水玻璃型壳文档格式.docx
《水玻璃型壳文档格式.docx》由会员分享,可在线阅读,更多相关《水玻璃型壳文档格式.docx(68页珍藏版)》请在冰豆网上搜索。
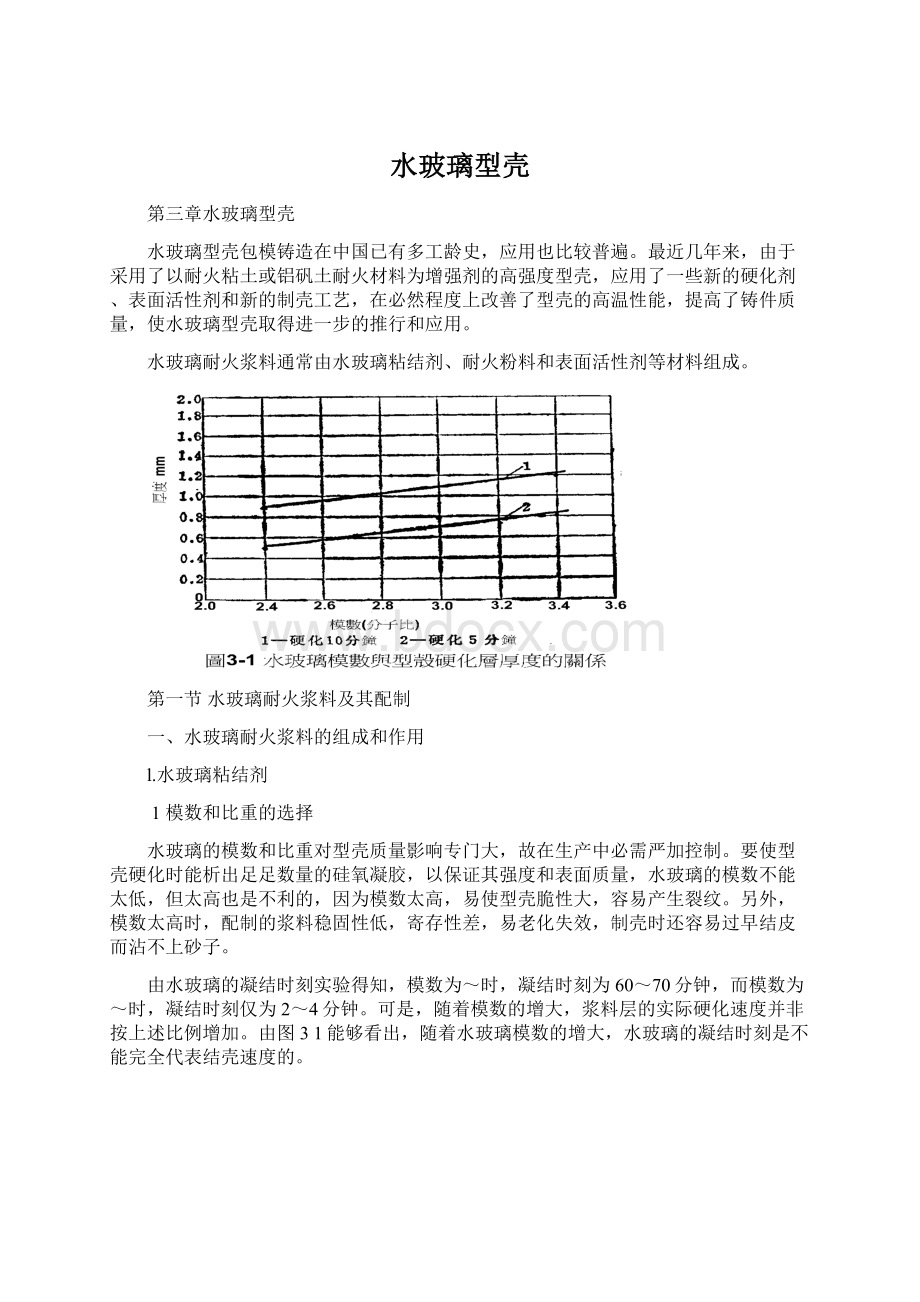
表3-1所示为一些工厂中常常利用的水玻璃性能指标。
层别
化学成分
模数
比重*
凝结时间
SiO
NaO
M
d
min
表面层
21~23
~
加固层
23~27
表3-1水玻璃性能指标
*用聚合氯化铝硬化时可取下限。
2水玻璃的处置
1)处置的目的和原理
市场上供给的水玻璃是供多种用途的,其模数和比重往往不符合表31的要求,故在配制浆料前需要进行调整,这就是水玻璃的处置。
对于M=~的水玻璃,只需加水调整其比重即可。
M<的水玻璃除调整比重之外,还需要提高其模数。
M>的水玻璃有时还要降低其模数。
对于包模铸造而言,直接采用高模数水玻璃,不进行提高模数的处置,能够大大简化工序,缩短生产周期和降低本钱,是值得推行的。
采用M=~的水玻璃时,要提高其模数,可通过提高SiO2含量或降低Na2O含量。
前者需专用设备,处置操作也较难掌握。
所以包模铸造中一般是用降低Na2O的方式来提高模数。
生产中常常利用的方式是在水玻璃中加入适量的工业氯化铵或工业盐酸,使水玻璃部份碱分取得中和,以达到提高模数的目的。
