煤制乙二醇技术进展Word格式文档下载.docx
《煤制乙二醇技术进展Word格式文档下载.docx》由会员分享,可在线阅读,更多相关《煤制乙二醇技术进展Word格式文档下载.docx(11页珍藏版)》请在冰豆网上搜索。
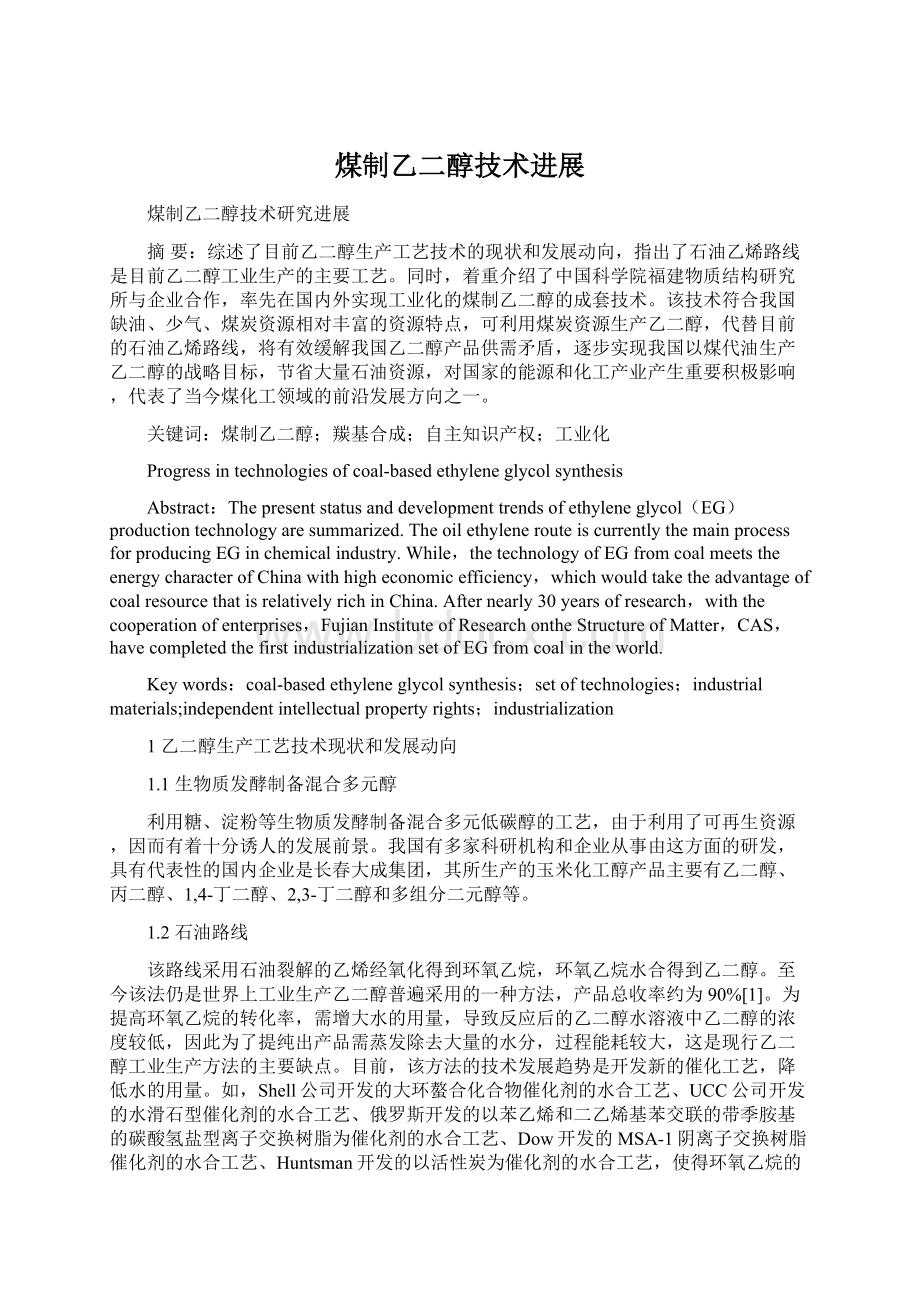
Thepresentstatusanddevelopmenttrendsofethyleneglycol(EG)productiontechnologyaresummarized.TheoilethylenerouteiscurrentlythemainprocessforproducingEGinchemicalindustry.While,thetechnologyofEGfromcoalmeetstheenergycharacterofChinawithhigheconomicefficiency,whichwouldtaketheadvantageofcoalresourcethatisrelativelyrichinChina.Afternearly30yearsofresearch,withthecooperationofenterprises,FujianInstituteofResearchontheStructureofMatter,CAS,havecompletedthefirstindustrializationsetofEGfromcoalintheworld.
