工业机器人行业专题分析报告.docx
《工业机器人行业专题分析报告.docx》由会员分享,可在线阅读,更多相关《工业机器人行业专题分析报告.docx(13页珍藏版)》请在冰豆网上搜索。
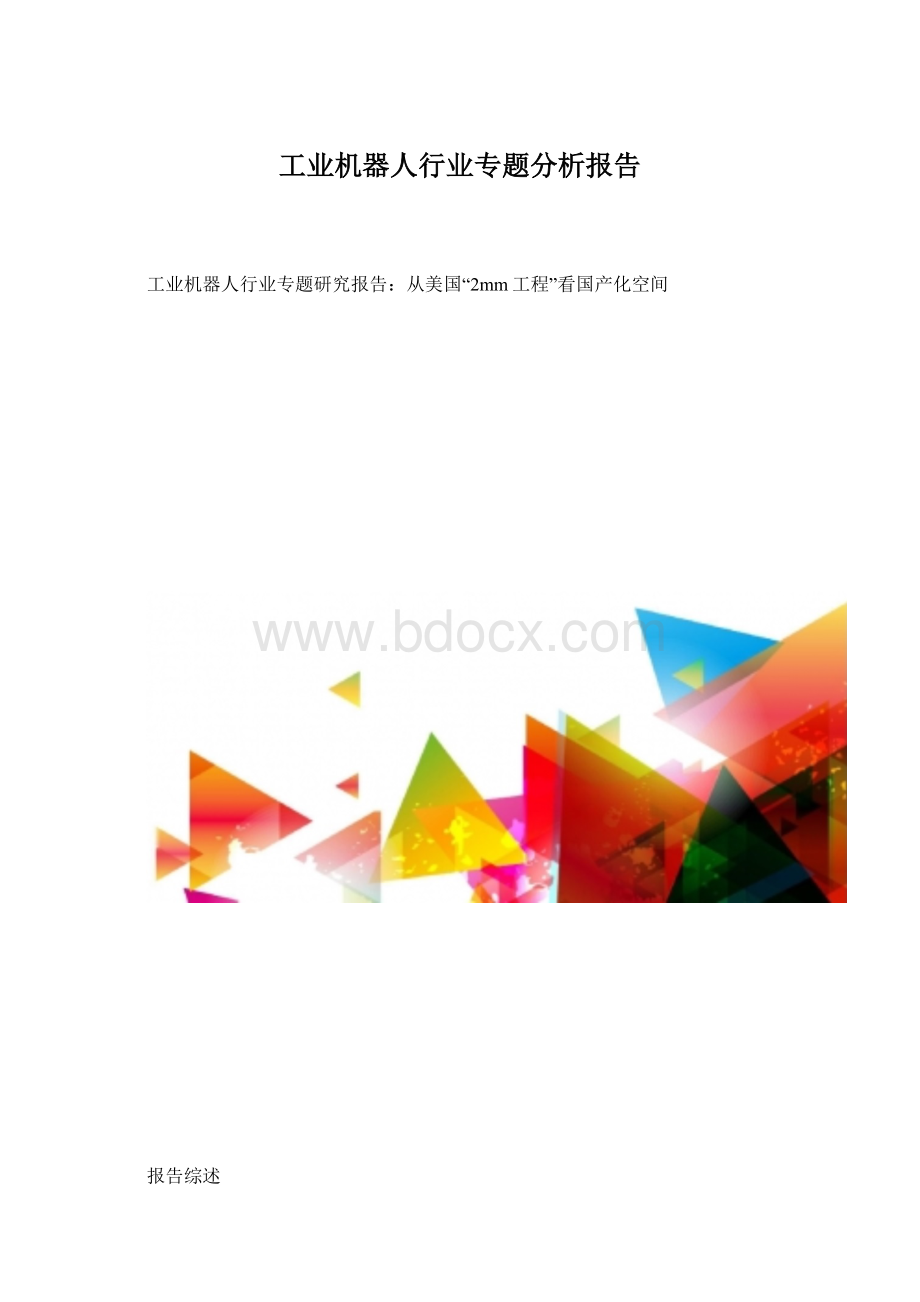
工业机器人行业专题分析报告
工业机器人行业专题研究报告:
从美国“2mm工程”看国产化空间
报告综述
工业机器人汽车行业应用领域保持下游需求规模第一位。
工业机器人下游应用广泛,主要应用行业包括汽车、电子电器、化学橡胶塑料、金属制品、食品制造等行业。
根据IFR统计,2019年全球范围内工业机器人在汽车和电子电气中的应用占比达28.15%、23.59%,合计占据工业机器人需求超过50%。
其中工业机器人在汽车行业中的应用比例,受电子行业规模扩张,基数变大的影响略有下滑,但汽车行业以其庞大的行业规模基础和较高的自动化率,我们预计汽车行业工业机器人下游需求规模仍将稳居高位。
20世纪90年代美国汽车市场发起“2mm工程”以应对日系车对市场份额的威胁。
20世纪70年代之前,美国三大车企福特、通用、克莱斯勒常年占有美国汽车销售市场份额的80%以上。
两次石油危机之后,日系车迅速抢占美国汽车市场,本田、丰田、日产共获得美国汽车市场份额的18.03%,日系车在美畅销的一大原因在于其车身尺寸误差小,整车质量高、返修率低。
为提高美国汽车品质以与日系车抗衡,美国汽车行业开展了“2mm工程”,该工程已成为系统性工程并延续至今,其主要目标就是将白车身的综合误差指数提升至日系车水平,从而提升汽车整车的质量,追回失去的市场份额。
“2mm”的尺寸偏差涉及多项工艺、涉及与操作等领域,工业机器人对产成品的精度影响仅占一小部分。
空间工序上的误差累积、设备磨损与误操作以及设计水平与装备水平等多方面都会对产成品造成尺寸误差,美国汽车行业为提高汽车质量而发起的“2mm工程”提出应重点控制冲压件尺寸偏差、焊接变形、人工操作等因素,相较之下,对零部件加工精度的要求是低于工业机器人可实现的重复定位及加工精度范围,工业机器人加工产生的尺寸误差的仅为整个生产过程中尺寸误差链中的一环。
国产汽车机器人精度紧跟国外,或迎百亿市场空间。
本文通过查阅公司官网与产品手册,以“2mm工程”中工业机器人主要涉及的工序为分类基础,比较同等负载量级下国内外机器人精度与其他参数,我们认为国产机器人在焊接、折弯等领域精度已经接近国外同类型产品。
一方面,我国工业机器人行业明显呈回暖趋势,汽车行业边际改善,汽车行业工业机器人的使用需求量存在提升空间。
另一方面,我国国产工业机器人的渗透率仍有很大提升空间,跟随中国工业机器人市场规模的扩大,并叠加国产工业机器人渗透率的提升,我国国产工业机器人2022年预期对应的市场规模区间在143.6~165.7亿元,年均增速预计可达30%以上。
