氨合成岗位培训教材.docx
《氨合成岗位培训教材.docx》由会员分享,可在线阅读,更多相关《氨合成岗位培训教材.docx(90页珍藏版)》请在冰豆网上搜索。
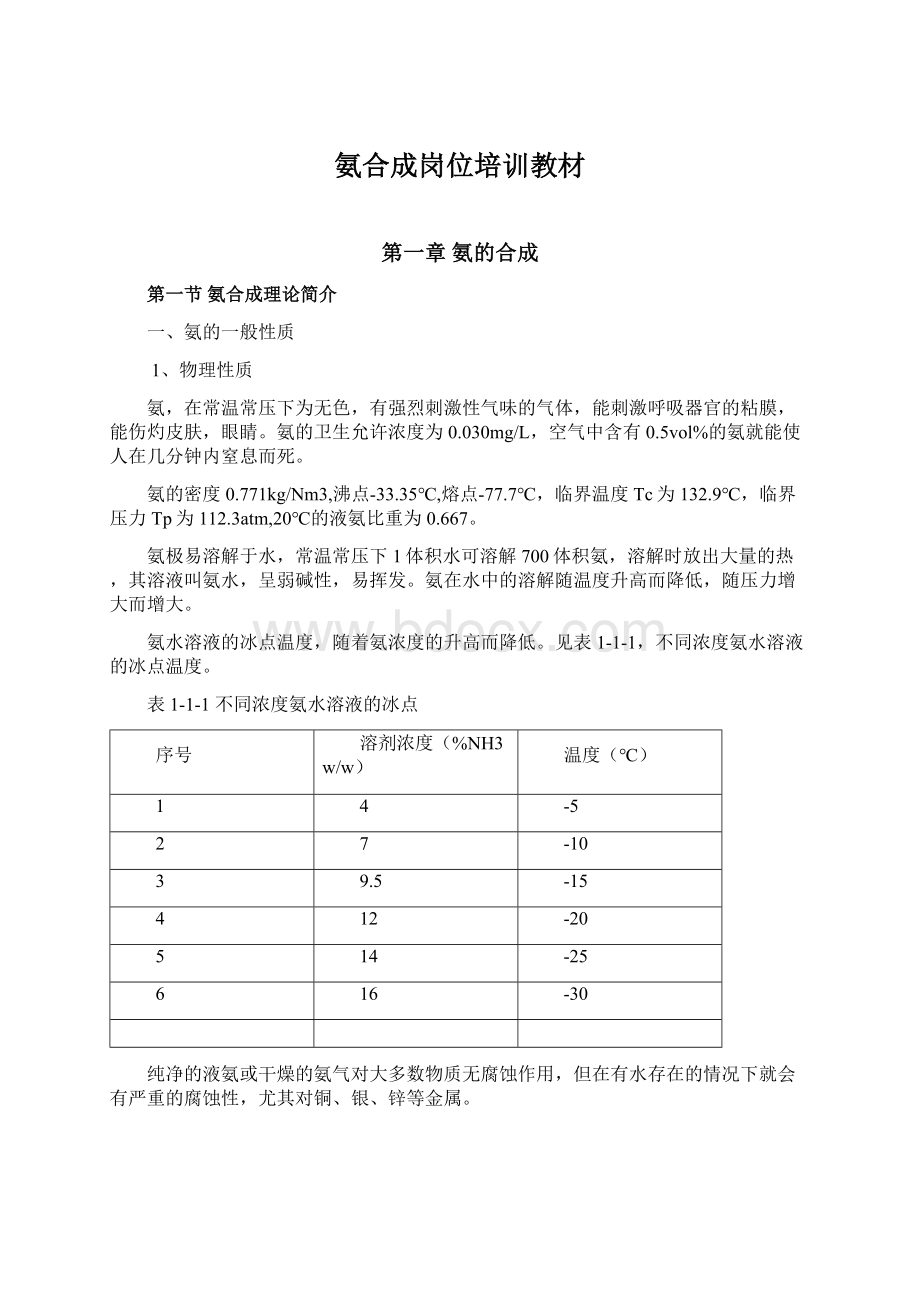
氨合成岗位培训教材
第一章氨的合成
第一节氨合成理论简介
一、氨的一般性质
1、物理性质
氨,在常温常压下为无色,有强烈刺激性气味的气体,能刺激呼吸器官的粘膜,能伤灼皮肤,眼睛。
氨的卫生允许浓度为0.030mg/L,空气中含有0.5vol%的氨就能使人在几分钟内窒息而死。
氨的密度0.771kg/Nm3,沸点-33.35℃,熔点-77.7℃,临界温度Tc为132.9℃,临界压力Tp为112.3atm,20℃的液氨比重为0.667。
氨极易溶解于水,常温常压下1体积水可溶解700体积氨,溶解时放出大量的热,其溶液叫氨水,呈弱碱性,易挥发。
氨在水中的溶解随温度升高而降低,随压力增大而增大。
氨水溶液的冰点温度,随着氨浓度的升高而降低。
见表1-1-1,不同浓度氨水溶液的冰点温度。
表1-1-1不同浓度氨水溶液的冰点
序号
溶剂浓度(%NH3w/w)
温度(℃)
1
4
-5
2
7
-10
3
9.5
-15
4
12
-20
5
14
-25
6
16
-30
纯净的液氨或干燥的氨气对大多数物质无腐蚀作用,但在有水存在的情况下就会有严重的腐蚀性,尤其对铜、银、锌等金属。
当空气中含氨为9~57vo1%时,其燃点为9.7~1000℃在常温常压下氨与空气混合后遇火爆炸范围为15.5~28%或13.5~82%(纯氧气中)。
气氨自燃点为630℃,与氧气反应生成N2和H2O。
2、化学性质
氨是活泼性化合物,能与酸及酸性氧化物反应生成盐,还能和许多有机物反应。
另外,液氨还能同活泼金属发生一些特别的反应,甚至一起作为有机反应的催化剂。
二、氨合成反应的机理
氨合成是一个可逆,体积减小的反应。
它和其他化学反应一样,由于温度对反应速度和化学平衡影响的双重性,因此,必须选择最适宜的温度,并在高压下采用催化剂才能使反应有效地进行。
反应式为:
平衡常数:
式中P、Pi—分别为总压和i组分平衡分压,MPa
yi—i组分的平衡组成(摩尔分数)
KP—化学平衡常数,MPa-1
氨合成反应的机理,符合多项催化原理。
但详细机理尚不完全清楚,其反应步骤一般认为分下面七步:
(1)氢气和氮气的混合物从气相主体通过物理作用力吸附在铁催化剂的外表面。
此为反应物的外扩散;
(2)绝大部分吸附在铁催化剂上的氢和氧,自外表面向催化剂毛细孔内部扩散,到达内表面。
此为反应物的内扩散;
(3)氢和氮分子在催化剂主要是内表面的晶面上垂直地进行化学吸附,消弱了H2和N2分子的化学键,其中一部份化学键断裂生成吸附态的活性氢、氮原子。
即:
H2=2H﹡,N2=2N﹡。
(4)吸附态的高能量活性氢、氮原子,在催化剂内表面上发生化学反应,生成一系列中间化合物后,形成吸附态的高能量活性氨(NH3)﹡。
