VOC管理目标技术及其标准工艺规范说明与VOC来源分解Word文档格式.docx
《VOC管理目标技术及其标准工艺规范说明与VOC来源分解Word文档格式.docx》由会员分享,可在线阅读,更多相关《VOC管理目标技术及其标准工艺规范说明与VOC来源分解Word文档格式.docx(14页珍藏版)》请在冰豆网上搜索。
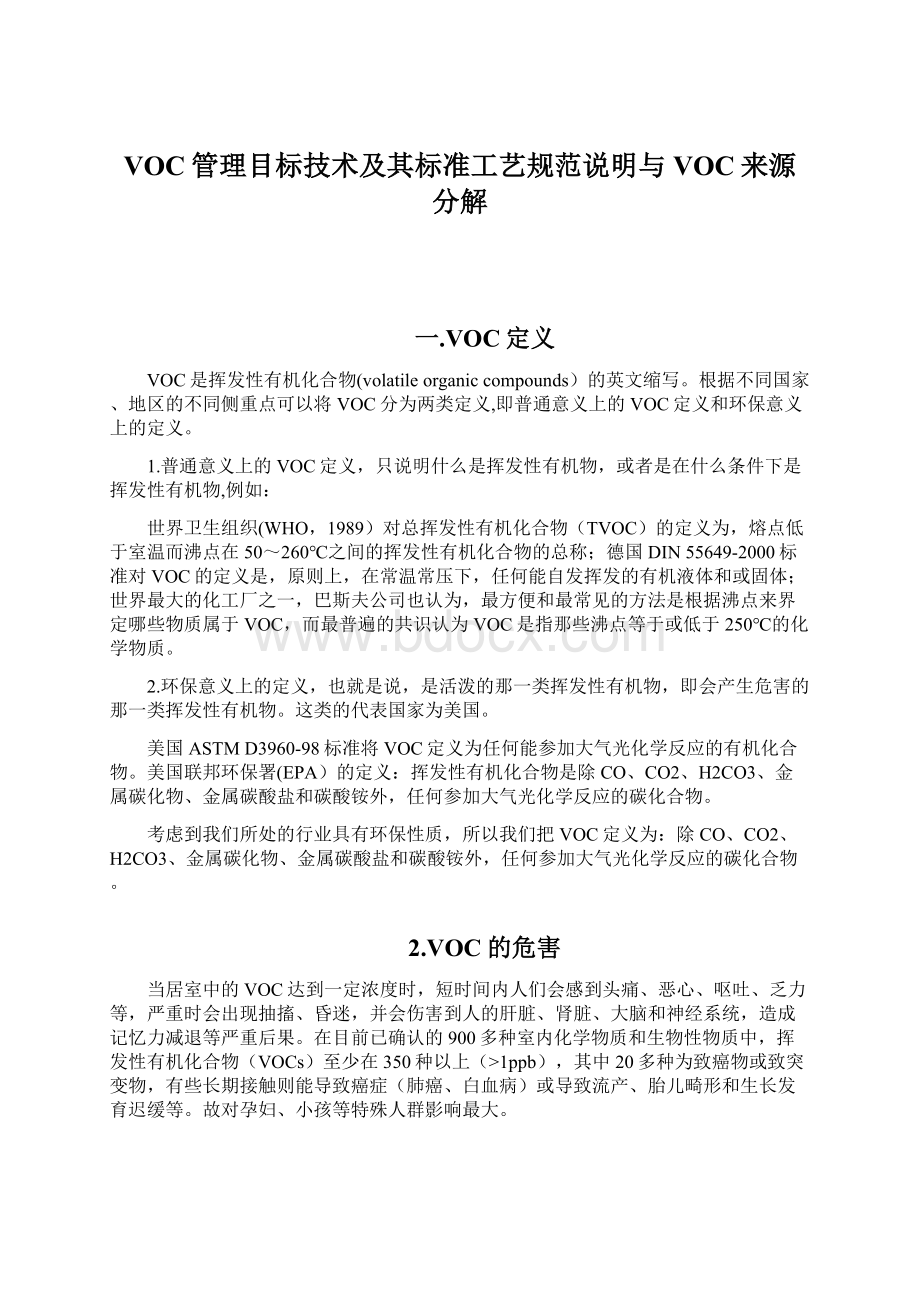
卤代烃类物质能引起神衰征候群及血小板减少、肝功能下降、肝脾肿大等病变,还可能导致癌症。
CFC类物质对大气臭氧层有破坏作用。
VOC中危害最大的两种化学成分就是苯和甲醛。
甲醛是一种无色,具强烈刺激性气味的气体,水溶液通称福尔马林。
室內燃料和不完全燃烧的烟叶、建筑材料、装饰用品、车内饰品及许多使用了有机涂料和材料的生活用品等均会散发甲醛。
甲醛对粘膜有强烈的刺激作用,特別对眼、鼻和呼吸道的刺激作用最强,是一种致癌物质,能引起皮肤过敏、还影响中枢神经系统,长时间吸入可引起胃癌。
3.VOC在各个行业的产生来源
涉及VOCs排放的行业主要为以下行业
1烟草行业:
油墨、有机溶剂;
2纺织品行业:
鞋类制品所用的胶水等;
3玩具行业:
涂改液、香味玩具等;
4家具装饰材料:
涂料、油漆、胶黏剂等;
5汽车配件材料:
胶水、油漆等;
6电子电气行业:
在较高温度下使用时会挥发出VOC、电子五金的清洁溶剂等;
7其他:
洗涤剂、清洁剂、衣物柔顺剂、化妆品、办公用品、壁纸及其他装饰品等。
3.1制鞋行业
(1)鞋面商标印刷,油墨挥发产生有机废气。
(2)鞋面材料高频压型工序产生的有机废气,皮革高频产生的废气属恶臭气体范畴。
(3)鞋底材料EVA、MD发泡过程,TPR、PVC注塑加热状态下产生的有机废气,该气体属高分子聚合物受热发生分子降解,释放出单体式低聚物。
(4)鞋底喷漆过程一般采用溶剂型油漆,该有机成分芬芳族树脂与苯溶剂的混合物,主要用于PVC、塑料、橡胶等材料的喷漆,子使用过程中苯溶剂全部挥发进大气。
(5)鞋底中底贴合,鞋面鞋底黏胶成型过程中使用的黏胶剂,最初粘胶剂所使用的溶剂是苯,溶解性极低,粘胶剂的性能也比较容易控制,但是苯的毒性相当大,后来采用甲苯做溶剂。
3.2人造板制造行业
(1)人造板制造业VOCs排放主要是在单板干燥过程及制(调)胶、涂胶、热压过程。
(2)刨花板制作工程中VOCs来源主要为涂料、热压和锯边过程中产生的甲醛。
3.3木制家具行业
(1)木制家具生产中有机废气主要来源于涂料中溶剂和辅料中有机成分的挥发,其中油漆喷涂是主要的污染环节。
(2)调漆和干燥过程中由于有机溶剂的挥发,也会有VOCs的排放。
产生的挥发性有机物主要为:
甲苯、二甲苯、甲醛、酚类、漆雾及其他的VOCs。
3.4印刷行业
由于印刷方式不同,VOCs的产生过程也不尽相同,下面分别介绍。
(1)平印:
平印主要选用轮转胶印油墨和平张纸胶印油墨。
轮转胶印油墨主要由于高沸点石油类溶剂挥发产生的VOCs。
