碱性蚀刻教材文档格式.docx
《碱性蚀刻教材文档格式.docx》由会员分享,可在线阅读,更多相关《碱性蚀刻教材文档格式.docx(12页珍藏版)》请在冰豆网上搜索。
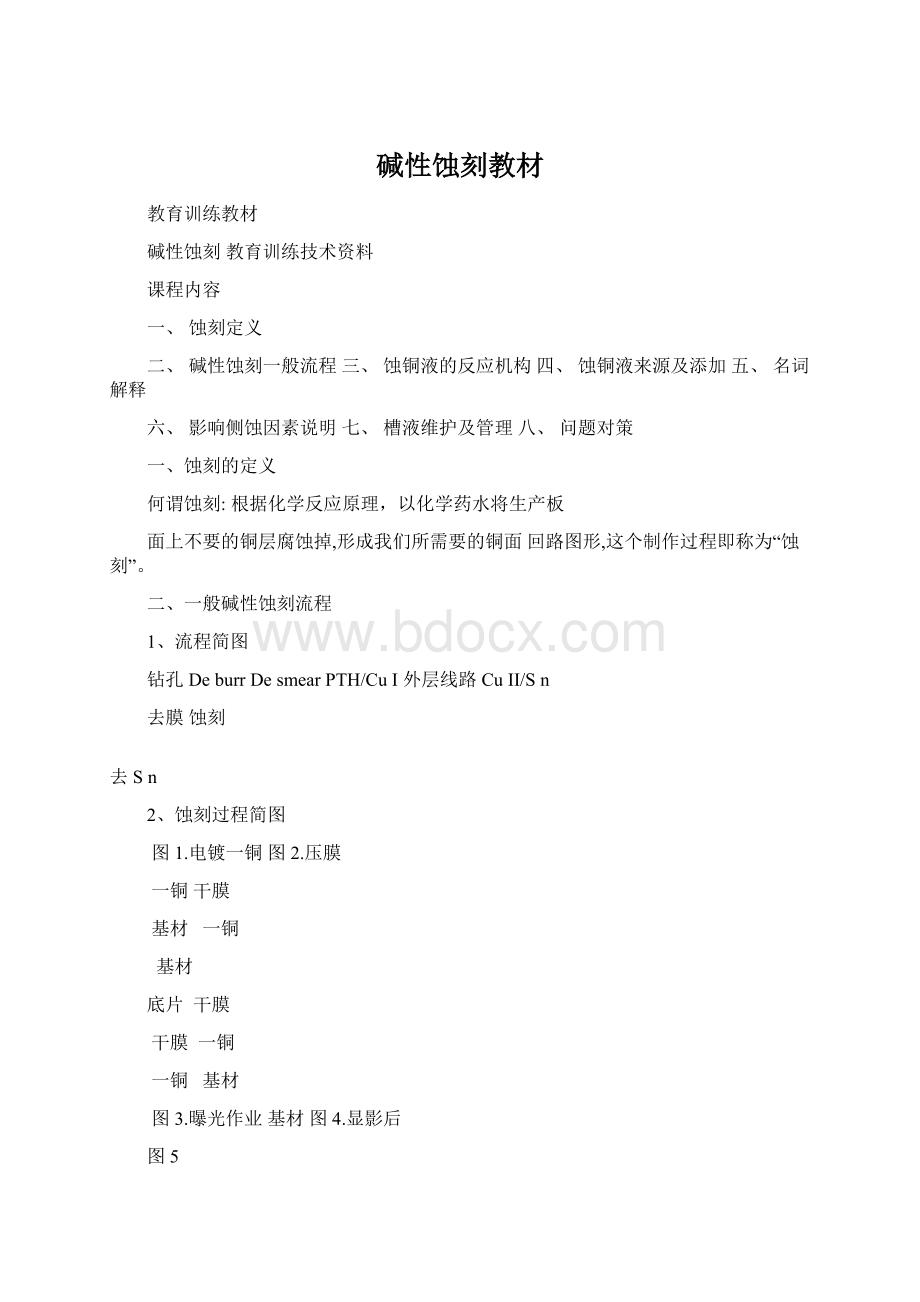
一铜
图6
镀锡铅
锡铅
图7图8
蚀刻药水
蚀刻阻剂
图9
蚀刻后
图10
去锡铅
线路
三、蚀铜液的反应机构
1.蚀刻2Cu+2Cu(NH3)4Cl2(母液)→4Cu+1(NH3)2Cl(亚铜离子)
2.再生4Cu+1(NH3)2Cl+4NH3+4NH4Cl+O24Cu+2(NH3)4Cl2+2H2O
3.净反应:
2Cu+4NH3+4NH4Cl+O2→4Cu+2(NH3)4Cl2+2H2O
第一式反应之中间态亚铜离子之溶解度很差,是一种污泥状的
沉淀物,若未迅速除掉时会在板面上形成蚀铜的障碍,必须辅助以氨水,氯离子及空气中大量的氧,使其继续氧化成可溶性的二价铜离子而又再成为蚀铜的氧化剂,周而复始的继续蚀铜直到铜量太多而减慢为止。
四、蚀铜液的来源及添加
NH4+….NH4ClCu+2..基板底铜+电镀铜(完全溶解)
Cl-……NH4ClCu+1..反应中产生(溶解度低)
NH3…..NH4OH或液氨Cu..基板铜
Stabilizer安定剂…无机添加剂BankingAgent护岸剂…有机添加剂
子液如何添加?
