集成电路工艺复习Word文件下载.docx
《集成电路工艺复习Word文件下载.docx》由会员分享,可在线阅读,更多相关《集成电路工艺复习Word文件下载.docx(32页珍藏版)》请在冰豆网上搜索。
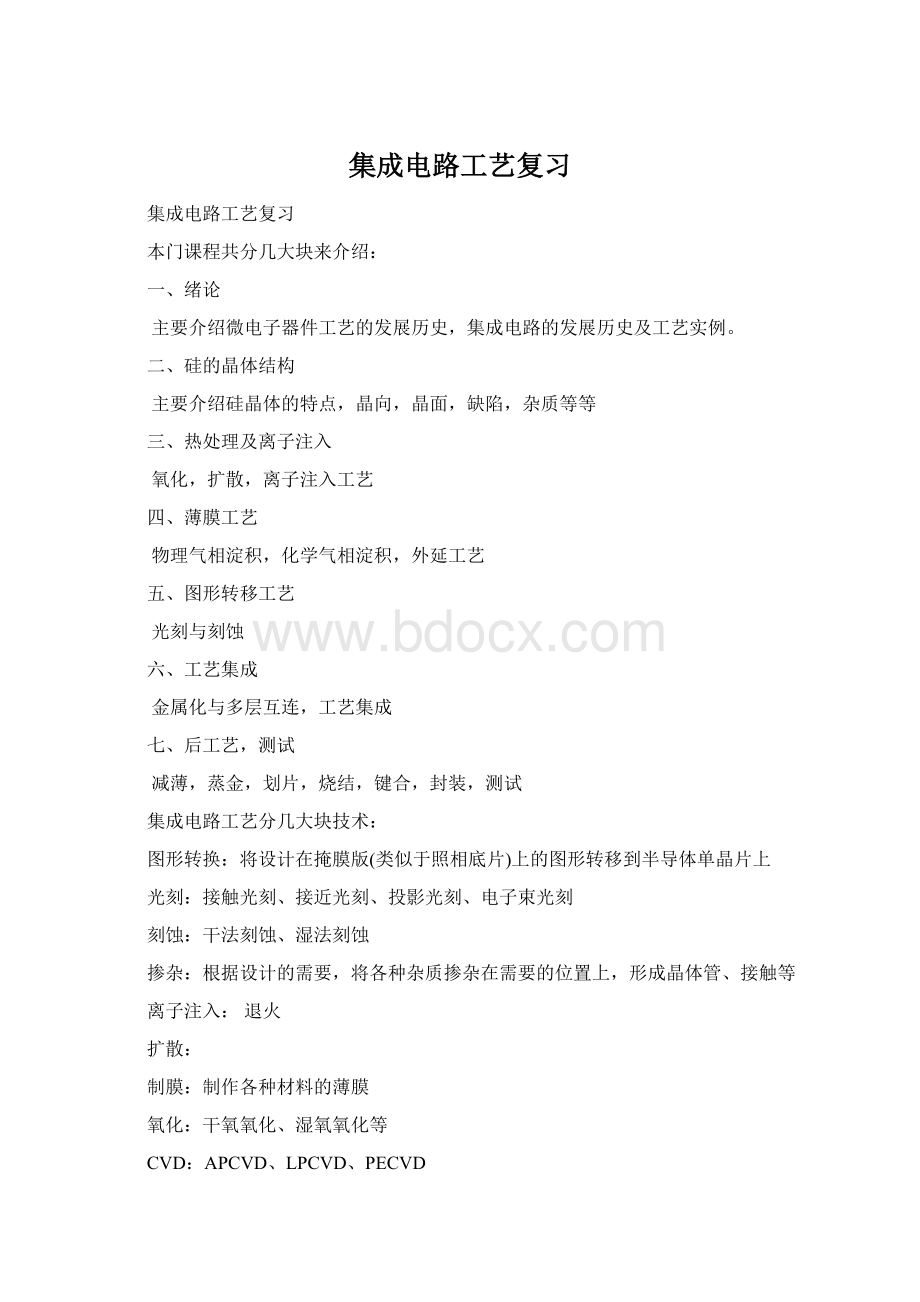
倒角机
1.4抛光:
利用抛光剂对研磨后的晶片进行物理、化学的表面加工,以获取无晶格损伤的高洁净度、高平整度的镜面晶片。
单/双面抛光机、单/多头抛光机
1.5清洗:
合理的清洗是保证硅片表面质量的重要条件。
在晶片制备过程中需要多次清洗,以去除残留在晶片表面或边缘的废屑等。
清洗机、冲洗甩干机
2.前道工艺
2.1外延:
在单晶衬底晶片上生长一层具有与基片不同电子特性的薄硅层。
外延炉
2.2氧化:
在高温下,氧和水蒸气跟硅表面起化学作用,形成薄厚均匀的硅氧化层。
氧化炉
2.3化学汽相淀积(CVD):
使一种或数种物质的气体以某种方式激活后,在衬底表面发生化学反应,并淀积所需固体薄膜。
CVD设备
2.4溅射:
正离子受强电场加速,形成高能量的离子流轰击靶材,当离子的动能超过靶原子的结合能时,靶表面的原子就脱离表面,溅射到对面的阳极上,淀积成薄膜。
溅射台
2.5光刻:
将掩模图形转印到涂有光刻胶的衬底晶片上。
对准和曝光是光刻工艺中最关键的工序
接触/接近式曝光机分步投影曝光机
2.6刻蚀:
活性气体可使曝光区,在晶片表面建立几何图形。
刻蚀机
2.7离子注入:
先使待掺杂的原子电离,再加速到一定能量使之“注入”到晶体中,经过退火使杂质激活,达到掺杂目的。
离子注入机
3.后道工艺
3.1探针测试:
对晶圆上的每个电路进行电性能测试及特性测试。
探针测试台
3.2划片:
将具有集成电路管芯的圆片用金刚砂刃具、激光束等方法分割成单独的管芯以便封装。
砂轮划片机
3.3粘片:
把集成电路芯片用银浆、银玻璃、低温焊料或共晶焊料装配到塑料封装的引线框架或陶瓷封装外壳底座上。
粘片机
3.4引线键合:
用金引线把集成电路管芯上的压焊点与外壳或引线框架上的外引线内引出端通过键合连接起来。
引线键合机
3.5封装:
密封组件用作机械和外界保护。
为保证封装质量,管壳必须具有良好的气密性、足够的机械强度、良好的电气性能和热性能。
塑封压机切筋打弯机打标机
3.6终测:
又叫成品测试,目的是确保IC能满足最低电气规范化要求,并按不同要求分类,统计出分类结果和不同参数分布,供质量和生产部门参考。
数字集成电路测试系统
3.7编带:
将IC成品经自动识别检测,热封覆盖膜并编入凹壳载带。
编带机
Chap0绪论
0.1微电子器件工艺的发展历史
大致分为三个阶段:
1.生长法:
在20世纪30、40年代,经过对半导体材料的性质及特点的深入研究和长时间的实践和探索,开始利用锗、硅晶体制造P-N结。
刚开始方法较为原始,它是在拉制锗、硅单晶体的过程中实现的。
