天舟COMAN设计仿真集成管理系统与PDMSDM系统的关系Word下载.docx
《天舟COMAN设计仿真集成管理系统与PDMSDM系统的关系Word下载.docx》由会员分享,可在线阅读,更多相关《天舟COMAN设计仿真集成管理系统与PDMSDM系统的关系Word下载.docx(8页珍藏版)》请在冰豆网上搜索。
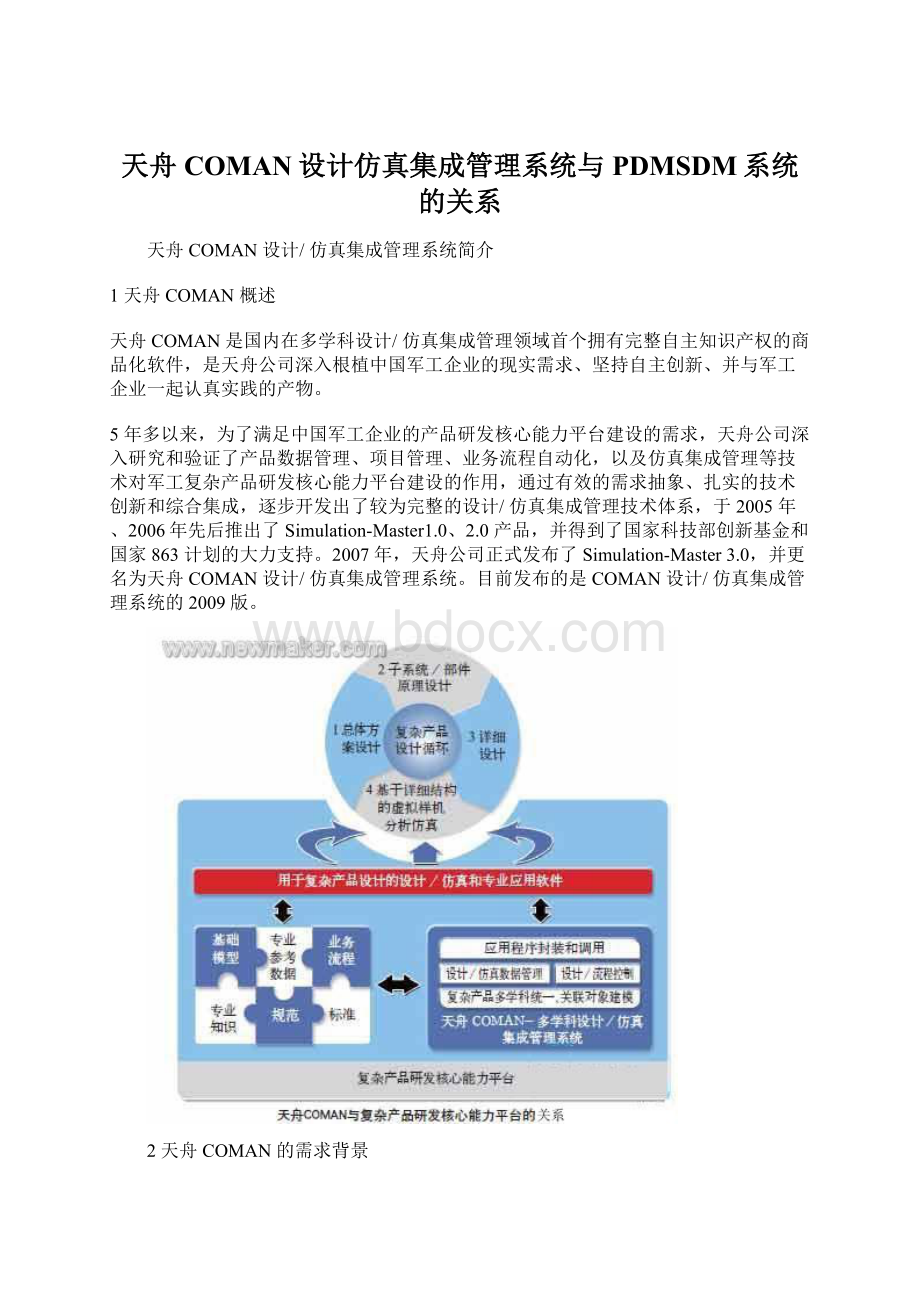
但是,信息技术与企业核心能力的融合还远远不够,信息技术对提升企业核心能力的可能贡献也还远远没有得到充分发挥。
目前,提升自主研发能力、掌握和发展不受制于人的自主知识产权军工核心技术,已经成为中国军工行业发展的重中之重,因此,越来越多的军工企业开始重视产品研发核心能力的积累和提升。
在此背景下,如何将各种信息化系统与企业的实际业务流程更加紧密地融合,帮助企业积累、整合和重用各种产品研发核心能力要素,正在成为军工企业越来越重视的问题。
同时,我们必须看到,传统信息化系统无法全面支持复杂产品生命周期中关键阶段(例如总体方案设计、部件/子系统原理设计,以及虚拟样机分析仿真等)的管理工作,也无法全面完成对军工企业研发核心能力要素的积累和整合任务。
因此,对军工复杂产品研制生命周期的“设计循环”,仍缺乏有效的信息化管理手段。
当前军工行业,以及其他具有自主研发需求的制造业企业,在研发核心能力要素的积累、整合以及重用等方面所面临的问题,以及在产品“设计循环”中所缺失的信息化管理手段,正是天舟COMAN设计/仿真集成管理系统所根植的关键需求基础。
3天舟COMAN的定位
COMAN主要面向航空、航天、船舶、兵器、电子、核工业等军工行业的专业研发单位,解决在复杂产品设计领域对于业务流程、工具、知识、规范和数据的集成管理需求,为复杂产品生命周期中的设计循环(如总体方案设计、部件原理设计、详细设计和基于虚拟样机的分析仿真等阶段)提供管理工具,并支持设计、试制和试验循环的衔接。
基于COMAN,可以封装集成用于特定专业产品设计/仿真的工具软件,容纳特定专业产品的多学科设计/仿真业务流程,嵌入特定专业产品的设计知识,融合、继承特定专业产品的设计方法和设计理念。
从而构造出支持特定产品的多学科设计/仿真并衔接其试制、试验过程的专业集成设计环境和研发核心能力平台。
COMAN是众多先进IT技术的结晶,但是,必须将COMAN与研发单位的业务流程、工具、知识、规范和专业参考数据等研发核心能力要素进行充分结合,才能对研发单位的产品研发核心能力平台建设工作有所帮助。
PDM、SDM系统在复杂产品生命周期中所发挥的作用
1复杂产品生命周期中的3个循环
军工产品的客户需求复杂、工作原理复杂、技术基础复杂、结构组成复杂,因此,军工产品几乎都是典型的复杂产品,而复杂产品研制生命周期会呈现下述3个循环。
(1)设计循环。
从图中可以看到,在已知产品战/技术指标的条件下,复杂产品的研制首先需要经历“设计循环”,包括“总体方案设计、部件/子系统原理设计、详细(结构)设计、基于详细结构的虚拟样机分析仿真”等阶段。
其中:
(a)总体方案设计可能会自循环,以便进行多个总体方案的构思和多方案的性能估算及选优;
然后基于一个或数个初步具备可行性的总体方案,分别为子系统/部件分配设计指标,并进入到子系统/部件原理设计阶段,以便进行子系统/部件的初步匹配设计。
