焚烧系统运行管理手册Word文档下载推荐.docx
《焚烧系统运行管理手册Word文档下载推荐.docx》由会员分享,可在线阅读,更多相关《焚烧系统运行管理手册Word文档下载推荐.docx(45页珍藏版)》请在冰豆网上搜索。
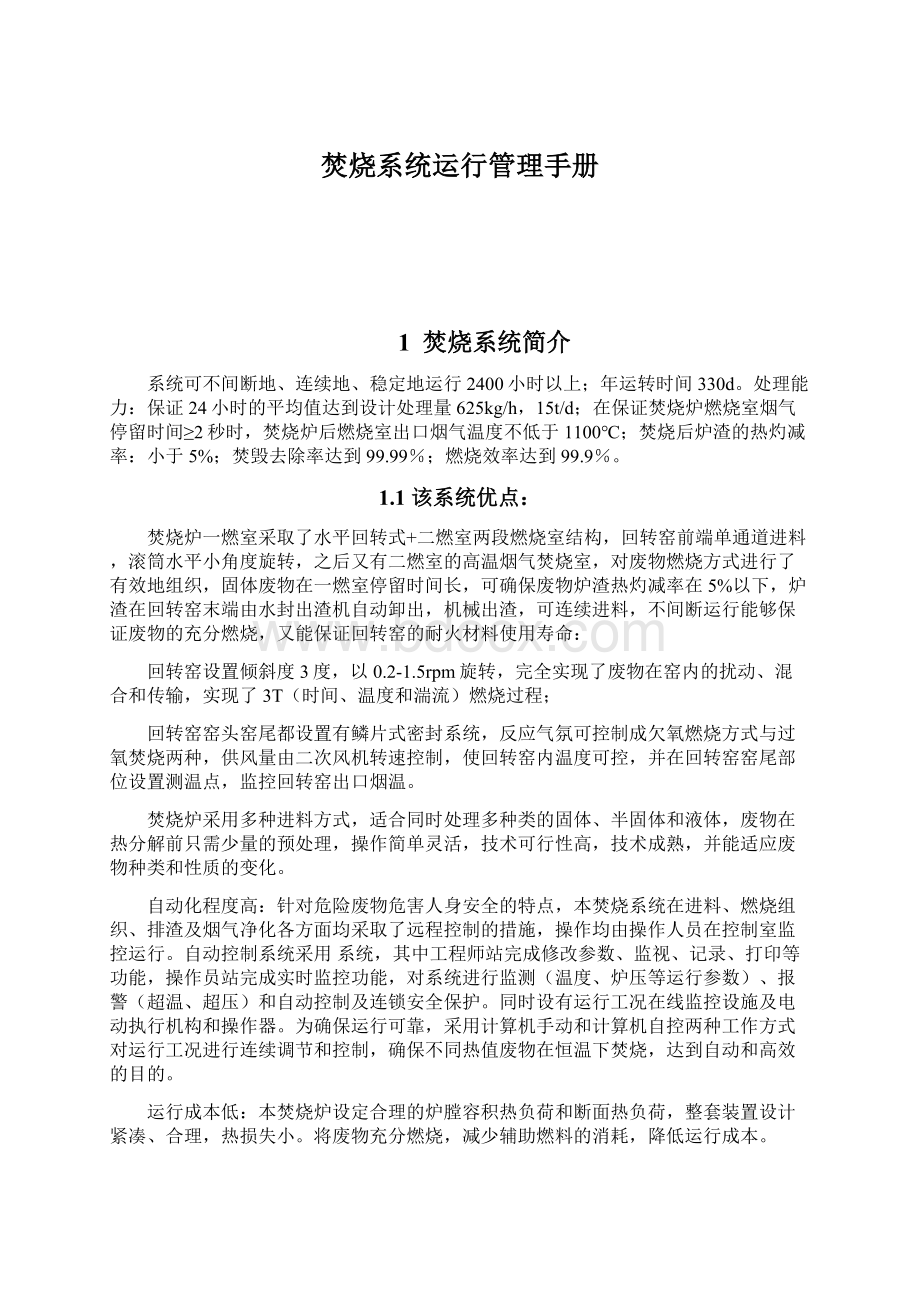
2.1.3液体废物进料
焚烧液体最好在焚烧固体工况稳定后进行,防止工况不稳造成系统负压等参数波动。
易燃液体废物从罐区储罐经过滤器由专用泵输送至废液间中间罐,在经过滤器由输送泵送至二燃室喷枪喷入燃烧室焚烧。
2.2焚烧系统
焚烧系统包括回转窑与二燃室,废物进入回转窑开始燃烧,回转窑通过旋转使物料不断往前翻滚,物料充分燃烧分解后落入出渣机,分解后产生的气体进入二燃室1100℃高温下充分燃烧。
要求进入二燃室的烟气停留时间应大于2秒,二燃室充分燃烧后空气中的氧量应控制在8-12%.
