选煤一些主要设备Word文档下载推荐.docx
《选煤一些主要设备Word文档下载推荐.docx》由会员分享,可在线阅读,更多相关《选煤一些主要设备Word文档下载推荐.docx(12页珍藏版)》请在冰豆网上搜索。
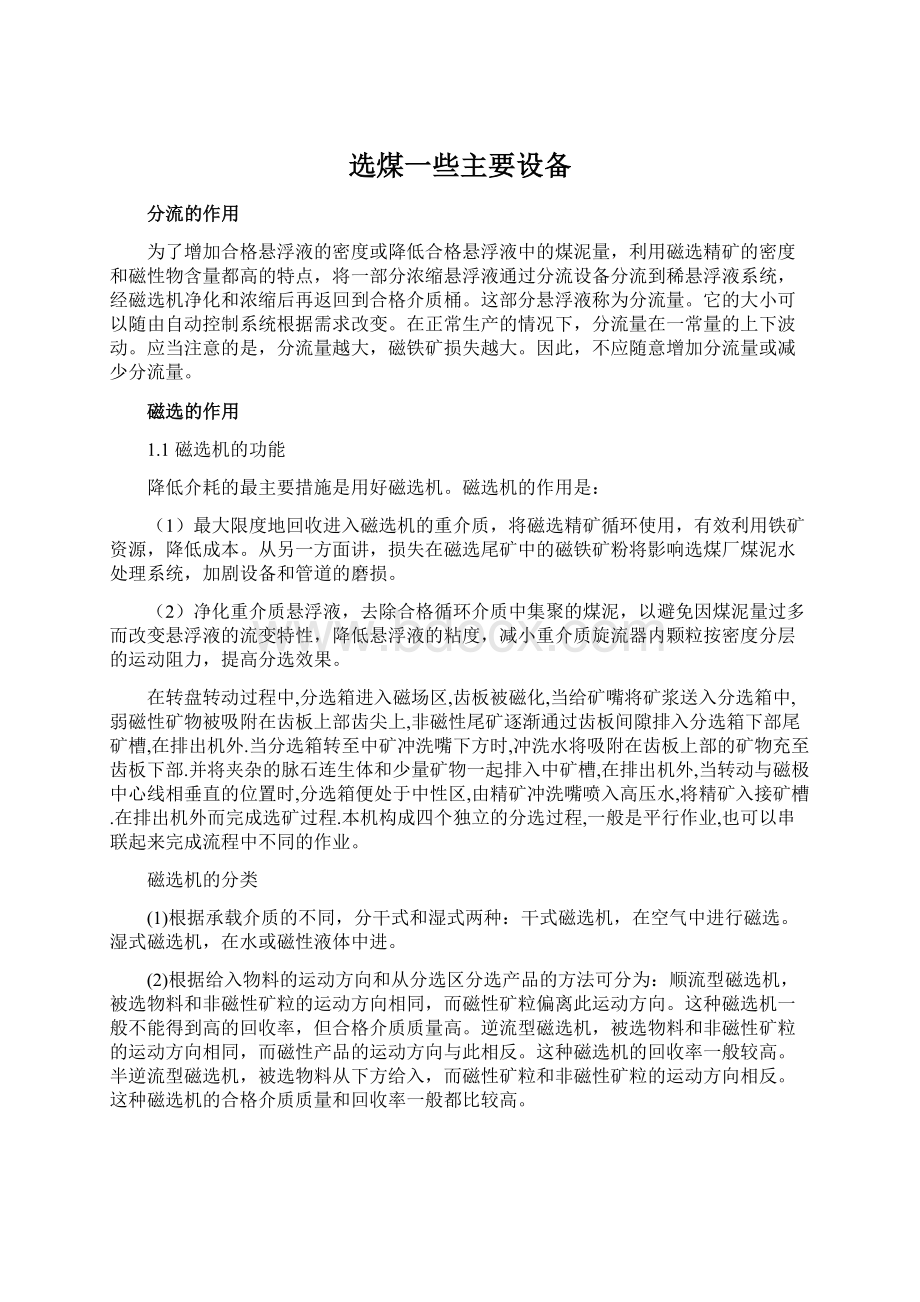
这种磁选机的合格介质质量和回收率一般都比较高。
(3)根据产生磁场的方法分为:
永磁型磁选机、电磁型磁选机、超导型磁选机。
选煤厂常用的磁选机是湿式、逆流、永磁筒式磁选机。
筒式磁选机又分为单筒和双筒两种。
1.2磁选机工艺效果的评定指标
1)磁性物回收率(%)
磁性物回收率是指精矿中所回收的磁性物占入料中磁性物的百分比,可用它来定量评定磁选机回收磁性物的多少。
式中:
γβ——精矿产率,%;
Mα——磁选入料中的磁性物含量,%;
Mβ——磁选精矿中的磁性物含量,%;
Mθ——磁选尾矿中的磁性物含量,%;
2)煤泥净化率(%)
煤泥净化率是指磁选机尾矿中排出的煤泥占入料的百分比,用来定量评定重介质悬浮液得以净化的效果。
磁选机入料中的非磁性物可视为煤泥,基于这一概念:
式中,ε'为精矿中非磁性物混杂率,
两段式磁选机的第二段入料是第一段的尾矿,其产率计算见图2,根据
(2)式分别计算第一段精矿产率γθ1=γα-γβ1和第二段的相对精矿产率γ'β2。
由于第二段的相对产率是以第一段尾矿为基数计算的,所以换算为以磁选机入料为基数的第二段精矿产率后,
根据式
(1)计算综合磁性物回收率:
根据式(4)计算综合非磁性物混杂率:
2清水脱介的关键作用
2.1清水选煤的技改措施
“1+1”模式选煤厂工艺流程实现了洗水一级闭路循环,若各环节正常工作,即可实现清水选煤。
由于该厂投产后煤质发生了变化,煤泥量增大,为此对原煤泥水系统实施了技术改造。
(1)2005年3月增加了一台ITT(B)70型斜管浓缩机(原设计已作为第一段斜管浓缩机预留位置,但未建设)。
原有的二台斜管浓缩机并联工作,使得用于第二段浓缩作业的澄清沉淀面积增加了一倍,添加絮凝剂后澄清水浓度为0.1%。
(2)2006年7月增加了两台XMGZ300/1600-X/U型精煤压滤机,将浮选精煤脱水回收能力增加了一倍,适应了全厂煤泥产率达35%的严峻局面。
2.2清水选煤是关键
重介质选煤厂的循环水主要用作脱介筛喷水。
是有实现了煤泥水的深度澄清,才能实现清水选煤脱介,降低介耗。
清水脱介之所以是关键,原因有二:
(1)喷水的固体浓度对脱介效果有直接影响
用清水喷洗和用一定浓度的循环水喷洗脱介筛筛上物,其效果截然不同。
经弧形筛预先脱介后,剩余的介质以极细小的颗粒形式粘附在煤粒表面,如果循环水携带煤泥,那么这些煤泥肯定是集中了全厂灰分最高、泥质最多、粒度最细的部分,它们的比表面积大、吸附能力强、与微细的磁性物亲和力高,对脱介是极其不利的。
(2)煤泥浓度对磁选效果的影响
q——煤泥浓度(用固体含量表示),g/L;
δ——煤泥平均密度,g/cm3。
磁选机入料中的煤泥浓度会影响磁性物颗粒粘附到滚筒上的速度。
