液压升降台设计Word下载.docx
《液压升降台设计Word下载.docx》由会员分享,可在线阅读,更多相关《液压升降台设计Word下载.docx(29页珍藏版)》请在冰豆网上搜索。
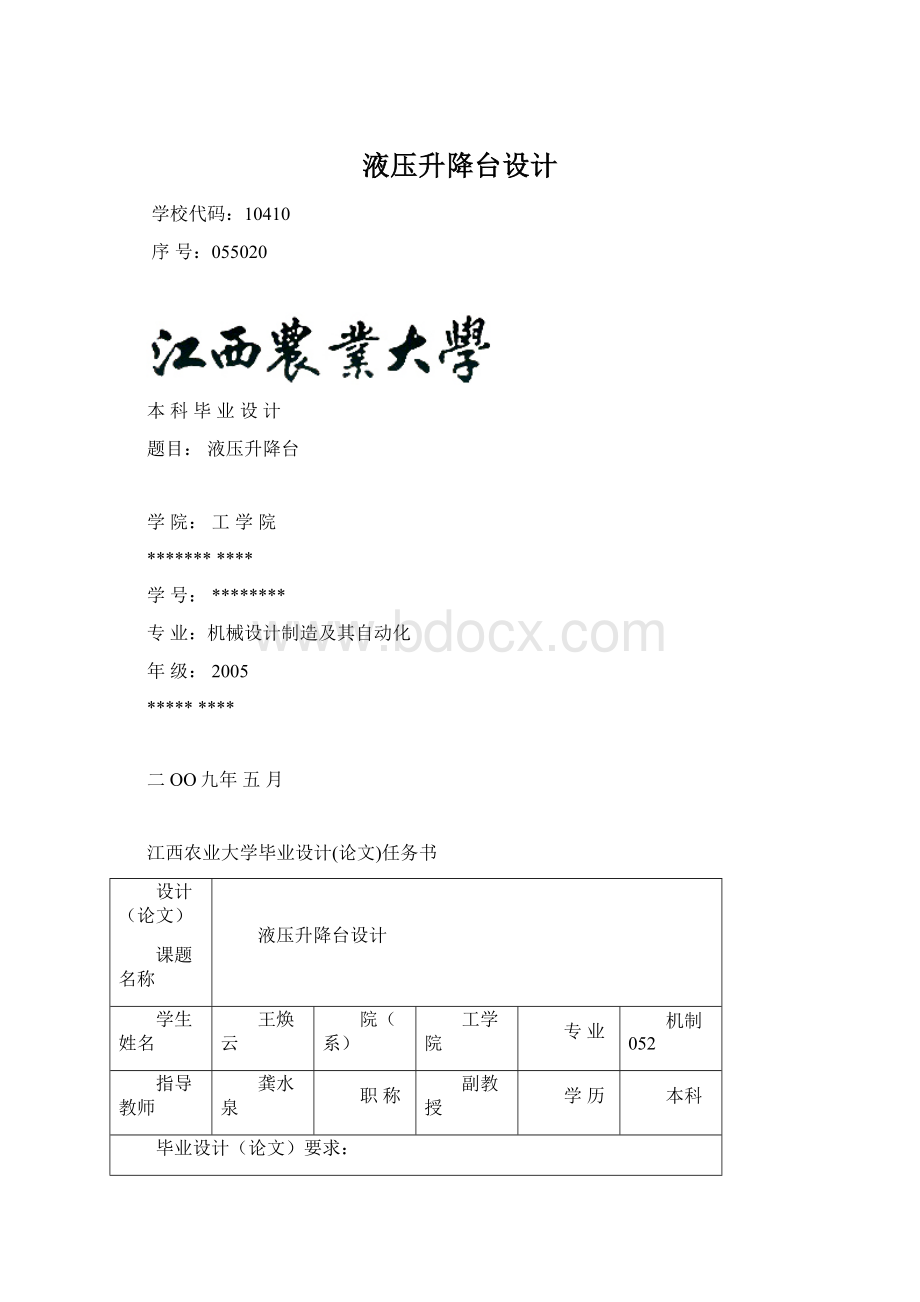
职称
副教授
学历
本科
毕业设计(论文)要求:
有以下图纸和技术文件:
装配图
零件图
液压原理图
零件表
液压元件表
标准件表
设计说明书
毕业设计(论文)内容与技术参数:
设计一台液压升降台主要技术参数如下:
幅面2600×
1400mm
起升最大重量3T
起升最大高度800mm
毕业设计(论文)工作计划:
接受任务日期2009年2月18日要求完成日期2009年5月20日
学生签名年月日
指导教师签名年月日
院长(主任)签名年月日
摘要
本次设计任务是液压升降台,它是一种升降稳定性好,适用范围广的货物举升设备。
其起升高度800mm,举升重量3T,幅面尺寸2600×
1400mm.其动作主要是由两个双作用液压缸推动“X”型架,带动上板移动来实现的。
该液压升降台主要由两部分组成:
液压部分和机械部分。
设计液压部分时,先确定了液压系统方案。
选择液压基本控制回路时,换向回路选择三位四通电磁换向阀;
平衡回路选择用液控单向阀。
确定各种基本回路后,又确定了液压系统传动形式,拟定液压系统原理图,然后对液压元辅件进行了设计、选择,并对其进行校核。
经过计算后液压缸直径选定为70毫米,液压泵选叶片泵。
根据系统工作的最大功率选Y90S-4三相异步电动机。
在确定泵后,又对其他的元辅件进行了合理的选择,最后确定阀块的设计及效率计算。
机械部分主要由上板架、下板架、内连杆和外连杆四部分组成。
通过设计、选择机械部分材料与结构,并对其进行受力分析与强度校核,结果证明机械部分结构设计可以满足要求,进一步完成了本次设计题目。
关键词:
液压;
升降平台;
上板架;
下板架;
内连杆;
外连杆
hydraulicliftplatform
Abstract:
Thetaskofthisdesignishydraulicliftplatform,itisancarpoliftingequipmentwithgoodstablityoftakingoffandlanding.Itsliftingheightis800mm,weightliftingisthreetons,andframesizeis2600×
1400mm.Itsactionismainlycomposedoftwopairsofhydrauliccylinderstopromotethe"
X"
