注塑模流分析报告模版Word文档下载推荐.docx
《注塑模流分析报告模版Word文档下载推荐.docx》由会员分享,可在线阅读,更多相关《注塑模流分析报告模版Word文档下载推荐.docx(43页珍藏版)》请在冰豆网上搜索。
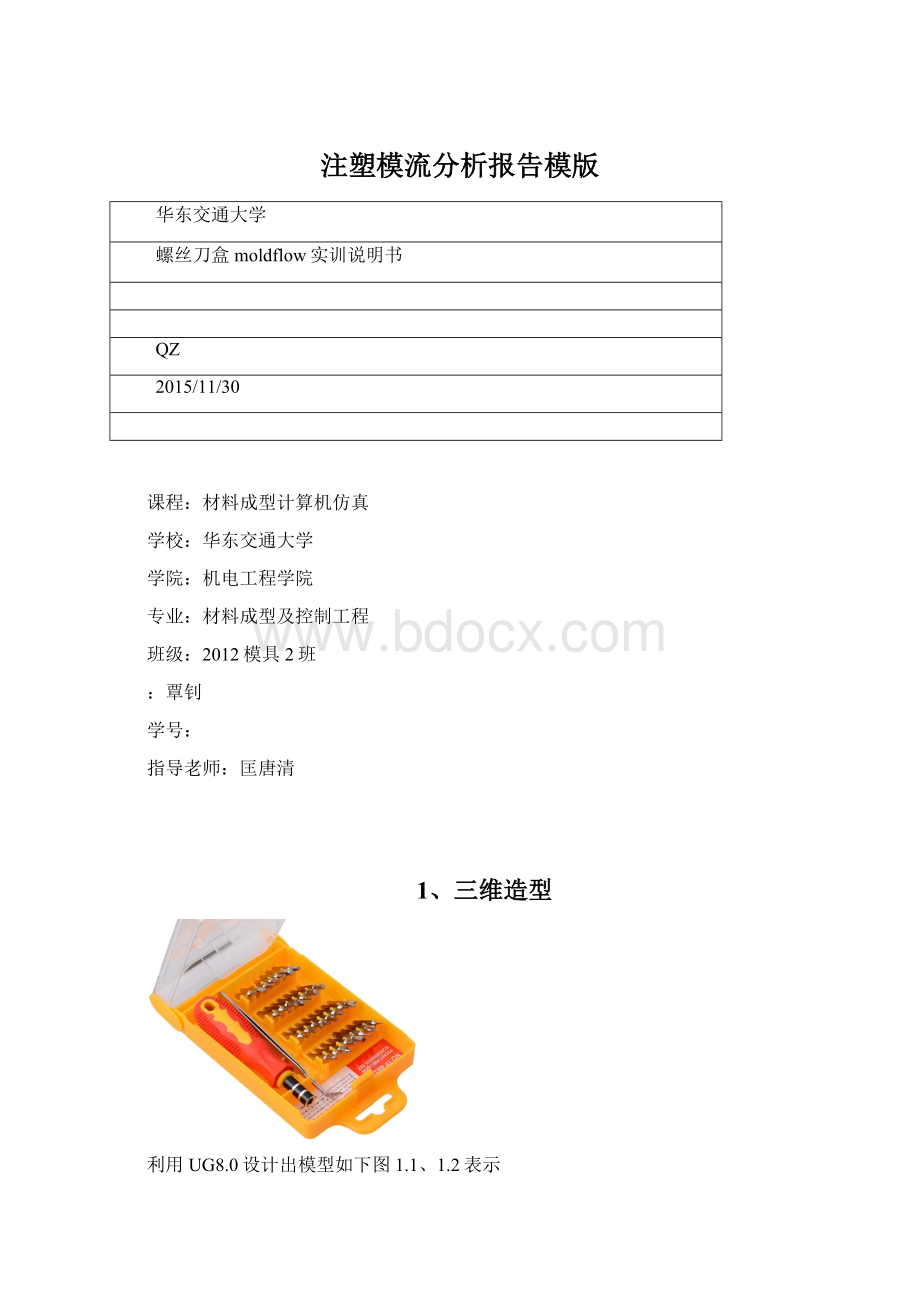
图3.1.1初次纵横比诊断
3.2网格诊断与修复
点击【网格】——【网格修复向导】,前进到选择目标纵横比,输入6,点击修复。
之后在进行手动修复,通过合并节点移动节点等方式进行,直到得到满意的结果。
如下图3.2.1:
图3.2.1修改后的纵横比诊断
修复后的纵横比为13.68,只出现少数,可以接受。
修复后的网格统计如下图3.2.2:
图3.2.2网格统计
由统计结果知,匹配率都达到了91%以上,合理。
3.3确定浇口位置
重复上述方案并冲命名为【浇口位置确定】,设置分析序列为【浇口位置】,选择材料为默认的PP材料(由于产品上信息为PP,且没有太高使用要求故选用默认的PP材料),该材料的推荐工艺如下图3.3.1:
最大剪切速率为100000(1/s),最大剪应力为0.25MPa。
图3.3材料推荐工艺
分析并等待结果,得到最佳的浇口位置如下圈出的位置
图3.3.2浇口位置分析
由于该零件比较小,需要大批量生产,故应做成一模多腔的形式,且考虑到美观的问题,浇口应设置在边沿位置,做成侧进浇,如下图3.3.3和3.3.4:
方案1:
图3.3.3方案一浇口
方案2:
图3.3.4方案二浇口
考虑过双浇口,但是快速成型分析发现双浇口的熔接痕比单浇口的要多,成型质量也相差无机。
