高线工艺技术操作规程修订版已阅Word文件下载.docx
《高线工艺技术操作规程修订版已阅Word文件下载.docx》由会员分享,可在线阅读,更多相关《高线工艺技术操作规程修订版已阅Word文件下载.docx(94页珍藏版)》请在冰豆网上搜索。
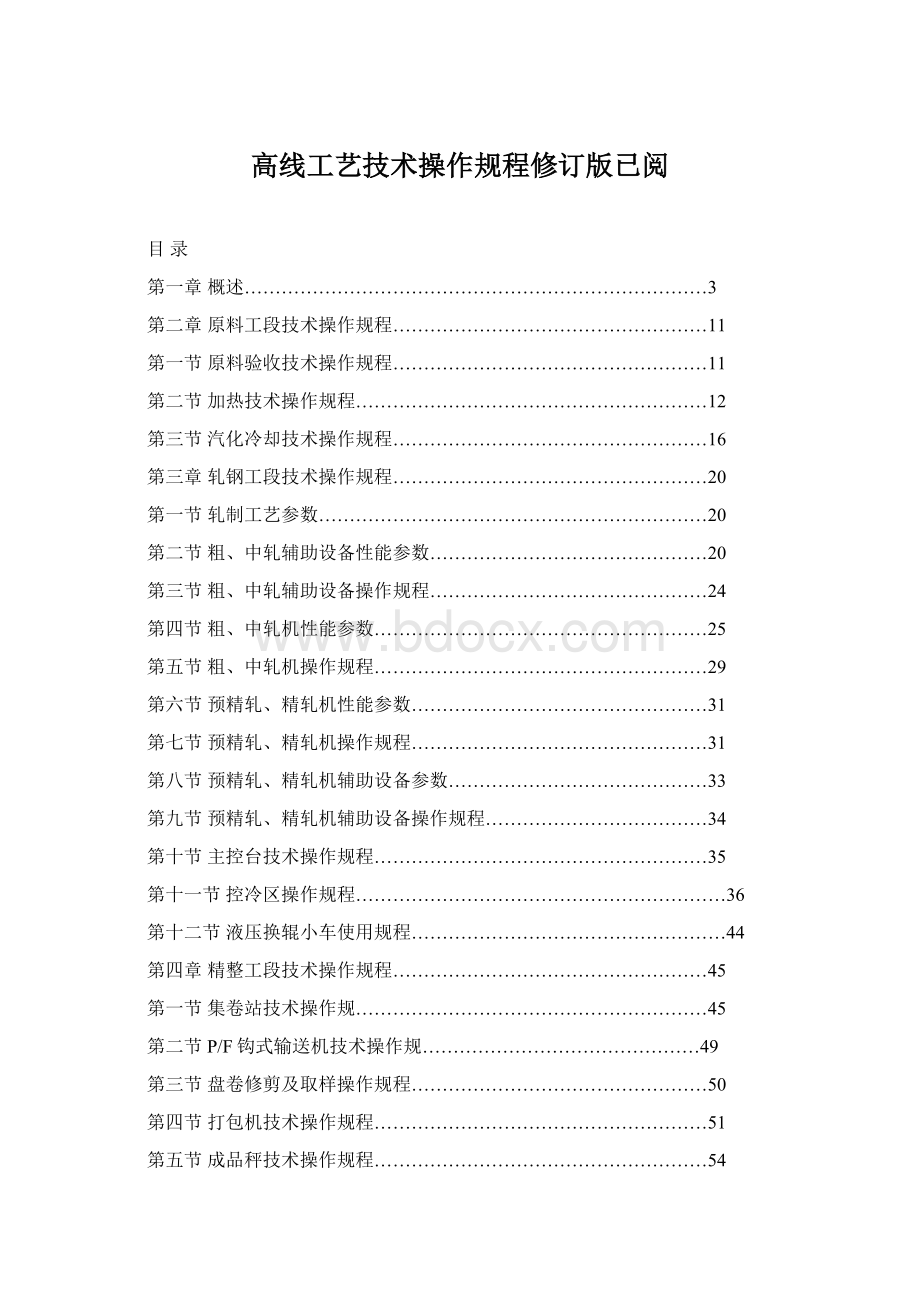
4mm/m总弯曲度不得大于0.4%D
D-公称直径mm
切斜度:
不得大于4.0%D最大不得大于20mm
表面质量执行荣钢关于连铸圆管坯的内控标准
连铸坯化学成分
化学成分符合中国国标(GB)和冶标(YB),其化学成分见下表。
序号
分类
典型钢种
成分
标准
C
Si
Mn
P
S
Ni
Cr
Cu
其他
1
奥氏体
不锈钢
S30210
≤0.15
≤1.00
≤2.00
≤0.035
≤0.030
8.00~10.00
17.00~1900
-
GB4356-2002
S30408
≤0.070
8.00~11.00
2
冷墩钢
ML20
0.17~0.24
≤0.07
0.20~0.50
GB6478-2001
ML40
0.37~0.45
≤0.20
0.30~0.60
3
弹簧钢**
65Mn
0.62~0.70
1.70~0.37
0.90~1.20
≤0.25
GB/T1222-84
4
轴承钢
GCr15
0.95~1.05
0.15~0.35
0.25~0.45
≤0.025
≤0.30
1.4~1.65
Mo≤0.10
YBT1-80
5
低合金钢
40Gr
0.37~0.44
0.17~0.37
0.5~0.8
<
0.035
0.3
0.8~1.1
Mo≤0.15
GB/T3077-88
6
焊条钢
H08
0.10
≤0.03
0.35~0.60
GB/T3429-2002
H08MnSi
0.11
0.4~0.7
1.20~1.50
7
碳素结构钢
Q195
0.06~0.12
0.12~0.30
0.25~0.50
≤0.04
GB/T701-1997
Q235
0.14~0.22
0.30~0.65
8
优质碳素钢
45
0.42~0.50
0.50~0.80
GB/T699-1999
60
0.57~0.65
80
0.77-0.85
0.17-0.37
0.50-0.80
9
优质高碳钢
72B
0.69~0.76
GB1222-84
82B
0.79~0.86
二、装炉温度冷坯:
环境温度
三、出炉温度:
900℃~1250℃
四、加热炉小时产量:
冷装140t/h.热装170t/h
五、轧制能力
粗轧机:
300~350t/h(全负荷运行)
精轧机
♦φ8.5-22mm线材使用无扭轧机:
150t/h(连续生产)
136.5t/h(间隙时间:
5s)
♦φ12.5-22mm线材使用2架或者4架无扭轧机
120t/h(连续生产)
111.2t/h(间隙时间:
六、最大终轧速度