aircraft,ledingtorealizethemobileplate.Thehydraulicliftingplatformismainlycomposedoftwoparts:
hydraulicpartsandmechanicalparts.Inthedesignofthehydraulicparts,Ifirstmadesurethehydraulicsystem.Intheprocessofselectingthebasicofhydrauliccontrolloop,thedirectionloopIchosentousethreepositionfour-wayelectromagneticvalve,andthebalanceloopIchosentousepilot-controlledcheckvalue.Aftertheidentificationofthebasicloop,Ialsomadesuretheformofhydraulictransmissionsystem,thedevelopmentofthehydraulicsystemschematicdiagram,andthenIdesigned,selectedthehydrauliccomponentsandaccessories,andcheckedthem.AftercalculatingIselectedtwo70mmhydrauliccylinder,Iselectedthevanepumpasthehydraulicpump.AccordingtothemaximumpowerofthissystemIchosenY90S-4three-phaseasynchronousmotor.Afterdeterminingthepump,IalsochosentheothercomponentsandaccessoriesreasonlyandfinalyIdesignedthevalveblockandcalculatedtheefficiency.ThemechanicalpartsismainlycomposedofinsideandoutsidelinkandOnboardaircraft,thenextboardaircraft.Throughthedesign,choiceofmaterialsandthestructureandafterthestressanalysisandstrengthoftheircheck,theresultsprovedthatthemechanicalpartscansatisfythedesignrequirements,whichfurthercompletedthedesignofthesubject.
