电池极片涂布技术研究Word文档下载推荐.docx
《电池极片涂布技术研究Word文档下载推荐.docx》由会员分享,可在线阅读,更多相关《电池极片涂布技术研究Word文档下载推荐.docx(6页珍藏版)》请在冰豆网上搜索。
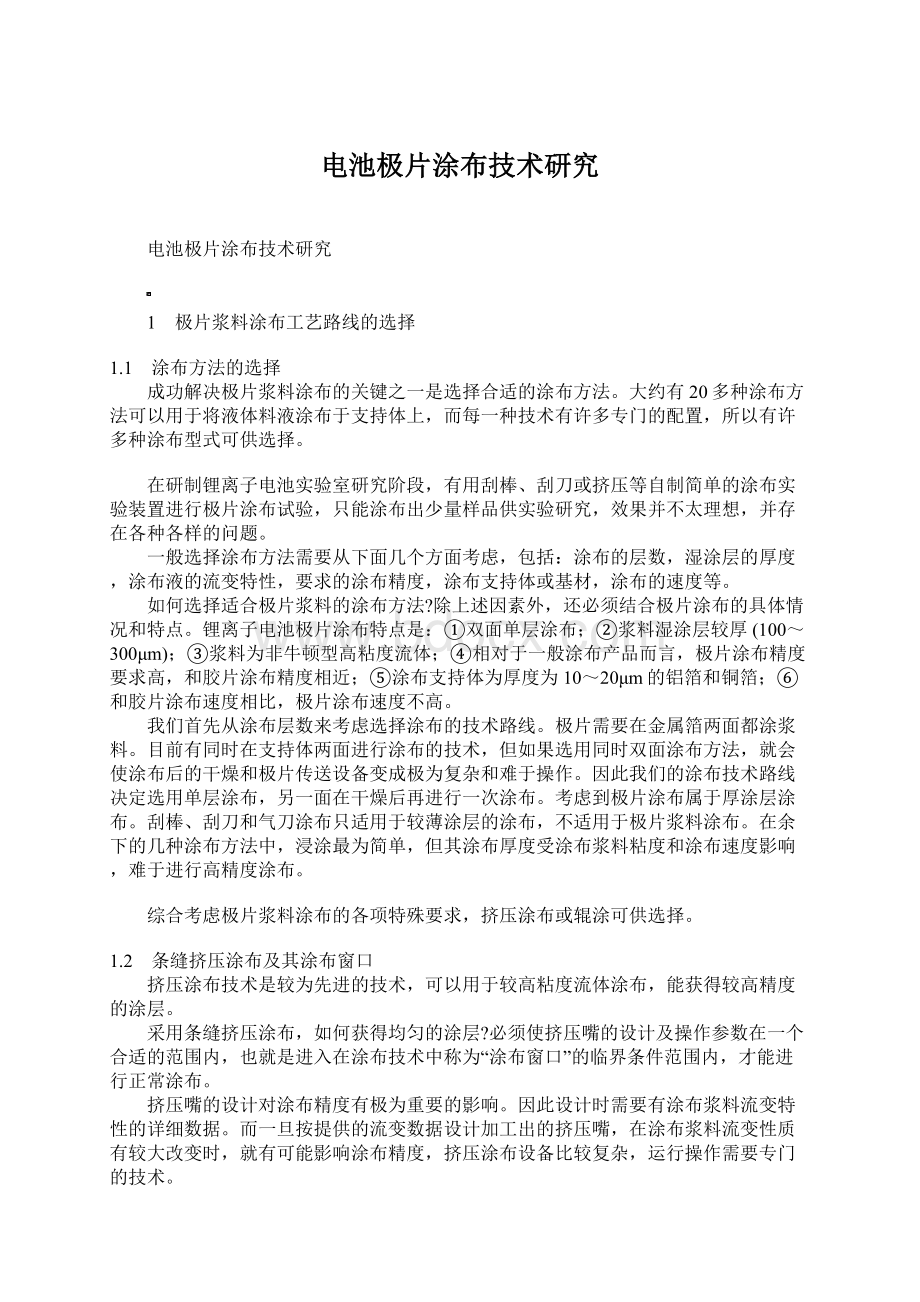
极片需要在金属箔两面都涂浆料。
目前有同时在支持体两面进行涂布的技术,但如果选用同时双面涂布方法,就会使涂布后的干燥和极片传送设备变成极为复杂和难于操作。
因此我们的涂布技术路线决定选用单层涂布,另一面在干燥后再进行一次涂布。
考虑到极片涂布属于厚涂层涂布。
刮棒、刮刀和气刀涂布只适用于较薄涂层的涂布,不适用于极片浆料涂布。
在余下的几种涂布方法中,浸涂最为简单,但其涂布厚度受涂布浆料粘度和涂布速度影响,难于进行高精度涂布。
综合考虑极片浆料涂布的各项特殊要求,挤压涂布或辊涂可供选择。
1.2 条缝挤压涂布及其涂布窗口
挤压涂布技术是较为先进的技术,可以用于较高粘度流体涂布,能获得较高精度的涂层。
采用条缝挤压涂布,如何获得均匀的涂层?