(比重控制器)随着蚀刻的进行,槽液不断溶铜而比重升高,比重控制器会反馈
讯号至添加马达,蚀刻子液便被Dosing(一般流量4-6L/min)进入槽液
如此稀释而达到恢复槽液的设定比重.关于抽风:
子液的PH值会高于槽液所需的PH,多余的游离NH3靠抽风抽走,而且在抽风的过程中会带入空气中的O2而补充再生反映之所需.
蚀刻液操作条件:
范围最适条件
氯离子含量:
175~210g/l190g/l
铜含量:
140~170g/l155g/l
PH值:
8.1~8.88.3
比重:
1.200~1.2301.215/50℃
温度:
45~54℃48℃蚀铜
速率:
(依设备及温度而异)2.5~3.5mil/min
注:
连续操作须具储冷却系统
五、名词解释
1.蚀刻速率(etchingrate):
蚀刻速率是衡量蚀刻液在某蚀刻机上,在一定条件下,单位时间内的蚀铜能力.
一般单位为mil/min或um/min.
测试方法:
a.准备基板做之前烘干(120C*10min).b.将烘干后的基板冷却后称重计W1.c.测试板经蚀刻后(以不露基材为准),烘干(120℃*10min).d.同样冷却后称重计W2.
e.计算:
E.R(mil/min)=(W1-W2)*线速*1000/(2*板面积*8.93*有效槽长*2.54)
影响E.R的因子:
温度、槽液浓度、蚀刻机喷盘喷嘴设计、喷洒压力等
2.蚀刻均匀性:
衡量蚀刻机各喷嘴/喷管在整板面蚀铜深度的均匀度蚀刻均匀性测试:
建议以2oz基板铜测试.测试后均匀性尽可能下喷达到90%,上喷达到85%.(上喷水池效应)均匀性测试方法:
a.以取点法测蚀刻均匀性(上下板面均匀的各取N个点)b.2OZ基板,尺寸为20″×
24″.
c.以CMI先测量蚀刻前上下板面的铜厚(各N个点),再测量蚀刻后的铜厚(N个点),计算出咬蚀量,并分析其在整个上下板面的分布情况,即蚀刻均匀性.
d.计算公式为:
U%=1-(MAX-MIN)/(2*平均咬蚀量).
影响蚀刻均匀性的因子:
喷洒压力、喷嘴形式、喷盘摇摆频率等.
3.蚀刻点测试
蚀刻点即蚀刻露出基材时,板子所处蚀刻槽中的位置.目的:
修饰线路的毛边和克服铜厚不均造成的蚀刻差异.基准:
70+/-5%.
a.准备基板、依现场条件做至前处理完毕后待用.
蚀刻过程
b.将测试板依次放入蚀刻段,并记录第1PNL从进入到出来的时间,算出实际的速度以便与设定速度作比较.
c.当第一PNL测试板出蚀刻段时立即关闭喷压,待走完水洗后,将板子取出并按放板的顺序依序排列在蚀刻段出板处.
d.依测试板的蚀刻程序,观察开始有蚀刻不净处,并量出长度,再除以蚀刻段的全长,计算出蚀刻点.
e.蚀刻点计算方式:
(未蚀刻干净的有效长度/蚀刻段的有效长度)×
100%.
f.蚀刻点未达标准时,检视蚀刻槽的喷嘴、喷压、速度与药液,若有异常则调整至标准值.
