连杆加工工艺规程及钻大头油课程设计说明书Word文档格式.docx
《连杆加工工艺规程及钻大头油课程设计说明书Word文档格式.docx》由会员分享,可在线阅读,更多相关《连杆加工工艺规程及钻大头油课程设计说明书Word文档格式.docx(25页珍藏版)》请在冰豆网上搜索。
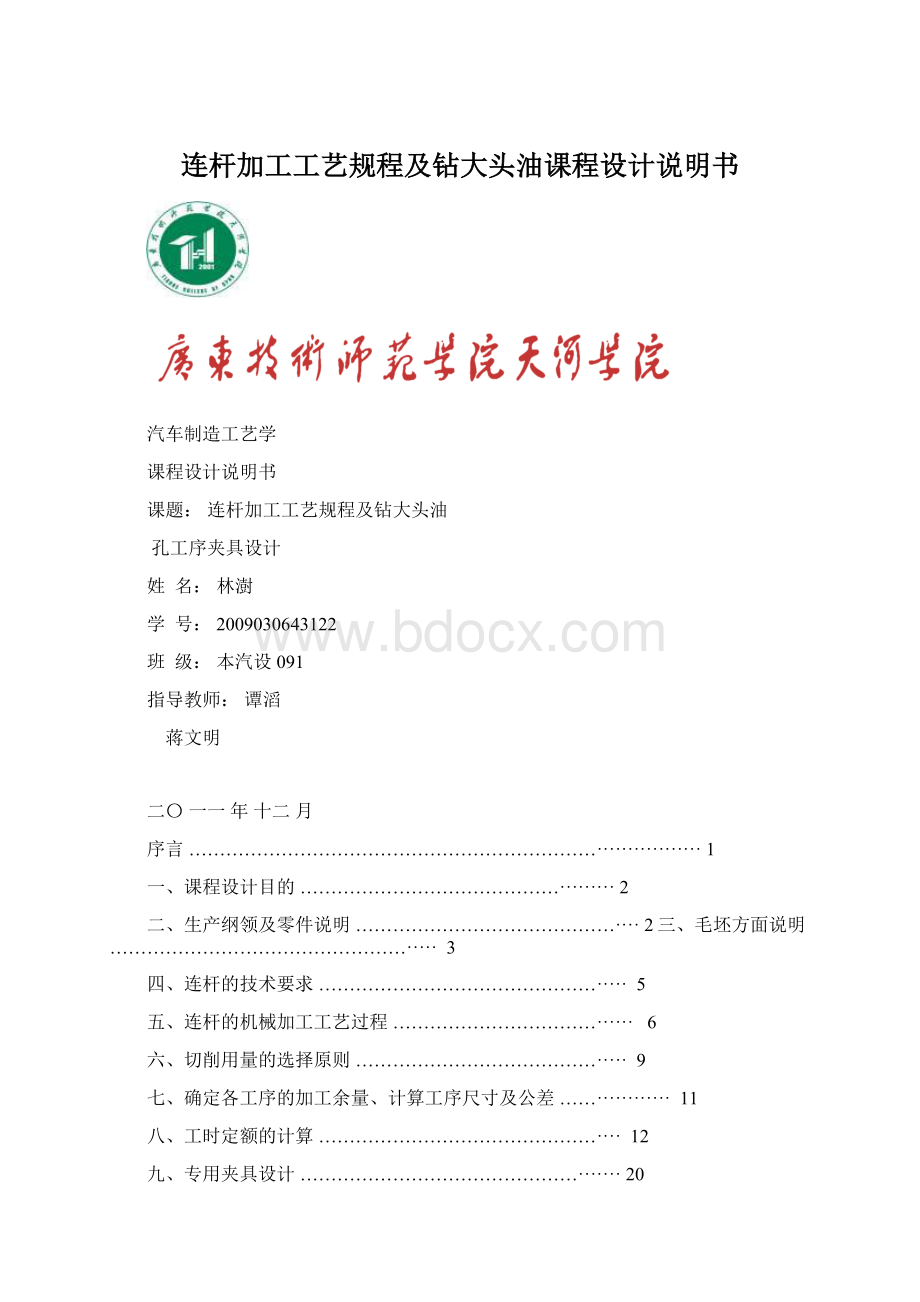
参考文献………………………………………………·
23
汽车制造工艺学学课程设计任务书
系部:
机电工程系课程代码:
0340132_班级:
一、设计题目:
连杆加工工艺规程及钻大头油孔工序夹具设计
二、主要内容:
1.毛坯选择;
2.连杆加工工艺路线制定;
3.钻大头油孔工序工序具体内容确定;
4.钻大头油孔工序夹具设计
5.确定生产类型(产量可自己确定或直接设定生产类型)
三、具体要求及应提交的材料
1.填写工艺过程卡时,除钻大头油孔工序,其它工序机床确定名称,夹具确定类型,刀具与量具也确定名称;
2.工艺路线制定因是同一个零件,必须独立完成;
3.同组夹具结构必须有差异;
4.必须按时完成、设计说明书按规定格式书写;
5.完成应提交的材料:
设计说明书一份、夹具装配总图一张、连杆体零件图一张、工艺过程卡片及钻大头油孔工序工序卡片各一份;
6.不校核设计能力,若要校核自己确定年产量(中批或大批生产或大量生产)。
四、主要技术路线提示
1.确定生产类型(设定为中批或大批量生产),对零件进行工艺分析,画零件图;
2.确定毛坯种类及制造方法;
3.拟订零件机械加工工艺过程,选择各工序的加工设备和工艺装备(刀具、夹具、量具、辅具),确定钻大头油孔工序及相关加工余量和工序尺寸,计算钻大头油孔工序的切削用量和工时定额;
4.夹具设计必须满足△d≤T/3。
五、进度安排(设计共两周10天)
1.准备一天(课程设计工艺讲解、画图工具准备、借阅相关工具书和资料等);
2.画零件图一天;
3.制定工艺路线两天;
4.确定钻大头油孔工序工序具体内容一天;
5.夹具设计及完成总装图三天;
6.完成设计说明书及答辩两天。
签名日期:
年月日
教研室主任:
系主任:
审核日期:
序言
《汽车制造工艺学课程设计》是我们学习完大学阶段的汽车类基础和技术基础课以及专业课程之后的一个综合的课程设计,它是将设计和制造知识有机的结合,并融合现阶段汽车制造业的实际生产情况和较先进成熟的制造技术的应用,而进行的一次理论联系实际的训练,通过本课程的训练,将有助于我们对所学知识的理解,并为后续的课程学习以及今后的工作打下一定的基础。
对于本人来说,希望能通过本次课程设计的学习,学会将所学理论知识和工艺课程实习所得的实践知识结合起来,并应用于解决实际问题之中,从而锻炼自己分析问题和解决问题的能力;