一、回顾美国汽车行业的“2mm工程”
20世纪90年代,为应对日系汽车在美市场份额扩大的挑战,美国汽车行业开展了“2mm工程”,取得了良好的成果。
美国是车轮上的国家,汽车工业是美国制造业的支柱产业,机动车产出占制造业行业增加值的15%~25%。
在20世纪70年代之前,美国三大汽车公司市场占有率总和高于80%。
20世纪70年代开始,日系车进入美国市场,市场份额快速上升,迅速抢夺了美国汽车市场约20%的份额。
日系车在美畅销,除了制定了正确的营销策略顺应了石油危机的影响和迎合了消费者的需求外,其主要原因在于日系汽车的质量明显高于车身精度较低、尺寸偏差较大的美国汽车。
为了应对市场份额流失,20世纪90年代,美国汽车行业发起了旨在提高汽车质量、降低车身误差、挽回市场份额的“2mm工程”。
在“2mm工程”开展的3年(1992-1995),美国汽车质量明显提高,工程取得良好成果。
(1)美国汽车工业成熟发达,千人汽车保有量世界第一
美国被称为“车轮上的国家”,汽车工业成熟且发达。
美国密集的公路是人流、物流的重要运输命脉,同时也促使了美国汽车行业的崛起。
美国汽车产业自20世纪以来发展至今,已经经历了完整的起步、成长、成熟阶段。
汽车制造业是美国制造业的支柱,机动车产出占制造业行业增加值常年稳定在15%~25%的区间,对维持制造业产出起到了重要的作用。
同时,美国汽车的总保有量与人均保有量也长期稳居世界第一,根据世界银行2019年公布的数据,美国每千人汽车保有量837辆,几乎人均配有一辆汽车。
(2)90年代高质量日系车抢占市场,美国“2mm工程”应运而生
20世纪70年代日系汽车大举进军美国市场,严重侵蚀美国市场份额。
20世纪70年代之前,美国三大车企福特、通用、克莱斯勒常年占有美国汽车销售市场份额的80%以上,而日系汽车在美市场占有率几乎为0。
两次石油危机之后(1973-1974年、1979-1980年),低油耗、高质量的日系汽车迅速抢占美国汽车市场,本田、丰田和日产于1990年共获得了18.03%的美国汽车销售市场份额,而与之相对的则是美国车企市场份额的迅速下降,福特、通用、克莱斯勒的市场份额之和从1965年的最高值90.60%下降至1990年的70.96%,失去了近20%的市场份额。
这对美国汽车制造业产生巨大冲击,并在相当程度上影响了美国整个国民经济的发展。
20世纪90年代,为提高美国汽车质量使之能与日系汽车抗衡,美国汽车行业开展了“2mm工程”。
日系汽车之所以能迅速获得美国汽车市场份额,除了其价格低、油耗低的特点之外,还有一个重要的原因就是质量高。
20世纪80年代末,日本依靠全面质量管理(TQC)使其品牌产品的车身制造综合偏差控制在2mm以内,为日本轿车产品全面占领欧美市场奠定了基础。