(b)在子系统/部件原理设计过程中,如果发现矛盾或无法满足的设计指标要求,可能会要求进行总体方案的修改。
因此该阶段与总体方案设计阶段可能出现反复迭代,并逐步选优、形成各子系统/部件性能匹配的详细方案。
(c)对于经过子系统/部件原理设计,预估可以到达或超过战/技术指标的方案,可以进入详细设计阶段,完成对子系统、部件(直至零件)的结构、电路、控制软件等方面的详细设计工作。
(d)在进行详细设计的同时,还需要基于详细设计结果进行单学科、乃至多学科的虚拟样机分析仿真,以便验证关键零件、部件、子系统、乃至全系统是否达到了各自的战/技术指标,并尽可能发现设计缺陷。
(e)如果针对详细设计结果的虚拟样机分析仿真发现了设计缺陷或设计结果达不到战/技术指标的情况,则需要对详细设计进行更改,甚至有可能导致对部件/子系统方案的更改,乃至对总体方案的更改。
因此,基于详细设计结果的虚拟样机分析仿真阶段与前面的几个设计阶段也可能形成跨一个阶段甚至跨多个阶段的反复迭代。
迭代逆向跨越的阶段越多,设计反复工作量就越大,设计周期越长。
但这些迭代毕竟是在设计循环内部完成的,因此代价还是比较低的。
(2)试制/验证和改进循环。
在设计循环进行到一定程度以后,需要基于通过审核的详细设计结果和对应的工艺制定试制计划、安排试制生产;
然后再利用试制出的零部件、子系统,乃至产品全系统进行各类试验验证。
一旦发现问题,则可能会引发设计更改,从而重新进入产品设计循环。
这些更改可能只涉及到详细设计结果,也有可能涉及到部件/子系统的方案,甚至是总体方案,更改所逆向跨越的设计阶段越多,需要付出的工作量、周期、成本代价越高。
这就是试制/验证和改进循环。
此循环所涉及的人员、周期,以及成本的开销要远远高于设计循环。
而在实际工作中,该循环往往迭代次数多,这将导致整个产品研制生命周期长、代价高。
因此,尽量减少试制/验证和改进循环次数是非常必要的。
(2)批生产、维护、改进循环。
在多次进行产品全系统试制和试验,达到产品定型大纲要求后,产品有可能定型、确认技术状态,并进入批生产阶段。
批生产前还需要进行批生产工艺的编制和审核、批生产计划的编制,随后进入批生产制造过程;
最后,定型产品提交用户或上级总成单位,进入服务和维护过程。
这就是“批生产、维护、改进循环”。
在这些阶段若发现必须进行设计更改的严重问题,则需要进行设计更改,并再次进入设计循环,这时所逆向跨越的阶段、涉及的人员、周期、成本将更大。
总结上述研制过程,可以非常明显地看到,要缩短研制周期、降低研制成本、保障研制质量,能在“试制/验证和改进循环”中解决的问题就坚决不应该遗留到“批生产、维护、改进循环”,能在“设计循环”中解决的问题就坚决不应该遗留到“试制/验证和改进循环”;
并且,在“设计循环”中解决主要设计问题,既能够节约成本,更可以大大缩短研制周期。
2PDM、SDM系统在复杂产品研制生命周期中发挥作用的阶段
在复杂产品的研制生命周期中,PDM、SDM系统可以在几个不同的阶段发挥作用,其中:
(1)PDM主要工作于复杂产品生命周期的“详细设计”阶段、“数据审核、技术状态管理、打印”阶段、“工艺设计”阶段;
