云母片冲压工艺及模具设计说明书Word格式文档下载.docx
《云母片冲压工艺及模具设计说明书Word格式文档下载.docx》由会员分享,可在线阅读,更多相关《云母片冲压工艺及模具设计说明书Word格式文档下载.docx(28页珍藏版)》请在冰豆网上搜索。
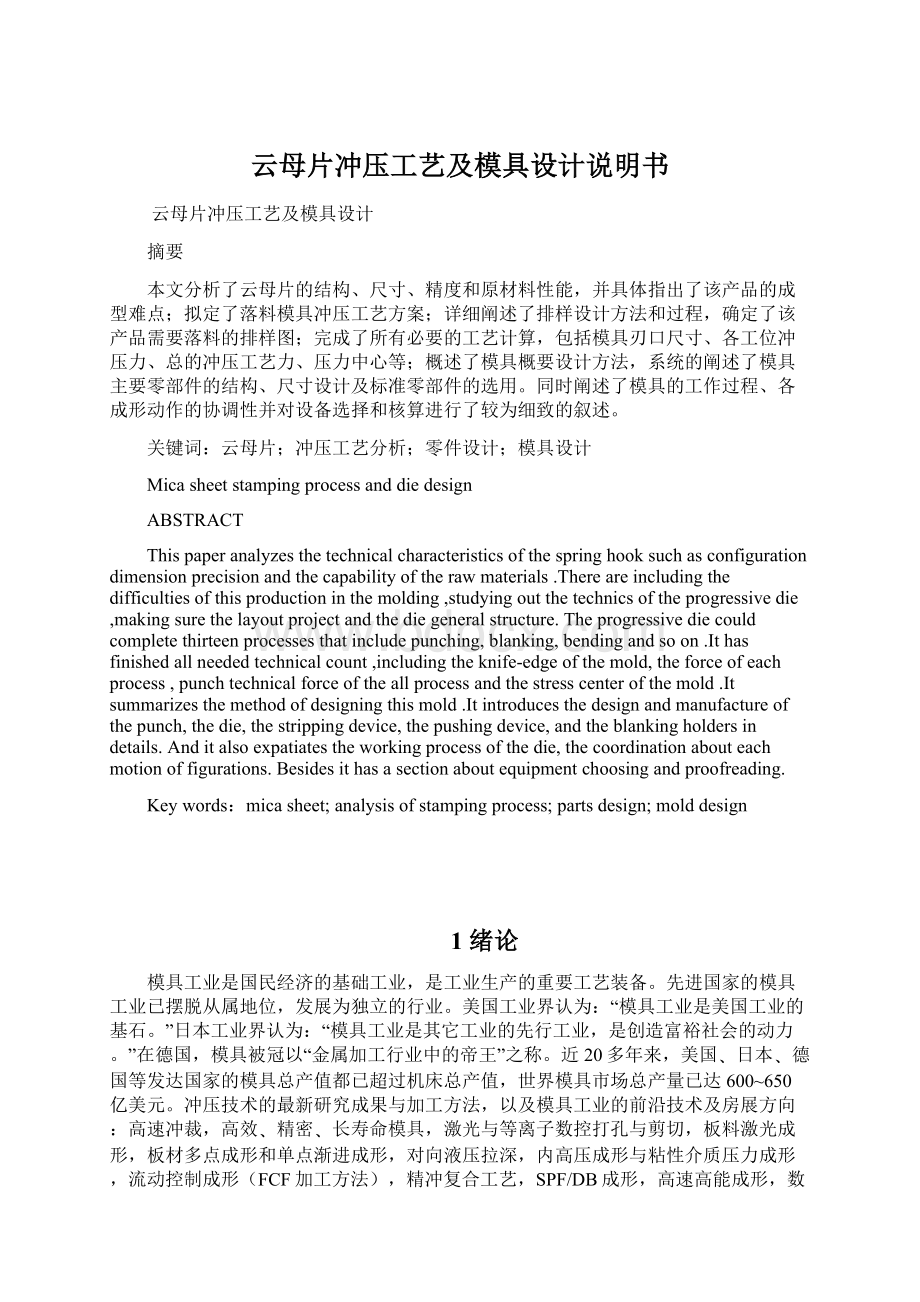
冲压技术的最新研究成果与加工方法,以及模具工业的前沿技术及房展方向:
高速冲裁,高效﹑精密﹑长寿命模具,激光与等离子数控打孔与剪切,板料激光成形,板材多点成形和单点渐进成形,对向液压拉深,内高压成形与粘性介质压力成形,流动控制成形(FCF加工方法),精冲复合工艺,SPF/DB成形,高速高能成形,数字化冲压成形关键技术,冲压成形有限元数值模拟和优化,快速样品生产,冲压生产自动化和柔性加工系统,冲压制品与模具的远程网络设计与制造,冲模CAD/CAE/CAM/PDM,RP技术与快速模具制造。
冲压加工技术应用范围十分广泛,在国民经济各工业部门中,几乎都有冲压加工或冲压产品的生产。
冲裁是冲压工艺的最基本工序之一。
冲裁是利用模具使板料的一部分沿一定的轮廓形状与另一部分产生分离以获得制件的工序。
冲压成形近年来有很多新的发展,在精密冲裁、精密成形、精密剪切、复合材料成形、超塑性成形、软模成形以及电磁成形等方面取得很大的进展。
冲压件的成型精度、生产率越来越高,冲压范围越来越广,由平板零件精密冲裁拓宽到精密弯曲、精密拉深及立体精密成形等。
计算机辅助工程(CAE)在冲压领域也得到了较好的发展和应用,模具计算机辅助设计∕辅助制造技术(CAD∕CAM)、板料成形模拟仿真技术(冲压CAE)、快速成形(RPM)等。
计算机辅助工程可进行应力应变的分析、排样、毛坯的优化设计及工艺过程的模拟与分析等,实现冲压过程的优化设计。
冲压生产主要是利用冲压设备和模具实现对金属材料(板料)的加工过程。
所以冲压加工具有如下特点:
(1)生产效率高、操作简单、内容实现机械化和自动化,特别适合于成批大量生产;
(2)冲压零件表面光滑、尺寸精度稳定,互换性好,成本低廉;
(3)在材料消耗不多的情况下,可以获得强度高、刚度大、而重量小的零件;
(4)可得到其他加工方法难以加工或无法加工的复杂形状零件。
本论文主要以云母片冲压模具设计为主线,云母材料为天然矿因其材料为天然矿制品,具有无污染、绝缘、耐电压性能好和化学稳定性的特点,而且云母片是一种多层结晶体的非金属材料。
因云母本身具有独特的耐高温、耐高压及高度的绝缘性能,因此,在电子、仪器仪表等行业应用广泛。
故可根据客户需求冲切各种规格的天然云母片。
采用云母板制得零件云母片,材料壁厚较薄,零件为异形件,结构虽较为复杂,但只要用适合的冲孔落料就可以获得所要的零件。
依据模具的基本组成部分,采取基础和设计技巧相结合,理论与实践相结合,图例与剖析相结合,模具设计与加工工艺相结合的方式,分析云母片的冲压工艺性,提出设计其模具的多种方案,通过比较分析设计出较合理的模具。
同时,从模具的加工工艺的角度出发,分析并提供便于加工的模具结构形式,使模具设计和加工更加紧密的结合在一起。
本论文在设计时广泛吸收了国内外各个领域成熟的经验和最新的参考资料,并在模具的成型零部件等关键部位采用了国内外的优质模具钢。