因此放弃,综合考虑之下选择这两个方案进行对比。
【充填时间的差别】:
方案一为1的充填时间为1.151秒,
图3.3.5方案一充填时间
方案二的充填时间为1.135秒,相差不大。
图3.3.6方案二充填时间
【压力之间的对比】方案一为38.26MPa,方案2为36.68,方案二的压力更小一些。
达到顶出温度的时间对比:
方案一为22.40秒:
图3.3.7方案一达到顶出温度时间
方案二为24.40秒,方案2要更多2秒。
方案一更优。
图3.3.8方案二达到顶出温度时间
【熔接痕的对比】方案一的:
图3.3.9方案一熔接痕
然后方案二的:
图3.3.10方案二熔接痕
从图中可以看出方案2的熔接线更少,出现的位置也不是很影响美观,因此方案2更优。
但总体来说两个方案是差不多的。
相差不大
【气穴】方案一的:
图3.3.11方案一气穴
方案二的:
图3.3.12方案二气穴
从此处可以看出方案2的气穴更多,方案一更优。
但总的来说,从前面分析结果来看,两个方案的结果相差都不太大,因而下面先尝试着用方案一进行下面的分析工作。
3.4成型窗口分析
(1)复制上述方案重命名【成型窗口】,并设置分析序列为【成型窗口】
(2)设置工艺条件:
注塑机最大注塑压力为140MPa,高级选项如图3.4.1。
图3.4.1成型窗口高级选项
(3)得到结果:
质量成型窗口3.4.2
图3.4.2质量xy图
最大剪切应力3.4.3(远小于材料的0.25MPa,可以接受)
图3.4.3最大剪切应力
区域切片图3.4.4,因此可以选择注射时间为1S.
