焊锡炉管理作业规范Word格式文档下载.docx
《焊锡炉管理作业规范Word格式文档下载.docx》由会员分享,可在线阅读,更多相关《焊锡炉管理作业规范Word格式文档下载.docx(30页珍藏版)》请在冰豆网上搜索。
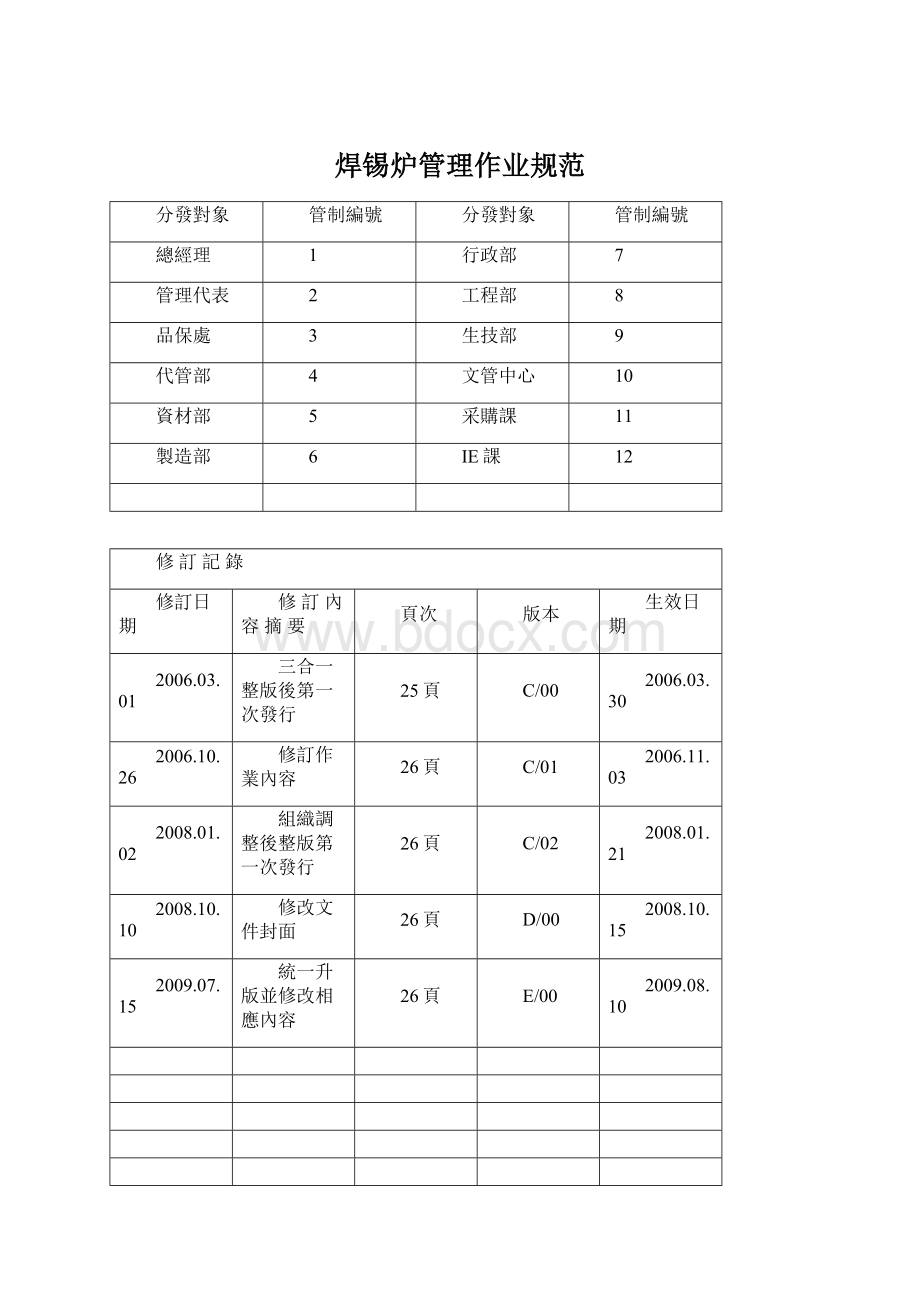
修訂作業內容
26頁
C/01
2006.11.03
2008.01.02
組織調整後整版第一次發行
C/02
2008.01.21
2008.10.10
修改文件封面
D/00
2008.10.15
2009.07.15
統一升版並修改相應內容
E/00
2009.08.10
制/修
定者
審
核
生
技
部
工
程
行
政
製
造
處
資
材
代
管
品
保
采購課
理
表
總
經
1.目的:
建立焊錫爐作業程序及達到規範作業之目的.
