典型液压传动系统实例分析课件Word文件下载.docx
《典型液压传动系统实例分析课件Word文件下载.docx》由会员分享,可在线阅读,更多相关《典型液压传动系统实例分析课件Word文件下载.docx(44页珍藏版)》请在冰豆网上搜索。
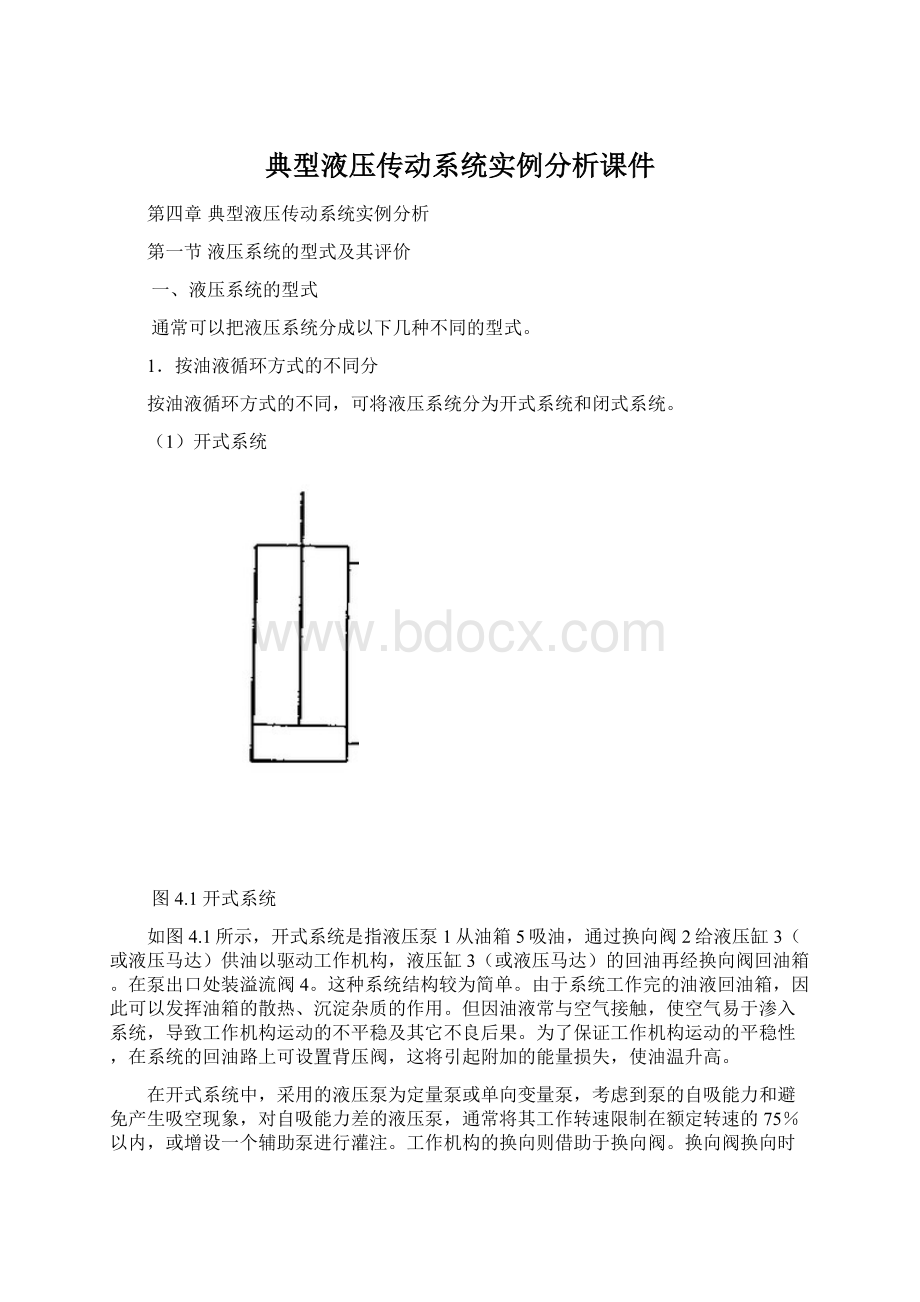
如大型液压挖掘机、液压起重机中的回转系统,全液压压路机的行走系统与振动系统中的执行元件均为液压马达。
闭式系统中执行元件为液压马达的另一优点是在起动和制动时,其最大起动力矩和制动力矩值相等。
2.按系统中液压泵的数目分
按系统中液压泵的数目可将其分为单泵系统、双泵系统和多泵系统。
(1)单泵系统
由一个液压泵向一个或一组执行元件供油的液压系统,即为单泵液压系统,如图4.3所示。
单泵系统适用于不需要进行多种复合动作的工程机械,如推土机、铲运机等铲土运输机械的液压系统。
对某些工程机械如液压挖掘机、液压起重机的工作循环中,既需要实现复合动作,又需要对这些动作能够进行单独调节,采用单泵系统显然是不够理想的。
为了更有效地利用发动机功率和提高工作性能,就必须采用双泵系统或多泵系统。
(2)双泵系统
图4.4为双泵液压系统图。
双泵液压系统实际上是两个单泵液压系统的组合。
每台泵可以分别向各自回路中的执行元件供油。
每台泵的功率是根据各自回路中所需的功率而定,这样可以保证进行复合动作。
图4.4双泵液压系统
1-双联液压泵;
2-换向阀;
3-多路换向阀;
4-变速阀;
5-先导阀;
6-行走马达;
7-缓冲制动阀;
8-回转马达;
9-回转马达换向阀
当系统中只需要进行单个动作而又要充分利用发动机功率时,可采用合流供油方式,即将两台液压泵的流量同时供给一个执行元件。
这样可使工作机构的运动速度加快。
这种双泵液压系统在中小型液压挖掘机和起重机中已被广泛采用。
(3)多泵系统
为了进一步改进液压挖掘机和液压起重机的性能,近年来在大型液压挖掘机和液压起重机中,开始采用三泵系统。
图4.5为三泵液压系统原理图。
这种三泵液压系统的特点是回转机构采用独立的闭式系统,而其它两个回路为开式系统。
这样,可以按照主机的工作情况,把不同的回路组合在一起,以获得主机最佳的工作性能。
3.按所用液压泵型式的不同分
按所用液压泵型式的不同,可将液压系统分为定量系统和变量系统。
(1)定量系统。
采用定量泵的液压系统,称为定量系统,如图4.3,图4.4所示。
定量系统中所用的液压泵为齿轮泵、叶片泵或柱塞泵。
图4.5三泵液压系统原理图图4.6定量系统与变量系统功率利用率比较
液压泵的功率是按理论功率
选取的。
对定量泵,当发动机转速一定时,流量Q也一定。
而压力是根据工作循环中需要克服的最大阻力确定的,因此液压系统工作时,液压泵功率是随工作阻力变化而改变的。
在一个工作循环中液压泵达到满功率的情况是非常少的。
据统计,在挖掘机中定量泵功率的平均利用率约为54~60%(图4.6)。
液压系统中液压泵的理论功率与发动机有效功率之比约为0.8~1.2。