图3.4.4区域切片图
因此,选用此方案,模具温度为42(42.2)°
C,熔体温度为250(249.5)°
C。
3.5充填分析
(1)复制上方案并命名为【充填分析】,设置分析序列为充填,
(2)设置工艺参数:
模具温度42°
C,熔体温度250°
C,注射时间1s,【速度/压力切换】设置为【由%充填体积】,取值99%,其他取默认值。
(3)分析结果:
充填时间图3.5.1:
图3.5.1充填时间图
可看出等值线的间距基本一致,说明料流前锋的前进速度一致。
壁上最大剪切应力,图3.5.2,均小于材料的许用最大剪切应力0.25,
图3.5.2壁上压力图
注射位置处的压力,图3.5.3,最大为38.25MPa。
图3.5.3注射位置处压力图
最大锁模力为20.8吨,均发生在速度/压力切换的时候。
3.6流道平衡分析
(1)复制上方案并重命名为【流道系统】
(2)设置浇注系统,因为结构比较简单,不需要手工创建浇口和流道,因此利用型腔重复向导,设置一模两腔,列间距设置为200,如图3.6.1。
(UG8.0注塑模向导中初始化后一个模具工件长为195,因此取200)。
图3.6.1型腔参数
利用流道系统向导创建流道,分型面选择浇口平面,图3.6.2
图3.6.2流道参数
之后下一步,分流道按表8-1,查的直径为5-10mm,取6mm,计算得主流道直径为7.56mm,长度依据模具模架取60,拔模角去2.4deg(取值围1-3deg),浇口为直浇口,入口直径为3mm,长度为1.5mm,拔模角2.4deg,点击完成,如图3.6.3、3.6.4。
得到流道系统如图3.6.5。
通过连通性诊断无误后准备进行下一步【流道平衡分析】。
图3.6.3流道参数
图3.6.4浇口参数
因为是边缘浇口(标准浇口),设置在分型面上,所以浇口形状应为矩形。
按照标准,将浇口设置为厚度h=1.5mm,宽度W=4.5mm,长度L=0.5mm,所以浇口的设置如图3.6.5
图3.6.5浇口设置参数
图3.6.7浇注系统
复制上方案,设置分析序列为【流道平衡】充填控制选为自动,压力选择38MPa。
分析结果如下图3.6.8:
图3.6.8流道优化结果
优化为分流道的体积更改-12.58%,说明流道设计比较合理。
注射处压力最大为42.64MPa。
3.7冷却分析
(1)复制上方案并重命名【冷却分析】,设置分析序列为冷却。
(2)设置冷却系统
由于模型工件结构简单、规则,方方正正,没有大的曲面,因此采用冷却回路向导设计冷却回路。
指定水管与直径为10mm,其他选择默认。
管道数量设置为4,如图3.7.1。
得到冷却回路(图3.7.2)并进行分析。
图3.7.1冷却回路参数
图3.7.2冷却回路
设置的参数如下图。
图3.7.3冷却设置
图3.7.4冷却液设置
目标温度为42°
C,因此设置水温为25°
C,分析后得到结果:
管壁温度为29.14,和水温温度差小于5°
C,合理,
回路管壁温度如下图3.7.5:
图3.7.5回路管壁温度
【型腔温度】如图3.7.6
图3.7.6型腔温度结果摘要
按要求,型腔表面温度应该和模具表面温度相差10°
C上下,但由日志结果可知道明显不符合要求。
因此要改进方案,将冷却液的入口温度改为30°
C、35°
C,40°
C,设置工艺参数其他一致,再进行分析。
最终30°
C的结果符合要求,选用此方案,结果如图3.7.7
图3.7.7型腔温度结果摘要
零件达到顶出温度的时间为25.78s,所以IPC时间设置为26S。
3.8流动分析
复制上述方案重命名【填充+保压】,进行恒温保压分析。
由前面的分析结果可知最大注射压力为44.68MPa,所以初涉保压压力设置为44.7MPa,保压时间=IPC时间25s-充填时间1s=25s,保压工艺设置如下图。