即:
(5)吸附态的高能量活性氨在催化剂表面上发生化学解吸,生成氨,(NH3)﹡→NH3+能量;
(6)解吸后的氨从毛细孔内部向催化剂外表面扩散。
此为产物的内扩散;
(7)氨分子从催化剂外表面扩散到气相主体。
此为产物的外扩散。
以上第(3)、(4)、(5)步属于化学过程,第
(1)、
(2)、(6)、(7)步属于物理过程。
其中第(3)步反应物分子的化学吸附是最慢的一步,决定着整个合成氨反应的速度。
第二节工艺条件对合成氨反应的影响
氨反应进行的程度直接取决于各个工艺条件。
在实际生产中,反应不可能达到平衡,合成工艺参数的选择除了考虑平衡氨含量外,还要综合考虑反应速率、催化剂使用特性以及系统的生产能力、原料和能量消耗等,以期达到良好的技术经济指标。
氨合成的工艺参数一般指压力、温度、空间速度、氢氮比、惰气含量和初始氨含量。
一、压力
从化学平衡和反应速度的角度看,在高压下进行氨合成反应,有利于向生成氨的方向移动,反应速度也随压力升高而提高。
所以压力增加时,平衡氨浓度和反应速度都增加,既有利于氮氢合成率提高,又使催化剂用量减少。
而且压力高时,气体中的氨浓度增加,气氨冷凝温度也相应提高,将氨冷凝所需冷量亦随之减少、有利于循环气中分离出氨和简化流程。
但是压力过高给设备制造和维修都带来困难,目前大型氨厂氮氢合成气压缩都使用离心压缩机,最终压力越高,离心压缩机的设计越困难,因氮氢气密度很小,压力越高则压缩态的流量越小,依靠离心力的叶轮设计也越困难,因此,大型氨厂的合成压力通常为10~27MPa。
生产上选择操作压力的主要依据是能量消耗以及包括能量消耗、原料费用、设备投资在内的所谓综合费用。
也就是说主要取决于技术经济效果。
能量消耗主要包括原料气压缩功、循环气压缩功和氨分离的冷冻功。
图1-2-1表示出合成系统能量消耗随操作压力的变化关系。
提高操作压力,原料气压缩功增加,循环气压缩功和氨分离冷冻功却减少。
总能量消耗在15~30MPa区间相差不大,原料气压缩功太大;压力过低则循环气压缩功、氨分离冷冻功又太高。
综合费用是综合性的经济技术指标,它不仅取决于操作压力,还与生产流程(主要指氨分离时的冷凝级数)、装置的生产能力、操作条件、原料及动力以及设备的价格、热量的综合利用等因素有关。
图1-2-2为装置能力日产1500吨氨,采用三种不同流程时综合费用与操作压力的关系。
通常原料气和设备的费用对过程的经济指标影响较大,在10~35MPa范围内,压力提高综合费用下降,主要原因在于低压下操作设备投资与原料气消耗均增加。
对不同的流程来说,低于20MPa时,三级冷凝流程的综合费用较低;20~28MPa二级冷凝流程(一级水冷、一级氨冷)的综合费用较低;更高压力时采用一级冷凝(仅一级水冷)的流程综合费用最低。
图1-2-2综合费用与操作压力的关系
(以30MPa,二级冷凝流程的综合费用为基准)
图中:
实线——三级冷凝流程;虚线——二级冷凝流程;点划线——一级冷凝流程
