现代模具的先进制造方法综述Word下载.docx
《现代模具的先进制造方法综述Word下载.docx》由会员分享,可在线阅读,更多相关《现代模具的先进制造方法综述Word下载.docx(19页珍藏版)》请在冰豆网上搜索。
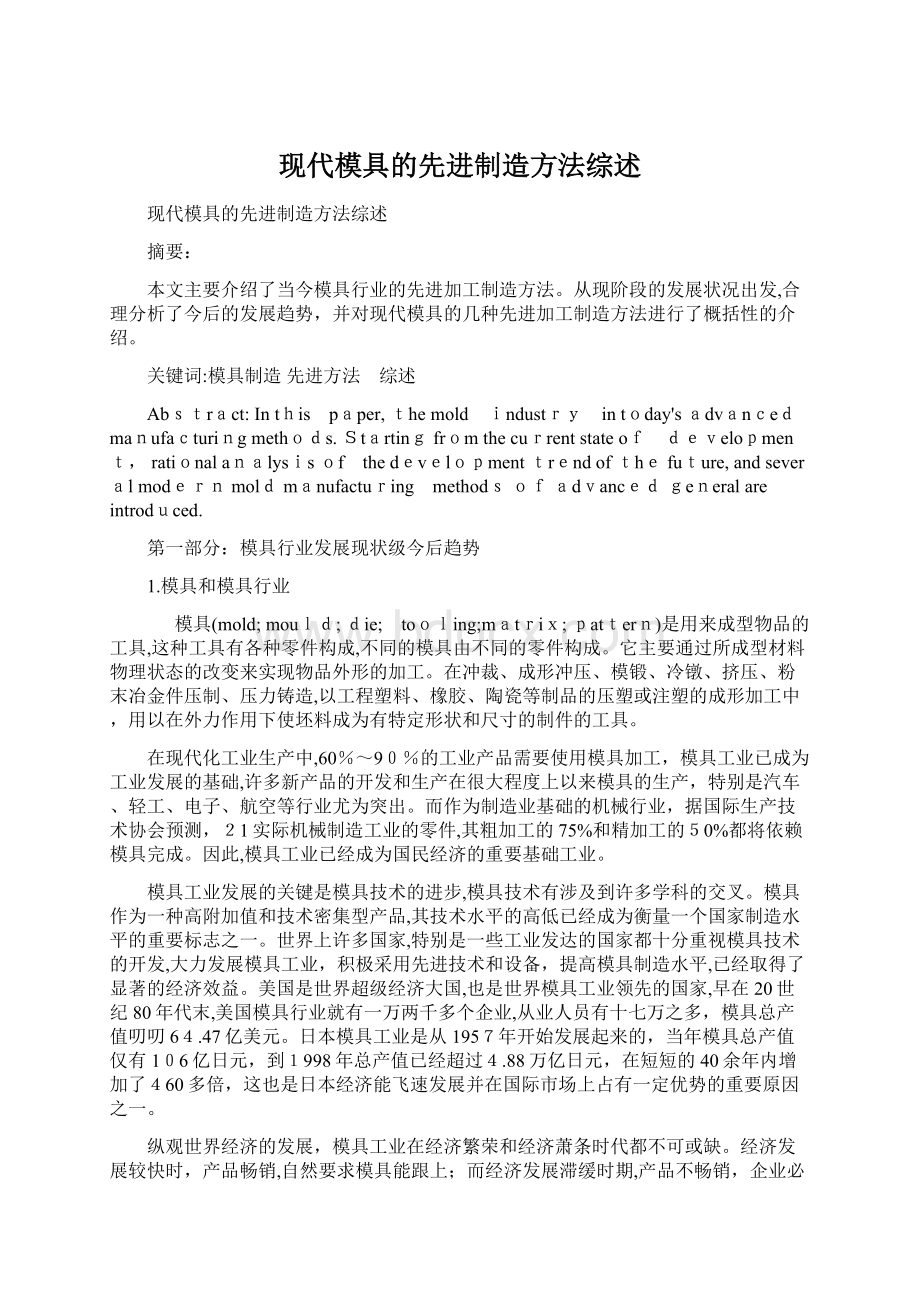
世界上许多国家,特别是一些工业发达的国家都十分重视模具技术的开发,大力发展模具工业,积极采用先进技术和设备,提高模具制造水平,已经取得了显著的经济效益。
美国是世界超级经济大国,也是世界模具工业领先的国家,早在20世纪80年代末,美国模具行业就有一万两千多个企业,从业人员有十七万之多,模具总产值叨叨64.47亿美元。
日本模具工业是从1957年开始发展起来的,当年模具总产值仅有106亿日元,到1998年总产值已经超过4.88万亿日元,在短短的40余年内增加了460多倍,这也是日本经济能飞速发展并在国际市场上占有一定优势的重要原因之一。
纵观世界经济的发展,模具工业在经济繁荣和经济萧条时代都不可或缺。
经济发展较快时,产品畅销,自然要求模具能跟上;
而经济发展滞缓时期,产品不畅销,企业必然千方百计开发新产品,这同样会给模具带来强劲的需求。
因此,模具行业是一个经久不衰的工业。
2、我国模具技术的现状及发展趋势
我国模具工业起步晚,底子薄,与工业发达国家相比有很大差距,但在国家产业政策和与之配套的一系列国家经济政策的支持和引导下,我国模具工业发展迅速。
据统计,我国现有模具生产厂家近两万家,从业人员有50万人。
但总体上看,自产自用占主导地位,商品化模具近卫1/3左右,国内模具生产仍供不应求,特别是精密、大型、复杂、长寿命模具,仍主要依赖进口。
目前,就整个模具市场来看,进口模具约占总量的20%左右,其中,中高档模具进口比例达到40%以上,因此我国模具产业任重而道远。
可喜的是近年来我国的模具技术和水平也取得了长足的进步主要表现在一下方面:
1)研究开发模具新钢种及硬质合金、钢结硬质合金等新材料,一些新的热处理工艺,延
长了模具的使用寿命。
2)开发了一些多工位级进模和硬质合金模等新产品,并根据国内生产需要研制了一批精密塑料注射模。
3)研究开发一些模具加工新技术和新工艺,如三维曲面数控、仿形加工;
模具钢的超塑
性成形技术和各种快速制模技术等。
4)模具加工设备已得到较大发展,国内已能批量生产精密坐标磨床、计算机数字控制
(CNC)铣床、CNC电火花线切割机床和高精度电火花成形机床等。
5)模具计算机辅助设计和制造已在国内开发和应用。
我国的模具技术虽然得到了较大的发展,但仍然还需花费大量资金向国外进口模具,其原因是:
1)专业化生产和标准化程度低。
2)模具品种少,生产效率低、经济效益较差。
3)模具生产制造周期长、精度不高,制造技术落后。
4)模具寿命短,新材料使用量少。
5)模具生产力量分散、管理落后。
根据我国模具技术发展的现状及存在问题,今后的发展方向为:
1)开发和发展精密、复杂、大型、长寿命的模具,以满足国内、外市场的需要。