必须使挤压嘴的设计及操作参数在一个合适的范围内,也就是进入在涂布技术中称为“涂布窗口”的临界条件范围内,才能进行正常涂布。
挤压嘴的设计对涂布精度有极为重要的影响。
因此设计时需要有涂布浆料流变特性的详细数据。
而一旦按提供的流变数据设计加工出的挤压嘴,在涂布浆料流变性质有较大改变时,就有可能影响涂布精度,挤压涂布设备比较复杂,运行操作需要专门的技术。
1.3 辊涂工艺的涂布窗口
辊涂是比较成熟的涂布工艺,如果有高精度涂布辊和精密轴承,有可能得到均匀度较好的涂层。
辊涂可以应用于极片浆料的涂布。
辊涂有多种型式,按辊的转动方向区分就有顺转辊和逆转辊涂布两种。
此外还有配置3辊、4辊等多达10多种辊涂型式。
究竟用哪一种辊涂型式比较好呢?
这要根据各种浆料的流变性质进行选择。
也就是所设计的辊涂型式,结构尺寸,操作条件,涂液的物理性质等各种条件必须在一个合理的范围内,也就是操作条件进入涂布窗口,才能涂布出无弊病的涂层。
2 极片涂布中的关键技术
在所有涂布产品中胶片所要求的涂布精度是最高的一种,因此胶片涂布中的许多技术是解决极片涂布的基础。
但极片涂布所特有的要求必须有特殊的技术才能解决。
2.1 高粘度极片浆料的涂布
极片浆料粘度极高,超出一般涂布液的粘度,而且所要求的涂量大,用现有常规涂布方法无法进行均匀涂布。
我们比较分析了各种涂布方法,依据其流动机理,结合极片浆料的流变特性和涂布要求,设计了各种实验方案进行验证,找到了几种可用于极片浆料的涂布方法,成功地解决了高粘度极片浆料连续稳定、均匀涂布难题。
2.2 极片定长分段和双面叠合涂布技术
无论是胶片涂布,还是其他涂布产品,绝大多数都是在片幅上进行连续涂布。
而锂离子电池极片是分段涂布,生产不同型号锂离子电池,所需要的每段极片长度也是不同的。
如果采用连续涂布,再进行定长分切生产极片,在组装电池时需要在每段极片一端刮除浆料涂层,露出金属箔片。
用连续涂布定长分切的工艺路线,效率低,不能满足最终进行规模生产的需要。
因此我们考虑采用定长分段涂布方法,在涂布时按电池规格需要的涂布及空白长度进行分段涂布。
采用单纯的机械装置很难实现不同电池规格所需要长度分段涂布。
我们在涂布头的设计中采用计算机技术,将极片涂布头设计成光、机、电一体化智能化控制的涂布装置。
涂布前将操作参数用键盘输入计算机,在涂布过程中由计算机控制,自动进行定长分段和双面叠合涂布。
因此涂布机可以任意设定涂布和空白长度进行分段涂布,能满足各种型号锂离子电池极片涂布的需要。
2.3 极片浆料厚涂层高效干燥技术
极片浆料涂层比较厚,涂布量大,干燥负荷大。
采用普通热风对流干燥法或烘缸热传导干燥法等干燥效率低。
我们将胶片干燥中的高效干燥技术应用于极片干燥器设计,采用优化设计的热风冲击干燥技术,提高了干燥效率,可以进行均匀快速干燥,干燥后的涂层无外干内湿或表面皲裂等弊病。
2.4 极片涂布生产流水线基片(极片)传输技术
在极片涂布生产流水线中从放卷到收卷,中间包含有涂布、干燥等许多环节,极片(基片)有多个传动点拖动。
这和胶片涂布干燥生产流水线是相似的。
我们成功地将胶片涂布机传输技术应用于极片涂布,又针对基片是极薄的铝箔铜箔,刚性差,易于撕裂和产生折皱等特点,在设计中采取特殊技术装置,在涂布区使极片保持平展,严格控制片路张力梯度,使整个片路张力都处于安全极限内。
