钢中氢氮氧的来源及其控制对策Word文件下载.docx
《钢中氢氮氧的来源及其控制对策Word文件下载.docx》由会员分享,可在线阅读,更多相关《钢中氢氮氧的来源及其控制对策Word文件下载.docx(13页珍藏版)》请在冰豆网上搜索。
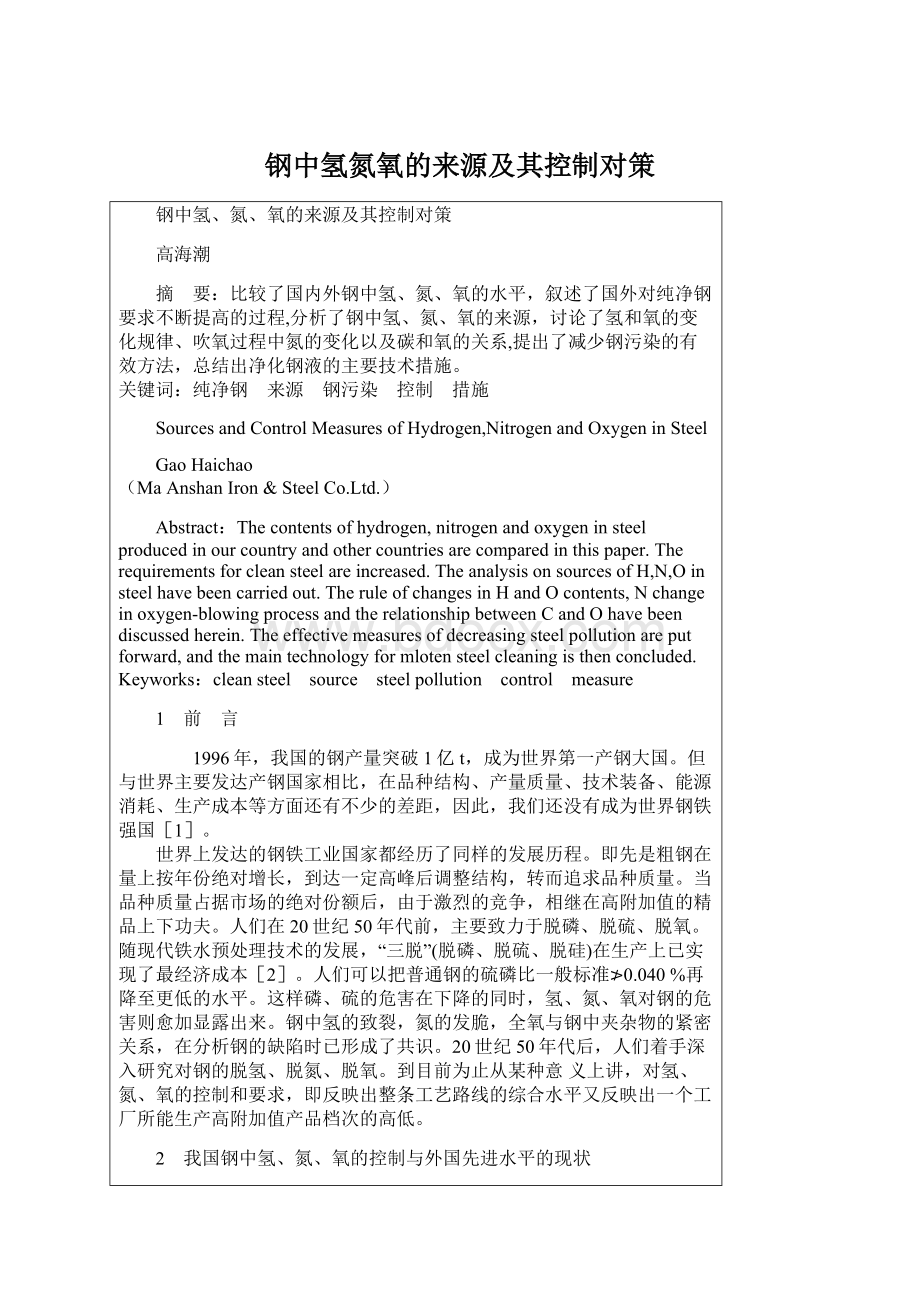
到目前为止从某种意义上讲,对氢、氮、氧的控制和要求,即反映出整条工艺路线的综合水平又反映出一个工厂所能生产高附加值产品档次的高低。
2 我国钢中氢、氮、氧的控制与外国先进水平的现状
对钢中氢、氮、氧要求,我国已有一些部门和行业标准,也包括企业内控标准,在一些特殊用途的钢上做出了规定。
如马钢快速客车轮钢中含氢(w)≤2×
10-6,重载货车轮钢中含氢(w)≤3.5×
10-6;
特钢企业生产的轴承钢对全氧提出明确的要求。
但在我国的国家标准(GB)中,除了众所周知的对优质碳素结构钢提出过钢中含氮的(w)≯80×
10-6以外,到目前为止,根据已有的资料,还没有见到将钢中氢、氮、氧作为有害元素控制的新标准发布或颁布。
我国有炉外精炼装置,经真空处理的钢不足钢产量的1/10。
以4大钢铁企业为例。
由于各家产品不同,工艺不同,精炼装置的不同,氢、氮、氧波动幅度较大。
即便以我国先进的拥有真空处理装备的炼钢厂与国外相比,在这方面仍有较大差距(见表1、表2)。
表1 我国钢中氢、氮、氧控制的先进水平及现状(w) ×
10-6
单位
[H]
[N]
T[O]
宝钢
0.7~1.5
10~27
12~28
武钢
≤2
≤25
43~75
太钢
1.5~3.3
25~55
25~33
马钢
1.5~3.5
40~50
22~38
表2 国外钢中氢、氮、氧控制的先进水平及现状(w) ×
品 种
车轮轮箍
30~40
≤15
重轨
<20
耐蚀结构钢
≤1.6
10~40
≤30
超低碳薄板
≤40
10~30
(D≤40μm)
优硬线材
40~60
20~30
(D≤20μm)
汽车钢板
≤20
中厚钢板
<1.5
合金钢棒材
<2
10~20
≤10
管线钢
≤35
冷墩钢
<30
表1、表2是我们收集到的资料,以及对国内外产品的检验报告,经整理列出的一些代表钢种,仅供参考。
3 结净钢或纯净钢的出现及发展
中国的钢铁市场是国际市场的一部分。
中国钢铁企业不能生产的或实物质量上尚存不足的产品,还得从国外大量进口,这个量每年仍有1000~1500万t。
要实现从量变到质变,值得一提的是国外生产的所谓“洁净钢”(Clean-steel)或“纯净钢”(Purity-steel),在对钢的纯净度上出现了质的飞跃。
通常这种钢是指[S]、[P]、[H]、[N]、T[O]含量(w)总和≯100×
10-6。
当然还有一种观点就是还得强调夹杂物的形态与尺寸。