对定量泵,其功率比值可取在l以上,但应小于发动机的功率储备,以免突然过载时造成发动机熄火而影响正常工作。
(2)变量系统
图4.7恒功率控制变量泵的功率特性曲线
变量系统中所用的液压泵为恒功率控制的轴向柱塞泵,泵的功率特性曲线如图4.7所示。
从图中可以看出,功率调节器中,控制活塞右面有压力油作用,控制活塞左面有弹簧力的作用,当泵的出口压力低于弹簧装置预紧压力时,弹簧装置未被压缩,液压泵的摆角处于最大角度,此时泵的排量也为最大。
随着液压泵出口压力的增高弹簧被压缩,液压泵的摆角也就随着减小,排量也就随之减少。
液压泵在出口压力和弹簧装置预压紧力相平衡时的位置,称为调节起始位置。
调节起始位置时,作用在功率调节器中控制活塞上的液压力称为起调压力。
当液压泵的出口压力大于起调压力时,由于调节器中弹簧压缩力与其行程有近似于双曲线的变化关系,因而在转速恒定时,液压泵出口压力与流量也呈近似于双曲线的变化。
这样液压泵在调节范围之内始终保持恒功率的工作特性。
由于液压泵的工作压力是随外载荷的大小而变化的,因此,可使工作机构的速度随外载荷的增大而减小,或随外载荷的减小而增大,使发动机功率在液压泵调节范围之内得到充分利用。
变量泵的起调压力p0是由弹簧装置的刚度和液压系统的要求决定的。
调节终了压力pmax是由液压系统决定、由安全阀调定。
相应于起调压力时的摆角为最大,相应于调节终了时的摆角为最小。
变量泵的优点是在调节范围之内,可以充分利用发动机的功率,缺点是结构和制造工艺复杂,成本高。
为了防止发动机因过载而突然熄火,一般将液压泵的理论功率与发动机有效功率之比限于0.8~l.0之间。
4.按向执行元件供油方式的不同分
按向执行元件供油方式的不同,可将液压系统分为串联系统和并联系统。
(1)串联系统
在系统中,当一台液压泵向一组执行元件供油时,上一个执行元件的回油即为下一个执行元件进油的液压系统称为串联系统,如图4.8。
在串联系统中,若液压泵输出的压力油以压力pl,流量Ql进入第一个执行元件,以压力p2、流量Q2进入第二个执行元件。
那么,在不考虑损失的情况下,对双作用单活塞杆液压缸,Ql≠Q2。
Q1、Q2与液压缸活塞的有效面积Sl、S2成正比,即
图4.8串联系统
(4—1)
在不考虑管路和执行元件中的能量损失时,第一个执行元件中的工作压力p1,取决于克服该执行元件上载荷所需的压力p′和第二个执行元件的工作压力p2,即:
p1=p′+p2(4—2)
这说明在串联系统中,每通过一个执行元件工作压力就要降低一次。
因此串联系统的特点是:
当主泵向多路阀控制的各执行元件供油时,只要液压泵出口压力足够,便可实现各执行元件的运动的复合。
但由于执行元件的压力是叠加的,所以克服外载荷的能力将随执行元件数量的增加而降低。
(2)并联系统
图4.9并联系统
并联系统是指在系统中,当一台液压泵同时向一组执行元件供油时,进入各执行元件的流量只是液压泵输出流量的一部分,如图4.9所示。
并联系统的特点是:
当主泵向多路阀所控制的各执行元件供油时,流量的分配是随各执行元件上外载荷的不同而变化,压力油首先进入外载荷较小的执行元件。
只有当各执行元件上外载荷相等时,才能实现同时动作。
液压泵的出口压力取决于外载荷小的执行元件上的压力与该油路上的压力损失之和。
由于并联系统在工作过程中只需克服一次外载荷,因此克服外载荷的能力较大。
除了上述的分类以外,按调速方法的不同,液压系统又有节流调速系统和容积调速系统之分。
这部分已在速度调节基本回路中介绍过,这里不再赘述。
二、液压系统的评价
随着液压技术的发展,液压传动在国内外工程机械、机床等方面应用越来越广泛。
任何一种机械的液压传动系统都应满足重量轻、体积小、结构简单、使用方便、效率高和质量好的要求。
其中尤应强调质量好和效率高,并在保证质量好、效率高的基础上应尽可能地采用先进技术。
液压机械性能的优劣,主要是取决于液压系统性能的好坏。
而液压系统性能的好坏则又以系统中所用元件的质量好坏和所选择的基本回路恰当与否为前提。
对一个液压系统的评价,应该从液压系统的效率、功率利用、调速范围和微调特性、振动和噪声等几个方面加以分析对比。
1.液压系统的效率
在保证主机性能要求的前提下,应该使液压系统具有尽可能高的效率。
液压系统效率的高低反映了液压系统中能量损失的多少。
这种能量损失最终是以热的形式出现,使系统的油温升高。
系统中引起能量损失的因素很多,主要有以下几个方面:
(1)换向阀在换向制动过程中出现的能量损失
在开式系统中工作机构的换向只能借助于换向阀封闭执行元件的回油路,先制动后换向。
当执行元件及其外载荷的惯性很大时,在制动过程中压力油和运动机构的惯性都迫使执行元件继续运动,同时压入回油腔的液体,使回油腔的压力增高,严重时可达几倍的工作压力。
液体在此高压作用下,将从换向阀或制动阀的开口缝隙中挤出,从而使运动机构的惯性能变为热耗,使系统的油温升高。
在一些换向频繁,载荷惯性很大的系统中,如挖掘机的回转系统,由于换向制动而产生的热耗是十分可观的,有可能成为系统发热的主要因素。
(2)元件本身的能量损失
元件的能量损失包括液压泵、液压马达、液压缸和控制元件等的能量损失,其中以泵和液压马达的损失为最大。
液压泵和液压马达中能量损失的多少,可用效率来表示。
液压泵和液压马达效率的高低,是作为其质量好坏的主要指标之一。
液压泵和液压马达的效率等于机械效率和容积效率的乘积,机械效率和容积效率是与多种因素有关的,如工作压力、转速和工作油液的粘度等。
一般,每一台液压泵和液压马达在一个额定的工作点,即在一定的压力和一定的转速下,具有最高的效率,当增加或降低转速和工作压力时,都会使效率下降。
管路和控制元件的结构,同样也可以影响能量损失的大小。
因为油液流动时的阻力与其流动状态有关,为了减少流动时的能量损失,可在结构上采取改进措施:
对于管件,可增大截面积以降低流动速度;
对于控制元件,可增大结构尺寸,以增大通流量。
但增加的结构尺寸超过一定数值时,就会影响到经济性。
此外,在控制元件的结构中,两个不同截面之间的过渡要圆滑以尽量减少摩擦损失。
