球墨铸铁球化处理方法Word格式文档下载.docx
《球墨铸铁球化处理方法Word格式文档下载.docx》由会员分享,可在线阅读,更多相关《球墨铸铁球化处理方法Word格式文档下载.docx(15页珍藏版)》请在冰豆网上搜索。
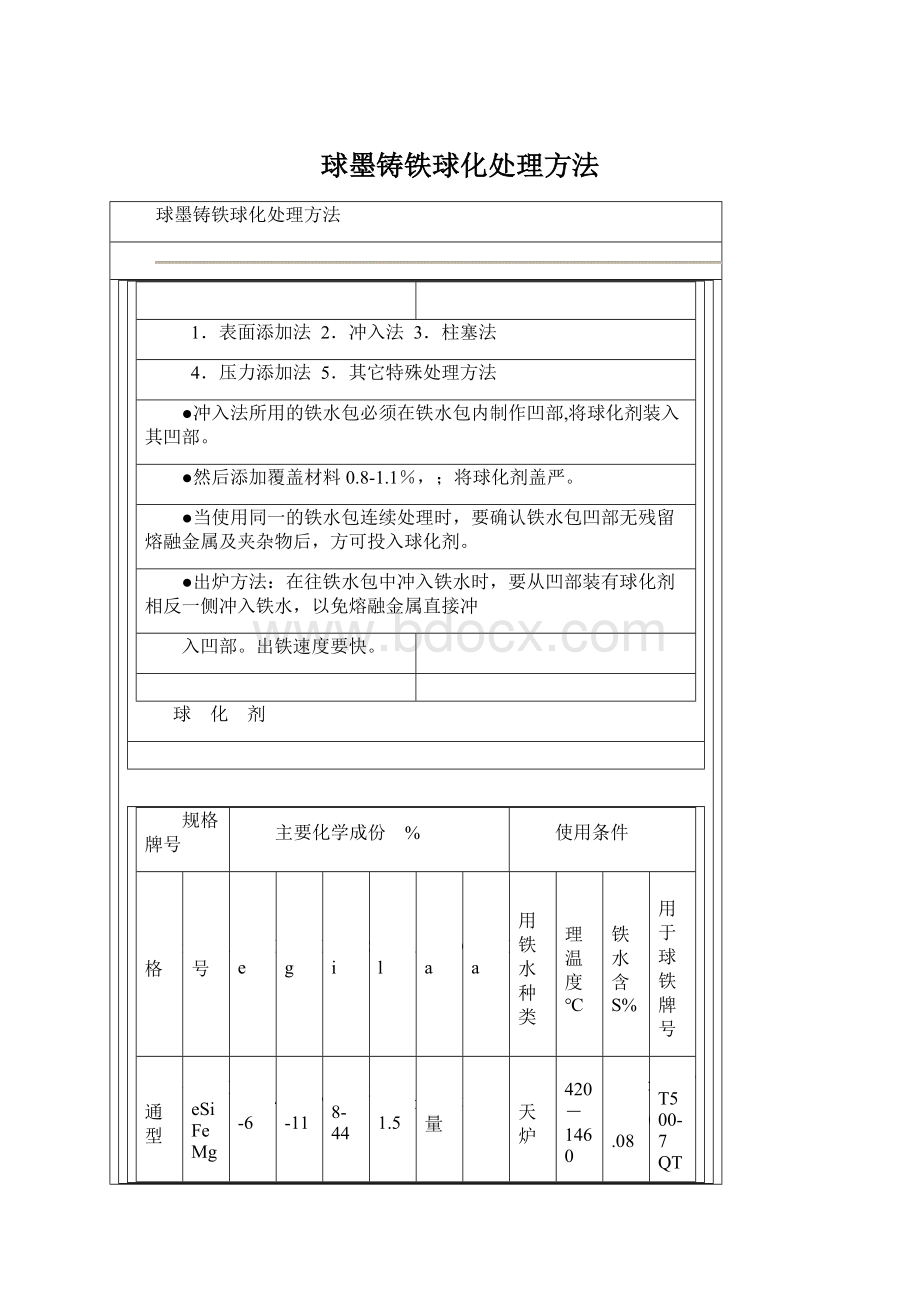
冲天炉
1420-1460
≤
0.08
QT500-7
QT600-3
ReSiFeMg7-8
6-8
7-9
复球铁素体型
ReSiFeMg3-8
2.5-3.5
冲天炉与电炉
1440-1520
QT400-18
QT450-10
ReSiFeMg2-7
1.5-2.5
电炉
0.04
ReSiFeMg1-6
0.5-1.5
5-7
深度脱硫铁水
≤0.015
厚大断面球铁专用
复球珠光体型
1420-1470
QT600-3
QT700-2
XX文库-让每个人平等地提升自我适量
ReSiFeMg1-7
钇基重稀土型
YReSiFeMg4-8
Y3-5
适用于对本体组织性能要求较高的铸件及厚大断面铸件
YReSiFeMg2-8
Y1-3
0.02
钇铈复合稀土型
YCeSiFeMg5-8
YCeSiFeMg3-8
2-4
☆
1420-1500
YCeSiFeMg1-8
0.015
注:
☆YCeSiFeMg3-8主要用于球铁件生产流水线上,球化处理后在保温浇注炉中存放30-60分钟场合;
Ca、Ba与Re、Mg含量可按用户要求特殊加工。
产品料度与包装:
通常粒度5-25mm, 也可按用户要求特殊加工,包装25Kg。
影响铸态球铁生产稳定性的因素很多,要稳定地生产球墨铸铁,必须在生产中把握好以下几点:
稳定的化学成分和铁液温度,准确的铁液量,合适的球化和孕育处理方法,以及可靠的炉前控制。
1设备选择
1.1熔炼设备选择
熔炼设备的选用首先是在满足生产需要的前提下,遵循高效、低耗的原则。
感应电炉的优点是:
加热速度快,炉子的热效率较高,氧化烧损较轻,吸收气体较少。
因此,用中频电炉熔炼,可避免增硫、磷问题,使铁水中P不大于0.07%、S不大于0.05%。
1.2球化包的确定
为了提高球化剂的吸收率,增加球化效果,球化处理包应比一般铁液包深。
球化包的高度与直径之比确定为2:
1。
2原材料选择
2.1炉料选择
球铁球化剂的加入效果条件是:
高碳、低硅、大孕育量。
为了稳定化学成分和有效地控制促进白口化元素和反球化元素,保证熔炼铁水的质量,选用张钢Z14生铁,其化学成分:
C>3.3%,Si1.25%~1.60%,P≤0.06%,S≤0.04%。
2.2球化剂的选择
球化剂的选用应根据熔炼设备的不同,即出铁温度及铁液的纯净度(如含硫量、氧化程度等)而定。
我国最常用的是稀土镁硅铁球化剂,采用这种球化剂处理时,由于合金中含硅量较高,可显著降低镁处理时反应的剧烈程度。
同时也能因增硅而有些孕育作用。
电炉生产时,因温度相对较高,所用球化剂的化学成分见表1。
表1球化剂FeSiMg8Re7化学成分
项目
出铁温度
/℃
S%
球化剂成分/%
Mg
Re
1420~1480
≤0.04
7.0~9.0
6.0~8.0
≤44.0
3炉前控制
3.1化学成分选择
球铁原铁液应高碳、低硅、低硫、低磷。