为了顺应形势发展的需要,在技术上也有一定的创新,使用了计算机辅助设计来绘图,如UG、AUTOCAD等,达到优化设计的目的。
毕业设计是按查阅资料、学习、消化、吸收、创新的思路进行的。
本论文是关于介绍我在毕业设计中做的一副云母片落料模具的全部设计资料,文中包含了较详细的工艺分析、模具结构设计及冲压机床的选择。
整个设计是在老师的辅导下以及和同学的相互探讨下完成,通过这次毕业设计的锻炼,我增加了专业知识,丰富了视野,提高了自主创新的能力。
但是,我毕竟是初次接触模具如此具体的设计,再加上知识经验的局限现性,设计内容可能会有一些漏洞和错误,学生的所有不足之处,殷切希望各位尊敬的老师及所有的评委能给予指正和指导,谢谢各位老师。
2工艺设计
2.1零件介绍
本次毕业设计的产品见图2.1所示,材料为厚1mm的Q235钢板料,要求批量为中批量。
该零件属于典型的冲裁件,如图2.1零件尺寸图,图2.2云母片工件图所示
图2.1零件尺寸图
图2.2云母片工件图
2.2零件工艺性分析
零件尺寸:
图中零件未注公差取ST8级,零件的尺寸较小,成形的位置较为紧凑,成形比较简单。
零件材料为Q235钢,是普通的碳素结构钢,有一定的塑性,料厚为1mm属薄料,冲压性能良好,零件需要经过一次冲裁,零件的结构比较对称,冲压性能仍然很良好。
综上所述,得到结论:
零件具有较好的可冲压性。
2.3工艺方案的确定
确定工艺方案首先要确定的是冲裁的工序数,冲裁工序的组合以及冲裁工序顺序的安排。
冲裁工序一般易确定,关键是确定冲裁工序的组合与冲裁工序顺序。
应在工艺分析的基础上制定几种可能的方案,再根据工件的批量、形状、尺寸等方面的因素,全面考虑、综合分析,选取一个较为合理的方案。
冲裁工序按工序的组合方式可分为单工序冲裁、复合冲裁和级进冲裁。
单工序模是只完成一种工序的冲裁模。
如落料、冲孔、切边、剖切等。
复合冲裁是在压力机的一次行程中,在模具的同一位置同时完成两个或两个以上的工序;
级进冲裁是把一个冲裁件的几个工序,排列成一定顺序,组成级进模,在压力机的一次行程中,模具的不同位置同时完成两个或两个以上的工序,除最初几次冲程外,每次冲程都可以完成一个冲裁件。
由零件的工艺分析及图可知:
该工件落料一个基本工序:
落料,故采用采用单工序模生产。
3排样设计
3.1毛坯排样设计
在进行模具设计时,首先要设计条料排样图,条料排样图的设计是模具设计时的重要依据。
模具条料排样图设计的好坏,对模具设计的影响是很大的,排样图设计错误,会导致制造出来的模具无法冲制零件。
条料排样图一旦确定,也就确定了被冲制零件各部分在模具中的冲制顺序、模具的工位数、零件的排样方式、模具步距的公称尺寸、条料载体的设计形式等一系列问题。
在本模具中,排样设计总的原则是先进行冲切废料,然后拉伸,最后切断,并要考虑模具的强度、刚度,结构的合理性。
冲裁件在条料、带料或板料上的布置方法叫排样。
排样合理就能用同样的材料冲出更多的零件来,降低材料消耗。
大批量生产时,材料费用一般占冲裁件的成本的60%以上。
因此,材料的经济利用是一个重要问题,特别对贵重的有色金属。
排样的合理与否将影响到材料的经济利用、冲裁质量、生产效率、模具结构与寿命、生产操作方便与安全等。