平张纸胶印油墨几乎不产生VOCs。
(2)凹印:
主要选用出版凹印油墨和特殊凹印油墨前者主要以产生甲苯为主。
而特殊凹印油墨主要产生低沸点有机溶剂(甲苯、醋酸乙烯、IPA等)。
(3)柔印:
主要选用水性柔印油墨和溶剂型柔印油墨。
水性柔印油墨几乎不排出VOCs而溶剂型柔印油墨主要产生低沸点有机溶剂(醋酸乙烯、IPA等)。
(4)丝网印刷:
主要选用溶剂型丝印油墨,产生的废气主要为高沸点有机溶剂;
而RC型丝印油墨几乎不排出VOCs。
(5)其他类印刷方式几乎不排出VOCs。
3.5塑料包装印刷行业
(1)印刷、烘干以及包装印刷中的印后加工(复合)工序是产生VOCs的重要环节。
(2)塑料薄膜印刷后,使用粘合剂复合的过程中由于使用了稀释剂(常用乙酸乙酯)会在复合和烘干过程中有VOCs的排放。
具体工艺流程及排放情况见图3-1。
3-1塑料包装印刷工艺流程及VOCs排放图
3.6炼油与石油化工行业
(1)炼油行业
1)主要工艺:
炼油的主要生产工艺有常压蒸馏和减压蒸馏、催化裂解、催化重整、加氢裂化、延迟焦化、炼气厂加工。
2)排放控制措施:
①炼油生产工艺单元排放的有机工艺尾气的回收利用。
不能(或不能完全)回收利用的,应采用锅炉、加热炉、焚烧炉、火炬等方式燃烧处理或采用吸收、吸附、冷凝等物理的方法处理;
②定期对生产装置、设备、管道等进行检查维修,防止发生跑、冒、滴、漏。
③炼油企业生产的汽油,其储存于运输均应进行油气回收,并采取相应的处理措施。
储罐应设置为浮顶罐减少油气的排放。
汽油运输车辆应进行改装,满足油气回收的要求。
(2)石油化工行业
1)主要工艺
石油化工生产指对炼油过程提供的原料油和气(如乙烷、丙烷)进行裂解及后续化学加工,生产以三烯(乙烯、丙烯、丁二烯)、三苯(苯、甲苯、二甲苯)为代表的石化基本原料、各种有机化学品、合成树脂、合成橡胶、合成纤维等的生产过程。
石化生产过程是通过一系列的物理、化学变化完成的,生产原料和产品大多具有易燃易爆、毒害和腐蚀性,生产工艺操作复杂。
从工艺上看,石化生产具有高温、高压、深冷的特点;
从原材料上看,石化生产中使用的原材料(含半成品、成品)大多为挥发性有机物,易燃易爆,石油化工行业在挥发性有机物排放中的比例是比较高的。
从生产方式看,石化生产自动化程度高,具有密闭化、连续化的特点,这也是石化生产企业为确保安全生产的必要条件。
石化生产设备类型繁多有贮罐、计量槽、气瓶及精馏、吸收、萃取塔和反应釜、塔、器、裂解炉等静态设备,也有压缩机、风机、输送液体的泵等动态设备,管道纵横交错,加之介质具有腐蚀性,若设备老化、长久失修,则极易发生跑、冒、滴、漏。
因此,应定期对生产装置、设备进行检查维修,是减少挥发性有机物有的排放,杜绝事故隐患,确保安全生产的重要措施。
①炼油生产工艺单元排放的有机工艺尾气应回收利用。
②定期对生产装置、设备、管道等进行检查维修,防止发生跑、冒、滴、漏;
③炼油企业生产的汽油其储存与运输均应进行油气回收,并采取相应的处理措施。