一期(配置NTM轧机):
φ5.5-8mm的线材保证速度105m/s
二期(配置RSM轧机):
φ5.5-7.5mm的线材保证速度112m/s
φ5和φ8mm的线材保证速度105m/s
线材轧机设计速度:
最大120m/s
七、产品
产品规格
φ5.5-22mm
(φ20mm以上产品规格递增为1mm)
二期(增置RSM轧机):
φ5.0-25mm
最大产量-700,000吨/年
产品规格(mm)
弹簧钢
碳结构钢
总产量(t)
比例(%)
5.5
2000
2500
5000
10000
7500
34500
4.93%
6.0
6.5
1000
30000
108000
15.43%
7.0
8.0
4500
17000
118000
16.86%
10.0
25000
50000
115000
26.43%
12.0
60000
130000
18.57%
14.0
15000
12500
40000
5.71%
16.0
18.0
20.0
22.0
总计
-
1.7
1.4
3.4
9.6
25.7
31.4
25
100
尺寸公差
热轧圆盘条执行的尺寸、外形标准是GB/T14981—2009《热轧盘条尺寸、外形重量及允许偏差》。
相关内容如下:
公称直径/mm
允许偏差/mm
不圆度/mm
A级精度
B级精度
C级精度
φ5~10
±
0.25
0.15
≤0.48
≤0.40
≤0.24
φ10.5~15
0.4
0.2
≤0.64
≤0.32
φ15.5~25
0.5
0.35
≤0.8
≤0.56
≤0.4
车间内部要求
规格(mm)
尺寸公差(mm)
椭圆度(mm)
8~10
0.12
80%的尺寸公差
11~20
21~22
0.18
切头尾值
小于等于8.0mm规格的头尾剪切量按实际情况修剪,将缺陷部分剪净
线材的头尾修剪量
产品范围(mm)
拉丝
冷墩
Min
Max
头部
尾部
9.5
11
11.5
20
成材率
≥96%,其中:
氧化铁皮烧损为1%,轧废为1.4%。
切头尾,取样为1.6%。
八、生产工艺流程
九、轧线控制系统
轧线控制系统采用最新的计算机控制系统。
控制系统可以实现数据加工,坯料跟踪和分析,坯料的温度和温度控制,显示对话界面,闭环冷却控制和轧制过程的自动控制。
每个控制功能和操作台控制范围如下:
1号操作台加热炉入口
-热/冷坯料通过上料台架到入炉辊道。
-坯料单支入炉。
-坯料入炉前称重。
-剔除不符合轧制和加热要求的坯料。
-入炉前测量坯料长度。
2号操作台轧机入口
-出炉拉料辊辅助轧件咬入#1V轧机
-出炉拉料辊把不符合要求的坯料退回到加热炉。
-加热炉控制仪表,加热炉整体的控制。
3号操作台主控制室
-控制整个轧线从#1V轧机到吐丝机,冷却运输辊道,集卷筒。
主要控制功能包括:
-跟踪监控
-坯料从原料库到成品库的位置
-从原料库到成品库数据收集
-1V轧机前除鳞
-剪切长度控制
-水冷箱