二、温度
氨合成为一可逆放热反应,温度对化学平衡和反应速度都有影响,温度升高,反应速度增加,但平衡氨浓度却下降。
由于氨合成是在催化剂存在下进行的,而催化剂又只有在一定的温度范围内才能显示出它的催化活性,温度太高会破坏催化剂的结构,降低催化剂寿命。
因比,仅仅从催化剂的使用来考虑,就必须有一个温度范围。
工业上使用的氨合成催化剂的活性温度为360~550℃,因此,氨的合成反应温度由所选用的催化剂型号和氨合成塔的结构决定。
床层进口温度的低限由催化剂起始反应温度所决定。
床层最高温度则由催化剂的耐热温度决定,目前工业上使用的氨合成催化剂起始反应温度已降低至350~360℃,而耐热温度则不超过550℃。
在催化剂活性温度范围选用操作温度应尽可能接近最适宜温度。
所谓“最适宜温度”(或最佳温度)是任一可逆放热的催化剂都存在的一个温度。
它取决于参与反应的气体组成、压力以及催化剂的活性。
若将反应式(1-2-1)对温度进行求导,并使其为零,即可得最适宜反应温度的条件为:
(KP)m==(1-2-1)
式中(KP)m—最适宜温度下的平衡常数的值;
(KP)s—与气体组成相平衡的温度(即平衡温度)下的平衡常数的值;
E1、E2—分别为包括内扩散因素在内的正、逆反应表观活化能(例如:
氨合成塔上层催化剂反应速率为内扩散控制时,E1将等于本征正反应活化能的1/2,在下层催化剂内扩散影响不大时,E1将等于本征正反应活化能,E2则利用E1-2△HR来计算)。
将式(1-2-2)中(KP)m和(KP)s表示为最适宜温度和平衡温度下正、逆反应速率常数与温度的关系,化简可得
(1-2-2)
图1-2-3为平衡温度曲线和某催化剂的最适宜温度曲线。
在一定压力下,氨含量提高,相应的平衡温度与最适宜温度下降。
惰性气体含量增高,对应于一定氨含量的平衡温度下降。
如图中1、2曲线所示,相应的最适宜温度亦下降,如6、7曲线所示。
氢、氮比对最适宜温度的变化规律同于对平衡温度的影响。
图1-2-3H2:
N2=3的条件下平衡温度与最适宜温度(1atm=0.10MPa)
l、2、3、4、5——分别为(300atm,yio=12%)、(300atm,yio=15%)、(200atm,yio=15%)、
(200atm,yio=18%)、(150atm,yio=13%)的平衡温度曲线;
6、7、8、9、10——分别为(300atm,yio=12%)、(300atm,yio=15%)、(200atm,yio=15%)、
(200atm,yio=18%)、(150atm,yio=13%)的最适宜温度曲线
压力改变时,最适宜温度亦相应变化,气体组成一定,压力愈高,平衡温度与最适宜温度愈高。
事实上,一定系统的平衡温度与最适宜温度有相应的变化关系,压力、气体组成都不影响Tm与Te之间的相对关系,只要催化剂的活性不变,E1和E2一定,Te与Tm之间的相对关系即不会改变。
