电石法生产氯乙烯Word格式文档下载.docx
《电石法生产氯乙烯Word格式文档下载.docx》由会员分享,可在线阅读,更多相关《电石法生产氯乙烯Word格式文档下载.docx(20页珍藏版)》请在冰豆网上搜索。
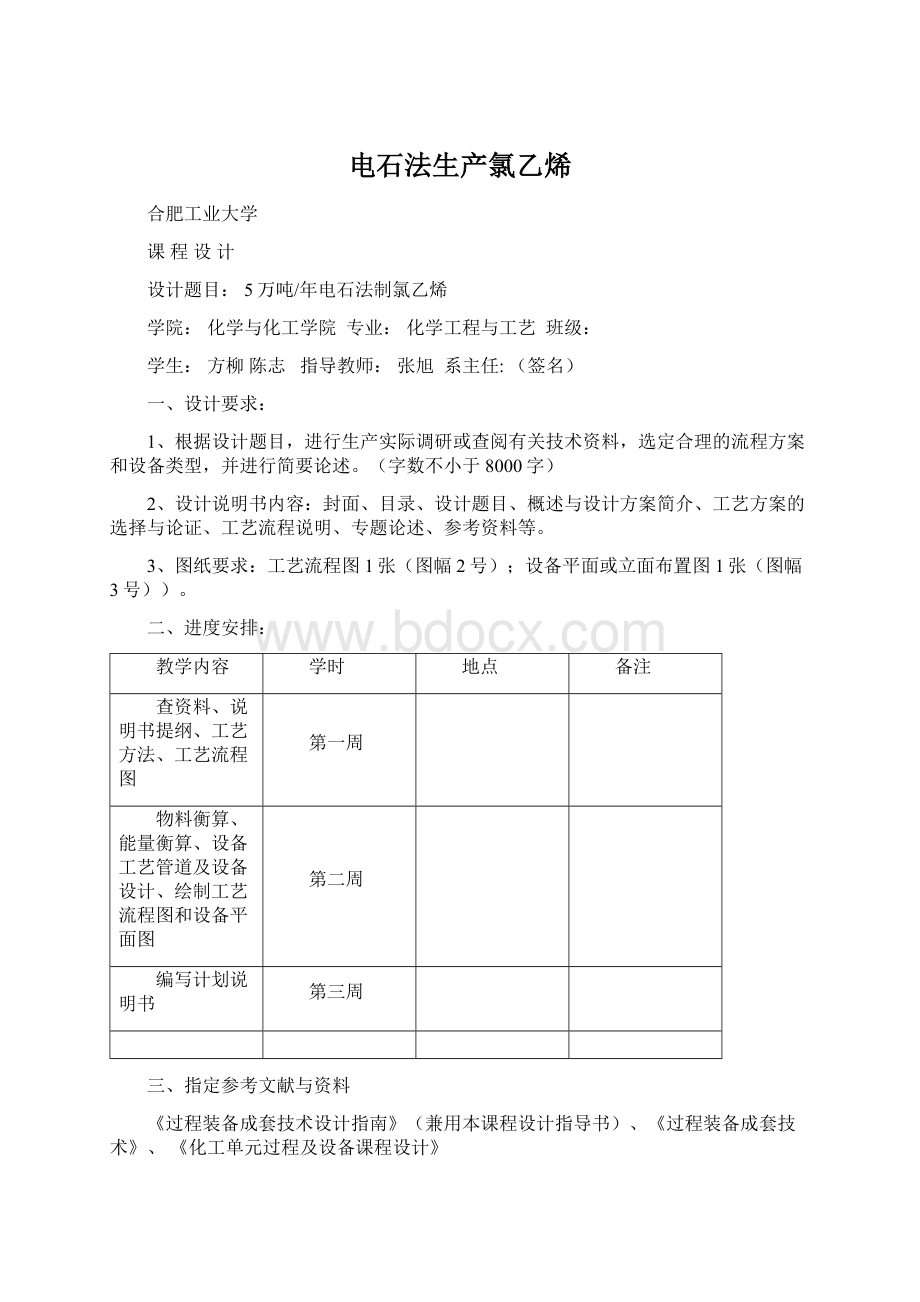
三、指定参考文献与资料
《过程装备成套技术设计指南》(兼用本课程设计指导书)、《过程装备成套技术》、《化工单元过程及设备课程设计》
摘要
本次课程设计主要是设计氯乙烯的生产成套装置。
氯乙烯是生产聚氯乙烯的主要原料,到目前为止,全球有93%以上的氯乙烯采用氧氯化法生产。
在国内,考虑到石油资源不足,价格较高,而电石资源丰富,所以大部分工厂都采用电石法制取氯乙烯。
本次主要介绍电石法制取氯乙烯。
先后介绍了从原料气氯化氢、乙炔的制备到氯乙烯的合成、氯乙烯的精馏等一系列生产过程的工艺流程、工艺原理以及主要设备选型等问题。
关键词:
氯乙烯;
电石法;
乙炔;
氯化氢;
工艺流程;
精馏
一乙炔的制备
乙炔生产的工艺原理
(1)电石的破碎
通常厂家采购的电石都是大块的电石,而电石料块进入发生器的合理径为25~50mm,因此在进发生器前必须破碎,通常是将大块的电石放入颚式破碎机,粗破后料块直径为80~100mm,通过皮带机输入电石仓库,然后经过二次破碎,径粒达到25~50mm,破碎后料块通过皮带机径除铁器除铁后输入日料库,作为发生器的入料电石。
进入破碎机的电石温度应≤130℃,否则会烫坏,烧坏皮带;
进入发生器的电石温度应该≤80℃,否则对发生系统不安全。
(2)电石的除尘
化学工程里把气体与微粒子混合物中分离粒子的操作称作除尘。
针对电石及其粉尘的特性,选用的除尘方法一般有以下几种。
①旋风除尘。
旋风除尘器对数微米以上的粗粉尘非常有效。
采用简单的旋风除尘器和风机进行除尘,利用电石粉尘在风机的作用下,在除尘器内旋转所产生的离心力,将电石粉尘从气流中分离出来。
这种方式结构简单,器身无运动部件,不需要特殊的附属设备,安装投资较少,操作、维护也方便,压力损失中等,动力消耗不大,运转维护费用低,也不受浓度、温度的影响。
但由于电石粉尘比较细,用这种简单的除尘方式很难达到环保要求,除尘效率不高。
②湿法除尘。
湿法除尘具有投资少,结构简单,占地面积小,特别是对易燃易爆气体的除尘效果更好,在操作时不会产生捕集到的电石灰尘再飞扬。
电石除尘通常采用旋风除尘和湿法的冲激式除尘器相结合。
这种除尘方式虽然效率较高,但由于系统压力损失大,管道容易积灰。
冬天用蒸汽时,积灰易受潮结块,造成管道堵塞,清理比较困难。
除尘器内排出的电石渣水,多耗了水又易造成二次污染,除尘器排出的气体中水蒸气在寒冷的北方也容易结冰,因此这种除尘方式适合于气候湿润、冬天不冷的地方使用。
