半导体的生产基本工艺作业流程精Word文件下载.docx
《半导体的生产基本工艺作业流程精Word文件下载.docx》由会员分享,可在线阅读,更多相关《半导体的生产基本工艺作业流程精Word文件下载.docx(10页珍藏版)》请在冰豆网上搜索。
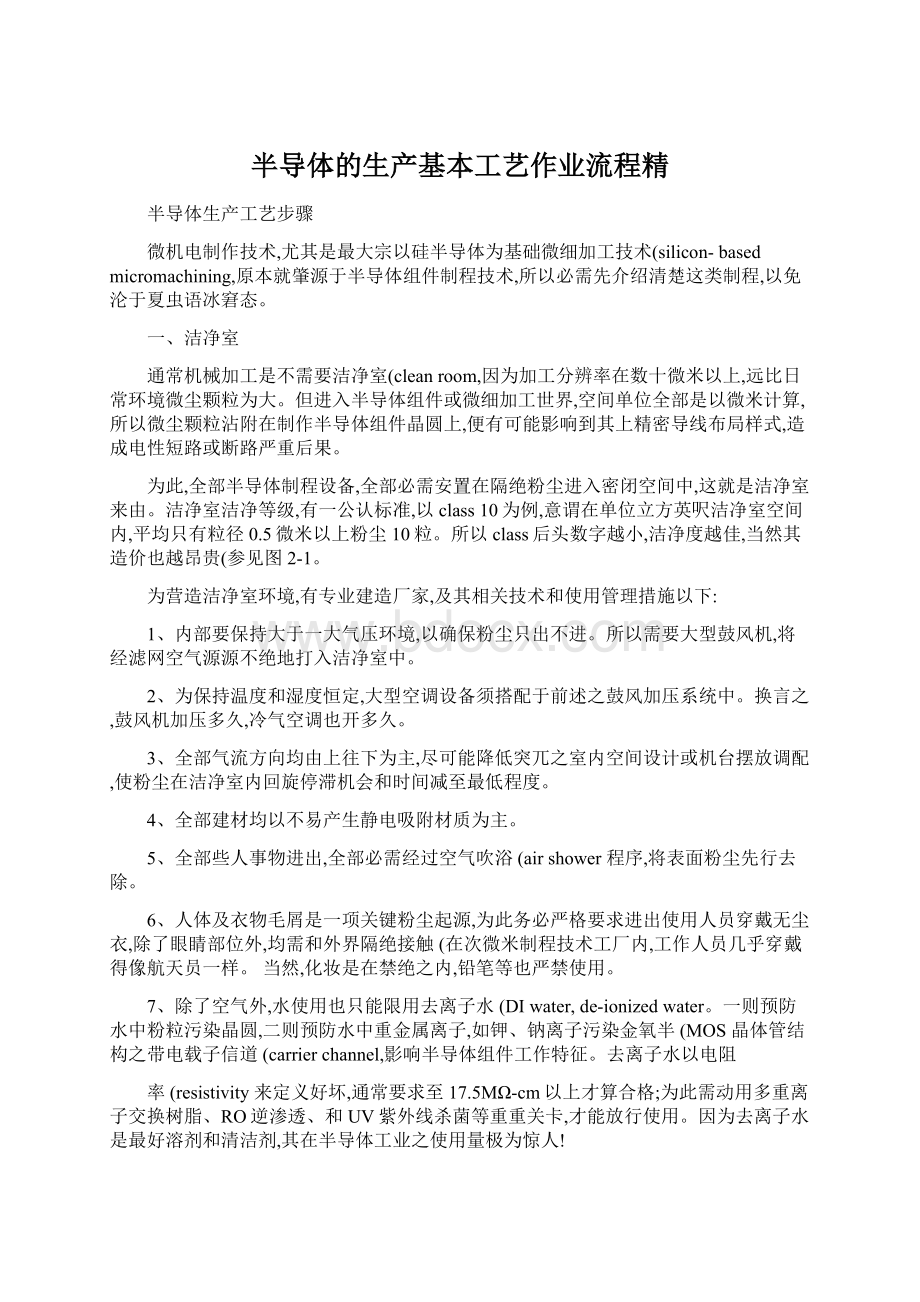
二、晶圆制作
硅晶圆(siliconwafer是一切集成电路芯片制作母材。
既然说到晶体,显然是经过纯炼和结晶程序。
现在晶体化制程,大多是采「柴可拉斯基」(Czycrasky拉晶法(CZ法。
拉晶时,将特定晶向(orientation晶种(seed,浸入过饱和纯硅熔汤(Melt中,并同时旋转拉出,硅原子便依据晶种晶向,乖乖地一层层成长上去,而得出所谓晶棒(ingot。
晶棒阻值假如太低,代表其中导电杂质(impuritydopant太多,还需经过FZ法(floating-zone再结晶(re-crystallization,将杂质逐出,提升纯度和阻值。
辅拉出晶棒,外缘像椰子树干般,外径不甚一致,需给予机械加工修边,然后以X光绕射法,定出主切面(primaryflat所在,磨出该平面;
再以内刃环锯,削下一片片硅晶圆。
最终经过粗磨(lapping、化学蚀平(chemicaletching和拋光(polishing等程序,得出具表面粗糙度在0.3微米以下拋光面之晶圆。
(至于晶圆厚度,和其外径相关。
刚才题及晶向,和硅晶体原子结构相关。
硅晶体结构是所谓「钻石结构」(diamond-structure,系由两组面心结构(FCC,相距(1/4,1/4,1/4晶格常数(latticeconstant;
即立方晶格边长叠合而成。
我们依米勒指针法(Millerindex,可定义出诸如:
{100}、{111}、{110}等晶面。
所以晶圆也因之有{100}、{111}、{110}等之分野。
相关常见硅晶圆之切边方向等信息,请参考图2-2。