催化剂活性高时(性能良好或使用初期),E1和E2均低,由于二者的差值不变,E2/E1比值增大,由(1—2)式Te与Tm差值增大,最适宜温度下降。
反之,活性差时(催化剂性能差、衰老或中毒)最适宣温度上升。
准确地计算最适宜温度,需先得出给定粒度的催化剂在各种不同温度及氨含量下的内表面利用率ξ,然后在rNH3ξ—T图上求取最大极值点的温度。
考虑到内扩散的影响,实际反应的最适宜温度较图1—3中的数据略低。
从理论上看,合成反应按最适宜温度曲线进行时,催化剂用量最少、合成效率最高。
但由于反应初期,合成反应速度很高,故实现最适宜温度不是主要问题,而实际上受种种条件的限制不可做到这一点。
例如,氨合成塔进气氨含量为4%(P—30MPa,yio=12%),由图1-2-3可知Tm已超过600℃,也就是说催化剂床层入口温度应高于600℃,而后床层轴向温度逐渐下降,此外温度分布递减的反应器在工艺实施上也不尽合理,它不能利用反应热使反应过程自热进行,需额外加高温热源预热反应气体以保证入口的温度。
所以,在床层的前半段不可能按最适宜温度操作。
在床层的后半段,氨含量已经比较高,反应温度依最适宜温度曲线操作是有可能的。
氨合成反应温度,一般控制在400~500℃之间(依催化剂类型而定)。
催化剂床层的进口温度比较低,大于或等于催化剂使用温度的下限,依靠反应热床层温度迅速提高,而后温度再逐渐降低。
床层中温度最高点,称为“热点”,不应超过催化剂的使用温度。
到生产后期,催化剂活性已经下降,操作温度应适度提高。
氨合成是放热反应,如果不及时移走反应热就会使合成塔内温度愈来愈高,对氨的生成是不利的,催化剂和设备也不容许这样。
因此,最适温度希望随着反应的进行而降低,而实际情况正好相反。
为了解决这个问题,工业上采用了两种办法。
第一种办法是在催化剂床层布置冷却设备把热量连续移出,反应与冷却同时进行。
这种反应器叫连续换热式或内部换热式。
第二种办法是采用一种特制的合成塔,当反应进行到一定程度后,再设法使之冷却,然后在较低的温度下进行第二阶段的反应,反应与冷却交替进行。
这种反应器(合成塔)叫分段换热式或中间换热式。
在床层之间布置冷却器直接冷却,或是在床层之间补入一定数量的冷原料气直接冷却。
二者都叫冷激式。
这种合成塔的优点是结构简单可靠,便于采用自动控制。
大型合成氨厂的合成塔都是冷激式。
在理论上,它可以使温度按最适温度的要求随着反应的进行使温度逐步下降,但从每一个绝热段来讲,温度是不断上升的,与最适温度的要求不符合。
所以说这种结构的合成塔每单位体积催化剂的生产能力不如连续换热式反应器好。
三、合成塔进口气组成
1.氢氮比
如前所述,当氢氮比为3时,对于氨合成反应,可得最大平衡氨含量,但从动力学角度分析,最适宜氢氮比随氨含量的不同而变化。
反应初期,离平衡甚远,采用动力学方程式(1-2-3),并设惰性气体为零,=0.5:
(1-2-3)
对上式求极值:
解:
r=1.0,即反应初期最适宜氢氮比r为