以锗单晶为例,由于熔化的晶体的导电类型为N型(或P型),在拉制过程中,某一时刻突然改变掺杂浓度,如放入某种受主杂质(或施主杂质),这样已拉制好的单晶,先头部分为N型(或P型),而后一部分就成为P型(或N型),然后将锗单晶切成小片,在P型和N型交界面处就形成了一个P-N结,这就是晶体二极管。
2.合金法:
到了20世纪50年代,采用合金法制造PN结。
它是将一个受主杂质(施主杂质)的小球,放在一块N型(P型)锗晶片上,然后,将它们一起放在高温下加热,使小球熔化,以合金方式浸入到锗晶体中,当晶片完全冷却后,小球上制成了合金二极管或合金三极管。
3.扩散法:
上述两种制备PN结的方法,虽然工艺十分简单,但是基区很难制的很薄,直接影响了晶体管的特性。
因此,经过探索研究,找到了一种更好的方法,这就是扩散法。
用这种方法可以把基区制得十分薄,而且电阻率可以不均匀,这样晶体管的电学特性就大大提高了。
扩散法是在硅平面工艺基础上发展起来的。
Chap2氧化
本章重点:
1、用途
2、氧化方法
3、质量监测
SiO2层的特点:
能紧紧地依附在硅衬底表面,具有良好的化学稳定性和电绝缘性。
对某些杂质能起到掩蔽作用。
极易溶解于氢氟酸中,而在其它酸中稳定。
2.1SiO2的结构和性质
SiO2的用途
1.扩散时的掩蔽层,离子注入的(有时与光刻胶、Si3N4层一起使用)阻挡层
二氧化硅对杂质扩散起到掩蔽作用,利用这个性质结合光刻工艺,就可以进行选择性扩散。
这种掩蔽作用是有条件的。
随着温度升高扩散时间延长,杂质也有可能会扩散穿透二氧化硅膜层,使掩蔽作用失效。
因此二氧化硅膜起掩蔽作用有两个条件:
(1)厚度足够;
(2)所选杂质在二氧化硅中的扩散系数要比在硅中的扩散系数小得多。
2.器件和电路的保护或钝化膜
在硅片表面生长一层二氧化硅膜,可以保护硅表面和P-N结的边缘不受外界影响,提高器件的稳定性和可靠性。
同时,在制造工艺流程中,防止表面或P-N结受到机械损伤和杂质玷污,起到了保护作用。
另外,有了这一层二氧化硅膜,就可以将硅片表面和P-N结与外界气氛隔开。
降低了外界气氛对硅的影响,起到钝化作用。
但是,钝化的前提是膜层的质量要好,如果二氧化硅膜中含有大量纳离子或针孔,非但不能起到钝化作用,反而会造成器件不稳定。
3.某些器件的重要组成部分
(1)MOS管的绝缘栅材料。
在MOS晶体管中,常以二氧化硅膜作为栅极,这是因为二氧化硅层的电阻率高,介电强度大,几乎不存在漏电流。
但作为绝缘栅要求极高,因为Si-SiO2界面十分敏感(指电学性能),SiO2层质量不好,这样的绝缘栅极就不是良好的半导体器件。
(2)电容器的介质材料。
集成电路中的电容器是以SiO2作介质的,因为SiO2的介电常数为3-4,击穿耐压较高,电容温度系数下,这些性能决定了它是一种优质的电容器介质材料。
另外,生长二氧化硅方法很简单,在集成电路中的电容器都以二氧化硅来代替。
4.集成电路中的隔离介质
集成电路中的隔离有P-N隔离和介质隔离两种,而介质隔离中的介质就是二氧化硅。
因为SiO2介质隔离的漏电流很小,岛与岛之间的隔离电压较大,寄生电容较小。
因此,用二氧化硅作介质隔离的集成电路的开关速度较好。