储罐应设置为浮顶罐,减少油气排放。
3.7汽车制造涂装和汽车维修行业
有机气态污染物主要产生于:
电泳底漆、中涂和面漆的喷涂及烘干过程和塑料件加工的涂漆工序。
在中涂和面漆喷漆过程中,大约80-90%的VOCs是在喷漆室和流平室排放,20-10%的VOCs随车身涂膜在烘干室中排放。
涂装废气的特点是:
大风量,中低浓度。
(1)底涂:
轿车基本采用电泳漆涂装。
目前90%以上车身防护都是采用阴极电泳涂装底漆工艺,并为适应环保、节能的要求,开发出了无铅、锡的阴极电泳材料,VOCs含量低和低温固化型阴极电泳材料。
该部分VOCs产量相对较少。
(2)中涂和面涂喷漆:
喷涂是产生VOCs的最主要环节,也是当前VOCs治理的薄弱环节,应重点控制。
(3)烘干和喷防护蜡的过程也会有相应的有机废气排放。
具体排放图见图3-2。
图3-2汽车行业工艺流程及VOCs排放图
3.8电子行业
(1)电子元件主要的挥发性有机污染物排放来自于电子元件生产过程中清洗零部件或材料使用的一些甲苯、二甲苯等挥发性有机物的溶剂。
(2)线路板生产过程有机废气主要来源于大量使用的油墨及稀释、清洁用挥发性有机物,其主要成分是苯、甲苯、二甲苯。
(3)电真空器件(CRT)生产的挥发性有机物主要来自屏玻璃有机膜涂层中甲苯及其他挥发性有机物的排放。
(4)TFT-LCD生产过程中要使用多种化学试剂和有机溶剂。
TFT-LCD生产排放的废气分为酸性气体、碱性气体、有机废气和有毒气体四种类型。
主要产生于基板清洗、化学气相沉积(CVD)、光刻涂胶、刻蚀、剥离、去胶、涂取向膜等主要工艺过程。
(5)电子终端产品装配中挥发性有机物主要来源为清洗有机废气及产品喷漆生产过程中产生的漆雾和挥发性有机物。
3.9半导体行业
(1)半导体制造工艺:
半导体行业废气排放具有排气量大、排放浓度小的特点。
挥发性有机废气主要来源于光刻、显影、刻蚀及扩散等工序,在这些工序中要用有机溶液(如异丙醇)对晶片表面进行清洗,其挥发产生的废气是有机废气的来源之一;
同时,在光刻、刻蚀等过程中使用的光阻剂(光刻胶)中含有易挥发的有机溶剂,如醋酸丁酯等,在晶片处理过程中也要挥发到大气中,是有机废气产生的又一来源。
(2)半导体封装工艺:
与半导体制造工艺相比,半导体封装工艺产生的有机废气较为简单,主要为晶粒粘贴、封胶后烘烤过程产生的烘烤废气。
3.10干洗行业
根据干洗机的结构,可分为开启式干洗机和全封闭干洗机。
开式四氯乙烯干洗机系指采用水冷回收系统,衣物在干洗过程中产生的气态四氯乙烯不能完全回收,在烘干结束时需要把废气排出机外。
全封闭式四氯乙烯干洗机采用制冷回收系统,不向大气环境排放含有四氯乙烯的废气,或者说排放量很少,因而溶剂消耗量低,一般为1%左右。
具体的产污环节主要为以下三个方面。
(1)干洗机在干洗过程中的泄漏引起污染。
溶剂泄漏:
包括:
油缸、外笼、金属过滤器、水分离器、尼龙过滤器,蒸馏冷凝器等各干洗机容腔的泄漏;
