铝的摩擦搅拌焊件的疲劳和断裂性能论文翻译.docx
《铝的摩擦搅拌焊件的疲劳和断裂性能论文翻译.docx》由会员分享,可在线阅读,更多相关《铝的摩擦搅拌焊件的疲劳和断裂性能论文翻译.docx(24页珍藏版)》请在冰豆网上搜索。
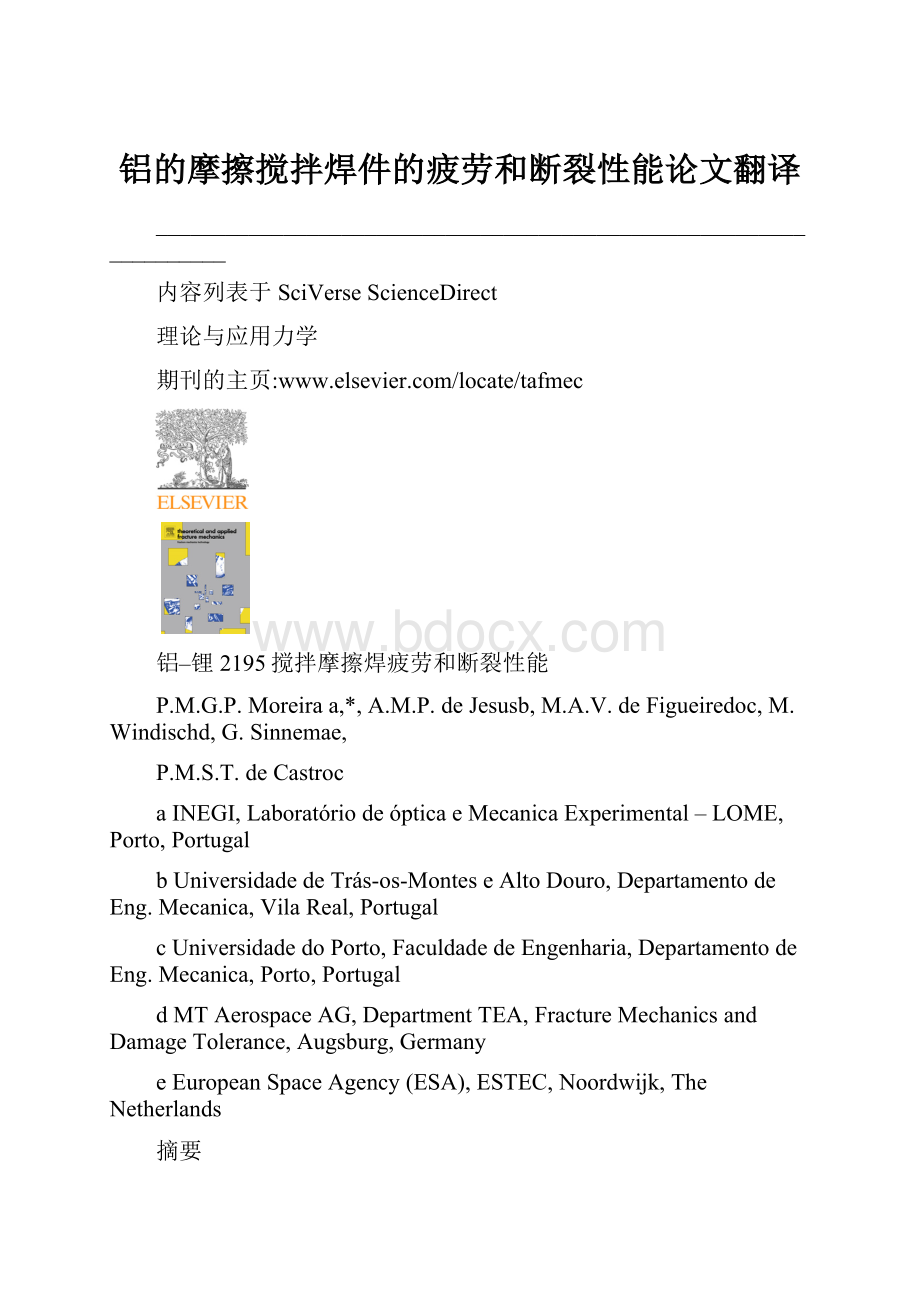
铝的摩擦搅拌焊件的疲劳和断裂性能论文翻译
__________________________________________________________________
内容列表于SciVerseScienceDirect
理论与应用力学
期刊的主页:
铝–锂2195搅拌摩擦焊疲劳和断裂性能
P.M.G.P.Moreiraa,*,A.M.P.deJesusb,M.A.V.deFigueiredoc,M.Windischd,G.Sinnemae,
P.M.S.T.deCastroc
aINEGI,LaboratóriodeópticaeMecanicaExperimental–LOME,Porto,Portugal
bUniversidadedeTrás-os-MonteseAltoDouro,DepartamentodeEng.Mecanica,VilaReal,Portugal
cUniversidadedoPorto,FaculdadedeEngenharia,DepartamentodeEng.Mecanica,Porto,Portugal
dMTAerospaceAG,DepartmentTEA,FractureMechanicsandDamageTolerance,Augsburg,Germany
eEuropeanSpaceAgency(ESA),ESTEC,Noordwijk,TheNetherlands
摘要
铝锂(Al–Li)合金因其低密度、高强度和疲劳裂纹增长抗力特性为轻质航空结构提供了强有力的性能。
虽然铝锂合金有很多优点,但使用传统的连接技术仍然有局限。
搅拌摩擦焊是一种行之有效的固体焊接方法,预计将减少许多Al–Li焊接的难度。
本文主要研究AA2195-T8X材料在室温下的疲劳性能特征,进行了5mm厚锡和基体材料试样的摩擦搅拌焊的裂纹扩展实验。
裂纹扩展实验中,三个不同的R值(最小远程应力/最大的远程应力)为0.1、0.5和0.8,分别在三个不同材料上使用:
基础材料,热影响区(HAZ),和焊接件。
M(T)试样缺口在焊缝的中心、热影响区和基础材料上分别进行了测试。
疲劳裂纹扩展试样留下了一个未完全断裂的韧带,最终结论是疲劳裂纹扩展与断裂韧性有关。
最新的结果呈现了T–L方向的疲劳裂纹扩展和韧性,并且SN疲劳特性、合金及其搅拌摩擦焊件的疲劳裂纹扩展和韧性与文献中找到的数据进行比较呈现出较高的值。
©2012Elsevier有限公司保留所有权利
文章信息
文章历史:
2012年6月28日在线提供
关键词:
铝锂合金裂纹扩展实验搅拌摩擦焊
1.简介
在航空和航天工业中最有效的一种减少重量的方法是运用合金来降低铝的密度。
为降低合金密度的,锂添加已被使用。
锂在铝中的溶解度在0–500℃的温度范围内迅速增加形成一个合金系统,通过沉淀硬化,形成良好的强度水平。
然而,铝锂合金又出现了其他问题,如延展性和断裂韧性的降低,分层问题和差应力腐蚀抗裂性。
在韧性降低的情况下强度的增加只有很少或根本没有,因此是一个重大问题[1,2]。
铝锂合金的发展来自于锂添加对铝的弹性模量的巨大作用,每1%质量锂的添加铝的弹性模量增加6%,并且每1%质量锂的添加铝锂合金的质量减少3%[3]。
这些变化适用于锂添加至3%质量。
早先铝锂合金历经了三代,(i)50~70年代生产的,包括2020和1420合金;这些合金存在延展性和断裂韧性差,或是强度相对较低的问题;(ii)上世纪80年代生产的,包括合金2090,2091,8090,和8091,具有高模量和低密度,但显示出各向异性的机械性能;(iii)最近的高强度合金,例如2195和2198合金[4–6]。
铝锂合金为轻质航空结构提供了有吸引力的性能,由于其低密度,高强度和疲劳裂纹增长抗性。
虽然铝锂合金有许多优点,但使用传统的连接技术仍有很多局限性,例如在焊接条件下的接合效率(焊缝强度与基体金属的强度比)低[7]。
在参考文献[8]中通过对GTAAA2195焊接样品的观察,焊后热处理提高了屈服强度,但疲劳强度并没有增加。
搅拌摩擦焊(FSW)是一种行之有效的固体连接方法,在参考文献[9–11]中有全面的分析,预计将减少许多铝锂焊接的难度。
这个项目在ESATRP的资助下进行旨在确定FSW技术运用于一次性运载火箭和可重复使用的运载火箭的低温储罐艺术的潜在可应用性的“破坏性低温压力容器的耐受性”实验。
*Correspondingauthor.