(3)袋式过滤除尘
布袋除尘室依靠编制的或毡织的滤布作为过滤材料来达到分离含尘气体中电石尘的目的,除尘效率一般可达99%。
滤布在长期与粉尘的接触和反复清理的过程中,其性能会发生变化,这在实际使用中影响很大。
滤布一般在一到两年内大多数孔眼就会被堵塞,及时清理也不能达到所需的气量,或产生滤布破损事故,此时需要更换滤布。
因此滤布的选型非常重要,一般要考虑材质、织法、透气率、阻力降、压损比等。
(4)乙炔的发生
仓库内经破碎至25~50mm的电石,在皮带机的输送下,加入到经氮气置换合格的第一贮斗,再加入到经氮气置换合格的第二贮斗,在由电磁振动加料根据发生器的控制需求加入发生器内。
电石遇到发生器内的水生成粗乙炔气体由发生器顶部逸出,经喷淋预冷器及正水封进入喷淋冷却塔及气柜中。
反应所放出的热量是由过量的冷却塔废水和清净塔废水及渣浆上清液或工业补充水连续加入发生器并通过溢流管溢流而出,上述加水量以维持发生温度在(85±
5)℃为标准。
为了使发生器液相中的电石颗粒表面因水解反应产生的浓渣浆层被耙齿不断更新破坏,使电石表面不断地能偶与水充分接触,发生器内设置了多层隔板和耙齿,通过耙齿的搅拌使电石颗粒的表面得到不断的更新并缓缓地向下一层隔板推动,使得水解速度更快,更完全;
水解反应的副产物电石渣浆不断从溢流管流出,而较浓的渣浆及矽铁杂质由发生器内的搅拌耙齿送至底部间歇排放。
当发生器压力因加料故障或停车时,压力低于控制范围时,气柜内贮存的乙炔将借压差经逆水封,进入发生器内以保持设备处于正压,确保安全生产。
发生器的安全水封连接管道安装于发生器液面略上方的气相部位。
当发生器气相出口管道或冷却内电石渣堵塞而压力剧增时,乙炔气经管道冲破安全水封自动排空。
在湿式发生器中电石加入液相中发生水解反应,生成乙炔,反应式如下:
CaC
+2H
O
+
由于工业品电石中含有不少杂质,在发生器水相中也同时进行一些副反应,生成相应的PH
、
、NH
等杂质气体,其反应时如下:
发生器生成的是由乙炔气和杂质气体共同组成的、含有大量水蒸气的粗乙炔气,进入清净工序。
乙炔发生工艺流程图见1-1。
(5)乙炔的净化
粗乙炔气由于电石内杂质常含有硫化氢、磷化氢、氨、砷比氢等杂质气体。
它们合对氯乙烯合成的氯化高汞触媒进行不可逆吸附,破坏其“活性中心”而加速触媒活性的下降,其中磷化氯会降低乙炔的自燃点,与空气接触会自燃,均应彻底脱除。
目前多数工厂均采用次氯酸钠液体清净剂,其与杂反进行氧化反应:
清净过程反应产物磷酸、硫酸等由后面的碱洗过程予以中和为盐类,再由废碱液排出:
对于生产中液体清净剂次氯酸钠浓度和pH值的选择,主要考虑到清净效果及安全因素两个方面。
塔内次氯酸钠溶液的有效氯含量不低于%,而补充新鲜溶液的有效氯应该控制在~范围内,pH值在7~为宜。