干洗剂输送管道、阀门的泄漏,溶剂泵的泄漏,洗笼主轴轴封的泄漏等。
气体泄漏:
干洗机在烘干衣物时,风道各密封的泄漏,平衡管路的泄漏,各腔体密封,风道口盖的泄漏等引起烘干过程含氯气体外溢污染环境。
残存泄漏:
在干洗过程中,残留在干洗机各容腔内、洗衣笼、风道、过滤器中的四氯乙烯,以及蒸馏器、水分器内绒毛、残渣等带有的四氯乙烯没能回收可能带出机外、或开启机门,各口盖形成气体溢出产生污染。
(2)残存气体污染:
干洗机在烘干衣物时在笼内和风道中的气流含有大量四氯乙烯,在干衣过程中没能完全把气流中的四氯乙烯回收,在干衣结束后,机内气体含有四氯乙烯,当开门取衣时会溢出机外产生污染。
(3)残渣污染:
在干洗过程和溶剂再生过程,溶剂过滤过程中,衣物带来的绒毛、杂质等会形成干洗残渣,这些残渣在排除机外时造成污染,如蒸馏残渣清理过滤器时,过滤内部粘附绒毛等残渣,在绒毛过滤器,纽扣捕集器中滤留的绒毛,干燥冷凝器干燥加热器翅片上的绒毛等等。
3.11橡胶制品行业
橡胶制品工业生产废气主要产生于下列工艺过程或生产装置:
炼胶过程中产生的有机废气;
纤维织物浸胶、烘干过程中的有机废气;
压延过程中产生的有机废气;
硫化工序中产生的有机废气;
树脂、溶剂及其它挥发性有机物在配料、存放时产生的有机废气。
具体来源主要有以下三个方面。
(1)残存有机单体的释放。
生胶如天然、丁苯、顺丁、丁基、乙丙、氯丁橡胶等,其单体具有较大毒性,在高温热氧化、高温塑炼、燃烧条件下,这些生胶解离出微量的单体和有害分解物,主要是烷烃和烯烃衍生物。
橡胶制品工业生产废气中可能含残存单体包括丁二烯、戊二烯、氯丁二烯、丙烯腈、苯乙烯、二异氰酸钾苯脂、丙烯酸甲酯、甲基丙烯酸甲酯、丙烯酸、氯乙烯、煤焦沥青等。
(2)有机溶剂的挥发。
橡胶行业普遍使用汽油等作为有机稀释剂,可能使用的有机溶剂包括甲苯、二甲苯丙酮、环己酮、松节油、四氢呋喃、环己醇、乙二醇醚、乙酸乙酯、乙酸丁酯、乙酸戊酯二氯乙烷、三氯甲烷、三氯乙烯、二甲基甲酰胺等。
(3)热反应生成物。
橡胶制品生产过程高温条件下进行,易引起各种化学物质之间的热反应,形成新的化合物。
3.12涂料行业
涂料行业主要分为:
油性涂料、粉末涂料、腻子、水性涂料、UV光固化涂料和建筑涂料。
不同的涂料生产流程和工艺手段均不相同。
但是根据各产品的生产工艺描述,易产生VOCs污染的主要为油性涂料。
为减少VOCs的排放,对油性涂料的生产进行控制,主要包括以下三点:
(1)油性涂料生产设备生产结束使用的清洗溶剂应进行回收;
(2)车间的生产废气必须通过集气罩收集,处理后高空排放;
(3)有机溶剂、各种助剂的废包装桶、活性炭吸附设备产生废活性炭等,收集后委托有资质的相关单位处理。
各类滤渣分类收集后能回用的尽量回用,不能回用的委托有资质单位处理。
四.VOC的处理技术及各技术的简要说明
VOC的回收技术主要有冷凝法、吸附法、吸收法和膜分离法;
