大专自动化专业毕业设计S7200PLC薄钢板自动剪切控制系统Word文件下载.docx
《大专自动化专业毕业设计S7200PLC薄钢板自动剪切控制系统Word文件下载.docx》由会员分享,可在线阅读,更多相关《大专自动化专业毕业设计S7200PLC薄钢板自动剪切控制系统Word文件下载.docx(37页珍藏版)》请在冰豆网上搜索。
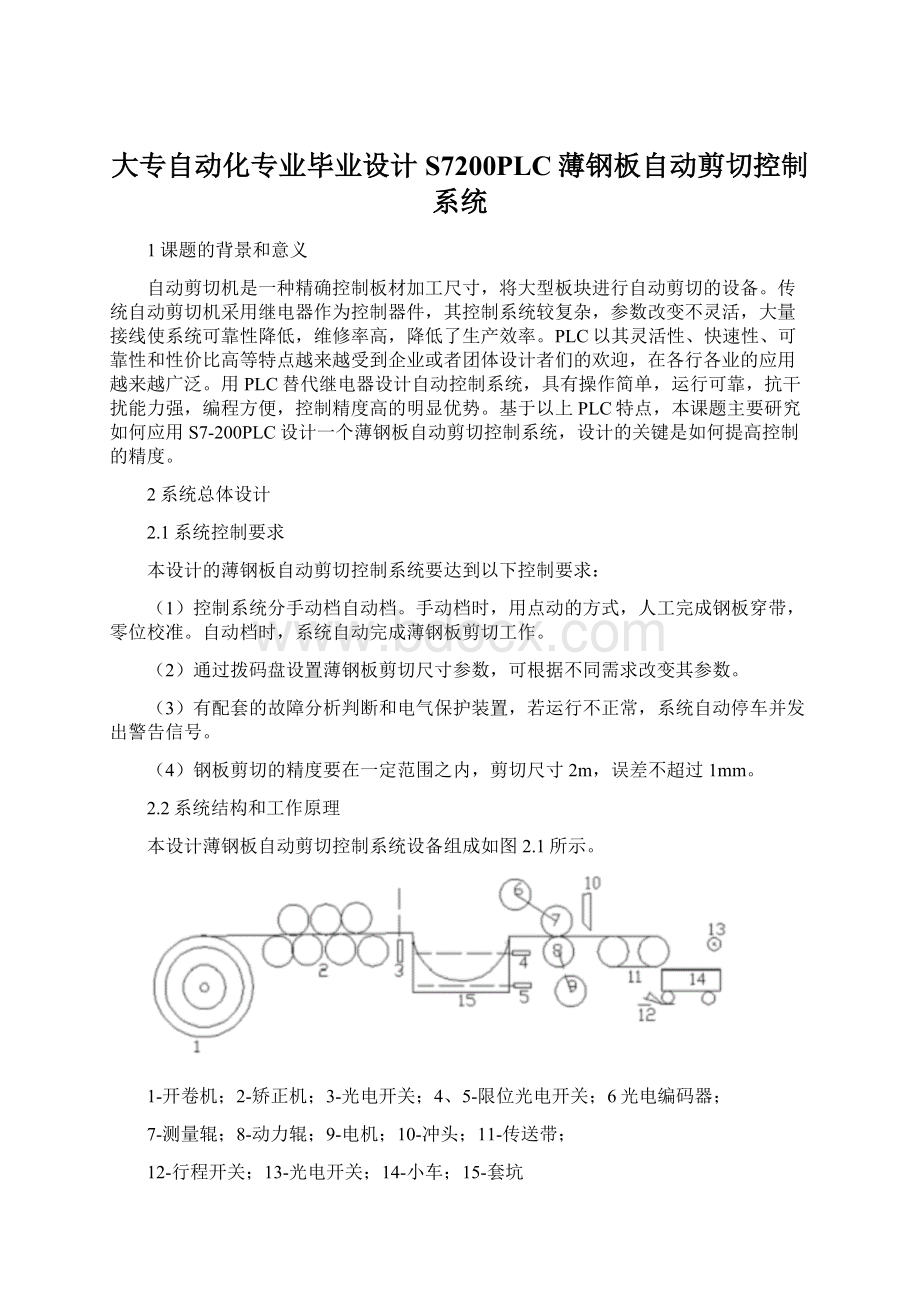
用拨码盘设定剪切尺寸参数,钢带头对好冲头,光电编码器处于零位,然后启动自动控制按键,如果检测到装料小车到位,系统进入自动控制状态,将钢板剪切,传送到装料小车上。
钢板经历加速,匀速,降速和爬行四个阶段后停车。
如果钢板尺寸和设定一致,则启动冲压系统进行剪切,如果超出或者不够,则电机反转或正转补充直到与设定值一致再剪切,接着剪切下一块钢板,不断循环。
套坑起着缓冲的作用,标号3光电开关检测套坑前是否有钢带,若没有系统停车;
标号4和5为一对限位光电检测开关,检测套坑钢板量是否合适,若过少加快矫正机速度一段时间,或过多减慢矫正机速度一段时间;
标号12为行程开关,若检测到小车没有到位,系统停车;
标号13为光电开关,若检测到小车钢板已经满载,系统自动停车并发出指示信息,等待小车把钢板运到下一道工序回来,系统继续开车。
本设计的薄钢板自动剪切控制系统简单分为控制部分,输入模块和输出模块,其结构组成和工作原理可以用图2.2所示的框图表示。
图2.2系统方框图
3系统硬件设计
3.1光电编码器
3.1.1光电编码器原理
光电编码器,是一种通过光电转换将输出轴上的机械几何位移量转换成脉冲或数字量的传感器。
这是目前应用最多的传感器,光电编码器是由光栅盘和光电检测装置组成。
光栅盘是在一定直径的圆板上等分地开通若干个长方形孔。
由于光电码盘与电动机同轴,电动机旋转时,光栅盘与电动机同速旋转,经发光二极管等电子元件组成的检测装置检测输出若干脉冲信号;
通过计算每秒光电编码器输出脉冲的个数就能反映当前电动机的转速。
脉冲序列能正确地反映转速的高低,但不能鉴别转向。
为了获得转速的方向,可增加一对发光与接收装置使两对发光与接收装置错开光栅节距的1/4,两组脉冲序列A和B的相位相差90度,如图3.1所示[2]。
正转时A相超前B相;
反转时B相超前A相。
(a)正转(b)反转
图3.1区分旋转方向的A、B两组脉冲序列
3.1.2光电编码器的选择和安装
选择合适的光电编码器,对提高系统整体性能到头重要。
本设计选择欧姆龙的编码器产品,型号E6B2-CWZ6C2000P/R(中空型,电源电压DC5~24V,消费电力80mA以下,输出形式NPN开路输出,最高响应频率100KHZ,相位差A相、B相差90度),A相、B相信号经过脉冲处理电路后,编码器每旋转一周可得到4000个脉冲。
中空型光电编码器的机械安装主要注意以下问题:
要避免与编码器刚性连接,应采用板弹簧;
安装时编码器应轻轻推入被套轴,严禁用锤敲击,以免损坏轴系和码盘;