1991年,美国密西根大学(UniversityofMichigan)吴贤明教授提出了命名为“2mm工程”的计划构想,从系统的观点出发对汽车产品采用车身制造综合误差指数(continuousimprovementindicator),即“6σ”来控制车身制造质量,从而得以用最经济的制造成本提高汽车产品的整体质量。
当时,日本汽车白车身(即不包括附件及装饰件的未涂漆的车身)尺寸误差综合指数控制在2mm以内,欧洲汽车控制在2.5~3mm以内,而美国汽车仅某些车型控制在4mm以内,部分车型误差值高达5~6mm。
白车身通常是指尚未装配门盖和发动机罩的未涂装的车身基本骨架,轿车白车身通常由前围、后围、左右侧围、车顶、底板等几大部分组成,在轿车车身生产中,白车身的装配质量很大程度上影响到最终整车性能,车身的精度也直接影响到整车的外观、使用性能和其商品价值。
1美国汽车车身尺寸误差较大,直接影响了美国汽车的质量,降低了美国汽车的竞争力。
汽车白车身精度的控制涉及冲压工艺分析、冲模结构的构思、总成件检具的使用、焊接工艺分析、焊接夹具机构的构想、零部件公差的正确选取与合理分配等众多方面。
一般而言,典型的轿车车身由400多个零件,经过200多道装配工序,2500个工装定位点,由4000、6000个焊点焊装而成。
白车身产品结构和制造工艺都非常复杂,工艺质量控制十分困难。
车身尺寸控制的好坏不仅能反映在整车外观及装配性的优劣,影响到顾客对产品的评价及汽车产品的市场前景,而且车身尺寸偏差还与整车性能息息相关,影响到产品的密封、噪音、寿命、动力性等性能。
根据J.D.Power全世界汽车产品质量关键问题调查评估的报告显示:
有41%的汽车产品质量问题由车身制造尺寸偏差所造成。
因此,对车身制造尺寸偏差的研究及控制尤为重要。
为改变在质量上落后的局面,美国汽车行业在美国密歇根大学华裔教授吴贤名和倪军的倡导下,联合通用、克莱斯勒等车企以及美国商务部等政府部门,与美国密歇根大学等科学院所共同投资,开展了一项旨在提高车身制造质量的全面计划,目标是将美国汽车的白车身尺寸误差降低至日系车水平,这就是“2mm工程”(2mmProject)。
(3)CII指数法控制误差,“2mm工程”成效斐然
1992年,“2mm工程”正式启动。
吴贤名教授Michigan大学团队、通用、克莱斯勒、等八家供应商、两所大学(密大和韦恩州立大学)向美国国家标准局(NIST)提出成立“车体精密制造联盟”(AutoBodyConsortium)的提案,目标就是利用各个汽车装配厂测量机的海量数据,由大学团队下工厂,提供数据分析支持,与车厂和供应商人员组成多个混合团队,集思广议,挖质量问题根源,提出测试和落实解决质量改进方案。
这个提案在1992年得到批准,并得到三年(1992-1995)约一千四百万美元的资金。