处理后的乙炔气经乙炔气冷却器出去饱和水分,制的纯度达%以上,不含S、P的合格精制乙炔气送氯乙烯合成工序。
乙炔生产中的主要设备
(1)乙炔发生器
乙炔发生器是是以电石水解反应制取乙炔的主要设备,目前国内多半采用的是湿式立式发生器。
本次设计采用φ的六层隔板发生器,其乙炔生产能力为每小时2400m
以上。
其示意图如图1-2。
图1-1乙炔发生工艺流程图
图1-2乙炔发生器示意图
(2)清净塔
清净塔式清净系统的主要设备。
图1-3为典型的填料式清净塔的结构。
清净塔常用的填料有拉西瓷环、塑料阶梯环或波纹填料,如采用陶瓷环尺寸越小,则接触表面积越大,空隙率越小,根据生产经验,一般使用φ25~50mm瓷环,每个瓷环的填充高度为6~9米。
作为清净作用的填料塔,推荐空塔气速在~s,气体在塔内总停留时间为40~60s,以确保化学吸收完全。
由于乙炔清净属于化学吸收过程,清净效果除了与吸收剂浓度、pH值以及吸收温度有关外,还与气液的接触时间有关。
由于清净塔的液相介质为次氯酸纳,以及清净反应生成的硫酸、磷酸等,它对塔体采用的碳钢有腐蚀作用,需要对其进行防腐处理,原来的清净塔采用的是钢衬胶,衬胶在有温度的情况下容易老化脱落,现在有些厂家采用新型的内衬材料,如内衬PO,内衬四氟等,使用寿命长。
图1-3清净塔示意图
(3)乙炔水环泵
在乙炔气输送设备的选择上,首先要考虑乙炔的性质和对输送设备的要求,从乙炔的化学、物理性质看,它是易燃易爆的气体,不一在高压条件下输送,以确保安全。
从输送要求看,乙炔要经过一系列的净化设备,必然产生压力损失,为了克服压力损失,就要有一定的压头,而同时又必须达到生产所需的气量,一确保生产平衡。
为此,选用水环泵来输送乙炔气体。
其特点是叶轮与泵壳间隙较大,不易因碰撞而产生火花,对易燃易爆的气体输送安全可靠。
泵内的工作液为水,使乙炔成湿气状态,抑制了乙炔的爆炸性质。
水环泵具有一定的抽气能力,输送压力不是很高,而量大的性能,虽然能量转换效率不高,但对输送乙炔气体是相当安全、适合的。
二氯化氢的制备
工艺流程
(1)原材料、辅助材料、公用工程规格及消耗
①原材料规格及消耗
(ⅰ)氯氢处理来的氢气
≥%(体积分数,干基)压力≤(G)
≤300ppm(体积分数,湿基)用量h
(质量分数,湿基)(
h;
h)
温度20℃
(ⅱ)氯氢处理来的氯气
≤%(体积分数,干基)用量h
≤50×
10
9(体积分数)(
kg/h)
温度≤45℃
(ⅲ)液氯尾气(废氯)
80%~90%压力≤Mpa(G)
≤2%(体积分数)用量kmol/h(
kg/h)
(Ⅵ)氯化氢气体
温度≥94%
游离氯≤%
a.合成总量:
kmol/h
温度≤45℃
压力≤Mpa(G)