同时,又希望能超越目前工厂的实际生产工艺,而将有利于加工质量和劳动生产率提高的新技术和新工艺应用到机器零件的制造中,为改善我国的汽车制造业相对落后的局面探索可能的途径。
但由于所学知识和实践的时间以及深度有限,本设计中会有许多不足,希望各位老师能给予指正。
一、课程设计目的
汽车制造工艺课程设计是车辆工程专业学生学完《汽车制造工艺学》后,进行的一个重要的实践性教学环节。
通过设计培养学生综合运用所学知识的能力,为以后的毕业设计进行一次综合训练和准备。
通过本课程设计使学生在下述各方面得到训练。
1、运用汽车制造工艺学课程中的基本理论解决零件在加工中的定位,夹紧以及工艺路线安排,工艺尺寸确定,机床,工具量具的选择等问题,以保证零件的加工质量。
2、通过设计,获得根据被加工零件的加工要求,设计出高效,省力,经济合理,能保证加工质量的夹具的能力。
3、学会使用手册及图表资料。
培养查阅各种资料的能力,同时掌握与本设计有关的各种资料。
二、生产纲领及零件说明
1.生产纲领
生产纲领的大小对生产组织和零件加工工艺过程起作用,它决定了各工序所需要专业化和自动化的程度,以及所选用的工艺方法和工艺装备。
发动机连杆零件的年产量位30000件,该产品属于轻型机械,根据生产类型和生产纲领的关系查阅参考文献,确定其生产类型位大批量生产。
大批量生产的工艺特征;
(1)零件的互换性;
具有广泛的互换性,少数装配精度较高处,采用分组装配法和调整法。
毛坯的制造方法和加工余量;
广泛采用金属模机器造型,模锻或其他商效方法。
毛坯精度高,加工余量小。
(2)机床设备及其布置形式;
广泛采用商效专用机床及自动机床,按流水线和自动排列设备。
(3)工艺装备;
广泛采用高效夹具,复合刀具,专用量具或自动检验装置,靠调整法达到精度要求。
(4)对工人的技术要求;
对调整工的技术水平要求高,对操作工的技术水平要求较低。
(5)工艺文件;
有工艺过程卡或工序卡,关键工序要调整卡和检验卡。
(6)成本:
较低。
(7)生产率:
高。
(8)工人劳动条件:
较好。
2.零件说明
连杆是汽车发动机中的重要零件,在发动机内的曲柄连杆机构中,连杆的大头孔与曲轴连接,小头孔通过活塞连接,其作用是将活塞的直线往复运动转变为曲轴的旋转运动并输出动力。
连杆承受动态载荷,因此,要求连杆质量小,强度高,高度好
连杆的结构特点
连杆由大头、小头和杆身等部分组成。
大头为分开式结构,连杆体与连杆盖用螺栓连接。
大头孔和小头孔内分别安装轴瓦和衬套。
为了减轻重量并保证连杆体具有足够的强度和刚度,连杆的杆身截面多为工字形,其外表不需要机械加工。
连杆的大头和小头端面,通常都与杆身对称。
有些连杆在结构上设计有工艺凸台、中心孔等,作为机械加工时的辅助基准
连杆的结构工艺性
连杆的结构形式,直接影响到机械加工工艺的可靠性和经济性。
