最新版数控车床零件加工及工艺设计毕业论文1Word文件下载.docx
《最新版数控车床零件加工及工艺设计毕业论文1Word文件下载.docx》由会员分享,可在线阅读,更多相关《最新版数控车床零件加工及工艺设计毕业论文1Word文件下载.docx(20页珍藏版)》请在冰豆网上搜索。
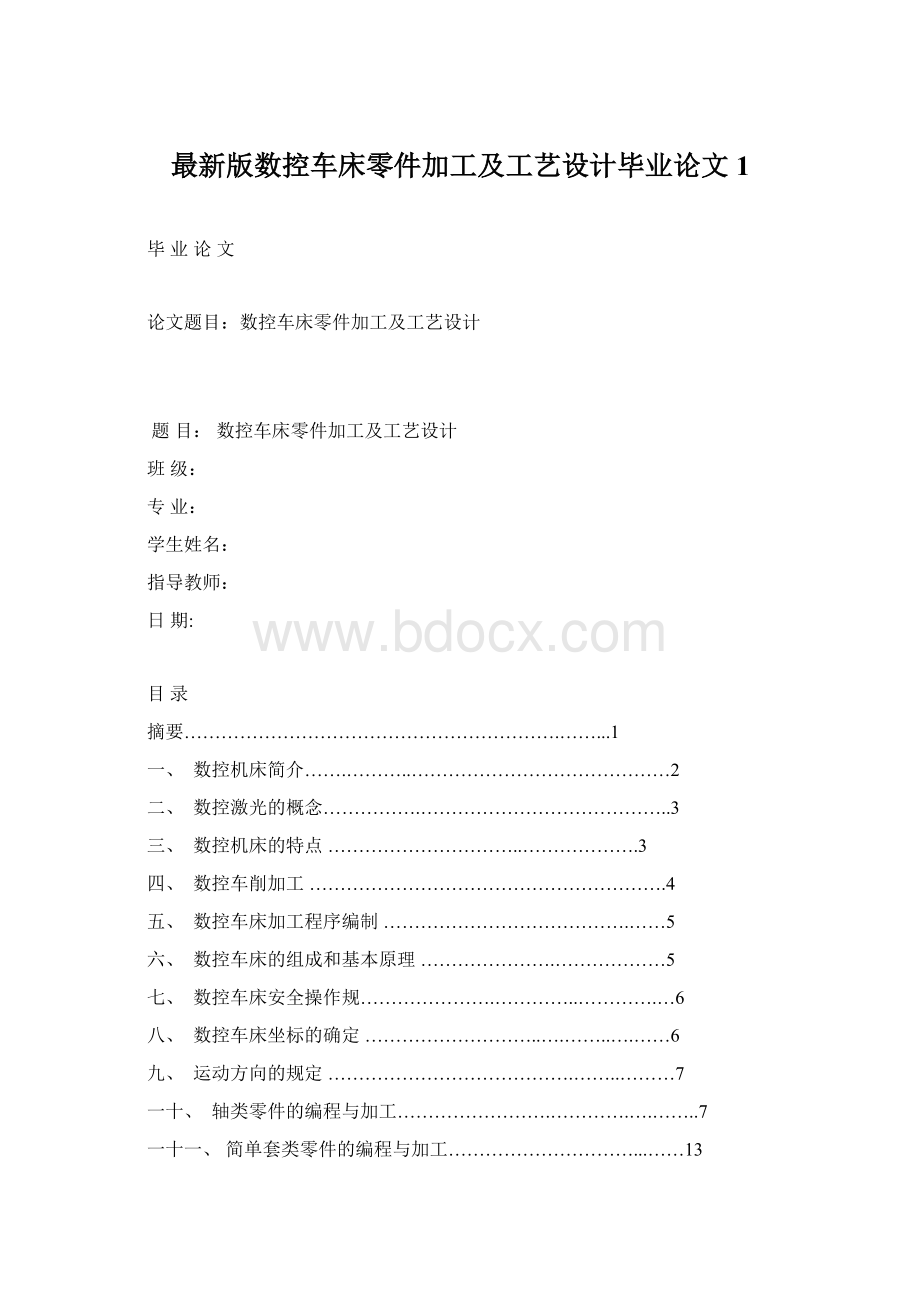
在各类金属切削机床中,车床是应用最广泛的一类,约占机床总数的50%。
车床既可用车刀对工件进行车削加工,又可用钻头、铰刀、丝锥和滚花刀进行钻孔、铰孔、攻螺纹和滚花等操作。
按工艺特点、布局形式和结构特性等的不同,车床可以分为卧式车床、落地车床、立式车床、转塔车床以及仿形车床等,其中大部分为卧式车床。
数控车削加工是现代制造技术的典型代表,在制造业的各个领域如航天、汽车、模具、精密机械、家用电器等各个行业有着日益广泛的应用,已成为这些行业不可或缺的加工手段。
为了子数控机床上加工出合格的零件,首先需根据零件图纸的精度和计算要求等,分析确定零件的工艺过程、工艺参数等内容,用规定的数控编程代码和格式编制出合适的数控加工程序。
编程必须注意具体的数控系统或机床,应该严格按机床编程手册中的规定进行程序编制。
但从数控加工内容的本质上讲,各数控系统的各项指令都是应实际加工工艺要求而设定的。
由于本人才疏学浅,缺乏知识和经验,在设计过程中难免出现不当之处,望各位给予指正并提出宝贵意见。
关键词:
车削加工刀具零件的工艺过程工艺参数程序编制
Onthelathe,usetherotationoftheworkpieceandtooloflineorcurvemovementtochangetheshapeandsizeofrough,meettherequirementsofdrawingsprocessingitinto.Turningonalatheisusedtheworkpiecerelativetothemethodofcuttingtoolrotationontheworkpiece.Cuttingismainlycomposedofworkpieceinturningratherthanthetoolprovided.Turningisthemostbasicandmostcommonmethodofcutting,occupiesaveryimportantplaceinproduction.TurnRotarysurfacesuitableforcutting,mostwithturningmethodforRotarysurfaceofworkpiecescanbeprocessed,suchasinnerandoutercylinderandinnerandoutertaper,surfacing,Groove,screwandRotaryformingsurface,thetoolismainlyusedtools.Inallkindsofmetal-cuttingmachinetools,latheisthemostwidelyusedcategory,percentofthetotalnumberofmachinetools50%.Turningthelathetoolavailableontheworkpiece,anddrills,reamers,tapsandknurlingcutterdrilling,reaming,tappingandrollingflower,andsoon.Technicalfeatures,layout,formsandstructurecharacteristicsofdifferentlathescanbedividedintomanufacturingtechnology,inallareasofmanufacturingindustriessuchasaerospace,automotive,molds,precisionmachinery,integralpartoftheseindustriesprocessingmeans.ToCNCprocessingqualifiedparts,firstaswellastheirprecisionandcalculationsrequiredunderpartdrawings,analysisoftechnologicalparametersofpartoftheprocess,content,NCprogrammingcodeandformatprovidedasuitableCNCmachiningprogram.Programmingmustpayattentiontospecificormachinetoolnumericalcontrolsystem,shouldbeconductedinstrictaccordancewiththeprovisionsofmachinetoolprogrammingmanualprogramming.ButinessenceofNCcontent,thenumericalcontrolsystemoftheinstructionsetistheactualprocessrequirements.SinceIprocess,精车切削速度vc=120mmin
然后利用公式vc=πdn1000技术主轴转速n(粗车直径D=60㎜,精车工件直径取平均值);
粗车500rmin精车1200rmin。
车螺纹时,参照式计算主轴转速n=320rmin
进给速度的选择查表选择粗车、精车每转进给量,再根据加工的实际情况确定粗车每转进给量为0.4㎜r,精车每转进给量为0.15㎜r,最后根据公式Vf=nf计算粗车、进给速度分别为200mmin和180mmin。
、
综合前面分析的各项内容,并将其填入表1-2所示的数控加工工艺卡片。
此表是编制加工程序的主要依据和操作人员配合数控程序进行数控加工的指导性文件。
主要内容包括:
工步顺序、工步内容、各工步所用的刀具及切削用量等。
表1-2数控加工工艺卡片
单位名称
产品名称或代号
零件名称
零件图号
典型轴
工序号
程序编号
夹具名称
使用设备
车间
001
三爪卡盘和活动顶尖
数控中心
工步号
工步内容
刀具号
刀具规格㎜
主轴转速rmm
进给速度
mmmin
背吃刀量
mm
备注
1
平端面
T02
25×
25
500
手动
2
钻中心孔
T01
5
950
3
粗车轮廓
200
自动
4
精车轮廓
T03
1200
180
0.25
5
粗车螺纹
320
960
0.4
6
精车螺纹
0.1
编制
XXX
审核
XXX
批准
年月日
共页
第页
8.编写程序
按该机床规定的指令代码和程序段格式,把加工零件的全部工艺过程编写成程序清单。
该工件的加工程序如下:
N0010G59X0Z195
N0020G90
N0030G92X70Z30
N0040M03S450
N0050N06T01