(3)溢流损失
当液压系统工作时,工作压力超过溢流阀(安全阀或过载阀)的开启压力时,溢流阀开启,液压泵输出的流量全部或部分地通过溢流阀而溢流。
可能出现溢流阀溢流的工况有:
回转机构的启动与制动过程;
负载太大,液压缸中的工作压力超过溢流阀的开启压力而仍继续工作;
工作机构液压缸达到终点极限位置,而换向阀尚未改变工作位置。
在系统工作时,应尽量减少溢流损失。
这可从设计因素和操作因素上采取措施。
(4)背压损失
为了保证工作机构运动的平稳性,常在执行元件的回油路上设置背压阀。
背压越大,能量损失亦越大。
一般情况下液压马达的背压要比液压缸大;
低速液压马达的背压要比高速马达大。
为了减少因回油背压而引起的发热,在保证工作机构运动平稳性的条件下,尽可能减少回油背压,或利用这种背压做功。
综上所述,为了保证液压系统具有高的效率,必须控制和减少系统与元件的能量损失,亦即控制和减少系统总发热量。
2.功率利用
液压系统的功率利用反映了主机的生产率。
一般情况下,采用恒功率变量泵的变量系统其功率利用率要比定量系统高。
在双泵系统中,为提高功率利用率除采用变量系统外,还可采用合流供油。
目前,为了提高功率利用,在国外的工程机械液压系统中,对液压泵采用了零位起调,即在工作压力小于液压泵起调压力时,液压泵的流量为最小。
这样可以减少低压时的功率损失。
3.调速范围和微调特性
大多数液压机械其工作机构的载荷及速度的变化范围较大,这就要求液压系统应具有较大的调速范围。
不同机械其调速范围是不同的,即使在同一机械中,不同的工作机构其调速范围也不一样。
调速范围大小可以用速比i来衡量。
对液压马达:
(4—3)
式中nMmax——液压马达最大转速;
nMmin——液压马达最小转速。
对液压缸:
(4—4)
式中vGmax——液压缸最大运动速度;
vGmin——液压缸最小运动速度。
在调速范围内执行元件扭矩或推力的变化表示如下。
对液压马达,用扭矩比WM表示:
(4—5)
式中MMmax——液压马达最大输出扭矩;
MMmin——液压马达最小输出扭矩。
对液压缸,用推力比WG表示:
(4—6)
式中PGmax——液压缸最大推力(大腔);
PGmin——液压缸最小推力(大腔)。
微调特性反映了工作机构速度调节时的灵敏程度。
不同的工程机械对微调特性有不同的要求。
如铲土运输机械、挖掘机械对微调特性的要求不高,而有的机械如吊装用工程起重机对微调特性则有严格的要求。
4.振动和噪声
液压系统的振动和噪声是由组成系统各元件的振动和噪声引起,其中以泵和阀最严重。
振动与噪声给液压系统带来一系列不良后果,严重时液压系统将不能工作,因此必须对振动和噪声予以控制。
减少液压系统振动和噪声的关键是控制系统中各元件的振动和噪声,减少液压泵的流量脉动和压力脉动以及减少液压油在管路中的冲击。
第二节液压随动恒功率控制系统
液压随动恒功率系统的特点是可控制工作机始终在恒功率状态下工作。
这对提高时效、提高工作效率及提高设备的寿命都大有益处。