回转窑的燃烧配风调节\转速控制,采用PLC控制系统,通过变频器实现;
设负压控制燃烧装置,调节引风机转速;
二燃室出口设置紧急排放口,当尾气净化系统故障时,烟气有紧急排放口排出,便于事故处理和停炉,防止对焚烧系统及后续设备造成伤害。
2.3余热回收系统
主要是对烟气热量进行利用,使锅炉出口烟气温度减低至650℃左右,产生的蒸汽可用来发电、供暖等。
锅炉补水设备由空气冷却器,凝结水回收器,加药装置,软水器组成。
空气冷却器是将水蒸气通过轴流风机的强制通风,使自然环境中的空气自下往上流过空冷器中的翅片管,将蒸气热量带走变成凝结水,进入回收器。
它主要由多组翅片管和三个轴流风机组成。
凝结水回收器是将冷凝水进行储备,以便给锅炉进行补水,当凝结水量不足回收器液位降低后,及时补充软化水并通过温控调节阀补充蒸气提高温度。
给锅炉补水的水质达不到要求时,通过加药装置补充锅炉厂家指定的药剂。
2.4尾气净化系统
尾气净化系统主要包括了急冷塔,活性炭、消石灰喷射装置,布袋除尘器,湿式脱酸塔,通过这四部分对烟气的处理,使排放的尾气优于国家相关标准。
2.4.1急冷塔
烟气从急冷塔顶部进入,与顶部喷入的冷却水直接接触,烟气温度在1秒内从650℃降到200℃,避免二恶英生成。
冷却水的形式:
分散雾化(双流体喷嘴),根据急冷塔出口烟气温度的变化,自动跟踪、调节喷水量。
应不过喷,不欠喷。
2.4.2活性炭、消石灰喷射装置
在急冷塔出口喉口处通过喷入消石灰,可以初步对烟气进行干式脱酸,并干燥烟气中多余水分,喷入活性炭吸附二恶英及其他有害物质。
吸收剂:
消石灰粉、活性炭。
该粉自文丘里管喷入飞灰、新鲜吸收剂和循环灰的固体颗粒在流化悬浮状态下激烈碰撞、摩擦,并与降温水和烟气充分接触,与酸性气体发生化学反应(去除)。
会出现小、中、大等粒径,分别呈现“随气流流动”、“流体化”、”“掉落”三种现象;
小粒径吸收剂会被除尘器收集,并通过灰循环设备回到脱酸塔中重复使用;
中粒径吸收剂与其他的粒状物或吸收剂聚成大粒径颗粒后自然掉落;
大粒径颗粒则由下方的管道排除,通过脱酸系统的气流完成祛除酸气的目的。
2.4.3布袋除尘器
含尘烟气通过过滤材料,尘粒被过滤下来,过滤材料捕集粗粒粉尘主要靠惯性碰撞作用,捕集细粒粉尘主要靠扩散和筛分作用。
滤料的粉尘层也有一定的过滤作用。
布袋除尘器除尘效果的优劣与多种因素有关,但主要取决于滤料,本系统选用优质PTFE覆膜滤袋。
2.4.4湿式脱酸塔
在布袋除尘器的后部,吸收烟气中残留的20-50%酸性物质(HCL、SO2、HF),采用氢氧化钠做中和剂,碱液维持一定的PH值,利用循环泵进行循环喷淋。
根据碱液的PH值(自动检测)调节加药量,电导率仪监测盐浓度,控制外排的废液量;
2.5系统及设备参数
2.5.1上料装置:
数量:
1台,提升高度11000mm,
运行周期25次/小时,电机功率3KW
2.5.2液压站:
数量:
1套,
油箱容积350L/套,功率3KW/套,油压压力2-10Mpa
油缸数量3/套,
2.5.3废液喷射装置
处理量:
55kg/h
2.5.4回转窑
窑体内径:
2490mm(内衬300mm)
温度:
870℃-1000℃;
长度9.84m;
转速:
0.2-1.5rpm,炉体倾斜度3;
垃圾停留时间20-150min
日处理量:
≥15吨/天,
炉渣热灼减率≤5%
2.5.5二燃室:
烟气温度1100℃左右
烟气停留时间≥2秒
直径:
2.4m;
高度13m;
总烟气流量7568Nm³
/h,含氧量8%;
2.5.6点火及辅助燃烧技术参数
回转窑燃烧器型号:
数量;
1台正常消耗量为40m³
/h二燃室燃烧器型号:
数量2台,正常消耗量为50m³
/h
2.5.7余热锅炉:
蒸发量:
3t/h;
蒸汽压力:
1.0Mpa,蒸汽温度:
186℃,出口温度:
650℃;
锅筒保温层厚100-120mm,锅炉运行时,外表面温度≤50℃;
低温腐蚀:
当管壁温度低于140-150℃;
高温腐蚀:
温度在350--450℃;
软水器流量:
4m³
2.5.8急冷塔:
处理烟气量:
7568Nm3/h
进口烟温:
出口烟温:
200℃,烟气流速12m/s,停留时间0.5-0.8s;
耗水量:
1.45t/h
喷雾粒径≤50微米;
喷嘴形式:
双流体哈氏合金;
急冷水箱:
约25立方米,配:
液位变送器及液位开关(高、低液位)
2.5.9活性炭、消石灰喷射
消石灰喷射装置,数量:
1台;
消石灰耗量:
30kg/h;
粒度:
150-200目活性炭喷射;
活性炭喷射装置,数量:
活性炭使用量:
0.82kg/h;
粒度:
150-200目,对碘的吸收能力大于900mg/g
2.5.10布袋除尘器:
烟气从下部进入,自下向上流动,
数量:
1台
除尘效率:
99.9%
烟气量:
9535Nm3/h
入口烟气温度:
170--180℃,最高220℃。
清灰频次2-3min一次;
出口烟气排放浓度:
10Nm3/h
运行阻力:
≤1500pa仓室数:
3个
滤袋数量:
150条
滤袋材质:
PTFE(含覆膜)
滤袋规格:
ф160*6000毫米
过滤风速:
约7m/min
清灰方式:
在线脉冲式反吹
清灰压力:
≥3.5kg/cm2
滤袋正常工作温度:
120-180℃
灰斗室:
3个(壁温110℃)
采用差压与定时清灰方式。
(PLC控制)
2.5.11湿式脱酸系统
设备数量:
1台
塔型:
逆流式喷淋塔;
材质316l
9705Nm3/h;
出口烟气温度:
74℃
70-75℃
烟气滞留时间:
7.18秒
脱酸率:
≥99%
100%氢氧化钠,使用量10kg/h,用水量760kg/h,废水:
102kg/h。
2.5.12引风机(使系统获得负压)
技术参数
1套
全压:
P=7000Pa;
风量:
443Nm³
/min;
功率:
110kw
调节方式:
变频
2.5.13供电
由树屏变电站引来一路10kv线路,断开电流20KA,安装两台630KVA干式变压器,同时一台350kw柴油发电机组做为焚烧系统的备用电源;
3系统操作
3.1焚烧系统
3.1.1操作程序
3.1.1.1系统开车前的准备与检查
通知各岗位按要求做好开车前的准备与检查工作。
本岗位做如下检查工作:
1)请电工检查电气设备是否完好,应具备开车条件。
2)请仪表工检查各检测仪表状态,校正零点。
3)检查耐火砖、下料口,是否完好。
4)检查各转动设备的润滑情况,对各转动设备进行盘车、点动并试空车。
设备各联接部位、各紧固件(包括联接管道)应联接牢固,防护罩等安全设施应齐全。
5)检查进料密封门是否严密,并了解各密封门是否处于正常状态。
6)检查出渣机水封液位是否正常,出渣机内应无异物。
7)检查供油系统油箱,油位是否在正常液位范围内。
8)液压系统检查:
油箱油位符合要求,各行程挡块在合适的位置,防护装置完好。
9)液压站冷却循环水必须畅通。
10)检查废液喷枪雾化情况。
11)准备好原始记录和安全防护用品。
3.1.1.2开车
本岗位完成检查准备工作,一切正常,联系其他岗位准备工作是否完成,如完成按以下程序进行系统开车。
1)通知空压机系统开车。
2)通知天然气送气
3.1.1.3点火