影响连杆结构工艺性的因素除应考虑一般的结构工艺性外,还要考虑以下几点:
①连杆盖和连杆体的连接方式连杆盖和连杆体的定位方式,有连杆螺栓、套筒、齿形定位和凸肩定位4种。
②连杆的大小头的厚度考虑到加工时的定位和加工时的传输等,连杆大、小头的厚度应相等。
③连杆杆身油孔的大小和深度由于活塞销与连杆小头衬套之间需要进行润滑,为此连杆杆身钻有油孔。
但为了使润滑油从连杆大头沿油孔通向小头衬套,油孔一般为Φ4-Φ8㎜的深孔,加工困难。
为了避免深孔加工,汽车发动机连杆可改为重力润滑,则只在连杆小头铣槽或钻孔就可。
三、连杆的材料和毛坯
连杆材料一般采用45钢或40Cr、45Mn2等优质钢或合金钢,近年来也有采用球墨铸铁的。
其毛坯多用锻造,可将连杆体和连杆盖分开锻造,也可整体锻造,主要取决与锻造毛坯的设备能力。
锻造可用自由锻或模锻,但模锻与自由锻相比,模锻的尺寸和精度比较高,机械加工余量小,材料的利用率高,锻件内部流线分布合理,操作方便,劳动强度低,生产率高。
汽车发动机连杆是承受冲击反动态应力最高的典型动力学定荷零件,连杆的结构形式,直接影响机械加工的可靠性和经济性。
因此,连杆做成工字形断面,轻量化可减少发动机运行时的噪声震动,提高连杆的力学性能。
现已40Cr作为原料并经调质处理,以提高其强度及抗冲击能力。
锻件的强度及可靠性很高,广泛应用于发动机变速器,转向器及其他零件上。
在大批量生产中采用模锻。
特点是;
(1)坯料整体塑性变形,三向受压:
(2)锻件尺寸精确,加工余量小(3)锻件形状可较复杂:
(4)生产效率高(5)锻模造价高,制造周期长
前面提过锻坯有2种形式,连杆体和盖在一起的整体锻造,以及连杆和盖分别分开的锻造。
2者比较整体锻造节省材料,并较少毛坯制造劳动量,又可使连杆体和盖端面同时加工,课减少毛坯制造劳动量,又可使连杆体和盖端面同时加工,课减少工序步骤。
毛坯生产工序:
锻坯有两种形式:
连杆体和盖在一起的整体锻件和两者分开的分开锻件。
整体较分体节省金属材料,并减少毛坯制造劳动量,又可使连杆体和盖断面同时加工,可减少工序数目,整体的毛坯需在机械加工过程中将其切开,为保证切开后粗镗孔时的量均匀,需将毛坯大头孔锻或椭圆形。
锥上模锻工艺规程:
切断毛坯——加热坯料——模锻——切除飞边——板正锻件——锻件热处理——表面清理——检验——称重——成堆存放
四、连杆的技术要求
连杆的作用是把活塞和曲轴联接起来,使活塞的往复直线运动变为曲柄的回转运动,以输出动力,同时又压缩汽缸内气体。
因此,连杆的加工精度将直接影响柴油机的性能,而工艺的选择又是直接影响精度的主要因素。
反映连杆精度的参数主要有5个:
(1)连杆大端中心面和小端中心面相对连杆杆身中心面的对称度;
(2)连杆大、小头孔中心距尺寸精度;