现今半导体业所使用之硅晶圆,大多以{100}硅晶圆为主。
其可依导电杂质之种类,再分为p型(周期表III族和n型(周期表V族。
因为硅晶外貌完全相同,晶圆制造厂所以在制作过程中,加工了供辨识记号:
亦即以是否有次要切面(secondaryflat来分辨。
该次切面和主切面垂直,p型晶圆有之,而n型则阙如。
{100}硅晶圆循平行或垂直主切面方向而断裂整齐特征,所以很轻易切成矩形碎块,这是早期晶圆切割时,可用刮晶机(scriber原因(它并无真正切断芯片,而只在表面刮出裂痕,再加以外力而整齐断开之。
实际上,硅晶自然断裂面是{111},所以即使得到矩形碎芯片,但断裂面却不和{100}晶面垂直!
以下是订购硅晶圆时,所需说明规格:
项目说明
晶面{100}、{111}、{110}±
1o
外径(吋3456
厚度(微米300~450450~600550~650600~750(±
25
杂质p型、n型
阻值(Ω-cm0.01(低阻值~100(高阻值
制作方法CZ、FZ(高阻值
拋光面单面、双面
平坦度(埃300~3,000
三、半导体制程设备
半导体制程概分为三类:
(1薄膜成长,(2微影罩幕,(3蚀刻成型。
设备也跟着分为四类:
(a高温炉管,(b微影机台,(c化学清洗蚀刻台,(d电浆真空腔室。
其中(a~(c机台依序对应(1~(3制程,而新近发展第(d项机台,则分别应用于制程(1和(3。
因为坊间不乏介绍半导体制程及设备汉字书籍,故本文不刻意锦上添花,谨就笔者认为较有趣见解,描绘一二!
(一氧化(炉(Oxidation
对硅半导体而言,只要在高于或等于1050℃炉管中,图2-3所表示,通入氧气或水汽,自然能够将硅晶表面给予氧化,生长所谓干氧层(dryz/gateoxide或湿氧层(wet/fieldoxide,看成电子组件电性绝缘或制程掩膜之用。
氧化是半导体制程中,最洁净、单纯一个;
这也是硅晶材料能够取得优势特征之一(她种半导体,如砷化镓GaAs,便无法用此法成长绝缘层,因为在550℃左右,砷化镓已解离释放出砷!
