份测验数控加工工艺与编程第三次作业Word文档下载推荐.docx
《份测验数控加工工艺与编程第三次作业Word文档下载推荐.docx》由会员分享,可在线阅读,更多相关《份测验数控加工工艺与编程第三次作业Word文档下载推荐.docx(13页珍藏版)》请在冰豆网上搜索。
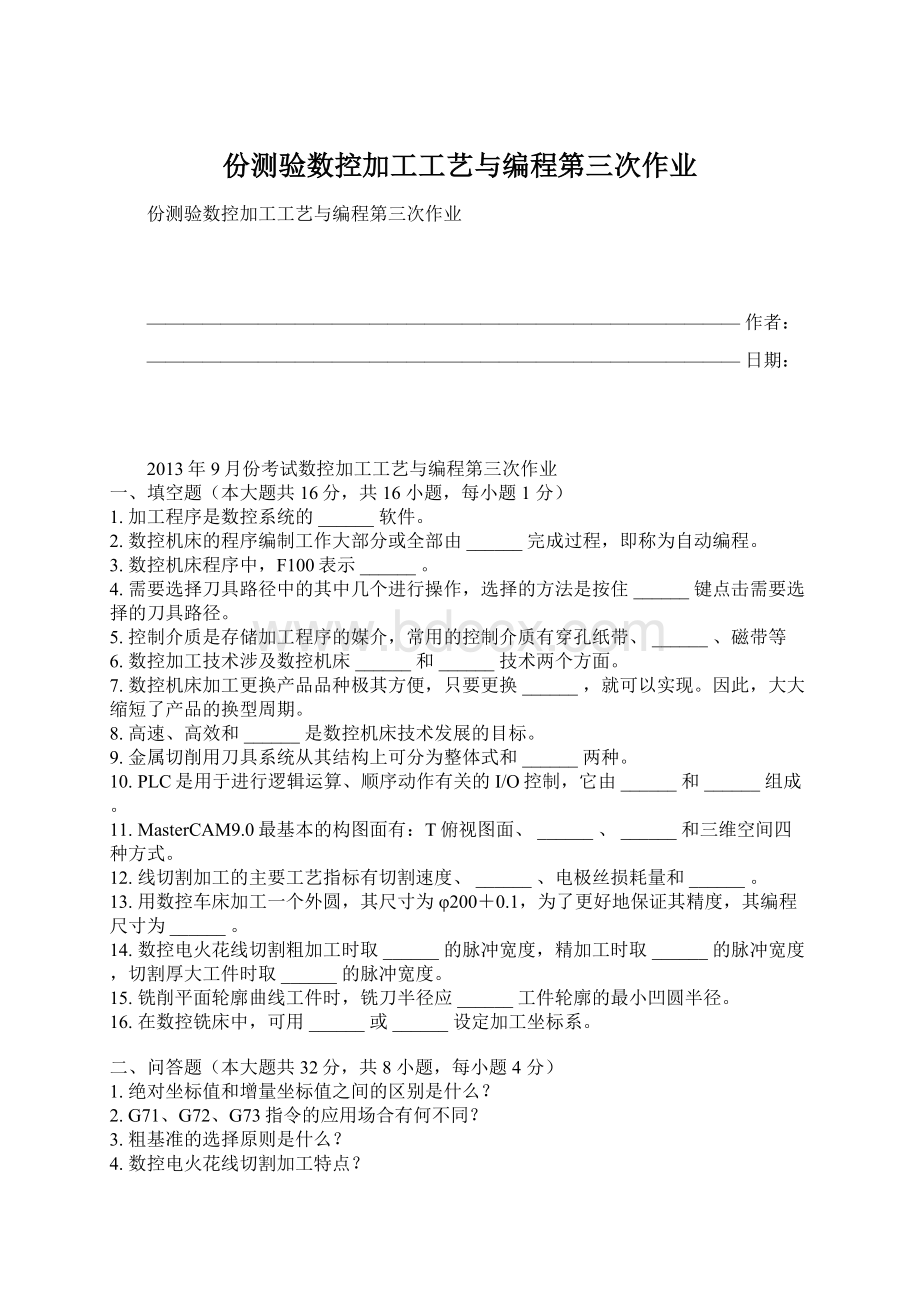
6.断丝原因分析及解决方法。
7.模态G代码和非模态G有何区别?