对不同的钢号有不同的要求,比如滚珠轴承钢,要求夹杂物D<15μm,轮胎钢帘线要求夹杂物D<10μm。
除此之外,随炼钢技术的不断提高,超纯净钢的概念也出现在世界冶金的论坛上[3]。
德国预测:
钢水中可能达到的元素含量为(w)/×
10-6:
[C]≤20、[P]≤15、[S]≤5、[N]≤15、T[O]≤10、[H]≤0.7,总含量≤65.7×
日本报告:
到2000年,在批量生产的超纯净钢中,上述几种有害元素的含量可控制在(w)/×
10-6,[C]≤16、[P]≤12、[S]≤4、[N]≤14、T[O]≤5、[H]≤0.5,总含量≤51.5×
10-6(见图1、图2)。
图1 日本商业生产纯净钢[C]、[P]、[S]的计划
图2 日本商业生产纯净钢[H]、[N]、[O]的计划
4 影响钢中氢、氮、氧的因素与其控制
4.1 钢中氢、氮、氧的来源
在常压下进行钢的冶炼,气体除铁水中已溶解的外,还可以通过各种原辅料及炉气进入钢液。
当进入钢中的气体量超过冶炼过程脱碳沸腾的脱气量时,钢中气体的含量就增加[4]。
各种不同的炼钢炉,终点钢水中都含有一定量的氢、氮、氧,实测和统计情况见表3。
表3 三种炼钢炉终点钢水中[H]、[N]、[O]的含量(w) ×
冶炼方法
[O]
平炉
3~8
(C=0.10%)400~600
电炉
4~7
70~140
造还原渣<100
转炉
3~5
20~40
(C=0.10%)300~500
4.1.1 氢的来源
氢气在炉气中的分压力很低,大气中氢的分压力为0.053Pa。
因此钢中的氢主要由炉气中的水蒸汽的分压力来决定的(见图3)。
氢进入钢液的主要途径是:
通过废钢表面的铁锈(XFeO.rFe3O4.2H2O);
铁合金中的氢气;
增碳剂、脱氧剂、复盖剂、保温剂、造渣剂(Ca(OH)2)、沥青和焦油中的水份;
未烤干的钢包、中间包、中注管、汤道;
钢锭模的喷涂料;
结晶器渗水以及大气中的水份与钢水或炉渣作用而进入钢中。
图3 冶炼时钢液中氢和氧的变化规律
4.1.2 氮的来源
氮气在炉气中的分压力很高,大气中氮的分压力大体保持在7.8×
104Pa。
因此钢中的氮主要是钢水裸露过程中吸入并溶解的。
电炉炼钢,包括二次精炼的电弧加热,加速了气体的解离,故[N]含量偏高;
平炉治炼时间长增加了氮含量;
转炉复吹控制不当,氮氩切换不及时也会增加氮的含量(见图4);
铁合金、废钢铁和渣料中的氮也会随炉料带入钢水。
图4 全程吹氧时钢中含氮量的变化
1.氮流量0.25Nm3/min.t终点w(C)-0.065%;
2.氮流量0.2Nm3/min.t终点w(C)-0.037%;
3.氮流量0.19Nm3/min.t终点w(C)-0.048%;
4.氮流量0.13Nm3/min.t终点w(C)-0.032%;
5.氮流量0.09Nm3/min.t终点w(C)-0.079%;
4.1.3 氧的来源
