国内虚拟切削加工仿真技术新动向Word文档下载推荐.docx
《国内虚拟切削加工仿真技术新动向Word文档下载推荐.docx》由会员分享,可在线阅读,更多相关《国内虚拟切削加工仿真技术新动向Word文档下载推荐.docx(28页珍藏版)》请在冰豆网上搜索。
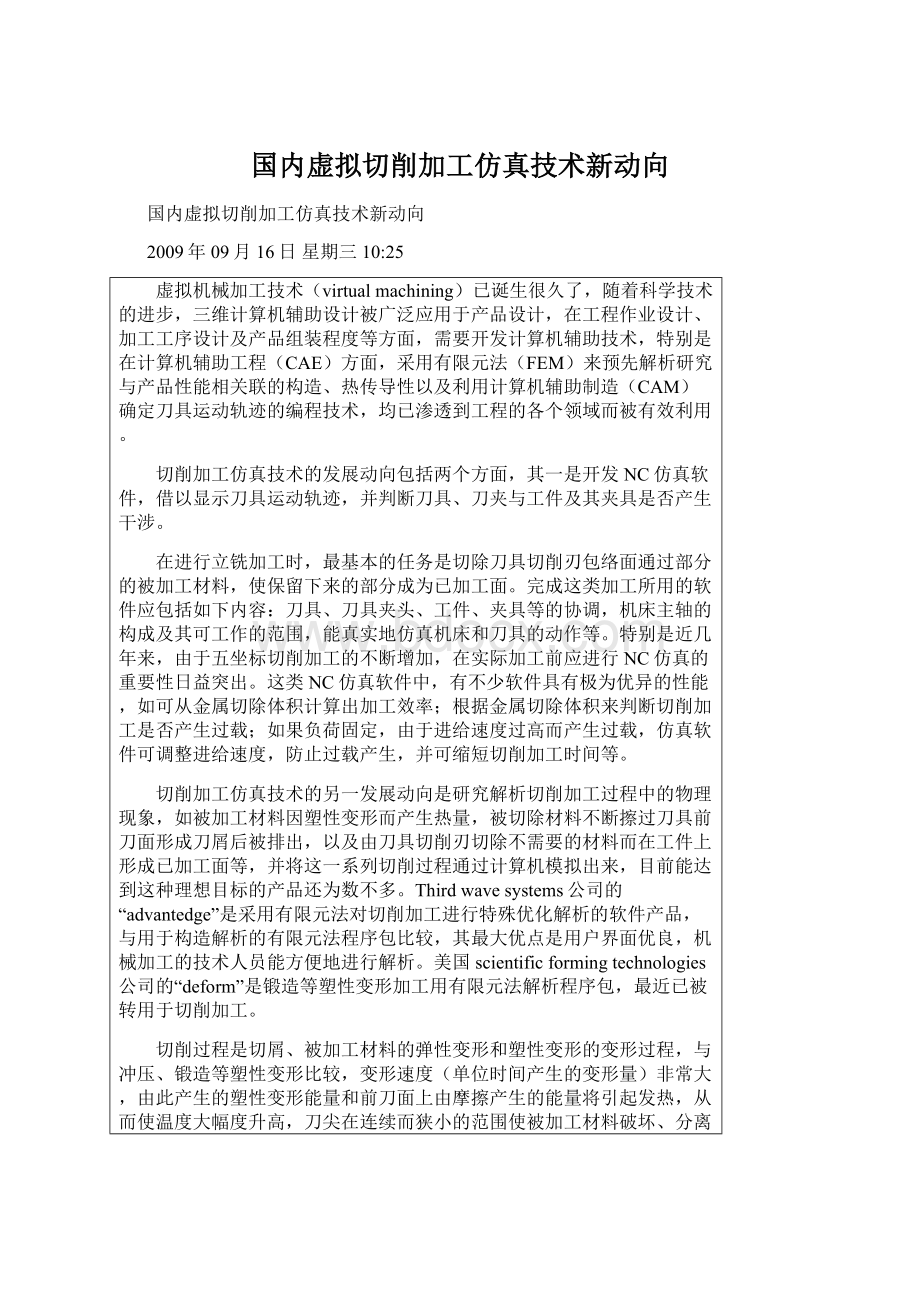
能否迅速普及的关键在于能否及时向用户提供所需的被加工材料的材料特性。
按需开发切削加工仿真技术软件
目前,许多科技人员正在进行生产工程中最基础的切削加工技术的研究,其中多数研究的目的是在弄清楚加工现象的同时,对加工过程进行预测。
如果这些研究内容实现了系统的计算机软件化,就意味着能形成一个切削仿真技术软件。
如东京农工大学机械学院的实验室就正在进行几种预测性的有关切削加工仿真技术软件的研究。
工艺流程和实用仿真采用了横向和纵向相匹配的研究体系,横向与产品设计到加工工序相对应;
在纵向上越往上,实用性越好,往下则不仅是实用性,还包括加工现象的解析和实现可视化。
1.刀具信息数据库和解析仿真技术并用的切削条件选择系统
在实际的切削过程中,不应照搬工具厂提供的推荐切削条件,而应根据机床、工具系统、工件装卡等具体情况,反复进行试切削来修正切削条件。
同时还应将过去加工中积累的行之有效的参考数据输入数据库,在有效利用这些数据的同时,借助解析方法使切削条件达到最佳化;
对于没有参考数据的新的切削加工,则应开发与此相关的切削条件选择系统。
该系统中把振动、加工精度、刀具升温、刀具寿命、残余应力等设定为解析内容,在解析的基础上,就能选择出最佳的刀具和调整切削条件。
本系统的数据大致分为三个部分:
刀具信息数据、工具系统组成、切削条件。
在切削条件中可积累有效的切削加工技术参数。
本文拟用图例表示平头立铣刀加工的最佳铣削效率和最佳化侧面的形状误差。
根据数据库选择所需刀具和刀夹,预测由立铣刀和刀夹的弯曲度及卡头和主轴锥度结合部分的旋转变化所导致的加工误差。
切削力的预测采用刀尖处的切削力乘以比切削抗力的模式。
这是一种最简便的的方法,但却得到了切削力波形与实测值一致的良好结果。
计算出每一瞬间由切削力引起的刀具挠曲量,将其和形成已加工面的切削刃位置的位移相连就能得到已加工面的形状。
与大规模有限元法的计算比较,计算时间是非常少的,输入刀具信息和切削条件信息,就能容易地仿真加工误差。
尽管数据库里已具有确实适应的切削加工条件,人们仍希望进一步减少加工误差,提高加工效率。
实例表明,用这种仿真和实现最佳化方式来修正切削条件是完全可能的。
2.立铣刀加工时的刀具温度
近年来,高速铣削已很普遍,由经验得知,它适用于小切深、大进给的铣削条件,而把握最佳条件却相当困难。
铣削加工与车削加工不同,前者属于断续切削,在加工过程中,刀具升温和冷却高速地反复进行。
由于热传导给刀具——切屑接触部分是断续进行的,必须根据这一特征来解析刀具温度的变化。
热传导量对预测精度影响很大,但不需要对切屑生成状态的变形和热解析相联系进行大规模计算,因此可快速获得解析结果。
切削速度、切深、进给的组合将影响最高温度,当加工效率一定时,提高进给速度,刀具温度就会降低,温度降低往往会使进给速度的提高达到极限,而提高进给速度,加工表面就会变得粗糙。
因此,如果能很好地平衡粗糙度和温度的关系,就能够选择到两者相互平衡的切削条件。