4.蚀刻因子(etchingfactor):
蚀刻过程中,蚀铜液除了做垂直向下的溶铜而且会攻击线路两侧无保护的铜面,称之为侧蚀(Undercut),因而造成如下的缺陷,etchingfactor即为蚀刻品质的一种指标.碱性蚀刻EF一般要求大于2.5
RESIST
底片宽度
CuII
CuI
基材铜
Overetching
Undercut
实际线宽
EF=2H/(B-A)
影响蚀刻因子之因素:
1、输入(PCB)
2、蚀刻设备
1.循环系统:
流量turn/4min
2.喷洒系统
a.喷嘴形式和排列方式;
b.摇摆频率;
c.喷洒压力均匀性。
3.自动添加系统。
4.抽风。
1.线路品质(前制程的品质影响);
2.电镀均匀性;
3.板面清洁度;
4.铜皮结构
六、影响侧蚀因素说明
比重
铜含量
蚀铜液
氯含量
影响undercut原因
铜皮结构与厚度
PH值
添加剂
温度
蚀刻速度
蚀刻机
喷管排列位置
喷嘴形式
喷压
1.温度
PH的测量注意点
PH值在常温时与50C的数值差异约0.4,计算公式如下:
PH(50)=PH(X)-0.21*50-X)/10
例如:
24C时测得PH为8.86,问50C的PH是多少?
8.86-0.21*(50-24)/10=8.314
2.PH误差影响因素
1)温度越低,PH越高,50C与常温时约差异0.4
2)电极会慢慢老化
3)不同厂牌或不同支电极,会差异约0.15
4)校正用的标准液会吸收CO2形成H2CO3而影响准确
性
Date07-03-2007
温度对比重的影响
50C时蚀铜液的比重比常温(25C)时约低0.01,比重每差异0.01其铜含量约差异10g/l.
50C
25C
铜含量g/l
1.190
1.200
135
1.210
145
1.220
155
1.215
1.225
160
1.230
165
七、子液与槽液维护
子液的维护及管理
槽液维护及管理
机台保养
每日保养
每周保养
每月保养
每半年保养
蚀刻子液及去锡液的维护及管理
蚀刻子液的结晶点约在15C,一般冬天温度低于15C时,容易结晶堵塞输送管路,而影响生产.故建议使用保
温措施.
蚀
TEMPSENSOR/不锈钢316
ES-480中央供料储存桶
40C热水
刻TANK
机
TEMP
输料管需保温
SENSOR/外包铁氟龙
锡
CH200中央供料储存桶
1.定期检查自动控制之比重和槽液比重是否符合而做适当校正(1次/周)
2.定期分析槽液PH值、铜含量、氯含量,并作成管制图.(1次/班)
3.每日下班时,使用子液冲洗蚀铜机前、后进出之滚轮,避免干燥氢氧化铜之累积
4.长期不使用时,可多添加3﹪~5﹪子液,避免NH3过量损失
1、每日保养
1)将机器外表的污点、污泥,化学结晶物一下列循序擦拭干净
a.以布沾20﹪的氨水擦拭b.以步沾水擦拭c.以干布擦拭或以高压气枪吹干
2)取下蚀铜帮浦的过滤网或过滤蕊,以水或高压器枪清洁
3)检查喷嘴是否堵塞,取下赌塞之喷嘴,将其侵入稀盐酸溶液中,取出后再以水洗,以高压气枪对准喷嘴入口喷气,去除堵塞,若仍不能去除,则以比喷口小的铁丝通喷嘴,注意不可伤喷嘴,装回时不得锁太紧否则牙会损
4)以毛刷沾20﹪的氨水除传动齿轮处的污泥,清除后切忌不得以
水冲洗否则会污染槽液
5)在传送链条处薄薄地抹上一层黄油
6)将温度设定到室温以下,查看冷却水是否循环,以确定循环电磁阀是否正常
2、每周保养
1)检查摆动马达减速箱和传动马达减速箱润滑油是否有漏,液面是否正常,否则补足。
注意液面不得补的太满,否则反而损坏减速箱
2)抽出槽液以氨水去除机器内部之任何污泥,以水冲洗后再抽入槽
液
*注意:
加热器及冷却管清洗务必彻底
3)检查机器所有『动态零件』是否松动或磨损现象,锁紧或更换
3、每月保养在摆动马达传动杆之轴承处涂上黄油
4.每半年保养
1)漏出传动马达减速箱摆动马达减速箱润滑油,更换减速箱润滑油
2)若传动马达系直流马达,则检查电刷是否磨损过度并更换,若调速盘细线圈式,则检查与线圈接触的电刷是否磨损过度并更换
3)于马达轴承处加润滑油
5.操作不连续或停机超过12hr以上操作注意事项:
5.1.停机前
将温度设定降至15~20℃,冷却系统继续运作,可减少自由氨挥发
关闭蚀铜段前后抽风
添加子液,可加速槽液降低温度速度及自由氨增加,但槽液含铜量须维持140g/l以上,氯离子含量须维持180g/l以上
5.2.开机后
建议将操作温度设定至46±
2℃,可减少自由氨挥发及测蚀
(如产量不大,可降温操作)
升温至操作温度时,分析槽液PH值,铜含量、氯离子调整槽液于操作范围内
操作刚开始,应以线路较宽或客户要求容易作的板子先作
1.在产量未达饱和时,因集中处理生产、减少蚀铜机待机时间.