(3)连杆大、小头孔平行度;
(4)连杆大、小头孔尺寸精度、形状精度;
(5)连杆大头螺栓孔与接合面的垂直度。
图3连杆的技术要求
1.大、小头孔的尺寸精度、形状精度
为了使大头孔与轴瓦及曲轴、小头孔与活塞销能密切配合,减少冲击的不良影响和便于传热。
大头孔公差等级为IT6,表面粗糙度Ra应不大于0.8μm;
大头孔的圆柱度公差为0.012mm,小头孔公差等级为IT8,表面粗糙度Ra应不大于3.2μm。
小头压衬套的底孔的圆柱度公差为0.0025mm,素线平行度公差为0.04/100mm。
2.大、小头孔轴心线在两个互相垂直方向的平行度
两孔轴心线在连杆轴线方向的平行度误差会使活塞在汽缸中倾斜,从而造成汽缸壁磨损不均匀,同时使曲轴的连杆轴颈产生边缘磨损,所以两孔轴心线在连杆轴线方向的平行度公差较小;
而两孔轴心线在垂直于连杆轴线方向的平行度误差对不均匀磨损影响较小,因而其公差值较大。
两孔轴心线在连杆的轴线方向的平行度在100mm长度上公差为0.04mm;
在垂直与连杆轴心线方向的平行度在100mm长度上公差为0.06mm。
3.大、小头孔中心距
大小头孔的中心距影响到汽缸的压缩比,即影响到发动机的效率,所以规定了比较高的要求:
195±
0.05mm。
4.连杆大头孔两端面对大头孔中心线的垂直度
连杆大头孔两端面对大头孔中心线的垂直度,影响到轴瓦的安装和磨损,甚至引起烧伤;
所以对它也提出了一定的要求:
规定其垂直度公差等级应不低于IT9(大头孔两端面对大头孔的轴心线的垂直度在100mm长度上公差为0.08mm)。
5.大、小头孔两端面的技术要求
连杆大、小头孔两端面间距离的基本尺寸相同,但从技术要求是不同的,大头两端面的尺寸公差等级为IT9,表面粗糙度Ra不大于0.8μm,小头两端面的尺寸公差等级为IT12,表面粗糙度Ra不大于6.3μm。
这是因为连杆大头两端面与曲轴连杆轴颈两轴肩端面间有配合要求,而连杆小头两端面与活塞销孔座内档之间没有配合要求。
连杆大头端面间距离尺寸的公差带正好落在连杆小头端面间距离尺寸的公差带中,这给连杆的加工带来许多方便。
6.螺栓孔的技术要求
在前面已经说过,连杆在工作过程中受到急剧的动载荷的作用。
这一动载荷又传递到连杆体和连杆盖的两个螺栓及螺母上。
因此除了对螺栓及螺母要提出高的技术要求外,对于安装这两个动力螺栓孔及端面也提出了一定的要求。
规定:
螺栓孔按IT8级公差等级和表面粗糙度Ra应不大于6.3μm加工;
两螺栓孔在大头孔剖分面的对称度公差为0.25mm。
7.对口面的技术要求
在连杆受动载荷时,对口面的歪斜使连杆盖及连杆体沿着剖分面产生相对错位,影响到曲轴的连杆轴颈和轴瓦结合不良,从而产生不均匀磨损。
结合面的平行度将影响到连杆体、连杆盖和垫片贴合的紧密程度,因而也影响到螺栓的受力情况和曲轴、轴瓦的磨损。