加入氯化铵或盐酸后,当即析出白色乳渣状混合物,其中含有初生硅氧胶、氯化钠和水玻璃。
用氯化铵处置时,尚有刺鼻的氨气析出。
处置时的化学反映如下
Na2OmSiO2.nH2O+2NH4Cl«
SkipRecordIf...»
mSiO2(n-1)H2O+2NaCl+2NH3↑+2H2O(3-1)
反映生成的初生硅氧胶不是顽强的化学键连系,它呈疏松多孔状态,并含有大量水玻璃。
由于处置时加酸量有限,故这些物质在水玻璃溶液中多余碱分的作用下,经2~5小时重行回溶而成为均匀、透明的水玻璃溶液。
碱分的减少就相对地提高了SiO2含量,这就达到了提高模数的目的。
处置后的水玻璃模数一般均在以上,pH值约为~。
处置时由于打破了Na2O和SiO2的平衡和稳固条件,使硅酸厚度增大,pH值降低,因此就使水玻璃成为介稳固状态的硅氧溶胶。
用它配制的浆料在制壳硬化时,能够迅速的析出硅氧凝胶而取得必要的强度。
处置时为了避免形成不溶性硅氧胶沉淀,一般是先把降低水玻璃比重所需的一部份水与氯化铵或盐酸配成厚度较小的溶液,然后再加到水玻璃中,这就是说,提高模数和降低比重是同时进行的。
降低水玻璃模数一般是增加水玻璃中的Na2O含量,方式是以10~30%水溶液形式加入工业氢氧化钠,并进行充分搅拌。
水玻璃处置的计算方式
计算的目的是肯定处置时需要的水、氯化铵、盐酸或氢氧化钠的加入量.