硅氧化层耐得住850℃~1050℃后续制程环境,系因为该氧化层是在前述更高温度成长;
不过每生长出1微米厚氧化层,硅晶表面也要消耗掉0.44微米厚度。
以下是氧化制程部分关键点:
(1氧化层成长速率不是一直维持恒定趋势,制程时间和成长厚度之反复性是较为关键之考量。
(2后长氧化层会穿透先前长氧化层而堆积于上;
换言之,氧化所需之氧或水汽,
势必也要穿透先前成长氧化层到硅质层。
故要生长更厚氧化层,碰到阻碍也越大。
通常而言,极少成长2微米厚以上之氧化层。
(3干氧层关键用于制作金氧半(MOS晶体管载子信道(channel;
而湿氧层则用于其它较不严格讲究电性阻绝或制程罩幕(masking。
前者厚度远小于后者,1000~1500埃已然足够。
(4对不一样晶面走向晶圆而言,氧化速率有异:
通常在相同成长温度、条件、立即间下,{111}厚度≧{110}厚度>
{100}厚度。
(5导电性佳硅晶氧化速率较快。
(6适度加入氯化氢(HCl氧化层质地较佳;
但因轻易腐蚀管路,已渐少用。
(7氧化层厚度量测,可分破坏性和非破坏性两类。
前者是在光阻定义阻绝下,泡入缓冲过氢氟酸(BOE,BufferedOxideEtch,系HF和NH4F以1:
6百分比混合而成腐蚀剂将显露出来氧化层去除,露出不沾水硅晶表面,然后去掉光阻,利用表面深浅量测仪(surfaceprofileroralphastep,得到有没有氧化层之高度差,即其厚度。
(8非破坏性测厚法,以椭偏仪(ellipsometer或是毫微仪(nano-spec最为普遍布正确,前者能同时输出折射率(refractiveindex;
用以评定薄膜品质之好坏及起始厚度b和跳阶厚度a(总厚度t=ma+b,实际厚度(需确定m之整数值,仍需和制程经验配合以判读之。
后者则还必需事先知道折射率来反推厚度值。
(9不一样厚度氧化层会显现不一样颜色,且有埃左右厚度即循环一次特征。
有经验者也可单凭颜色而判定出大约氧化层厚度。
不过若超出1.5微米以上厚度时,氧化层颜色便渐不显著。
(二扩散(炉(diffusion
1、扩散搀杂
半导体材料可搀杂n型或p型导电杂质来调变阻值,却不影响其机械物理性质特点,是深入发明出p-n接合面(p-njunction、二极管(diode、晶体管(transistor、以至于大千婆娑之集成电路(IC世界之基础。
而扩散是达成导电杂质搀染早期关键制程。
众所周知,扩散即大自然之输送现象(transportphenomena;
质量传输(masstransfer、热传输(heattransfer、和动量传输(momentumtransfer;
即摩擦拖曳皆是其实然三种已知现象。
本杂质扩散即属于质量传输之一个,唯需要在850oC以上高温环境下,效应才够显著。
因为是扩散现象,杂质浓度C(concentration;
每单位体积含有多少数目标导电杂质或载
子服从扩散方程式以下:
这是一条拋物线型偏微分方程式,同时和扩散时间t及扩散深度x相关。
换言之,在某扩散瞬间(t固定,杂质浓度会由最高浓度表面位置,往深度方向作递减改变,而形成一随深度x改变浓度曲线;
其次,这条浓度曲线,却又伴随扩散时间之增加而改变样式,往时间无穷大时,平坦一致扩散浓度分布前进!
既然是扩散微分方程式,不一样边界条件(boundaryconditions施予,会产生不一样之浓度分布外形。
固定表面浓度(constantsurfaceconcentration和固定表面搀杂量(constantsurfacedosage,是两种常被讨论含有解析正确解扩散边界条件(参见图2-4:
2、前扩散(pre-deposition
第一个定浓度边界条件浓度解析解是所谓互补误差函数(complementaryerrorfunction,其对应之扩散步骤称为「前扩散」,即我们通常了解之扩散制程;
当高温炉管升至工作温度后,把待扩散晶圆推入炉中,然后开始释放扩散源(p型扩散源通常是固体呈晶圆状之氮化硼【boron-nitride】芯片,n型则为液态POCl3之加热蒸气进行扩散。
其浓度剖面外形之特征是杂质集中在表面,表面浓度最高,并随深度快速减低,或是说表面浓度梯度(gradient值极高。
3、后驱入(postdrive-in
第二种定搀杂量边界条件,含有高斯分布(Gaussiandistribution浓度解析解。
对应之扩散处理程序叫做「后驱入」,即通常之高温退火程序;
基础上只维持炉管驱入工作温度,扩散源却不再释放。
或问曰:
定搀杂量起始边界条件自何而来?
答案是「前扩散」制程之结果;
盖先前「前扩散」制作出之杂质浓度集中于表面,可近似一定搀杂量边界条件也!