b.去VCM装置量:
c.去I段降膜吸收器量:
kmol/h(
h:
;
②辅助材料规格及消耗
(ⅰ)氮气
供应压力Mpa(G)温度常温
(ⅱ)仪表空气
供应压力≥Mpa(G)温度常温
露点≤—40℃用量2
/h
尘、油无尘、无油
(ⅲ)循环水
进水温度30℃回水温度40℃
进水压力约Mpa(G)回水压力约(G)
用量约244
/h
(Ⅵ)纯水
进水温度25℃用量≤15
进水压力≤Mpa(G)
(4)本工序产品质量标准及消耗指标
产品质量标准
①氯化氢质量指标
氯化氢纯度≥94%含游离氯≤%
②氯化氢消耗指标
氯化氢消耗指标见表2-1。
表2-1氯化氢消耗指标
氯气
氢气
纯水
二次水
动力电
972kg/t
30kg/t
3t/t
17t/t
·
h/t
本工序的生产原理
(1)合成氯化氢的反应机理
生产氯化氢的主要反应时氯气与氢气的化合反应,氯气与氢气在一定的条件下(如光,燃烧或触媒)下,会迅速化合,发生链反应,其反应式如下:
在实际生产中,氯气与氢气在燃烧前并不混合(否则发生爆炸反应)而是通过一种特殊的设备“灯头”使氯与氢均衡燃烧。
(2)影响氯化氢合成的因素
①温度的影响。
氯气与氢气在440℃以上会迅速化合,但温度高于1500℃时,就有显著的热分解现象。
氯气与氢气的反应时放热反应,有大量的热量产生,这种热量使生成的氯化氢温度升高,因此必须设法把合成过程中产生的反应热出去,反应才能向有利于生成氯化氢的方向移动,所以合成炉采用夹套式冷却移走反应热。
②水分和其他触媒的影响。
绝对干燥的氯气和氢气是很难起反应的,当有微量的水分存在时往往可以加快反应速度,所以水分是促进氯气与氢气化合的媒介,但是当水分含量超过一定值时,对反应速度就没有多大影响。
(3)盐酸的生成机理
合成氯化氢气体时,用水吸收,即生成盐酸。
当用水吸收氯化氢时,伴随着溶解的进行,将释放大量的溶解热,热量会是盐酸温度升高,不利于对氯化氢气体的吸收,因为当氯化氢纯度一定时,溶液温度越高,氯化氢气体的溶解度就越低,就使得制得的盐酸浓度越低。
根据化学平衡的原理,必须移走这部分热量,才能使溶液向有利于生成盐酸的方向进行,在化工生产中采用二段降膜式吸收法吸收生产盐酸。
还有采用一段降膜式吸收法和二段绝热式吸收法进行吸收生产盐酸。
氯氢纯度、流量、冷却水量、氯化氢纯度等要素都对氯化氢及盐酸的生产过程有很大的影响。
工艺流程简述
(1)生产氯化氢的工艺流程简述
原料(氢气)由氯氢处理工序用氢气压缩机压缩过来,经过氢气缓冲罐,进入氢气管道阻火器,经流量计计量后,经过回阀、调节阀进入二合一石墨合成炉灯头。
氢气通过氢气缓冲罐上的压力自动调节阀自动调节,放空氮气经过氮气放空阻火器后放空。