对于本连杆,要求结合面的平面度的公差为0.025mm。
五、连杆的机械加工工艺规程
1.工艺过程的安排
在安排工艺进程时,就要把各主要工序的粗、精加工工序分开,即把粗加工安排在前,半精加工安排在中间,精加工安排在后面。
这是由于粗加工工序的切削余量大,因此切削力、夹紧力必然大,加工后容易产生变形。
粗、精加工分开后,粗加工产生的变形可以在半精加工中修正;
半精加工中产生的变形可以在精加工中修正。
这样逐步减少加工余量,切削力及内应力的作用,逐步修正加工后的变形,就能最后达到零件的技术条件。
各主要表面的工序安排如下:
(1)两端面:
先精铣后精磨;
(2)小头孔:
扩孔、铰孔、精镗、压入衬套后再精镗;
(3)大头孔:
粗镗、半精镗、精镗、研磨。
一些次要表面的加工,则视需要和可能安排在工艺过程的中间或后面。
2.定位基准的选择
在连杆机械加工工艺过程中,大部分工序选用连杆的一个指定的端面和小头孔作为主要基面,并用大头处指定一侧的外表面作为另一基面。
这是由于:
端面的面积大,定位比较稳定,用小头孔定位可直接控制大、小头孔的中心距。
这样就使各工序中的定位基准统一起来,减少了定位误差。
具体的办法是在安装工件时,注意将成套编号标记的一面不与夹具的定位元件接触(在设计夹具时亦作相应的考虑)。
在精镗小头孔(及精镗小头衬套孔)时,也用小头孔(及衬套孔)作为基面,这时将定位销做成活动的称“假销”。
当连杆用小头孔(及衬套孔)定位夹紧后,再从小头孔中抽出假销进行加工。
3.确定合理的夹紧方法
既然连杆是一个刚性比较差的工件,就应该十分注意夹紧力的大小,作用力的方向及着力点的选择,避免因受夹紧力的作用而产生变形,以影响加工精度。
在加工连杆的夹具中,应注意夹紧力的作用方向和着力点的选择。
在铣两端面的夹具中,夹紧力的方向与端面平行,在夹紧力的作用方向上,大头端部与小头端部的刚性高,变形小,既使有一些变形,亦产生在平行于端面的方向上,很少或不会影响端面的平面度。
夹紧力通过工件直接作用在定位元件上,可避免工件产生弯曲或扭转变形。
在加工大小头孔工序中,主要夹紧力垂直作用于大头端面上,并由定位元件承受,以保证所加工孔的圆度。
在精镗大小头孔时,只以大平面(基面)定位,并且只夹紧大头这一端。
小头一端以假销定位后,用螺钉在另一侧面夹紧。
小头一端不在端面上定位夹紧,避免可能产生的变形。
4.连杆两端面的加工
连杆两端面在扩粗镗大小头孔之前先进行精铣以保证两端面的平行。
而之后采用精磨工序,并将精磨工序安排在精加工大、小头孔之前,以便改善基面的平面度,提高孔的加工精度。
精磨在M7130型平面磨床上用砂轮的周边磨削,这种办法的生产率低一些,但精度较高。
5.连杆大、小头孔的加工