控制好硫的含量,是生产球铁的一个重要条件。
几种牌号的球铁的化学成分见表2。
3.2球化和孕育处理
球化剂加入量应根据铁液成分、铸件壁厚、球化剂成分和球化处理过程的吸收率等因素分析比较确定。
一般为1.6%~2.0%,若球化剂放置时间较长,则应适量多加。
球化反应控制的关键是镁的吸收率,温度高,反应激烈,时间短,镁烧损多,球化效果差;
温度低,反应平稳,时间长,镁吸收率
表2球铁化学成分%
牌号
C
Mn
S
P
QT400~18
球化前
球化后
3.6~4.1
0.9~1.2
≤0.4
≤0.05
≤0.07
3.5~4.0
2.6~3.2
≤0.02
QT450~10
3.5~3.9
2.5~3.0
QT600~3
3.6~3.9
0.6~0.8
3.5~3.8
2.2~2.6
QT700~2
2.1~2.5
高,球化效果好。
因此,一般在保证足够浇注温度的前提下,宜尽可能降低球化处理温度,控制在1420~1450℃。
球化剂要砸成小块,粒度一般在5~25mm,加在包底,再在上面加硅铁和铁屑。
孕育处理是球墨铸铁生产过程中的一个重要环节,它不仅促进石墨化,防止自由渗碳体和白口出现,而且有助于球化,并使石墨变得更细小,更圆整,分布均匀,从而提高球墨铸铁的力学性能。
孕育剂一般多采用FeSi75,其加入量根据对铸件的力学性能要求,一般为0.8%~1.0%。
孕育剂的粒度根据铁液量多少,一般砸成5~25mm的小块。
孕育剂应保持干净、干燥。
球化剂和孕育剂要在出铁前加入包中,在连续生产时,刚出完前一炉铁后,包很热,过早加入会使其粘结在包底而削弱球化和孕育效果。
为了延迟球化反应时间,增强球化和孕育效果,要在球化剂和孕育剂的上面覆盖一层铁屑。
球化处理的方法较多,一般多采用操作简便的冲入法处理球铁。
3.3球化效果炉前检验
炉前检验孕育、球化效果好坏,一般采用三角试样。
浇注三角试样,冷至暗红色,淬水冷却,砸断后观察断口。
断口银白色,尖端白口,中心有疏松,两侧凹缩,同时砸断时有电石气味,敲击声和钢相似,则球化良好,否则球化不良。
3.4浇注
由于球铁液容易出现球化衰退,因此,铁液球化处理后要尽快浇注,一般在处理后15min内浇注完毕,不会有球化衰退问题。
4结语
在生产中,用Z14号生铁作原材料,中频感应电炉熔化铁水,控制铁水化学成分为:
C3.5%~3.99%,Si1.2%~1.5%,P<0.06%,S<0.05%。
采用高度与直径之比为2∶1的球化包,把球化剂与孕育剂砸成10~20mm小块,球化剂按1.8%,孕育剂按0.9%比例,向包内先加球化剂,再加孕育剂,最后在上面覆盖干燥的铁屑。
铁水在炉中升温到1480℃左右出铁,待反应结束后10min内浇注完毕。
生产的φ530mm轧机用球墨铸铁梅花套管,其化学成分为:
C3.5%~3.8%,Si2.2%~2.6%,Mn0.6%~0.8%,S≤0.02%,P<0.07%,各项力学性能指标均达到较高要求,使用效果相当理想。
使用1年后证明,球墨铸铁本身具有高强度、耐磨、抗热疲劳等特性,能完全起到轴联接作用;
能大大减小噪音、改善工人劳动环境;
当过冷钢等超负荷情况下,梅花套管能自动破裂,起到过载安全保护作用;
还能显著延长轧辊和梅花轴的使用寿命。