Keywords:
Hydraulic;
take-offandlandingplatform;
Insideandoutsidelink
1总论
液压传动是以液体作为工作介质,以液体的压力能进行运动和动力传递的一种运动方式。
它先通过能量转换装置(液压泵),将原动机(电动机)的机械能转变为液体的压力能,再通过密封管道,液压控制原件等,经另一能量转换装置(液压缸、液压马达)将液体的压力能转换为机械能,以驱动负载,实现执行机构所需要的直线或旋转运动,与机械传动相比,液压传动具有许多优点,因此在机械工程中广泛应用。
液压传动操纵控制方便,可实现大范围的无级调速(调速范围达2000:
1),它还可以在运动过程中进行调速,调速方便。
液压传动简化了机器结构,减少了零件的数目。
由于系统充满了油液,对各液压件有润滑和冷却的作用,使之不易磨损,又由于容易实现过载保护,因而寿命长。
液压装置工作比较平稳,由于重量轻、惯性小、反应快,液压装置易于快速启动、制动和频繁的换向,既易实现机器的自动化,又易于实现过载保护,液压元件实现了标准化、系列化、通用化,便于设计、制造和使用。
但液压传动也有缺点,其主要缺点为:
(1)液体为工作介质,易泄漏,油液可压缩,故不能用于传动比要求准确的场合。
(2)液压传动中有机械损失、压力损失、泄漏损失,故不宜作远距离传动。
(3)液压传动对油温和负载变化敏感,不宜在低、高温度下使用;
对污染很敏感。
(4)液压传动需要有单独的能源(如液压泵站),液压能不能像电那样从远处传送;
液压元件精度高、造价高,所以需要组织专业生产。
(5)液压传动装置出现故障时不易查找原因,难以迅速排除。
总之,液压传动优点很多,而其缺点正随着生产技术的发展逐步加以克服,因此,液压传动在现代工业中有着广阔的应用和发展前景。
5wT)
液压传动在国民经济各部门应用广泛。
常用于机床工业、汽车工业、航空工业、工程机械、农业机械、轻工机械、冶金机械、起重运输机械、矿山机械、建筑机械、船舶港口机械、铸造机械等。
液压升降平台是一种升降稳定性好,适用范围广的货物举升设备,由于升降平稳、安全可靠、操作简单,经济实用,被广泛应用于生产流水线和仓库、造纸、医药等行业,物料上线、下线;
工件装配时调节工件高度;
高处给料机送料;
大型设备装配时部件举升;
大型机床上料、下料;
仓库装卸场所与叉车等搬运车辆配套进行货物快速装卸等。
因此,对于液压升降平台的设计与研究具有重要意义。
;
固定式液压升降平台主要用于生产流水线和仓库、造纸、医药等行业,可作为送货电梯、输送货物、升降平稳、安全可靠、经济实用,本机适用于人造板生产线中各种板材加工设备进、出料端的等高推接合中间转运。
也可应用于类似用途的其它板形材料生产线中。
优势:
采用液压传动升降机构,升降平稳、快捷、操作简便、易于维护保养、节约能源。
结构稳固、故障率低、运行可靠、安全高效、维护简单方便。
控制方式可选无线遥控等多种方式。
我国液压、气动和密封工业虽取得了很大的进步,但与主机发展需求,以及和世界先进水平相比,还存在不少差距,主要反映在产品品种、性能和可靠性等方面。
液压元件由于制造精度高,因而造价相对于机械零件要求高,为了做到经济实惠,在选择液压元件时,尽量以国内同类产品代替国外产品。
比如电磁换向阀,我选择了沈阳液压件厂的产品,并且有直流电源和交流电源两种,我选择了交流电源。
因为,用交流电源,电磁换向阀如果卡位,电磁铁不至于被烧坏。
但配置一套直流电源的价格远比一个电磁铁的价格高,况且电磁阀被卡住的情况也是偶而的。
权衡了一下还是选择了交流电源。
同理,在一些产品性能不相上下时,我尽量选用了国内液压件厂的产品。
可以省去运费和避免一些其它问题,这都降低了成本。
2确定液压系统方案
液压系统方案的确定是液压系统设计的一个重要环节。
目的是选择回路,并把各回路组成系统,以便以后确定液压系统原理图。
理论课上,我们知道任何复杂的液压系统都是由一些简单的基本回路构成的。
液压元件又组成了基本回路。
所以根据液压系统的动作要求和性能特点选液压元件组成液压系统。
这次毕业设计的液压升降平台要求为:
1、起升最大高度为800mm;
2、台面原始高度为623mm;