在同样入料流量的条件下,必然会使部分磁性物颗粒来不及被回收,而损失到尾矿中。
磁选机工作原理见图3。
理想条件下,在磁选机A点处,磁性物颗粒主要受到磁力Fe、重力G0和水的粘性摩擦阻力Rs三者作用,当Fe大于G0与Rs的合力时,磁性物颗粒才能具有朝向滚筒的运动速度V0。
实际上,由于进入磁选机的入料中还携带相当数量的煤泥,干扰了磁性物的运动速度V0,干扰作用的大小,与煤泥的浓度有关,可用下列经验公式表示:
V=V0(1-λ)n。
V——磁性物颗粒趋向于滚筒的干扰运动速度cm/s;
n——浓度干扰系数,一般n=4.7
λ——固容积浓度,λ=q/100δ;
以325#精煤磁选机为例,其入料中煤泥浓度为175g/L,则干扰运动速度。
由此表明,由于非磁性物粒群的干扰,磁性物颗粒朝向滚筒运动的速度减小了41.99%。
如果不用清水脱介,那么喷水中所携带的细煤泥必然也进入磁选机,使入料中的煤泥浓度增高,干扰程度越发严重。
图4所示为磁性物颗粒朝向滚筒的运动速度随磁选机入料中煤泥浓度的增加而减小的趋势。
只有实现了清水选煤脱介,才能将煤泥对磁选工艺效果的影响降到最低。
3降低介耗的主要措施
3.1优化介质供应基地
按照磁性物含量>95%,<0.045mm(325网目)粒级产率>
85%的质量指标以及价格适中的原则,选择诚信度高的供应厂商,并严格进货管理,加强计量工作,做到不掺水、不亏吨,贮存、堆放、保管无损失。
3.2强化脱介喷水效果
(1)保证脱介喷水压力在0.2MPa以上,每个喷嘴喷水量约3m3/h,喷射水流强而有力。
(2)喷嘴沿着各脱介筛筛箱横断面均匀布置,形成完整的连续水帘。
精煤脱介筛设置三排喷嘴,每排14或16个,中煤脱介筛设置两排喷嘴,每排14个,矸石脱介筛设置两排喷嘴,前排5个,后排7个。
(3)中煤和矸石脱介弧形筛分别设置了9个一排和5个一排的喷嘴。
各脱介筛的单位负荷和单位喷水量见表2,与GB50359-2005《煤炭洗选工程设计规范》的推荐值相比,该厂各项喷水指标均已达到国家标准。
(4)脱介筛的选型也是影响脱介效果的主要因素。
针对精煤产率高、粒度组成细、携带煤泥量大的特点,该厂选用DMS3636超宽型双通道直线振动筛作为精煤脱介筛。
该振动筛振幅大(双振幅>11mm),振次高(890次/min),长宽比为1:
1,所以料层薄,物料能在筛面上抛掷式前进,喷水也能较容易的穿透物料层。
3.3提高磁性物回收率
磁性物回收率是磁选机工艺效果最为重要的指标,一般情况下,设备制造商提出的磁性物回收率保证值为99.8%,若每小时进入精煤磁选机的磁性物为15t,则从尾矿中损失的磁性物为30kg,如果磁性物回收率降到99.7%,则每小时损失的磁性物将达45kg。
该厂投产时选用了2台5磁系单滚筒HMDAφ914×
2972型磁选机,并联用于回收精煤稀介质和分流的浓介质。
经多方调试,磁性物回收率达不到厂商的保证值,介耗一度高达3kg/t以上。
2005年2月购置了两台6磁系单滚筒HMDAφ914×