长期使用时,请检查板弹簧相对编码器是否松动;
固定编码器的螺钉是否松动。
编码器在电气连接方面注意以下事项:
接地线应尽量粗,一般应大于φ3;
编码器的输出线彼此不要搭接,以免损坏输出电路;
编码器的信号线不要接到直流电源上或交流电流上,以免损坏输出电路;
与编码器相连的电机等设备,应接地良好,不要有静电;
配线时应采用屏蔽电缆;
避免在强电磁波环境中使用。
前面曾经考试过,为了方便,不用外置电源,用PLC内部电源给各种传感器和光电开关提供电源。
后来考虑到PLC的电源的稳定性,光电编码器的电源接外接直流电源5V,其它光电开关和传感器也一样单独接电源。
3.2拨码盘的应用
3.2.1拨码盘原理
在工业控制中,输人设备必不可少。
对PLC控制系统而言,人机交互的输人方式广泛采用触摸屏、拨码盘、光电及电磁开关等.。
由于拨码盘具有接口简单、数据锁存、操作方便直观、便于安装等优点,因此在需要输人少量控制参数和数据的系统中,经常采用拨码盘作为输人部件[5]。
本设计采用BCD码拨码盘作为数据输入部件。
BCD拨码盘是十进制输入,BCD码(即2-10十进制)输出,又称为8421拨码盘。
如图3.3所示,每片BCD拨码开关可输入1位10进制数,N片BCD拨码开关拼接可得N位10进制输入。
每片BCD拨码盘后面有5个接点,其中C为输入控制线,另外4根是BCD码输出信号线。
拨码盘拨到不同的位置时,输入控制线C分别与4根BCD码输出线中的某根或某几根接通。
其接通的BCD码输出线状态正好与拨盘指示的10进制数相一致,符合2-10进制编码关系。
(a)拨码盘外形(b)拨码盘接线端子
图3.34位BCD拨码开关示意图
3.2.2拨码盘与PLC的连接
一片只有一位十进制数输出的BCD拨码盘与PLC连接非常简单,只要将4根BCD码输出信号线分别与PLC的4个输入端相连,控制线C直接接高电平就可实现数据输入。
如图3.4所示。
图3.4一片拨码盘与PLC连接
本设计为了满足脉冲数设定需要使用了3片2位十进制数输出的BCD拨码盘,其与PLC连接如图3.5所示,最大设定数为99999。
图3.5多片拨码盘与PLC连接
在图3.5中,3片拨码盘分为A、B、C三组,各组拨码盘的每个开关输出点都串入二级管,利用二极管单向导电的特性来接通、断开拨码开关选通组和非选通组的输出信号。
当需要读取A组拨码盘所设定的数据时,PLC的输出端Q1.2输出高电平,Q1.3和Q1.4输出低电平,则A组拨码开关所串联的8个二极管处于正向接法,而B和C组拨码盘串联的16个二极管处于反向接法。
虽然A、B、C三组拨码盘输出是并联的,但从PLC的输入所读到的数是A组拨码盘所设定的数。
依此类推,如果需要读取B或C组拨码盘所设定的数时,只要令本身的控制端为高电平,其它两组的为低电平即可。
通过编程,PLC依次读入A、B、C三组拨码盘设定的数。
3.3检测开关的安装
3.3.1光电开关
在自动控制系统中,往往应用到许多传感器,检测生产过程的各个物理量,为控制器做出合理的判断提供依据。