图3.8.1工艺参数
分析后得出顶出时的体积收缩率最大为12.54%,壁厚为1.5mm的PP塑料制件体积收缩率围应在1.39%到5.43%之间,此方案的体积收缩率局部过大,需要改善,再根据结果取合适的方案。
图3.8.2顶出时的体积收缩率
压力XY图3.8.3
图3.8.3压力xy图
由图可知达到最大压力时间为2.76s,凝固时间为5.28,取中间值4s为恒压/降压转换点,查看分析日志,压力/速度转换时间为1.12s,因此第一段恒压保压时间为2.9s,查看冻结层因子,发现浇口在14s时冻结。
所以保压控制曲线控制为下图:
3.8.4和3.8.5
图3.8.4保压控制曲线设置图3.8.5保压控制曲线
进行优化后的结果如下:
图3.8.6顶出时的体积收缩率
压力XY图
图3.8.7压力xy图
优化后的压力XY图曲线发生了明显的变化,制件大部分的体积体积收缩率颜色相近
可以看出体积收缩更为均匀,但是制件厚度较大的地方的最大的收缩率仍在11.78%,仍需要进一步优化。
其他条件不变,将保压压力提高到65MPa,体积收缩率仍没有改善,反而下限更大,因此排除是保压压力的因素影响,此处不再贴出图片。
顶出时的体积收缩率:
最小不小于0,最大仍为12.42,可见优化有效,但是制件最厚的地方的收缩率仍然无法得到大的改善。
原因可能是因为该处比制件大部分壁厚要厚很多且在充填末端,无法避免。
尝试过很多种方法,仍然无法得到明显的改观。
因此,尝试着再次更改浇口位置,再次尝试方案二。
4、再次尝试方案2
4.1成型窗口分析2
(1)复制上述方案二重命名【成型窗口】,并设置分析序列为【成型窗口】
注塑机最大注塑压力为140MPa,其他默认。
高级选项如图4.1.1
图4.1.1成型窗口高级选项设置
质量成型窗口4.1.2
图4.1.2质量xy图
区域切片图
图4.1.3区域切片图
所以选择注射时间为0.6s
最大剪切应力,图4.1.3,远小于材料许用应力,合理
图4.1.4最大剪切应力
4.2充填分析2
(1)复制上方案并命名为【充填分析2】,设置分析序列为充填,
C,注射时间0.6s,【速度/压力切换】设置为【由%充填体积】,取值99%,其他取默认值。
壁上剪切应力:
小于材料的许用应力0.25,图4.2.1,合理。
图4.2.1壁上剪切应力
压力:
37.54为注射位置处最大压力。
图4.2.2压力
达到顶出温度的时间:
图4.2.3达到顶出温度时间
检查其他各项,没有不合理的地方,进行下一步。
4.3浇注形态及优化2
大体步骤如前面3.6流道系统与平衡分析,不再赘述,只讨论分析结果。
注射位置处的压力
图4.3.1注射位置处压力xy图
最大注射压力为42MPa。
剪切应力方面:
图4.3.2剪切应力
,可知远小于材料的0.25,合理。
查看优化方案:
图4.3.3
图4.3.3流道优化
可知系统将分流道的体积缩小了12.5%,优化结束。
进行下一步——冷却系统的分析。
4.4冷却分析2
设置也如【3.7冷却分析】,得到的冷却回路如下图4.4.1
图4.4.1冷却回路
冷却液温度依然设置为默认的25°
C,得到结果图4.4.2:
1型腔温度数据
图4.4.2型腔温度结果摘要
型腔表面温度平均值为42.8744,与模具温度非常接近,非常合理。
2回路冷却液温度:
图4.4.3
温差不超过2℃,合理。
图4.4.3回路冷却液温度
3回路管壁温度:
最大为29.04℃,也不超过冷却液入口温度5℃,合理。
图4.4.4回路管壁温度
4.5保压分析及优化2
(1)进行首次保压分析,分析序列设置为【冷却+填充+保压】,设置好工艺参数如图4.5.1、4.5.2、4.5.3
图4.5.1冷却设置
图4.5.2充填控制
图4.5.3保压曲线控制