吸附法、吸收法和膜分离法是通过采用选择性吸附剂和吸收剂、选择性膜渗透来分离回收废气中的有机溶剂。
处理技术主要有催化燃烧、直接燃烧等,它是通过化学反应,将气体中的有机物转变为CO2和水。
4.1回收技术
4.1.1
冷凝法
冷凝法是最简单的回收方法,它是将废气冷却到低于有机物的露点温度,使有机物冷凝成液滴而从气体中分离出来。
通常使用的冷却介质主要有冷水、冷冻盐水和液氨。
通常该技术仅用于VOC
含量高(百分之几)、气体量较小的有机废气的回收处理。
其回收率与有机物的沸点有关,沸点较高时,回收率高;
沸点较低时,回收效果不好。
由于大部分VOC系易燃、易爆气体,受到爆炸极限的限制,气体中的VOC含量不会太高,所以,要达到较高的回收率,需采用较很低温度的冷凝介质或采用高压措施,这些都势必会增加设备投资和提高处理成本,而且在通常的操作条件下,由于相平衡的制约,有机物蒸汽压较高,故离开冷凝器的排气中的VOC含量仍不能达到排放标准,因此,该技术一般是作为一级处理技术并与其它技术结合使用。
4.1.2
吸附法
吸附法早已用于VOC的回收处理,尤其是活性炭吸附法已经广泛应用于苯系物、卤代烃的吸附处理。
吸附法去除VOC的原理是利用比表面积非常大的粒状活性炭、炭纤维、沸石等吸附剂的多孔结构,将VOC分子截留。
当废气通过吸附床时,VOC就被吸附在孔内,使气体得到净化。
吸附法又分为固定床吸附法、流动床吸附法和浓缩轮吸附法。
①固定床吸附法
固定床吸附法的特点是吸附与脱附在同一个床层上实现,为了保证吸附过程的连续性,需要2台或2台以上的吸附器同时工作,其中一些吸附器进行吸附时,另一些进行再生。
活性炭是应用最为广泛的固定床吸附剂,由于其容易吸附水,所以不适用于温度高于40℃、气体相对湿度超过50%的气体的吸附处理此外也不适用于易发生反应、活性大的溶剂的吸附,该类有机物会与活性炭或在活性炭表面进行反应而堵塞碳孔,这种情况可采用炭纤维或沸石作为吸附剂。
活性炭纤维是以有机化合物纤维(如聚丙烯、酚醛树脂、聚乙烯醇等)为基本原料经特殊加工制成的。
它是一种很细的纤维状物质,具有巨大的比表面积、外表面积和非常发达的微孔结构,纤维上有很多微孔可以直接与有机物接触而不是象颗粒活性炭那样要先通过大孔、过渡孔,才能到达微孔,因此,活性炭纤维更易于吸附低浓度的VOC。
与颗粒活性炭相比,其吸附有机物的能力高出1.5~2.0倍,吸附速度也快3倍左右。
由于活性炭纤维的吸附能力强,故吸附装置可以小型化,吸附剂的用量也可以少些,降低处理费用。
②流动床吸附法
流动床吸附系统由吸附单元和脱附单元组成。
废气由吸附床底部进入,自下而上地流动,使吸附剂流态化,VOC与吸附剂接触后被吸附,净化后的废气由顶部排出,吸附了VOC的吸附剂由底部排出,进入脱附单元。
在脱附单元内,加热吸附剂,使有机物脱附出来,将气体引入冷凝单元去回收有机溶剂。
再生后的吸附剂送回吸附单元顶部继续进行吸附操作。
③浓缩轮法
浓缩轮是一个装满吸附剂的旋转轮。
