桩基淤泥溶洞裂隙等处理专项施工方案Word文件下载.docx
《桩基淤泥溶洞裂隙等处理专项施工方案Word文件下载.docx》由会员分享,可在线阅读,更多相关《桩基淤泥溶洞裂隙等处理专项施工方案Word文件下载.docx(10页珍藏版)》请在冰豆网上搜索。
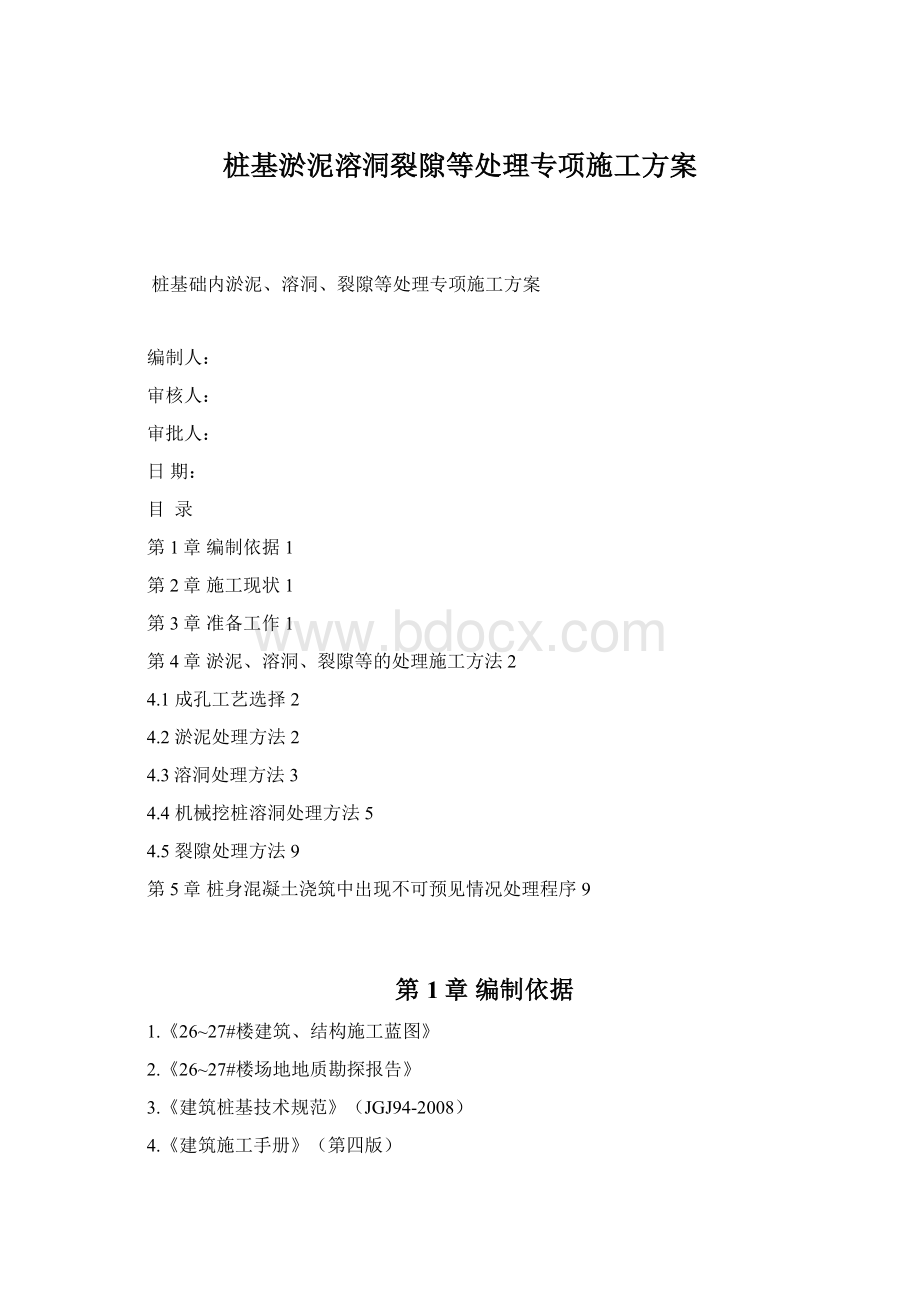
第3章准备工作1
第4章淤泥、溶洞、裂隙等的处理施工方法2
4.1成孔工艺选择2
4.2淤泥处理方法2
4.3溶洞处理方法3
4.4机械挖桩溶洞处理方法5
4.5裂隙处理方法9
第5章桩身混凝土浇筑中出现不可预见情况处理程序9
第1章编制依据
1.《26~27#楼建筑、结构施工蓝图》
2.《26~27#楼场地地质勘探报告》
3.《建筑桩基技术规范》(JGJ94-2008)
4.《建筑施工手册》(第四版)
5.《建筑地基基础设计规范》(GB50007-2002)
6.《建筑地基基础施工质量验收规范》(GB50202-2002)
7.《贵州建筑地基基础设计规范》DB22/45-2004
8.《建筑工程施工质量验收统一标准》(GB50300-2002)
9.《建筑施工安全技术规范》
10.本工程特点、施工条件、现场具体情况。
第2章施工现状
26~27#楼自4月29日场地移交至今已施工到一定阶段,上部土层已基本开挖到位,大部分桩已进入岩层施工。
目前,在施工中遇到的问题主要有溶洞、淤泥、裂隙等,现有7根有溶洞的桩已改为机械成孔,其它还有部分桩存在较深淤泥,如ZH-20、ZH-29、ZH-30、ZH-33、ZH-78等,这几根桩从井口往下约5-10m不等的位置遇淤泥,淤泥较稀,木枋、钢筋等置于其上均自己下沉,人无法站立其上作业,用3米长钢筋往下探,不见底,四周约2~3m范围有淤泥。
淤泥、溶洞处理是本工程施工的重点和难点,也是影响本工程施工工期的关键。
通过对地勘报告内容阅读和分析,本工程溶洞部分由软塑状粘土夹风化残块充填,部分无充填。
为保证桩基承载力,要求在桩基施工中采取揭穿顶板下挖,将桩基支撑于溶洞下部完整中风化灰岩中。
第3章准备工作
3.1要求现场管理人员和挖桩操作人员必须熟悉每个桩孔的地质柱状图,清楚淤泥、溶洞的位置、大小、充填情况等,做好安全技术交底,保证施工人员安全;
3.2施工现场一定要有处理漏浆的备用机具设备,如挖掘机、铲车、泥头车、吊车等,以免发生险情无法实行溶洞处理措施,造成不必要的人员伤亡和财产损失;
3.3注意在冲孔过程中,桩位附近只能堆放用于填充溶洞的粘土及片石。
粘土的质量好、含砂率低才能制造优质泥浆。
片石尺寸大约300mm×
300mm,方便填充。
桩孔附近设立防护范围,避免施工机械在防护范围内通过,减少对桩孔护壁的压力和振动。
不能将机械和材料放置在桩孔附近,防止大面积塌孔;
