塑料软包装生产质量影响因素Word格式文档下载.docx
《塑料软包装生产质量影响因素Word格式文档下载.docx》由会员分享,可在线阅读,更多相关《塑料软包装生产质量影响因素Word格式文档下载.docx(7页珍藏版)》请在冰豆网上搜索。
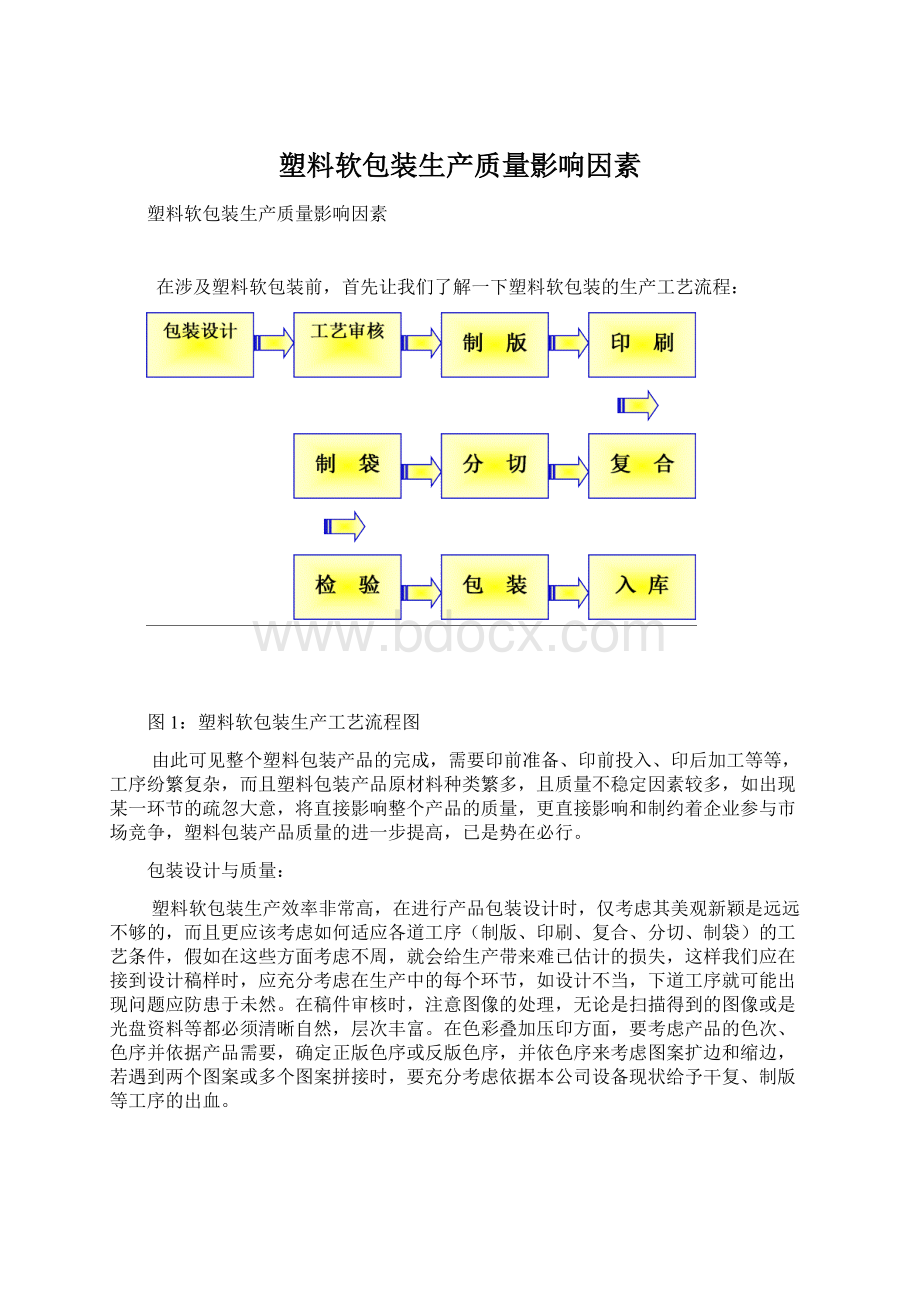
尽量避免采用10%以下的网点,因为在软包装印刷中由于使用的油墨挥发速度不同,加之刮刀对印版的磨损造成印刷品过程中网点的损失,
10%以下的网点几乎无法再现。
在产品设计中应结合本厂印刷主机实际现状,在审核样稿时应充分考虑印机机械走版等因素,结合客户要求或国标中(GB7707-87)的有关条款,修改每色之间的套印误差,减少或避免因设计和审核不当带来的产品质量问题。
在风琴袋(或T型袋)设计时应考虑制袋机和操作员工的技能水平,在折叠处应避开实地和层次的结缝及主图案和主色调平稳过渡,那怕稍有跑边、歪斜对整体设计效果和质量都不会有太大的影响。
工艺制定与质量:
作为塑料包装企业生产或技术管理人员,只有熟悉于加工的产品,才能制定合理的加工方案,正确指导操作员工生产出好的产品达到合格的质量要求。
工艺技术管理人员在接到样稿时应参入评审,在评审和制定工艺要求时,首先要了解工艺要求、客户要求、技术要求和所需材料的品质,并对照加工指令单认真复核来样和所有要求,确认加工时能否达到和满足加工单指定的要求。
在复合包装的生产过程中,印刷是生产的第一道工序,也是最重要的工序,因为衡量一个包装产品的档次,印刷质量首当其中,所以印刷工艺的制定是软包装生产关键之一。
制定详细的加工方案:
技术要求、质量标准、包括加工顺序、工艺方法、材料搭配等等是否满足内在物的需求,然后将方案细分到每一工序。
做好以上工作不仅可以预先排除影响质量的因素,而且还可以有的放失,检查和杜绝前工序出现的漏洞和险患。
印刷控制与质量:
印刷操作员工在接到下达的加工指令单时,首先应仔细了解其产品要求,确定印刷方式,塑料薄膜的印刷有二种方式:
表印和里印。
表印是与纸张相似的方式,以白色为第一色,是由浅色到深色依次排列;
里印则是透明塑料薄膜特有的印刷方式,是运用反向图文的印刷在被印刷材料的正面表现正像图案的一种印刷方式,是由深色到浅色依次排列。
由于里印更加光亮美观、色彩鲜艳并经过复合加工后牢固耐磨、不掉色、不粘连,因此软包装印刷中基本采用里印工艺生产。
在日常的生产过程中,印刷作为产品的第一道工序,印刷薄膜的表面张力检测至关重要,当然在材料进货检验中绝大多数厂家在入库时已完成了此项检验,但为了防止印刷品问题的出现,在使用每卷印刷基材时,最好再检测一次,因表面张力的好坏对油墨附着力、后工序生产都有直接的影响,所以一般薄膜在生产时都要经过表面电晕检测。
印版质量的检测,通常情况下印刷操作员工只能进行外观质量的检测,真正印版质量的好坏取决于制版供应商的内控和品控来满足印刷质量的要求,印刷企业对印版的检测通常只能进行外观质量的检测,铬层的外观有无任何划伤和撞伤的痕迹,表面应光洁平整,光洁度要达到
Δ8~Δ10级。
上机后印版的同心度等,当印版图案和印刷效果无法满足产品需要时,只有重新返工达到印刷和客户需求。
