国内外电子装联标准比较Word文件下载.docx
《国内外电子装联标准比较Word文件下载.docx》由会员分享,可在线阅读,更多相关《国内外电子装联标准比较Word文件下载.docx(49页珍藏版)》请在冰豆网上搜索。
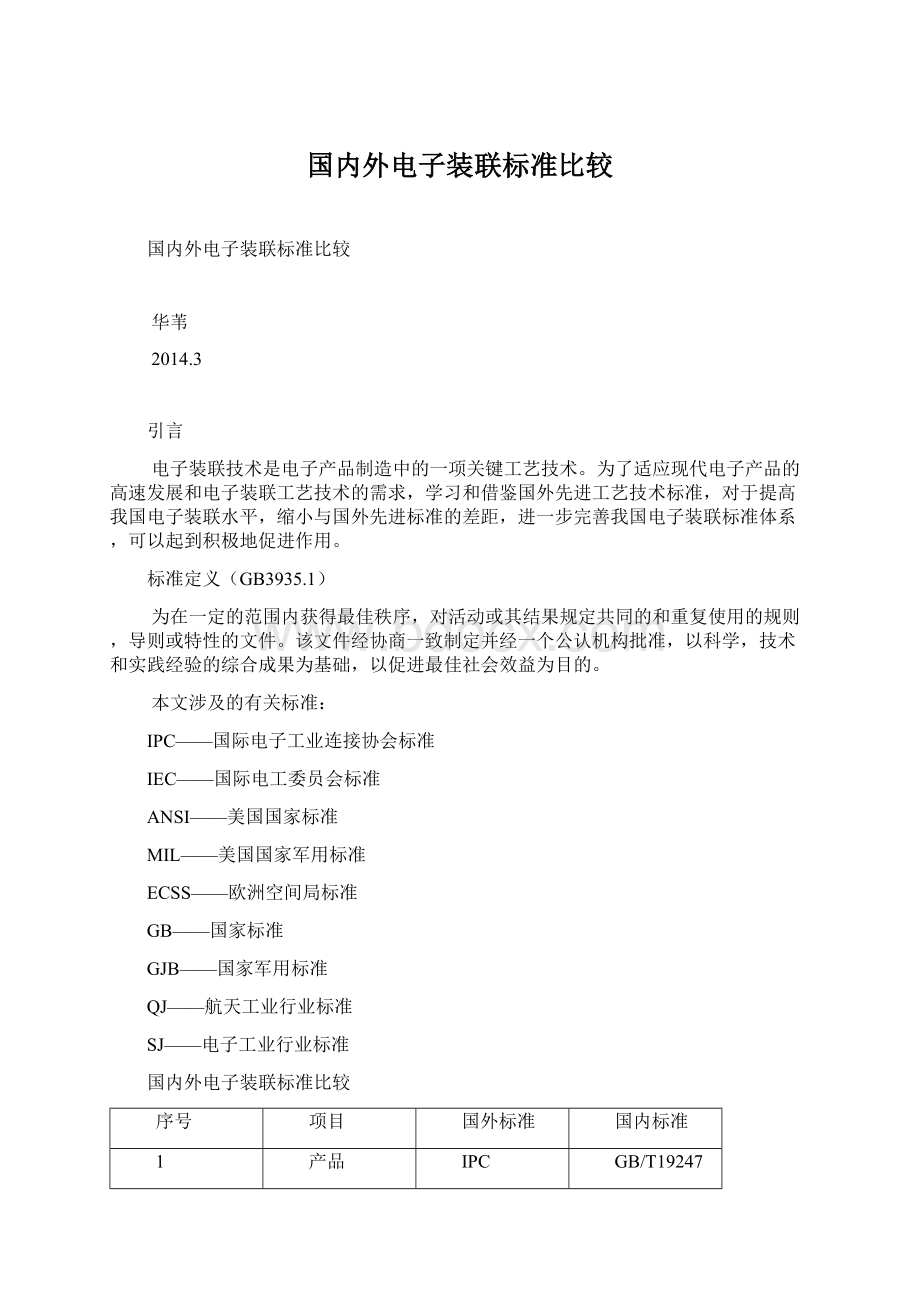
安装
场地
环境
条件
温度:
18~30℃,HR:
30%~70%
照明:
1000lm/m2
静电防护符合ANSI/ES0-20
ECSS
22±
3℃,HR:
55±
10%
1080LUX
静电防护符合EN100015-1
静电防护符合IEC61340-5
QJ165B
23±
5℃,HR:
1000LX
静电防护符合QJ2846GJB1696
3
3.1
焊接
材料
焊料
IPC-005IPC-006
焊料成分:
Sn60A,Sn63A
焊料控制:
焊料槽中Sn含量偏差±
1.5%,焊料槽杂质总量不超过0.4%
锡铅焊料:
Sn62.5~63.5%
Sn61.5~62.5%Ag1.8~2.2%
Sn59.5~61.5%
符合ISO9453Sn60Pb40Sn62Pb36Ag2Sn63Pb37
GB3131
S—Sn63Pb(AA.A.B)
S—Sn60Pb(AA.A.B)
AA级:
Sn62.5~63.5%,杂质总量≤0.05%
Sn62~64%,杂质总量≤0.06%
Sn61.5~64%,杂质总量≤0.08%
注:
1.配比为Sn63Pb372.杂质总量为除Sb、Bi、Cu以外
QJ165
焊料应符合GB3131中的有关规定,PCA焊接采用S—Sn63PbAA,其它场合可采用S—Sn60PbAA
3.2
焊剂
符合J-STD-004或相应要求
材料:
松香(RO)树脂(RE)有机物(OR)
松香(RO):
低活性ROL0、ROL1(IPC004)
●中等活性ROM0、ROM1
●高等活性ROH0、ROH1
ROM、ROH类型焊剂不能用于多股导线的搪锡
MIL
RRMARA
焊剂活性等级分类按IPCJ-STD-004
搪锡:
未氧化ROL1,氧化搪锡ROH1,氧化严重:
INH1
焊接:
推荐ROL0,有清洁度测试要求ROL1
IEC61190-1-1
L—低或无活性焊剂
M—中等活性焊剂
H—高等活性焊剂
L或M型用于组装焊接
H型用于接线端子,硬导线,密封元器件搪锡,使用后需清洗
GB19247.1
根据IEC61190-1-1焊剂分类
焊料应符合GB3131中有关规定,航天电子产品焊接采用松香焊剂,导线、电缆芯线焊接不应使用RA
GB9491
松香型焊剂类型
R:
纯松香基焊剂
RMA:
中等活性的松香基焊剂
RA:
活性松香基焊剂
GB15829
焊剂分类:
树脂型有机型无机型
GJB3243
焊膏中焊剂可采用GB9491中规定的R、RMA型焊剂,不允许使用RA
SJ10670-95
焊膏中焊剂可采用RMA、RA和免清洗焊剂
4
工具与
设备
工具与设备的选择和维护应不降低或损害元件或组装件的设计和使用功能,电烙铁和焊接设备的选择和使用应保证温度控制和对电气过载(EOS)或静电放电(ESD)的保护