连杆大、小头孔的加工是连杆机械加工的重要工序,它的加工精度对连杆质量有较大的影响。
小头孔是定位基面,在用作定位基面之前先进行了扩孔、镗孔。
加工时以小头孔外形定位,这样可以保证加工后的孔与外圆的同轴度误差较小。
小头孔在粗镗后,在金刚镗床上与大头孔同时精镗,达到IT6级公差等级,然后压入衬套,再以衬套内孔定位精镗大头孔。
由于衬套的内孔与外圆存在同轴度误差,这种定位方法有可能使精镗后的衬套孔与大头孔的中心距超差。
大头孔经过扩孔、粗镗、半精镗、精镗、研磨达到IT6级公差等级。
表面粗糙度Ra为0.4μm,大头孔的加工方法是在铣开工序后,将连杆与连杆体组合在一起,然后进行精镗大头孔的工序。
这样,在铣开以后可能产生的变形,可以在最后精镗工序中得到修正,以保证孔的形状精度。
6.连杆螺栓孔的加工
连杆的螺栓孔经过钻、扩、铰工序。
加工时以大头端面、小头孔及大头一侧面定位。
精铣螺栓孔端面采用工件翻身的方法,这样铣夹具没有活动部分,能保证承受较大的铣削力。
精铣时为了保证螺栓孔的两个端面与连杆大头端面垂直度,使用两工位夹具。
连杆在夹具的工位上铣完一个螺栓孔的两端面后,夹具上的定位板带着工件旋转1800,铣另一个螺栓孔的两端面。
这样,螺栓孔两端面与大头孔端面的垂直度就由夹具保证。
7.连杆体与连杆盖的铣开工序
剖分面(亦称结合面)的尺寸精度和位置精度由夹具本身的制造精度及对刀精度来保证。
为了保证铣开后的剖分面的平面度不超过规定的公差0.03mm,并且剖分面与大头孔端面保证一定的垂直度,除夹具本身要保证精度外,锯片的安装精度的影响也很大。
如果锯片的端面圆跳动不超过0.02mm,则铣开的剖分面能达到图纸的要求,否则可能超差。
但剖分面本身的平面度、粗糙度对连杆盖、连杆体装配后的结合强度有较大的影响。
因此,在剖分面铣开以后再经过磨削加工。
六、切削用量的选择原则
正确地选择切削用量,对提高切削效率,保证必要的刀具耐用度和经济性,保证加工质量,具有重要的作用。
1.粗加工时切削用量的选择原则
粗加工时加工精度与表面粗糙度要求不高,毛坯余量较大。
因此,选择粗加工的切削用量时,要尽可能保证较高的单位时间金属切削量(金属切除率)和必要的刀具耐用度,以提高生产效率和降低加工成本。
金属切除率可以用下式计算:
Zw≈V.f.ap.1000
式中:
Zw单位时间内的金属切除量(mm3/s);
V切削速度(m/s);
f进给量(mm/r);
ap切削深度(mm)。
提高切削速度、增大进给量和切削深度,都能提高金属切除率。
但是,在这三个因素中,影响刀具耐用度最大的是切削速度,其次是进给量,影响最小的是切削深度。
所以粗加工切削用量的选择原则是:
首先考虑选择一个尽可能大的吃刀深度ap,其次选择一个较大的进给量度f,最后确定一个合适的切削速度V.