排样的意义就在于保证用最低的材料消耗和最高的劳动生产率得到合格的零件。
毛坯在板料上可截取的方位很多,这也就决定了毛坯排样方案的多样性。
典型毛坯排样:
单排、斜排、对排、无费料排样、多排、混合排。
根据此次毕业设计的零件结构特征及材料的利用率,决定采用对排,采用这种毛
坯排样的模具结构的相对简单,模具制造较为方便。
1﹑条料搭边值的确定
搭边是指排样中相邻两冲裁件之间的余料或冲裁件与条料边缘间的余料。
其作用是补偿定位误差和保持条料有一定的强度和刚度,防止由于条料的宽度误差、送进步距误差、送料歪斜等原因而冲裁出残缺的废品,保证送料的顺利进行,从而保证制件的质量。
由参考文献[3]得
材料厚度为1mm时,条料长度大于20mm,搭边可以取a=2mm,a1=2mm。
2、条料的宽度
条料是由板料(或带料)剪裁下料而得,为了保证送料顺利,规定条料宽度B的上级极限偏差为零,下偏差为负值(-Δ)。
条料在模具上送进时常用导尺导向,使用导尺又分为有侧压导向和无侧压导向两种情况。
两种导向情况下的条料宽度计算不同,但目的是一致的,要求既能保证条料的顺利送进,又能保证冲裁件与条料侧边之间有不低于规定的搭边值。
条料采用无侧压,可以确定条料与导料销的间隙和条料宽度偏差分别为c1=0.5mm,Δ=0.6mm由参考文献[3]中公式得
条料宽度
(3.1)
3、步距
冲裁模的步距是确定条料在模具中每送进一次,所需要向前移动的固定距离。
步距的精度直接影响到冲件的精度。
设计连续模时,要合理的确定步距的基本尺寸和精度。
步距的基本尺寸,就是模具中相邻工位的距离。
此次毕业设计的条料为单排,步距的基本尺寸等于冲压件的外形轮廓尺寸和两冲压件间的搭边宽度之和,其步距基本尺寸由参考文献[3]得:
h=L+a(3.2)
式中h---冲裁步距
L---沿条料送进方向,毛坯外形轮廓的最大宽度值
a----沿送进方向的搭边值
排样方式图3.1所示
图3.1坯料排样图
=[45+2×
﹙2+0.6)﹢0.5﹚0-0.6=50.70-0..6mm
该零件的步距确定为:
h=L+a=35+3=38mm
借助UG软件分析可得单个零件的面积为A=1032mm2,一个步距的材料利用率η为
η=﹙A∕h×
B﹚×
100%=﹙1032/38×
50.7﹚×
100%=53.6%
排样方式图3.2所示
图3.2坯料排样图
条料宽度
步距hh=62.5mm
一个步距的材料利用率η为
100%=﹙1032×
2/50.7×
62.5﹚×
100%=65.1%
由上计算知道方案的材料利用率分别为56.9%和67%。
其中第一种排样方式材料的利用率少于60%,这样原材料没有得到合理的利用。
而第二种排样方式虽然需要二次送料,但材料利用率高,为此我们选择方案二的排样方式。
3.2材料的利用率
1、排样方式的确定
根据冲裁件的结构特点,排样方式可选择为:
对排,有废料排样。
2、送料进距的确定
为了节约材料,应合理的选择搭边值。
搭边值过小,会使作用在凸模侧表面上的发向应力沿切口分布不均,降低冲裁质量和模具寿命,故必须使搭边的最小宽度大于冲裁时塑性变形区的宽度,一般可以取材料的厚度。
若搭边值小于材料的厚度,冲裁时搭边可能被拉断,有时还会被拉入到凸、凹模间隙中,使零件产生毛刺,甚至损坏模具刃口。
