼機和手機等幾乎所有的電子產品生產中都得到廣泛應用。
SMT是電子裝聯技術的發展方向,已成為世界電子整機組裝技術的主流。
SMT是從厚、薄膜混合電路演變發展而來的。
美國是世界上SMD和SMT最早起源的國家,並一直重視在投資類電子產品和軍事裝備領域發揮SMT高組裝密度和高可靠性能方面的優勢,具有很高的水準。
日本在70年代從美國引進SMD和SMT應用在消費類電子產品領域,並投入世資大力加強基礎材料、基礎技術和推廣應用方面的開發研究工作,從80年代中後期起加速了SMT在產業電子設備領域中的全面推廣應用,僅用四年時間使SMT在電腦和通信設備中的應用數量增長了近30%,在傳真機中增長40%,使日本很快超過了美國,在SMT方面處於世界領先地位。
歐洲各國SMT的起步較晚,但他們重視發展並有較好的工業基礎,發展速度也很快,其發展水準和整機中SMC/SMD的使用效率僅次於日本和美國。
80年代以來,新加坡、韓國、香港和臺灣省亞洲四小龍不惜投入钜資,紛紛引進先進技術,使SMT獲得較快的發展。
據飛利浦公司預測,到2010年全球範圍插裝元器件的使用率將由目前和40%下降到10%,反之,SMC/SMD將從60%上升到90%左右。
我國SMT的應用起步於80年代初期,最初從美、日等國成套引進了SMT生產線用於彩電諧器生產。
隨後應用於錄影機、攝像機及袖珍式高檔多波段收音機、隨身聽等生產中,近幾年在電腦、通信設備、航空航太電子產品中也逐漸得到應用。
據2000年不完全統計,我國約有40多家企業從事SMC/SMD的生產,全國約有300多家引進了SMT生產線,不同程度的採用了SMT。
全國已引進4000-5000台貼裝機。
隨著改革開放的深入以及加入WTO,近兩年一些美、日、新加坡、台商已將SMT加工廠搬到了中國,僅2001-2002一年就引進了4000餘台貼裝機。
我國將成為SMT世界加工廠的基地。
我國SMT發展前景是廣闊的。
SMT總的發展趨勢是:
元器件越來越小、組裝密度越來越高、組裝難度也越來越大。
最近幾年SMT又進入一個新的發展高潮。
為了進一步適應電子設備向短、小、輕、薄方向發展,出現了0210(0.6mm*0.3mm)的CHIP元年、BGA、CSP、FLIP、CHIP、複合化片式元件等新型封裝元器件。
由於BGA等元器件技術的發展,非ODS清洗和元鉛焊料的出現,引起了SMT設備、焊接材料、貼裝和焊接工藝的變化,推動電子組裝技術向更高階段發展。
SMT發展速度之快,的確令人驚訝,可以說,每年、每月、每天都有變化。
1.2SMT相關技術
一、元器件
1.SMC――片式元件向小、薄型發展。
其尺寸從1206(3.2mm*1.6mm)向0805(2.0mm*1.25mm)-0603(1.6mm*0.8mm)-0402(1.0mm*0.5mm)-0201(0.6mm*0.3mm)發展。
2.SMD――表面組裝器件向小型、薄型和窄引腳間距發展。
引腳中心距從1.27向0.635mm-0.5mm-0.4mm及0.3mm發展。
3.出現了新的封裝形式BGA(球柵陣列,ballgridarrag)、CSP(UBGA)和FILPCHIP(倒裝晶片)。
由於QFP(四邊扁平封裝器件受SMT工藝的限制,0.3mm的引腳間距已經是極限值。
而BGA的引腳的球形的,均勻地分佈在晶片的底部。