2.適用範圍:
適用於所有焊錫爐生產機種之參數管理.
3.名詞定義:
無.
4.職責:
錫爐操作人員:
每日做機台點檢記錄、各參數之設定、調整與量測.
5.作業內容:
5.1開機操作程序(適合公司所有波峰焊機):
5.1.1設定好錫爐時間制,在上班前6H使錫爐自動打開:
(1)錫溫加熱器,使錫溫達至工作溫度.
5.1.2檢查Flux是否足夠,不足應加滿;
檢查爪片清洗液是否足夠,不足應加滿;
檢查氣壓是否正常.總氣壓表是否達到;
檢查預熱區域是否有雜物,有則清除;
檢查運輸鏈條爪片是否正常;
檢查錫波馬達是否正常;
打開抽風機檢查工作正常否.
5.1.3打開各開關:
(1)照明(LIGHT);
(2)鏈條(Speed);
(3)助焊劑自動噴霧(nozzlesprayfluxer);
(4)預熱器(PREHEATER):
Zone1Calod、Zone2Caold、Zone3Calod;
(5)第二錫波馬達(SOLDERWAVE);
(6)第一錫波馬達(CHIPWAVE);
(7)運輸鏈爪片清洗馬達;
(8)冷卻風扇.
5.1.4生產開機前及更換機種前,依據錫爐制程規格品質保證表進行量測並記錄各項參數.在制程規格範圍內,方可正常生產.如出現異常事故,立即按急停開關.
5.2關機操作程序:
5.2.1關機前應全面檢查一遍機器內是否有PCB'
A在機器內,各部件運行是否正常;
如有異常情況,關機后應馬上處理.關機時,應先關掉錫波.然後再依開機順序逆向順序關掉其餘按鈕.關掉電源總制(如果用時間制控制自動開關機.則不應關總制).
5.3保養程序:
5.3.1錫爐每日保養依錫爐<
<
日保養檢查記錄表執行>
>
.
5.3.2每周、每月、半年保養依<
錫爐保養計划表>
5.4錫爐所使用之輔材規格,注明機台所使用之輔材詳細規格.
5.5各項參數需明確注明以下選項:
5.5.1客戶代碼(OwnerCode).
5.5.2基板版本(PCBRev).
5.5.3基板板號(PCBnumber).
5.5.4所用程式命稱(programname).
程式命名方式:
新程式名為(機種全名(注:
如超出8個字符可用簡要名稱)+後綴A/00)後續升版之程式管控以A/01A/02以此類推,並記錄程式變更記錄表.
5.5.5助焊劑噴霧氣壓;
(依產品需要進行設定)
助焊劑噴霧延時距離;
助焊劑噴霧停止距離;
霧化距離(Pitch);
噴嘴起動位置(StartPosition);
噴嘴返回位置(StopPosition);
噴嘴移動速度(Speed);
噴霧量(Pumpfrequency);
(依產品需要進行設定)
5.5.6預熱器使用類型:
5.5.6.1有指定PTH貫穿孔需上錫到75%時需使用板面加熱器.
5.5.6.2預熱器溫度:
Zone1Calod設定;
Zone2Calod設定;
Zone3Calod設定;
板面預熱一段設定;
5.5.7鏈條速度;
鏈條角度;
手指爪片類型(本公司所有錫爐使用直鉤型爪片).