3、起升最大重量为3吨。
所设计系统必须能完成举升动作,并达到以上要求,考虑系统效率以及经济上的一些问题。
2.1确定液压基本回路
2.1.1换向回路
换向回路一般都采用换向阀来换向。
换向阀的控制方式和中位机能依据主机需要及系统组成的合理性等因素来选择。
换向回路采用二位四通、三位四通或五通换向阀可使执行元件换向,用二位四通换向阀换向最为方便。
但电磁阀动作快,换向有冲击。
另外,交流电磁阀一般不宜作频繁的切换。
换向回路主要有以下几种:
1.换向阀换向回路
如图2-1采用换向阀的换向回路所示:
该回路采用三位四通电磁换向阀,换向阀在右位或左位时,液压缸活塞向左或向右运动,电液阀处于中位时,液压缸活塞停止运动,液压泵可依靠阀中位机能实现卸荷功能。
2.双向泵换向回路
如图2-2采用双向泵的换向回路所示:
当双向液压泵左侧油口排油时,液压缸活塞右行;
通过调节变量机构(使斜盘倾斜方向或偏心方向改变),使双向液压泵右侧油口排油时,液压缸活塞左行。
图中阀K为安全阀,Y为补油泵溢流阀,P为背压阀
3.用差动缸的换向回路
如图2-3所示:
用差动缸的换向回路是用二位三通阀实现差动缸的换向。
图2-1采用换向阀的换向回路
图2-2采用双向泵的换向回路
图2-3用差动缸的换向回路
我在设计中选择了第一种换向方式,因为换向阀互不相通的油口间的泄漏小,其换向可靠,迅速且平稳无冲击。
2.1.2平衡回路的确定
许多机床或机电设备的执行机构是沿垂直方向运动的,这些机床设备的液压系统无论在工作或停止时,始终都会受到执行机构较大重力负载的作用,如果没有相应的平衡措施将重力负载平衡掉,将会造成机床设备执行装置的自行下滑或操作时的动作失控,其后果将十分危险,液压升降平台也是如此。
平衡回路的功能在于使液压执行元件的回油路上始终保持一定的背压力,以平衡掉执行机构重力负载对液压执行元件的作用力,使之不会因自重作用而自行下滑,实现液压系统对机床设备动作的平稳、可靠控制。
平衡回路主要有以下几种:
采用单向顺序阀的平衡回路
如图2-4(a)所示是采用单向顺序阀的平衡回路,调整顺序阀,使其开启压力与液压缸下腔作用面积的乘积稍大于垂直运动部件的重力。
当活塞下行时,由于回油路上存在一定的背压来支承重力负载,只有在活塞的上部具有一定压力时活塞才会平稳下落;
当换向阀处于中位时,活塞停止运动,不再继续下行。
此处的顺序阀又被称作平衡阀。
在这种平衡回路中,顺序阀调整压力调定后,若工作负载变小,则泵的压力需要增加,将使系统的功率损失增大。
由于滑阀结构的顺序阀和换向阀存在内泄漏,使活塞很难长时间稳定停在任意位置,会造成重力负载装置下滑,故这种回路适用于工作负载固定且液压缸活塞锁定定位要求不高的场合。
图2-4平衡回路
采用液控单向阀的平衡回路
如图2-4(b)所示。
由于液控单向阀1为锥面密封结构,其闭锁性能好,能够保证活塞较长时间在停止位置处不动。
在回油路上串联单向节流阀2,用于保证活塞下行运动的平稳性。
假如回油路上没有串接节流阀2,活塞下行时液控单向阀1被进油路上的控制油打开,回油腔因没有背压,运动部件由于自重而加速下降,造成液压缸上腔供油不足而压力降低,使液控单向阀1因控制油路降压而关闭,加速下降的活塞突然停止;
阀1关闭后控制油路又重新建立起压力,阀1再次被打开,活塞再次加速下降,这样不断重复,由于液控单向阀时开时闭,使活塞一路抖动向下运动,并产生强烈的噪音、振动和冲击。
采用远控平衡阀的平衡回路
在工程机械液压系统中常采用图2-4(c)所示的远控平衡阀的平衡回路。
这种远控平衡阀是一种特殊阀口结构的外控顺序阀,它不但具有很好的密封性,能起到对活塞长时间的锁闭定位作用,而且阀口开口大小能自动适应不同载荷对背压压力的要求,保证了活塞下降速度的稳定性不受载荷变化影响。
这种远控平衡阀又称为限速锁。
由于液压升降台是要保证上升到最高位置时能够较长时间的停留在最高位置处不动,所以综合以上分析,平衡回路我选择采用液控单向阀的平衡回路。
2.2液压传动系统的形式确定
液压传动系统可分为开式系统和闭式系统。
开式液压系统马达或缸的油回油箱,泵从油箱直接吸油;
闭式液压系统马达或缸回的油不回油箱直接去泵的进油口。