废气由旋转轮的上游侧进入浓缩轮的吸附区,其中被吸附净化后的废气由旋转轮的下游排出;
同时另一股流量较小的、温度较高的脱附气朝废气气流相反的方向进入浓缩轮的脱附区,将已吸附的VOC脱附出来。
浓缩轮以一定速度缓慢旋转,这样在一个系统内就可以完成吸附和脱附操作,使VOC得到浓缩,大大降低了设备投资。
4.1.3吸收法
吸收技术是一种成熟的化工单元操作过程,适合于大气量、中等浓度的含VOC废气的处理。
吸收技术是利用液体吸收剂与废气直接接触而将VOC转移到吸收剂中。
吸收按其机理可分为物理吸收和化学吸收,通常VOC的吸收为物理吸收,使用的吸收剂常为柴油、煤油、水和其它溶剂。
任何可溶解于吸收剂的有机物均可以从气相转移到液相中,然后,对吸收液进行处理。
当吸收液为水时,采用精馏处理就可以回收有机溶剂;
当为非水溶剂时,考虑到回收成本,需进行吸收剂的再生。
4.1.4膜分离
膜分离技术是采用对有机物具有选择性渗透的高分子膜,在一定压力下使VOC渗透而达到分离的目的。
当VOC气体进入膜分离系统后,膜选择性地让VOC气体通过而被富集,脱除了VOC的气体留在未渗透侧,可以达标排放富集了VOC的气体可去冷凝回收系统进行有机溶剂的回收。
选择此种方法可以分离90%的VOC。
膜分离法适用于中高浓度(VOC含量高于1×
10-3)的废气的处理。
膜系统的费用与进口气体流速成正比,与VOC的浓度关系不大。
此法最好用于高浓度、小流量和有较高回收价值的有机溶剂的回收,但其设备投资较高。
随着对环境问题的越来越重视,膜分离技术的应用前景会很广阔,这是因为膜法是一种清洁技术,从膜分离系统出来的是回收的有机溶剂和净化了的排放气,减少了二次污染的产生。
随着高效分离膜的开发和价格的降低,膜技术的应用会越来越广。
4.2综合应用技术
4.2.1蓄热式热氧化处置装置(RTO)
RTO,是一种高效有机废气治理设备。
与传统的催化燃烧、直燃式热氧化炉(TO)相比,具有热效率高(≥95%)、运行成本低、能处理大风量低浓度废气等特点,浓度稍高时,还可进行二次余热回收,大大降低生产运营成本。
第一代RTO是单体式结构,以最简单的一进一出为风流导向。
第二代RTO是采用阀门切换式,也是最常见的一种RTO。
其由两个或多个陶瓷填充床,通过阀门的切换,改变气流的方向,从而达到预热VOC废气的目的。
第三代RTO采用旋转式分流导向,并把炉膛内蓄热体分成多个等份的单体密封单元,通过不停转动把VOC导向至各个蓄热体单元进行氧化。
第四代RTO是最新的治理供热一体化设备,简称BHI(BurningHeatingIntegrated),采用旋转式阀门分流,把多个蓄热式紧凑结合为一个燃烧室,内置换热器或热风调节装置,达到治理废气的同时满足供热需求。
1.1基本原理
其原理是把有机废气加热到760摄氏度以上,使废气中的VOC在氧化分解成二氧化碳和水。
氧化产生的高温气体流经特制的陶瓷蓄热体,使陶瓷体升温而“蓄热”,此“蓄热”用于预热后续进入的有机废气。