原料(氯气)由氯氢处理工序用氯气压缩机送过来、液氯尾气(废氯)由液氯工序送过来分别进入氯气缓冲罐,混合后的氯气进入氯气管道阻火器,经流量计计量后,经截止阀、调剂阀进入合成炉灯头。
氮、氢气在合成炉灯头混合燃烧,生成的氯化氢由合成炉上部送出,经冷却槽、石墨冷却器冷却后,进入氯化氢分配台,从氯化氢分配台出来的氯化氢气体,按合成车间的需求量经流量计计量送往VCM工序,开停车时不合格的氯化氢则进入吸收系统用于生产高纯盐酸。
从石墨冷却器中冷凝下来的盐酸,从石墨冷却器的底部流入冷凝酸排放槽,然后排入盐酸储槽。
软水槽中的软水,经软水泵加压后送入二合一石墨合成炉夹套的下部,之下而上流入合成炉,合成炉夹套顶部产生的低压蒸气经闸阀及压力自动调节阀送入低压蒸气管道。
(2)生产高纯度盐酸的工艺流程简述
用于制酸的氯化氢气经过氯化氢分配台上的截止阀进入高纯盐酸吸收系统Ⅰ段降膜吸收器上封头,与来自Ⅱ段降膜吸收器的稀酸从管内自上而下并流吸收生成成品盐酸,成品盐酸从Ⅰ段降膜吸收器的底部流经盐酸液封罐,然后流入盐酸储槽,未被吸收的氯化氢气体经返气管由Ⅱ段降膜吸收器的上风头进入,与水在管内自上而下进行并流吸收,生成的稀酸经U型管进入Ⅰ段降膜吸收器,废气从Ⅱ段降膜吸收器的底部流出进入水流喷射器,痛循环水一起进入循环液储槽,经过分离后的尾气排入大气。
成品酸流入酸储槽,分析合格后用酸泵送去自用或打入盐酸高位槽供给客户。
氯化氢合成的主要设备
(1)合成炉
合成炉是制造氯化氢气体的主要设备。
过去工艺上应用比较广泛的是钢制合成炉,有空气冷却式和水冷夹套式两种。
现在均以石墨合成炉为主。
由于石墨合成炉具有耐高温、耐腐蚀、传热效率高等优点,石墨合成炉的应用十分广泛。
工业上多见炉内体的块孔壁通入冷却时的水冷式石墨炉,以降低炉内氯化氢的温度和提高生产能力。
尤其是副产低压蒸汽的合成炉,起副产低压蒸汽输送距离较远、利用范围较广泛,如图2-1。
(2)石墨换热器
石墨换热器是用于冷却或加热氯化氢或其它腐蚀性气体的设备,主要有块孔式(如图2-2)和列管式(如图2-3)。
列管式石墨换热器,可用于合成炉经空气冷却导管后的高温氯化氢的冷却,水箱的设计可以降低气体进口部位特别是上管板的温度,不至于经受高温而使管板与列管的交接缝处因材料热膨胀系数差异而胀裂损坏。
对于列管式石墨换热器,立式安装比斜式安装或卧式安装更有利于浮头的自由伸缩。
块孔式石墨换热器是由若干带有无聊孔道、冷却水孔道的石墨换热块(多块上下叠加),上下石墨封头及其金属盖板以及圆筒钢壳体(圆块孔式)或两端侧盖(矩块孔式)等主要零件组成,零件之间用衬垫密封,并以长螺栓紧固。
(3)膜式吸收塔
膜式吸收塔是一种等温吸收器,是哟个不透性石墨制成的,是近年来发展起来的用于氯化氢吸收制取盐酸的主要设备,起基本结构与一般列管式石墨换热器相似,所不同的是吸收塔在上管板的板孔上设置有吸收液的分配器。