搭边值的大小与材料的性能、零件的外形及尺寸、材料的厚度、送料及挡料的方式、卸料方式有关。
硬材料的搭边值可以小一些,软材料和脆材料的搭边值应大一些。
零件尺寸大或有尖突时,搭边值应大一些,厚材料的搭边值取大一些。
4工艺计算
4.1冲压工艺力的计算
工艺计算是模具设计的基础,只有正确的计算出各道工序的凸凹模尺寸、冲压力、毛坏尺寸等,才能设计出正确的模具。
而且是选用压力机、模具设计以及强度校核的重要依据。
为了充分发挥压力机的潜力,避免因超载而损坏压力机,所以计算是非常必要的。
工艺计算是选用压力机、模具设计以及强度校核的重要依据。
4.2冲裁力计算
冲裁力是冲裁力、卸料力、推件力和顶料力的总称。
冲裁力是凸模与凹模相对运动使工件与板料分离所需要的力,它与材料的厚度、工件的周长、材料的力学性能等参数有关。
冲裁力是设计模具、选择压力机的重要参数。
计算冲裁力的大小是为了合理的利用冲压设备和设计模具。
选用冲压设备的标准冲压压力必须大于所计算的冲裁力,所设计的模具必须能够传递和承受所计算的冲裁力,以适应冲裁的要求。
该模具采用弹性卸料和下方出料方式。
总冲压力
由冲裁力
、卸料力
和推件力
组成。
若采用复合冲裁模,其冲裁力由落料冲裁力
和冲裁力
两部分组成。
冲裁力是冲裁过程中凸模对材料的压力,它是随凸模行程而变化的。
通常说的冲裁力是指冲裁力的最大值。
平刃冲模的冲裁力可按下式计算:
(4.1)
式中F——冲裁力(N);
L——零件剪切周长(mm);
t——材料厚度(mm);
——材料抗拉强度(MPa)。
K——系数,一般取K=1.3。
已知零件材料是Q235,取
=400Mpa,材料厚度t=1mm,L值由全部冲裁线即冲裁零件周长尺寸组成,由于零件是异形件,形状比较复杂,用手工计算零件的周长比较困难,借助CAD中“面域、查询面域∕质量特性”等命令测出该零件的周长为L=187.98mm,取L=188mm。
1)落料、冲裁力。
材料Q235铜的抗拉强度可按
2)推件力,K推=0.055
F推=nK推F=1×
0.055×
112.8=6.2kN
3)力。
查表得卸料力系数
4)总冲压力
的确定
所以总冲压力
=F落+F推+F卸=112.8+6.2+5.64=134.64kN
冲压力合力的作用点称为冲模压力中心。
冲模压力中心应尽可能和模柄的轴线以及和压力机滑块的中心线重合,以使冲模平稳地工作,减少导向机构滑动件之间的磨损,提高运动精度以及模具和压力机的寿命。
求合力作用点可转化为求轮廓线的重心。
具体的方法如下:
(1)按比例画出每个凸模刃口轮廓的位置;
(2))建立坐标轴线,分别凸模刃口轮廓的压力中心及坐标位置x1,x2,x3,...,xn和y1,y2,y3,...,yn。
(3)分别计算凸模刃口轮廓的冲裁力F1,F2,F3,…,Fn或每一个凸模刃口轮廓的周长L1,L2,L3,…Ln。
(4)对平行系,冲裁力的合力等于各力的代数和,即F=F1﹢F2﹢F3﹢…Fn。
(5)根据力学原理,即可求出压力中心的坐标(x0,y0)。
按下列公式求出冲模压力中心的坐标值(x0,y0)
(4.2)
(4.3)
由于该零件形状对称,所以压力中心在该零件的中点上坐标值(X0,Y0),如图3.1所示