1)当回转窑炉膛温度达到650~750℃、二燃室达到800~1000℃时,即可进料燃烧,并空载启动二次风机,根据烟气检测氧含量情况,可逐渐加大二次风阀门,调节二次风量,进而逐渐加大负荷,控制氧含量在指标范围内,并及时检查尾气情况。
2)待物料燃烧火焰完整形成,回转窑温度约850℃时,停窑头燃烧器,二燃室温度1000℃以上并持续工作,停二燃室燃烧器。
3)投料后启动出渣机,通知锅炉岗位、尾气处理岗位启动卸灰系统。
4)投料后通知尾气处理岗位启动消石灰活性炭头家装置,启动脱酸系统,同时开始投加活性炭,启动循环泵和浓碱液投加控制系统。
5)当系统投料运行且回转窑燃烧工况稳定后,通知尾气处理岗位切断布袋除尘器旁路。
布袋除尘器投入正常运行操作。
3.1.1.4停车
(1)短期停车
短期停车:
停止固体废物进料,停止废液泵、开启旁路阀,关闭布袋除进出口阀门,关二次风阀门。
将所有喷枪拨出炉体,并用硅酸铝纤维封住接口。
根据温度情况通知尾气处理岗位停急冷水泵、碱液泵、循环泵,停空压机。
①在停炉后第一个小时内,每5~10分钟转窑1/4圈;
②在停炉后第二个小时内,每15~20分钟转窑1/4圈;
③在停炉后第三个小时内,每30分钟转窑1/4圈;
④其后每小时转炉一次,每次转1/4圈。
在回转窑停止进料1小时后,通知尾气处理岗位停止供石灰粉,停止投加活性炭。
(2)紧急停车
在突然停电备用发电机又不能立即启动或系统工艺、设备、电气、仪表等出现重大故障系统无法维持正常运行、尾气无法正常处理必须立即停车时,进行紧急停车。
1 首先将二燃室紧急排放烟囱打开,(炉门处应关闭,若未关闭,应采取方式封闭炉门,防止烟气量过大),使前段高温烟气直接从二燃室顶部排出,防止高温烟气进入尾气处理系统,同时保护余热锅炉及其后续设备。
2 手动开启布袋除尘器旁路阀,关闭布袋除尘器进出口阀门防止高温烟气损坏布袋。
3 然后让系统降温,降温的过程中必须定期人工转动窑体。
4 所有换热设备,如锅炉等禁止在高温条件下排出循环冷却水或排污操作。
5 再次启炉时要按开车程序重新检查各设备情况,如:
该进行清灰的要进行清灰,需要补充水的要补充水,需要调整的阀门要重新调整。
(3)长期停车
①系统停机时,设备的停止顺序与启动顺序正好相反,首先停止固体废物进料(停止行车、停止斗式上料)、停止废液泵、停止投入石灰粉、停止投入活性炭粉、停止碱液泵。
然后将废液喷枪从炉体移出(防止高温损坏设备),当炉膛内物料完全燃尽并排出后,关闭燃烧器,开启布袋旁路阀,关闭布袋烟气进出口阀门,停止布袋除尘器。
在保证一级密封门关闭、二级密封门开启、推料机构退回的情况下关闭液压站。
关窑体供风阀门,其它设备及阀门维持运行状态使炉体和后续系统降温。
系统的降温速度在高温段(400℃以上)不得大于40℃/h,在低温段(400℃以下)不大于60℃/h;
注意:
物料燃尽后需继续转动窑体,将窑内灰渣排净。
②停炉过程中需定期转动窑体,在高温下如不经常转动,窑体将发生弯曲。
因此防止炉体弯曲是十分重要而又十分细致的工作,切不可疏忽,必须执行下列规定:
a.在停炉后第一个小时内,每5~10分钟转窑1/4圈;
b.在停炉后第二个小时内,每15~20分钟转窑1/4圈;
c.在停炉后第三个小时内,每30分钟转窑1/4圈;
d.其后每小时转炉一次,每次转1/4圈,直至炉膛温度降低到50℃以下;
e.如果长时间停炉,须平均每周转动一次,每次转1/4圈。
③当回转窑出口温度、二燃室出口温度全部低于200℃时停止蒸汽冷凝循环冷却装置、锅炉给水泵、急冷雾化泵、空气压缩机、循环泵、引风机等,并继续观察回转窑和二燃室的温度。
设备停止间隔为10秒。
④系统设备在降温过程中应根据正常操作温度指标调整其喷水量、给水量、压缩空气量等。