5.5.8焊錫溫度設定;
5.5.9焊錫波峰類型:
5.5.9.1有SMT零件必須使用雙錫波(第一錫波+第二錫波),沒有SMT零件可使用單錫波(第二錫波).
5.5.9.2當PCB與PCB的過爐之間間距小於10CM時不需要使用追蹤斷續性波峰,反之則設定為追蹤斷續性波峰.
5.5.9.3chipwave為第一錫波峰(擾流波)其噴嘴到板底高度:
(依產品需要進行設定)mainwave為第二錫波峰(主流波)其噴嘴到板底高度;
5.5.9.4第一錫波峰馬達轉速;
(依產品需要進行設定)
5.5.9.5第一錫波峰馬達轉速;
(依產品需要進行設定)
5.5.9.6調整波峰高度後需重新測量波峰接觸面積.
5.5.10以上所有量測頻率依<
錫爐制程規格品質保証表>
進行量測.
5.5.11排風管風速率(Exhaustrange):
噴霧系統排風口風速
700±
100CFM;
錫槽排風口風速700±
100CFM.
5.6操作注意事項:
5.6.1安全:
工作時必須戴防毒口罩、護目鏡、靜電手套或靜電手環.
5.6.2品質:
(1)不能有假焊與短路
(2)不能有錫珠,錫渣(3)錫點要飽滿,光滑.
5.6.3技術員每小時抽樣6pcs(抽樣標准為5%).
5.6.4嚴禁有撞板和卡板現象,PCB進入鏈條軌道時需平穩.
5.6.5PCB'
A在進入錫爐時PCB'
A保持的間隔距離不能少於5cm的距離.
5.6.6PCBA出爐口溫度需低於125℃.
5.6.7在調整過爐品質時(如調整波峰高度等)需保証爐內無PCB,方可進行調試.
5.6.8爪片清洗劑統一用超盟CM-801清洗劑.
5.6.9無鉛系列要有無鉛圖示(如圖).
5.7助焊劑噴霧系統測量:
本公司所有錫爐使用來回式噴霧系統.
5.7.1助焊劑比重量測作業:
5.7.1.1從flux槽里取出250毫升flux放進清潔乾燥的量筒內.
5.7.1.2把比重計放進量筒,待比重計靜止後,眼睛必須平視凹液面刻度觀看flux比重值是否在管制範圍內(比重管制範圍依SOP規定),並記錄於錫爐制程參數記錄表.
5.7.1.3當flux比重值超出管制上限時適量釋放槽里的flux於空桶里,再往槽內添加稀釋劑直到比重定於規格範圍內;
當比重值超出管制下限時適量釋放槽里的flux,再往槽里添加全新的助焊劑直到比重定於規格範圍內(此項用於flux發泡式).
5.7.1.4當flux比重值超出管制上下限時需更換槽內所有flux,加入全新flux.(此項用於flux噴霧式).
5.7.2Flux酸值滴定測試作業:
5.7.2.1從Flux槽提取30毫升Flux液體倒進清潔,乾燥的燒杯內.
5.7.2.2將3滴Phenolphtalein滴于FLUX中,並搖勻.
5.7.2.3在玻璃滴管中加入KOH溶液直到"
0"
刻度.
5.7.2.4讓KOH溶液滴進Flux與Phenolphtalein混合液中,同時輕輕搖動燒杯,混合液體呈現粉紅色即停止滴定.
5.7.2.5平視滴管刻度,然後算出Flux酸值(參見附表)並記錄於錫爐制程參數記錄表.
5.7.2.6當flux酸值超出管制上限時適量釋放槽里的flux於空桶里,再往槽內添加稀釋劑直到比重定於規格範圍內;
當酸值超出管制下限時適量釋放槽里的flux,再往槽里添加全新的助焊劑直到酸值定於規格範圍內(此項用於flux發泡式).
5.7.2.7當flux酸值超出管制上下限時需更換槽內所有flux,加入全新flux.(此項用於flux噴霧式).
5.7.3霧化均勻度量測作業.
5.7.3.1將鋁板(霧化均勻度量測作業專用鋁板)清潔干淨.
5.7.3.2在鋁板一面貼滿一層傳真紙,傳真紙面向上.