-管理软件
-坯料清单
-盘卷清单
-轧机清单
-速度控制
-主要设备和辅助设备速度的设置
-联级速度控制
-张力控制
-粗轧机和一中轧机组的最低张力控制
-中轧机组,预精轧机组和无扭轧机的活套
-无扭轧机夹送辊张力控制
-废品检查
-粗轧机组
-中轧机组
-无扭轧机
-斯太尔摩运输线和集卷筒
-水箱和吐丝机之间的夹送辊
-头部的校正
-尾部速度控制
-温度控制
-无扭轧机入口
-无扭轧机中间冷却
-吐丝机
-斯太尔摩运输线
-控制冷却和自动调整
-尾部的制动
-尾部加速
-集卷筒
-线圈分配器
-立式卷取系统
-自动排序
4号操作台P&
F线
-P&
F线驱动控制
-跟踪监控P&
-故障显示
5号操作台压紧打捆机
-跟踪监控盘卷进入压紧机
6号操作台称重和标牌
-跟踪监控盘卷进入称重和打印装置
-标记打印
-输出重量
第二章加热工段技术操作规程
第一节原料验收技术操作规程
一、原料规格
端面:
Ф250㎜2
定尺:
6530mm、8000mm
二、原料验收
1、钢坯验收标准:
钢坯弯曲度:
每米小于4mm,全长不超过1%;
钢坯端部切斜度不大于边长的8%;
端部切扁度不大于宽度的10%;
2、按供料单位生产流动卡片、转移单查对实物,作到卡物相符。
发现问题及时与钢坯管理组联系,查清。
3、验收合格的钢坯及时在字头端用石笔描写炉号、盘号、钢种。
4、钢坯描好字头后,按炉号、规格成层、成排集中整齐堆放,归堆的钢坯同层字头朝向一致,上下层字头朝向相邻。
5、钢坯归堆后及时在卡片上注明钢坯堆放的区排号。
6、钢坯在钢坯跨结存时间超过两个月的,需用白色油漆重新描写字头(炉号、盘号、钢种)
7、红送钢坯经查对卡片,转移单,判定联确认无误后,必须按红送装炉要求即时装炉。
三、钢坯抛丸
技术参数:
钢丸丸粒直径:
φ1.5~φ2.5mm;
丸粒投射量:
0-200kg/min(单机);
每次需注入丸粒量:
1500-2000kg;
每班需添加丸粒量:
20-30kg;
V形辊速度:
2-10m/min;
操作规程:
1、除尘器水箱用水每班更换两次,接班及本班第4小时各更换一次。
2、抛丸过程中须经常观察料斗中丸粒量,不足时应及时添加。
3、根据被抛钢坯的抛丸效果,适当调节丸粒流量。
4、每班作业完毕,应清理提升机底部的丸粒,以免丸粒潮湿锈蚀结块。
5、班后应将除尘器泥浆排放干净。
四、钢坯修磨
1、所有的初轧坯必须上台精整,全长方向打蛇形检查;
连铸坯必须20%的打蛇形抽查,发现一支坯表面有缺陷时必须整炉、整批全部上台精整,缺陷超标的立即报废,进行隔离。
2、钢坯表面缺陷的清除深度不得大于钢坯公称尺寸的8%,同一截面相对表面同时清理时,两处清理深度之和不大于钢坯公称尺寸的8%,棱角处清理深度不应大于钢坯公称尺寸的8%。
3、钢坯缺陷清理处应圆滑,长:
宽:
深不得小于10:
6:
1。
4、发纹麻点深度0.5mm;
压痕、凹坑、凸包,实际尺寸算起1/4公差;