E-mailaddresses:
pmgpm@fe.up.pt(P.M.G.P.Moreira),ptcastro@fe.up.pt(P.M.S.T.deCastro).
0167-8442/$-seefrontmatter©2012ElsevierLtd.Allrightsreserved.
http:
//dx.doi.org/10.1016/j.tafmec.2012.06.001
2.SN疲劳实验
我们在室温(RT)下进行了AA2195-T8X的基础材料和摩擦搅拌焊(FSW)的5mm厚试样的Sn和疲劳裂纹扩展实验。
每个试样的实验结果关系到样本的切割方案[12]。
AA2195合金经过6.35mm初始厚度的T3R78和T8X的时间条件下获得了较高的强度。
将板在低温启动器中加工成5mm厚的典型焊缝厚度。
更多详细的信息可以在参考文献[13]中找到。
FSW经过MT-航天进行优化获得了高强度和良好的延展性。
在优化过程中主要分析的参数是旋转速度,进给速度,和垂直向下的力。
最终的焊接件选择的标准是有完美的外观、焊接强度高、在弯曲实验中形成大角度弯曲而不开裂、在拉伸和弯曲实验中断裂面平整的焊接件。
优化参数获得后,制备了接近应用条件的约20米的焊接件。
焊后处理用了手刮法来去除焊缝侧面锋利的尖刺。
焊接方向平行于材料轧制方向,加载力垂直于焊件。
初步进行拉伸实验,以获得AA2195-T8X搅拌摩擦焊接材料的强度值。
这些值,见表1,用于定义疲劳实验的负载水平,确定其适用于预制疲劳裂纹和裂纹扩展程序以防止塑性的影响的最大负载。
2.1.测试的定义
应力寿命曲线根据ASTM[14,15]评估采用垂直于焊缝的整体试样。
试样的几何形状见图1[12]。
为了计算应用于SN实验中的最大荷载,初始部分取5×12=60mm2,FSW屈服应力值见表1(300MPa)。
基础金属的表面粗糙程度为Ra(粗糙量度的平均值)=0.26μm和Rz(峰值)=1.84μm(测量范围80μm和截断值0.800mm)。
测试取两个不同的R值,0.1和0.8,每个应力比对应三不同的最大载荷。
R值为0.1代表压力循环(耐压实验、泄漏实验等);R值为0.8代表操作期间的外部负荷。
R值为0.1和0.8的负载频率分别为8Hz和15Hz。
测试根据下面表2的参数进行。
2.2.测试程序和设置
这个实验是在有100kN压力传感器的MTS810伺服液压机上进行的,并设计了在标准测试计划[16]中定义的符合试件几何形状和最大载荷的机械夹具。
每个试样的几何形状在每次测试之前都进行了准确测量,尤其是该试样在焊接过程中受影响的部分。
表1.测试材料及其强度值
表2.SN测试,远程载荷的定义图1.试件的疲劳实验(SN)的几何图
3.疲劳裂纹扩展
根据ASTM[17,18],疲劳裂纹生长曲线的测定考虑使用5mm厚的M(T)试样。
最初的切口方向与试样的轧制方向一致(T–L曲线根据ASTM[19]确定),试样的几何形状见图2[16]。
三个不同的R值,R=0.1、0.5、0.8分别在三个不同的材料条件下进行测试:
基本材料、热影响区(HAZ)、和焊接件。
火花腐蚀切口的疲劳预开裂了为了实现最小0.2mm的尖锐裂纹扩展。
在测试的最后KC值和K–R曲线的结果为15mm的最小剩余韧带。
在加载到断裂之前的裂纹长度为25mm。
根据参考文献[16],裂纹的长度应选择在此疲劳测试之前的合理的韧带长度(15mm)的情况下的裂纹扩展的最大可能长度。
应采取实验措施保证对称裂纹的增长,这应满足2a=50mm和(W–2a)/2=15mm的验证要求。