图4.1零件轮廓线划分图
=2788.17/173.83=16
=4134.46/173.83=24
由以上计算可知冲裁件(云母片)的压力中心的坐标为(16,24)。
如下图3.2所示
图4.2零件压力中心图
5模具总体结构设计
5.1模具概要设计
冲压制件的质量,不仅依赖于模具的正确设计,而且在很大程度上取决于模具的制造精度,而模具生产又多为单件小批量生产,这给模具生产带来许多困难,为了获得高质量的冲压制件,冲模制造时,在工艺上要充分考虑模具零件的材料、结构形状、尺寸、精度、工作特性和使用寿命等方面的不同要求。
模具是用多个零件按照一定关系装配而成的有机整体,结构是模具的“形”。
模具的优劣很大程度上体现在模具结构上,因此落料模具的结构对模具的工作性能、加工性、成本、周期、寿命等起着决定性作用。
在此次模具的结构设计大体可以分为两步:
第一步根据工序排样的结果确定模具的基本结构框架,确定组成落料模具的主要结构单元及形式,对模具制造和使用提出要求;
第二步确定各结构单元的组成零件及零件间的连接关系。
结构设计的结果是模具装配图和零件明细表。
在结构设计中概要设计是模具结构设计的开始,它以工序排样图为基础,根据产品零件要求,确定落料模具的基本结构框架。
结构概要设计包括:
(1)模具主要零件凸凹模的设计,计算过程;
(2)模具基本结构:
定位方式以及导向方式确定;
卸料方式以及出件方式确定;
(3)模具基本尺寸:
模具工作空间尺寸、各个板件的厚度、模具闭合高度;
(4)模架基本结构:
模架的类型,导柱与导套选配以及模柄类型的选择;
(5)压力机的选择:
压力机的类型,压力机规格;
(6)设备校核:
压力机的校核。
5.2模具零件结构形式确定
该零件是用落料模具完成的。
模架是模具的主体结构,采用自行设计的模架机构导向,采用后侧导柱模架,导向装置在后侧,横向或纵向送料都比较方便,并采用弹性卸料装置,落料模具总装图如图5.1所示
注:
1—模柄;
2—止动销;
3—凸模;
4—内六角螺钉;
5—上模座;
6—凸模固定板;
7—橡胶;
8—卸料板;
9—凹模;
10—下模座;
11—导柱;
12—导套;
13—内六角螺钉;
14—卸料螺钉;
15—圆柱销;
16—圆柱销;
17—挡料销;
18—垫板
5.1模具整装图
凹模外形尺寸应保证有足够的强度和刚度。
由于凹模的结构型式不一,受力状态又比较复杂,首先考虑是在冲裁工位所要受到的冲裁力,所以要适当增加凹模厚,一般根据冲裁件尺寸和板料厚度,由文献[2]凹模的厚度H可按以下经验公式计算
H=Kb(≥15mm)(5.2)
式中K—考虑坯料厚度影响的系数;
b—冲裁件最大外形尺寸(mm);
查文献[1]表8-1,得K=0.35;
H=0.35×
45mm=14.6mm=15.75mm
考虑到压窝凸模的高度,则H调整为25mm,此凹模用于大批量生产,其厚度要考虑修磨量(5~6mm),所以凹模厚度H为25mm。
确定凹模周界尺寸L×
B
由文献[2]可得凹模最小壁厚为1.6mm。
由文献[2]可得凹模壁厚(刃口到外边缘的距离)可按下列公式确定
C﹦(1.5~2.0)H(≥30mm)(5.3)
C﹦1.5×
40mm﹦60mm
所以L=160mm;
B=160mm如下图5.3所示
图5.3凹模图