5.7.3.3將其放入錫爐進口進入錫爐噴霧,噴霧完成後經過預熱在過完預熱一段後將其拿出.(雙手托板邊,手指不要觸及板面和板底).
5.7.3.4確認噴霧均勻度是否合格(板底傳真紙前後邊緣露出之半圓部分不可有噴到FLUX以及中間部份變色均勻,板面传真纸目視無回落点為合格狀態),並記錄於錫爐制程參數記錄表.
噴霧均勻 OK 未噴到FLUX NG OK OK
已噴到FLUXNGOK
5.7.3.5每次所測合格之傳真紙需在其右下腳處註明所測日期,技術員簽名,所生產之機種名.
5.7.3.6如有不合格狀態需調試flux噴霧霧化均勻度,直到合格.
5.7.4Flux厚度測量作業.
5.7.4.1將一塊干淨的鋁板(Flux厚度測量作業專用鋁板規格為:
250mm*250mm*1.5mm)放在電子秤上稱出其淨重量.
5.7.4.2然後將鋁板放入錫爐過噴霧噴上助焊劑以及預熱.
5.7.4.3在過完噴霧&預熱,將鋁板在波峰口上面取出.
5.7.4.4取出後立即將附有助焊劑的鋁板放在電子秤上秤出其重量.
5.7.4.5將秤得之數據套入以下公式計算出Flux所噴在PCB上的厚度(如下图):
鋁測試板:
W*L*H=25*25*0.15(cm)
G=W*L*T*r
T=G/(W*L*r)
r=1.23g/cm3(Dry)
重量=密度*體積(長*寬*厚度)
G=重量 T=松香厚度 r=松香密度
W=鋁板寬度 L=鋁板長度 H=鋁板厚度
5.7.4.6如有不合格狀態需調試flux噴霧噴霧量大小,直到合格(2.0±
0.3um)方可,並記錄於錫爐制程參數記錄表.
5.7.5助焊劑噴霧量檢查:
5.7.5.1當噴頭有助焊劑噴出時,檢查噴霧機流量計所顯示之數據,並記錄於錫爐制程參數記錄表.
5.7.6助焊劑延遲、持續時間測量作業:
5.7.6.1相應字母表示因子:
A1=感應器到噴頭之間距離單位:
mm
A2=PCB前端非有效焊接面積約二分之一單位:
mm
A3=PCB後端非有效焊接面積約二分之一單位:
A4=速度單位:
mm/secA5=距離(PCB長度)單位:
當PCB進入錫爐後,從感應器到噴頭之間的時間段為噴霧
延遲時間,計算公式如下:
(A1+A2)/速度=延遲時間單位:
sec
從開始噴霧到噴霧完成為噴霧持續時間,計算公式如下:
[A5-(A2+A3)]/速度=持續時間單位:
sec.
5.7.6.2如有不合格狀態需調試flux噴霧Ontime&
Offtime(具體設定可依據當線所使用之SOP),直到合格方可,並記錄於錫爐制程參數記錄表.
5.7.7噴霧機噴嘴距離PCB板底高度測量作業:
5.7.7.1噴霧機噴嘴距離PCB板底高度用數顯深度尺進行測量,將深度尺開關打開.
5.7.7.2將PCB放入錫爐,讓其輸送至噴霧機噴嘴正上方,停下鏈條速度進行測量噴霧機噴嘴距離PCB板底高度,記錄其數據.
5.7.7.3將所測噴霧機噴嘴距離PCB板底高度減去PCB厚度等於噴霧機噴嘴距離PCB板底高度實際高度,並記錄於錫爐保養、檢查記錄表.
5.7.8助焊劑發泡高度量測作業.
5.7.8.1雙手扶住支架把手按正確方向()讓其進入錫爐.