3.用有限元法进行切削过程的物理仿真
在用有限元法进行切削过程的物理仿真中,作为切削条件输入的内容包括:
切削速度、切削厚度、刀具前角、刀具后角、工件材料特性等。
对这些参数进行解析后,就能获得切削力、切屑形状、刀具和切屑上的温度分布、应力分布、形变分布、残余应力分布等物理特性输出结果。
这种仿真对特殊切削状态(如动态切削)也是适用的。
切削成波形表面的波形切除过程(waveremoval)和刀具边振动边切削的波形生成过程都显示出在切屑厚度变薄的过程中,剪切角变小、变形集中而产生大的变形。
在这样的动态切削过程中,剪切角发生变化,与此相对应的是切屑生成的变形范围大小也发生变化,因此切削力与刀尖的切削厚度不成正比。
由与刀尖切削厚度的变动相对应的剪切角度变化图可知,即使刀尖切削厚度相同,振幅增大时比振幅减小时的剪切角还大,利萨如(lissajou)图形下方呈凸半月形。
根据这样的解析结果,才能使现象的可视化及理解成为可能,从而开发出更为实用的高精度近似解析法。
另外,对于材料特性不同的复合金属材料的切削加工,以及象超声波振动切削那样的刀具在切削方向边振动边断续切削等加工,均可采用物理仿真技术进行解析。
由铁素体和珠光体以层状分布时的解析实例可知,由于各层分布的位置不同,切屑卷曲的状态有很大的差异。
如果在材料设计中能够有效应用物理仿真的解析结果,就有可实现不依靠断屑槽来进行切屑处理。
在超声波振动切削中切削力减小,是因为振动切削的振动频率大大高于刀具——被加工材料系统固有振动频率。
这种解析所获得的切削力是断续作用在刀具和切屑间的力,假设没有摩擦减小等其它因素的影响,这种切削力和通常的切削是一样的。
浅析虚拟制造中的虚拟切削加工
作者:
张雪莲潘铁强
来源:
万方数据
时间:
2008-9-910:
34:
03
随着全球化竞争的加剧,企业之间的竞争由过去的局部竞争演变成全球范围内的竞争;
同行业与跨行业之间的相互渗透、相互竞争也日益激烈。
为了适应快速变化的市场需求,企业必须以最快的上市速度T(time)、最优品质Q(quality)、最低成本c(cost)和最佳服务S(service)来满足不同顾客的需求,这给传统的制造技术带来严峻的挑战。
下载报告《管理企业信息》RSA企业内控,不再繁杂线上会议
资讯创造价值—IT导购专家HR/ERP等企业软件注册免费试用
引言
随着全球化竞争的加剧,企业之间的竞争由过去的局部竞争演变成全球范围内的竞争;
为了适应快速变化的市场需求,企业必须以最快的上市速度T(time)、最优品质Q(qualITy)、最低成本c(cost)和最佳服务S(service)来满足不同顾客的需求,这给传统的制造技术带来严峻的挑战。
随着计算机网络和虚拟现实等先进技术的出现,在20世纪90年代产生了一种新的制造概念和理论——虚拟制造VM(virtualmanufacturing),其全新的制造体系和模式已成为现代制造技术与系统发展的必然趋势。
虚拟制造利用信息技术,仿真技术,计算机技术对现实制造活动及控制过程进行全面仿真,以发现制造过程中产生可能出现的问题,在产品实际生产之前就采取预防措施,从而达到产品一次性制造成功。
由此看来,它可以降低成本,缩短产品开发周期;
还可以对想象中的制造活动进行仿真,而不消耗现实的资源和能量。
1国内外虚拟制造相关技术发展状况
由于虚拟制造技术具有诱人的应用前景,促使发达国家对其进行深入研究。