铬层硬度关系到印版滚筒的耐印率,印版镀铬硬度应达到HV750-1000。
油墨的选择是塑料凹版质量控制的重点,油墨质量的检测根据印刷要求,油墨在塑料产品上的质量地位是至关无上的。
好的油墨印出好的产品,这是塑料软包印刷行业的共识。
选择凹印油墨时,首先应确认被印刷基材———印刷条件———印刷效果———加工条件———最终产品用途等诸多要素,如何控制油墨质量取决于油墨生产厂家,那么印刷厂家应掌握主动权,在选择使用上应对它的颜色色相、粘度、细度、附着力、适用性能等指标进行检测控制,这样才能达到和满足印刷的需要。
套印误差、刀丝、油印等是印刷中常见的缺陷,其现象是在多色套印过程中,每一色不能完全重叠,有一定的偏差,如果偏差超过规定要求(GB7707-87正面图案≤0.3mm,背面图案≤0.5mm),就成为不合格品。
造成以上误差因素有人员因素———设备因素———印版因素———操作工艺等因素,因为这些误差是客观存在的,要使其控制在一定的范围内,就要求操作员工要有极强的工作能力。
印刷是一项细致的工作,必须做到有:
三心:
责任心、用心、细心;
三快:
眼快(及时盯台、及时发现),腿快(发现问题、及时到位),手快(注意安全、及时调整);
三勤:
勤加(定时查粘度、及时加溶剂),勤查(勤查质量、观查设备运行状况),勤看(对照标准样检查)。
三检、三签样:
自检:
由印刷机长对打出样张进行来样、标样及指令单对照检查,查尺寸、文字、图案、颜色是否符合要求,确认后再签字。
首检:
通过自检后由工序检验员或生产管理人员进行首次检查确认,符合所有要求后签字确认。
复检:
由检验员对照标样、来样进行重复检查发现问题及时通知机台人员整改、确认无误后签字,并依据所有签字样张做好巡检依据,我们把它叫做印刷签样制度缺一方签字,机台应无权生产,这样可以杜绝因工艺审核、印刷调整等不到位所造成的质量损失。
应将三快、三勤、三检三签样形成制度化、规范化管理。
还有印刷压力的控制、印刷张力的控制、烘道温度的调节、稀释剂的调配、油墨粘度控制、印刷色差的控制等等都与印刷操作员工的技能等有关。
这些方面的控制有的涉及专业知识,绝大部分是靠我们平时操作的经验积累。
建议大家做到
“勤笔勉思”,就是把我们平时遇到的问题、解决的办法、成功与否的样张都一一做好记录,遇到相同的问题时,可及时借鉴。
干式复合与质量:
复合工序是塑料软包装的灵魂,它在于性能的叠加,这也是复合生产技术核心所在。
复合工序作为塑料软包装的关键工序,它质量的好坏直接关系到产品的投入和产品合格率,它工艺复杂、操作技能要求高。
在此首次让我们了解一下干式复合的工艺流程(见下图):
图2:
干式复合的工艺流程图
我们在了解上述流程后,首先应对基材进行检测,表面张力是否达到要求,放卷张力系统
———复合张力系统———收卷张力系统是否符合质量要求,张力控制是复合工艺中最重要的工艺条件之一,它包括三部分内容:
一是张力初始值的设定,二是张力匹配关系,三是锥度的设定。
张力控制不当可造成膜卷曲、发皱、制袋困难、剥离强度下降、制袋变形等质量问题。
粘合剂的选择是干式复合质量把关的重要环节之一,因为使用的粘合剂是将两种和两种以上的基材经涂覆后粘合在一起,粘合剂在干复生产中的用量少,但对复合膜质量性能有较为重要的影响,它决定了复合膜的剥离强度、透明度、热封强度、耐热性、抗介质性等。