光电开关是一种常用的传感器,光电开关(光电传感器)是光电接近开关的简称,它是利用被检测物对光束的遮挡或反射,由同步回路选通电路,从而检测物体有无的。
光电开关将输入电流在发射器上转换为光信号射出,接收器再根据接收到的光线的强弱或有无对目标物体进行探测。
在本设计中,用到了4对对射式光电开关检测薄钢板在不同位置的信息,安装方式如图3.6所示。
图3.6光电开关示意图
假如选用DC5V的光电开关,为了PLC的运行稳定,电源不由PLC直流电流供电,而是直接由外接电源供电。
光电开关的Ov按扭和PLC的输入公共端COM连接,光电开关的输出端与PLC的输入端口连接。
当光电开关输出高电平时表明光电开关发射器发射的光源被遮挡,光电开关接收器无法接收到光源,即光电开关发射器和接收器间存在物体。
在系统运行时,正常情况下,3号光电开关一直检测到传送带上一直有钢板;
若是检测到钢带上没有了钢板,PLC控制系统即判定为开卷机已经没有钢带,发出停车指令。
相关电路图如图3.7所示。
光电开关在本设计的薄钢板自动剪切控制系统中有着重要的作用,光电开关实时检测系统运行时钢板在各个位置的存在状况,为PLC提供系统是否能够正常运行的实时数据,保证系统的安全。
图3.7光电开关与PLC连接
3.3.2行程开关
行程开关又称限位开关,用于控制机械设备的行程及限位保护。
在实际生产中,将行程开关安装在预先安排的位置,当装于生产机械运动部件上的模块撞击行程开关时,行程开关的触点动作,实现电路的切换。
因此,行程开关是一种根据运动部件的行程位置而切换电路的电器,它的作用原理与按钮类似。
行程开关广泛用于各类机床和起重机械,用以控制其行程、进行终端限位保护。
在电梯的控制电路中,还利用行程开关来控制开关轿门的速度、自动开关门的限位,轿厢的上、下限位保护。
本设计的自动控制系统中有三个行程开关,分别是检测剪切钢板的冲头上下位置各一个,检测载物小车是否到位一个,其安装示意如图3.8所示。
冲头上下位置开关给PLC目前冲头位置信息,说明冲头是在原位还是已经下冲,或者下冲是否到位。
若冲头下冲到位,SQ2给PLC信息,说明钢板已经剪切成功,接着进行复位,SQ1给复位位置信号,复位不成功,系统不会开车。
小车的位置检测行程开关SQ3,既给PLC小车位置信息,又给下一道工序控制系统小车位置信息。
(a)检测冲头位置行程开关(b)检测小车位置行程开关
图3.8行程开关安装示意图
3.4变频器
3.4.1变频器的一般架构
在本设计中,需要对矫正机和夹送机构的转动速度和幅度进行有效控制,为矫正机和夹送机构提供动力的装置可以选择交流伺服系统,比如用步进电机作为动力装置,其控制精度比较高,使用也较方便,但是交流伺服系统的造价一般比较高。
在PLC和变频器技术日趋成就的今天,选择PLC和变频器搭配,有效地控制三相异步电机转速和幅度,从而控制系统传送机构启动,运行,降速和准确停车,达到的控制效果与交流伺服系统相近,是一种比较高性价比的方案。