在美国已形成了由政府、产业界、大学组成的多层次、多方位的综合研究开发力量。
在欧洲,许多大学和研究机构通过相互间的合作并联合企业进行虚拟制造技术的研究工作,例如:
由Bath大学进行的AvirtualworkshopforDesignbyManufacturing研究,由Herriot-Watt大学进行的VirtualManufacturingGroup研究等。
在日本,已经形成了以大阪大学为中心的研究开发力量,主要进行虚拟制造系统的建模和仿真技术的研究,并开发出了虚拟工厂的构造环境VirtualWorks。
目前,虚拟制造技术已经在国外有所应用,典型的例子有波音777,其整机设计、部件测试、整机装配以及各种环境下的试飞均是在计算机上完成的,使其开发周期从过去8年时间缩短到5年。
又如PerotSystemTeam利用DenchRobotics开发的QUEST及IGRIP设计与实施一条生产线,在所有设备订货之前,对生产线的运动学、动力学、加工能力等各方面进行了分析与比较,使生产线的实施周期从传统的24个月缩短到9.5个月。
Chrycler公司与IBM合作开发的虚拟制造环境用于其新型车的研制,在样车生产之前,发现其定位系统的控制及其他许多设计缺陷,缩短了研制周期。
又如:
美国Boneing公司设计的一架VS-X虚拟飞机,可用头盔显示器和数据手套进行观察与控制,使飞机设计人员身临其境地观察飞机设计的结果,并对其外观、内部结构及使用性能进行考察;
日本MatsushITa公司开发的虚拟厨房设备制造系统,允许消费者在购买商品前,在虚拟的厨房环境中体验不同设备的功能,按自己的喜好评价、选择和重组这些设备,他们的选择将被存储并通过网络送至生产部门进行生产;
美国CoventrySchoolofArtandDesign开发的虚拟原型制作系统,设计者在设计的初始阶段能够在计算机中构造虚拟原型并对此原型进行评价。
国内的研究刚刚起步,主要集中在三个方面:
(1)产品虚拟设计技术:
主要包括虚拟产品开发平台、虚拟测试、虚拟装配以及机床、模具的虚拟设计实现等。
其中清华大学利用美国国家仪器公司的1.abview开发平台实现了锁相电路的虚拟,北京机械科学研究院采用C语言和OpenGL进行编程初步实现了立体停车库的虚拟现实下的参数化设计,可以直观地进行车库的布局、设计、分析和运动模拟。
(2)产品虚拟制造技术
主要包括材料热加工工艺模拟、加工过程仿真、板材成型模拟、模具制造仿真等。
北航与一汽用OPTRIS开发的板料成型软件已经基本能够模拟类似车门的中等复杂程度的汽车覆盖件和其他冲压成型件的冲压成型过程;
沈阳铸造研究所开发的电渣熔铸工艺模拟软件包ESRD3D已经应用于水轮发电机变曲面过流部件生产中。
其产品在刘家峡、李家峡、天生桥、太平役等7个电站中使用;
合肥工业大学研制的双刀架数控车床加工过程模拟软件已经在马鞍山钢铁股份有限公司车轮轮箍厂应用,使数控程序现场调试时间由几个班缩短到几小时,并保证一次试切成功;
北京机床研究所、机械科学研究院、东北大学、上海交大和长沙铁道学院等单位也研制出一些这方面的仿真软件。
(3)虚拟制造系统
主要包括虚拟制造技术的体系结构、技术支持、开发策略等。
其中提出了比较成熟的思想并可能实现的是由上海同济大学张曙教授提出的分散网络化生产系统和西安交通大学谢友柏院士组建的异地网络化研究中心。