同期相比,轧辊消耗降低8%,梅花轴消耗降低11%,连同设备维修工时减少而使同期产量的提高,共取得经济效益近7万元。
AAA*球化剂:
我国广泛采用的球化剂是稀土镁合金。
镁是重要的球化元素,但它密度小(1.73g/cm3)、沸点低(1120℃),若直接加入铁液,镁将浮于液面并立即沸腾,这不仅使镁的吸收率降低,也不够安全。
稀土元素包括铈(Ce)、镧(La)、镱(Yb)和钇(Y)等十七种元素。
稀土的沸点高于铁水温度,故加入铁水中没有沸腾现象,同时,稀土有着强烈的脱硫、去气能力,还能细化组织、改善铸造性能。
但稀土的球化作用较镁弱,单纯用稀土作球化剂时,石墨球不够圆整。
稀土镁合金(其中镁、稀土含量均小于10%,其余为硅和铁)综合了稀土和镁的优点,而且结合了我国的资源特点,用它作球化剂作用平稳、节约镁的用量,还能改善球铁的质量。
球化剂的加入量一般为铁水质量的1.0%~1.6%。
孕育剂:
促进铸铁石墨化,防止球化元素造成的白口倾向,使石墨球圆整、细化,改善球铁的力学性能。
常用的孕育剂为含硅75%的硅铁,加入量为铁水质量的0.4%~1.0%。
由于球化元素有较强的白口倾向,故球墨铸铁不适合铸造薄壁小件。
球化处理:
以冲入法最为普遍,如图1-50所示。
将球化剂放在铁液包的堤坝内,上面铺硅铁粉和稻草灰,以防球化剂上浮,并使其缓慢作用。
开始时,先将铁液包容量2/3左右的铁液冲入包内,使球化剂与铁液充分反应。
尔后,将孕育剂放在冲天炉出铁槽内,用剩余的1/3包铁液将其冲入包内,进行孕育。
BBB*由于原铁液含硫量较高,不可能达到<
0018%的要求,球化剂的加入量需考虑去硫耗镁量。
碳硫分析仪的快速测定,能及时提供原铁液的含硫量,试验中原铁液的含硫量在002%~003%,去硫耗镁量在00076%上下波动,这在工艺上是可以接受的。
球化剂的用量直接影响残余镁量的多少。
如果球化剂加入量过多,就会引起残余镁量过多,虽然不致于影响球化合格率(球径大小仍属正常),但是它会增加收缩,引起脆性。
同时由于原铁液含锰量偏高,球化剂加入量过多,较易出现碳化物,白口倾向严重,导致球数合格率的下降;
如果球化剂加入量过少,就会导致残余镁量不足,影响球化的合格率,球数合格率也会降低。
表1是在正常试验情况下的结果,并说明如下:
①球化剂加入量14%时,由于残余镁量不足,出现蠕虫状石墨;
②加入量18%时,由于残余镁量过多,出现碳化物,导致球数下降,不过二者球径大小仍合乎要求;
③球化合格率非球化率。
铸铁的热处理
铸铁生产除适当地选择优学成分以得到~定的组织外,热处理也是进一步调整和改进基体组织以提高铸铁性能的一种重要途径。
铸铁的热处理和钢的热处埋有相同之处
,也有不同之处。
铸铁的热处理一般不能改善原始组织中石墨的形态和分布状况。
对灰口铸铁来说,由于片状石墨所引起的应力集中效应是对铸铁性能起主导作用的困素,因此对灰口铸铁施以热处理的强化效果远不如钢和球铁那样显著。
故友口铸铁热处理工艺主要为退火、正火等。
对于球铁来说,由于石墨呈球状,对基体的割裂作用大大减轻,通过热处理可使基作组织充分发挥作用,从而可以显著改善球性的机械性能。
故球铁像钢一样,其热处理工艺有退火、正火、调质、多温淬火、感应加热淬火和表面化学热处理等。
铸铁的热处理工艺:
1.消除应力退火