BGA和QFP相比最突出的優點首先是I/O數的封裝面積比高,節省了PCB面積,提高了組裝密度。
其次是引腳間距較大,有1.5mm、1.27mm和1.00mm,組裝難度下降,加工視窗更大。
例:
31mm*31mmRBGA引腳間距為1.5mm時,有400個焊球(I/O);
引腳間距為1.0mm時,有900個焊球(I/O)。
同樣是31mm*31mm的QFP-208,引腳間距為0.5mm時,只有208條引腳。
BGA無論在性能和價格上都有競爭力,已經在高(I/O)數的器件封裝中起主導作用。
二、窄間距技術(FPT)是SMT發展的必然趨勢
FPT是指將引腳間距在0.635-0.3mm之間的SMD和長*寬小於等於1.6mm*0.8mm的SMC組裝在PCB上的技術。
由於電腦、通信、航空航太等電子技術飛速發燕尾服,促使半導體積體電路的集成度越來越高,SMC越來越小,SMD的引腳間距也越來越窄。
目前,0.635mm和0.5mm引腳間距的QFP已成為工業和軍用電子裝備中的通信器件。
三、無鉛焊接技術
為了防止鉛對環境和人體危害,元鉛焊接也迅速地被提到議事日程上,日本已研製出無鉛焊接並應用到實際生產中,美國和歐洲也在加緊研究。
由於目前無鉛焊接的焊接溫度較高,因此焊接設、PCB材料及焊盤表面鍍錫的工藝、元器件耐高溫性能及端頭電極工藝、再流焊與波峰焊接工藝等等一系列新技術有待研究和解決。
四、SMT主要設備發展情況
1、印刷機
由於新型SMD不斷出現、組裝密度的提高以及免清洗要求,印刷機的高密度、高精度的提高以及多功能方向發展。
目前印刷機大致分為三種檔次:
(1)半自動印刷機
(2)半自動印刷機加視覺識別系統。
增加了CCD圖像識別,提高了印刷精度。
(3)全自動印刷機。
全自動印刷機除了有自動識別系統外,還有自動更換漏印範本、清洗網板、對QFP器件進行45度角印刷、二維和三維檢查印刷結果(焊膏圖形)等功能。
目前又有PLOWERFLOWER軟料包(DEK擠壓式、MINAMI單向氣功式等)的成功開發與應用。
這種方法焊膏是密封式的,適合免清洗、元鉛焊接以及高密度、高速度印刷的要求。
2、貼片機
隨著SMC小型化、SMD多引腳窄間距化和複合式、組合式片式元器件、BGA、CSP、DCA(晶片直接貼裝技術)、以及表面組裝的接外掛程式等新型片式元器件的不斷出現,對貼裝技術的要求越來越高。
近年來,各類自動化貼裝機正朝著高速、高精度和多功能方向發展。
採用多貼裝頭、多吸嘴以及高解析度視覺系統等先進技術,使貼裝速度和貼裝精度大大提高。
目前最高的貼裝速度可達到0.06S/Chip元件左右;
高精度貼裝機的重複貼裝精度為0.05-0.25mm;
多功能貼片機除了能貼裝0201(0.6mm*0.3mm)元件外,還能貼裝SOIC(小外型積體電路)、PLCC(塑膠有引線晶片載體)、窄引線間距QFP、BGA和CSP以及長接外掛程式(150Mm長)等SMD/SMC的能力。
此外,現代的貼片機在傳動結構(Y軸方向由單絲械向雙絲杠發展);
元件的對中方式(由機械向鐳射向全視覺發展);
圖像識別(採用高分辨CCD);
BGA和CSP的貼裝(採用反射加直射鏡技術);
採用鑄鐵機架以減少振動,提高精度,減少磨損;
以及增強電腦功能等方面都採用了許多新技術,使操作更加簡便、迅速、直觀和易掌握。
3、再流焊爐
