模具毕业设计13变速叉的热锻模设计Word下载.docx
《模具毕业设计13变速叉的热锻模设计Word下载.docx》由会员分享,可在线阅读,更多相关《模具毕业设计13变速叉的热锻模设计Word下载.docx(19页珍藏版)》请在冰豆网上搜索。
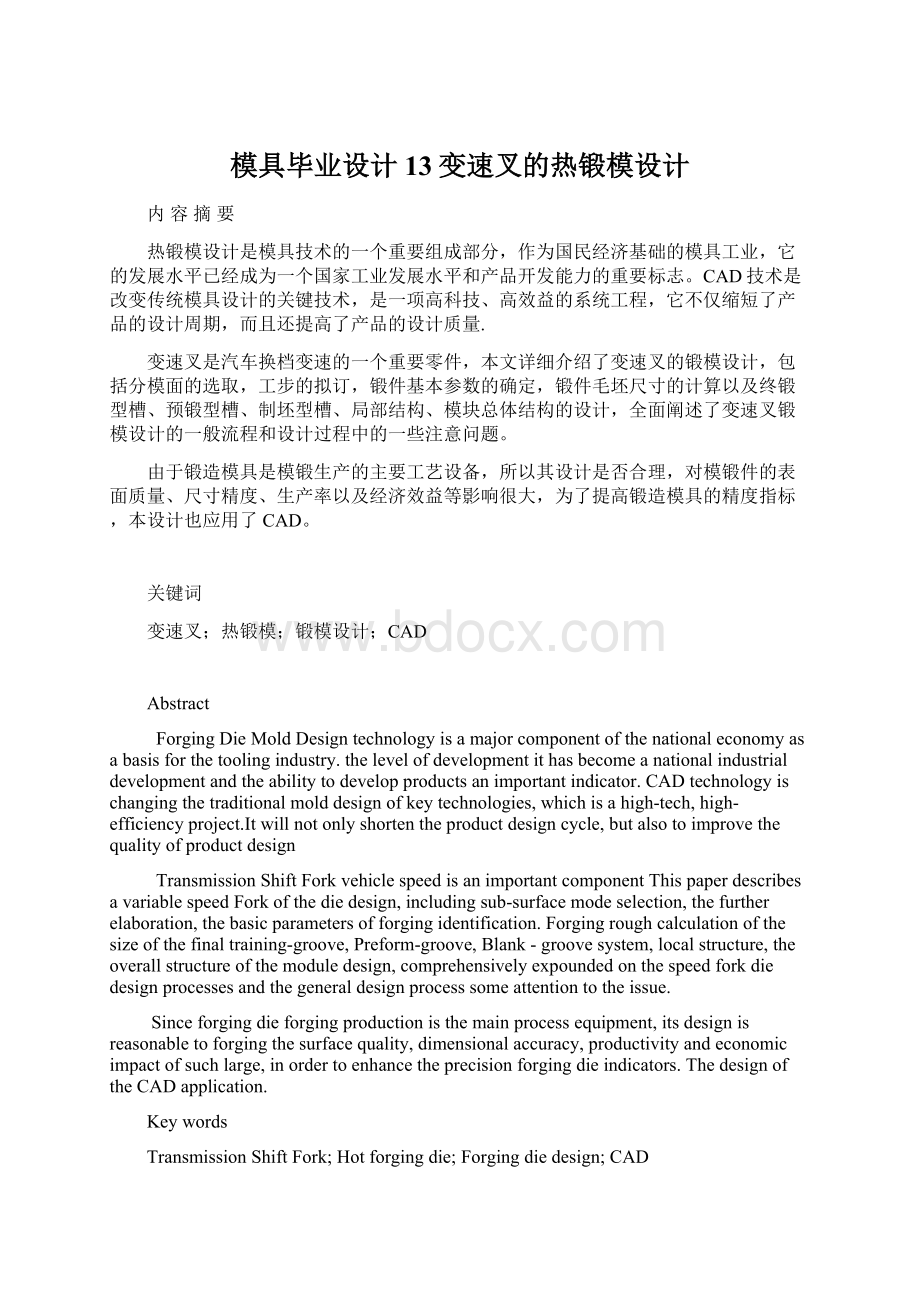
结束语………………………………………………………………24
致谢…………………………………………………………………25
参考文献……………………………………………………………26
变速叉的热锻模设计
Xxxxxxxxxx
1、引言
现代工业的迅猛发展使模锻技术得到越来越广泛的应用,对锻造模具的设计与制造的要求越来越高。
由于锻造模具是模锻生产的主要工艺装备,所以其设计是否合理,对模锻件的表面质量、尺寸精度、生产率以及经济效益等影响很大。
因此提高锻造模具的设计水平和锻造模具的各项技术指标,对现代模锻工业的发展是十分必要的。
锻造是一种借助工具或模具在冲击或压力作用下加工金属机械零件或零件毛坯的方法。
与其它加工方法相比,锻造加工生产率最高;
锻件的形状、尺寸稳定性好,并有最佳的力学性能。
锻件的最大优势是韧性高、纤维组织合理,件与件之间性能变化小;
锻件的内部质量与加工历史有关,不会被任何一种金属加工工艺超过。
锻件的优势是由于金属材料通过塑性变形后,消除了内部缺陷,如锻(焊)合空洞,压实疏松,打碎碳化物、非金属夹杂并使之沿变形方向分布,改善或消除成分偏析等,得到了均匀、细小的低倍和高倍组织。
而铸造工艺得到的铸件,尽管能获得较准确的尺寸和比锻件更为复杂的形状,但难以消除疏松、空洞、成分偏析、非金属夹杂等缺陷;
铸件的抗压强度随高,但韧性不足,难以在受拉应力较大的条件下使用。
机械加工方法获得的零件,尺寸精度最高,表面光洁,但金属内部流线往往被切断,容易造成应力腐蚀,承载拉压交变应力的能力较差。
锻造应用的范围很广。
几乎所有运动的重大受力构件都由锻造成形,不过推动锻造(特别是模锻)技术发展的最大动力是来自交通工具制造业——汽车制造业和后来的飞机制造业。
锻件尺寸、质量越来越大,形状越来越复杂、精细,锻造的材料日益广泛,锻造的难度更大。
这是由于现代重型工业、交通运输业对产品追求的目标是长的使用寿命,高度的可靠性。
如航空发动机,推重比越来越大。
一些重要的受力构件,如涡轮盘、轴、压气机叶片、盘等,使用温度范围变得更宽,工作环境更苛刻,受力状态更复杂而且受力急剧增大。
随着科技的进步,工业化程度的日益提高,要求锻件的数量逐年增长。
据国外预测,到本世纪末,飞机上采用的锻压(包括板料成形)零件将占85%,汽车将占60%-70%,农机、拖拉机将占70%。
目前全世界仅钢模锻的年产量就在1000万吨以上。
锻造在机器制造业中有着不可代替的作用,正如前面所论述的,由锻造方法生产出来的锻件,其性能是其是它加工方法难以与之匹敌的。