如果是不对称疲劳裂纹扩展,原则是当有一条韧带达到15mm时停止疲劳裂纹扩展实验。
试样的切口分别在焊接件中心、焊接热影响区和基础材料(BM)上,如图3中的线1、2和3。
第一种类型试样的切口在焊缝的中心(第1条线),这正好沿着焊缝中心。
第二种类型试样的切口位于HAZ(第2条线)。
HAZ的切口被稍微蚀刻在每个试样的两侧,根据显微组织这预计将作为切口的定位。
切口位置的后退方向是根据室温下整体拉伸试样断裂的位置确定的。
图2.M(T)试样的几何形状定义
图3.裂纹通过的位置[16]
3.1.实验参数的计算
表3根据ASTM[17]给出了试样和裂纹尺寸的定义。
根据ASTM[17]标准选定的试样类型应满足以下方程,其中(W–2a)是未断裂裂韧带试样,σYS为表1的屈服应力。
(1)
实验中载荷的选择基于项目合作伙伴[16]的提议以及以前NASA[20]的研究结果考虑ΔK的初值约为6MPam1/2。
该参考值与应力强度因数的校正根据ASTM标准[17]制定,并进行计算以确定每个R值使用的负载。
(2)
对于所有的R值及其最大载荷,ΔK(最大裂纹尺寸2a=50mm)最终的值为18.41MPam1/2。
R=0.1使用的是最大21.76kN的载荷;R=0.5测试试样最大载荷为35kN,如果是这样的话,这个负荷率测试的ΔK值将在5.36MPam1/2和16.45MPam1/2之间;对于R=0.8,最大载荷也为35kN,ΔK值将在2.14MPam1/2和6.58MPam1/2之间。
这些测试的结果包括:
da/dN曲线及其各个数据点和基本a–N数据、按照ASTM[18]的K–R曲线以及基于前面结果的负载–位移曲线,记录和拍摄每个破碎的试样、断口和不同材料区的裂纹生长的一些结论。
疲劳预开裂在恒定振幅的载荷下测试,裂纹长度通过立体显微镜目测得到。
R曲线的测定通过夹持测量仪和用螺栓连接的刀尖沿着一定范围内的裂纹测量。
本程序中夹持测量仪和试样的连接按照ASTM[18]的标准进行。
3.2.测试程序和设置
裂纹扩展实验是在250kN压力传感器的MTS321.21上实施的,频率为6Hz。
并设计了在标准测试计划[16]中定义的符合试件几何形状和最大载荷的机械夹具。
裂纹的扩展通过在试样两边的立体显微镜测定。
每个试样的几何形状在每次测试之前都经过准确测量,尤其是该试样在焊接过程中受影响的部分。
表3.试件的尺寸[17]
4.最终的断裂:
测试程序和设置
疲劳裂纹扩展实验中试样在室温下被加载到断裂,得出的裂纹长度(2a)约为50mm。
这些实验在位移控制的条件下进行,速度为0.1mm/min。
每个测试输出的是一个与用传感器测量的远程载荷P和通过夹持测量仪测量的位移ν有关的曲线。
每个M(T)试样上都开了2个M3的孔以固定夹持测量仪,如图4所示。
尝试按照ASTM[18]来分析实验获得的K–R曲线。
位移ν设为2y(y=12.5mm)。
有效裂缝长度(ae)是通过ν/P(从原点画出的不同直线斜率的倒数)的值获得的,下面是ASTM[18]定义的有关ae的校准方程。
这个校准方程通过调整来验证已知的初始裂纹长度。
Kr的值通过ae和P–ν曲线获得的P值,利用ASTM[18]的式
(2)获得。
P–ν曲线的数据点,可以进一步用来验证下面的公式(3)(网截面应力准则Rν):
(3)
σnet是剩余截面的平均应力,σyld是材料的屈服应力
该标准确保试样在每一个点的剩余部分都足够大,以避免塑性崩溃。
变量ap是物理裂纹长度,通过每个点使用下面的方程迭代获得。