由于铸件壁厚不均匀,在加热,冷却及相变过程中,会产生效应力和组织应力。
另外大型零件在机加工之后其内部也易残存应力,所有这些内应力都必须消除。
去应力退火通常的加热温度为500~550℃保温时间为2~8h,然后炉冷(灰口铁)或空冷(球铁)。
采用这种工艺可消除
铸件内应力的90~95%,但铸铁组织不发生变化。
若温度超过550℃或保温时间过长,反而会引起石墨化,使铸件强度和硬度降低。
2.消除铸件白口的高温石墨化退火
铸件冷却时,表层及薄截面处,往往产生白口。
白口组织硬而脆、加工性能差、易剥落。
因此必须采用退火(或正火)的方法消除白口组织。
退火工艺为:
加热到550-950℃保温2~5
h,随后炉冷到500—550℃再出炉空冷。
在高温保温期间
,游高渗碳体和共晶渗碳体分解为石墨和A,在随后护冷过程中二次渗碳体和共析渗碳体也分解,发生石墨化过程。
由于渗碳体的分解,导致硬度下降,从而提高了切削加工性。
3.球铁的正火
球铁正火的目的是为了获得珠光体基体组织,并细化晶粒,均匀组织,以提高铸件的机械性能。
有时正火也是球铁表面淬火在组织上的准备、正
火分高温正火和低温正火。
高温正火温度一般不超过950~980℃,低温正火一般加热到共折温度区间820~860℃。
正火之后一般还需进行四人处理,以消除正火时产生的内应力。
4.球铁的淬火及回火
为了提高球铁的机械性能,一般铸件加热到Afc1以上30~50℃(Afc1代表加热时A形成终了温度)
,保温后淬入油中,得到马氏体组织。
为了适当降低淬火后的残余应力,一般淬火后应进行回火,低温回火组织为回火马氏作加残留贝氏体再加球状石墨。
这种组织耐磨性好
,用于要求高耐磨性,高强度的零件。
中温回火温度为350—500℃回火后组织为回火屈氏体加球状石墨,适用于要求耐磨性好、具有一定效稳定性和弹性的厚件。
高温
回火温度为500—60D℃,回火后组织为回火索氏作加球状石墨,具有韧性和强度结合良好的综合性能,因此在生产中广泛应用。
5.球铁的多温淬火
球铁经等温淬火后可以获得高强度,同时兼有较好的塑性和韧性。
多温淬火加热温度的选择主要考虑使原始组织全部A化、不残留F,同时也避免A晶粒长大。
加热温度一般采用Afc1以上30~50℃,等温处理温度为0~350℃以保证获得具有综合机械性能的下贝氏体组织。
稀土镁铝球铁等
温淬火后σb=1200~1400MPa,αk=3~3.6J/cm2,HRC=47~51。
但应注意等温淬火后再加一道回火工序。
6.表面淬火
为了提高某些铸件的表面硬度、耐磨性及疲劳强度,可采用表面淬火。
灰铸铁及球铁铸件均可进行表面淬火。
一般采用高(中)
频感应加热表面淬火和电接触表面淬火。
7.化学热处理
对于要求表面耐磨或抗氧化、耐腐蚀的铸件,可以采用类似于钢的化学热处理工艺,如气体软氯化、氯化、渗硼、渗硫等处理。
铸铁的熔炼方法及其特点
铸铁是含碳量大于2.11或者组织中具有共晶组织的铁碳合金。
工业上所用的铸铁,实际上都不是简单的铁一碳二元合金,而是以铁、碳、硅为主要元素的多元合金。
铸铁的成分范围大致为:
C2.4-4.0%,Si0.6-3.0%,Mn0.2-1.2%,P0.1-1.2%,S0.08-0.15%。
有时还加入各种合金元素,以便获得具有各种性能的合金铸铁。