N0060G00X57Z1
N0070G01X57Z-170F80
N0080G00X58Z1
N0090G00X51Z1
N0100G01X51Z-113F80
N0110G00X52Z1
N0120G91
N0130G81P3
N0140G00X-5Z0
N0150G01X0Z-63F80
N0160G00X0Z63
N0170G80
N0180G81P2
N0190G00X-3Z0
N0200G01X0Z-25F80
N0210G00X0Z25
N0220G80
N0230G90
N0240G00X31Z-25
N0250G01X37Z-35F80
N0260G00X37Z1
N0270G00X23Z-72.5
N0280G00X26Z1
N0290G01X30Z-2F60
N0300G01X30Z-25F60
N0310G01X36Z-35F60
N0320G01X36Z-63F60
N0330G00X56Z-63
N0340G01X56Z-170F60
N0350G28
N0360G29
N0370M06T03
N0380M03S400
N0390G00X31Z-25
N0400G01X26Z-25F40
N0410G00X31Z-23
N0420G01X26Z-23F40
N0430G00X30Z-21
N0440G01X26Z-23F40
N0450G00X36Z-35
N0460G01X26Z-25F40
N0470G00X57Z-113
N0480G01X34.5Z-113F40
N0490G00X57Z-111
N0500G01X34.5Z-111F40
N0510G28
N0520G29
N0530M06T05
N0540G00X30Z2
N0550G91
N0560G33D30I27.8X0.1P3Q0
N0570G01X0Z1.5
N0580G33D30I27.8X0.1P3Q0
N0590G90
N0600G00X38Z-45
N0610G03X32Z-54I60K-54F40
N0620G02X42Z-69I80K-54F40
N0630G03X42Z-99I0K-84F40
N0640G03X36Z-108I64K-108F40
N0650G00X48Z-113
N0660G01X56Z-135.4F60
N0670G00X56Z-113
N0680G00X40Z-113
N0690G01X56Z-135.4F60
N0700G00X50Z-113
N0710G00X36Z-113
N0720G01X56Z-108F60
N0730G00X36Z-45
N0740G00X36Z-45
N0750M03S800
N0760G03X30Z-54I60K-54F40
N0770G03X40Z-69I80K-54F40
N0780G02X40Z-99I0K-84F40
N0790G03X34Z-108I64K-108F40
N0800G01X34Z-113F40
N0810G01X56Z-135.4F40
N0820G28
N0830G29
N0840M06T03
N0850M03S400
N0860G00X57Z-168
N0870G01X0Z-168F40
N0880G28
N0890G29
NO900M05
N0910M02
9.加工过程
1此工件要经两个过程加工完成,所以调头时重新确定工件原点,程序中编程原点要与工件原点相对应。