膜式吸收塔具有典型的气液相在固定界面传质的特点,因而出酸浓度高,温度低,操作稳定,易于修剪等特点。
其许用的技术特性:
①许用温度。
气体入口温度<250℃;
②许用压力。
壳程,管程Mpa。
图2-1副产低压蒸汽的氯化氢合成炉和块孔式石墨换热器
图2-2块孔式石墨换热器图2-3列管式石墨换热器
三氯乙烯的制备
乙炔工段送来的精制乙炔气体(纯度≥%)经乙炔砂封后,与氯化氢工段送来的氯化氢(纯度≥93%),不含游离氢)在混合器以一定的比例(1:
)混合后进入一级石墨冷却器,用—35度冷冻水冷却至(2±
4)℃,再经二级石墨冷却器用-35,冷冻盐水间接冷却至(—14±
2)℃左右,在这两级石墨设备内各依重力作用出去大部分冷凝液后一次进入一级酸雾过滤器、二级酸雾过滤器,由氟硅油玻璃棉过滤捕集出去少量晶粒很小的酸雾,排出40%的盐酸送氯化氢脱吸或作为副产品包装销售。
得到含水分≤%的混合气体一次进入石墨预热器,蒸气预热器预热至70~80℃送入串联的两端装有氯化高汞触媒的转化器,课分别由数台并联操作,反应生成粗氯乙烯,第一段转化器出口气体中尚有20%~30%的乙炔未转化,再进入第二段转化器继续反应,使其出口处的乙炔含量控制在3%以下。
第二段转化器装填的是活性高的新催化剂,第一段转化器装填的则是活性低的催化剂,即由第二段更换下来的旧催化剂。
合成反应热通过转化器列管间的循环热水移去。
粗氯乙烯经过装有活性炭填料的除汞除去大部分汞以后,进入粗氯乙烯冷却器冷却至<30℃,进入一级水洗组合塔,以二级水洗塔填料的稀酸及解吸后的稀酸吸收混合气体中的大部分氯化氢气体,制的氯化氢含量为28%~30%的盐酸送氯化氢脱吸或做为副产品包装销售;
经过吸收后的粗氯乙烯气体进入二级填料水洗塔二次清洗,水洗后含有微量的氯化氢酸雾、二氧化碳及惰性气体,进入碱洗塔用8%~20%的NaOH溶液洗涤,净化后的气体经汽水分离部分脱水后送入压缩工序。
生产间的流动则有设置的氯乙烯气柜来实现缓冲。
工艺原理
(1)混合气脱水
利用氯化氢吸湿性质,预先吸收乙炔气体中的大部分水,生成40%左右的盐酸,降低混合气体中的水分;
利用冷冻方法混合脱水,是利用盐酸冰点低,盐酸上水蒸气分压低的原理,将混合气体冷冻脱酸,以降低混合气体中水蒸气分压来降低气相中水含量,达到进一步降低混合气体中水分至所必需的工艺指标。
在混合气体冷冻脱水过程中,冷凝的40%盐酸,除少量是以液膜状自石墨冷却器列管内壁流出外,大部分呈极细微(≤2μm)的“酸雾”悬浮于混合气体流中,形成“气溶胶”,该“气溶胶”无法依靠重力自然沉降,要采用3%~5%憎水性有机氟硅油的5~10μm细玻璃长纤维过滤除雾,“气溶胶”中的液体微粒于垂直排列的玻璃纤维想碰撞后,大部分雾粒被截留,在重力作用下向下流动的过程中液滴逐渐增大,最后滴落下来并排出。