根据碳在铸铁中存在的形态不同,通常可将铸铁分为白口铸铁、灰口铸铁及麻口铸铁。
而灰铸铁中又可根据石墨的形态不同而分为普通灰铸铁,蠕虫状石黑铸铁,球黑铸铁以及可锻铸铁。
灰铸铁通常是指具有片状石墨的灰口铸铁,这中铸铁具有一定的机械性能、良好的铸造性能以及其它多方面的优良性能,因而在机械制造中业获得最广泛的应用。
表1为灰铸铁的新的国家标准。
该标准是以灰铸铁的抗拉强度作为分级依据的。
由于灰铸铁对冷却速率的敏感性(壁厚效应),同一种牌号铸铁在不同铸件壁厚条件下的实际强度有很大的差别(薄壁与厚壁之间在强度上的差别达50-80MPa)。
表1
灰铸铁分级
抗拉强度MPa(kg/mm2)
HT100
≥100(10.2)
HT150
≥150(15.3)
HT200
≥200(20.4)
HT250
≥250(25.5)
HT300
≥300(30.6)
HT350
≥350(35.7)
2
球墨铸铁及蠕墨铸铁
球墨铸铁和蠕墨铸铁一般是用稀土镁合金对铁液进行处理,以改善石墨形态,从而得到比灰铸铁有更高机械性能的铸铁。
球墨铸铁依照其基体和性能特点而分为六种:
即铁素体(高韧性)球墨铸铁,珠光体(高强度)球墨铸铁,贝氏体(耐磨)球墨铸铁,奥氏体一贝氏体(耐磨)球墨铸铁,马氏体一奥氏体(抗磨)球墨铸铁及奥氏体(耐热、耐蚀)球墨铸铁。
蠕墨铸铁具有不同比例的珠光体—铁素体基体组织。
铸铁性能与其石墨的蠕化程度(蠕化率)及基体有关。
在石墨蠕化良好条件下,珠光体蠕墨铸铁的强度和硬度较高,耐磨性强。
适于制造耐磨零件,如汽车的刹车鼓等。
而铁素体蠕墨铸铁的导热性较好,在高温作用下,不存在珠光体分解问题,组织较稳定,适用于制造在高温下工作、需要有良好的抗热疲劳能力、导热性的零件,如内燃机汽缸盖、进排气岐管等。
3
可锻铸铁
可锻铸铁是将白口铸铁通过固态石墨化热处理(包括有或无脱碳过程)得到的具有团絮状石墨的铁碳合金。
采用不同的热处理方法,可以得到具有不同组织和性能的可锻铸铁,即黑心可锻铸铁、珠光体可锻铸铁和白心可锻铸铁。
当将白口铸铁毛坯件在密封的退火炉中进行热处理,即在中性炉气条件下退火时,得到的铸铁组织中有呈团絮状的石墨(退火碳)存在。
这种石墨虽不很圆整和紧密,但它对基体的割裂作用则比灰铸铁中的片状石墨要小得多,因此它能使铸铁得到较高的强度及良好的韧性。
铸铁的基体可以通过热处理来加以控制。
使之成为铁素体或珠光体。
用这种方法得到的铁素体基体可锻铸铁因组织中有石墨存在,因而铸铁的断面呈暗灰色,而在表层经常有薄的脱碳层呈浅灰色,故通称为黑心可锻铸铁。
而珠光体可锻铸铁则是以其基体命名的。
当将白口铸铁毛坯件在氧化性质的炉气条件下进行退火时,铸件断面上从外层到心部,发生强烈的氧化和脱碳。
在完全脱碳层中无石墨存在,铸铁的组织为铸素体。
实际上,在小断面尺寸条件下,铸铁的组织基本上为单一的铁素体和退火碳。
而在大断面尺寸条件下,表层为铁素体,中间区域为珠光体和铁素体及退火碳,而心部区域则为珠光体及退火碳(间或有少量铁素体)。
这种铸铁断面由于其心部区域有发亮的光泽,而表层色泽较暗,故通称为白心可锻铸铁。
5
铸铁的熔炼
9.1熔炼对保证铸件质量的重要性
熔炼铁液是生产铸铁件的重要环节。