划线深度2mm;
深:
宽1的缺陷可不清理。
5、钢坯表面不允许有夹杂,裂纹、重皮、折叠、耳子。
6、研磨时研磨方向应与缺陷方向垂直,作到“横裂直磨,纵裂横磨”。
7、研磨钢坯时,应在清理范围内经常移动砂轮,修磨时用力不宜过猛,防止金属表面发兰。
8、未经抛丸的钢坯,应进行蛇形检查,发现缺陷,加强精整。
9、钢坯精整时,应按有关规定做好毛头标志。
精整时,抽根报废的钢坯应在端部用黄油漆打上:
“X”标记并单独存放,以防混乱。
开废品小票。
10、钢坯精整完毕,钢坯已分盘段号的,须按盘、按段集中堆放,作到同盘钢集中,同炉、同盘中同段节号的钢坯集中堆放。
11、认真作好各相关生产、工艺记录。
第二节加热炉技术操作规程
一、加热炉主要设备技术性能:
炉型:
侧进侧出蓄热步进梁式加热炉
有效尺寸:
L*B=36000*86000mm
钢坯断面规格:
250圆
加热钢种:
优碳钢、冷镦钢、焊条钢、弹簧钢、轴承钢、不锈钢
钢坯长度:
钢坯出炉温度:
970-1180℃
小时产量:
冷装碳素结构钢140t/h热装碳素结构钢180t/h(热装温度大于600度时)
燃料种类:
高炉煤气
步进梁驱动方式:
液压驱动
步进梁冷却方式:
汽化冷却
空气预热温度:
不小于1000度
煤气预热温度:
支撑梁:
3根动梁、4根固定梁(在均热段和第二加热段交接处动梁和静梁错位布置,以消除“黑印”)。
烧嘴配置:
均热段:
上:
4下:
第二加热段:
6下:
第一加热段:
炉内分为均热段、I加热段、II加热段和预热段四段。
步进梁机械组成:
平移框架,提升框架,提升平移滚轮装配,提升平移导向装配,提升平移辊道,提升平移液压钢,斜台面,行程检测装置.
步进梁出钢动作:
“上升”“前进”“下降”“后退”,步进轨迹为“矩形”
步进梁出钢的运动方式:
正循环,逆循环,踏步和停中位动作。
升降液压缸:
280/200*1050mm2个
平移液压缸:
220/160*420mm1个
工作压力:
16MPa
上料推钢机:
同步轴驱动四支推杆,将料从装料辊道上推上固定梁。
二、钢坯上料、装、出炉
1、上料钢坯标准:
钢坯规格:
250mm圆,连铸坯
每米小于15mm,全长不超过1%;
2、步进梁步距:
升降行程200mm,平移行程360mm。
步进周期:
最快40秒,更换钢质装炉间距5步,更换炉号装炉间距1步,交接班装炉间距2步。
3、流动卡片上所有记录完整才能收料。
钢坯在上料台架上钢坯端面整齐的一律朝西放置。
4、同一炉号的钢坯集中进炉。
5、查对计划、流动卡片和来料实物,确保炉号、根数正确。
6、钢坯入炉前要逐根测长、称重,入炉后钢坯在炉膛内对中。
7、钢坯不合格剔除时,应在钢坯上注明炉号、卡片号、钢种,同时在流动卡片上减掉剔除根数,并报当班调度。
8、电渣钢进炉时必须在卡片上填写子炉号进炉顺序。
9、为保证一火材连铸轴承钢的高温扩散时间,计划应排于换规格的头几个号,以充分利用间歇时间.