电烙铁:
空载/待用温度应控制在±
5℃,空载/待用时实际测量的烙铁头温度应在±
15℃范围内,接地电阻≤5Ω,瞬态电压峰值≤2V
电烙铁选择
烙铁头形状应与焊盘相适应,要求使用温控烙铁并要定期校验,烙铁应在1~2秒内将连接部位加热至焊料液相线温度,并应保持适当焊接温度。
切割工具不能造成冲击损坏元件引线密封或相互连接
热控型绝缘剥离器可适用于各种类型导线绝缘层,最适合用于AWG22号和更细导线
工具和设备在使用前应清洁,并在使用中保持清洁,使用期间远离污物,油污和其他杂质,使用能提供温度控制和绝缘承受ESD或静电放电的电气过应力的烙铁,设备和系统
QJ
工具和设备性能安全可靠,满足产品安装要求,便于操作和维修
电烙铁选定原则:
⏹烙铁温控精度±
5℃,并定期校验
⏹待焊时,烙铁设置温度与实际测量温度的偏差应在±
15℃以内
⏹烙铁头形状满足焊接空间要求
⏹操作舒适,工作寿命长,维修方便
⏹接地良好,电源地与烙铁头部的电位差不大于2mv
剪切工具应保证导线或引线切口整齐,无毛刺
导线绝缘层剥除一般应使用热控型剥线钳,限制使用机械剥线工具
5
5.1
引线
导线
预处理
镀金层去除
具有2.5μm或更厚金层的通孔元器件引线至少95%的被焊表面;
具有镀金层的表面安装元器件被焊表面95%以上
2.5μm或更厚镀金层的焊端通过两次搪锡工艺或波峰焊接工艺去除金层
在PCB上化学浸镍金(ENIG)的表面涂层可不进行除金
将引线浸入到250~280℃焊料槽内(1号槽)2~3秒除金
再将引线浸入到210~260℃焊料槽内(2号槽)3~4秒搪锡
不允许在已用于除金的焊料槽内进行搪锡处理
1号焊料槽内金元素含量不应超过1%,2号焊料槽内金、铜元素总量不应超过0.3%
为使焊料在金镀层上脆裂最小,任何焊点上的金元素总体积不应超过现有焊料体积的1.4%(即质量的3%)
引线搪锡应使用双搪锡工艺或动态波峰焊有效去除金层
使用浸焊、波峰焊、汽相焊或拖焊工艺焊接通孔元器件时,符合下列条件时可不进行除金
⏹现有金层厚度符合可焊性要求
⏹焊接过程中有足够时间温度和焊料,使焊点中金元素含量小于3%
⏹PCB焊盘不镀金,当通孔引线的金层厚度不大于2.5μm,且焊料槽温度超过240℃时,一般不会出现金脆裂
印制板焊盘上镀金层厚度不超过0.15μm
QJ标准
镀金引线或焊端均匀进行除金处理,不允许在镀金引线上直接焊接
镀金引线除金应进行两次搪锡处理,两次搪锡应分别在两个焊料槽中操作
印制板焊盘镀金厚度小于0.45μm可以直接焊接
镀金引线的搪锡一般仅限于焊接部位
5.2
导线端头处理
热剥头导致的绝缘层变色是允许的,但绝缘层不应被烧焦。
化学剥除绝缘层只能用于实芯导线
被焊接的多股导线在安装前应搪锡,焊料应渗透到多股引线内部
焊料的芯吸不能超过导线需要保持柔性的部分,未搪锡长度不大于导线的直径
热控型剥离的加热温度要加以控制以防止绝缘层起泡和过度熔化
在剥离操作中,导线不应被扭曲、环绕、裂口、割断或擦伤
导线搪锡时,应采用标注有导线规格的抗浸锡工具。
GB19247.4
导线应剥除足够的绝缘层,又要保证规定的绝缘距离