2)加速模具的标准化和商品化,以提高模具质量,缩短模具生产周期。
3)大力开发和推广应用模具CAD/CAM 技术,提高模具制造过程的自动化程度。
4)积极开发模具新品种、新工艺、新技术和新材料。
5)发展模具加工成套设备,以满足高速发展模具工业的需要。
第二部分:
模具制造的基本要求和特点
1、模具制造的要求
(1)制造精度高为了生产合格的产品和发挥模具的效能,设计、制造的模具必须具有
较高的精度。
模具的精度主要是由模具零件精度和模具结构的要求来决定的。
为了保证制品精度,模具工作部分的精度通常要比制品精度高2—4级;
模具结构对上、下模之间的配合有较高要求,因此组成模具的零件都必须有足够的制造精度。
(2)使用寿命长
(3)制造周期短 模具制造周期的长短主要取决于制模技术和生产管理水平的高低。
为
了满足生产需要,提高产品竞争能力,必须在保证质量的前提下尽量缩短模具制造周期。
(4)模具成本低模具成本与模具结构的复杂程度、模具材料、制造精度要求及加工方
法等有关,必须根据制品要求合理设计模具和制订其加工工艺。
2、模具制造的特点
模具制造属于机械制造范畴,但与一般机械制造相比,它具有许多特点:
(1)单件生产用模具成型制品时,每种模具一般只生产 1—2副,所以模具制造属于单
件生产。
每制造一副模具,都必须从设计开始,制造周期比较长。
(2)制造质量要求高
(3)形状复杂模具的工作部分一般都是二维或三维复杂曲面,而不是一般机械的简单
几何体。
(4)材料硬度高模具实际上相当于一种机械加工工具,硬度要求高,一般用淬火工具
钢或硬质合金等材料,采用传统的机械加工方法制造有时十分困难。
第三部分:
模具先进制造技术
1.先进制造技术的范畴:
一般认为先进制造技术有以下四部分组成,但它是动态的,变化的。
1.现代设计技术
合理的设计是决定产品品质、环境相容性、经济性和满足需求的基础,设计的水平、质量和效率是决定产品开发能力和市场竞争能力的重要环节。
在新的技术环境下,现代设计技术以计算机辅助工具和包含丰富的数据库、知识库支撑体系的智能技术为基础,将设计、制造和生产过程有机结合在一起,形成一些新的理论和方法。
主要包括:
计算机辅助设计(CAD)、计算机辅助工程(CAE)、反求工程技术(RE)、并行工程(CE)、协同设计技术(CSCW)、稳健设计技术(RobustDesign)与质量功能配置、再生工程、绿色产品设计等。
2.先进制造工艺技术
先进制造工艺是先进制造系统的基础,是实现优质、高效、低耗、清洁生产和保证产品质量与市场竞争力的前提。
例如金属超塑性的发现、金属紧密铸锻冲压工艺的进步已经可以实现不经切削加工或极少加工余量即可成形,使得成型制造技术正在从制造工件毛坯或接近零件形状向直接制成工件或净成形的方向发展;
用于汽车、飞机、精密机械的精密加工精度已达(um)级,用于磁盘、磁鼓制造的精密加工精度已达到亚微米级(0.01um),用于超精密电子器件的精密加工精度已经达到毫微米级(0.001um),而超精密加工的精度也已经达到纳米级(0.1-100nm)级的阶段,这些都是实现高效清洁生产的关键技术。