目前市场上出现的变频器各类繁多,但基本的架构一样,也为其使用提供了依据。
变频器的一般结构框图如图3.11所示。
图3.11变频器的一般结构框图
其中,直流供电电源输入一般为24V直流电源;
数字量输入和模拟量输入一般是PLC输出端口和PLC扩展模拟量输出端口来控制;
三相电输入为50HZ三相交流电;
制动电阻用来制动时机;
三相变频输出是指经过变频后,用于给被控制的时机提供的三相电,其频率是根据速度信息得到的频率。
3.4.2变频器的选择
本设计采用西门子的MICROMASTER420变频器。
MICROMASTER420变频器适合用于各种变速驱动装置,尤其适合用于水泵,风机和传送带系统的驱动装置。
它的特点是设备性能面向用户的需求,并且使用方便。
它的电源电压规格很多,因而可在世界范围内应用。
MICROMASTER420变频器调试简单;
模块化的结构,因而组态具有最大的灵活性;
具有三个完全可编程的隔离的数字输入;
一个可标定的模拟输入(0V
至10V);
它也可以作为第4个数字输入来使用。
;
一个可编程的模拟输出(0mA至20mA);
一个完全可编程的继电器输出(30V,直流/5A,电阻负载或250V,交流/2A,感性负载);
采用较高的开关频率时,电动机运行的噪声很小(在脉冲的开关频率较高的情况下,额定输出电流要降格使用);
完善的变频器和电动机保护功能。
本设计主要用PLC的3个输出端口通过MICROMASTER420变频器3个可自由编程的数字输入实现对变频器的控制。
Q1.2、Q1.3、Q1.4、Q1.5、Q1.6、Q1.7的通断情况选择变频器的输出,其对应情况如表3-1所列。
表3-1变频器控制输入与三相输出对应表
矫正变频器
送送变频器
控制端接通
三相输出
Q1.2、Q1.3、Q1.4
50HZ,向前
Q1.5、Q1.6、Q1.7
Q1.2、Q1.3
40HZ,向前
Q1.5、Q1.6
Q1.3、Q1.4
40HZ,向后
Q1.6、Q1.7
Q1.4
20HZ,向前
Q1.7
Q1.2、Q1.4
20HZ,向后
Q1.5、Q1.7
Q1.2
10HZ,向前
Q1.5
Q1.3
10HZ,向后
Q1.6
3.5主电路设计
本设计的PLC薄钢板自动剪切控制系统主电路设计主要有两块,一是电机与变频器电气连接,二是冲头执行机构、指示灯电气连接,分别如图3.9和3.10所示。
图3.9主电路(a)
在图3.9主电路(a)中,电源为三相市电输入,为了保护变频器和电机安全,串连两个低电断路器QF1和QF2,串接了熔断器,三相异步电机M1和M2接地。
其中,M1电机负责矫正机的传动,M2电机负责夹送机构和输送皮带的传动。
变频器电源的通断控制由PLC控制两个接触器开关KM1和KM2的通断来实现。
一般情况下,把QF1和QF2合上,在系统上电时,KM1和KM2默认为断开。
图3.10主电路(b)
另外,在图3.10主电路(b)中,单相市电接入串接熔断器FU起保护作用。