2972型磁选机,根据厂房空间位置的实际情况,取代了原有的一台精煤磁选机和中煤、矸石磁选机,并将换下来的磁选机安装在下层,与两台精煤磁选机串联使用,改动后工艺效果良好(见表1)。
从表1可以看出:
(1)6磁系磁选机中,327#中煤、矸石磁选机比325#精煤磁选机第一段的磁选效果好,磁性物回收率为99.81%,其原因是前者入料流量较少;
磁性物颗粒较粗,所受到的磁力大;
而且随同进入的煤泥量较少,对磁选机的干扰程度低。
(2)在精煤磁选机第一段中,6磁系(325#)比5磁系(326#)的磁选效果好,但它们的磁性物回收率远小于99.8%。
(3)同样是双段串连的磁选机,325#的磁选效果要好于326#,磁性物回收率达99.85%,原因是325#第一段是6磁系的。
(4)精煤磁选机两段串联后,磁性物平均回收率达到了99.8%,325#综合磁性物回收率与单段相比提高了0.21%,326#提高了0.19%,按每小时进入的磁性物为15t计算,分别少损失31.5kg和28.5kg。
磁性物颗粒在设备中回收时间短暂,以精煤磁选机为例,矿浆平均流速约0.35m/s,回收时仅3s左右。
受生产条件的影响,磁选机入料中不可避免地会混入>0.5mm的颗粒,这些颗粒沉淀在磁选机槽底,堵塞或部分堵塞矿浆流道,致使流速突增,尤其是细颗粒磁性物来不及粘附在滚筒上,就随尾矿流失了。
为此,在每台磁选机上增设排粗装置,及时排除沉淀的粗颗粒,使矿浆沿槽宽均匀流动,有助于磁性物回收。
三产品重介质旋流器
三产品重介质旋流器是由两台两产品旋流器串联组装而成的。
第一段为主选,采用低密度悬浮液进行分选,选出精煤和再选入料,同时由于悬浮液浓缩的结果,为第二段准备了高密度悬浮液。
第二段为再选,分选出中煤和矸石两种产品。
三产品重介质旋流器是用一台圆筒旋流器和一台圆锥旋流器串联而成(见下图
双圆筒串联型无压给料三产品重介质旋流器见图
图1-2无压给料三产品重介质旋流器结构简
一台三产品重介质旋流器代替两台两产品重介质旋流器,其优点是:
可以省掉一个悬浮液循环系统和再选物料的运输;
减少厂房空间,并方便生产管理。
但是,第二段悬浮液是由第一段旋流器浓缩而来,所以第二段旋流器的分选密度除与第一段分选密度有关外,还与第二段底流口直径有关。
因此,在正常情况下,只改变入料悬浮液的密度和第二段底流口直径两个参数,即可达到所需分选密度的调整范围
1.工作原理
煤和矸石的混合物渐开线给料方式进入充满给定密度悬浮液的旋流器中,受到重力和离心力的作用而分离;
大于悬浮液密度的矸石,所受作用力的方向与离心加速度方向相同,在悬浮液中做离心运动,集中在外层形成矸石带,由于干扰沉降作用,紧贴器壁的是大矸石,其次是中等粒度、小粒度矸石,汇合成螺旋运动沿器壁由底流口排出;
小于悬浮液密度的煤,在旋流器中做向心运动,并集中在旋流器的中心轴附近呈旋涡运动形成中煤和精煤带,在溢流管附近,由于溢流管底部的涡流作用发生二次分选,精煤沿溢流管排出,中煤和矸石将再旋流,中煤带在轻颗粒与重颗粒间起隔栅作用,该处可使灰分较低的中煤向底流口方向运动,作为尾煤排出或随精煤沿溢流管排出。