(4)
(5)
ry是塑性区尺寸
裂纹扩展实验在四个裂纹长度(二边,正面以及背面)之一达到25mm时停止,K–R曲线实验(4个裂纹扩展实验最终测量值的平均值)的初始裂纹长度对于所有的样品并不一样。
到切口一侧的裂纹长度和其他方向的不同,有时很明显。
这意味着,裂纹试样在加载到断裂前是不对称的。
在试样的两表面,正面和背面测得的裂纹长度也不同。
这种宽度(w=80mm)的试样,对所有的试样来说裂纹长度在加载到断裂时太大了,因为它们超出了ASTM[18]定义的2a0(0.25w–0.4w)的范围。
图4.M(t)试样,支撑夹持测量仪的定位孔的位置
5.测试结果
5.1.疲劳寿命
通过70%σyield试样的实验我们发现了疲劳寿命这样的现象;第一试样在800000周期左右断裂而第二试样经过107个周期也未断裂,因此认为试样的疲劳寿命为107次。
R=0.1的疲劳寿命见图5。
在参考文献[21]中,证实了基体材料R=0.1的疲劳实验对应于105个周期的最大应力值为350–400MPa,而对FSW焊接件,R=0.1载荷垂直于焊件,最大应力在同一周期下为260–280MPa,减少了仅约30%。
值得注意的是在参考文献[8,22]中AA2195材料105个周期对应的疲劳寿命的数据约为σmax=240MPa,但是实验条件在不同的试样方向和50Hz的载荷频率下也不同。
为了作比较,使用了参考文献[23,24]中其他铝锂合金的的结果。
参考文献[23]给出了AA2050材料在105周期下的σmax≈220MPa;参考文献[24]给出了AA2198材料在105周期下纵向和横向分别为σmax≈250MPa和σmax≈225MPa。
这在本文中说明了摩擦搅拌焊良好的性能。
每个SN试样断裂表面的位置见表4。
SN疲劳试样上各种类型断裂位置见图6。
选择的类型为:
IT23,IT26和IT28,分别见图6的a–c。
表4.每个SN试样断裂表面的标记
图5.R=0.1和R=0.8的Sn测试结果图6.每种类型断裂位置的显微图
样本(a)IT23、(b)IT26和(c)IT24
5.2.疲劳裂纹扩展
测试了27个试样,下面的段落顺序分别为R=0.1、0.5和0.8的实验一张图对应一段。
5.2.1.R=0.1试样的测试
分析图7的疲劳裂纹扩展数据,可以确定的是疲劳裂纹扩展速率值较高是因为焊件的中心有一个小的切口,相比基本材料较低的裂纹扩展速率。
分析基本材料试样可以发现,对于较低的ΔK值,在6和8MPam1/2之间有一个稳定的裂纹扩展速率。
这个区域对应于疲劳裂纹在不规则表面的扩展。
在该图中也可以发现ΔK值在10和11MPam1/2之间时,所有试样的数据收敛为相同的裂纹扩展速率。
接下来,还会测试ΔK值高于18MPam1/2的相似的试样。
5.2.2.R=0.5试样的测试
分析裂纹扩展的数据,如图8,可以确定对于R=0.5的所有类型试样的裂纹扩展出现出类似的结果。
图7.R=0.1测试试样的疲劳裂纹扩展数据(a)基本材料
试样(b)焊接试样(c)HAZ试样
图8.R=0.5测试试样的疲劳裂纹扩展数据(a)基本材料
试样(b)焊接试样(c)HAZ试样
5.2.3.R=0.8试样的测试
分析裂纹扩展的数据,如图9,可以确定对于R=0.8的所有类型试样的裂纹扩展呈现出类似的结果。
试样M(T)34提供了一个独特的和令人惊讶的特性当最终的断裂发生在疲劳裂纹扩展实验的裂纹长度约21mm的时候。
断裂表面很不规则,并且疲劳裂纹扩展在试样的内部而不是在表面。
5.2.4.疲劳裂纹扩展结果的比较