开式系统中,油泵自油箱吸油,供给执行机构,低压油直接返回油箱,有系统简单、散热条件好等优点。
闭式系统中油泵进油管直接与执行机构的排油管相连通,形成一个闭合回路。
为了补偿系统中泄漏损失,还需有一个辅助供油泵,其优点是1)油箱所需容积小;
2)无论是高压管路还是低压管路都有一定压力。
因此空气难进入,运转平稳;
3)系统中采用变量轴向柱塞泵,一般不需要换向阀来改变执行机构运行方向,减少了换向时的冲击。
综合以上传动系统的特点我选用开式系统。
2.3液压系统原理图
液压系统原理图是表示液压系统的组成和工作原理的重要技术文件,拟定液压系统原理图对系统的性能及设计方案的合理性、经济性具有决定性的影响。
在以上基本回路确定的基础上,将挑选出来的各个典型回路合并、整理,增加必要的元件或辅助回路,加以综合,构成一个结构简单、工作安全可靠、动作平稳、效率高、调整和维护保养方便的液压系统,拟定液压系统工作原理图,如图2-5所示。
根据原理图可知:
液压升降平台的工作原理为
升降平台工作的时候液压油由液压泵形成一定的压力,经滤油器、电磁换向阀、节流阀、液控单向阀进入液缸下端,使液缸的活塞向上运动,提升重物,液缸上端回油经电磁换向阀回到油箱,其额定压力通过溢流阀进行调整,通过压力表观察压力表读数值。
1-油箱2-滤油器3-空气滤清器4-电动机5-联轴器6-液压泵7-溢流阀
8-压力表开关9-压力表10-电磁换向阀11-单向节流阀12-液控单向阀13-液压缸
图2-5液压系统原理图
3计算和选择液压元件、辅件
3.1液压缸的计算
3.1.1初选执行元件的工作压力
工作压力是确定执行元件结构参数的主要依据,它的大小影响执行元件的尺寸和成本,乃至整个系统的性能,工作压力选得高,执行元件和系统的结构紧凑,但对元件的强度、刚度及密封要求高,且要求采用较高压力的液压泵。
反之,如果工作压力选得低,就会增大执行元件及整个系统的尺寸,使结构变得庞大,所以应根据实际情况选取适当的工作压力,执行元件工作压力可以根据总负载值选取。
系统压力选定是否合理直接关系到整个系统设计的合理程度。
根据我所要设计的机器的特点,并参照有关资料,我初选系统工作压力4MPa。
确定液压缸的主要结构参数:
液压缸一般来说是标准件,但有时也需要自行设计,液压缸需要确定的主要结构尺寸是指液压缸的内径D和活塞杆的直径d。
液压缸的内径D和活塞杆直径d可根据最大总负载和选取的工作压力来确定。
取液压泵的机械效率η为0.97
由资料[1]式(3.2)知活塞面积A=F/ηp=3×
104/(0.97×
4×
106)=7732mm2
D=99.2mm
查资料[3]表3.50,取液压缸的内径为100mm。
杆径比d/D,一般按下述原则取:
当活塞杆受拉时,一般选取d/D=0.3-0.5.当活塞杆手压时,一般取d/D=0.5-0.7。
所以本设计我取d/D=0.7,即d=0.7D=0.7×
100=70mm,
根据液压技术行业标准,由资料[3]表3.51取活塞杆直径为70mm。
(2)泵组选择:
液压杠所需流量为
q=2Av=2×
1/4π(D2-d2)×
V
=2×
0.25×
3.14×
(1002-702)×
10-4×
0.2×
60
=9.6L/min
q=9.6L/min
由资料[3]表2.58YB1系列中压定量叶片泵的型号和技术参数,选取叶片泵YB1—16,排量为16ml/r,公称压力6.3MPa,理论流量为13.6L/min。
转速为960r/min。
(3)电动机选择
电动机最大功率P=pqt
P=106×
16×
10-6×
960/60=1.024kw
根据资料[6]表11.4-1取电动机为Y90S-4。
(4)联轴器的选择
本次设计选择联轴器将电动机和液压泵联接起来。
计算转矩Tca=KAT,查资料[16]表10.1得:
KA=2.2。
名义转矩Y=9550
=9550×
=11.54N·
m
所以Tca=KAT=2.2×
11.54=25.39N·
查手册选LM3型梅花型弹性联轴器。
3.2液压辅助元件的计算及选择
液压辅助元件有滤油器,蓄能器,管件,密封件,油箱和热交换器等。
除油箱通常需要自行设计外,其余皆为标准件。
3.2.1管道的设计