计算机辅助制造(CAM)、少无切削制造技术、精密加工和超精密加工技术、非机械加工制造技术、快速原型制造(RPM)、仿生制造、虚拟制造技术(VMT)等。
3.综合自动化技术
综合自动化技术事实上是一个包含计算机技术、网络技术、自动化技术的运作系统,通过现代系统管理思想贯穿在一起,以实现从信息、功能、过程直至企业的集成和优化技术的物化环节,能过将制造企业的人、技术、管理和资源以及物流、信息流、、与价值流有机结合在一起。
主要包括:
分布式数控技术(DNC)、柔性制造技术(FMT)、集成制造技术(CIMT)、智能制造技术(IMT)。
4.现代系统管理技术
现代系统管理技术是一项富有哲学意味的系统理论和方法,它在信息集成、功能集成、过程集成和企业集成的基础上,着重讨论如何最大限度的发挥已有技术、设备、资源和人员的作用和最大限度的提高企业经济效益和竞争能力的组织与经营管理策略。
制造资源计划(MRPII)、准时制造(JIT)和精益生产(LP)、敏捷制造(AM)、全球化制造(GM)和星系管理系统(IMS)、可持续发展战略及相关技术等。
2.传统加工与特种加工的比较
1.传统的模具加工制造方法,也就是机械加工,即用传统的切削与磨削加工与现代数控机床加工,机械加工也常作为零件粗加工和半精加工的主要方法。
机械加工的主要特点是加工精度高、生产效率高,而且用相同的设备和工具可以加工出各种形状和尺寸的工件。
但是,用机械加工方法加工形状复杂的工件时,其加工速度很慢,高硬度材料难以加工。
2.特种加工特种加工是有别于传统机械加工的加工方法,例如电加工。
从广义上讲,
特种加工是指那些不需要用比工件更硬的工具,也不需要在加工过程中施加明显的机械力,
而是直接利用电能、声能、光能、化学能等来除去工件上的多余部分,以达到一定形状、尺寸和表面粗糙度要求的加工方法。
3.几种先进制造技术方法:
1.高速切削技术
它是一项高新技术,以高效率、高精度和高表面质量为基本特征,在模具制造行业中获得了愈来愈广泛的应用,并已取得了重大的技术经济效益,是当代先进制造技术的重要组成部分。
1.1 高速刀具技术模具制造业中将普遍应用高速(超高速)干式切削技术。
超硬刀具材料的应用、复合(组合)式各类高速切削刀具(工具)的结构设计与制造技术,是刀具(工具)品种发展的主导技术。
其中无屑加工工艺的搓、挤滚压成形类刀具(工具)应用会更加广泛;
超硬刀具材料将在各类刀具的涂层材料、SiN 陶瓷及Ti基陶瓷领域发展更快、应用更加广泛。
1.2 高速机床技术我国高速机床技术重点:
一是研发机床关键功能部件,如转速20000r.P.m以上的大功率高刚度主轴、无刷环形扭矩电机、直线电机、快速响应数控系统等;
二是多功能复合机床设计、制造网络、通讯网络技术的应用等。
随着数控系统,关键功能部件、网络通讯技术的进步与完善,将促使多轴联动、多面高速加工中心,铣、车功能为一体的复合加工中心技术达到实用化;
相应出现各类数控专用高效率加工机床;