采用切削仿真加工来代替或减少实际中的试切工作。
对切削加工有十分重要的意义。
切削仿真加工在虚拟制造中占有重要地位,它通过对机床一工件一刀具构成的工艺系统中的各种加工信息的有效预测与优化,为实现加工过程的智能化创造了有利条件。
同时它也是研究加工过程的重要手段。
2虚拟切削加工
(1)介绍
虚拟仿真加工是利用计算机来模拟实际的机械加工过程,是验证虚拟仿真加工可靠性和预测切削过程的有力工具,以减少工件的试切,提高生产效率。
从试切环境的模型特点来看,目前虚拟切削仿真加工主要包括几何仿真和物理仿真两个方面。
几何仿真不考虑切削参数、切削力及其它物理因素的影响,只仿真刀具一工件几何体的运动,以验证加工过程及工序的正确性,可减少或消除因程序错误而导致的机床损伤、夹具破坏或刀具折断、零件报废等问题;
同时可以减少从产品设计到制造的时间,降低生产成本。
切削过程的力学仿真属于物理仿真范畴,它通过仿真切削过程的动态力学特性来预测刀具变形、切削热、控制切削参数,从而达到优化切削过程的目的。
(2)主要问题
由于加工过程仿真还处于起步阶段,目前尚存在以下问题:
①仿真的加工形式少,研究范围窄。
在众多的切削加工种类与形式中,目前的仿真主要集中于铣、磨等部分,仿真也局限在很窄的范围内。
其原因是机械加工种类繁多,存在着车、铣、刨、磨、撞等多种加工形式;
另一方面加工理论复杂,不同的加工方法、刀具形状的加工模型有较大差别。
同时,目前的仿真系统大多进行几何仿真,即对刀位轨迹、工件与刀具的干涉校验等,有称之为NC校验(NCVerification)。
但在机加过程中,几何校验只是前提条件,更为重要的是切削力、切削温度及刀具磨损等在切削过程中起决定因素的各物理量。
②物理仿真过程都是考虑理想切削状态,与实际切削过程有较大差距。
在目前的仿真系统中预先设定了大量假设因素,如设定工艺系统刚性满足要求,无振动;
加工材料结构统一。
无硬点等缺陷;
刀具无磨损;
切削要素不发生变化等。
这种假定的理想状态不能将切削过程中的随机干扰如工件硬点造成的材质变化、振动造成的切深变化等因素考虑进去,使仿真系统不能真实地反映实际切削过程。
3虚拟切削加工系统的关键技术
虚拟加工环境建模:
采用面向对象的虚拟加工环境中的对象如机床设备、刀具、工件等进行建模,并对这些对象加以管理和调度使用。
虚拟加工过程建模:
它包括加工过程中的运动学建模、动力学建模及几何建模。
建立该模型关键是建立描述加工过程的集成仿真模型,包括机床---V件一工件系统的加工过程几何模型、物理仿真模型及加工误差分析模型。
虚拟产品建模:
虚拟制造的最终输出为数字产品,因此建立描述产品的模型十分关键。
虚拟产品模型包括具有特征制造造型和特征表示功能描述,制造产品的误差描述及产品表面特征描述。
4结束语
虚拟制造技术是一门新兴的先进制造技术,本文在阐述虚拟制造的概念、特点、现状的基础上,对在虚拟制造中具有重要地位的虚拟切削加工进行了介绍,分析了目前其主要存在的问题和虚拟切削加工系统的关键技术。
可以看出,尽管近年来国内外取得了一定的研究成果,但还有许多难题需要进行进一步深入的研究,特别是切削仿真加工中的物理仿真和建模等的研究和开发。
金属切削刀具虚拟设计方法初探
(时间:
2007-10-168:
50:
44
中华机床网)
0引言