从而节省废气升温的燃料消耗。
陶瓷蓄热体应分成两个(含两个)以上的区或室,每个蓄热室依次经历蓄热-放热-清扫等程序,周而复始,连续工作。
蓄热室“放热”后应立即引入适量洁净空气对该蓄热室进行清扫(以保证VOC去除率在95%以上),只有待清扫完成后才能进入“蓄热”程序。
三床式RTO的工作示意图
1.2工艺分类
RTO目前有两床式、三床式和旋转式等多种形式。
因为如果采用两床RTO,在蓄热床换向时,会出现污染物未经有效处理直接排放的现象。
因此建议至少有三个蓄热床,其中一个用于预热进气,另一个用于蓄热降温排气,还有一个用于吹扫循环,吹扫循环可避免蓄热床换向时产生冲击排放。
1.3适用范围
原则上适用于24小时连续运转的生产企业,进口浓度在1.5g/m3以上。
如果非24小时连续运转,需要考虑在非运转期的保温措施,否则会带来较高的运行成本。
1.4工艺优点
(1)几乎可以处理所有含有机化合物的废气;
(2)可以处理风量大、浓度低的有机废气;
(3)处理有机废气流量的弹性很大(名义流量20%~120%);
(4)可以适应有机废气中VOC的组成和浓度的变化、波动;
(5)对废气中夹带少量灰尘、固体颗粒不敏感;
(6)在所有热力燃烧净化法中热效率最高(>
95%);
(7)在合适的废气浓度条件下无需添加辅助燃料而实现自供热操作;
(8)净化效率高(三室>
99%);
(9)维护工作量少、操作安全可靠;
(10)有机沉淀物可周期性的清除,蓄热体可更换;
(11)整个装置的压力损失较小;
(12)装置使用寿命长;
1.5工艺缺点:
(1)装置重量大,因为采用陶瓷蓄热体
(2)装置体积大,只能放在室外
(3)要求尽可能连续操作
(4)一次性投资费用相对较高
(5)不能彻底净化处理含硫含氮含卤素的有机物、
4.2.2固定床吸附脱附-催化氧化处置装置
吸附催化燃烧净化是利用工业废气中污染物可以燃烧的特性,将污染物中含碳氢的化合物,经活性炭吸附浓缩后,在催化剂和较低温度(250~450℃)下进行氧化分解,使其转化为二氧化碳与水蒸汽;
或者将分子结构中含有卤素及其他元素的有机物转化成卤化氢、二氧化硫、二氧化氮或其它金属氧化物,再经过吸收等净化措施,将有害气体彻底转化为无害气体的一种净化方法
2.1基本原理
沸石转轮浓缩-催化氧化装置,包括了沸石转轮浓缩装置和催化氧化装置。
在沸石转轮浓缩装置中,VOCs气体进入吸附区被吸附,成为净化气体排放。
当吸附区接近饱和时,旋转至脱附再生区释放VOCs浓缩气体,并送至催化氧化炉燃烧分解。
经脱附再生处理后的转轮再旋转至冷却区降温后,继续进行吸附处理。
典型的工艺流程如下图7.3所示。
沸石转轮-催化氧化装置流程示意图
2.2应用要点
转轮吸附区的设计面风速不应小于3m/s,转轮厚度不宜小于400mm。
蓄热燃烧装置应设置保温,保证炉体外表面温度须小于60℃。
如果进口VOCs浓度高于1.5g/m3,则需要考虑后续处理技术,以确保达标。
2.3净化工艺特点
与普通的吸附