将激光技术更加广泛应用于机械成形加工、切割加工领域;
机床数控系统的功能将可实施网络化通讯与生产,
进一步提升数控机床的利用率。
1.3零件毛坯制造技术快速成形技术的实用化,将进一步提升目前的精铸、精锻及其它成形制造技术,使其几何尺寸精度能满足少无切屑加工的要求,其材料的选择将适应绿色制造工程的技术要求,零件材料的可加工性能将适应高速切削技术要求。
1.4其它技术自动生产线技术:
将以各类高速加工中心组成,大力发展柔性、敏捷制造工程技术;
测量技术:
随着高速加工系统工程技术广泛应用,数字化CCD、激光图形处理测量技术和随机在线高速测量技术将广泛应用于柔性数控生产线及数控专用高效率加工机床上;
网络技术:
将在不断进步的计算机技术支持下,大力发展宽带网及网络安全技术。
2.特种加工技术
面向快速制造的特种加工技术是在传统的特种加工技术与材料技术、控制技术、微电子技术和计算机技术紧密结合的基础上,随着快速响应市场需求而逐步发展起来的。
2.1 分层制造技术为有效地简化问题的复杂性,将采用类似快速成形的分层制造加工模式,并严格控制每一层的加工余量,确保工具只有底面实现加工,而侧面不参与加工,从而使复杂的模具三维型面加工问题转化为一系列平面加工问题。
2.2基于电场控制、溶解与切削相结合的复合加工技术以钝性工作液为纽带,结合电场控制策略,探索这些工艺的复合方法,以充分发挥其各自的长处,可发展出复杂曲面形状和光整一体化加工技术。
具体包括电化学机械复合加工技术,化学机械加工技术,超声放电复合/jn-r-技术,时变场控制、磁场辅助的电化学及电化学机械复合加工技术,时变场控制的电解在线修整砂轮磨削加工技术,时变场控制电化学及磁粒研磨的复合加工技术等。
电化学加工
2.3三维型腔的精密成形及镜面电火花加工一体化技术通过采用在普通煤油工作液中添加固体微细粉末的方法,来增大精加工的极间距离、减小电容效应、增大放电通道的分散性。
从而可使该工艺排屑好、放电稳定、加工效率提高,并有效降低加工表面的粗糙度。
同时,混粉工作液的使用还可在模具工件表面形成硬度较高的镀层,提高模具型腔表面的硬度和耐磨性,实现模具三维型腔的精密成形及镜面电火花加工一体化。
2.4 面向RP技术的特种加工工艺组合技术
2.4.1直接利用RP工艺,结合相应的后处理工艺或快速精密铸造工艺制造模具的方法,利用金属粉末烧结(SLS)制成的原型件,直接进行金属熔渗处理,形成金属模具零件。
利用SLA、FDM或LOM方法,直接制造树脂、ABS塑料模具零件。
用SLS方法直接制造铸造用的消失蜡模,实现零件的快速精密铸造。
2.4.2基于RP原型件,结合相应的特种加工工艺,间接制造模具的方法。
基于RP原型,与电铸工艺、金属喷涂、陶瓷涂覆工艺相结合,快速制造金属或陶瓷模具的工艺技术;
浇注硅橡胶、环氧树脂或聚氨脂等软材料,直接制造软模具。
2.4·
3 基于RP原型,结合相应的特种加工工艺,快速制造电加工的电极,实现复杂模具零件的快速电火花成形加工。
在原型或原型制作的母模上刷涂导电层,再电铸或电镀形成金属电极。