化学剥离仅应用于硬引线,且在焊接前应进行中和或除去剥离剂
安装前导线端头需进行焊接的部位应浸锡,焊料应渗透到各线芯内部,应尽量减少绝缘层下焊料芯吸
导线脱头应使用热控型剥线工具,限止使用机械剥线工具
脱去绝缘层的芯线应在4h内进行搪锡处理
多股绞合线搪锡,应使焊料浸透到芯线之间,芯线根部应留0.5~1mm的不搪锡长度
导线脱头不应将导线绝缘层烧焦或发黑
5.3
成形
引线成形不应损伤引线密封、元件焊点或内部连接(引线不能有裂口或超过10%的变形)。
引线弯曲前至少离开本体或熔接点一倍引线直径或厚度的距离,但不得小于0.8mm。
引线弯曲半径
引线直径(D)或厚度(T)
最小内弯半径
<0.8mm
1D或1T
0.8~1.2mm
1.5D或1.5T
>1.2mm
2D或2T
引线弯曲内侧半径应不小于引线直径或带状引线厚度
引线弯曲最小距离,圆形引线应为引线直径的2倍,带状引线应为0.5mm
应对元器件本体与焊点之间的引线进行应力消除,如图所示
GB19247
引线成形工艺不应损坏元器件内部连接
不管引线是由手工、机器或模具成形,若出现超过引线截面积10%的缺口或变形,则不应安装。
外露本体金属不超过引线可焊表面积5%的缺陷是允许的
引线从元器件本体或弯曲半径前的熔焊点的伸出长度,至少应为引线直径或厚度,但不得小于0.8mm,如图所示
引线成形应符合应力消除原则,使两个制约点间的引线具有较大的活动自由度
元器件本体或熔接点到弯曲点的最小距离应为2倍的引线直径或厚度,但不应小于0.75mm
引线成形一般应使用专用工具或工装
引线成形尺寸应符合元器件安装要求,并与PCB焊盘相匹配
表面安装器件引线应采用专用工装和设备成形,以保证引线共面性≤0.1mm,引线与焊盘相接触长度至少应保证1.5倍引线宽度。
5.4
PCB组装前的预烘
PCB应在焊接前8h内进行清洗和去湿处理
去湿处理可在90~120℃烘干炉中进行,时间不超过4h
PCB在组装前应进行清洗和预烘去湿处理
单双面板PCB预烘温度为80~85℃,多层板预烘温度为110~120℃
预烘时间2~4h
6
6.1
元器件通孔
插装
元器件
元器件居中放置于两焊盘之间;
轴向引线元件水平安装到PCB表面时,元件本体接触板的表面。
元件体和板表面之间最大间隙不超过0.7mm。
需要离开板面安装的元件至少抬高1.5mm。
径向引线元器件本体与板面平行且与板面充分接触。
元器件标识清晰;
无极性的元器件依据识别标记的读取方向而放置,且保持一致(从左至右或从上至下)。
应力释放,被成型的引线具有应力释放
GB19247.3
在PCB金属化孔内的引线焊端型式规定为全部折弯,局部折弯和引线直接穿通;
引线应沿印制导线连接到焊盘方向折弯
直接穿通引线伸出的长度,C级不应超过1.5mm,A、B级不应超过2.5mm
金属外壳元器件,应与相邻导电部件绝缘,绝缘材料应与电路和印制板材料相容
元器件安装方式不应堵塞焊料流入需焊接到金属化孔上层焊盘
通孔的焊锡填充
元器件的安装位置不妨
碍焊锡填充需焊接的部位。
空气
引线伸出的长度
非支撑孔中引线的伸出长度
1级
2级
3级