5.7.8.2發泡高度應當接觸第2格(1.6mm)或第3格玻璃板(0.8mm),而不接觸第一格玻璃板(2.4mm),由此可測出發泡高度為0.8mm<
H<
2.4mm,如發泡高度未接觸第3格玻璃板(0.8mm),則發泡偏低需進行適當調整;
又如發泡高度接觸第1格(2.4mm),則發泡偏高需進行適當調整;
直到發泡高度定於正常規格0.8mm<
2.4mm范圍內方可正常生產,並記錄於錫爐制程參數記錄表.
5.7.9FLUX發泡接觸面積量測作業:
5.7.9.1雙手扶住高溫玻璃並按正確方向(--->
)讓其進入錫爐.
5.7.9.2在輸送到FLUX發泡面時讀取高溫玻璃與FLUX發泡面的接觸面積((標准為30mm-50mm)高溫玻璃每格為10mm),並記錄於錫爐制程參數記錄表.
5.7.10FLUX噴霧氣壓檢查作業:
5.7.10.1檢查第一個氣壓表,此為助焊劑噴霧氣壓.
5.7.10.2檢查第二個氣壓表,此為助焊劑出水壓力.
5.7.10.3檢查第三個氣壓表,此為助焊劑噴嘴氣壓.
5.7.10.4以上項目如有不合格狀態需調試到合格方可,並記錄於錫爐制程參數記錄表.
5.7.11FLUX發泡氣壓檢查作業:
5.7.11.1檢查錫爐正面氣壓表,此為助焊劑發泡氣壓.
5.7.11.2如有不合格狀態需調試合格方可,並記錄於錫爐制程參數記錄表.
5.8預熱溫度測量作業:
5.8.1測溫模板制作:
5.8.1.1測溫線及測量點選擇:
5.8.1.1.1首先依據使用之錫條、助焊劑.PCB耐熱性.元件熱敏度項目之間都需滿足的條件最大輿最小值定義標准曲線.(圖1)
圖一
上限 下限
5.8.1.1.2據PCB板上零件耐熱溫度:
客戶指定元件=>
BGA=>
QFP=>
Connector=>
Cap=>
Chip元件次序,以及PCB過爐時,由於受熱方式的緣故,其本身的溫度又比IC的溫度高的特點,選取PCB邊緣的IC、PCB中央的IC以及線檢反應最多問題的零件選擇5個測量點.(原則上5個點之點間距在3CM以上,其中一量測點需為PCB板面,測量PCB板面溫度,當PCB板尺寸≦100MM時可選擇4個測量點).(依客戶要求除外)
5.8.1.1.3PCB板為Top,Bottom兩面制程時,在制作測溫板時,需在Top面選擇一熱敏度最差及體積校大而吃錫面小的元件作為測量點,以防止溫度過高造成Top面元件脫落.
5.8.1.1.4擇OK的測溫點記錄於標准工程PROFILER中.
5.8.1.1.5擇其外層為玻璃纖維包覆、內層是鋁、鉻合金有兩根內芯,其耐熱最高溫度為330℃的測溫線.
5.8.1.2測溫線之安裝:
5.8.1.2.1測溫線一端連接在測試插頭上,另一端焊接於選擇OK的測量點PCB板上.
5.8.1.2.2測溫線在連接測試插頭上時需分清正負,紅芯接負,黃芯接正,不可錯接.
5.8.1.2.3安裝在測量點上時測溫線不可斷裂.(如圖一)
5.8.1.2.4測溫線不可有絞線情形(如圖二);
必須兩端焊接成0點為OK(如圖三);
5.8.1.2.5安裝OK後的測溫線焊接於IC腳時,不可翹高(圖一)
5.8.1.2.6測溫線設置高於IC腳1/2處為佳.(如圖二)
5.8.1.2.7測溫線頭焊在ICPin上時,若ICPin腳間距≧0.5時,測量線頭要求焊在兩個Pin腳上,若ICPin腳間距<0.5時,測量線頭要求焊在三個Pin上.
FinePitch最多只能焊3隻腳.(如圖三)
5.8.1.2.8如板底無任何零件時,測溫線直接焊於DIP零件銅箔處.
5.8.1.2.9測溫線使用高溫錫絲(規格:
熔點為285℃以上,錫銀合金)將測溫線頭焊接(固定)於量測板上(如圖).