氧在各种炼钢炉冶炼终点时都以一定量存在于钢水中,氧是我们供给的这是不言而喻的。
因为炼钢过程首先是氧化过程,脱[P]、脱[S]、脱[Si]、脱[C]都需要向铁水供氧。
但随着炼钢过程的进行,尽管工艺操作千变万化,可是炼钢炉内熔池中钢液的[C]、[O]的关系却有着共同的规律性。
即随着[C]的逐步降低,[O]却在逐步增高,[C]和[O]有着相互对应的平衡关系。
(见图5)。
图5 吹炼终点时钢液中碳含量与氧含量之间的关系
1.氧气顶吹转炉(圆点) 2.平炉金属中氧含量范围
3.钢液中的碳-氧平衡线
4.2 控制氢、氮、氧的主要对策
4.2.1 在炼钢生产的全过程中,建立起洁净钢质的思想观念
我公司铁前生产的格局已定,以2500m3大高炉为首的新系统,拥有先进的料场、烧结,在2号大高炉建设时将进一步完善。
钢后的轧机,以H型钢、棒材、高线、中板、车轮组成先进轧机和优特产品的优势,潜力很大。
钢承铁启材,现在又是我公司的弱项,弱项就更应予以扶持、保护。
不断提高钢的内在质量,是我们开发各种新产品的基础。
所谓洁净钢的生产不要局限于狭义的概念,要有广义的思想。
不要眼睛只盯着某一道工序上,而应该在整个系统上下功夫。
传统的炼钢热力学原理至今未变,但动力学条件则在不断的创新。
人们在炼钢的工艺过程及设备上努力找出最佳的配合条件。
从现实情况看,不要认为洁净钢离我们还远,各个企业都可以因地制宜就现有的条件,通过严格的科学管理,按标准执行操作。
首先是预防为主,制定本单位洁净钢的生产目标,使产品实物质量提上新水平。
4.2.2 生产含氢、氮、氧较低的洁净钢,炉外精炼是关键
生产含氢、氮、氧较低的洁净钢,就我国钢铁企业的现状来看,应以炉外精炼为关键,增添或完善必要的设备。
对设备功能的选择,应保证最终所生产产品的质量要求。
从粗放型转至集约型的生产经营,在大型钢铁企业中,优化炼钢生产工艺流程,必须坚持“三位一体”的方针,走铁水预处理→顶底复吹转炉→带真空的炉外精炼→连铸之道路。
以我公司为例,尽快上马铁水预处理工程;
在三钢LF工位炉上增加VD工位;
淘汰一钢平炉建95t转炉,改造SKF炉与转炉匹配,用圆坯连铸机生产车轮轮箍用的坯料,都是提高钢质出高附加值产品乃至精品,必须解决的主要的问题。
4.2.3 炼钢生产防止污染的主要技术措施
(1)炼钢生产所用的铁水、废钢、各种造渣材料及辅料、铁合金同样需要“精料”。
铁水必须要经过预处理,入炉前必须扒渣,硫的含量应控制在100×
10-6以下。
废钢必须在料场经过分选、切割加工,严禁含有害元素的废钢入炉。
造渣材料如活性石灰等,要新鲜、干燥,出窑到入炉的时间要短;
辅料如碳粉等要不存堆、袋装化、定量周转。
铁合金的块度和烘烤温度必须达标。
氧气、氩气的纯度也必须绝对保证。
现代炼钢仍靠这些基本条件支撑,只不过是各家钢厂在管理上有很大的差别,而这些差别最终则反映在钢的内在质量上。