5.用于电极引线和硅器件之间的绝缘介质
在集成电路制备中,电极引线和器件之间,往往有一种绝缘材料,工艺上大多采用二氧化硅作为这一层绝缘材料,使得器件之间,电极引线之间绝缘。
2.2SiO2的掩蔽作用
一、杂质在二氧化硅中的存在形式
1.本征二氧化硅
2.非本征二氧化硅
3.按杂质在网络中所处位置可分为两类:
网络形成者和网络改变者。
(1)网络形成者:
可以替代网络中硅原子的杂质。
其离子半径与Si相近。
(2)网络改变者:
存在于二氧化硅网络间隙中的杂质。
一般是以离子形式存在于网络中,其离子半径大,替代硅的可能性很小。
2.3硅的热氧化生长动力学
一、硅的热氧化
1.SiO2的制备方法很多,有热分解淀积法、溅射法、真空蒸发法、阳极氧化法、化学气相淀积法、等离子氧化法和热氧化法等等。
2.热氧化是应用最为广泛的。
这是因为它具有工艺简单、操作方便、氧化膜质量最佳、膜的稳定性和可靠性好等特点。
3.硅的热氧化是指硅与氧或水汽等氧化剂,在高温下经化学反应生成SiO2的过程。
二、SiO2的制备方法
1.三种氧化
速度均匀重复性结构掩蔽性水温
干氧:
慢好致密好
湿氧:
快较好中基本满足95℃
水汽:
最快差疏松较差102℃
实际采用:
干氧--湿氧--干氧
进行干氧和湿氧氧化的氧化炉示意图
2.水汽氯化氢氧化
(1)作用:
减少钠离子的玷污,抑制氧化垛层错,提高少子寿命,也就是提高器件的电性能和可靠性。
在生产中广泛应用。
SiO2-Si界面未饱和键和氯离子结合,减少其被杂质原子的价键所占据造成的玷污。
在半导体材料中,经常存在一些重金属杂质,如铜、金等,另外,在氧化过程中,也很容易引入这些杂质。
它们在半导体中形成复合中心,使少子寿命变短,如果面外有氯离子存在,它能与这些金属杂质发生作用,生成易挥发的氯化物,而被排除,从而减少了复合中心。
3.其他常用氧化
(1).氢氧合成氧化:
氢氧合成水----汽化===>
水汽氧化,比湿氧优,均匀/重复性好。
(2).低温氧化:
缺陷少,(1000℃以下)但钝化效果差---加1100℃N2退火。
(3).高压氧化:
指高压水汽氧化,高密度、高折射率低腐蚀速率,杂质分凝效应小。
2.9二氧化硅膜质量控制
一、二氧化硅膜的质量要求
二氧化硅膜的质量,直接关系到半导体器件及集成电路的性能。
因此,对二氧化硅膜的质量要求是很严格的。
从宏观上看,要求表面无斑点、裂纹、白雾及发花现象以及没有针孔等缺陷存在。
其膜质量要符合要求而且均匀,结构致密,对一些缺陷,尤其是可动钠离子要求含量越低越好。
2、二氧化硅质量检验
1.厚度测量:
测量SiO2膜厚度的方法很多,如果精度要求不高,可以用比色法、腐蚀法等。
如果有一定精度要求可以用双光干涉法、电解电容法。
如果精度要求高,还可以用椭圆偏振光法。
1)比色法(薄层用):
硅片表面生成的SiO2膜是无色透明的,有白光照射时,SiO2膜表面与Si-SiO2界面的反射光相干涉生成干涉色,氧化膜的厚度不同,干涉色也不同。
因此利用干涉色可直接估计氧化膜的厚度。