现代金属切削加工技术正朝着高速度、高效率、高精度、低成本、节约资源、绿色环保等方向发展。
而传统的刀具开发过程需要经历材料研制→刀具设计→制造成型→切削试验→反馈修改→投入生产等多个环节,开发周期很长,已难以满足现代切削加工技术发展的要求。
近年来,出现了一门基于现代数学、力学等多学科理论、借助于计算机技术及先进算法的新型技术——虚拟设计技术。
应用该技术可对许多工程问题进行数值模拟,从而可加快产品的设计速度,提高设计精度及可靠性。
虚拟设计技术也可应用于金属切削刀具的研究开发中。
通过将材料性能参数输入计算机、建立有限元模型、加载、计算等步骤,即可逼真地模拟出整个切削过程,并对刀具几何参数进行优化设计。
应用该技术不仅可大大缩短刀具产品的设计开发周期,而且可提高设计的成功率和可靠性。
数值模拟技术是虚拟设计的核心技术,而数值模拟技术采用的主要分析方法为有限单元法。
近年来,有限元分析技术在计算机技术发展的推动下也不断发展,开发出了许多优秀的有限元分析软件,有力促进了虚拟设计技术的推广应用。
本研究应用国际通用的大型有限元软件ANSYS,成功模拟出了金属切削过程中刀具所受应力的变化及剪切角的形成过程,并以刀具前角为变量进行了一系列计算,验证了刀具前角与剪切角之间的变化关系。
在切削过程中,影响上述变化过程的因素较多,不仅取决于刀具几何参数、切削用量等,而且与工件材料性能密切相关。
在数值模拟过程中,不仅要考虑材料非线性、几何非线性和状态非线性,而且对解算器的选择及载荷步的控制也有严格要求。
ANSYS软件强大的非线性处理功能可为切削过程的数值模拟提供强有力的帮助。
1建模与计算
1.有限元建模
建立正确的有限元模型是实现数值模拟的关键。
结合金属切削的实际情况,建模时应重点考虑以下几个问题:
图1两种屈服准则的屈服轨迹比较
a.建立合理的材料模型是模拟切削过程的首要条件。
考虑到刀具材料硬度远大于工件材料硬度,建模时可将刀具视为弹性体,将工件建成为弹塑性模型。
在整个切削过程中,材料的变化是非线性的,因此需要确定材料的屈服准则、流动准则及强化准则。
在复杂应力状态下,连续体进入屈服状态的判断标准通常采用Tresca屈服准则和VonMises屈服准则。
Tresca屈服准则认为:
变形体内的最大剪应力达到某一临界值时即进入屈服状态。
而VonMises屈服准则认为:
当变形体内单位体积的形状改变弹性能或单位体积的弹性形变能达到某一极限值时,变形体即进入屈服状态。
由于Tresca屈服准则中未反映出中间主应力σ2对屈服准则的影响,因此它在数学上和几何上都是不连续的;
而VonMises屈服准则的几何图形在σ1-σ2应力平面中是一个外接于Tresca六角形的椭圆,这就消除了屈服轨迹上的角点,解决了数学上的不连续问题。
两种屈服准则的屈服轨迹比较如图1所示。
对于大多数金属材料,VonMises屈服准则与实验数据更为吻合,故本研究建模时选择VonMises屈服准则作为材料是否进入屈服状态的判定标准。
材料在热软化过程中将出现流动性,单个塑性应变分量εplx、εply的发展方向可通过流动准则来描述,其表达式为
(1)
式中:
εpl——材料的塑性应变
λ——塑性增量系数
Q——决定材料应变方向的应力函数
随着塑性应变的发展,屈服准则可用等向强化和随动强化两种强化准则来描述,本研究选用了多线性等向强化准则(MISO),它采用输入最多5个应力—应变数据点的方法来表示应力—应变曲线,适用于遵守VonMises屈服准则、按比例加载的情况以及大应变分析。