该模具使用定位销定位夹紧,冲压条料时,销定位挡料销进行导向挡料,由导柱导套导向向下运动,凸模和凹模完成零件的落料工序,弹性元件由于受压反弹,致使得卸料板进行推出材料,制件从下孔掉出,完成整个落料过程。
模具主要有模柄、上模座、垫板、凸模固定板、凸模、凹模、卸料板、凸模固定板、螺钉、销钉、下模座、导柱、导套等。
落料模具凹模周界长160mm,宽160mm,模具总长250mm,总宽215mm。
模具的闭合高度是h﹦40+10+20+21+1+16+25+45﹦178mm。
凸模固定板用于安装所有凸模、凹模板用于落料。
采用螺钉紧固、销钉定位的方式固定。
卸料板是一整块,采用四个螺钉固定。
5.2.1定位机构
为限制被冲材料的进给步距和正确地将工件安放在冲模上完成下一步的冲压工序,必须采用各种形式的定位装置。
用于冲模的定位零件有导料销、导料板、挡料销、定位板、导向销、定距侧刃和侧压装置等。
定位装置应避免油污、碎屑的干扰并且不与运动机构干涉。
定位精度要求较高时,要考虑粗精度和精精度两套装置,分步进行;
坯料需要两个以上工序的定位时,它们的定位应该一致,如图5.2圆柱销图所示
图5.2圆柱销图
5.2.2卸料机构
卸料机构的主要作用是把材料从凸模上卸下,有时也可作压料板用以防止材料变形,并能帮助送料导向和保护凸模等。
可分为固定卸料装置、弹压卸料装置和废料切刀。
固定卸料板仅起卸料作用时,凸模与卸料板的双边间隙取决于板料厚度,一般在0.2~0.5mm之间,板料薄时取小值,板料厚时去大值。
当固定卸料板兼起导板作用时,一般按H7/h6配合制造,但应保证导板与凸模hi之间间隙小于凸、凹模之间的冲裁间隙,以保证凸、凹模的正确配合。
固定卸料板的卸料力不大,卸料可靠。
因此,当冲裁板料较厚(大于0.5mm)、卸料力较大、平直度要求不很高的冲裁件时,一般采用固定卸料装置。
弹压卸料装置既起卸料作用又起压料作用,所得冲裁质量较好,平直度较高。
因此质量要求较高的冲裁件或薄板宜用弹压卸料装置。
废料切刀是在冲压过程中将废料切断成数块,避免卡箍在凸模上,切刀夹角α一般为78~80度。
主要用于小型模具和切断薄废料以及大型模具和切断厚废料。
在本次模具设计中采用弹压卸料板,弹性卸料板具有卸料和压料的双重作用,多用于冲制薄料,使工件的平面度提高,卸料板的尺寸取160×
160×
20mm如图5.3卸料板图所示
图5.3卸料板图
5.2.3导向机构
对生产批量大,要求模具寿命和制件精度较高的冲模。
一般应采用导向机构来保证上、下模的精确导向。
上、下模导向,在凸、凹模开始闭合前或压料板接触制件前就应该充分的合上。
导向机构有导柱、导套机构,侧导板与导板机构和导块机构。
在此副模具中由于零件的尺寸较小,对制件的精度要求较高。
所以采用后置导柱、导套和压入式模柄配合,这样的后置导柱导向精度比较平稳,精度较高,图5.4所示
图5.4滑动导柱、导套
6模具零件的设计与计算
6.1工作零件
6.1.1冲裁凸、凹模刃口尺寸计算
1、冲裁凸、凹模刃口尺寸计算原则
计算冲裁凸、凹模刃口的依据为:
①冲裁变形规律,即落料件尺寸与凹模刃口尺寸相等,尺寸与凸模刃口尺寸相同。
②零件的尺寸精度。
③合理的间隙值。
④磨损规律,如圆形凹模尺寸磨损后变大,凸