L最小
焊点内端头可辨
足够的折弯
L最大
无短路危险
2.5mm
支撑孔中引线的伸出长度
焊点中引线末端可辨
1.5mm
元器件通孔插装应符合QJ3012的要求。
轴向引线元器件采用水平安装。
元器件安装表面如无印制导线,且功率不大于1W时,可采用贴板安装。
轴向引线玻璃二极管不允许贴板安装。
元器件若安装在裸露电路上,元器件本体与印制导线之间应至少留有0.25mm间隙,但最大距离一般不应超过1.0mm。
非轴向引线元器件本体与印制电路板板面水平安装时(如径向引线电容的水平安装),元器件本体与板面应充分接触,并采取固定措施。
印制电路板元器件安装孔径与元器件引线直径之间应保持0.2mm~0.4mm的安装间隙。
插入任何一个焊盘孔的引线或导线数量不应超过一根。
金属壳体元器件安装时应与相邻印制导线和导体元器件绝缘。
元器件安装应不妨碍焊料流动到被焊接的金属化孔在焊接终止面的焊盘。
元器件安装位置妨碍焊料流动到被焊接的金属化孔在焊接终止面的焊盘的情况如图所示。
从PCB上穿过的每根引线应单独有孔,最好是电镀通孔(金属化)
金属化孔的直径应为引线直径留有0.3~0.65mm的间隙,以便焊料流过
元器件安装时,引线伸出板面的长度为1.5±
0.8mm,如图所示
对于重量超过5g的元器件,应提供辅助支撑
金属壳体元器件安装在印制导体上,相互直接接触时,应有绝缘支撑保护;
玻璃封装元器件可封入到透明弹性套管内
元器件安装后,引线伸出板面的长度为1.5mm±
0.8mm。
元器件安装后,引线端头采用弯曲连接时,应符合下图。
跨接线的安装应符合轴向引线元器件的安装要求。
硬跨线下有印制导线时应套绝缘套管
6.2
非支撑孔焊接最低可接受条件
标准
引线与焊盘的
焊缝和润湿
270°
330°
焊料覆盖
75%
支撑孔焊接
⏹焊料仅施用于电镀通孔的任一个面;
⏹实现电镀通孔的100%焊料填充并在上下两面润湿良好。
引脚修整
当焊后切割引脚,焊接端头或者被再流,或者用10X放大镜目视检查,保证原有焊点未损伤或变形。
界面互连
不运用大批量焊接的(波峰焊)的电镀通孔,用于界面互连时,可不用焊料填充。
焊点应良好润湿,且金属孔填充应达到规定要求,焊料应润湿孔壁,如图
进行焊接的装置应充分加热,以使焊料完全熔融且润湿焊接表面
手工焊接时,焊料只用于金属化孔一面,烙铁头温度不应超过所用焊料规定的工作温度,可以要求预热,以防止元器件损坏
焊料应流满到引线周围和整个焊接区域,角焊缝至少应在引线四个面中的三个面出现
PCB的焊接面的角焊缝应满足规范要求,焊料显示出流过金属化孔
焊料仅用于金属化孔的焊接面
高压连接点应有平滑的角焊缝覆盖,避免锐角和尖角
手工焊接时,对于电子元器件的一般焊接,建议烙铁头温度为280℃,但任何情况下不能超过330℃,对于特殊用途,允许烙铁头温度为360℃
应采用先剪切后焊接的方法,如采用先焊接后剪切方法,应对焊点重熔
金属化孔焊接,焊料只能从PCB焊接面流向元件面,焊料应覆盖整个焊盘,金属化孔内应填满焊料
手工焊接温度,一般元器件,烙铁头温度为280~330℃,特殊场合为360℃