2)干涉法(a)劈尖干涉:
n2-二氧化硅的折射率,N-干涉条纹数
(b)双光干涉
3)椭圆偏振光法:
以光的波动性为理论基础。
P波(振动方向在入射面内),S波(振动方向垂直于入射面)。
4)高频C-V测试:
利用金属-氧化物-半导体(MOS)结构,测量电容-电压关系曲线。
2、二氧化硅膜缺陷检验:
二氧化硅膜的缺陷有宏观缺陷和微观缺陷两种。
所谓宏观缺陷是指用肉眼就可以直接观察到的缺陷。
所谓微观缺陷是指必须借助于测试仪器方能观察到的缺陷。
1)宏观缺陷:
又称表面缺陷。
它是指:
氧化层厚度不均匀、表面有斑点、氧化层上有针孔等等。
(a)氧化层厚度不均匀;
(b)氧化斑点;
(c)氧化层针孔
2)微观缺陷:
指的是钠离子玷污和热氧化层层错。
Chap3扩散工艺
3.1杂质扩散机构
1、间隙式扩散
1、间隙式杂质:
存在于晶格间隙的杂质。
主要那些半径较小、并且不容易和硅原子键合的原子,它们在晶体中的扩散运动主要是以间隙方式进行的。
如下图所示。
图中黑点代表间隙杂质,圆圈代表晶格位置上的硅原子。
2、间隙式扩散:
间隙式杂质从一个间隙位置到另一个间隙位置上的运动。
3、间隙杂质要从一个间隙位置运动到相邻的间隙位置上,必须要越过一个势垒,势垒高度Wi一般为0.6~1.2ev。
4、间隙杂质只能依靠热涨落才能获得大于Wi的能量,越过势垒跳到近邻的间隙位置上。
5、跳跃率:
Pi=v0e-wi/kT。
温度升高时Pi指数地增加。
6、Na、K、Fe、Cu、Au等元素
7、扩散系数要比替位式扩散大6~7个数量级
二、替位式扩散
1、替位杂质:
占据晶格位置的外来原子。
2、替位式扩散:
替位杂质从一个晶格位置到另一个晶格位置上。
只有当替位杂质的近邻晶格上出现空位,替位杂质才能比较容易地运动到近邻空位上。
运动如下图所示。
3、替位杂质运动比间隙杂质更困难,首先要在近邻出现空位,同时还要依靠热涨落获得大于势垒高度Ws的能量才能实现替位运动。
4、跳跃率Pv=v0e-(Ws+Wv)/kT。
Wv表示形成一个空位所需能量。
3.3扩散杂质的分布
1.恒定表面源扩散:
扩散过程中,硅片表面杂质浓度始终不变这种类型的扩散称为恒定表面源扩散。
其扩散后杂质浓度分布为余误差函数分布。
特点:
(1)杂质分布形式:
在表面浓度一定的情况下,扩散时间越长,杂质扩散的就越深,扩到硅内的杂质数量也就越多。
(2)结深
(3)杂质浓度梯度:
在CS和CB一定的情况下P-N结越深,在结处的杂质浓度梯度就越小
2.有限表面源扩散:
扩散散前在硅片表面先淀积一层杂质,在整个过程中,这层杂质作为扩散源,不再有新源补充,杂质总量不再变化。
这种类型的扩散称为有限表面源扩散。
其扩散后杂质浓度分布为高。
当温度相同时,,扩散时间越长,杂质扩散的就越深,表面浓度就越低。
当扩散时间相同时,扩散温度越高,杂质扩散的就越深,表面浓度下降的就越多。
(2)结深:
在杂质分布形式相同的情况下,CB越大,结深就越深。
随扩散深度的增加而减小。
预淀积(或预扩散):
温度低、时间短