至于为何扩散要分成此二类步骤,当然不是为了投数学解析之所好,而是因应阻值调变之需求。
原来「前扩散」杂质植入剂量很快达成饱和,即使拉长「前扩散」时间,也无法大幅增加杂质植入剂量,换言之,电性上之电阻率(resistivity特征很快趋稳定;
但「后驱入」使表面浓度及梯度减低(因杂质由表面往深处扩散,却又营造出再一次「前扩散」来增加杂质植入剂量机会。
所以,借着数次反复「前扩散」和「后驱入」,既能调变电性上之电阻率特征,又可改变杂质电阻之有效截面积,故依大家熟知之电阻公式;
其中是电阻长度可设计出所需导电区域之扩散程序。
4、扩散之其它关键点,简述以下:
(1扩散制程有批次制作、成本低廉好处,但在扩散区域之边缘所在,有侧向扩散误差,故限制其在次微米(sub-micron制程上之应用。
(2扩散以后阻值量测,通常以四探针法(four-pointprobemethod行之,示意参见图2-5。
现在市面已经有多个商用机台可供选购。
(3扩散所需之图形定义(pattern及遮掩(masking,通常以氧化层(oxide充之,以抵挡高温之环境。
一微米厚之氧化层,已足敷通常扩散制程之所需。
(二微影(Photo-Lithography
1、正负光阻
微影光蚀刻术起源于摄影制版技术。
自1970年起,才大量使用于半导体制程之图形转写复制。
原理即利用对紫外线敏感之聚合物,或所谓光阻(photo-resist之受曝照是否,来定义该光阻在显影液(developer中是否被蚀除,而最终留下和遮掩罩幕,即光罩(mask相同或明暗互补之图形;
相同者称之「正光阻」(positiveresist,明暗互补者称之「负光阻」(negativeresist,图2-6所表示。
通常而言,正光阻,如AZ-1350、AZ-5214、FD-6400L等,其分辨率及边缘垂直度均佳,但易变质,储存期限也较短(约六个月到十二个月之间,常见于学术或研发单位;
而负光阻之边缘垂直度较差,但可储存较久,常为半导体业界所使用。
2、光罩
前段述及光罩制作,是微影之关键技术。
其制作方法经几十年之演进,已由分辨率差缩影机(由数百倍大红胶纸【rubby-lith】图样缩影技术,改良为直接以计算机辅助设计制造(CAD/CAM软件控制雷射束(laser-beam或电子束(E-beam书写机,在具光阻之石英玻璃板上进行书写(曝光,分辨率(最小线宽也改善到微米等级。
因为激光打印机分辨率越来越好,未来一些线宽较粗光罩可望直接以打印机出图。
举例而言,3386dpi出图机,最小线宽约为七微米。
3、对准机/步进机
在学术或研发单位中之电路布局较为简易,一套电路布局可全部写在一片光罩中,或甚至多反复制。
加上使用之硅晶圆尺寸较小,配合使用之光罩原来就不大。
所以搭配使用之硅晶圆曝光机台为通常「光罩对准机」(maskaligner,图2-7。
换言之,一片晶圆只需一次对准曝光,便可进行以后显影及烤干程序。
但在业界中,使用晶圆大得多,我们不可能任意造出7吋或9吋大小光罩来进行对准曝光:
一来电子束书写机在制备这么大光罩时,会耗损巨量时间,极不划算;
二来,大面积光罩进行光蚀刻曝光前和晶圆之对准,要因应大面积精密定位及防震等问题,极为棘手!
所以工业界多采取步进机(stepper进行对准曝
光;
也就是说,即使晶圆大到6或8吋,但光罩大小还是小小1~2吋见方,一则光罩制备快速,二则小面积对准问题也比较少;
只是要曝满整片晶圆,要花上数十次「对准→曝光→移位」反复动作。
但即便如此,因每次「对准→曝光→移位」仅费时1秒左右,故一片晶圆总曝光时间仍控制在1分钟以内,而保持了工厂高投片率(highthrough-put;
即单位时间内完成制作之硅芯片数。
图2-7双面对准曝光对准系统(国科会北区微机电系统研究中心。
4、光阻涂布
晶圆上微米厚度等级光阻,是采取旋转离心(spin-coating方法涂布上去。
光阻涂布机图2-8所表示。
其经典程序包含:
(1晶圆表面前处理(pre-baking:
即在150°
C下烘烤一段时间。
若表面无氧化层,要另外先上助粘剂(primer,如HMDS,再降回室温。
换言之,芯片表面在涂敷光阻前要确保是亲水性(hydrophilic。
(2送晶圆上真空吸附转台,注入(dispensing光阻,开始由低转速甩出多出光阻并均布之,接着以转速数千rpm,减薄光阻至所需厚度。
(3将晶圆表层光阻稍事烤干定型,预防沾粘。
但不可过干过硬,而妨碍后续曝光显影。
通常光阻涂布机涂布结果是厚度不均。
尤其在晶圆边缘部份,可能厚达其它较均匀部份光阻3倍以上。
另外,为了确保光阻全然涂布到整片晶圆,通常注入光阻剂量,是真正涂布粘着在晶圆上之数十甚至数百倍,极其可惜;
因为甩到晶圆外光阻中有机溶剂快速挥发逸散,成份大变,不能回收再使用。
5、厚光阻
德国Karl-Suss企业开发了一个新型光阻涂布机,称为GYRSET?