为了对R值在各个试样上的影响作直接的比较,每个试样裂纹扩展速率的比较图类型如图10所示。
需要强调的,R=0.1的裂纹增长在第一个9mm的基本材料试样上表现出一个特定的行为,在第5.2.1节提到的。
图9.R=0.8测试试样的疲劳裂纹扩展数据(a)基本
材料试样(b)焊接试样(c)HAZ试样
图10.对于不同类型的试样的裂纹扩展的比较(a)基本
材料试样(b)HAZ材料试样(c)焊接材料试样
5.3.韧性
5.3.1.P–ν曲线
图11~13分别是焊件、HAZ和BM试样的P–ν曲线。
图的尺度是相同的以允许不同类型试样的曲线的的比较。
经验证,本试样几何曲线大幅落在在ASTME561适用范围之外;因此,实验数据的处理中将在下一节给出。
图11.焊接试样的P-ν曲线
图12.HAZ试样的P-ν曲线
图13.BM试样的P-ν曲线
图14.基本材料的结果比较
图15.焊件试样的结果比较
表5.BM试样的Kc值
5.3.2.断裂韧性的测定
为了估计基体材料断裂韧性的KC值,采用了ASTM[18]中的方程
(2)。
这个方程中a为疲劳裂纹扩展实验后和最终残余强度实验前的左右裂纹长度的平均值。
载荷对应于第一个pop-in,表5中给出了基本材料试样的Kc韧性值。
J0的计算根据EFAM程序的描述,例如根据参考文献[25]为M(T)的试样进行编号13到21,这是最有代表性的左右裂纹更相似的焊件和HAZ试样。
这些试样分别对应焊核材料和热影响区。
必要的弹性常数假设为E=70GPa并采用了P–ν曲线的最大载荷。
为了计算使用了初始裂纹长度物理值,P–ν曲线下的面积通过数值积分获得。
根据焊件和HAZ试样的KJ近似估计值获得了每个试样的试样韧性图。
值得注意的是弹塑性特性使韧性的估计大幅增加;例如试样M(T)21当弹性K为55.3MPam1/2时KJ=93.6MPam1/2。
这些试样的适当韧性表征应包括材料阻力曲线特性的描述。
然而,由于试样的几何形状的选择和材料的稀缺,有效的ASTME561的K–R曲线的Δa值只有小的变动。
因此,本文近似提供的单一数量焊件和HAZ试样的韧性或许可以与BM试样的第一个pop-in获得的KC值进行对比。
根据已经提到的EFAM[25]的程序对所有实验的R曲线计算KJ值。
在近似的情况下,本文证实了基础材料的韧性(平均值42.3MPam1/2,从表5的数据获得)低于搅拌摩擦焊材料。
焊件材料的KJ的平均值是99.6MPam1/2,HAZ材料的为92.8MPam1/2。
6.结论
目前的结果与参考文献[20]中相同材料数据的比较示于图14和15。
需要指出的是,参考文献[20]中仅给出了0.25和0.50英寸厚度仅在75oF的时数据,尽管NASA给出了其他厚度和温度的参考数据。
目前的结果与NASA的R分别为0.1和0.5的两种类型的试样(基本和焊接材料)的数据有一个合理的联系。
由图14可以看出,参考文献[20]中给出的基本材料的疲劳裂纹扩展在L–T和T–L方向上近似相同,接近于目前的T–L的结果。
对于FSW试样,参考文献[20]中只给出了L–T方向数据而现在的结果为T–L。
参考文献[26]中给出了AA2195合金FSW试样的疲劳裂纹生长结果。
几何形状是12.5mm厚度的M(T)与和垂直于焊件的L–T方向。
FSW试样的结果与本文的结果没有直接的可比性因为在参考文献[26]中的试样为L–T方向而本文研究的是T–L方向的试样。
然而我们发现参考文献[26]中给出的基本材料的数据与本文的研究一致。