在涂布流水线的传动设计中,我们采用了直流电机智能调速控制技术,使涂布点片路速度保持稳定,从而确保了涂布的纵向均匀度。
在涂布机传输片路设计中,在涂布、收卷等关键部位,都设计有自动纠偏装置,在涂布时使浆料准确地涂布于基片上,两边留有均匀的片边,在极片收卷时能得到边缘整齐的片卷,为极片生产的下一道工序创造了有利条件。
3 极片涂布工艺流程
极片涂布的一般工艺流程如下:
放卷→接片→拉片→张力控制→自动纠偏→涂布→干燥→自动纠偏→张力控制→自动纠偏→收卷
涂布基片(金属箔)由放卷装置放出供入涂布机。
基片的首尾在接片台连接成连续带后由拉片装置送入张力调整装置和自动纠偏装置,经过调整片路张力和片路位置后进入涂布装置。
极片浆料在涂布装置按预定涂布量和空白长度分段进行涂布。
在双面涂布时,自动跟踪正面涂布和空白长度进行涂布。
涂布后的湿极片送入干燥道进行干燥,干燥温度根据涂布速度和涂布厚度设定。
干燥后的极片经张力调整和自动纠偏后进行收卷,供下一步工序进行加工。
4 设备安装调试及涂布情况
研制的设备由机械设备,电气控制,干燥通风等系统组成,安装后先后进行了机械试车,机电联试和联动试车,均达到设计和使用要求。
按锂离子电池的技术要求和设计技术指标投料涂布。
涂布条件:
涂布基片厚度为20μm的铝箔,涂布基片宽度为350mm,涂布速度5m/min。
在上述条件下用浆料进行单面定长涂布,双面叠合涂布,同时进行干燥。
整条生产线运行平稳,涂布干燥均匀。
5 样品测试结果
5.1 涂布均匀度
涂布量相对偏差范围为2.22%~-1.85%,绝对误差为4.07%。
信息来自:
输配电设备网
表1 研制涂布机涂布样品涂量测试数据
表2 引进涂布机涂布样品涂布量测试数据
涂布量相对偏差范围2.67%~-1.53%,绝对误差4.2%。
在双面涂布的极片上随机抽取一段极片,在其纵向以均匀距离用圆形取样器取样在精密天平上称重,称得的质量m包括两面浆料涂层和基片的质量,浆料量除以试样面积S得单位面积的极片涂量g/cm2。
实测数据见表1、表2。
5.2 定长和叠合精度
在不同批次的涂布极片中随机抽取若干段测试样品,测量每段的涂布长度和空白间隔长度和双面叠合位置。
结果见表3、表4。
表3 研制设备涂布A批次的定长和叠合数据 mm
表4 研制设备涂布B批次定长和叠合数据 mm
6 结论
实际测试数据表明,我们研制成功的涂布机主要技术性指标达到了引进设备水平。
研制成功的锂离子电池极片涂布机的技术性能完全能满足制作锂离子电池要求,对促进我国锂离子电池研制和产业化具有重要意义。
1、浆料分布不均匀,3、留取的单面未有存放措施;
4、负极常有未烘干,5、两边卷起的现象;
6、正极材料(LiCOO2)常有白色印记及黑色水印;
7、正极材料(LiMn2O4)颗料较多,
8、且有掉粉、分层的现象及表面颜色较差;
9、正极浆料与前段时间的稠稀度不同;
10
11、政权极浆料放置时间过长未搅拌,
12、易结块;
13、配料材料更改频繁,
14、涂布厚度有差异;
15、种浆料、16、
种型号所涂布的厚度不同17、;
18、正极浆料颗料较多,19、卡在刀口极片严重缺料且有痕;
10、现Al箔W254mm、100×
100mm重0·
50g,前Al箔W266mm、100×
55g;