根据叶片泵的额定流量13.6L/min,查资料[6]表10.5-1(JB827-66)。
根据推荐管路通过流量25L/min的管径为8mm,管路通过6.3L/min的管径为5.6mm,所以选取公称直径D=8mm的钢管,钢管外径为14mm.管接头连接螺纹M14x1.5。
与液压缸相连的管道选择用橡胶管,弯曲成型方便。
3.2.2管接头的类型
管接头按材料可分为金属管接头、软管接头和快速接头。
通常选用金属管接头。
金属管接头又可分为扩口式管接头、卡套式管接头、焊接式管接头、球面焊式管接头。
各管接头的特点如下:
扩口式管接头:
利用管子端部扩口进行密封,不需其他密封件;
结构简单,适用于薄管连接,工作压力〈8MPa。
卡套式管接头:
利用卡套变形卡住管子进行密封,装拆方便,但对管子尺寸精度要求较高,工作压力〈31.5MPa。
焊接式管接头:
利用“0”型密封圈端面密封,连接牢固可靠,对管子尺寸精度要求不高。
管壁要求较厚,装配时需要焊接。
工作压力〈31.5MPa。
球面焊接式管接头:
利用球面进行密封,不需要其它密封件,但加工精度要求较高,装配时需要焊接。
工作压力≤35MPa。
根据以上介绍的各种管接头的特点,我选择了焊接式管接头,因为它的特点更适合于我所设计的系统。
3.3油箱的设计
油箱的基本功能是:
储存工作介质;
散发系统工作中产生的热量;
分离油液中混入的空气;
沉淀污染物及杂质。
3.3.1油箱的设计要点
(1)油箱必须有足够大的容积以满足散热、容纳停机时因重力作用而返回油箱的油,操作时油面保持适当高度的要求;
(2)油箱底部做成适当的斜度,并设放油塞,箱底应朝向清洗孔和放油塞倾斜(通常为1/25~1/20),油箱底至少离开地面150mm,以便放油和搬运。
(3)从构造上应考虑清洗换油方便,应设置人孔,便于清洗污物;
(4)箱壁上需装油面指示器,油箱上并装上温度计;
(5)油箱上应有带空气滤清器的通气孔,有时注油孔和通气孔可兼用;
(6)吸油管和回油管应尽量远隔开,吸油管离箱底距离H≥2D(管径)。
距箱边≥3D,回油管插入最低油面以下,防止回油时带入空气。
(7)吸油侧和回油侧要用隔板隔开,用以分离回油带来的气泡和赃物。
隔板高度不低于油面到管底高度的3/4;
(8)为了防锈、防凝水,油箱内壁应用好的耐油涂料。
综合以上的设计要点,我设计我的油箱,但由于机器工作不频繁,所以没有设计温度计,并设计了两个隔板。
3.3.2油箱容积计算
按资料[1]式(4.5)可得V=mqp,低压m=2-4,中压m=5-10,高压m=6-15,本设计取m=3,
V=3x13.6=40.8L
我所设计的油箱没有设冷却器,在这种情况下,油箱的长:
宽:
高为1:
1:
1到1:
2:
3。
油面达到油箱高度的80%。
油箱的长为380mm,宽为360mm,高为300mm。
3.4其它元、辅件的选择
3.4.1.吸油滤油器
液压系统的故障大多数是由于油液中杂质而造成的,油液中的杂质会使液压元件运动副的结合面磨损,堵塞阀口,卡死阀芯,使系统工作可靠性大为降低,在系统中安装滤油器,是保证液压系统正常工作的必要手段。
按滤芯材料和结构形式,滤油器有以下几种形式,其用途特性如下:
(1)网式滤油器装在油泵吸油管上,可以保护油泵。
特性为结构简单,清洗方便,通油能力大,过滤效果差,精度低,常作吸滤器;
(2)线隙式滤油器用铜线或铝线密绕在筒形骨架的外部来组成滤芯,油液经线间间隙和筒形骨架槽孔汇入滤芯内,再从上部孔道流出。
过滤材料强度低,一般用于低压系统,特性为结构简单,过滤效果较好,通油能力大,但不易清洗,多为回油过滤器;
(3)纸芯滤油器用于油的粗过滤,最好与其它滤油器联合使用,特性为过滤效果好,精度高,但易阻塞,无法清洗,需要经常更换纸芯;
(4)烧结式滤油器用于特别要求过滤质量的液压系统中,最好与其它滤油器合用,特性是能在高温下工作与承受较高压力,抗腐蚀能力强,制造简单,性能稳定,滤芯的强度高,抗冲击性能好,且可安装在不同的位置;
(5)磁式滤油器利用磁性吸附油液中的铁质微粒,但一般的磁性滤油器对其他非铁质污染物不起作用,通常用作回油过滤或被用作其他形式滤油器的一部分,用于滤清带磁性铁屑与磨料,特性是效果好,维护复