直接在原型上进行金属冷喷涂形成金属电极。
利用原型制造母模,充实粉末,再压实烧结形成电极。
在原型制作的母模内充人石墨粉与粘接剂的混合物,固化形成石墨电极。
在原型制作的母模内充入环氧树脂与碳化硅粉的混合物,首先形成研磨模,再在专用振动研磨机上研磨出石墨电极。
3.虚拟现实技术
3.1虚拟技术的重要技术特征虚拟现实是利用计算机生成一种模拟环境(如飞机驾驶舱、操作现场等),通过多种传感设备使用户“投入”到该环境中,实现用户与该环境直接进行自然交互的技术。
因此,具有以下四个重要特征:
多感知性、存在感、交互性、自主性。
3.2虚拟现实系统的构成主要由以下模块构成:
检测模块:
检测用户的操作命令,并通过传感器模块作用于虚拟环境。
反馈模块:
接受来自传感器模块信息,为用户提供实时反馈。
传感器模块:
一方面接受来自用户的操作命令,并将其作用于虚拟环境;
另一方面将操作后产生的结果以各种反馈的形式提供给用户。
控制模块:
对传感器进行控制,使其对用户、虚拟环境和现实世界产生作用。
建模模块:
获取现实世界组成部分的三维表示,并由此构成对应的虚拟环境。
3.3虚拟现实系统的关键技术
3.3.1 动态环境建模技术虚拟环境的建立是虚拟现实技术的核心内容。
动态环境建模技术的目的是获取实际环境的三维数据,并根据应用的需要,利用获取的三维数据建立相应的虚拟环境模型。
三维数据的获取可以采用CAD技术(有规则的环境),而更多的环境则需要采用非接触式的视觉建模技术,两者的有机结合可以有效地提高数据获取的效率。
3.3.2 实时三维图形生成技术三维图形的生成技术关键是如何实现“实时”生成。
为了达到实时的目的,至少要保证图形的刷新率不低于15桢/秒,最好是高于30桢/秒。
在不降低图形的质量和复杂度的前提下,如何提高刷新频率将是该技术的研究内容。
3·
3·
3立体显示和传感器技术虚拟现实的交互能力依赖于立体显示和传感器技术的发展。
现有的虚拟现实还远远不能满足系统的需要,需要开发新的三维显示技术。
3.3.4系统集成技术由于虚拟现实中包括大量的感知信息和模型,因此系统的集成技术起着至关重要作用。
集成技术包括信息的同步技术、模型的标定技术、数据转换技术、数据管理模型、识别和合成技术等等。
4.表面工程技术
4.1稀土表面工程技术表面工程技术中加入稀土元素通常采用化学热处理、喷涂喷焊、气相沉积、激光涂覆、电沉积等方法。
4.1.1 稀土元素对化学热处理的影响主要表现为有显著的催渗作用,大大优化工艺过程;
加入少量稀土化合物,渗层深度可以明显增加,改善渗层组织和性能。
从而提高模具型腔表面的耐磨性、抗高温氧化性的抗冲击磨损性。
4.1.2利用热喷涂和喷焊技术,将稀土元素加入涂层,可取得良好的组织与性能,使模型腔表面具有更高的硬度和耐磨性。
4.1.3物理气相沉积膜层性能的优劣和膜与基体结合强度大小密切相关,稀土元素的加入有利于改善膜与基体的结合强度,膜层表面致密度明显增大。
同时,加入稀土元素可以使膜层耐磨性能也得到明显改善,例如应用于模具表现的超硬TiN膜(加入稀土元素),使模具型腔表面呈现出高硬度、低摩擦系数和良好的化学稳定性,提高了模具的使用寿命。