锻造(主要是模锻)的生产效率是相当高的,一个国家的锻造水平,反映了这个国家机器制造业的水平。
锻压经过100多年的发展,今天已成为一门综合性学科。
它以塑性成形原理、金属学、摩擦学为理论基础,同时涉及传热学、物理化学、机械运动学等相关学科,以各种工艺学,如锻造工艺学、冲压工艺学等为技术,与其它学科一起支撑着机器制造业。
锻压这门较老学科至今仍朝气蓬勃,在众多的金属材料和成形加工的国际、国内学术交流会议上仍十分活跃。
我国的经济体制发生了根本的变化,有过去的计划经济过渡到现在的市场经济。
锻压生产虽然效率高,锻件综合性能高,节约原材料和机械加工工时;
但生产周期较长,成本较高,处于不利的竞争地位。
铸造、焊接、机械加工都加入了竞争。
锻造生产要跟上当代科学技术的发展,需要不断改进技术,采用新工艺、新技术,进一步提高锻件的性能指标;
同时要缩短生产周期,降低成本,使之在竞争中处于优势地位。
锻造业既面临着发展机遇也面临着挑战,要想有较大的发展,锻造工艺技术必须要先行发展,不断完善和提高,这也是摆在从事锻压技术的每一位工程技术人员、管理人员和科研人员面前的共同任务。
2、锤锻模具的设计内容
2.1设计任务
零件为汽车变速叉,如图。
变速叉是汽车换挡变速的主要零件之一,主要作用是拨动变速箱中的齿轮,使汽车达到变速的目的.由于零件经常拨动齿轮承受变载荷和冲击性载荷,宜采用锻造,以使金属纤维尽量不被切断,保证零件工作可靠.因为为大批量生产,且零件的轮廓尺寸不大,故采用模锻成型。
热锻件图已给出,如图1所示:
图1变速叉的热锻件图
2.2分模面的选取
选择分模面的基本要求是保证锻件锻件能从模膛中取出来,因此锻件的侧表面不得有内凹的形状。
此外还要考虑以下原则:
1)在锻件高度一半处分模,使锻件的余块,机械加工余量最小;
2)使模膛的宽度大而深度小,这样金属容易充满模膛,锻件容易出模;
3)为了使模具制造方便,尽量采用平面分模,凸出部分也尽量不高于分模面;
4)分模面应设在容易看出锻件错差的位置;
5)应使飞边能切除干净,不致产生飞刺;
6)对金属流线方向有要求的锻件,应保证锻件有最好的纤维分布.
锻件分模位置合适与否,关系到锻件成形、锻件出模、材料利用等一系列问题。
对于长轴对称类锻件和形状较简单可采用直平面分模,圆饼类锻件,其锻件分模面应为通过具有最大水平投影面积位置的直平面,当锻件不含通孔时,最大水平投影面积位置就是锻件在水平面垂直方向上最大截面的位置。
该设计属于长轴对称类且形状较复杂,但具有较大弯曲,分模位置选择如下图
分模面
图2分模面位置
2.3终缎模膛设计
终锻模膛是锻件最后成型的模膛,通过终锻获得带飞边的锻件,终锻模膛设计的主要内容是绘制热锻件图和确定飞边槽的尺寸、钳口和锁扣。
由于金属的热胀冷缩现象,热锻件的尺寸应比冷锻件的尺寸有所增大。
冷锻件的所有尺寸放大
%(
为终锻温度下金属的收缩率),得到热锻件图。