该电路主要完成两个功能,一个是系统启动后,KM1和KM2闭合,L1和L2指示变频器已经正常上电;
二是接触器开关KM3和KM4分别控制冲头执行机构下冲或复位。
3.6PLC控制系统
3.6.1PLC选型
西门子公司的S7-200PLC是一种叠装式结构的小型PLC,它指令丰富,功能强大,可靠性高,结构紧凑,便于扩展,性能价格比高。
从CPU模块的功能来讲,S7-200系列PLC具有以下五种不同结构配置的CPU单元[8]。
(1)CPU221有6输入/4输出,无扩展,存储容量较小,有一定的高速计数能力,适合于点数少的控制系统。
(2)CPU222有8输出/10输出,可以进行模拟量的控制和2个模块的扩展,应用更广泛的全功能控制器。
(3)CPU224有14输入/10输出,存储容量扩大了一倍,有7个扩展模块,内置时钟,有更强的模拟量和高速计数的处理能力,是S7-200系列中使用最多的产品。
(4)CPU224XP最新推出的一款实用机型,最大的不同是主机上增加了2输入/1输出的模拟量单元和一个通信口,适合有少量模拟信号的系统中使用。
(5)CPU226有24输入/16输出,增加了通信口的数量,通信能力大大增强,用于点数较多,要求较高的小型或中型控制系统。
根据以上S7-200系列PLC不同CPU资源的了解,考虑到本设计的薄钢板自动剪切控制系统所要求的点数较多,故选择CPU226DC/DC/DC(6ES7216-1AD21-0XB0)。
设计涉及的CPU226相关技术参数如表3-2所列。
表3-2CUP226相关技术参数
输入/输出
24/16
时间中断
2个
定时器总数
256个
高速计数器总数
6个
边沿中断
4上升/4下降
1ms
4个
单相计数器个数
6个,30KHZ
脉冲捕捉
14个
10ms
16个
两相计数器个数
4个,20KHZ
计数器总数
256个
100ms
236个
由表3-2可以看出,S7-200CPU226的资源是相当丰富的,基本满足了本设计的薄钢板自动剪切控制系统的端口要求和编程时所需要的功能要求。
3.6.2PLC端口分配
控制系统PLC的I/O点及地址分配如表3-3所列。
表3-3I/O口信号代码和地址编号表
名称
代码
地址编号
启动按扭
SB1
I0.2
正常灯指示
L3
Q1.0
停止按扭
SB2
I0.3
异常灯指示
L4
Q1.1
手动/自动方式选择
SA
I0.4
主电路电源通断
KM1
Q0.0
矫正机前进
SB3
I0.5
KM2
Q0.1
矫正机后退
SB4
I0.6
冲头下冲控制
KM3
Q0.2
夹送辊前进
SB5
I0.7
冲头复位
KM4
Q0.3
夹送辊后退
SB6
I1.0
拨码盘控制
Q1.2~Q1.4
光电脉冲信号P
SP1
I0.0
矫正变频器设定
Q1.2~1.4
光电脉冲方向D
SP2
I0.1
夹送变频器设定
Q1.5~1.7
光电开关3信号
SQ1
I1.1
光电开关4信号
SQ2
I1.2
光电开关5信号
SQ3
I1.3
光电开关13信号
SQ4
I1.4
冲头上限行程开关