近年来,我国选煤厂开始采用小直径重介旋流器来分选0~1mm的煤泥,一般10台一组,结构材料为Q235A外壳,内用耐磨聚氨酯弹性体,在煤泥分选方面有一定的效果。
二、操作要点
(1)旋流器在工作过程中要保持给料压力和给料浓度的稳定,这样有利于保持较高的分选效率。
(2)加强巡回检查,发现入料管口和底流口堵塞及时停机处理。
(3)经常检查底流口磨损情况,当磨损量达到影响分选效率的尺寸时要及时更换。
工作条件:
在实际生产中,实现重介旋流器有效分选的条件是,旋流器轴心必须形成空气柱。
在正常情况下,因底流口附近悬浮液所受离心力大,切线速度大,底流必定呈幅射伞状排出。
因此,要求有足够的给料速度和压力以保持其稳定。
旋流器因制造粗糙和磨损造成旋流器内凹凸不平或阻塞等,都将破坏悬浮液在旋流器中的正常流态,降低分选效果。
优点:
1)分选效率高2)分选粒度范围宽;
3)可使用粘度很高的悬浮液;
4)简化工艺节约投资;
5)结构简单,易实现自动化。
缺点:
设备磨损严重,悬浮液的用量较大,液流在旋流器内的工作不能直接调节。
三、影响重介旋流器分选效果的因素
(一)旋流器结构参数对分选效果的影响
锥角大小的影响
锥比的影响
入料口尺寸的影响
溢流管插入深度的影响
安装角的影响
(二)操作调整对分选效果的影响
1、入料压力的影响
入料压力是旋流器内产生离心力作用的动力,是使物料得到有效分选的重要因素。
增大入料压力悬浮液进入旋流器的速度增大,离心力增高。
因此,在一定程度上增大入料压力,可以加速分选过程,提高旋流器的处理量和分选效果。
但入料压力过高,悬浮液本身的浓缩作用加强,一方面使悬浮液的密度在旋流器中分布更加不均匀,另一方面增大物料的实际密度,反而降低了分选效果。
此外入料压力增大还将增加设备的磨损和动力消耗。
现在趋向采用无压给料或低压给料,一般给料压力为0.05MPa~0.10MPa。
2、入料固液比的影响
入料固液比的操作中经常调整的一个因素,它直接影响旋流器的处理量和分选效果。
当入料固液比增大时,旋流器的处理量将增加,但物料分层阻力增大,轻重矿物彼此混杂的可能性增加,分选效果降低。
一般情况下采用1:
4~1:
6的固液比为宜,处理难选煤时固液比可以降至1:
8。
3、加重质粒度和悬浮液中煤泥含量的影响
悬浮液密度的稳定性是影响分选效果的重要因素。
由于加重质粒度越粗,旋流器内浓缩作用越加显著,而过高的浓缩对分选是不利的。
因此对加重质的粒度组成要求比较严格,尤其是低密度分选条件下加重质粒度要求更细。
一般重介旋流器要求磁铁矿中粒度小于0.028mm级含量不低于90%。
4、悬浮液密度的影响
产品质量主要靠调节悬浮液产密度来调节。
悬浮液密度的大小要根据原煤性质和产品质量来确定。
一般入料中悬浮液密度比实际分选密度低0.2~0.4。
要求的分选密度越高,这种差别就越大。
在实际生产过程中这个差值可以通过旋流器的入料压力与底流口大小来调节。
离心脱水机