由于该设计方案即为热锻件图则不用进行缩放。
3、飞边槽的设计
3.1飞边槽的结构形式
开式模锻的终锻型槽周边必须设计飞边槽,其形式和尺寸对锻件质量影响很大。
飞边槽有如下几种形式:
形式Ⅰ是使用最广泛的一种,其优点是桥部设在上模块,与坯料接触时间短,吸收热量少,因而温升少,能减轻桥部磨损或避免压塌。
形式Ⅱ适用于高度方向形状不对称锻件。
因复杂部分设在上模,为简化切边冲头形状,通常将锻件翻转180o,故桥部设在下模,切边时锻件也易放平稳。
形式Ⅲ适用于复杂零件,坯料体积不易计算准确而往往偏多的锻件,由于增大仓部容积,不致于发生上下模压不靠。
形式Ⅳ使用对象同形式c,由于加宽下模飞边槽桥部,因而提高桥部强度,以避免过快地磨损和过早地压塌。
形式Ⅴ只用于锻模局部,桥部增设阻尼沟,增加金属向仓部流动的阻力,迫使金属流向型槽深处或枝芽处。
形式Ⅵ称为楔形飞边槽,其特点是终锻时水平方向金属流动愈来愈困难,适用形状更复杂的锻件,缺点是切除毛边困难。
飞边槽的主要尺寸是桥部高度h、宽度b及入口半径R1当h减小,b增大,则水平方向流动阻力增大,有利于充满型腔。
但如果过度增大,将导致锻不足,并使锻模加速磨损。
但若h太大,b过小,导致金属向外流动的阻力太小,不利于充满型腔槽,并产生厚大毛边。
人口处原角半径R1太小,用意压塌内陷,影响锻件出模;
R1太大,又影响切边质量。
典型飞边槽(b)楔形飞边槽(c)扩张形飞边
图3 飞边槽结构形式
图3飞边槽形式
楔形飞边槽的填充能力最好,但所需的打击力大,因此对模具的磨损较为严重;
扩张形飞边槽由于模具与坯料之间的摩擦力较小,其填充性能较差,但所需打击力小;
常规的典型飞边槽的填充性和所需打击力居中。
因此,应根据不同锻件对各项工艺参数的不同要求,选取适当的飞边槽型式,以最低的消耗生产出合格的锻件。
该锻件选用形式Ⅰ型飞边槽,简图参照图4。
按锻件在分模面上的投影面积用计算的方法确定飞边桥部的高度h,计算公式如下:
h=0.015
式中F分—锻件在分模面上的投影面积,mm2
根据h的值按表7.10(见《锻造工艺学与模具设计》)选定飞边槽的尺寸。
h=1.6mm,h1=4mm,b=8mm,b1=25mm,r=0.8mm,F飞槽=144mm2
图4飞边槽
3.2钳口设计
钳口位于预锻和终锻模膛的前方,由夹钳口和钳口颈两部分组成,夹钳口在模锻时放置棒料及夹钳,钳口颈是用于加强夹钳料头与锻件之间的连接,便于锻件起模。
钳口的简图如下:
钳口的尺寸有表7.27(见《锻造模具简明设计手册》)查出
:
宽度B=80mm
高度h=40mm
圆角R=15mm
宽度a=1.5mm
钳口颈的高度b=6mm,
壁厚L=20mm
L1按布排情况定为50mm
图5钳口
4、锻件基本参数的确定
经过估算,此锻件的主要参数如下:
(1)锻件在分模面上的投影面积:
F分=8876mm2
(2)锻件的周边长度:
L周=492.3mm
(3)锻件的体积:
V锻=176026mm3
(4)锻件质量:
G=0.176×
7.85=1.4kg
5、锤锻吨位的选择
模锻锤吨位选择恰当,既能获得优质锻件,又能节约能量,保证锻模具有一定的寿命。
关于模锻变形力的计算方法,尽管有不少理论的计算方法,但因模锻过程是一个短暂的动态变化过程,受到诸多因素的制约,要获得准确的理论解是很难的。
因此,生产中,为方便起见,多用经验公式或近似解的理论公式确定设备吨位。
有时,还可采用更为简易的办法,即参照类似锻件的生产经验,通过类比来选择吨位。
查《锻造模具简明实际手册》知,通常用下面的公式来确定模锻锤吨位G(t)
G=
KF
式中F——即为总面积,(㎝2)
K——钢种系数,按表4-15选用。
取K=6
总变形面积F为锻件在平面图上的投影面积与毛边面积之和,假定一个飞边宽度L飞宽,计算出总面积F总=F分+L周L飞宽,参考表7.10(见《锻造工艺学与模具设计》)按1~2t锤飞边槽的尺寸考虑。
假设飞边槽的平均宽度为23mm,算出总变形面积F总
F总=F分+L周L飞宽=8876+492.3×
23=20198.9mm2
根据12.6.3(见《锻造工艺学与模具设计》)中相应表确定选用1.5t模锤锻。
因此选用1.5t模锻锤。
锻件飞边的平均截面积F飞=0.75F飞槽=108mm2
飞边的体积V飞=L周F飞=492.3×
108=53168.4mm3
6、锻件毛坯尺寸的确定
由热锻件图可知,该锻件具有较大的弯曲,对于弯曲轴线类锻件,应先将轴线展开成直线,然后作计算毛坯截面图和直径图。
在弯曲型槽内弯曲时,坯料一定会夹紧,并会拉长,因此轴线展开时,两端的长度L1和L3不变,只是9转折处L2要考虑有拉长的现象。
弯曲锻件展开图如图6。
长轴类锻件在终锻前,最好先将等截面的原材料沿轴向预制成近似锻件各截面面积不等截面的中间毛坯,使中间毛坯上每一横截面面积等于带飞边锻件的相应截面积,以保证终锻时,锻件各处充填饱满,飞边均匀,从而节省金属,减轻锻模型槽磨损,按要求计算的坯料,通常称为计算毛坯。
计算毛坯可用计算毛坯截面图和计算毛坯直径图表示。
计算毛坯的依据是,假定轴类锻件在模锻时属平面应变状态,因而计算毛坯的长度与锻件长度相等,而轴向各截面面积应与锻件上相应截面面积和飞边面积之和相等。
-
图6锻件未展开
图7锻件弯曲部分展开后
(1)计算毛坯的长度(包括模锻斜度在内的热锻件的长度)L计=164mm
(2)计算毛坯的体积V计
V计=V锻+V飞=176026.5+53168.4=229195mm3
(3)计算毛坯的平均截面积F平
F平=V计/L计=229195÷
164=1398mm2
(4)计算毛坯的平均截面直径d平
d平=1.13
=42.2mm
(5)计算毛坯的各截面F计
F计=F锻+2F飞,计算结果见下表1-1
(6)计算毛坯各截面直径d计
计算结果见下表1-1
参数
1
2
3