SQ5
I1.5
冲头下限行程开关
SQ6
I1.6
小车位置行程开关
SQ7
I1.7
拨码盘输入
I2.0~2.7
本设计所选型号CPU226DC/DC/DC,其电源接入和信号输出有直流电源也有交流电源,而且各种电源的等级不尽相同,在接线时选择各种电源是独立分开的,互不干扰。
系统所采用开按扭有两种,一种是能够锁存状态的按扭,即手动/自动方式选择按扭;
另外一种是点动按扭,主要是在手动方式下对电机进行手动控制。
特别值得注意的是,本设计的系统中,由于要对光电编码器的脉冲进行高速计数,使用了CPU226的某一个高速计数器。
光电编码器的脉冲信号经光电脉冲电路处理后得到两个信号,光电脉冲P和方向信号D,这两个信号接入PLC的端口不是随便的,而是根据规定,P信号接I0.0(时钟),D信号接I0.1(方向),否则高速计数器将得不到正确的信号。
3.7变频分段调速
与交流伺服系统不同,变频器和三相异步电机不可能在高速运行状态下迅速停车,必须有一个降速和低速爬行的过程,才能保证定位点的准确,可以选择多档调速,控制精度更高,其运行曲线见图3.12。
图3.12变频器定位运行降速控制规律
另外,钢板剪切的长度与毛巾平网印花机的花色间距不同,它不是定值,而是从几十毫米到数千毫米不等,因此不可能采用同样的运行速度和同样的降速爬行距离。
否则,变频器的定位停车会处于一种无序状态,剪切精度和生产效率也不能得到平衡和兼顾……[9]。
从图3.12可以看出,不同的剪切钢板尺寸,选择加速上升时间和匀速运行时间以及降速运行时间不能够完全一样,假定所有的情况下到达定位目标前的爬行速度一样,就要根经验保证爬行的距离基本一样,能很好保证钢板准确停车。
本设计以剪切2m的薄钢板为例说明各段参数设定。
已知所选的电动机为4级,额定转速为1500r/min,减速箱的减速比为20/1,测量辊周长400mm,额定辊速75r/min,变频器固定频率输出有多档,如50HZ,40HZ,30HZ,20HZ,10HZ。
剪切2m的钢板,在加速到匀速段变频器选择输出40HZ,在降速段选择输出20HZ进行降速,在爬行阶段选择10HZ输出,直到检测脉冲数和设定脉冲相等,变频器停机,钢板准确停车。
3.8制动过程
当系统开始减速时,电动机处于再生发电制动状态。
传动系统中所储存的机械能变成电能并经变频器中的逆变器回馈到直流侧。
此时的逆变器处于整流状态,中间回路的滤波电容器的电压会因吸收这部分能量而提高,产生泵生电压。
当电压值超过上限700V时,制动单元电路导通,电流流过与滤波电容器并联的制动电阻,从而将电能变成热能消耗掉,泵生电压随之下降,待下降到设定下限680V值时断开。
继续采样泵生电压,制动单元将重复导通和截止,使系统完成动力制动。
4系统软件设计
4.1主流程
本设计薄钢板剪切自动控制系统主要分为两大块,一个是系统在手工操作方式下运行,一个是系统在自动方式下运行。
主流程如图4.1所示。
图4.1主流程图