恒功率系统及其随动装置广泛应用于各行各业,这里以钻机的恒功率控制为例说明它的作用及原理。
石油钻井,依靠钻头产生的力矩M及钻头的转速n,进行钻进,当钻头碰到硬地层或钻压加大时,钻头上的负载增大,即转矩增大,此时,要求转速自动下降,当碰到软地层或钻压减小,钻头上的转矩减小,此时要求钻头的转速自动升高。
使其钻头上消耗的功率为恒定值,这就是恒功率钻进。
实现其恒功率钻进的液压系统叫恒功率控制系统。
这个控制系统是以液压随动为核心达到恒功率之目的,因而称之为液压随动恒功率控制系统。
如图4.10所示为钻井示意图。
图4.10钻井示意图
图4.11所示为液压随动恒功率控制系统图。
该系统由三套油路组成。
主系统由双向变量泵及马达组成,它驱动钻头转动,这是高压系统。
控制系统由低压定量泵组成,控制先导阀位移,其控制压力称为p控约在0~4.5MPa之间。
操纵系统由低压定量泵组成,操纵随动阀跟踪,其操纵压力称为p操约为1.5MPa。
图4.11中,由先导阀、随动阀组成的液压随动机构工作原理参看第三章容积调速一节。
图4.11中的恒功率阀如图4.12所示,其结构及原理介绍如下:
恒功率阀由平衡阀1,壳体2,平衡弹簧3,溢流阀弹簧4,锥阀5组成。
壳体上分别同p主、p控、p溢三条油路连接。
恒功率阀的职能就是使p控值的大小同p主值成反比。
当p主的压力为0时,弹簧4的预压力最强,要打开锥阀5的控制压力p控也最高。
当主油压力p主不断升高,打开锥阀卸压,压力p控不断降低,因而,p控的大小决定于p主的大小,两者的关系可由下式表示:
图4.11液压随动恒功率系统
p控
(4—7)
图4.11所示的恒功率控制系统的工作原理及操作规程如下:
(1)起动主油泵1,操纵油泵3,控制油泵2,三位四通电磁阀4不通电,此时电磁阀位于中位,先导阀随之位于中位,角等于0,主油泵空运转,无排量,马达不转,钻头不转,无钻进。
(2)按2DT通电,三位四通电磁换向阀右位进入系统。
先导阀、随动阀向左移动,设摆角为+,主油泵供油方向由AB,马达、钻头为正转。
若按1DT通电,三位四通电磁阀左位进入系统,先导阀、随动阀将向右移动,设摆角为-,主油泵供油方向由BA,马达钻头反转。
综上所述,1DT、2DT只决定钻头的转向。
钻头转速大小则要根据钻头上的扭矩大小而定。
(3)当钻头上的力矩M增加时,p主增加。
由于恒功率阀的作用,p主上升时,p控下降。
相应产生先导阀的位移S减小,随动阀跟随移动相同的位移S获得相应较小的和较小的排量,从而产生较小的转速。
(4)根据
(2)、(3)的传递关系,可实现恒功率的控制。
力矩与转速的变化过程:
若M↑、p主↑、p控↓、S↓α↓Q↓n↓
得M↑n↓
若M↓、p主↑、p控↓、S↑α↑Q↑n↑
得M↓n↑
得N=M↓·
n↑=M↑·
n↓=C
C表示恒定功率。
恒定功率曲线如图4.13所示。
(a)(b)
图4.12恒功率阀工作原理图4.13恒功率曲线
1-平衡阀;
2-壳体;
3-平衡弹簧;
4-溢流阀弹簧;
5-锥阀
第三节Baker修井机起升系统