4
5
6
7
8
F锻
1087
690
1305
540
409
611
650
65
2F飞
216
F计=F锻+2F飞
1519
1122
1737
972
841
1043
1082
497
d平=1.13
44
37.9
47.1
35.2
32.8
36.5
37.2
25.2
表1-1
根据零件的形状特点,分别选取8个主要截面,根据表中的数据在坐标纸上绘出变速叉的截面图和直径图,如图7所示,计算毛坯图按热锻件尺寸计算,这样也有利于后面型槽的设计。
图8计算毛坯图
(a)毛坯截面图(b)毛坯直径图
7、模锻工步的选择
由于此锻件杆部不是等断面的,并且要求杆部表面光滑,为了易于充满模膛,所以必须预先采用滚压以及弯曲等工步,改变坯料的形状。
长轴类锻件的基本特征是其纵向尺寸比横向尺寸大的多,由于锻件大头部分是叉形,在终锻前需要进行劈料;
杆部与大头连接处宽度有突变,又是大批量生产的锻件,所以应尽量提高锻模的寿命,因此采用预锻是合理的,一次确定该锻件采用开式滚压——弯曲——预锻——终锻几个模锻工步成形。
下图为长轴类锻件制坯工步选用拔长工步及滚压工步的图解法
图9选定拔长工步及滚压工步的图解法
图示:
1—拔长或拔长加滚压区;
2—滚压区;
3—不需拔长或滚压区;
Fmax—计算毛坯的最大截面积;
F—计算毛坯的平均截面积;
L—锻件的长度。
经计算可知,其在第二区域,故只需滚压就可以了。
8、毛坯尺寸的确定
采用弯曲-滚压工步,参考表3.5(见《锻造工艺学与模具设计》)可知,滚压时在有聚料作用的情况下,可采用以下公式
坯料截面积F坯=0.8F最大=0.8×
1737=1389.6
d坯=1.13
=42.1mm
式中d坯—圆柱形坯料的直径
可取d坯=43mm
毛坯的体积V坯,可用下式计算,查《锻造模具简明实际手册》得,取
=3
V坯=(V锻+V飞)(1+
%)=V计(1+
%)
式中V计=229195mm3
—烧损率,取
V坯=V计(1+
%)=229195×
(1+3%)=236070.85mm3
毛坯的长度为L坯,可用下式计算
L坯=
=
=162.6mm
根据实际计算,下料长度可取为L坯=164mm
9、制坯型槽的设计
制坯在锻件的生产中有至关重要的作用,一个锻件能够顺利锻出与出好的坯料有直接关系,好的坯料有利于金属流动,易于充满模膛。
9.1开式滚压模膛的设计
滚挤型槽用来减小坯料局部截面积,增大另一部分的截面积,使坯料体积分布符合计算毛坯的要求,兼有滚光和清除氧化皮的作用。
滚挤型槽由钳口、型槽本体和毛刺槽组成,钳口用来容纳卡钳并卡细坯料,毛刺槽是用来容滚压时产生的端部毛刺,本体使坯料变形。
也分开式和闭式两种形式。
本锻件采用开口式滚压模膛的形式,如图11所示,这种模膛的端面为矩形,聚料作用较小,适合用于坯料各段截面变化较小时。
所滚压表面不圆滑。
但此种模膛制造较为方便。