此外,PDM通过汇总产品“物料清单”来衔接“工艺设计”阶段和“生产/供应计划”阶段。
(2)SDM主要工作于“基于详细结构的虚拟样机分析仿真”阶段,用以管理仿真数据和仿真流程。
正因为如此,站在PDM、SDM管理支撑范围来看,对于决定产品能否达到战/技术指标的源头阶段——产品“设计循环”,是缺乏完整的信息化管理手段的。
而COMAN设计/仿真集成管理系统则恰恰定位于对复杂产品生命周期的“设计循环”提供业务流程和数据管理支撑,综合管理在复杂产品“设计循环”的“总体方案设计”、“部件原理设计”、“详细结构设计”、“基于详细结构的虚拟样机分析仿真”等阶段反复迭代进行的设计/仿真流程和迭代过程中产生的设计/仿真数据,并为设计/仿真流程、设计/仿真工具软件、设计规范、标准、经验参考数据等支撑设计循环的研发核心能力要素提供积累、整合和重用的手段。
可见,COMAN设计/仿真集成管理系统的定位与PDM、SDM有很大区别,但COMAN可以提供管理支撑的领域与PDM、SDM又是有联系的。
PDM系统可以解决的问题以及COMAN与PDM的关系
1PDM系统可以解决的问题
从20世纪80年代开始,CAD软件普遍应用于产品的详细设计之后,开始出现一系列相关的管理问题,尤其是三维CAD软件从20世纪90年代开始得到普及之后,这些问题更加严重。
而这正是PDM诞生的需求基础,诸如:
(1)CAD模型和图档大量生成,难以有序管理,导致模型、图档和设计物料清单的技术状态混乱。
(2)要正常的生产,必须要有完整的设计物料清单并正确控制零部件模型、图纸技术状态的变更过程。
基于上述需求,PDM技术和相关系统从20世纪90年代开始得到迅速发展。
至今,PDM系统已经得到的发展和广泛的应用,为无数企业产品研制能力的提升做出了贡献。
其功能范围和管理能力有了很大的发展,但其核心应用仍然是对产品详细设计模型和图纸进行管理、对产品设计物料清单进行统计、对基于详细结构的产品技术状态和审核变更流程进行控制,从而从设计的角度支撑技术状态正确的生产制造。
因此我们必须看到,就像任何一种管理系统一样,PDM并非万能系统,它也有自己的局限性,例如:
(1)PDM的业务流程管理功能主要局限于数据审核和更改流程。
(2)PDM对需调用工具软件,且需要控制软件之间数据流的设计和仿真业务流程,基本无法提供管理能力。
(3)此外,PDM缺乏适合于分析仿真数据和试验数据的专业管理能力,更难于针对设计、仿真、试验数据的不同特点提供专业管理能力,并对它们进行综合关联。
因此,PDM实际上是连接产品研发和生产的枢纽环节,它可以供产品研发部门和档案部门使用,并为产品制造提供支撑数据。
但它无法全面承担对复杂产品生命周期中完整“设计循环”的管理工作。
2COMAN设计/仿真集成管理系统与PDM的关系
COMAN设计/仿真集成管理系统与PDM在需求背景、应用目标,以及复杂产品生命周期中的管理位置等方面有很大差异,但是2者在产品生命周期中的作用又有交叉点,即对产品“详细设计”的管理。
因此,从应用需求来看,有必要实现COMAN与PDM之间的集成以避免2者互为信息孤岛,使COMAN可以在产品反复迭代设计达到一定技术状态之后,把所管理的产品详细设计数据发布给PDM系统,以便以PDM系统为中心来控制支持生产的产品技术状态。