试举例说明。
8.什么是可变程序段格式?
三、程序设计题(本大题共52分,共4小题,每小题13分)
1.用FANUC-Oi系统指令编写下图所示零件的数控车削程序。
毛坯:
Φ52×
120棒料,材料:
45钢,刀具材料:
普通硬质合金,T01为粗车刀、T02为精车刀、T03为4毫米宽切槽刀。
注意:
粗加工吃刀深度选择应合理。
2.按下图编写精加工程序,T01为中心钻,T02为Ø
8钻头,T3为Ø
12立铣刀。
3.毛坯为70㎜×
70㎜×
18㎜板材,六面已粗加工过,要求数控铣出下图所示的槽,工件材料为45钢。
4.按下图编写加工程序,T01为偏刀,T02为切槽刀,T03为螺纹车刀。
答案:
一、填空题(16分,共16题,每小题1分)
1.
参考答案:
应用
解题方案:
评分标准:
2.
计算机
3.
进给速度为每分进给100mm
4.
Ctrl
结合实际的操作方法分析。
5.
磁盘
见程序编制及控制介质。
6.
加工工艺数控编程
从数控加工技术的特点考虑。
7.
加工程序
从数控机床的特点考虑。
8.
高精度
见数控加工技术。
9.
模块式
见数控镗铣加工用工具系统。
10.
硬件软件
见PLC、机床I/O(输入/输出)电路和装置。
11.
F前视图面S侧视图面
从空间视图的平面来考虑。
12.
表面粗糙度加工精度
见线切割加工的主要工艺指标。
13.
φ20.05
14.
较大较小较大
见影响线切割工艺指标的若干因素。
15.
小于
写出数学符号或文字给分
16.
G92G54-G59
从机床设定坐标系指令考虑。
二、问答题(32分,共8题,每小题4分)
绝对坐标是表示刀具(或机床)运动位置的坐标值是相对于固定的坐标原点给出的。
增量坐标:
增量坐标所表示的刀具(或机床)运动位置的坐标值是相对于前一位置的(相对于前一位置实际移动的距离),而不是相对于固定原点给出的。
其区别是:
绝对坐标是相对于原点确定;
增量坐标是相对于前一点位置确定。
71适用于外圆柱面需多次走刀才能完成的粗加工;
G72适于Z向余量小,X向余量大的棒料粗加工;
G73指令用于零件毛坯已基本成型的铸件或锻件的加工,铸件或锻件的形状与零件轮廓相接近,这时若仍使用G71或G72指令,则会产生许多无效切削而浪费加工时间。
1、如果必须保证工件上加工表面与不加工表面之间的相互位置精度要求,则应以不加工表面为粗基准。
如果工件上有多个不加工表面,则应以其中与加工表面位置精度要求较高的表面作为粗基准。
2、若必须首先保证工件上某重要表面加工余量均匀,则应选择该表面作为粗基准。
3、选作粗基准的表面应尽量平整光洁,不应有飞边、浇冒口等缺陷。
4、粗基准一般只使用一次。
粗基准的选择主要影响不加工表面与加工表面之间的相互位置精度,以及加工表面的余量分配。
特点是:
1、直接利用线状的电极丝作电极,缩短了生产准备周期。
2、可以加工用传统切削加工方法难以加工或无法加工的微细异形孔、窄缝和形状复杂的工件。
3、利用电蚀原理加工,电极丝与工件不直接接触,工件的变形很小,电极丝、夹具不需要太高的强度。
4、传统的车、铣、钻加工中,刀具硬度必须比工件硬度大,而数控电火花线切割机床的电极丝材料不必比工件材料硬,可以加工硬度很高或很脆,用一般切削加工方法难以加工和无法加工的材料。
在加工中作为刀具的电极丝无须刃磨,可节省辅助时间和刀具费用。
5、直接利用电、热能进行加工,可以方便地对影响加工精度的加工参数(如脉冲宽度、间隔、电流)进行调整,有利于加工精度的提高,便于实现加工过程的自动化控制。
6、电极丝是不断移动的,单位长度损耗少,特别是在慢走丝线切割加工时,电极丝一次性使用,故加工精度高(可达±
2μm)。
7、采用线切割加工冲模时,可实现凸、凹模一次加工成形。
见数控电火花线切割加工特点及应用。
1、在实际使用中,在不影响生产率(金属切削率)的前提下,应尽量选取较大的切削深度αp和较小的切削速度υ,使进给量f大小适中。
2、粗加工切削用量的选择
(1)切削深度的选择:
在机床有效功率允许的情况下,应尽可能选择较大的切削深度。
在切削表面有硬皮的铸、锻件或切削不锈钢等加工硬化比较严重的材料时,应可能使切削深度超过硬皮或硬化层深度。
(2)进给量的选择:
根据机床——夹具——刀具组成的工艺系统的刚性,尽可能选择较大的进给量。
(3)切削速度的选择:
根据工件材料和刀具材料确定切削速度,使之在已选定的切削深度和进给量的基础上能够达到规定的刀具耐用度。