加水量可按下式计算
«
式中C加水量(克);
A处置水玻璃重量(gm),
d原水玻璃比重(gm/cm3);
——處理後要求的水玻璃比重(gm/cm3)。
为简便起见,可将上式制成图表形式。
图3-3所示为将水玻璃比重调整到gm/cm3时,每千克水玻璃的加水量。
按照生产经验,欲使水玻璃比重改变时,每100千克水玻璃需增减水2千克左右。
用工业盐酸处置时,总加水量尚须减去盐酸中的含水量。
氯化铵加入量可按下式计算
式中«
——氯化銨加入量(克);
A处置的水玻璃重量(克),
b原水玻璃中Na2O含量(%);
a原水玻璃中SiO2含量(%)
M'处置后要求的模数,
Q工业氯化铵中NH4Cl含量(%),
中和l克Na2O所需NH4Cl数量。
工业盐酸加入量可按下式计算
式中«
——鹽酸加入量,
——鹽酸中HCl含量(%),
——鹽酸比重(gm/cm3);
中和1克Na2O所需HCl数量。
工業鹽酸濃度通常為29~31%,相應的比重«
為~。
氢氧化钠加入量可按下式计算
——氫氧化鈉加入量,
——工業氫氧化鈉中NaOH含量(%),
系数(Na2O·
H2O/Na2O=80/62=。
由NaOH须以10~30%水溶液形式加入,故处置时应考虑到水玻璃比重也随着发生转变。
3)水玻璃处置方式
提高模数的处置方式是,称量出所需的水和NH4Cl重量,为了加速析出物的溶解,避免硅氧胶沉淀,先用总加水量的一部份溶解NH4Cl配成厚度小于10%的NH4Cl水溶液,其余水用来稀释原水玻璃。
由于NH4Cl溶解时和同水玻璃反映时均为吸热反映,为使反映加速,最好用60~70℃热水。
待NH4Cl全溶后,边搅拌边把热NH4Cl水溶液缓缓加到水玻璃中。
现在,当即形成白色乳渣状析出物和氨气。
加完后继续搅拌16~20分钟,使大块析出物破碎,然后加盖静置几小时,析出物即全数回溶,成为稀薄透明的水玻璃溶液。
用工业盐酸处置时,与上述方式类似。
由于HCl与水玻璃为放热反映,故稀释盐酸的水没必要加热。
处置时须强力搅拌40~50分钟,至析出物全数回溶为止。
用氯化铵处置的长处是操作安全、方便,但析出物回溶较慢,由于有NH3逸出,劳动条件不好,处置后需较长时刻静置,消除NH4OH的干扰,才能达到稳固的结果。
用工业盐酸处置的长处是析出物回溶较快,无氨味,劳动条件较好,处置后性能稳固,析出物溶清后可当即便用,工业盐酸价钱比氯化铵廉价得多。
但用盐酸处置时要注意安全和劳动保护,避免灼伤。
处置操作正常时,析出物在搅拌和静置时老是悬浮于溶液中或漂浮在表面上。
有时由于操作不妥而生成不溶性硅氧凝胶,其特点是比较致密,比重大且白色絮状物周围包覆一层透明胶体,极易沉淀于容器底部。
在这种情形下,即便再行搅拌或长时刻静置也难以回溶。
为了避免形成这种不溶性硅氧胶沉淀,氯化铵或工业盐酸水溶液的厚度勿太高(氯化铵不大于10%,盐酸不宜大于8%),更不宜用固体氯化铵或厚盐酸直接加入。
加入速度不要过快,不然即便总加入量不大,也不易回溶。
若原水玻璃模数较低时,最好采用少吃多餐方式,分批加入之。
操之过急往往达不到提高模数的目的。
用酸性盐或酸处置过的水玻璃,即便与购进的水玻璃有相同的模数和比重,但稳固性较低,不宜长时刻寄存,一般不超过4~6天。
水玻璃模数的提高不是没有限度的,一般情形下能提高~个单位。
故原水玻璃的模数太低时,为达到要求的模数,加酸量必然较多,处置时极易形成不溶性硅氧胶,所以包模铸造用水玻璃模数应在以上。
高模数水玻璃加水调整比重或加氢氧化钠调整模数的处置方式比较简单,但加水或加氢氧化钠水溶液后,要仔细搅拌,务必使加入物同水玻璃均匀溶合,方可用于配制浆料。