10、填写好毛头切除记录,并在钢坯出炉前报调度室。
11、同一规格的各种钢类正常情况下入炉顺序为“先低温钢,后高温钢;
先易脱碳钢,后其它钢”。
12、凡生产中换导卫、换辊、换眼时应装入2-3根试车料。
13、轧机或加热炉检修后,应待生产正常后才能装入易脱碳钢。
14、每个炉号出炉时的实际根数应和流动卡片核对,如不符,应暂停出钢,待查明原因处理后再出钢;
15、当出完一个大号(20支钢坯以上的),或若干个卡片号合计多于20支钢坯时,跑号工应将该生产流动卡片随同该卡片或最后一卡最后一根钢送到冷床,钢到人到。
小卡片号生产时应经常保持电话联系,及时核对出钢情况,防止混乱。
16、凡钢坯因各种原因轧废,跑号工应及时通知冷床,并在流动卡片上作好记录。
17、钢坯出炉温度参见《钢坯加热温度制度表》,坯料端面温差±
20℃,坯料长度方向温度偏差±
20℃,并应保证钢温西高东低。
18、红送钢坯入炉温度必须在300-600℃之间。
三、钢坯加热制度
1、坯料出炉温度
钢种
出炉温度(℃)
温度波动范围(℃)
980~1020
30
980~1050
1000~1050
1140~1180
螺纹钢
奥氏体不锈钢
1150~1250
铁素体不锈钢
2、坯料温差
头部到中部(前端):
+30℃最少2000mm(长度)
尾部到中部(尾端):
中心到表面:
<
30℃
3、故障降温制度:
停轧或故障停机时间降温表
停轧或故障停机时间
加热一段降温℃
加热二段降温℃
均热段降温℃
升温时间开轧前(分钟)
0.5~1小时
不降温
20~40
10~20
20~30
1~2小时
20~50
40~80
2~4小时
800℃保温
850℃保温
900~950℃保温
60~80
4~6小时
关闭烧嘴熄火
120~180
注:
停轧时间大于6小时或以上时加热一、二段烧嘴关闭熄火,均热段保留两个烧嘴保温
4、生产过程中应经常监视加热炉的工况:
炉内水梁冷却水水压须大于0.35Mpa,出口水温须小于55℃;
煤气压力大于8000Pa,助燃空气压力7Kpa;
助燃空气预热温度≥1000℃;
煤气预热温度≥1000℃;
炉区仪表用氮气压力大于0.4Mpa。
发现工况不对时应及时采取措施加以纠正。
5、排烟温度≤180C
6、排烟温度超过160C时应适当调整排烟阀门开口度。
7、加热时煤气、空气配比应合理。
煤气热值750X4.18KJ/Nm3(加热炉蓄热烧嘴可供燃烧最多掺20%转炉煤气的混合煤气,热值小于950X4.18KJ/Nm3的燃料,冷炉升温及烘炉阶段使用焦炉煤气),煤、空比为1:
8、炉膛压力控制正确,炉门处火苗不许外漏,也不许吸冷风。
一般控制在15至25Pa左右。
9、定期用测温仪抽测各炉号钢温,以掌握钢坯的实际加热情况,及时调整各区段温度制度。
10、加热制度以最终保证出钢温度为准,当轧制节奏较快,钢温跟不上时,可适当调整加热炉各区段的炉温,但根据钢质炉温最高不得超过1300℃。
轧制节奏再次降低时,应及时调整炉温。
加热过程中,炉温的调整应确保炉内各点钢温不大于规定的出钢温度。
11、出钢温度和钢坯颜色对照
温度℃
颜色特征
800
鲜红樱桃色
黄色
850
鲜红色
1100
鲜明黄色
900
黄红色
1200
黄白色
950
浅黄色
1300
亮而有点白色
四、停炉、吹扫、点火
1、停炉
1.1接调度通知后停炉,停炉时除第一组碳结钢外,其他钢种均不得存炉。
1.2停炉时先关闭所有烧嘴的煤气阀,并根据降温速度的要求调整空气阀的开度,停炉时间较长时还应关闭V1、V2阀,并放散煤气管网中的煤气。
1.3当炉温降到300℃以下时可以停助燃风机。
1.4降温停冷却水时