滚挤型槽也是以计算毛坯为依据进行设计的,根据滚挤型槽与锻件截面积相等原理,有下列计算公式:
(1)计算开式滚压模膛的高度h1(参见表7.16)
h1=K
计
式中K——系数,查出的K列于表1-2
K
1.15
0.80
0.85
计算值h1=kA计
44.9
26.8
48
25
24.7
25.8
26.3
19
取用的h/mm
26
24
(2)计算开式滚压模膛的宽度B
杆部宽度:
头部宽度:
调整型槽头部和杆部宽度,均取B=80mm
(3)型槽的长度
型槽的总长度及各部分的长度等于计算毛坯相应的长度。
为了使头部易于充满,可将滚压型槽的头部的长度加大。
图11开式滚压型槽
9.2弯曲模膛的设计
弯曲模膛的作用是将坯料在弯曲模膛内压弯,使其符合于预锻或终锻模膛在分模面上的形状.弯曲变形时金属轴向流动很小,没有聚料作用,但在个别截面处可对坯料卡压。
弯曲模膛的设计依据是预锻或终锻模膛的热锻件图在分模面上的投影形状.其设计要点是:
1弯曲模膛的急剧弯曲处应设计成较大的圆角,特别是弯曲处转角接近或小于90o时,应加大转角半径R以免在预锻,终锻时产生折叠;
2弯曲模膛的下模上应有两个支点,以放置压弯前的坯料并使处于水平位置;
3弯曲模膛下模应有固定的或可调整的坯料定位装置;
4手工操作的弯曲模膛应有夹钳口.
根据弯曲变形时坯料有无拉伸现象来考虑的。
弯曲型槽有自由弯曲式和夹紧弯曲式两种。
在自由弯曲型槽中弯曲制坯时,坯料没有明显的拉长现象,它适用于圆浑弯曲的锻件,且一般只有一个弯角。
在夹紧弯曲型槽中弯曲时,毛坯拉伸变形大且兼有成形,它适用于多个拐弯的且又为急突弯曲形状的锻件,如多拐曲轴等。
该锻件采用自由弯曲模膛简图如下:
图12自由弯曲型槽
弯曲型槽的纵剖面形状是根据终锻模膛在分模面上的外形(水平投影),以作图法制出。
型槽各处高度尺寸比锻件相应处宽度尺寸减小2~lOmm,大锻件减小多些,小锻件减小少些,或按下式(见《锻造模具简明实际手册》)确定:
h=(0.8~0.9)b锻
式中:
b锻—热锻件在分模面上相应位置的宽度。
模膛高度尺寸减小的目的是使弯曲后的坯料放进终锻型槽更方便。
弯曲型槽的宽度B按下式(见《锻造模具简明实际手册》)计算确定:
B=
+(10~20)(mm)
式中F1——在型槽最深度处的坯料截面积,F1=1737mm2
hmin——在模膛最小深度处的模膛深度,
弯曲型槽的深腔处,尺寸应加,起容纳氧化皮的作用。
取B=80mm
为避免在弯曲过程中损坏毛坯端部,弯曲型槽上模两端应加大腔,如图中的G处。
为便于操作和控制弯曲长度,型槽必须设支承面图中的K处。
为防止毛坯横向转动,上模凸起部分应做成凹圆状,凹圆面深度h1按下式(见《锻造模具简明实际手册》)确定:
h1=(0.1~0.2)h
式中:
h—弯曲型槽转角深腔处的高度。
该锻件做成整体式,应尽可能的使上下的凸出部分大致相等,即z1=z2。
上下模相互渗入出应留间隙△,其值按表4-2