必须避免温度降低后喷水量不变造成下部流水。
⑤锅炉的停炉:
随着锅炉负荷逐渐降低,相应地减少锅炉给水,维持锅筒内正常水位,待冷却后再关闭给水阀;
在锅炉停止供汽后,应关闭锅炉主汽阀,在汽压继续下降后,锅炉副汽阀也应关闭;
如此时锅筒汽压仍继续上升,则可向锅内进水,并进行少量排污,或加强疏水阀的排汽,但不应使锅炉有显著的冷却;
在正常停炉4~6小时内上水,排污一次。
⑥在回转窑停止进料一小时后通知尾气处理岗停止供石灰料,停止投加活性炭。
⑦在系统冷却到常温后,检查所有设备,若停炉时间较长,须打开所有阀门将窑头水套、所有水泵和水箱、罐、水池等排空。
锅炉设备要按照要求进入保养阶段。
工艺管线上的阀门不得完全开关到头,并可放到下次启炉时需要的位置。
3.1.1.5停车后的重新启动
2停车后因窑内温度低,可能出现放炮现象,在班人员应远离回转窑。
⑵短期停车后的开车,窑内温度略低于正常温度。
先主引风机,风机转速15~20Hz,启动一次风机,点燃燃烧器,若温度高于400℃,则启动回转窑电机,温度至500℃时开始投料,随着系统温度逐渐升高,引风量、投料量、窑速逐渐增加,二次风量根据燃烧、温度情况酌情加减。
⑶若停车时间较长,窑内温度较低,翻窑后窑内仍发暗,二燃室温度也很低,启动回转窑燃烧器,二燃室燃烧器根据情况启动。
⑷通知各岗位密切注意本岗位操作参数的变化,按操作规程进行正常操作。
3.1.1.6正常操作要点
(1)一、二次风即一、二次助燃空气。
二次风量的调整应根据窑尾烟气和尾气含氧量进行调整。
(2)回转窑、二燃室温度升高太快,应减少投料量。
当出现温度在短时间内急剧上升的异常情况,可立即加大引风量和一二次风量,温度回到正常范围时恢复正常操作。
(3)窑速的快慢应根据物料燃烧的难易程度(亦即燃烧速度)来调整。
(4)物料的焚烧量根据物料的特性和系统的运行状况来调整。
通常情况下焚烧热值较高的废物产生的烟气量较大,反之则少。
由于系统设计时所处理的烟气量相对一定,所以当焚烧热值较高的废物时,需适当减少系统的焚烧量。
但当焚烧热值太小的废物时必须减少焚烧量,并增加耗气量才能保证焚烧效果。
当焚烧的废物较难燃尽时,需适当减少系统的焚烧量。
当废物产生的有害气体较多时,需适当减少系统的焚烧量,以保证废物的燃尽程度和尾气处理效果。
(5)严格控制焚烧系统各工艺指标在要求范围内,即稳定回转窑和二燃室的温度。
(6)一、二次风、引风、窑速、下料量的调整要勤调、小范围调,尽量避免大的波动。
稳定是长期安全运转的前提。
(7)提高操作的预见性,任何事故的发生均有前兆。
要根据工艺参数的变化趋势,提高预见性,及时采取措施,防止事故发生。
(8)及时了解掌握物料变化情况,适时调整操作。
(9)三班统一,步调一致。
3.1.2注意问题
(1)整个点火到正常过程,引风机负荷根据窑内情况逐渐加大,保持窑尾负压在-50Pa左右,保持火焰稳定、顺畅。
(2)从点火到投料过程最短不少于3小时,防止因升温过快破坏回转窑和二燃室耐火材料。
(3)启动一、二次风机时,风机必须在轻载或无载荷情况下启动。
(4)为保证焚烧工况稳定,应保证上料的连续性和均匀性。
(5)废液喷枪启动后必须检查和调整废液喷枪的压力维持在0.4~0.6Mpa之间,保证废液压力比压缩空气压力高0.02~0.05Mpa。
处理液体废物前与处理结束后,用压缩空气对废液管路进行吹扫。
(6)启动出渣机后,随时检查出渣机水封,注意炉体负压是否突然偏离设定值,随时注意是否有大块物料或未完全燃烧的物料落入出渣机,导致出渣机卡死。
(7)转窑变频起动时最低不小于10Hz。
(8)焚烧固体量与窑速成一定比例。