(2)钢水在熔池中的脱碳沸腾是消除污染关键环节之一,脱碳速度的快与慢,沸腾的强与弱有一个最佳点[5]。
当氩气资源满足要求时,顶底复吹转炉可由过去的前程底吹氮改为全程吹氩;
出钢时采用长寿的出钢口或快速更换出钢口技术,出钢口始终维护良好,做到不散流;
使用性能可靠的下渣检测技术和挡渣技术,尽可能使钢渣分离,阻止炼钢炉终点高氧化性炉渣进入钢包。
这些要求不属于高、难操作,但严格认真执行工艺规范操作后,可以减少钢水受到污染。
由图6我们可以看出,随钢包渣中(FeO)+(MnO)含量的增加,钢水中全氧的含量也增加。
图6 钢包渣中(FeO)%+(MnO)%对钢全氧的影响
(3)所有用于盛装钢水的普通钢包、精炼包及连铸中间包都必须清洁干燥,做到红热包时才能受钢水。
所有与钢水相接触的耐火材料必须性能稳定,抗侵蚀性能好。
要按标准采集相关数据,使之处于受控状态。
应为精炼炉提供优质钢水,而不要增加额外的负担,使钢水在精炼过程中的时间缩短。
如钢水升温时间长则会增加气体的含量,破了真空不出站反回去加热则更加重钢水的污染。
由于有了钢包炉的炉外精炼,使炼钢工艺发生了变化。
如采用无铝出钢技术[6],可以降低钢中[N]。
从图7中可以看出,因为粗炼钢水终点含氧高(w)500×
10-6~1000×
10-6,故先用SiFe、MnFe预脱氧,而暂不用Al深脱氧,这样钢水中的氧含量相对较高,使钢水与空气相接触时,因氮的传质常数降低,减弱钢水吸氮能力。
我公司实践表明:
在钢包内加Al块脱氧会增加氮的含量(见图8)。
图7 在1500℃时氧对铁中氮传质常数
图8 钢包加铝块与[N]的关系
(4)在连铸系统采用新技术使钢水的污染大大降低。
保护浇注技术已取得了显著成效。
中间包密封及中间包钢液面使用保护渣,长水口或浸入式水口浇注技术,有效地避免了钢水的吸气及二次氧化。
中间包钢水控流技术[7],消除了死区使夹杂物被过滤或大量上浮,这包括挡墙、挡坝、过滤器、吹氩搅拌等多种手段。
其中新近开发的阻流器(Turbostop)见图9,可降低钢中全氧的(w)为20%~30%。
在连铸结晶器上新近也开发了系列新技术[8]:
如钢水液面控制仪、电磁制动阀(EMBr)、新型FC结晶器(见图10),均能有效地防止夹杂物卷入钢水。
图9 中间包阻流器示意图
图10 FC结晶器
4.2.4 炼钢生产净化钢液的主要技术措施
(1)以企业产品大纲的质量要求而定
酌情选用性能可靠的炉外精炼设备,既要使功能充分发挥作用,又不要使功能过剩,以达到经济化净化钢水的目的,随着对钢质量的要求逐步增高,真空脱气是炉外精炼不可缺少的功能。
(2)向计算机控制的自动化炼钢技术迈进。
企业依据自身的原料条件,总结经验,开发适合于自己的软件包。
采用声纳、副枪等技术,提高终点命中率,把5大有害元素的含量控制在较低的水平。
优化炼钢工艺。