离心式污泥脱水机的特点和工作原理离心机是继板框压滤机和带式压滤机之后,又一代新型先进的污泥脱水设备,它与带式机相比,有着独特优点,具体体现为:
①卧螺离心机利用离心沉降原理,使固液分离,由于役有滤网,不会引起堵塞,而带机利用滤带使固液分离,为防止滤带堵塞,需高压水不断冲刷;
②离心机适用各类污泥的浓缩和脱水,带机也适用各类污泥,但对油性、粘性、剩余活性污泥需投药量大且脱水困难;
③离心机在脱水过程中当进料浓度变化时,转鼓和螺旋的转差和扭矩会自动跟踪调整,所以可不设专人操作,而带滤机在脱水过程中当进料浓度变化时,带速、带的张紧度、加药量、冲洗水压力均需调整,操作要求较高;
④在离心机内,细小的污泥也能与水分离,所以絮凝剂的投加量较少,一般混合污泥脱水时的加药量为:
1.5kg/t[干泥],污泥回收率为95%以上,脱水后泥饼的含水率为60%-85%左右,而带滤机由于滤带不能织得太密,为防止细小的污泥漏网,需投加较多的絮凝剂以使污泥形成较大絮团,一般混合污泥脱水时的加药量大于3kg/L〔干泥〕,污泥回收率为90%以上,脱水后泥饼含水率80%左右;
⑤离心机每立方米污泥脱水耗电为1kw/m3,运行时噪音为小于85db,全天24h连续运行滁停机外,运行中不需清洗水;
而带机每立方米污泥脱水耗电为0.8kw/m3,运行时噪音为80db,滤布需松驰保养,一般每天只安排二班操作,运行过程中需不断用高压水冲洗滤布;
⑥离心机占用空间小,安装调试简单,配套设备仅有加药和进出料输送机,整机全密封操作,车间环境好;
而带机占地面积大,配套设备除加药和进出料输送机外,还需冲洗泵,空压机,污泥调理器等等,整机密封性差,高压清洗水雾和臭味污染环境,如管理不好,会造成泥浆四溢;
⑦离心机易损件为轴承和密封件,卸料螺旋推料器的维修周期一般在3年以上,进口名牌轴承和密封件可保证设备长时间高强度运行,正常的保养后可大大延长维修周期;
而带机易损件轴承数量比离心机多数倍外,滤带也需更换,价格昂贵,冲洗泵,空压机,污泥调理器也需要常维护,劳动强度大。
工作原理离心式污泥脱水机主要由转鼓、螺旋、差速系统、液位挡板、驱动系统及控制系统等组成。
离心式污泥脱水机是利用固液两相的密度差,在离心力的作用下,加快固相颗粒的沉降速度来实现固液分离的。
具体分离过程为污泥和絮凝剂药液经入口管道被送入转鼓内混合腔,在此进行混合絮凝(若为污泥泵前加药或泵后管道加药,则已提前絮凝反应),由于转子(螺旋和转鼓)的高速旋转和摩擦阻力,污泥在转子内部被加速并形成一个圆柱液环层(液环区),在离心力的作用下,比重较大固体颗粒沉降到转鼓内壁形成泥层(固环层),再利用螺旋和转鼓的相对速度差把固相推向转鼓锥端,推出液面之后(岸区或称干燥区)泥渣得以脱水干燥,推向排渣口排出,上清液从转鼓大端排出,实现固液分离。
转筒式离心机的工作原理1.1离心分别的原理物体高速旋转,发生离心力。
在离心力场内的各质点,都将遭遇较其本身重力大很多倍的离心力。
离心力的大小取决于该质点的质量。