图4.14所示为Baker修井机的起升系统,它是不压井修井作业机液压传动系统的一部分,用来提升、下放油管柱。
这套系统设计比较巧妙,使用元件不多,完成的功能多,即一个元件可完成几个功能,操作又集中,这些是该系统的设计特点。
该系统具有如下功能:
(1)液缸可以起下油管,在起下过程中管柱可在任一位置停止和锁紧。
(2)提放管柱时,要求实现上行快,下放慢。
(3)无级调速。
(4)调速换向集中在一个手柄上完成操作。
图4.14修井机起升系统
(5)系统有安全保护。
完成上述功能的工作原理:
(1)液缸的起、下、停、锁,是由操纵三位四通换向阀2来实现。
起动油泵,操纵换向阀2上位进入系统时,泵来的压力油经阀2,单向阀3进入油缸5,油缸油流不通,导致泵压上升,在液控单向阀4的控制油作用下,打开单向阀,使油缸5的回油路畅通,实现油管柱下放。
当阀2的下位进入系统时,泵来的油进入液控单向阀4,进入油缸下端,此时油缸的回油路不通,泵压上升,二位二通阀6的控制油路压力上升,使阀6的右位进入系统,则油缸上部的油经阀6进入油缸5的下部,使油缸实现上升,使阀2的中位进入系统,靠阀2的O型阀芯机能,使油管柱暂停不动。
单向阀3、液控单向阀4在弹簧作用下,球阀关闭,油缸5的进出油路不通,油管柱被锁止在某一位置。
(2)采用差动油路,实现油管柱下行慢、上行快。
按照油缸摆放方式,活塞杆朝上。
由于油缸下腔的活塞有效面积大,上腔活塞有效面积小,若给以同量供油,则油管柱上行慢,下行快,这同工况要求上起快下放慢正好相反,不能满足工况要求。
因此,在系统中采用差动油路实现工况要求。
差动基本回路属于速度控制基本回路,工作原理如图4.15所示。
Q1=Q泵+Q回(4—8)
采用差动油路,将油缸的回油Q回引入油缸另一腔,提高油缸的供油量,大大提高了活塞杆牵引速度。
在图4.14系统中,是通过二位二通阀6来实现油缸5的差动。
如图4.14所示,当阀2下位进入系统,泵来油经阀4进入油缸下腔,上腔回油路不通,阀6的控制油路油压升高,右位进入系统,油缸5上腔的油进入油缸的下腔,大大提高了上行速度,实现了工况要求。
在图4.14中,由换向阀2、二位二通液控阀8和梭形阀7组成调速回路。
如图4.16所示为梭形阀,它由壳体1、钢球2组成。
壳体上有三个孔A、B、C接油路管线。
两油路A、B谁的油压高谁就同C油路接通。
用换向阀2控制过流断面大小,控制泵供给油缸的流量,实现油缸的速度调节。
用二位二通阀8的控制油的压差控制溢流量Q的大小。
当操作人员将阀2全开(设阀2的上位进入系统)P、B的过流断面积为最大,P、B两点的压差最小,这两点压差分别反馈到二位二通阀8的两端。
由于P、B压差最小,阀8不开,处于不通状态,无泄流量,此时油缸以全速运行。
当操作人员将阀2开到最小,P、B的过流断面积最小,P、B两点的压差最大,这两点压差分别反馈到二位二通阀8的两端。
由于P、B压差最大,阀8开大溢流,此时油缸的牵引速度最小。
(a)(b)
图4.15差动回路图4.16梭形阀
(a)结构;
(b)两种元件符号