在复吹转炉的冶炼后期和精炼炉的出站前,采用增大供氩量,延长后搅拌时间的方法,有利于降低钢中的夹杂物,氩气的纯度越高,吹氩量越大,钢中[O]降的越低(见图11)。
图11 惰性气体中氧含量对钢液脱碳和脱氧的影响
(在P=0.15MPa时)
1.纯氩气;
2.含0.1%O2;
3.含1.0%O2
(3)采用顶渣改质技术,向钢包顶渣内加入炉渣改质剂。
比如美国VonValley钢厂,使用CaC2+CaO改质剂,使包内炉渣w(MnO+FeO)≤5%,其钢中全氧含量控制在(w)5×
10-6~15×
10-6之间。
在精炼炉采用复合脱氧剂,比如硅钡系合金取代部分铝进行脱氧,不仅可以深脱氧,还有利于夹杂物的排除。
(见图12)。
图12 脱氧合金含钡与夹杂物总量
(4)对钢液进行钙处理技术。
向钢水中加入钙,不仅使钢中[O]急剧降低(见图13)。
并且随加钙量增加钢中夹杂物数量减少,尺寸变小(见图14)。
使钢相对洁净度提高。
图13 加Ca对Al脱氧后[O%]的影响
图14 钙脱氧对夹杂物数量尺寸的影响(按DIN标准统计夹杂物的个数)
1.未加钙 2.加钙0.39kg/t 3.加钙1kg/t
4.加钙1.34kg/t 5.加钙1.78kg/t 6.加钙2kg/t
目前加Ca的方法仍以喂线方式最好,喂线的位置很重要。
即可以在钢包中喂线,也可以在中间包和结晶器中喂线,值得引起注意的是,喂线机的功率宜大些、包芯线的质量必须保证,必须由贯标审核过的厂家供货。
(5)真空处理参数的选择
提高钢包精炼炉的真空度(见图15)或适当延长真空时间(见图16),是净化钢液,去除[H]、[N]、[O]的主要手段。
图15 氢含量与真空度的关系
1.根据PH2计算的平衡氢溶解度
2.真空浇注 3.倒桶真空脱气处理
图16 VAD法去气时间与[H]含量的关系
在真空状态下,钢液的底吹氩创造了良好的动力学条件[10]。
当底吹氩和真空度相匹配时,可以最大限度地脱除钢中有害气体。
5 结 语
(1)文中论述了钢中氢、氮、氧的来源及其主要的控制对策。
其目的是引起现场冶金工程师的高度重视,在我国从钢铁大国走向钢铁强国的道路上加快我们的速度。
(2)企业开发和生产高附加值的钢铁产品,其技术核心在钢的结净度上。
钢水的洁净度将是产品质量竞争的焦点。
在这方面我们与世界发达国家相比差距较大,马钢与武钢和宝钢相比也有一定的差距。
(3)转换思想观念。
除过去常规的硫、磷必须严格控制以外,应建立起对氢、氮、氧的控制标准。
当务之急是强化对氢、氮、氧的检测手段,做好信息的收集、整理、研究、反馈工作,建立起洁净钢质的思想观念。
(4)提高钢水洁净度是一项系统工程,在这项工程中就现有的条件看,技术涵盖的难度小于管理涵盖的难度。
以炉外精炼为关键,优化整个炼钢工艺,必须坚持防污染与净化并重的方针,一手抓硬件、一手抓软件。
作者简介:
联系人:
高海潮,高级工程师