根据废物热值高低和炉膛温度决定投料量。
回转窑温度连续10分钟超过950℃、二燃室连续10分钟超过1200℃,停止进料,此时应加大引风机频率,使高温区快速后移。
(9)焚烧毒性相对较大的废物时,必须相应地增大系统负压。
(10)窑头出灰。
定期打开窑头下部的清扫门,清除密封处的物料。
(11)尾气一氧化碳含量过高时,应快速加大二次风,根据系统负压调整引风量。
3.2上料系统
3.2.1操作说明
焚烧系统的废物进料方式采用分系统进料。
3.2.1.1箱装废物上料系统上料
3.2.1.2行车上料系统
3.2.1.3液体废物进料
3.2.2开、停车操作程序
3.2.2.1箱装物料与行车上料系统开机前的准备:
1 检查电源为3相5线制,380V、50HZ,无缺相;
2 确认提升机的进口处及提升机上端倒料处无不安全情况(对设备和人体)存在;
3 确认控制柜上及现场按钮盒上的紧急停止开关操作头均处于拔出位置;
4 检查确认后,方能进行下述操作。
3.2.2.2电源操作:
1 旋转打开控制柜右侧的隔离开关,该系统总电源接通;
2 合上控制柜内各断路器,检查变频器参数,断路器过载保护电流,热保护电流为电机额定电流的约1.2倍,检查散热风扇是否起动,PLC上RUN灯是否亮起;
3 注:
首次使用时,需进行上述操作;
以后开机时,只需旋转控制柜上隔离开关旋钮为ON位置,关机时,旋转控制柜上隔离开关旋钮为OFF位置即可。
3.2.2.3开机:
(1)选择运行方式:
将现场电控柜上的手动/自动选择开关置手动位置,为手动方式;
置自动位置,为自动方式。
(注:
在系统运行过程中切换手动/自动运行方式时,系统会自动停机,再次启动系统需重新开机。
(2)选择进料方式(将焚烧物送入焚烧炉的方式):
将控制柜上的三位选择开关医废/危废置医废位置,为单独皮带加提升机进料模式,置危废位置,为单独漏斗进料模式,注:
(在系统运行过程中切换医废/危废运行方式时,系统会自动停机,再次启动系统需重新开机,所以请在开机前请准备好要选择的方式。
3.2.2.4运行操作
◆手动运行操作:
当运行方式选择为手动运行模式时,按压控制柜上的启动按钮,系统有5秒钟的启动提示报警,控制柜上绿色塔灯由1秒闪烁变为4秒闪烁,系统手动启动完成,即可进行以下的手动操作。
◆手动开进料门操作:
推杆进料系统的动作顺序为:
进料门开启—进料门关闭—炉门开启—推杆推进—推杆退回—炉门关闭(手动操作时炉门开启推杆才会推进)炉门、进料门、推杆在动作时指示灯会闪烁,到位时指示灯均由闪烁变为常亮。
◆自动运行操作:
当运行方式选择为自动运行模式且满足自动运行条件--提升机轿厢位于下降到位位置(注当选择是医废方式时提升机要位于下降位置)、推杆进料器处于回退到位位置、进料门处于关闭到位位置、炉口滑动门处于关闭到位位置,按压控制柜上的启动按钮,5秒后,塔灯蜂鸣器停止鸣响,绿色塔灯由闪烁变为常亮,系统自动启动完成,即可进行以下的自动运行操作。
若不满足自动启动条件启动自动运行时,系统不会自动启动,同时塔灯声讯报警器和绿指示灯以2S周期闪烁和蜂鸣,提示未满足自动启动条件,此时需按推杆手动回退系统自动初始化,初始化完成后系统自动进入自动运行模式,绿色塔灯变为常亮。
)
1 医废自动运行控制:
当选择为自动模数启动系统后,现场操作人员把待焚烧处理的两桶桶装输送物固定在升降机轿厢里,固定好左边的桶装输送物后,按压左右两边的提升开始按钮,当提升机倒料漏斗下的输送皮带机累计运行时间到达10秒钟(该时间由控制程序确定)后,提升机上升(上升过程中在机械机构的作用下自动关闭安全门)上升到顶部后在机械机构的作用下自动倒料上升倒料到位后停止5秒,提升机轿