执行完成第一个程序后,工件调头执行另一个程序时需重新对两把刀的Z向原点,因为X向的原点在轴线上,无论工件大小都不会改变的,所以X方向不必再次对刀。
2输入程序。
3进行程序校验及加工轨迹仿真。
4自动加工。
5零件精度检测。
十一.简单套类零件的编程与加工
用数控车床加工如图所示的简单套类零件,工件长度为44㎜,外圆两个阶台尺寸分别为Φ45㎜,Φ65㎜,两端同轴度要求为0.04㎜,并有一个C1倒角。
内孔两个阶台尺寸分别为Φ30㎜,52㎜,内孔中两阶台端面垂直度要求为0.02㎜,有一个C5倒角和一个4㎜×
2㎜的内槽。
图2-1套类零件图
1.套类零件的分析:
图中所示为简单套类零件,该零件表面由两个阶台组成,其中多个直径尺寸与轴向尺寸有较高的尺寸精度和表面粗糙度要求,零件尺寸标注完整,符合数控加工尺寸标注要求;
轮廓描述清楚完整;
零件材料为45号钢,加工切削性能较好,无热处理和硬度要求。
套类零件是机械加工中常见的一种加工形式,套类零件哟哀求除尺寸、形状精度外,内孔一般作为配合和装配基准,孔的直径尺寸公差等级一般为IT7,精密轴套可取IT6,孔的形状精度应控制在孔径公差以内。
对于长度较长的轴套零件,除了圆度要求以外,还应注意内孔面的圆柱度,端面内孔轴线的圆跳动和垂直度,以及两端面的平行度等项要求。
2.套类零件的装夹方案
套类零件的内外圆、端面与基准轴线都有一定的形位精度要求,套类零件精基准可以选择外圆,但常以中心线及一个端面为精加工基准。
对不同结构的套类零件,不可能用一种工艺方案就可以保证其形位精度要求。
根据套类零件的结构特点,数控车加工中可采用三爪卡盘、四爪卡盘或花盘装夹,由于三爪卡盘四年定心精度存在误差,不适于同轴度要求高的工件的二次装夹。
对于能一次加工完成内外圆端面、倒角、切断的套类零件,可采用三爪卡盘装夹;
较大零件经常采用四爪啦盘或花盘装夹;
对于精加工零件一般可采用软卡爪装夹,也可以采用心轴上装夹;
对于较复杂的套类零件有时也采用专用夹具来装夹。
3.刀具的选择
加工套类零件外圆柱面的刀具选择与轴类零件相同。
加工内孔是套类零件的特征之一,根据内孔工艺要求,加工方法较多,常用的有钻孔、扩孔、镗孔、磨孔、拉孔、研磨孔等。
套类零件一般包括内外圆、锥面、圆弧、槽、孔、螺纹等结构。
根据加工需要,常用的刀具还有粗车镗孔车刀、精车镗孔车刀、内槽车刀、内螺纹车刀以及特殊形状的成型车刀等。
4.切削用量的选择
根据被加工表面质量要求、刀具材料和工件材料,参考切削用量手册或有关资料选取切削速度与每转进给量,然后计算主轴转速与进给速度(计算过程略),并将结果填入工序卡中。
背吃刀量的选择因粗、精加工而有所不同。
粗加工时,在工艺系统刚性和机床功率允许的情况下,尽可能取较大的背吃刀量,以减少进给次数;
精加工时,为保证零件表面粗糙度哟哀求,背吃刀量一般取0.1~0.4㎜较合适。
5.切削液的选择
套类零件在数控车加工比轴类零件有更大的难度,由于套类零件的特性使的切削液不易达到切削区域,切削区的温度较高,切削车刀的磨损也比较严重。
为了使工件减少加工变形,提高加工精度,应根据不同的工件材料,选择适合的切削液浇注位置。
6.填写加工刀具和工序卡
图所示简单套类零件的加工刀具和工艺卡
2-1-1
数控车床加工工序卡
机床型号
CKA6150
简单套类零件
机床编号
刀具表
量具表
刀补号
刀具名称
刀具参数
量具名称
规格(mmmin)
T01
01
93º
外圆车刀
D型刀片
游标卡尺
千分尺
0~1500.02
50~750.01
T02
02
91º