用于层间连接的导通孔,一般可以不要求充填焊料
7
表面
表面安装器件引脚成型
⏹引脚按规定的方式成型,不能损伤或降低引脚与本体的密封。
⏹在装配过程中成型的引脚至少有一段有效长度能与焊盘相接触(1~2倍引脚宽度或直径)。
⏹引脚成型后,如引脚有裂口或若超过直径、宽度或厚度的10%的变形,元器件都不能被安装。
表面安装元器件引线弯曲不应延伸到密封部分,弯曲半径(R)必须大于引线厚度,如图所示
表面安装元器件引线(焊端)位置
片式元件安装
⏹
底部可焊端头
A:
25%W或25%P,二者较小者
B:
不允许
C:
75%W或75%P,二者较小者
D、G:
润湿正常
⏹三面和五面焊端片式元件
A:
B:
C:
50%W或50%P,二者较小者
D:
75%R或75%S,二者较小者
E:
(最大焊缝高度):
不能延伸到元件本体上
F:
(最小焊缝高度):
G+25%H或G+0.5mm
G:
(焊点厚度):
侧面安装:
宽度与高度比不超过2:
扁平带状、L和翼形引脚
⏹圆柱体焊端
焊缝边缘不能越过元件本体
G+25%W或G+1.0mm
J:
(最小末端重叠):
75%R
圆形、压扁(压铸)引线
城堡型可焊端
25%W
75%W
G+H
G+50%H
H(城堡引脚高度)
J型引线
25%W或0.5mm,二者较小者
不违背最小电气间隙
3W或75%L,二者较大者
焊缝可扩展到弯曲的顶部,未接触封装本体或
末端密封处。
至少达到引线弯弧的中点以上(G+T)
长方形或方形引线
J型引脚
25%W
150%W
焊料不接触封装体
G+T
圆柱形焊端
内向L型扁平引脚
75%L
H+G(焊缝不可接触元件体)
K:
50%H或0.5mm
底面焊端
表面安装阵列封装
排列:
焊球偏离不违背最小电气间隙
焊点:
满足标准4.14
BGA焊球接触并润湿焊盘,形成连续椭圆或柱台状焊点。
空洞:
X射线图像,焊球空洞小于25%面积。
城堡型焊端
ECSS(ECSS-Q-ST-70-38C)
片式元件
最大侧面偏移
A
0.1倍引线直径
端部突出
B
最小搭接长度
L
0.13mm
最小填充高度
M
X+0.3h或X+0.5mm,取两者最小值
站高
X
可见~0.4mm
最大翘起角度限制
C
10度
最小焊料覆盖焊盘面积比
-
对接连接
⏹底部焊端
0.75W
从0.1mm到0.4mm
⏹圆柱形焊端
最小填充宽度
E
0.5D
最小侧面搭接长度
0.5T
从可见范围到最大0.4mm
内向带形
城堡型器件
最大搭接长度
P
0.25H
0.1mm~0.4mm
鸥翼型器件
0.1W
最小脚趾距离焊盘长度
0.2mm
最小脚跟距离焊盘长度
0.5W
D
1.5W
最小爬锡高度
X+T
底部焊料填充高度
可见
GJB3243-98“电子元器件表面安装要求”
GJB3835-99“表面安装印制板组装件通用要求”
GJB4907-2003“球栅阵列封装器件组装通用要求”
SJ10670-95“表面组装工艺通用技术要求”
QJ3086“表面和混合安装印制板组装件的高可靠性焊接”
QJ3171-2003“航天电子电气产品再流焊接技术要求”
上述标准中的表面安装均参考I