图2-9所表示,其卖点在于强调可降低二分之一光阻用量,且得出更均厚光阻分布。
其原理极为单纯:
只是在真空转台上加装了跟着同时旋转盖子。
如此一来,等于强迫晶圆和盖子之间空气跟着旋转,那么光阻上便无高转速差粘性旋转拖曳作用。
故光阻在被涂布时,其和周遭流体之相对运动并不显著,只是离心彻体力效果,使光阻稳定地、且是呈同心圆状地向外涂布。
依据实际使用显示,GYRSET?
只需通常涂布机55%光阻用量。
另外,其也可应用于厚光阻之涂布(厚度自数微米至数百微米不等。
受涂基板也可由晶圆改为任意工作外型,而不会造成边缘一大部份面积厚度不均花花外貌。
[注]厚光阻是新近发展出来,供微机电研究使用材料,如IBMSU-8系列光阻,厚度由数微米至100微米不等,以GYRSET?
涂布后,经过严格烘干程序,再以紫外线或准
分子雷射(excimerlaser进行曝光显影后,所得到较深遂凹状图案,可供深入精密电铸(electro-forming金属微结组成长填塞。
这种加工程序又称为「仿LIGA」制程(poormansLIGA,即「异步X光之深刻模造术」。
(三蚀刻(Etching
蚀刻机制,按发生次序可概分为「反应物靠近表面」、「表面氧化」、「表面反应」、「生成物离开表面」等过程。
所以整个蚀刻,包含反应物靠近、生成物离开扩散效应,和化学反应两部份。
整个蚀刻时间,等于是扩散和化学反应两部份所费时间总和。
二者之中孰者费时较长,整个蚀刻之快慢也卡在该者,故有所谓「reactionlimited」和「diffusionlimited」两类蚀刻之分。
1、湿蚀刻
最普遍、也是设备成本最低蚀刻方法,其设备图2-10所表示。
其影响被蚀刻物之蚀刻速率(etchingrate原因有三:
蚀刻液浓度、蚀刻液温度、及搅拌(stirring之有没有。
定性而言,增加蚀刻温度和加入搅拌,均能有效提升蚀刻速率;
但浓度之影响则较不明确。
举例来说,以49%HF蚀刻SiO2,当然比BOE(Buffered-Oxide-Etch;
HF:
NH4F=1:
6快多;
但40%KOH蚀刻Si速率却比20%KOH慢!
湿蚀刻配方选择是一项化学专业,对于通常不是这方面研究人员,必需向该化学专业同侪请教。
一个选择湿蚀刻配方关键观念是「选择性」(selectivity,意指进行蚀刻时,对被蚀物去除速度和连带对其它材质(如蚀刻掩膜;
etchingmask,或承载被加工薄膜之基板;
substrate腐蚀速度之比值。
一个含有高选择性蚀刻系统,应该只对被加工薄膜有腐蚀作用,而不伤及一旁之蚀刻掩膜或其下基板材料。
(1等向性蚀刻(isotropicetching
大部份湿蚀刻液均是等向性,换言之,对蚀刻接触点之任何方向腐蚀速度并无显著差异。
故一旦定义好蚀刻掩膜图案,暴露出来区域,便是往下腐蚀所在;
只要蚀刻配方具高选择性,便应该止于所该止之深度。
然而有鉴于任何被蚀薄膜皆有其厚度,当其被蚀出某深度时,蚀刻掩膜图案边缘部位渐和蚀刻液接触,故蚀刻液也开始对蚀刻掩膜图案边缘底部,进行蚀掏,这就是所谓下切或侧向侵蚀现象(undercut。
该现象造成图案侧向误差和被蚀薄膜厚度同数量级,换言之,湿蚀刻技术因之而无法应用在类似「次微米」线宽精密制程技术!