2.如有可报废的裸铜板子,应以裸铜板子先行蚀铜,使药水活化,增加稳定性.
6.停机超过3日以上时,应清洗蚀刻机槽,维护步骤如下:
a.将槽液排出到预备桶
b.用水喷洗5分钟后排放c.将浮球取出放置,物使浮球悬空造成比重传感器失灵d.使用3﹪(v/v)HCL清洗并喷洗5分钟后排放e.检查喷嘴喷洒情况是否正常f.用水再清洗一次并检查加热器,冷却水管及滤网板是
否阻塞
g.加水与约2﹪氨水或子液混合后喷洗5分钟后排放
h.将槽液抽回
7.氯化氨添加时请先在槽外以槽液溶解后,在加入蚀铜机内,或用阳
极袋装氯化氨放入蚀铜机内慢慢溶解
8.(氯离子标准值-分析值)×
(NH4Cl/Cl)×
槽体积L/1000
=添加氯化氨重量
9.建议:
凡停机超过24hr应采下列措施
9.1加热器开关
9.2抽风开关
9.3不喷洒
9.4维持槽液循环及槽液温度20~30℃间预防冬天结晶,造成喷嘴阻塞及齿轮变形
9.5加子液将比重计调至下限1.2(25℃)
9.6比重计控制器关闭(注意浮球取出,并清洗以免拉坏传感器)
9.7比重计每周校正一次,并清洗浮球
八、问题与对策
可能原因
对策
1.速度降低a.温度低或加热器损坏b.比重过高,子液未补充
(铜含量高)c.比重过低(铜含量低)可能冷却水管漏水
d.压力太低e.氯离子过低f.氧气不够
增加温度添加子液至比重介于
1.200~1.220之间
添加废液修理冷却管调整压力添加NH4Cl增加打气
2.蚀刻不均
a.上下两面不均喷嘴阻塞
喷管管位或方向不对滚轮重迭喷管流量不正确
喷管破裂常发生摆动接头处液面太低,Pump空转
检查喷管(嘴)调整位置与角度调整滚轮调整每只喷管喷压整修或更换喷压补充蚀铜液
b.铜板面上局部不均匀显影去膜Scum未彻底底片不良导至干膜制程发生膜渣压模前板面清洁不够镀铜厚度不均去膜液碱性太强,回锡
电镀渗锡
检查修补底片
3.沈淀
a.氨/铜比重不对b.PH值低或漏水,带入水太多c.比重过高
调整氨铜比重减低抽风、修理水管或更换吸水滚轮添加子液
4.侧蚀大、蚀铜过度
a.PH高b.速度太慢c.压力过大d.氯离子过高
e.喷管或喷嘴角度不对f.比重太低g.阻剂破损或浮启
增加铜含量与抽风速度、厚度、药液关系降低压力
加水或铵水调整喷管或喷管角度增加铜浓度
5.蚀铜不足a.速度太快b.PH低c.比重太高d.温度太低e.喷压不足
调整速度添加子液添加子液加热器损坏
6.蚀铜机结晶太多
a.PH低于8以下
子液用完或管路堵塞控制器故障或不准确抽风太强
8.板子在蚀铜机内行径不直不正a.装机未在水平状态b.喷管喷压集中单边c.输送齿轮破损使输送杆停用d.输送杆变形e.上下喷压不均匀下压太大时
,轻板子会被举起
检查机台水平
调整上、下喷压
9.蚀刻液槽起泡a.子液、母液本身起泡b.油墨未充份烘干,在蚀刻槽内有溶出,溶出物引起泡沫
c.因过滤处阻塞,使pump抽取不足管路引入空气起泡d.pump或管路有细缝引入空气e.槽本身已累积过多杂质或污染附在槽壁,逐渐溶解
f.蚀刻液起泡原因:
过滤心前处理未完全,其树脂溶出造成起泡,滤心先以热(50℃)浸泡约20min后,才装在过滤机内使用
以新鲜子液、母液充分摇动是否起泡查Ink烘箱是否有堵塞,或温度变化循环不良