因此,我们在选择粘合剂时应根据产品最终性能来确定使用粘合剂。
在确定粘合剂后,涂胶系统控制,使产品涂覆干基固含量应保证在3g/m2左右为宜。
烘箱干燥控制是干式复合中的主要因素,干燥直接影响到复合的剥离强度、透明度,通过干燥系统将涂布在基材上的粘合剂中的溶剂加热蒸发并抽出,干燥温度设定主要基于基材的耐热性,机械线速度,通常情况下,温度设定为三段:
第一段为
50~60℃;
第二段为65~75℃;
第三段为75~80℃,温度一定是梯级递增。
热覆合辊温度一般控制在85~90℃之间为宜,必要时根据实际情况调节。
由于选择粘合剂和操作的不当造成产品报废的现象屡见不鲜,还应根据产品内在物及包装要求检查相应的基材指标,通过熟化后检测剥离强度。
这些指标的检测往往被一些软包装企业所忽视。
复合最终质量的好坏与剥离强度的关系与制袋封焊强度的关系,有关直接的关联。
熟化也叫固化,就是把已复合好的膜放进熟化室(烘房),使聚氨酯粘合剂的主剂和固化剂反应交联并被复合基材表面相互作用的过程,熟化的目的就是使主剂和固化剂在一定时间内充分反应,达到最佳复合强度。
熟化控制主要是温度和时间。
有些企业为了满足客户的交货时间要求,提高固化温度,缩短固化时间来提前交货,有的导致产品质量不合格和报废。
因为粘合剂生产厂家的质量和特性的不同,建议以粘合剂说明书中所要求的温度和时间控制,尽量不宜提前出熟化室。
复合中环境温度对溶剂的挥发、胶液的涂布状态有一定的影响,环境温度在20~28℃最为适宜的范围。
湿度对干式复合的影响较大,一般湿度控制在50~75%较为适宜。
当湿度过低时易产生静电火花,危险性较大,当湿度过高随乙脂的挥发,使涂布辊、胶盘、导辊等温度下降形成大的水汽凝结成水珠,这样会极大的影响粘合剂的性能,过高的湿度也会消耗大量的固化剂,造成剥离强度下降或固化剂不足,所以遇湿度过高时,控制环境并适量增加一些固化剂使之达到产品要求。
制袋控制与质量:
复合软包装材料要制成各种式样的包装袋才能使用。
制袋有两种,一种是包装厂家采用卷膜在灌装机上成型,产品的包装袋另一种是由专业制袋机制成包装袋后再装填内容物。
由于专业制袋机控制精确,袋形整齐美观,变化大、袋形多,因此在相当多的产品中都选择专业制袋机制袋。
因为选择了机械制袋,那么制袋热封强度(又称封焊强度)是制袋最主要的质量隐患。
所谓热封,即指塑料薄膜在机械传动过程中由专用的热封刀具焊缝,达到一定的牢度,从而满足不同内装物的包装要求。
热封质量是衡量复合包装的最主要的项目之一,因为热封效果不好,直接影响到包装内容物质诸如保质期等。
影响热封程度的因素有:
热封材料的种类、厚度以及材质质量都有决定性影响,我们常用的内层材料有:
LDPE、CPE、CPP、EVA以及一些离子型树脂的共挤或共混改性薄膜等,它们一般厚度为20~80um,热封强度是各种材料熔融温度的终合,各种材料的熔融温度直接决定复合袋的最低热封温度,而热封温度对热封强度的影响最直接,在实际生产过程中,封焊压力、封焊时间(频率)、冷却过程、复合剥离强度等等都容易影响复合袋热封强度,造成热封复合袋子热封强度偏差的因素还有很多,还需要我们在实际生产过程中不断总结提高。