然后进行分析,得到结果如下,图4.5.4:
1顶出时的体积收缩率:
达到了12.97%,主要仍然集中在制件最厚的地方以及浇口处。
该PP材料制件体积收缩率围(1.5mm)应在1.39%到5.43%之间,明显需要进行优化。
图4.5.4顶出时的体积收缩率
2压力XY图:
图4.5.5压力xy图
体积收缩率过小的地方,说明该处过保压,制件较厚处收缩率大,说明保压补缩不够,还需要提高保压压力。
(2)保压优化
将保压压力设置为40MPa,其他参数不变,分析得到结果:
最大的收缩率降低到9.275,但最小的体积收缩也出现了-0.636,说明过保压加剧了。
图4.5.6方案1的顶出时体积收缩率
尝试其他方案:
将压力分别设置成:
方案2为60MPa、方案3为75MPa,其他参数不变,依次分析得到结果。
方案2(60MPa)的顶出时体积收缩率:
最大为8.986,最小为-1.228
图4.5.7方案2的顶出时体积收缩率
方案3(75MPa)的顶出时体积收缩率:
最大为8.697,最小的为-1.670
图4.5.8方案3的顶出时体积收缩率
还是未能达到要求。
通过对比数据发现在40-75MPa的围,压力越大,体积收缩率约小,但同时也会出现负收缩越来越大的情况,也就是过保压越来越严重。
综合比对,最终选择以40MPa为恒压保压压力。
并且通过创建保压曲线并优化,以缩小制件上主体积的收缩率的差异。
尽可能实现均衡收缩。
压力XY图如下
图4.5.9压力xy图
通过分析,充填末端在2.5s时达到最大,5s的时候为0,取中间值3.8s作为恒压/降压转换点。
查看冻结层因子结果,得到浇口在15s处冻结。
速度压力时间切换为0.66s,由此确定第一段恒压保压时间为3.1s,第二段卸压时间为12.2s。
设置参数如图:
图4.5.10保压控制曲线设置
图4.5.11保压压力与时间图
得到的结果如下:
图4.5.12顶出时的体积收缩率
最大的体积收缩率为9.798,最小为0.0650,(壁厚为1.5mm的收缩率应在1.39%到5.43%之间,壁厚为5mm的收缩率应在1.71%到6.75%之间)没有过保压现象。
主要问题还是集中在制件较厚的地方还有浇口附近,但相比之前的方案得到了很大的改善,且收缩率大的区域十分小,制件主体的收缩率也很均衡。
如果要改善浇口附近制件较厚处的收缩率过大的情况,那么就要增大保压压力,但是通过分析可以发现这样会使其他区域的收缩率大大降低,而且区域会想当大,甚至很多区域会出现过保压的情况。
制件主体部分也会受到影响。
所以到此保压优化完成,最终确定使用此方案。
4.6翘曲分析2
翘曲分析与优化是分析流程的最后一个步骤,充填、冷却、保压这三个因素都是翘曲变形的主要因素。
翘曲分析结果的好坏说明前面工作的质量。
若翘曲变形过大,则需要重新对前面的方案进行优化。
分析后的结果:
所有因素:
可以看到在侧面的孔洞处的变形为0.28mm,其他各个地方的变形都很小,
图4.6.1变形,所有因素
Y方向:
变形量为0.264
图4.6.2变形因素Y方向
X方向:
变形量为0.1761,变形量较小。
图4.6.3变形因素X方向
冷却不均匀:
变形量为0.1427
图4.6.4变形,冷却不均
收缩不均匀:
变形量达到了0.28
图4.6.5变形,收缩不均
取向因素:
图4.6.6变形,取向因素
从上面的结果可以得出,变形量主要是由于收缩不均匀引起的,接近总的变形量。
图4.6.7收缩不均X方向
图4.6.8收缩不均Y方向
由上图可以分析得出,收缩不均匀的地方是注射末端以及制件厚度突变的卡扣处和侧孔,而引起收缩不均匀的原因一部分是制件厚度并非一致,以及保压方面的问题。
总之还是不可避免地引起了翘曲变形,但总体来说变形量不算很大,可以接受。