工艺条件的选择:
冷冻混合脱水的关键是温度的控制,温度高达气体含水达不到工业要求,会腐蚀碳钢设备和管道,还会在转化器内和乙炔发生反应生成乙醛类的缩合物(粘稠状),触媒结块堵塞转化器列管,部分触媒失去作用,转化系统阻力增大:
温度太低,低于浓盐酸冰点(—18℃),则盐酸结冰,该冰堵塞设备通道,系统阻力增大、流量下降,扬中市流量降为零,无法继续生产。
因此,混合脱水二级石墨冷却器出口的气体温度必须稳定地控制在(—14±
2)℃范围内。
经混合脱水后的混合气体温度很低,需要在预热器中加热到70~80℃后才能进入转化器进行反应。
这是因为混合气体加热后,使未除尽的雾滴全部气化,可以降低氯化氢对碳钢的腐蚀性,气体温度接近转化温度有利于提高转化反应的效率。
(2)氯乙烯的合成
一定纯度的乙炔气体和氯化氢气体按照1:
(~)的比例混合后,在氯化高汞触媒的作用下,在100~180℃温度下反应生成氯乙烯。
反应方程式如下:
在合成反应中还有少量的副反应发生:
乙炔在与氯化氢反应生成二氯乙烷:
副反应是我们所不希望的,既消耗掉宝贵的原料乙炔,又给氯乙烯精馏增加了负荷,其关键是催化剂的选择、摩尔比、反应热的及时移出和反应温度的控制。
生产条件的选择如下。
①摩尔比:
使一种原料气的配比过量,可使另一种原料气的转化率增加。
因此大多数化学反应利用这一原理,使价值低的原料过量,尽量使价值高的原料反应完全。
由于乙炔的价值远远高于氯化氢,因此要将氯化氢过量配比。
但氯化氢过量太多,则不但增加了原料消耗,还会增加生成1,1-二氯乙烷副产物。
实验与实践的经验,控制乙炔与氢气的摩尔比在1:
(~)范围为宜。
实际操作中,是通过控制乙炔和氯化氢流量计来进行摩尔配比,并以合成二段转化器出口粗氯乙烯气体中氯化氢和乙炔的含量分析值来进行校正的。
②催化剂:
目前乙炔法氯乙烯合成所使用的催化剂都是氯化汞类的催化剂。
这是因为该催化剂的得率和选择性都很高,价格又不算贵,但伴随有汞污染。
虽然国内的许多科学家对无汞类的催化剂进行了大量的研究和应用实验,但人未能找到能与氯化汞相比肩的催化剂,非汞类催化剂的研究是一个漫长而艰巨的任务。
氯乙烯合成所使用的催化剂,是将氯化汞吸附在活性炭载体上。
纯的氯化高汞对合成反应并不催化作用,纯的活性炭也只有较低的催化作用,而当氯化高汞吸附到活性炭上后,即具有很强的催化活性。
对氯乙烯催化剂载体的活性炭是又相应要求的,其内部“通道”是由10μm左右的微孔构成的多孔结构,比表面积应在800~1000㎡/g。
目前做氯乙烯催化载体的是φ3×
6mm颗粒活性炭,为了满足内部孔隙率其吸苯率应≥30%,机械强度应≥90%。
一般来讲,椰子壳或核桃壳制得的活性炭效果较好。