“2mm工程”的核心目标是降低车身制造误差,控制车身制造质量,主要的测评方法是CII指数法。
CII指数(ContinuousImprovementIndex,持续改进指数)是Michigan大学吴贤名先进制造技术研究中心提出的质量评价指标,它的计算方法是:
在一定的时间段内,对车身全部测量点进行尺寸误差测量,计算6σ(均方差的六倍),并从小到大进行排序,取第95%测点的6σ值作为白车身的CII值。
例如,假设有一串共100个数字由小到大排序0.01、0.02、0.03……1.00,代表了车身上100个测量点的尺寸误差6σ值,第95%测点的6σ值为0.95,则0.95就是当次生产车身的CII值。
对尺寸误差大于该CII值的测量点所在区域,需要重点进行质量控制。
将车身精度控制在“2mm”,是指车身至少95%的测量点的尺寸误差6σ值小于2mm,不可将其简单理解为接缝的宽度小于2mm。
运用CII指数,可以直接寻找车身尺寸误差严重的区域并进行控制。
CII指数具有的重大创新意义,不仅在于提出了新的车身尺寸波动水平的度量指标,更在于通过锁定尺寸误差最大的5%的测点所在位置,可以明确需要重点质量控制的区域。
应用CII指数时,大体上需要经过如下几个步骤:
(1)测量车身各处误差,求出每个测点的6σ值并由大到小进行排序,取第95%的测点的6σ值,即为CII值;
(2)确定6σ值大于CII值的测点,并判断造成尺寸波动的区域和需要控制的对象;
(3)列出所有可能产生此问题的原因,根据数据分析和实际经验确定各原因的权重;
(4)针对问题提出改进措施,并争取获得其他部门支持;
(5)重复上述步骤,确定新的波动控制点,再进行改良。
如此不断改进,车身的整体尺寸质量就会达到很高的水平。
1992-1995年的“2mm工程”,在提高车身质量和创新运营模式两方面取得了优秀的成绩。
自1992年启动,历经3年努力的“2mm工程”很快显现出了效果,参与其中的两大主机厂(通用和克莱斯勒)将CII值成功地控制在了2mm以内,车身质量得到显著提高。
同时,一方面精度的提高减少了返修的发生,从而降低了生产成本;另一方面误差小了也就减少不必要的耗材,质量精度提高带来的技术性研发费用也可以通过量产来抵消,因而从这一方面来说也是对成本有很好的消减作用。
“2mm工程”的成功之处不仅在于提高了白车身的制造质量,而且在于形成了一种提高产业精度的可行运营模式。
在1995年,由于“2mm工程”的重大成功,及密大团队其它的项目业绩,美国国家标准局(NIST)批准并赞助了汽车机械加工精度有关的14个联盟项目,工作范围扩大至喷漆、焊接、轻金属加工、薄板冲压等领域,同时也和非汽车产业公司如波音、GE等进行合作。
若干制造业中心也用类似的运营模式,这些联盟一定程度上增强了汽车业的技术能力,改善了汽车工业的质量。
二、尺寸偏差源于多方面,工业机器人仅为因