再流焊爐主要有熱板式、紅外、熱風、紅外+熱風和氣相焊等形式。
再流焊熱傳導方式主要有輻射和對流兩種方式。
輻射傳導――主要有紅外爐。
其優點是熱效率高,溫度陡度大,易控制溫度曲線,雙面焊接時PCB上、下溫度易控制。
其缺點是溫度不均勻;
在同一塊PCB上由於器件的顏色和大小不同、其溫度就不同。
為了使深顏色和大體積的元器件達到焊接溫度、必須提高焊接溫度,容易造成焊接不良和損壞元器件等缺陷。
對流傳導――主要有熱風爐。
其優點是溫度均勻、焊接品質好。
缺點是PCB上、上溫差以及沿焊接長度方向的溫度梯度不易控制。
(1)目前再流焊傾向採用熱風小對流方式,在爐子下面採用製冷手段,以保護爐子上、下和長度方向的溫度梯度,從而達到工藝曲線的要求。
(2)是否需要充N2選擇(基於免清洗要求提出的)
充N2的主要作用是防止高溫下二次氧化,達到提高可焊性的目的。
對於什麼樣的產品需要充N2,目前還有爭議。
總的看起來,無鉛焊接,以及高密度,特別是引腳中心距為0.5mm以下的焊接過程有必要用N2,否則沒有太大必要。
另外,如果N2純度低(如普通20PPN)效果不明顯,因此要求N2純度為100PPN。
蒸蒸汽焊爐有再次興起的趨勢。
特別是對電性能要求極高的軍品。
1.3常用基本術語
SMT――表面組裝技術;
PCB――印製電路板;
SMA――表面組裝元件;
SMC\SMD――片式元件片/片式器件
FPT――窄間距技術。
FPT是指將引腳間距在0.635-0.3mm之間的SMD和長乘寬小於等於1.6mm*0.8mm的SMC組裝在PCB上的技術。
MELF――園柱形元器件
SOP――羽翼形小外形塑膠封裝;
SOJ――J形小外形塑膠封裝;
TSOP――薄形小小外塑膠封裝;
PLCC――塑膠有引線(J形)晶片載體;
QFP――四邊扁平封裝器件;
PQFP――帶角耳的四邊扁平封裝器件;
BGA――球柵陣列(ballgridarray);
DCA――晶片直接貼裝技術;
CSP――晶片級封裝(引腳也在器件底下,外形與BGA相同,封裝尺寸BGA小。
晶片封裝尺寸與晶片面積比≦1.2稱為CSP);
THC――通孔插裝元器件。
第二章SMT工藝概述
2.1SMT工藝分類
一、按焊接方式,可分為再流焊和波峰焊兩種類型
1、再流焊工藝――先將微量的錫鉛(SN/PB)焊膏施加到印製板的焊盤上,再將片式元器件貼放在印刷板表面規定的位置上,最後將貼裝好元器件的印製板放以再流焊設備的傳送帶上,從爐子入口到出口(大約5-6分鐘)完成乾燥、預熱、熔化、冷卻全部焊接過程。
2、波峰焊工藝――先將微量的貼片膠(絕緣粘接膠)施加到印製板的元器件底部或連忙緣位置上,再將片式元器件貼放在印製表面規定的位置上,並進行膠固化。
片式元器件被牢固地粘接在印製板的焊接面,然後插裝分立元器件,最後對片式元器件與插裝元器件同時進行波峰焊接。
二、按組裝方式,可分為全表面組裝、單面混裝、雙面混裝三種方式(見表2-1)
組裝方式
示意圖
電路基板
元器件
特徵
全
表
面
組
裝
單面表面組裝
單面PCB陶瓷基板
表面組裝元器件
工藝簡單、適用於小型、薄型簡單電路
雙面表面組裝
雙面PCB陶瓷基板
高密度組裝、薄型化
單
混
SMD和THC都在A面
雙面PCB
表面組裝元器件和通孔插裝元器件
一般採用先貼後插,工藝簡單
THC在A面SMD在B面