5、总结分析(最终方案)
5.1浇口位置
浇口位置应设置在如下图圈出的位置处。
图5.1.1浇口位置
5.2制件材料
选用一般的PP料。
5.3浇口
将浇口设置为厚度h=1.5mm,宽度W=4.5mm,长度L=0.5mm
5.4流道
主流道直径为7.56mm,拔模角2.4度,长度60mm。
分流道直径为6mm,
图5.4.1流道主视图
图5.4.2侧视图
5.5注射设置
模具材料选用P20;
模具温度:
42℃;
熔体温度250℃,开模时间5s,
注射时间0.6s,保压压力为40MPa,保压控制如下,【注射+保压+冷却时间】设置为25s。
图5.5.1保压控制
5.6冷却系统
水管直径为d=10mm,水管与零件间的距离为25mm,水管与零件排列方式为沿X方向。
冷却介质选用纯水,冷却介质入口温度设置为25℃。
流动类型为层流,所以雷诺数Re设置为2000。
查表得纯水在25℃时的密度为ρ=0.997kg每平方毫米,粘度为η=0.8937N*s每平方毫米,冷却液平均流速U=Re*η/(ρd)=17.928mm/s=0.17928m/s取0.18米每秒。
图5.4.1冷却回路主视图
6、致
非常感匡老师,不辞辛劳地解答各种疑问。
现在看来,当初的问题很多都问得甚至是相当的愚蠢,例如纵横比修复和优化这种比较低级问题,但匡博还是手把手教到会为止,不胜惭愧。
很难想象匡博这样的忙人,怎样抽出时间,才能录制了近十五个小时的教学视频,孜孜不倦地一点一点地教会,再简单再细小的细节也没有略过,语言已经无法来形容这种敬业的态度,五体投地也不能。
甚至在有些视频里甚至可以听得出匡博是感冒了的,声音明显变了,还咳嗽……这种情况下老师依然给我们录制视频。
有此良师,只能说三生有幸。
7、感受与建议
总体来说,这个课设总算是亲力亲为一步一个脚印做下来了,不断地重复和更改,花了大量的精力去优化和改进,最终才得到相对满意的结果,然而并没有做到完美,有比较细小的地方仍然是无法优化,累觉不爱。
在这个设计和分析的过程当中,就是不断地尝试,修改,得出结果,比对,在尝试在修改再比对,不断地循环不断的改进。
每个方案,每个数据,都是亲力亲为,用心血写成,虽然到最后还是得不到最满意的结果,但看着自己的成果还是有小小的成就感。
在这个课设里,最大的感触就是,行就是行,不行就是不行,没有“大概可以了”“差不多”的说法,要求的就是一丝不苟,精益求精。
有时候,为了百分之几的数据,都要进行数十次的尝试优化,虽然相差不是太大,但更好就是更好,得到更优解总会让人欣慰。
收获还是有的,对这款软件的认识和把握基本上已经进入了入门阶段,有了一定的理解和认知,这对以后走更远的路来说,起码我已经迈出了7、8个步伐。
很喜欢这种讲课之后马上实践的模式,课堂上讲理论和注意事项,机房动手,避免走弯路,上手更快。
接受起来也比较快。
建议的话,感觉要是上机课再多一些比较好,理论:
实践的比例在1:
2这样,操作更多一些,在操作中发现问题并及时解决会有更好的效果。
当然因人而异,这只是个人观点。
以上,为所有报告容。
1、三维造型1
2、模型修复与简化2
3、moldflow模流分析2
3.1网格划分2
3.2网格诊断与修复2
3.3确定浇口位置4
3.4成型窗口分析8
3.5充填分析10
3.6流道平衡分析11
3.7冷却分析14
3.8流动分析17
4、再次尝试方案220
4.1成型窗口分析220
4.2充填分析221
4.3浇注形态及优化222
4.4冷却分析224
4.5保压分析及优化225
4.6翘曲分析230
5、总结分析(最终方案)34
5.1浇口位置34
5.2制件材料35
5.3浇口35
5.4流道35
5.5注射设置36
5.6冷却系统36
6、致37
7、感受与建议37