由于含水污泥中有比重大于1的污泥,有比重等于1的水及很少的比重小于1的污油,在离心力的作用下,这几种物资所受到的离心力也不同,质量大的污泥被甩到水的外侧,再通过必须的手法使它们分别,就使含油污泥中的水和污油得到脱除,大大减少了污泥的体积。
1.2转筒式离心机的工作原理污泥从空心转轴的分配孔进入离心机,依赖转筒高速旋转发生的离心力分别固体。
螺旋输送器与转筒的旋转方向雷同,但转速稍慢。
两者之间的速差,可将脱水污泥送出血液离心机,分别液则从另一端排出。
离心脱水可以连续进行。
1.3工艺流程污水处置场发生的含油污泥先进到三渣池进行沉降脱水,浓缩后的含油污泥由泵打入污泥浓缩罐进一步沉降脱水,脱水后污泥由螺杆泵输送至离心机再次脱水分别。
液体(离心液)回到三渣池,离心机出料(固体)运送至堆泥场,污泥干化后外运至废渣坑。
2存在的问题寻常情形下,离心机进料后有两种出料情形。
一种是出料斗处能出大批泥,离心液为黑水;
另一种是出料斗出泥量有限,离心液出清水。
依据计算和实际视察,离心液为黑水时,黑水要循环处置,含油污泥的体积减少量有限;
离心液为清水时,清水用泵打到前端污水体系处置,含油污泥体积减少明显。
因此,要做到三泥减量,离心液出清水最佳。
在刚引进离心机处置炼油污水处置场污泥的很长一段时光里,由于离心机运行存在处置后果差,无法正常分别的情形,离心机运行只能做到出少量泥,离心液从来没有出过清水,只能在偶然分别出一些干污泥。
离心机运行无法解决外运废渣堆埋场污泥量大的问题。
详细问题剖析:
(1)常常展示出料口阻塞现象,影响分别后果;
(2)用聚合铝做絮凝剂,对浮渣占6O%一80%的污泥几乎没有絮凝后果;
(3)用聚丙烯酰胺做絮凝剂,溶药装备后果不好,无法施展絮凝剂作用;
(4)对聚丙烯酰胺的特色不领略,没有施展出这种絮凝剂的最佳后果;
(5)离心机操作间内H:
s严峻超标,到达100mg/L以上(安全指标为<
10mg/L),对职工性命安全是个挟制,同时也给调整操作带来了拮据。
3对策
(1)通过对离心机解体反省发掘,出料口是被粘度较大的污泥阻塞,这种情形往往展示在停机后再开机的时候,通过实验判断在开机前和停机前必须用清水对离心机进行清洗。
在随后的运行中未展示出料口阻塞情形。
(2)对含油污泥的处置,用无机的聚合铝、聚合铝铁做絮凝剂后果都不计划,通过交换和考核得知,必须利用阳离子聚丙烯酰胺做絮凝剂能力有较好的絮凝、处置后果。
(3)在利用聚丙烯酰胺做絮凝剂的历程中,对分子量不同的的聚丙烯酰胺进行实验,得出利用分子量大于1×
10的阳离子聚丙烯酰胺后果较好。
聚丙烯酰胺溶解性差,配药时简易结块,也不简易溶解,驰过对溶药装备的现状进行剖析,进行了如下革新,后果最著,使底本只能溶解2ks/次的溶药池溶药量进步到了10ks/次。
a)将搅拌机的搅拌杆加长,在底部增添一级搅拌浆,同时,将两级搅拌浆的浆叶替换成长大型浆叶。
b)创建了特地的加药斗,使聚丙烯酰胺颗粒能均匀进入溶药池。
(4)阳离子聚丙烯酰胺在投加前须要充足搅拌混杂并在搅拌形态下放置4小时以上,能力施展较好的絮凝后果。