处置好的水玻璃要进行质量查验。
查验内容有比重、模数和凝结时刻等。
2.耐火粉料的选择和应用
配制水玻璃浆料的耐火粉料有石英粉、钢玉粉、耐火粘土、铝矾土等。
迄今为止,石英粉仍是用得较多的耐火粉料。
它的选择要知足耐火度和粒度的要求。
石英粉中SiO2愈高,耐火度也愈高。
对于表面层浆料,专门是浇注厚大的钢铸件时,为了保证表面光洁度,SiO2含量要求高些(>98%);
对于薄小铸钢件,非铁合金铸件和用于加固层浆料时,要求SiO2含量>96%即可。
石英粉的粒度,表面层选用过270目筛70%,200目筛残留量10%,140目筛子5%。
石英粉过粗时表面质量差,表面强度也不好。
加固层浆料一般选用200~140目石英粉,型壳透气性好,但过粗了浆料易沉淀。
水玻璃型壳浇注合金钢铸件时,也能够选用钢玉粉配制表面层浆料。
钢玉粉的耐火度高、热化学稳固性好,但比重较大,配制的浆料容易沉淀,宜用320目或更细(V28)的粒度并须常常进行机械搅拌。
最近几年来还普遍利用耐火粘土,铝硅系熟料或铝矾土等配制浆料,以制高强度型壳。
高强度型壳用耐火粘土的选择主要考虑Al2O3形态和含量、胶质价、粒度和当场取材等问题。
1Al2O3形态和含量
型壳高温强度的提高主要依赖于粘土中的Al2O3含量。
Al2O3对型壳的增强作用与其结晶形态有紧密关系,不同的Al2O3晶形由于其化学活性不同而具有不同的增强作用。
常温下,生粘土中的Al2O3多半以高岭石(Al2O32SiO22H,O)形态存在,在600℃以上,即开始分解成为颗粒细小、分散度大和化学活性高的初生的无定形的Al2O3和γAl2O3,称为活性Al2O3。
它们以弥散状态散布于型壳中,极易在高温下同SiO2Na2O系化合物形成新相并易溶于液相中。
耐火粘土通过800~900℃焙烧后,其中的Al2O3大体形态与上述情形类似,它们的化学活性也很高。
经更高温度下(>1000℃)焙烧过的粘土质熟料,其中的Al2O3经高温作用而颗粒长大,形成份散性小、活性较低的αAl2O3和莫来石。
上述几种晶形的Al2O3其化学活性依次递减,故其在型壳中的增强作用也依次递减。
所以耐火粘土中Al2O3含量的选择,不仅要考虑其总含量,也要考虑到它的化学活性。
按照许多工厂的生产经验,用普通生粘土配料时,Al2O3含量一般要求>23%,最少不能低于20%。
但也不宜太高,因为Al2O3含量太高时,型壳浇注后的残留强度相应增大,使铸件清砂困难,另外,还可能在某些铸钢件中形成热裂。
2胶质价(胶质价测定方式是将粘土在140~160℃下烘乾,称15±
,倒入容量100cc、直径25mm的带磨口塞的量筒中。
注入蒸馏水至95cc处,将量筒塞塞上,摇幌数分钟,再加入MgO10gm,加水至100cc处,摇动10分钟,静置24小时,使之沉淀。
24小时后沉淀的土柱高度,就是这种粘土的胶质价。
)
粘土-水系也是一种胶体溶液。
胶质价就是衡量粘土胶体性能的指标之一。
普通软质粘土粒子遇水发生膨胀并有良好的可塑性,脱水乾燥时产生收缩。
粘土的胶质价愈高,吸水膨胀性就愈大,粘结性和可塑性就愈强。
以高岭石为主要矿物组成的普通粘土,其胶质价一般为25~50。
用生粘土配料时,粘土的胶质价不可太高。
胶质价愈高,浆料粘度转变就愈大,寄存性差,浸浆作业时流动性不好,容易局部堆积而造成硬化不透,致使型壳分层、鼓胀和变形;
再有,胶质价太高时,为达到适宜的浆料粘度,粘土的加入量必然要减少,或增加水玻璃含量,这就破坏了浆料的正常配比,从而影响型壳强度。