选用较大的ap和f以后,刀具耐用度t显然也会下降,但要比V对t的影响小得多,只要稍微降低一下V便可以使t回升到规定的合理数值,因此,能使V、f、ap的乘积较大,从而保证较高的金属切除率。
此外,增大ap可使走刀次数减少,增大f又有利于断屑。
因此,根据以上原则选择粗加工切削用量对提高生产效率,减少刀具消耗,降低加工成本是比较有利的。
(1)切削深度的选择:
粗加工时切削深度应根据工件的加工余量和由机床、夹具、刀具和工件组成的工艺系统的刚性来确定。
在保留半精加工、精加工必要余量的前提下,应当尽量将粗加工余量一次切除。
只有当总加工余量太大,一次切不完时,才考虑分几次走刀。
(2)进给量的选择:
粗加工时限制进给量提高的因素主要是切削力。
因此,进给量应根据工艺系统的刚性和强度来确定。
选择进给量时应考虑到机床进给机构的强度、刀杆尺寸、刀片厚度、工件的直径和长度等。
在工艺系统的刚性和强度好的情况下,可选用大一些的进给量;
在刚性和强度较差的情况下,应适当减小进给量。
(3)切削速度的选择:
粗加工时,切削速度主要受刀具耐用度和机床功率的限制。
切削深度、进给量和切削速度三者决定了切削功率,在确定切削速度时必须考虑到机床的许用功率。
如超过了机床的许用功率,则应适当降低切削速度。
2.精加工时切削用量的选择原则
精加工时加工精度和表面质量要求较高,加工余量要小且均匀。
因此选择精加工的切削用量时应先考虑如何保证加工质量,并在此基础上提高生产效率。
精加工时的切削深度应根据粗加工留下的余量确定。
通常希望精加工余量不要留得太大,否则,当吃刀深度较大时,切削力增加较显著,影响加工质量。
精加工时限制进给量提高的主要因素是表面粗糙度。
进给量增大时,虽有利于断屑,但残留面积高度增大,切削力上升,表面质量下降。
切削速度提高时,切削变形减小,切削力有所下降,而且不会产生积屑瘤和鳞刺。
一般选用切削性能高的刀具材料和合理的几何参数,尽可能提高切削速度。
只有当切削速度受到工艺条件限制而不能提高时,才选用低速,以避开积屑瘤产生的范围。
由此可见,精加工时选用较小的吃刀深度ap和进给量f,并在保证合理刀具耐用度的前提下,选取尽可能高的切削速度V,以保证加工精度和表面质量,同时满足生产率的要求。
七、确定各工序的加工余量、计算工序尺寸及公差
1.确定加工余量
用查表法确定机械加工余量:
根据《机械制造学技术课程设计指导》(以下简称《设计指导》表1—9表1—44)表1平面加工的工序余量(mm)
工艺名称
单面余量
经济精度
工序尺寸
尺寸公差
表面粗糙度
精磨
0.1
IT7
40
0.8
精铣
1
IT9
40.2
6.3
则连杆两端面总的加工余量为:
A总=
=(A精铣+A精磨)
2=(1+0.1)
2=2.2mm
连杆铸造出来的的厚度为H=(40+2.2)=42.2mm
46.2÷
100×
0.2=0.0924所以毛坯尺寸为42.2±
0.09
毛坯的结构形状、尺寸应尽量与零件相近,以减少材料消耗,提高零件加工生产率,降低生产成本,以满足零件的质量要求。
2.确定工序尺寸及其公差
(根据《设计指导》表1—8表1—46)
表2大头孔各工序尺寸及其公差(铸造出来的大头孔为
74mm)
工序名称
直径余量
工序经
济精度
粗镗
2
IT12
72.4
12.5
半精镗
IT11
73.4
73.9
1.6
精镗
0.5
IT8
珩磨
IT6
74
72
0.4
(根据《设计指导》表1—8表1—46)
表3小头孔各工序尺寸及其公差
工序
名称
工序基
本余量
尺寸
公称尺寸
钻扩
4
37.6
33
铰
0.2
37.8
IT8
38
八、工时定额的计算
1.铣连杆两侧面(选用铣床X52K)
根据《切削用量手册》表1选取数据采用标准高速钢圆柱铣刀铣刀直径D=80mm齿数Z=8
根据《机械制造技术课程设计指导》表1-147表1-148
切削速度V=24m/min铣削宽度ae=2mmfm=0.5mm/r
则主轴转速n=1000v/
D=95.5r/min
按机床选取n=95r/min
则实际切削速度V=
Dn/1000=23.9m/s
Li:
刀具切入行程一般取2到3mm.Lo:
刀具切出行程;
一般取3到5mL3:
为单件小批量生产时的试切附加长度,对大批量汽车零件加工时,一般取L3=0,LW:
工件加工长度,单位mm.L=Li+Lo+L3+LW
Li=2mm,Lo=3mm,L3=0mm,LW=45mm
基本时间Tb=LI/nf=1.05min
2.加工小头孔
(1)扩小头孔
根据《机械制造技术课程设计指导》P49表1—70(选用摇臂钻床Z3025)
根据《机械制造技术课程设计指导》P107表1—162选取数据
扩刀直径D=37.6mm根据《机械切削工艺参数速查手册》P486表9-14切削速度V=58m/min
切削深度ap=2mm进给量f=0.8