由于天舟公司曾经多年自主开发PDM系统,因此对COMAN设计/仿真集成管理系统如何与PDM系统实现有效集成,有充分的技术储备。
SDM系统可以解决的问题以及COMAN与SDM的关系
1SDM系统可以解决的问题
CAE技术从20世纪60年代开始在尖端领域得到局部应用,到20世纪90年代后则开始越来越广泛的应用于复杂产品设计中各个学科的分析仿真领域,并与三维CAD系统的普及应用一起逐步推动形成了虚拟样机分析仿真支持下的产品虚拟样机设计模式,使产品研制者在产品研制生命周期的“设计循环”中就有可能对设计方案的性能进行量化评估,从而大幅度提高了在设计循环内部发现并解决设计问题的能力。
但是,CAE软件大量应用于虚拟样机分析仿真后也带来了一系列问题,而这些问题正是SDM系统的需求来源,诸如:
(1)仿真数据大量生成却难以有序管理。
(2)复杂产品的虚拟仿真需要不同学科的多种仿真软件按一定流程配合工作,而仿真软件之间又会有必须配合的数据流关系。
如果没有专门的管理工具支撑,多学科协作仿真很难开展,更无法保障效率。
基于上述需求,SDM技术和相关系统从20世纪90年代中后期开始得到发展,至今,SDM系统已经在某些领域获得了一定的应用。
SDM可以定义和管理仿真过程,整合不同学科的仿真软件,并对仿真数据进行有序管理和传递,从而提高多学科协同仿真分析的效率。
当然,SDM也存在一些局限性,例如:
(1)SDM强调对仿真数据的管理,但却不适用于对设计数据进行管理,更不便于对设计数据和仿真数据进行综合管理。
(2)SDM作为仿真管理平台,其定位并非支撑完整的设计循环,因此,SDM的数据管理架构和数据流控制功能往往并不适合对反复迭代的设计过程提供完整的支持。
2COMAN设计/仿真集成管理系统与SDM的关系
COMAN设计/仿真集成管理系统和SDM存在明显的定位差异:
COMAN定位于解决复杂产品设计领域对于业务流程、工具、知识、规范和数据的集成管理需求,为复杂产品生命周期中的设计循环(如总体方案设计、部件原理设计、详细设计和基于虚拟样机的分析仿真等阶段)提供管理工具,并支持设计、试制和试验循环的衔接,因此COMAN在数据管理和流程管理方面所适应的范围大于SDM,COMAN可以支持对设计/仿真数据的综合关联管理,并综合管理跨专业、多学科的反复迭代设计/仿真过程;
而SDM则主要对仿真数据和仿真流程进行管理。
对于一个需要完成复杂产品研发全过程的研发单位来讲,由于仿真过程/仿真数据在一个复杂产品的实际研发过程中与设计数据和设计过程是难以拆分的,因此,COMAN有更强的适用性。
当然,对于已经采购了SDM,甚至已经在SDM上进行了定制开发工作的研发单位,可以将COMAN和SDM集成起来,既充分发挥COMAN支撑复杂产品反复迭代设计/仿真过程的优势,也可以使SDM继续发挥其作用。
结束语
COMAN设计/仿真集成管理系统是天舟公司基于“根植需求、坚守使命、自主创新”发展道路,根植于中国军工行业研发核心能力建设需求而发展的新一代管理信息系统,它并不是按照教科书编写的软件,而是基于一系列核心技术进行综合集成和自主创新的产物,并将跟随复杂产品研发行业在产品研发核心能力方面的建设进程而得到进一步发展和完善。
因此,COMAN与相关信息系统的集成和融合也将随应用需求的发展而得到进一步深化。
(end)