粗加工的切削速度一般选中等或较低的数值。
3、精加工切削用量的选择
(1)切削深度的选择:
精加工通常选用较小的切削深度来保证工件的加工质量。
进给量大小主要依据表面粗糙度的要求选取,表面粗糙度Ra的值较小时,一般选取较小的进给量。
精加工的切削速度应避开积屑瘤形成的切削速度区,硬质合金刀具一般多采用较高的切削速度,高速钢刀具则采用较低的切削速度。
从切削用量的性质考虑,在切削参数中对刀具的寿命影响最大的是切削速度,影响最小的是吃刀深度。
粗加工时应尽快地切除多余的金属,同时还要保证规定的刀具耐用度;
精加工时首先应保证零件的加工精度和表面质量,同时也要考虑刀具耐用度和获得较高的生产效率。
断丝原因分析:
1、在没有超过电极丝使用寿命的情况下,断丝可分为三个阶段的断丝,若在刚开始加工阶段就断丝,则可能的原因有:
(1)加工电流过大。
(2)钼丝抖动厉害。
(3)工件表面有毛刺或氧化皮。
2、若在加工中间阶段断丝,则可能的原因有:
(1)电参数不当,电流过大。
(2)进给调节不当,开路短路频繁。
(3)工作液太脏。
(4)导电块未与钼丝接触或被拉出凹痕。
(5)切割厚件时,脉冲过小。
(6)丝筒转速太慢。
3、若在加工最后阶段出现断丝,则可能的原因有:
(1)工件材料变形,夹断钼丝。
(2)工件跌落,撞落钼丝。
解决方法:
在快走丝线切割加工中,要正确分析断丝原因,采取合理的解决办法。
在实际中往往采用如下方法:
(1)减少电极丝运动的换向次数,尽量消除钼丝抖动现象。
根据线切割加工的特点,钼丝在高速切割运动中需要不断换向,在换向的瞬间会造成钼丝松紧不一致,即钼丝各段的张力不均,使加工过程不稳定。
所以在上丝的时候,电极丝应尽可能上满储丝筒。
(2)钼丝导轮的制造和安装精度直接影响钼丝的工作寿命。
在安装和加工中应尽量减小导轮的跳动和摆动,以减小钼丝在加工中的振动,提高加工过程的稳定性。
(3)选用适当的切削速度。
在加工过程中,如切削速度(工件的进给速度)过大,被腐蚀的金属微粒不能及时排出,会使钼丝经常处于短路状态,造成加工过程的不稳定。
(4)保持电源电压的稳定和冷却液的清洁。
电源电压不稳定会使钼丝与工件两端的电压不稳定,从而造成击穿放电过程的不稳定。
冷却液如不定期更换会使其中的金属微粒成分比例变大,逐渐改变冷却液的性质而失去作用,引起断丝。
如果冷却液在循环流动中没有泡沫或泡沫很少、颜色发黑、有臭味,则要及时更换冷却液。
它们的区别是:
模态代码在连续多个程序段中有效,直到被相同级别的代码取代。
例:
N50G01X60.0Z-30F100;
N60X80.0;
程序中G01为模态指令,N60也用的是G01指令,两段指令相同,所以N60段程序可省略G01指令。
非模态代码:
只在本程序段有效。
从模态指令和非模态指令的定义考虑。
由顺序号、数据字和程序段结束组成。
各字后有地址,字的排列顺序要求不严格,数据的位数可多可少,不需要的字以及与上一程序段中相同的续效字可以不写。
N60G01X-155.0F200;
式中:
N:
程序段地址码(字),用于指令程序段号;
G:
指令动作方式的准备功能地址(G01为直线插补指令);
X:
坐标轴地址,其后面的数字表示刀具在该坐标移动的目标点坐标;
F:
进给量指令地址,其后面的数字表示进给量,F200表示进给量为200mm/min;
程序段末尾的“;
”为程序段结束符号(EOB)。
三、程序设计题(52分,共4题,每小题13分)
00001;
S500M03;
T0101;
(粗车外圆刀)
G00G90X52.0Z2.0;
G71U2R5;
G71P10Q20U1.0W0.1F60;
G00X100.0Z150.0;
M05;
M00;
S800M03;
T0202;
(精车外圆刀)
N10G00X0Z2.0;
G01Z0F60
G03X35.0Z-17.5R17.5;
G01Z-32.5;
X45.0Z-42.5;
G02X50.0Z-72.5R30.0
N20G01Z-100.0;
S300M03;
(切槽刀)
T0303;
G00X52.0Z-82.5;
G01X45.0F20
G00X52
Z-97.5
G01X1.0
G00X100.0;
Z150.0;
M30;
O0002;
T1M06;
(中心钻)
G90G54G0G40X-15.0Y-15.0S1200M03;
G43Z100H01;
M08;
G81Z-5.0R2.0F160;
M05;
M09;
T2M06;
(?