镗孔车刀
T型刀片
内径百分表
25~500.01
T08
08
钻头Φ28
工序
工艺内容
切削用量
加工性质
S(rmin)
F(mmr)
ap(mm)
车端面确定基准
800
0.2~0.3
自动
2
钻孔
300
手动
3
车Φ45㎜外圆
0.1~0.2
0.5~2
4
调头软爪夹Φ45外圆,车端面确定基准
1000
0.05~0.1
0.5~1.5
车Φ65㎜外圆
6
镗孔至尺寸
0.3~3
7.编写加工程序
根据图2-1所示零件,分析了工件内外圆及内槽的加工路线,并且确定了加工时的装夹方案,以及采用的刀具和切削用量,根据工艺过程按工序内容划分三个部分,并随影编程三个程序以完成加工。
1.机床钻孔、车Φ45㎜外圆的程序
O0001;
N1;
G99M03S800T0101;
G00X200.0Z150.0;
G00X68.0Z2.0;
M08;
G71U1.5R0.5;
G71P10Q20U0.5W0.05F0.15;
N10G00X0;
G01Z-16.0;
N20G00X68.0;
G99M03S1200T0101;
G00X200.0Z150.0;
G70P10Q20;
M05;
M30;
2.机床车Φ65㎜外圆的程序
00002;
N1;
G99M03S800T0101;
N10G00X65.0;
G01Z-28.0;
N20G00G40X68.0;
M09;
M00;
N2;
3.机床镗孔的程序
G99M03S800T0202;
G00X26.0Z2.0;
G71U1.5R0.5;
G71P10Q20U-0.3W0.05F0.15;
N10G00X52.0;
G01Z-20.0F0.1;
X40.0;
X30.0Z-25.0;
N20G00X26.0;
G00Z150M09;
G99M03S1200T0202;
十二.简单盘类零件的编程与加工
加工如图3-1所示的盘类零件,分析盘类零件图样上的技术要求,确定加工方法,加工工艺以及常用的刀具,编写数控程序加工。
要求加工后符合精度和公差要求。
该工件材料为45号钢,155㎜×
55㎜盘料。
图3-1盘类零件图
1.盘类零件分析
盘类是机械加工中常见的一种零件,端盖、齿轮、法兰盘等都是盘类零件。
盘类零件的加工从它的切削方式看,既可纵向切削也可横向切削,但要根据工件毛坯的形状、材料以及产品精度要求等确定切削方式,同时选取相应的刀具、切削用量、编程方法,以达到对产品精度的保障。
2.盘类工件的装夹
根据盘类零件的结构特点,数控车加工对于中、小型零件经常采用三爪卡盘装夹;
较大零件经常采用四爪卡盘或花盘装夹;
对于精加工零件一般可采用软卡爪装夹,也可以采用心轴装夹;
对于较复杂的盘类零件有时也采用专用夹具装夹。
确定工件装夹方案的基本原则:
1.保证工件装夹的稳定性和牢固可靠。
2.装夹能符合工件基准的设定,并保证工件的加工精度。
3.对于工件的装、卸较方便,能缩短工件加工的辅助时间。
盘类零件一般由高速钢和硬质合金车刀加工,对于一些特殊材料工件可采用立方氮化硼、聚晶
金刚石等刀具材料来进行加工,使刀具的加工性能和范围更加广泛。
刀具类型按结构类分,有整体式、焊接式和机械夹固式三种。
一般盘类零件由外圆、锥面、圆弧
槽、孔、螺纹等构成,所以刀具也从基本常见的外圆车刀、端面车刀、纵向槽刀、横向槽刀、镗孔车刀、螺纹车刀以及特殊形状的成型车刀中选择。
盘类零件的切削用量要根据工件材料、刀具强度、机床性能等因素来确定。
盘类零件的结构特点是最大外径较大,长度较