主淀积(或推进):
温度高、时间长
预淀积(或预扩散)现已普遍被离子注入代替
3.4影响杂质分布的其他因素(实际杂质分布(偏离理论值))
一、二维扩散
一般横向扩散(0.75~0.85)*Xj(Xj纵向结深)
3.5扩散工艺
Chap4离子注入工艺
一.离子注入工艺设备结构
4.1核碰撞和电子碰撞
LSS理论:
注入离子在靶内的能量损失分为两个彼此独立的过程
(1)核碰撞,
(2)电子碰撞,总能量损失为它们的和。
(一)、核阻止本领
能量为E的一个注入离子,在单位密度靶内运动单位长度时,损失给靶原子核的能量。
(2)电子阻止本领
同注入离子的速度成正比,即和注入离子能量的平方根成正比。
(3)射程的概念
4.2注入离子的分布
(3)沟道注入
1、入射离子的阻挡作用与晶体取向有关;
2、可能沿某些方向由原子列包围成直通道--沟道,离子进入沟道时,沿沟道前进阻力小,射程要大得多。
3、沟道效应的存在,将使得对注入离子在深度上难以控制,尤其对大规模集成电路制造更带来麻烦。
如MOS器件的结深通常只有0.4um左右,有了这种沟道效应万一注入距离超过了预期的深度,就使元器件失效。
因此,在离子注入时,要考虑到这种沟道效应,也就是说要抑止这种现象的产生。
4、目前常用的解决方法有三种。
(1)是将硅片相对注入的离子运动方向倾斜一个角度,7度左右最佳;
(2)是对硅片表面铺上一层非结晶系的材料,使入射的注入离子在进入硅片衬底之前,在非结晶层里与无固定排列方式的非结晶系原子产生碰撞而散射,这样可以减弱沟道效应;
(3)是对硅片表面先进行一次离子注入,使结晶层破坏成为非结晶层,然后进入离子注入。
这三种方法都是利用增加注入离子与其他原子碰撞来降低沟道效应。
工业上常用前两种方法。
4.4热退火
退火:
将注入离子的硅片在一定温度和真空或氮、氩等高纯气体的保护下,经过适当时间的热处理,部分或全部消除硅片中的损伤,少数载流子的寿命及迁移率也会不同程度的得到恢复,
电激活杂质:
使不在晶格位置上的离子运动到晶格位置,以便具有电活性,产生自由载流子,起到杂质的作用。
分为普通热退火、硼的退火特性、磷的退火特性、扩散效应、快速退火(包括脉冲激光法、扫描电子束、连续波激光、非相干宽带频光源(如卤光灯、电弧灯、石墨加热器、红外设备等))
4.5离子注入优缺点
一.离子注入的优缺点
优点:
1)可在较低的温度下,将各种杂质掺入到不同的半导体中;
2)能精确控制掺入基片内杂质的浓度分布和注入深度;
3)可以实现大面积均匀掺杂,而且重复性好;
4)掺入杂质纯度高;
5)获得主浓度扩散层不受故浓度限制。
6)由于注入粒子的直射性,杂质的横向扩散小;
7)可以置备理想的杂质分布;
8)可以通过半导体表面上一定厚度的四SiO2膜进行注入而实行掺杂;
9)工艺条件容易控制。
缺点:
1)高能离子注入改变晶格结构;
2)设备贵。
Chap5物理气相沉积
5.1真空蒸发法制备薄膜的基本原理
一、真空蒸发设备
三大部分
(1)真空系统:
为蒸发过程提供真空环境
(2)蒸发系统:
放置蒸发源,以及加热和测温装置。
(3)基板及加热:
放置衬底,对衬底加热装置及测量装置。
真空蒸发法过程:
(1)加热蒸发过程。
(2)气化原子或分子在蒸发源与基片之间的输运过程。
(3)被蒸发的原子或分子在衬底表面的淀积过程。
二、汽化热和蒸汽压
三、真空度与分子平均自由程
四、多组成薄膜的蒸发方法
单源蒸发法:
单源,合金溶液
多源同时蒸发法:
多坩埚,同时蒸发
多源顺序蒸发法:
多坩埚,按顺序蒸发
5.2蒸发源5.3气体辉光放电
5.4溅射
溅射是利用等离子体中的离子,对被溅射物体电极进行轰击,使气相等离子体内具有被溅射镀物的粒子,使其淀积到硅片表面并形成薄膜的一种PVD方法,因此将高纯粒子从某种物质的表面撞击出原子的物理过程叫溅射。
溅射是目前大规模集成电路制造中应用得最广泛的一种镀膜方法,它可以用来淀积不同的金属,包括铝、铝合金、钛、钨钛合金。
溅射具有以下优点:
1)可在一个面积很大的靶子上进行,这样解决了大尺寸硅片淀积铝膜厚度均匀性的问题
2)在选定的工作条件下,膜厚容易控制,只要调节时间就可得到所需厚度
3)溅射淀积薄膜的合金,成分要比蒸发容易控制
4)改变加在硅片上的偏压和温度,可以控制薄膜的许多重要性能,如台阶覆盖和晶粒结构等。
5)在溅射之前进行预溅射,做一番清洁处理,这样可以获得质量更好的薄膜。
一、溅射特性
1.溅射阈值:
10~30ev取决于靶材料
2.溅射率:
被溅射出来的原子数与入射离子数之比,其大小于入射离子的能量、种类、靶材料的种类等有关。
3.溅射原子的能量和速度
二、溅射方法
1.直流溅射:
溅射率低,靶材料有较好导电性时可以很方便的溅射淀积各类金属薄膜。
2.射频溅射:
导电性很差的非金属材料的溅射。
3.磁控溅射:
店家速率较高,工作气体压力较低,薄膜质量好,是目前应用最广泛的一种溅射淀积方法。
4.反应溅射:
在淀积同时形成化合物。
5.偏压溅射:
在一般溅射基础上,加一定偏置电压在衬底与靶材料之间,改变入射到衬底表面的带电粒子的数量和能量。
6.接触孔中薄膜的溅射淀积:
带有准直器。
7.长投准直溅射技术:
不用准直器便能改善接触孔底部覆盖效果的溅射技术。
需要解决的问题:
1)溅射会导致反应室室壁表面凝结靶材料的原子,从而形成污染;
2)远离硅片中心的通孔存在台阶覆盖的不对称性;
3)在低压下获得等离子体比较困难。
总结:
1.PVD概念,分类;
2.真空蒸发概念,过程;
3.汽化热,饱和蒸汽压;
4.目前对蒸发法加热方式有几种;
5.溅射概念,其基础是什么;
6.溅射的用途;
7.溅射方法有几种,接触孔中薄膜的溅射淀积方法。
Chap6化学气相淀积
6.1CVD模型
1.CVD的基本过程
6.2CVD系统
CVD系统构成:
一、CVD的气体源
1.液态源的好处
2.冒泡法
3.冒泡法存在问题
4.对冒泡法的改进方法
二、质量流量控制系统
三、CVD反应室的热源
分为热壁和冷壁系统两种。
四、化学淀积方法:
1.常压化学气相淀积APCVD
AtmosphericPressureCVD