4.1.4含稀土化合物的涂覆层,可大幅度提高模具金属材料表面对激光辐照能量的吸收率,对降低能耗和生产成本,以及推广激光表面工程技术都有重要意义。
稀土涂覆层经激光处理后,组织和性能发生明显改善,涂覆层的硬度和耐磨性显著提高。
对加入Ce02的热喷涂层进行激光重溶,研究发现合金化层的显微组织明显改变,晶粒得到细化。
激光重熔加入稀土后的喷焊合金,稀土化合物质点在其中弥散强化,降低晶界能量,提高晶界的抗腐蚀性能,模具型腔表面的耐磨性也大大增强,有的文献报道稀土元素提高了耐磨性达1~4倍。
4.1.5把稀土元素加入镀层可采用电刷镀、电镀等电沉积方法。
稀土甘氮酸配合物的加入使镀层防氧钝化寿命明显提高;
稀土元素有催化还原S02的作用,可以抑制Ni—Cu—P,MoS2电刷镀镀层中MoS2的氧化,明显改善了镀层的减摩性能,提高了抗腐蚀的能力,使模具型腔表面的耐磨寿命延长近5倍。
4.2 纳米表面工程技术纳米表面工程是以纳米材料和其它低维非平衡材料为基础,通过特定的加工技术、加工手段,对固体表面进行强化、改性、超精细加工,或赋予表面新功能的系统工程。
4.2.1 制作纳米复合镀层。
在传统的电镀液中加入零维或一维纳米质点粉体材料可形成纳米复合镀层。
用于模具的Cr—DNP纳米复合镀层,可使模具寿命延长、精度持久不变,长时间使用镀层光滑无裂纹。
纳米材料还可用于耐高温的耐磨复合镀层。
如将n—Zr02纳米粉体材料加入Ni—W—B非晶态复合镀层,可提高镀层在550—850。
C的高温抗氧化性能使镀层的耐蚀性提高2~3倍,耐磨性和硬度也都明显提高。
在传统的电刷镀溶液中,加入纳
米粉体材料,也可制备出性能优异的纳米复合镀层。
4.2.2制作纳米结构涂层。
热喷涂技术是制作纳米结构涂层的一种极有竞争力的方法。
其优越性在于:
工艺简单、涂层和基体选择范围广,涂层厚度变化范围大、沉积速率快,容易形成复合涂层等等。
与传统热喷涂涂层相比,纳米结构涂层在强度、韧性、抗蚀、耐磨、热障、抗热疲劳等方面都有显著改善,且一种涂层可同时具有上述多种性能。
5.模具并行工程
5.1并行工程的定义:
1988年美国国家防御分析研究所(IDA—InstituteofDefense Analyze)完整地提出了并行工程(CE—ConcurrentEngineering)的概念,即“并行工程是集成地、并行地设计产品及其相关过程(包括制造过程和支持过程)的系统方法。
这种方法要求产品开发人员在一开始就考虑产品整个生命周期中从概念形成到产品报废的所有因素,包括质量、成本、进度计划和用户要求。
并行工程的目标为提高质量、降低成本、缩短产品开发周期和产品上市时间。
并行工程的具体做法是:
在产品开发初期,组织多种职能协同工作的项目组,使有关人员从一开始就获得对新产品需求的要求和信息,积极研究涉及本部门的工作业务,并将所需要求提供给设计人员,使许多问题在开发早期就得到解决,从而保证了设计的质量,避免了大量的返工浪费.