在参考文献[27]中给出了AA2195–T8合金基本和搅拌摩擦焊接材料的疲劳裂纹扩展行为的分析。
结果发现基本材料的疲劳裂纹扩展与本文的研究类似。
然而参考文献[27]中摩擦搅拌焊试样的裂纹扩展速率比本文研究的低。
参考文献[27]中的测试用的R=0.1的C(T)8mm厚试样是由初始板厚(12.7mm)加工得到的。
参考文献[27]中较低的裂纹扩展速率可能是C(T)试样中的残余应力导致的,众所周知这种类型的试样裂纹前端区域的残余压应力表现明显,最近的研究表明在不同的材料上也是如此[28]。
以上的论证表明,FSW试样疲劳裂纹扩展速率测定的测试结果与相应的基本材料试样相比表现更好。
基本材料的韧性值均低于焊接材料,基体材料的平均值42.3MPam1/2与文献中的数据基本一致,如参考文献[29]中的AA2090或者参考文献[30]中的AA2195的韧性值钧低于等效的屈服应力。
7.结语
测试中AA2195–T8X的FSW试样在室温下表现出了良好的的SN疲劳特性。
基本材料与搅拌摩擦焊SN实验在R=0.1和105周期下获得的数据相比FSW试样的最大应力只降低了30%,与已发表的包括其他铝锂合金的SN实验数据比较表明FSW技术表现的很好。
铝锂合金2195–T8X基本材料和搅拌摩擦焊件的中间拉伸试样在室温下进行了疲劳裂纹扩展实验。
现有的2195合金FSW焊件的疲劳裂纹扩展给出的是L–T方向试样的数据,本文的实验提供的是T–L方向试样的数据。
疲劳裂纹扩展的数据并不能看出搅拌摩擦焊材料显著的应力比依赖性。
对于AA2195合金的基本材料,进行了一些压力比依赖性的验证。
一般情况下,疲劳裂纹扩展的数据与文献中类似材料的数据是一致的。
可以肯定,FSW试样的断裂韧性基本上普遍高于基本材料试样。
致谢
PedroM.G.P.Moreira博士感谢‘POPH–QREN-Tipologia4.2–PromoçãodoEmpregoCientíficoESF和MCTES的赞助以及PauloC.M.Azevedo和SérgioM.O的合作,Tavares已确认。
参考文献
[1]E.J.Lavernia,T.S.Srivatsan,F.A.Mohamed,Review–strength,deformation,
fracturebehaviourandductilityofaluminium–lithiumalloys,Journalof
MaterialsScience25(1990)1137–1158.
[2]E.A.Starke,J.T.Staley,Applicationofmodernaluminumalloystoaircraft,
ProgressinAerospaceSciences32(1996)131–172.
[3]CommitteeonNewMaterialsforAdvancedCivilAircraft,Newmaterialsfor
next-generationcommercialtransports,NationalAcademyPress,Washington,
DC,1996.
[4]D.L.Chen,M.C.Chaturvedi,Near-thresholdfatiguecrackgrowthbehaviorof
2195aluminum–lithium-alloy–predictionofcrackpropagationdirectionand
influenceofstressratio,MetallurgicalandMaterialsTransactionsA31A(