还有诸如包装袋前后片图案不齐,上下、左右不对称,封焊边有花斑、气泡、尺寸误差、热封膜皱等等质量缺陷,总之能否生产出精美而上档次的包装袋与印刷、复合、制袋有着千丝万缕的必然关系。
全员质量意识、实施规范生产:
产品质量是生产出来的、不是检验出来的。
真正合格的产品是靠全体生产管理、技术管理、质量监控和全体员工共同合作生产出来的,只有所有参与生产的人员质量意识提高,并严格依照相关的产品标准、质量检验规程进行生产和控制,产品质量的提高才能有保证,企业才能在激烈的市场竞争中立于不败之地。
要提高全员质量标准意识,各岗位人员必须做到以下几点。
1.认真学习工艺要求、技术标准,掌握本岗位质量标准,熟悉和了解上下工序质量标准。
2.学以致用,树立自觉的质量意识,用所学的质量标准指导生产,检验产品,克服处处依赖别人,以及凡事要工序管理员、机长或相关管理人员点头才行的心理。
人人都要主动肩负自己所在环节的产品质量的职责。
3.严格按照生产工艺标准实施生产,使日常生产管理工作规范化、程序化、制度化,消灭生产中的主观行为和随意行为。
实事证明制度标准完善后,关键还在于落实、有制度无检查落实等于白做,而落实则要靠大家的协作和努力。
进行严格的质量检查:
检查是保证生产质量不可或缺的依据和途径,否则质量无从谈起。
1.首检:
即各道工序的车长检查自己的产品,否则质量无从谈起。
2.层层检查:
主要抓巡检,检查到实处不搞形式,做到事前控制的目的。
下工序对上工序的检查如此层层把关,树立全局观念确保产品最终合格。
3.抽样检查:
因印刷产品生产的特殊性,不可能在材料中途进行检测,那么如何做好抽样检查这就需要我们动脑筋、想办法做到生产和专职质检人员对各工序状况进行控制检查,发现问题及时纠正。
作为一种监督机制推动产品质量的提高,制定和完善相应的考核制度,做到制度公开化、规范化、人性化,只有质量和产量挂钩,实施质量否决制,才能彻底根除员工“轻质量、重产量”的思想。
建立产品工艺档案、确保产品质量:
随着技术、市场的发展,软包装印刷加工也面临着越来越多的新材料、新工艺、新产品的引进应用及新问题的解决处理,企业员工应不仅要熟悉设备性能、操作技能还应了解新工艺的要求。
相关部门和人员应做好不同工艺、不同材料加工时出现各种情况的数字记录,并对其进行留样,保存建立相应的工艺档案,通过对工艺档案进行归纳、整理、总结为生产提供可靠的、可操作性的指导和帮助。
对检查中发现的质量问题,对制定的解决方法进行认真记录,建立产品质量档案,确定影响产品质量因素的瓶劲,有针对性的加以解决,有效避免同样错误的产生。
产品工艺质量档案作为生产管理、质量管理的第一手资料,有助于我们少走弯路,实现产品质量的良性循环。
软包装产品质量的提高当然也离不开广大客户的理解和支持。
如果客户能在产品的设计和原材料选用上多与印刷企业沟通,相信产品质量会得到更大的提升。
以上只是作者对软包装产品质量影响因素的点滴浅析,相信会对相关企业带来启示,共同发展塑料包装产品,提高塑料包装档次是每个软包装生产人员的共同责任和愿望,愿我们的产品能够满足客户的需要,为客户的产品景上添花。
(注:
素材和资料部分来自网络,供参考。
请预览后才下载,期待你的好评与关注!
)