b.在切屑形成过程中,切屑中单元位移的改变和单元取向的改变会影响模型的总体刚度,这是一个包括大应变和大挠度的几何非线性问题,对于此类问题,可以通过激活大应变效应方程迭代出一个正确的解。
c.刀具前刀面与切屑之间以及刀具后刀面与已加工表面之间均存在摩擦。
为了正确描述摩擦模型,必须考虑整个过程的状态非线性接触问题,本研究选用了刚性体对柔性体的接触模式。
由于前刀面上存在粘结区和滑动区,且两区域的位置因切削条件不同而异,故可通过设置一个最大许可剪应力τmax来加以控制,即界面剪应力低于τmax的区域为粘结区,界面剪应力高于τmax的区域为滑动区。
为使数值模拟实验更具代表性,本研究选取硬质合金WC-TiC-TaC-Co作为刀具材料,其弹性模量E=550GPa,泊松比µ
=0.3;
选取A3钢作为工件材料,其弹性模量E=210GPa,泊松比µ
=0.3,极限应力σb=520MPa,屈服应力σs=320MPa,极限变形为20%。
图2直角自由切削有限元模型
图3剪切角形成图
图4刀具体有效应力分布图
图5刀具前刀面上各点的有效应力与其距刀尖距离的关系
图6Lee&
Shaffer剪切角理论
表对应不同刀具前角的剪切角
刀具前角
-15°
-10°
-5°
5°
10°
15°
剪切角
38°
41°
44°
48°
52°
56°
建立如图2所示的直角自由切削二维有限元模型。
在此模型中,将工件划分为1750个单元,将刀具划分为100个单元;
在工件底部约束X、Y向两个自由度,在工件左侧约束X向自由度;
刀具则约束Y向自由度。
2.加载与计算
在刀具右端施加水平向右的位移,刀具在给定速度和不同的位移边界条件下向右移动,形成切削过程。
然后通过计算软件的解算器进行综合计算。
通过ANSYS后处理器可观察到切削过程中剪切角的形成(如图3所示)和刀具所受有效应力的变化情况(如图4所示)。
由此,可借助于AutoCAD软件测
虚拟制造技术在切削加工中的应用
2007-5-12来源:
机电商情网编辑一部收藏此信息推荐给好友
利用虚拟制造技术对金属的切削加工过程进行了模拟仿真研究。
按照实际加工条件建立了切削模拟模型,按照国家标准建立的硬质合金可转位刀片的三维模型既考虑到真实的刀片几何形状,也考虑了其安装角度参数。
利用软件DEFORM3D对金属切削过程中的切屑流动状态及过程中的温度场和应力场进行了模拟加工并分析了模拟结果。
1、引言
随着计算机技术和信息技术的发展,虚拟制造技术在传统加工制造业中得到广泛应用。
应用虚拟制造技术可以缩短产品开发周期、降低成本、提高产品质量,从而提高产品的市场竞争力。
对车削过程进行虚拟仿真,可以合理选择参数工艺中的车削速度,背吃刀量及进给率;
对车刀几何结构(前角,后角和断屑槽等)进行优化设计。
目的在于减小切削力,提高金属切除效率并改善加工表面质量,优化加工工艺等。
当前,国内外针对车削过程模拟已开展了很多研究并取得了实际的意义。
例如:
日本HSasahara等应用弹塑性有限元法,在忽略温度和应变速率影响的前提下模拟了加工表面残余应力的分布[1]。
美国TAltan与意大利ECeretti合作开展了直角与斜角切削过程应力/温度场分布的二维和三维有限元分析[2~3],并将结果应用于改善实际加工参数。