当阀2关闭,油缸被停止在某位置,油泵完全卸荷,阀8全开溢流。
由上述可知,阀2开口大小决定了对油缸的供油量和阀8的溢流量,即是决定了油缸的牵引速度。
Q阀=KApm(4—9)
Q泵=Q缸+Q溢(4—10)
(4)由上述可知,无论是油缸的起、下、停及速度调节,均由操作人员控制阀2即可实现。
(5)系统的安全由溢流阀9保护。
当系统压力没有超过安全压力时,溢流阀不开,超过安全压力时,溢流阀卸流降压,保护系统安全。
第四节推土机液压系统
推土机是土石机械之一。
适用于建筑、水利工程、修建路堑、平整场地、露天剥离等工程的刮削、堆积等作业。
在推挖重级土壤时,应预先松土。
与其它铲土运输机械相比,由于工作装置即推土板的运动较为简单,故其液压系统也较为简单。
下面以TY180推土机为例,分析推土机的液压系统。
一、TY180推土机主要性能参数
图4.17TY180推土机工作装置液压系统
1-油箱;
2-滤油器;
3-液压泵;
4-溢流阀;
5-精滤油器;
6-安全阀;
7-推土缸换向阀;
8-松土缸换向阀;
9-过载阀;
10-补油单向阀;
11-松土缸;
12-推土缸
最大牵引力184kN
最大顶推力165kN
最大爬坡能力30°
在横向坡度工作能力20°
转向液压泵型号CB-F40C
操纵系统液压泵型式CB-F32C
推土板容量4.37m3
推土板提升速度0.56m/s
推土板最大提升高度1300mm
推土板最大切土深度530mm
推土板回转角25°
二、TY180液压系统分析
图4.18TY180推土机转向系统
1—油箱;
2—粗滤油器;
3—液压泵;
4—精滤油器;
5—安全阀;
6—右离合器;
7、9—控制阀;
8—调压阀;
10—左离合器;
11—背压阀;
12—变速箱
TY180推土机除了工作装置液压系统外,还有转向液压系统。
工作装置液压系统如图4.17所示。
所有的操纵阀、压力控制阀均置于工作油箱内。
液压缸包括推土缸和松土缸,组成串联油路。
液压系统压力为14MPa,由溢流阀控制,溢流阀为先导型。
操纵松土器的换向阀为三位五通换向阀,操纵推土板的换向阀为四位五通换向阀,
多一个浮动位置。
这是为了使推土机在平整场地时,推土板能随地面的起伏而作上下浮动。
为了防止松土器因外载荷过大而损坏液压元件,特设过载阀。
TY180推土机采用液压转向。
转向系统如图4.18所示。
系统压力为1MPa。
液压油从后桥箱内经粗滤器进入液压泵,再经精滤器(内设安全阀)进入转向控制阀。
转向时可以操纵转向阀使压力油进入左或右离合器油路,打开左边或右边的常闭式离合器进行转向。
不转向时,油从旁路回油箱。
在回油路上有0.15MPa背压阀,以此压力对变速箱进行强制润滑。
第五节单斗挖掘机液压系统
一、概述
单斗液压挖掘机由工作装置、回转机构和行走机构三大部分组成。
工作装置包括动臂、斗杆以及根据施工需要而可以更换的各种换装设备,如正铲、反铲、装载斗及抓斗等。
以单斗挖掘机的反铲为例,每一工作循环的主要动作包括:
挖掘——一般以斗杆缸动作为主,用铲