所以,从型壳质量和浆料工艺性考虑,粘土胶质价一般宜<35~40%。
对于熟料(如铝矾土、焦宝石、匣钵粉等),由于预经高温焙烧,高岭石晶格破坏而失去吸水膨胀能力,所以遇水膨胀性极小。
例如某种山西大同粘土,胶质价为30%,经860℃焙烧后仅为19%。
故配制的浆料粘度稳固,流动性好,浆层较为均匀,硬化速度也较快。
3粒度
从型壳强度性能考虑,粘土粒度细时分散性大,增强作用好,浆料也不易沉淀。
但生粘土粒度愈细,吸水膨胀性愈大,所以普通耐火粘土粒度一般为70~100目。
其他粘土质熟料粉或铝矾土粉,由于它们的比重较生粘土大,遇水膨胀性很小,故粒度不宜过粗,以避免浆料沉淀,一般选为180~200目。
4当场取材
粘土选择应当符合因地制宜、当场取材和就近取材为原则。
选择粘土时应在调查研究和分析实验的基础上,尽可能采用本地材料,以避免远途运输,还可降低本钱。
3.表面活性剂
在水玻璃浆料中加入表面活性剂主要有两个作用,一是降低浆料与蜡模间的接口张力,提高它们之间的润湿性,改善浆料的亲和性;
二是增大浆料的分散性,浆料粘度转变小,稳固性较好。
表面活性剂的加入量通常由其临界胶束厚度来决定。
那个厚度一般都很小~%)。
由于其分子结构和碳原子数的不同,各类活性剂的临界胶束厚度也不同,另外,那个厚度还受到温度、电解质厚度和溶液极性等因素的影响。
所以在实际生产中多用实验方式加以肯定。
但其加入量不可过量,因为非离子型活性剂在溶液中会自成胶束或凝聚体,使粘度变大。
故对多数非离子型表面活性剂而言,加入量过量时,浆料粘度反而增大。
表面活性剂最好以水溶液形式加入,厚度可为25~50%。
在稀释或处置水玻璃时,同稀释水一道加入,可借机械搅拌作用,使活性剂分子能均匀地分散于水玻璃当中,以增大水玻璃硅氧溶胶的分散性。
在搅拌后的静置期间,气泡得以逸出。
常常利用非离子型表面活性剂,在常温下呈油状液体,温度较低时呈粘稠状液体,更低时呈膏状,利用前可用40~50℃热水溶解再行稀释。
对于聚乙二醇型非离子表面活性剂而言,受热时可呈浑浊状,这是因为加热温度超过了它的浊点之故。
疏水基相同时,环氧乙烷加成的分子数愈多,亲水性也愈大,浊点就愈高。
但冷却以后又复澄清,对其性能没有什么影响。
在浆料中加入表面活性剂后,对型壳的强度性能的影响,目前尚未进行深切的研究,但从实际利用效果来看,加入量超过%时,型壳残留强度似有所下降。
二、水玻璃耐火浆料的质量控制
衡量浆料的质量指标主要有;
适宜的配比和粘度,良好的分散性,流动性、亲和性和必然的稳固性等。
1.浆料的粘度
粘度是指浆料流动时悬浮液内部质点之间的内摩擦。
粘度不但决定了流动性,也决定了浆料层的厚度和涂敷的均匀程度,所以粘度是浆料质量的主要指标。
浆料粘度通常常利用漏斗形粘度计来测定。
目前中国包模铸造工厂所用的粘度计有好几种。
漏斗容量有550毫升和100毫升的两种,前一种出口直径为毫米,后一种出口直径有4毫米、5毫米和6毫米等几种。
其中以容量100毫升、出口直径为6毫米的用得最多,其结构尺寸如图3-4所示。
漏斗可用钢(镀铬抛光)、黄铜、铝合金或塑料等材料制成。
测定方式是先用手指堵住下端流出口,把搅拌均匀的浆料倒入其中并稍有过量,使多余浆料溢流到边槽中以自行定量,然后放开手指,让浆料流出,同时揿动秒表计时,直到浆料全数流出至持续流第一次断流为止。
记录这段时刻,就代表浆料粘度的大小。
流出时刻愈长则粘度愈大,反之就愈小。
测定完毕后应当即将粘度计用清水洗净,以备下次再用。