8钻头)
G43Z100H02;
G83Z-20.0R2.0Q3.0F80;
T3M06;
12立铣刀)
G90G54G0G40X15.0Y40.0S1200M03;
G43Z100H03;
Z2.0;
G01Z-10.0F80;
G01G41Y25.0D03F200;
G02I0J-10.0;
G01G40Y30.0;
G01G41X-15.0Y25.0D03;
G03X25.0Y-15.0R40.0;
G01Y-25.0;
X-25.0;
Y25.0;
X-15.0;
G01G40X0Y40.0;
G0Z100.0;
M30;
1、确定工艺方案及加工路线;
2、工步顺序;
3、确定切削用量;
4、确定工件坐标系和对刀点;
5、根据编程指令编写程序。
1、根据图样要求、毛坯及前道工序加工情况,确定工艺方案及加工路线
以已加工过的底面为定位基准,用通用台虎钳夹紧工件前后两侧面,台虎钳固定于铣床工作台上。
2、工步顺序
(1)铣刀先走两个圆轨迹,再用左刀具半径补偿加工50㎜×
50㎜四角倒圆的正方形。
(2)每次切深为2㎜,分两次加工完。
3、选择机床设备
根据零件图样要求,选用经济型数控铣床即可达到要求。
故选用XKN7125型数控立式铣床。
4、选择刀具
现采用φ10㎜的平底立铣刀,定义为T01,并把该刀具的直径输入刀具参数表中。
5、确定切削用量
切削用量的具体数值应根据该机床性能、相关的手册并结合实际经验确定,详见加工程序。
6、确定工件坐标系和对刀点在XOY平面内确定以工件中心为工件原点,Z方向以工件表面为工件原点,建立工件坐标系,如图3所示。
O1
T01M06
G90G54G00X0YOZ20
S800M03
X15Y0M08
G00Z2.0
G01Z-2.0F80
G03X15Y0I-15J0G01X20G03X20Y0I-20J0G41G01X25Y15D01
G03X15Y25I-10J0G01X-15?
G03X-25Y15I0J-10G01Y-15G03X-15Y-25I10J0G01X15G03X25Y-15I0J10G01Y0G40G01X15Y0
G00X15Y0
G03X-25Y15I0J-10G01Y-15G03X-1
(外圆车刀)
G0Z2.0;
X30.0M8;
G73U2.5R8;
G73P10Q11U1.0W0.1F100;
N10G0X0;
G1Z0;
X12.8;
X15.8Z-1.5;
Z-20.0;
X18.0;
X20.0Z-21.0;
X-28.0;
G02Z-40.0R10.0;
G1X25.0Z-55.0;
N11Z-60.0;
G0X150.0;
M0;
G50S2000;
G96S120;
G70P10Q11F0.1;
G0X100.0;
Z100.0;
G97G99G40;
S400M03;
G0Z-20.0;
X17.0;
G1X12.0F0.06;
G04X1.0;
G99G97G40;
S200M03;
(螺纹车刀)
X18.0M8;
G92X15.0Z-17.0F1.5;
X15.2;
X14.6;
X14.2;
X14.05;
G28U0W0;