(2非等向性蚀刻(anisotropicetching
先前题到之湿蚀刻「选择性」观念,是以不一样材料之受蚀快慢程度来说明。
然而自1970年代起,在诸如JournalofElectro-ChemicalSociety等期刊中,发表了很多相关碱性或有机溶液腐蚀单晶硅文章,其特点是不一样硅晶面腐蚀速率相差极大,尤其是<
111>
方向,足足比<
100>
或是<
110>
方向腐蚀速率小一到两个数量级!
所以,腐蚀速率最慢晶面,往往便是腐蚀后留下特定面。
这部份将在体型微细加工时再详述。
2、干蚀刻
干蚀刻是一类较新型,但快速为半导体工业所采取技术。
其利用电浆(plasma来进行半导体薄膜材料蚀刻加工。
其中电浆必需在真空度约10至0.001Torr环境下,才有可能被激发出来;
而干蚀刻采取气体,或轰击质量颇巨,或化学活性极高,均能达成蚀刻目标。
干蚀刻基础上包含「离子轰击」(ion-bombardment和「化学反应」(chemicalreaction两部份蚀刻机制。
偏「离子轰击」效应者使用氩气(argon,加工出来之边缘侧向侵蚀现象极微。
而偏「化学反应」效应者则采氟系或氯系气体(如四氟化碳CF4,经激发出来电浆,即带有氟或氯之离子团,可快速和芯片表面材质反应。
干蚀刻法可直接利用光阻作蚀刻之阻绝遮幕,无须另行成长阻绝遮幕之半导体材料。
而其最关键优点,能兼顾边缘侧向侵蚀现象极微和高蚀刻率两种优点,换言之,本技术中所谓「活性离子蚀刻」(reactiveionetch;
RIE已足敷「次微米」线宽制程技术要求,而正被大量使用中。
(四离子植入(IonImplantation
在扩散制程末尾描述中,曾题及扩散区域之边缘所在,有侧向扩散误差,故限制其在次微米制程上之应用。
但诚如干蚀法补足湿蚀法在次微米制程能力不足一样,此地另有离子植入法,来进行图案更精细,浓度更为稀少正确杂值搀入。
离子植入法是将III族或IV族之杂质,以离子型式,经加速后冲击进入晶圆表面,经过一段距离后,大部份停于离晶圆表面0.1微米左右之深度(视加速能量而定,故最高浓度地方,不似热扩散法在表面上。
不过因为深度很浅,通常还是简单认定大部份离子是搀杂在表面上,然后深入利用驱入(drive-in来调整浓度分布,并对离子撞击过区域,进行结构之修补。
基础上,其为一低温制程,故可直接用光阻来定义植入区域。
(五化学气相沉积(ChemicalVaporDeposition;
CVD
到现在为止,只谈到以高温炉管来进行二氧化硅层之成长。
至于其它如多晶硅(poly-silicon、氮化硅(silicon-nitride、钨或铜金属等薄膜材料,要怎样成长堆栈至硅晶圆上?
基础上仍是采取高温炉管,只是因着不一样化学沉积过程,有着不一样之工作温度、压力和反应气体,统称为「化学气相沉积」。
既是化学反应,故免不了「质量传输」和「化学反应」两部份机制。
因为化学反应随温度呈指数函数之改变,故当高温时,快速完成化学反应。
换言之,整体沉积速率卡在质量传输(diffusion-limited;
而此部份实际上随温度之改变,不像化学反应般敏感。
所以对于化学气相沉积来说,图2-11所表示,提升制程温度,轻易掌握沉积速率或制程之反复性。
然而高制程温度有几项缺点:
高温制程环境所需电力成本较高。
安排次序较后面制程温度若高于前者,可能破坏已沉积之材料。
高温成长之薄膜,冷却至常温后,会产生因各基板和薄膜间热胀缩程度不一样之残留应力(residualstress。
所以,低制程温度仍是化学气相沉积追求目标之一,惟如此一来,在制程技术上面临之问题及难度也跟着提升。
以下,按着化学气相沉积研发历程,分别介绍「常压化学气相沉积」、「低压化学气相沉积」、及「电浆辅助化学气相沉积」:
1、常压化学气相沉积(AtmosphericPressureCVD;
APCVD
最早研发CVD系统,顾名思义是在一大气压环境下操作,设备外貌也和氧化炉管相类似。
欲成长之材料化学蒸气自炉管上游均匀流向硅晶,至于何以会沉积在硅晶表面,可简单地以边界层(boundaryl