表面层浆料的粘度要着重从型壳和铸件表面质量考虑。
粘度过大时,浆料流动性低,浆层过厚且难以将浆料均匀包覆在蜡模表面上,尤其是容易堆积在蜡模的拐角、小孔和凹槽处,使这些部位硬化不透而引发粉化、起皮和脱落,型壳透气性也低,铸件表面易形成夹砂、粘砂和砂眼等缺点。
若粘度过小,则浆料厚度过薄,在撒砂时容易被砂粒打穿或被气流吹走,边角处浆料更易流失而撒不上砂粒,从而在硬化和硬化后乾燥时容易沿边角开裂,浆料过薄时,铸件表面也易于形成铁刺。
表面层浆料粘度选择要与铸件形状复杂程度相适应。
外形复杂的且具有小孔、深槽、齿形和其他不规则表面时,浆料粘度要小些,以使浆料能进入这些细小部位,又不致在哪里堆积过量而影响硬化深度;
对于形状简单的厚实铸件,粘度可适当大些。
另外,表面层浆料粘度也要与所用硬化剂性质相适应,用聚合氯化铝为硬化剂时,粘度宜小些。
用氯化铵为硬化剂时,粘度则可大些。
加固层浆料粘度要着重从型壳强度和硬化深透性考虑。
粘度小了,浆层过薄,撒砂时砂粒粘附不牢,型壳强度低;
粘度过大时,浆层过厚,往往硬化不透,容易产生分层、鼓胀等缺点,型壳强度也很低。
脱蜡时容易开裂和煮烂。
与表面层相较,加固层浆料撒砂较粗。
型壳外表面积增大,故粘附的浆料层必然耍厚些,为使其硬化充分。
浆料粘度比表面层小些,对高强度型壳加固层浆料有时粘度比表面层浆料大。
粘度选择还与制壳操作方式有关。
手工操作时,能够甩浆料使之散布均匀,这时粘度可大些,在机械化流水联机生产时,浸浆后靠撒砂前一段吊具位移和转动而使其散布均匀,没有甩的动作,故浆料粘度宜小些。
2.原材料的性质、配比和粘度的关系
浆料需要有适宜的配比,为的是保证型壳的表面质量、强度和透气性等要求,同时配比还应保证浆料有适宜的粘度。
浆料的配比第一由原材料的性质,如水玻璃模数和比重,耐火材料的化学成份、粒度、粒形和湿度和胶质价等因素来决定。
浆料粘度主要由配比决定,反过来,粘度又会影响配比关系。
在实际生产中,正确的掌握和控制原材料性质、配比和粘度这三者的关系和各类因素对它们的影响,对于保证型壳和铸件质量有重要意义。
(l)表面层浆料
对于表面层浆料,通常是采用粉料重量略大于粘结剂重量的配比,即水玻璃:
石英粉=1:
~(表3-2例l)。
这样的配比在一般情况下都能保证型壳的耐火度和表面质量而粘度也比较合适。
水玻璃
石英粉
匣钵粉
接口活性剂
粘度
1
JFC
20~30
2
TX10与松节油混合物(各半)
15~25
3
~
同上
11~20
表3-2表面层浆料配比举例
例l中水玻璃M=~,d=,氯化铵硬化剂,铸钢件。
例2中水玻璃M=~,d=~,聚合氯化铝硬化剂,铸钢件。
例3中水玻璃M、d与例2相同,聚合氯化铝硬化剂,铸钢件。
假设水玻璃(a=~中含SiO223%,Na2O7%,略去杂质,则含水量约为70%。
若按水玻璃;
石英粉=l:
l配料,在搅拌均匀的情形下,浆料中SiO2含量应为%,
Na2O为%,水为35%,石英粉为50%。
在如此的浆料中,石英粉起了充填剂的作用,而钠盐和水分占了近40%。
这些物质在以后的硬化、乾燥、脱蜡和焙烧进程中将被去除而在型壳中留下孔隙。
浆料中石英含量愈高,则型壳表面愈致密,孔隙度就愈小,表面愈光洁;
从那个意义上来讲,石英粉含量大于水玻璃含量,对提高表面质量是有利的,生产实践也证明了这一点。
石英粉含量也不宜太高。
太高了浆料粘度太大,浆层堆集过厚,同时由于水玻璃含量减少,表面强度将下降。
故生产中若水玻璃模数为~时,表面层浆料水玻璃:
石英粉为1:
之内。
若是水玻璃模数高于和用聚合氯化铝硬化时,为了降低浆料粘度,保证硬化深透,一般是降低水玻璃比重来控制粘度,而不宜减少粉料加入量,如表3-2中例2、例3所示。
许多工厂表面层浆料常按照粘度来控制其配比,虽然不十分准确,一般生产条件下仍是可行的。
可是必需考虑到因原材料(如水玻璃或石英粉)来源和性质改变或气温转变所引发的粘度转变,这对稳固型壳质量是十分重要的。
2加固层浆料
对于加固层浆料来讲,原材料性质、配比和粘度的关系不像表面层浆料那么单纯,有三种情形要别离考虑。
第一种情形,普通水玻璃型壳加固层浆料中不含粘土,一般采用与表面层浆料相反的配比,即水玻璃;
石英粉(200目)=~:
,同时采用比重较大的水玻璃。
由于浆料中粘结剂成份增大,型壳强度有所提高,而粘度却较表面层浆料小些。
在这种情形下,也可用粘度来控制配比,但也必需考虑到原材料来源和气温转变的影响。
第二种情形,加普通粘土的高强度型壳。
这时的浆料配比不仅要考虑粘结剂与粉料的比例,还要考虑到石英粉与粘土的比例,就是说,要综合考虑粘结剂、石英粉和粘土这三者的比例关系,目的是保证型壳有足够的耐火度、常温和高温强度并使浆料有适宜的粘度。
这种浆料的配比要使型壳中有足够的活性Al2O3含量,此含量是由粘土加入量来保证的。
按照国内一些工厂的经验,用Al2O3>25%,胶质价<30%的耐火粘土时,加固层浆料常常利用的配比是水玻璃:
石英粉:
耐火粘土=1:
~:
~(表3-3)。
这种配比在粘结剂性能合格和工艺操作正常情形下,是能够保证型壳强度性能的,浆料粘度也比较适合。
在如此的型壳加固层中Al2O3的加入量可做一个粗略的计算。
依照上述配比,浆料中含粘土量取20%。
假设粘土中Al2O2含量为30%,则浆料中Al2O3含量应为%。
又设加固层撒砂重量略等于浆料重量,那么焙烧后的型壳中Al2O3含量约为3~5%。
经实际生产证明,当型壳中以粘土形式加入的Al2O3为3~5%时,高温强度是足够的,配料时粘土加入量应当知足那个要求。
若是粘土中Al2O3含量较低,则上述配比就不适合了。
这时为了保证型壳中Al2O3含量,须增加粘土含量。
若是粘土胶质价低,这仍是可能的。
若胶质价高时(>30%),多加粘土必然引发浆料粘度增大乃至无法用浸浆作业,可见,如此的浆料单纯控制配比,就容易使粘度失调。
反之,若单纯控制粘度,就会使配比失调。
因为达到一样粘度时,三种材料能够有多种配比。
为使粘度适合,要么少加粉料,要么多加水玻璃,再加上温度因素的影响,因此单纯控制粘度,往往不能保证型壳中的Al2O3含量,高温强度就必然会受到影响。
由此可见,用石英粉和普通粘土配料时,保证浆料中有足够Al2O3和粘结剂的含量,同适宜粘度之间是有矛盾的。
为了解决这个矛盾,首先要选择Al2O3含量较高,胶质价较低的粘土,其次,若粘土中Al2O3含量较高而胶质价也高时,则可减少石英粉含量,同时适当提高水玻璃模数并降低其比重来调正粘度(表3-3例2);
也可以采用生熟料搭配的方法配料,即加入适量熟粘土粉以减少生粘土含量。
对于Al2O3含量低和胶质价高的粘土,一般只作为调整粘度和改善浆料悬浮性之用,而不宜作为主要耐火粉料配制浆料。
举例
沈阳粘土Al2O329%胶质价26%
山西大同粘土Al2O327%胶质价35%
接口活性剂%
25~40
农乳130
30~50
表3-3普通粘土加固层浆料配比举例
例l水玻璃M=~,d=~,NH4Cl硬化剂,铸钢件
例2水玻璃M=~,d=,NH4Cl硬化剂,铸钢件
第三种情况,用硬质粘