第4章淤泥、溶洞、裂隙等的处理施工方法
4.1成孔工艺选择
(1)对地质条件特别复杂的不能保证作业人员安全的人工挖孔桩采用机械成孔;
(2)对能保证作业人员安全的人工挖孔桩内出现淤泥、溶洞、流砂、裂隙等复杂
地质现象的采用针对性特殊处理方法;
4.2淤泥处理方法
在淤泥层向下按500mm一模作业,淤泥情况较恶劣时,按200~300mm一模,桩侧面做法分两层施工;
(1)外侧支挡结构:
用木枋、模板固定外模,木枋支撑呈梅花桩排列,长度不小于500mm,再用钢模做内模,浇筑300mm厚成C30毛石砼;
(2)护壁:
厚度250mm,B14@100单层双向,C30砼,竖向筋与上节护壁钢筋搭接250mm。
淤泥处环境较潮湿,护壁砼浇筑时,加入早强剂,可以加快砼凝固,按此方法,大约每两天可做1模,具体做法如下图示:
图1淤泥处理剖面图
图2淤泥处理平面图
4.3溶洞处理方法
进入溶洞层后,要根据溶洞高度和周边地质情况分别采取不同的措施:
(1)若溶洞较小,不方便砌砖,采取灌注C30砼封严实,再按蓝图做护壁。
(2)溶高小于2m:
首先将积水抽干,确保没有有毒有害气体之后用标砖砌外圈,370mm~500mm厚,具体厚度根据现场情况确定,要求其具有足够的强度和刚度,以防止灌注砼时护壁被挤垮,然后立模浇注钢筋混凝土护壁,此处护壁加厚,为200mm,配筋按图纸。
溶洞处理完成后,继续向下挖进。
如图3所示。
图3溶高小于2m溶洞处理详图
(3)若溶洞较高(大于2m),无法按正常护壁施工和砌筑砖围挡,为保证工人操作的安全,采用钢护筒。
钢护筒采用4mm钢板,现场焊接制作,直径略小于砼护壁内径,利用砼护壁作支点,用小型油压千斤顶将钢护筒逐渐压入土中,阻挡流泥。
按3m一节,上下节护筒搭接长度1m。
护筒第一节露出溶洞顶1m,最后一节进入底层溶洞底1m,上下节两端与钢筋砼护壁竖向筋焊接。
要求做好钢护筒后才能继续往下施工。
如图4、图5所示。
图4溶洞较高时处理详图
图5钢护筒详图
4.4机械挖桩溶洞处理方法
(1)范围小,溶高小于1m,没有充填物或洞内注满水的溶洞,采用抛填片石、粘土等,使溶洞范围形成护壁后,再继续施工。
桩身钢筋笼制作时,按实际测量确定溶洞上下各1m范围内相应的桩身钢筋笼位置,在其定位筋上焊接厚4mm的钢板圆筒,保证成桩砼的质量;
图6溶高<
1m的溶洞处理详图
(2)溶高在1~3m,且洞内为填充或半填充状态的溶洞,采取先填充碎石、砂混合物和注水泥浆,然后用小冲程冲击碎石挤压到溶洞边形成水泥浆碎石外护壁,水泥浆碎石空隙初步堵塞后,停止冲击。
24h后,待水泥强度达到2.5MPa后,再继续冲击,穿过溶洞。
桩身钢筋笼制作时,按实际测量确定溶洞上下各1m范围内相应的桩身钢筋笼位置,在其定位筋上焊接厚4mm的钢板圆筒,保证成桩砼的质量,如图7所示:
图71m<溶高<3m的溶洞(填充或半填充)处理详图
(3)溶高在1~3m,且洞内无填充或填充物较少的溶洞:
向洞内填满砼干料,待固结体达到2.5MPa后即可进行冲孔施工。
砼干料采用P42.5普通硅酸盐水泥拌制,若洞内空间容积大,导水性强,可在砼干料中添加一定量的水玻璃,固结稳定后,再继续施工。
桩身钢筋笼制作时,按实际测量确定溶洞上下各1m范围内相应的桩身钢筋笼位置,在其定位筋上焊接厚4mm的钢板圆筒,保证成桩砼的质量。
如图8所示:
图81m<溶高<3m的溶洞(无填充或较少填充)处理详图
(4)溶高在3~5m的单个或多层溶洞,而多层溶洞间的间距较小:
采用钢护筒穿越处理。
先用冲击锤进行冲孔、扩孔,然后采用振锤把钢护筒振沉至溶洞底部,钢护筒下面要进入最底层溶洞底部1m,上面要露出顶层溶洞顶1m。
如图9所示:
图93m≤溶高<5m的单个或多层溶洞处理详图
(5)溶高大于5m的多层溶洞,且溶洞间距较大时:
采用套内护筒法施工,即用内护筒穿过溶洞的方法进行施工。
内护筒内径比桩径大200mm,内护筒外径小于外护筒内径50mm。
若遇第二层溶洞,第二层溶洞的内护筒外径比上层内护筒内径小50mm,并以此类推。
由于溶洞较高,护筒采用4mm钢板,现场焊接制作,按3m一节,上下节护筒搭接长度1m,在孔内焊接。
护筒第一节露出溶洞顶1m,最后一节进入底层溶洞底1m。
如图10、图11所示:
图10溶高>
5m的单个或多层溶洞处理详图
图11套内护筒详图
4.5裂隙处理方法
(1)人工挖桩裂隙处理:
若裂隙较小,不方便砌砖,采取灌注C30砼封严实,再按蓝图做护壁,
(2)机械挖桩裂隙处理
——采用粘土和袋装水泥填塞溶洞,防渗堵漏:
向孔内回填大量粘土,目的是堵漏,同时堵住岩石裂隙,防止漏浆,粘土可不必装袋,直接倒入孔内,水泥则需整袋抛入,使其沉底,如此反复处理保证继续成孔。
这样,堵住了漏浆,堵住了溶洞,保证泥浆质量且能正常返浆,正常进尺,砼时在灌注砼时,不会出现大量超灌,且能保证成桩质量;
——对于一些溶漕、溶沟、小裂隙等,冲孔时可采取投放片石、碎石夹粘土或投入整袋水泥堵塞起到护壁作用,保证泥浆不流失,使钻孔顺利通过岩溶区。
第5章桩身混凝土浇筑中出现不可预见情况处理程序
本工程根据具体桩孔实际情况采用不同方式浇筑桩身砼:
当孔底积水小于10cm时,采用常规砼浇注方法,当孔底积水大于10cm,且涌水量较大难以抽干时,采用导管法进行水下砼施工,并严格按水下砼施工操作规程进行。
桩身混凝土在浇筑过程中如果出现因溶洞、裂隙等造成的砼理论与实际浇筑数量不符,要迅速通知监理和业主单位到现场确认,分析其现象的发生原因,及时要求业主单位联系设计、地勘单位到现场确定处理方案,保证桩基础的结构安全。
现场做好原始资料的收集与整理工作,及时办理现场发生工程量的签证工作。