铸件质量包括内在质量、外观质量以及是否形成缺陷等,这些都与铁液方面因素有直接的关系。
如铁液的流动性、薄壁和结构复杂铸件的成型性以及冷隔缺陷等受铁液温度的影响,而熔炼的铁液化学成分是否符合要求,则对铸件的机械性能有直接的影响。
铁液中的气体和非金属夹杂物含量不仅影响铸铁的强度和铸件的致密度,而且还与铸件形成气孔、裂纹等缺陷有关。
随着机械制造科学的发展,对铸铁提出薄壁、高强度的要求,铸件的最小壁厚由过去4~6mm减小至2~3mm,这要求相应提高铁液浇注温度。
铁液温度还对铸铁件的内在质量有重要的影响,如灰铸铁件的质量指标(GZ),即与铁液温度有显明的关系。
在球墨铸铁生产方面,熔炼出铁液的温度及原始含硫量成为球化及孕育处理有否成功的先决条件。
9.2对铁液质量的基本要求
1.出炉温度
不同牌号灰铸铁件的浇注温度范围大致为1330-14100C。
在一般情况下,铁液的出炉温度至少比浇注温度提高500C,故根据铸铁牌号(自HT100至HT350)和铸件结构条件的具体情况,铁液出炉温度应不低于1380-14600C。
当需要浇注特薄(2-4mm)铸件时,出炉温度还应提高20-300C。
为了满足浇注铸件的需要,不同牌号可锻铸铁的出炉温度应不低于1460-14800C。
对球墨铸铁及其它变质处理的铸铁,在其球化一孕育处理过程中铁液的温度会有显著的下降,为了补偿铁液的温度损失,需相应提高铁液的出炉温度。
2.化学成分
熔炼得到的铁液化学成分需要满足铸件的规格要求。
用冲天炉熔炼时,配料计算是保证铁水化学成分合乎要求的首要环节。
即根据铁水化学成分的要求,考虑冲天炉在熔炼过程中元素的变化和炉料的实际情况,计算出各种金属炉料的配合比例。
各种牌号铸铁要求的化学成分随铸件壁厚和铸造方法而异。
例如,HT20-40铸铁的化学成分范围为:
C3.3-3.5%、Si1.5-2.0%、Mn0.5-0.8%、S<
0.12%、P<
0.25%。
用于配置HT20-40的金属料平均成分如表2。
表2配置HT20-40的金属料平均成分
炉料名称
化学成分%
Z15生铁
4.19
1.56
0.76
0.036
回炉料
3.28
1.88
0.66
0.07
0.098
废钢
0.15
0.35
0.50
0.05
所用铁合金为含硅45%硅铁,含锰75%的锰铁。
熔炼过程中元素的变化为:
Si–15%、Mn–20%、S+50%。
其配料计算如下:
(1)计算炉料中各元素的变化
a)炉料含碳量:
C铁水%=1.8%+0.5C炉料%
已知铁水所需的平均含碳量为3.4%,按上式算得C炉料%=3.2%;
b)炉料含硅量:
已知铁水所需的平均含硅量1.75%,硅的熔炼烧损为15%,则
Si炉料=1.75/(1-0.15)=2.06%;
c)炉料含锰量
已知Mn铁水=0.65%,熔炼烧损20%,故Mn炉料=0.65/(1-0.20)=0.81%;
d)炉料含硫量
已知S铁水=0.12%,增硫50%,则:
S炉料=0.12/(1+0.5)=0.08%;
e)炉料含磷量
磷在熔炼过程中变化不大,P炉料=P铁水<
0.25%
综合上列计算结果,所需配置的炉料平均化学成分为:
C炉料3.2%、Si炉料2.06%、Mn炉料0.81%、S炉料<
0.08%、P炉料<
(2)初步确定炉料配比