5.8.1.2.10再用導熱高溫膠將焊接OK測溫線在板上固定防止松散.
5.8.1.2.11模板及測溫線使用記錄卡進行管制,同一模板和測溫線使用同一記錄卡進行管制,在記錄卡上標明機種名稱及編號.模板及測溫線使用一次在記錄卡上就以"
V"
標識.(模板使用期限為40次,測溫線使用期限為120次).
5.8.2錫爐溫度設定及量測(工程標准曲線圖制作)依據材料,設備,热传导、焊接等方面以及標准曲線設定爐溫參數.
5.8.2.1預熱區設置:
预热区通常指由室温升至125℃左右的区域。
在这个区域,PCB平稳升温,助焊劑中的部分溶剂能够及时挥发,活化剂开始激活,并有效地去除焊接表面的氧化物,在焊接時減小被焊表面張力.元器件特别是IC器件缓缓升温,以适应以后的高温;
但PCB表面由于元器件大小用銅鉑面積不一,其温度有不均匀现象,在预热区升温的速率通常控制在1℃-3℃/sec.若升温太快,由于热应力的作用,导致PCB变形、IC芯片损坏,電容破損等;
一般板面與板底預熱溫度溫差在過波峰前須控制在35℃以下;
其升溫斜率计算方式如下:
设环境温度为25℃,板底最高溫度為125℃,在25℃到125℃所經歷的時間為50sec计算则(125-25)/50即为2℃/sec;
根据元件大小差异程度调整时间以调控升温速率在2℃/sec以下为最佳.
5.8.2.2錫爐溫度和焊接時間設置:
有鉛焊錫溫度一般設定於250±
3℃,焊接時間3-5S;
無鉛焊錫溫度一般設定於252~263℃之間,焊接時間3~6S。
若时间过长会导致助焊劑活性失效,以致焊接后短路等不良增多,板面溫度升高,板面SMT元件二次熔錫,造成不良,一般過完波峰後,板面頂點溫度要低於160度為宜;
時間過短,易造成通孔單面吃錫等不良.
5.8.2.3降溫斜率控制:
PCB從波峰離開時的頂點溫度下降到160℃之間的降溫斜率須控制在4-10℃/sec.
5.8.3Profiler量測方法與量測時機:
5.8.3.1按住Mode開關(大約2秒鐘)Status指示燈連續閃爍,此時將Profiler儀器放入波峰爐.
5.8.3.2Profiler儀器過完波峰爐后,再按一下Mode開關(約2秒鐘),將Profiler之信號線與電腦連接,利用電腦對Profiler進行資料分析
5.8.3.3程序:
5.8.3.3.1進入電腦ProfilerV4.5文檔.
5.8.3.3.2下載資料於Profiler界面里,點擊記錄設定於“開始模式”中選擇“手控開始”;
“CommunicationMade”中選擇“RF”.
5.8.3.3.3點擊“下載資料”.
5.8.3.3.4再點擊“溫度曲線”選擇“Statistics”,讀取數據.
5.8.3.4確認數據符合規格后,點擊生產設定,編輯生產資料:
點擊“生產設定”a.OperaterName.b.生產名稱.c.批量數碼.d.爐子名稱.e.爐子編號.
5.8.3.5對測試資料進行存檔處理,模式:
DN×
×
×
日班夜班日期月份年份線別
5.8.3.6《曲線分析》《溫度上升斜率分析》《預熱區時間及溫度分析》《焊接時間及錫爐溫度分析》.
5.8.3.7若測出之溫度曲線都符合標準後,將溫度曲線標準圖存檔列印,並手寫上預熱器設定溫度,機種,鏈速,錫溫;
由工程師確認後掛在機台上,方可生產;
將所測值記錄於《錫爐制程參數記錄表》中.
5.8.3.8分析測出之曲線溫度不符合標準,如有差異則及時反饋工程師進行分析處理並記錄於《錫爐異常停機PCB處理記錄表》.
5.8.3.9溫度曲線度需每4小時測量一次,換線生產前及品質異常時也需進行量測.每天所測之曲線圖需與工程標准曲線圖進行比照,確認是否在規格范圍內.