單面PCB
PCB成本低,工藝簡單,先貼後插如採用先插後貼,工藝複雜。
雙
THC在A面,A、B兩面都有SMD
適合高密度組裝
A、B兩面都有SMD和THC
工藝複雜,儘量不採用
2.2施加焊膏工藝
一、工藝目的
把適量的SN/PB焊膏均勻地施加在PCB焊盤上,以保證片式元器件與PCB相對應的焊盤達到良好的電氣連接。
二、施加焊膏的要求
1、要求施加的焊膏量均勻,一致性好。
焊膏圖形要清晰,相鄰的圖形之間儘量不要粘連,焊膏圖形與焊盤圖形要一致,儘量不要錯位。
2、一般情況下,焊盤上單位面積的焊膏量應為0.8mg/mm2左右,窄間距元器件應為0.5mg/mm2左右。
3、焊膏應覆蓋每個焊盤的面積,應在75%以上;
4、焊膏印刷後,應無嚴重塌落,邊緣整齊,錯位不大於0.2mm;
對窄間距元器件焊盤,錯位不大於0.1mm。
5、基板不允許被焊膏污染。
三、施加焊膏的方法
施加焊膏的方法有三種:
滴塗式(即注射式,滴除式又分為手工操作和機器製作)、絲網印刷和金屬範本印刷。
各種方法的適用範圍如下:
1、手工滴塗法――用於極小批量生產,或新產品的模型樣機和性能樣機的研製階段,以及生產過程中修補、更換元器件等。
2、絲網印刷――用於元器件焊盤間距較大,組裝密度不高的中小批量生產中。
3、金屬範本印刷――用於大批量生產以及組裝密度大,有多引線窄間距元器件的產品。
金屬範本印刷的品質比較好,範本使用壽命長,因此一般應優先採用金屬範本印刷工藝。
2.3施加貼片膠工藝
在片式元件與插裝元器件混裝採用波峰焊工藝時,需要用貼片膠把片式元件暫時固定在PCB的焊盤位置上,防止在傳遞過程或插裝元器件、波峰焊等工序中元件掉落。
在雙面再流焊工藝中,為防止已焊好面上大型器件因焊接受熱熔化而掉落,也需要用貼片膠起輔助固定作用。
二、表面組裝工藝對貼片膠的要求及選擇方法
1、表面組裝工藝對貼片膠的要求
(1)具有一定粘度,膠滴之間不拉絲,在元器件與PCB之間有一定的粘接強度,元器件貼裝後在搬運過程中不掉落。
(2)觸變性好,塗敷後膠滴不變形,不漫流,能保持足夠的高度;
(3)對印製板和元器件無腐蝕,絕緣電阻高和高頻特性好;
(4)常溫下使用壽命長(常溫下固化速度慢);
(5)在固化溫度下固化速度快,固化溫度要求在150℃以下,5分鐘以內完全固化;
(6)固化後粘接強度高,能經得住波峰焊時260℃的高溫以及熔融的錫流波剪切刀的衝擊;
在焊接過程中無釋放氣體現象,波峰焊過程中元件不掉落。
(7)有顏色,便於目視檢查和自動檢測;
(8)應無毒、無嗅、不可燃,符合環保要求;
2、貼片膠的選擇方法
用於表面組裝的貼片膠主要有兩種類型:
環氧樹脂和聚丙烯。
環氧樹脂型貼片膠屬於熱固型,一般固化溫度在140±
20℃/5min以內;
聚丙烯型貼片膠屬於光固型,需要先用UV(紫外)燈照一下,打開化學鍵,然後再用150±
10℃/1-2min完成完全固化。
(1)目前普通採用熱固型貼片膠,對設備和工藝的要求都比較簡單。
由於光固型貼片膠比較充分,粘接牢度高,對於較寬大的元器件應選擇光固型貼片膠。
(2)要考慮固化前性能、固化性能及固化後性能,應滿足表面組裝工藝對貼片膠的要求。
(3)應優先選擇固化溫度較低、固化時間較短的貼片膠。
目前較好的貼片膠的固化條件一般在120-130℃/60c-120s.