2.低压化学气相淀积LPCVD
LowPressureCVD
3.等离子化学气相淀积PCVD(即等离子体增强化学气相淀积PECVD)PlasmaEnhancedCVD
第一种质量输运控制,后两种表面反应控制。
了解各自特点,原理,优缺点。
6.3CVD多晶硅的特性和淀积方法
6.4CVDSiO2的特性和淀积方法
6.5CVD氮化硅的特性及沉积方法
6.6金属的化学气相淀积
Chap7外延
定义:
外延(epitaxy)是在单晶衬底上生长一层单晶膜的技术。
它是在低于晶体熔点的温度下,在表面经过细致加工的衬底上沿着原来的结晶轴方向,生长一层导电类型、电阻率、厚度和晶格结构完整性都符合要求的新单晶层的过程。
新生单晶层按衬底晶相延伸生长,并称此为外延层。
长了外延层的衬底称为外延片。
7.1硅气相外延工艺的基本原理
7.2外延层中的杂质分布
1.掺杂原理
2.扩散效应:
衬底中的杂质与外延层中的杂质在外延生长时互相扩散引起衬底与外延层界面附近的杂质浓度缓慢变化的现象。
3.自掺杂效应:
衬底和外延层中的杂质进入到边界层中,改变了边界层中的掺杂成分和浓度,导致了外延层中杂质的实际分布偏离理想情况。
7.3低压外延7.4选择外延7.5硅烷热分解法外延
7.6SOS技术7.7分子束外延7.8层错、图形漂移及利用层错法测量厚度7.9外延层电阻率的测量
7.10外延层质量控制及外延层的测量
Chap8光刻工艺
1、光刻的定义:
光刻是一种图形复印和化学腐蚀相结合的精密表面加工技术。
它是集成电路制造中最关键的一道工序。
随着集成电路的集成度越来越高,特征尺寸越来越小,晶圆片面积越来越大,给光刻技术带来了很高的难度。
尤其是特征尺寸越来越小,对光刻的要求更加精细。
通常人们用特征尺寸来评价集成电路生产线的技术水平。
二、光刻的目的:
光刻的目的就是在二氧化硅或金属薄膜上面刻蚀出与掩膜版完全对应的几何图形,从而实现选择性扩散和金属薄膜布线的目的。
三、在ULSI中对光刻的基本要求:
1、高分辨率:
分辨率的表示方法:
第一种是以每毫米最多能够容纳的线条数来表示。
即线宽。
条数/mm;
第二种是以剥蚀后的二氧化硅尺寸减去光刻掩膜版的图形尺寸除以2表示。
2、高灵敏度:
为了提高产量要求曝光所需要的时间越短越好,也就是要求灵敏度高。
也称感光度,以光刻胶发生化学反应所需要的最小曝光量的倒数来表示。
3、精密的套刻对准
4、大尺寸硅片的加工
5、低缺陷
四、光刻三要素:
光刻胶、掩膜版和光刻机
8.1光刻工艺流程
以负胶为例来说明这八个步骤,一般可分为:
打底膜->
涂胶->
前烘->
曝光->
显影->
后烘(坚膜)->
腐蚀(刻蚀)->
去胶。
1、打底膜(六甲基二硅亚胺HMDS)
二、涂胶
1.目的:
在硅片表面形成厚度均匀、附着性强,并且没有缺陷的光刻胶薄膜。
2.质量要求。
3.方法:
滴涂法,喷涂法。
4.影响因数:
转速,时间
三、前烘
去除胶层内的溶剂,提高光刻胶与衬底的粘附力及胶膜的机械擦伤能力。
2.方法:
烘箱法,热板式,干燥循环热风,红外线辐射等。