5.8.3.10每個機種需有一個標准的工程溫度曲線圖.
5.8.3.11工程標准曲線圖是依據使用之錫條、助焊劑.PCB耐熱性.元件熱敏度項目之間都需滿足的條件最大輿最小值定義標准曲線.
5.8.3.12當所測之溫度曲線與標准溫度曲線之間的溫差超出判定標准時需立即停線進行原因分析,找出問題點所在,並盡快修復.修復后需從新進行測量,測量ok後方可過爐.
5.8.3.13以上爐溫曲線如客戶有明確文件定義,則依客戶文件執行。
5.8.4錫爐溫度精度量測:
5.8.4.1准備一塊合成石板250*250mm,將四條熱電偶用導熱高溫膠固定在合成石板底四周另用一條熱偶固定於板面中央位置上,如圖
5.8.4.2設定錫爐常用最高參數,預熱溫度每個區為350℃,鏈速設定為1.2M/min,無鉛錫溫度為260℃待溫度穩定後進行量測,下載分析生成標准校驗曲線圖
5.8.4.3每月用以上參數進行比對分析,熱偶5點錫波最高溫度差不能大於2℃,預熱溫度最高溫度差不能大於3℃.若不能達到此標准,則需分析原因,對設備和測溫板進行檢查後,再測若仍然不達標則需聯繫供應商處理並記錄《錫爐異常停機PCB處理記錄表》.
5.8.4.3開新機時首次量測需量測6次或6次以上,後續平均每月量測一次,每次測量時需待合成石板達到室溫狀態才可開始測試。
5.9爪片&
鏈條測試:
5.9.1鏈條輸送速度精度測試作業:
5.9.1.1在錫爐溫度精度測試儀進入錫爐鏈條完成(測試儀末端)時打開Profiler測試儀.
5.9.1.2在錫爐溫度精度測試儀到達錫爐鏈條出口且完整(測試儀末端)出爐時時關閉Profiler測試儀.
5.9.1.3對所測Profiler進行下載分析總測溫時間,根據此時間算出鏈條輸送速度,公式如:
軌道長度/時間=鏈條輸送速度.並記錄於錫爐精度校准表.
5.9.1.4此每月測量一次,其誤差值不可大於0.01M/Min.
5.9.2軌道角度測量作業:
5.9.2.1此項測試用數顯水平儀進行測量,將水平儀打開.
5.9.2.2選取軌道量測位置並將其清潔干淨,將水平儀放置在上面讀取所顯示之數據.
5.9.2.3所顯示之數據為錫爐軌道傾斜角度.
5.9.3檢查錫爐爪片是否整齊,且無變形保証所有的都是OK.
5.9.4錫爐本身爪片數量是以機臺出廠默認值來確定,由於機臺本身差別故
每臺機本身爪片數量有所不同.在有特定情況下使用過錫載具過爐.
5.10錫爐中心鋼線調校作業:
5.10.1錫爐中心鋼線調校:
5.10.1.1在過板前檢查PCB板有無設計之中心線位置,如有需用上中心鋼線,如PCB板無設計中心線位置則不用中心鋼線.
5.10.1.2如有設計中心鋼線位置,需在過板前用空板進入錫爐入口,調整中心鋼線使之與PCB板所設計之中心線位置相符合.
5.10.1.3如果錫爐中心鋼線偏離PCB板中心線位置,則調整錫爐中心鋼線支架.
5.11錫槽相關測試:
5.11.1錫爐焊接時間測試作業:
5.11.1.1測試前檢查確定焊接時間感應探針長度到板底1mm.
5.11.1.2將電源開關打“ON”狀態,再按一次"
RESET"
鍵.使The1stwaveDwelltime與The2ndwave Dwelltime顯示為"
0"
5.11.1.3按正確方向(--->
)放進錫爐入口,讓焊接時間測試儀標準測試.
5.11.1.4將The1stwaveDwelltime所顯示的數據填寫在報表上,以及將The2ndwaveDwell time