5.2并行工程本质特点
(一)并行工程强调面向过程(process-oriented)和面向对象(object-oriented)
一个新产品从概念构思到生产出来是一个完整的过程(process)。
传统的串行工程方法是基于二百多年前英国政治经济学家亚当·
斯密的劳动分工理论。
该理论认为分工越细,工作效率越高。
因此串行方法是把整个产品开发全过程细分为很多步骤,每个部门和个人都只做其中的一部分工作,而且是相对独立进行的,工作做完以后把结果交给下一部门。
西方把这种方式称为“抛过墙法”(throwoverthewall),他们的工作是以职能和分工任务为中心的,不一定存在完整的、统一的产品概念。
而并行工程则强调设计要面向整个过程或产品对象,因此它特别强调设计人员在设计时不仅要考虑设计,还要考虑这种设计的工艺性、可制造性、可生产性、可维修性等等,工艺部门的人也要同样考虑其他过程,设计某个部件时要考虑与其他部件之间的配合。
所以整个开发工作都是要着眼于整个过程(process)和产品目标(productobject)。
从串行到并行,是观念上的很大转变。
(二)并行工程强调系统集成与整体优化
在传统串行工程中,对各部门工作的评价往往是看交给它的那一份工作任务完成是否出色。
就设计而言,主要是看设计工作是否新颖,是否有创造性,产品是否有优良的性能。
对其他部门也是看他的那一份工作是否完成出色。
而并行工程则强调系统集成与整体优化,它并不完全追求单个部门、局部过程和单个部件的最优,而是追求全局优化,追求产品整体的竞争能力。
对产品而言,这种竞争能力就是由产品的TQCS综合指标--交货期(time)、质量(quality)、价格(cost)和服务(service)。
在不同情况下,侧重点不同。
在现阶段,并货期可能是关键因素,有时是质量,有时是价格,有时是它们中的几个综合指标。
对每一个产品而言,企业都对它有一个竞争目标的合理定位,因此并行工程应酬围绕这个目标来进行整个产品开发活动。
只要达到整体优化和全局目标,并不追求每个部门的工作最优。
因此对整个工作的评价是根据整体优化结果来评价的。
5.3并行工程在先进制造技术中的地位与作用
并行工程在先进制造技术中具有承上启下的作用,这主要体现在两个方面:
1.并行工程是在CAD、CAM、CAPP等技术支持下,将原来分别进行的工作在时间和空间上交叉、重叠,充分利用了原有技术,并吸收了当前迅速发展的计算机技术、信息技术的优秀成果,使其成为先进制造技术中的基础。
2.在并行工程中为了达到并行的目的,必须建立高度集成的主模型,通过它来实现不同部门人员的协同工作;
为了达到产品的一次设计成功,减少反复,它在许多部分应用了仿真技术;
主模型的建立、局部仿真的应用等都包含在虚拟制造技术中,可以说并行工程的发展为虚拟制造技术的诞生创造了条件,虚拟制造技术将是以并行工程为基础的,并行工程的进一步发展方向是虚拟制造(VM?
/FONT>
Virtual Manufacturing)。
所谓虚拟制造又叫拟实制造,它利用信息技术、仿真技术、计算机技术对现实制造活动中的人、物、信息及制造过程进行全面的仿真,以发现制造中可能出现的问题,在产品实际生产前就采取预防措施,从而达到产品一次性制造成功,来达到降低成本、缩短产品开发周期,增强产品竞争力的目的。
6.模具CAD/CAE