在主流程图中,先进行PLC初始化,读拨码盘值,然后按启动按扭,主电路通电,接着按选择条件选择手动工作方式或者是自动运行工作方式。
若选择手动工作方式,因为其运行的次数比较少,所以每执行一次手动子程序都将直接返回到工作方式选择。
自动运行子程序相对比较复杂,每次执行完之后,进行一个判断,如果工作方式没有改变,则直接返回自动子程序,若工作方式已经改变,返回到工作方式选择。
因此,在主流程图中,有两个主体,一个是手动控制流程,一个是自动控制流程。
这两个主体的切换,因为使用了顺序控制继电器指令而变得相对方便。
在自动控制子流程图中,进入自动控制状态后,在满足小车到位和小车没有满载条件下,才启动变频器。
因为矫正机负载不稳定,可能造成和夹送辊速度不同步,造成套坑钢带量不合适。
4和5光电开关检测套坑里面的钢带量是否合适,如果过多或者过少都会引进系统的振荡和故障,正常状态下4光电开关为开,5号光电开关为开,若5号光电开关为闭,说明套量过多,矫正变频器减速一小会再跟夹送变频器同步速度,若4为开,说明套量过少,矫正变频器加速一小会再跟夹送变频器同步速度。
到达变速点,变频器进行降速爬行输出,最后判定高速计数器的值等于拨码盘的设定值后,发出冲压信号。
由于其它原因造成停车后实际板长与设定的板长不符合,调用停车异常子程序,经过微小调整,再进行判断,实际值等于设定值后,发冲压信号。
4.2手动控制流程
手动控制子流程比较简单,即四个按扭分别控制矫正机和夹送辊的前进或者后退,以便在系统进行自动运行方式前,人工将钢带穿过矫正机和送辊一直到达冲头的位置。
手动控制流程如图4.2所示。
在图4.2中,手动方式下四个按扭SB3/SB4/SB5/SB6均是点动式按扭,分别对应了矫正机和夹送辊的前进和后退。
按下相应的按扭,PLC根据指令的编程,控制输出端Q1.2、Q1.3、Q1.4的通断组合情况,控制矫正变频器脉冲方向输出和频率输出,实现控制矫正机前进和后退的目的;
控制输出端Q1.5、Q1.6、Q1.7的通断组合情况,控制夹送变频器脉冲方向输出和频率输出,实现控制夹送辊前进和后退的目的。
值得注意的是,电机前进和后退控制按扭控制电机运行的效果是矛盾的,为了避免出现混乱,程序编程采用了互锁的手段。
图4.2手动控制流程
电气控制电路中,各电器之间具有互相制约、互相配合的控制,称为联锁控制。
在顺序控制电路中,要求接触器KM1得电后,接触器KM2才能得电。
在电动机正、反转控制电路中,要求接触器KM1得电后,接触器KM2不能得电吸合。
则需将前者的常闭触点串接在KM2线圈电路中。
反之,也然。
这种联锁关系称为互锁[10]。
因此,手动控制流程编程中采用的互锁手段,增强了可靠性和安全性。
4.3编程软件
STEP7-Micro/WIN32[11]编程软件是基本Windows的应用软件,由西门子公司专门为SIMATIC[12]S7-200系列PLC设计开发。
该软件功能强大,界面友好,并有方便的联机帮助功能。
用户可利用该软件PLC应用程序,同时也可实时监控用户程序的执行状态。