(5)通过实验发掘,阳离子聚丙烯酰胺絮凝速度较快,加注点不能距离心机进口太远。
须要通过实验判断最佳加注点的地位。
依据阳离子聚丙烯酰胺这个性质,将底本设在螺杆泵之间的絮凝罐放弃(絮凝罐的作用是使污泥和絮凝剂在絮凝罐中充足缓和絮凝),在距离心机进1210.5m、2m、10m三个地位设加药口投加聚丙烯酰胺,通过对比实验判断利用距离心机进口2m的加药口的后果最好。
(6)通过实验,加药量对处置后果的影响也非常大。
按每吨污泥70g,200g、300g3种用量投加絮凝剂,当加药量在70g/t时后果不明显,当加药量在200g/t时离心机运行后果明显变好,能够安然出清水。
当加药量在300g/t时,处置以浮渣为主的污泥,可以大批出泥。
(7)操作空间的H:
s含量高对操作人员的性命安全是一个极大的挟制。
离心机的出料口和离心液出12I在原装备设计中没有封闭,由于含油污泥中会有大批H:
s溢出,造成操作空间中H:
S含量高,经实际测定,不采用任何措施操作空间的H2s含量都在100mg/L以上(安全指标为<
10mg/L),采用强迫对流通风措施后操作空间的H:
S含量在20mg/L以上;
冬季因为保温、通风后果差,H:
s含量在30mg/L以上。
将离心机的出料12I和离心液出12I封闭,并增添排气管,操作空间的H2S含量可以有效控制在10mg/L以下。
4运行后果将加药量控制在每吨污泥200g时,离心液以清水为主,进料应控制含水率在84%一96%,平均值在88.5%;
含油量在0.5%一1.22%,平均值在0.9%;
处置量在0.7—5.1t/h,平均在2.8t/h。
当絮凝剂加药量到达每吨污泥300g时,处置以浮渣为主的污泥,出泥量最多到达60kg/h。
驰过离心机分别后,含油污泥的含水率由平均97%降到90%,含油率由平均1.2%降到平均0.6%,后果比拟显明。
离心出料在堆泥场堆放一段时光后,在空气、阳光的作用下由黑色粘稠状变为黄色粉末状。
给运送、储存勤俭了大批的人力、物力、财力。
离心清液直接打人污水体系处置,切实减少了含油污泥量,较离心机没有运行前减少了2/3左右。
5结论
(1)转筒式离心机运转费用较低,其自身功率惟独18.5kW,连续运转每月只耗电13320kW•h,按每kW•h0.19元计算,每月运转电花费用为2109元。
(2)对粘度较大的含油污泥的浓缩脱水后果较好。
(3)可以连续运行,处置效力高,简易中意工艺请求。
(4)操作简便,操作工简易节制。
(5)离心机转子强度不高,运转一段时光后转子磨损造成出料不畅,需对转子修补后方可继承利用。
浓缩机
在选煤厂,耙式浓缩机是用于浓缩煤泥水的主要浓缩机械。
煤泥水经浓缩后分离成浓稠的煤泥沉淀物和固体含量很低的澄清水。
煤泥沉淀物送入精选或脱水作业回收煤泥,澄清水供选煤厂循环使用。
一般,耙式浓缩机煤泥的入料粒度为—0.5mm,溢流水的煤泥粒度为—0.05mm,底流的浓度大约为300-500g/L。
工作原理
耙式浓缩机是利用煤泥水中固体颗粒自然沉淀来完成对煤泥水连续浓缩的设备。
其实质是由一个供煤泥水沉淀的池