3、貼片膠的使用與保管
(1)必須儲存在5-10℃的條件下,並在有效期(一般3-6個月)內使用;
(2)要求使用前一天從冰箱中取出貼片膠,待貼片膠達到室溫後才能打開容器蓋,防止水汽凝結;
(3)使用前用不銹鋼攪拌棒將貼片膠攪拌均勻,待貼片膠完全無氣泡狀態下裝入注射器,添加完貼片膠後,應蓋好容器蓋;
(4)點膠或印刷操作工藝應在恒溫條件下(23±
3℃)進行,因為貼片膠的粘度隨溫度而變化,以防影響塗敷品質。
(5)採用印刷工藝時,不能使用回收的貼片膠;
(6)為預防貼片膠硬化和變質,攪拌後貼片膠應在24小時內使用完。
剩餘的貼片膠要單獨存放,不能與新貼片膠混裝一起;
(7)點膠或印刷後,應在24小時內完成固化;
(8)操作者儘量避免貼片膠與皮膚接觸,若不慎接觸,應及時用乙醇擦洗乾淨。
4、施加貼片膠的技術要求
(1)採用光固型貼片膠,元器件下面的貼片膠致少有一半的量處於被照射狀態;
採用熱固型貼片膠,貼片膠可完全被元器件覆蓋,見圖2-1;
(2)小元件可塗一個膠滴,大尺寸元器件可塗敷多個膠滴;
(3)膠滴的尺寸與高度取決於元器件的類型,膠滴的高度應達到元器件貼裝後膠滴能充分接觸到元器件底部的高度。
膠滴量(尺寸大小或膠滴數量)應根據元器件的尺寸和重量而定;
尺寸和重量大的元器件膠滴量應大一些,但也不宜過大,以保證足夠的粘接強度為准。
(4)為了保護可焊接以及焊點的完整性,要求貼片膠在貼裝前和貼裝後都不能污染元器件端頭和PCB焊盤
三、施加貼片膠的方法和各種方法的適用範圍
施加貼片膠主要有三種方法:
分配器滴塗、針式轉印和印刷。
5、分配器滴塗貼片膠
分配器滴塗可分為手動和全自動兩種方式。
手動滴塗用於試驗或小批量生產中;
全自動滴塗用於大批量生產中。
全自動滴塗需要專門的全自動點膠設備,也有些全自動貼片機上配有點膠頭,具備點膠和貼片兩種功能。
手動滴塗方法與焊膏滴塗相同,只是要選擇更細的針嘴,壓力與時間參數的控制有所不同。
6、針式轉印貼片膠
針式轉印機是採用針矩陣元件,先在貼片膠供料盤上蘸取適量的貼片膠,然後轉移動PCB的點膠位置上同時進行多點塗敷。
此方法效率較高,用於單一品種大批量生產中。
7、印刷貼片膠
印刷貼片膠的生產效率較高,用於大批量生產中,有絲網和範本兩種印刷方法。
印刷貼片膠的方法與焊膏印刷工藝相同,只是絲網和範本的設計要求,印刷參數的設置有所不同。
2.4貼裝元器件
一、定義
用貼裝機或人工將片式元器件準確地貼放在印好焊膏或貼片膠的PCB表面上。
二、貼裝元器件的工藝要求
1、各裝配位號元器件的型號、標稱值和極性等特徵標記要符合裝配圖和明細表要求。
2、貼裝好的元器件要完好無損。
3、元器件焊端或引腳不小於1/2的厚度要浸入焊膏。
元器件的端頭或引腳均應與焊盤圖形對齊、居中。
由於再流焊時有自定位效應,因此元器件貼裝位置允許有一定的偏差。
2.5再流焊
再流焊是通過重新熔化預先分配到印製板焊盤上的膏狀軟纖焊料,實現表面組裝元器件焊端或引腳與印製板焊盤之間機械與電氣連接的軟釺焊。
二、再流焊原理
從溫度曲線(見圖2-2)分析再流焊的原理:
當PCB進入升溫區(乾燥區)時,焊膏中的溶劑、氣體蒸發掉,同時,焊膏中的助焊劑潤濕焊盤、元器件端頭和引腳,焊膏軟化、塌落、覆蓋了焊盤、元器件端頭和引腳與氧氣隔離→PCB進入保溫區時,PCB和元器件得到充分的預熱,以防PCB突然進入焊接高溫區而損壞PCB和元器件→當PCB進入焊接區時,溫度迅速上升使焊膏達到熔化狀態,液態焊錫對PCB的焊盤、元器件端頭和引腳潤濕、擴散、漫流或回流混合形成焊錫接點→PCB進入冷卻區,使焊點凝固。
此時完成了再流焊。
一、再流焊特點
與波峰焊技術相比,再流焊有以下特點:
1、不像波峰焊尋樣,要把元器件直接浸漬在熔融的焊料中,所以元器件受到的熱沖小。
2、能控制焊料的施加量,避免了虛焊、橋接等焊接缺陷,因此焊接品質好,