③反应温度:
温度对氯乙烯很成反应有较大影响。
提高反应温度有加快合成反应的速度,获得较高转化率;
但是过高的温度会使催化剂吸附的氯化高汞升华,降低催化剂活性和使用寿命,还会使副反应产物二氯乙烷增多,催化剂上的升汞易会被还原成干汞和水银。
工业生产中尽可能将合成反应温度控制在100~180℃。
要控制反应温度就要控制适当的乙炔空间流速和提高转化器的传热能力,最佳的反应带温度应该在130~150℃之间,只是可以做到的。
④反应压力:
乙炔与氯化氢的合成反应时两分子合成一分子的反应,是体积减小的反应,加大反应压力有利于反应的正向进行。
要实现较高的反应压力,则需要较大的流体输送动力,过大的反应压力对流体输送机械提出了更高的要求,有较大的困难,且输送动力过大也不经济;
乙炔在较高的压力下安全性下降。
因此合成反应压力控制在~为宜。
⑤空间流速:
空间留宿是指单位时间内通过单位体积催化剂的气体流量(习惯上用乙炔气体来表示),其单位为
乙炔/(
催化剂·
h)。
在实际生产过程中,比较恰当的乙炔空间流速为25~35
h),在这一空间流速范围内,既能保证乙炔有较高的转化率,又能保证高沸点副产物的含量少。
(3)粗氯乙烯的净化
①净化目的。
除去过量配比的氯化氢、未反应的乙炔、氮气、氢气、二氧化碳和为除尽的微量汞蒸气等气体,以及副产物反应所产生的乙醛、二氯乙烷、二氯乙烯、三氯乙烯、乙炔基乙烯等杂质气体。
②净化原理。
水洗和碱洗。
水洗是属于一种对于气体的物理吸收的操作。
是利用适当的液体作为吸收剂来处理气体混合物,即利用吸收剂吸收混合气体中溶解度大的气体组分,使之达到分离的目的。
水洗石粗氯乙烯净化的第一步,除去了溶解度较大的氯化氢、乙醛及汞蒸气等,二氧化碳可以通过碱洗除去,通常用10%~15%的氢氧化钠溶液作吸收剂,粗氯乙烯气体经碱洗至中性
(4)盐酸脱吸
副产盐酸脱吸是将水洗脱酸塔产出的含有杂质的废酸进行脱吸,可以回收其中的氯化氢,并返回前部继续生产氯乙烯。
由浓酸槽来的31%以上的浓盐酸进入脱吸塔顶部,在塔内与经再沸器加热而沸腾上升的气液混合物充分接触,进行传质、传热,利用水蒸气冷凝时释放出的冷凝热将浓盐酸中的氯化氢气体脱吸出来,直至达到沸腾状态平衡为止。
塔顶脱吸出来的氯化氢气体经冷却使温度降低至-5~-10℃、除去水分和酸雾后,其纯度可达%以上,送往氯乙烯合成前部;
塔底排出的稀酸经冷却后送往水洗塔,作为水洗剂循环使用。
氯乙烯合成的主要设备
(1)酸雾过滤器
根据气体处理量的大小,酸雾过滤器有单筒式和多筒式两种结构形式。
多筒式结构如图3-1所示。
为了防止盐酸腐蚀,设备筒体、花板、滤筒可采用钢衬胶或硬聚氯乙烯制作。
过滤器的每个筒可包扎硅油玻璃棉,厚度35mm左右,总的过滤面积为8m
这样的过