11、现正极涂布两边重中间轻,相差0·
2g;
12、正极涂布单现留边双面未留边,且留边宽度不同,导致极片缺料且有较多的白痕(即涂料不均匀);
13、极片两边烘烤的干湿度不同;
14、正负极的单面双面未有温度控制;
15、极片两边的干湿度不同;
16、涂布前段部分未调好,导致极片两面附料不均匀;
17、Cu、Al箔L、W、H应由RD定标准后采购;
18、手动裁切定位不齐,有斜角且有掉粉;
19、自动裁切改为手动裁切,未有新的作业指导书;
20、工作指引中极片左中右厚度≤10μm现工艺单面≤2μm,双面≤3μm;
21、负极附料的更改,品质部未知,常有判断错误;
22、负极涂布双面温度无法升起(设125℃最多升至118℃);
23、开窗后外面的温湿度对极片有影响吗?
24、正、负单面涂布都是右边卷起,且正极收卷不齐易打皱;
25、涂布机的温度与走速是成正比的,如何控制?
未有标准;
26、单面调机人员未带手套,留在Cu、Al上的手印(即汗渍),导致双面涂布后有明显的黑印迹;
27、Al较窄不能留边,导致附在单面两干料,双面极易拉断且拉断次数较多,产生报废;
28、涂布未有自检记录及习惯;
29、刚停机,极片存放在烘箱中易掉粉;
30、涂布完的极片未有明确规定如何存放;
31、涂布后放Cu、Al箔位,未经其他部门认可已更换,且Cu、Al箔多次撞伤及两边松紧度不同;
32、涂布机内辊轮未经常擦洗,易有干料附在极片上;
33、加料未经常搅拌浆料稀稠不同,极片附料不均匀;
34、同一大片分切后6小片,极片左中右厚度不稳定且重量在上中下限都有;
35、加料最后的浆料(有干料、较稠、结块)对所涂极片都有影响;
36、停机卡在刀口处的印记应切除,辊压后易断裂(正极);
37、涂布工艺上所给的公差较大,能否缩小;
38、涂布工艺两边附料不同,如063048–ve单:
1·
7±
0·
05g
双:
3·
41±
05g;
083048+ve单:
74±
08g
7·
48±
15g;
39、未涂完的单面,用保鲜纸包后露置于空气中;
40、Cu、Al箔未用后,露置于空气中且边缘未包;
41、试机时所用碎布擦Cu、Al上浆料,对极片附为都有较多影响,且极片中有气泡(浆料);
42、停机时,前段80mm处置于空气中,极片上浆料变色,有气泡;
43、裁切大片定位不整齐,极片四角偏斜,不成直角,且切口处有毛剌及掉粉,手按片不稳定;
44、RD规定涂布报废片回收,但放置空气中过久,+ve起泡-ve掉粉;
45、未用电子称测量大片重量,也未规定多少时间分切小片测重;
46、牵引极片受力不均,导致附料不均,试片调机应保留,经确认后方可执行;
47、牵引Cu、Al箔的过程中,辅助转轴较多,箔两边受力不均;
48、正极单面前加多一辊轮,负极未有;
49、塞尺划痕,露基体极片较多;
50、收卷越大,速度加速,应减慢,否则不能干;
51、接带断带后,手拉附料不均匀(拉太快);
52、负极拉完转拉正极时,极片存放烘箱过长;
53、涂布机的保养未有当事人的审核;
54、涂布机的排风扇未有见过清洗;
55、裁切大片(手动)无设备操作、工位作业指导书,且工作台面太脏,极片易有±
ve极粉到极片上;
56、未调好机就涂布,造成两面附料不均匀
WelcomeTo
Download!
!
欢迎您的下载,资料仅供参考!