Keywords:
coal-basedethyleneglycolsynthesis;
setoftechnologies;
industrialmaterials;
independentintellectualpropertyrights;
industrialization
1乙二醇生产工艺技术现状和发展动向
1.1生物质发酵制备混合多元醇
利用糖、淀粉等生物质发酵制备混合多元低碳醇的工艺,由于利用了可再生资源,因而有着十分诱人的发展前景。
我国有多家科研机构和企业从事由这方面的研发,具有代表性的国内企业是长春大成集团,其所生产的玉米化工醇产品主要有乙二醇、丙二醇、1,4-丁二醇、2,3-丁二醇和多组分二元醇等。
1.2石油路线
该路线采用石油裂解的乙烯经氧化得到环氧乙烷,环氧乙烷水合得到乙二醇。
至今该法仍是世界上工业生产乙二醇普遍采用的一种方法,产品总收率约为90%[1]。
为提高环氧乙烷的转化率,需增大水的用量,导致反应后的乙二醇水溶液中乙二醇的浓度较低,因此为了提纯出产品需蒸发除去大量的水分,过程能耗较大,这是现行乙二醇工业生产方法的主要缺点。
目前,该方法的技术发展趋势是开发新的催化工艺,降低水的用量。
如,Shell公司开发的大环螯合化合物催化剂的水合工艺、UCC公司开发的水滑石型催化剂的水合工艺、俄罗斯开发的以苯乙烯和二乙烯基苯交联的带季胺基的碳酸氢盐型离子交换树脂为催化剂的水合工艺、Dow开发的MSA-1阴离子交换树脂催化剂的水合工艺、Huntsman开发的以活性炭为催化剂的水合工艺,使得环氧乙烷的转化率及乙二醇的选择性分别得到了显著提高,但这些高效的新工艺技术还没有实现真正的工业化[2]。
1.3半石油路线
该路线采用环氧乙烷先与二氧化碳反应生成碳酸乙烯酯,再在缓和条件下水解生成乙二醇,此法有能耗小的优点,但还没有实现工业化[3-4]。
如,三菱化学于1979年开始该技术路线的研发,1982年完成实验室规模试验,1997年在鹿岛建造1.5万吨/年的中试装置,并于2001年7月投入运转;
2002年4月,三菱化学与Shell公司签定了独家转让权,以共同推进“Shell/MCC”联合工艺,并计划在中东、亚洲等地区新增的装置中推广该新工艺,但到目前还没有建厂的报道。
在我国,中国科学院兰州化学物理研究所近期也开展了该技术路线的研究。
1.4非石油路线
即基于合成气制备乙二醇的工艺,主要包括:
①以甲醛和甲醇为原料的DuPont甲醛羰化法;
②以一氧化碳和氢气为原料的UCC直接合成法[5-6];
③以CO和低碳醇为原料的日本宇部和UCC共同开发的氧化偶联法[7];
④以甲醇和甲醛为原料的由Redox和Celanese共同开发的Redox法;
⑤甲醛缩合法等。
其中以一氧化碳和氢气为原料的制备方法受到广泛关注。
1.5其它方法
(1)乙烯氧化水解法是乙烯不经环氧乙烷而氧化水解成乙二醇的方法。
反应过程实际上分两步进行。
首先,使乙烯、氧和乙酸在催化剂存在下反应生成中间产物乙酸乙二醇酯。
然后,在酸催化下使酯水解为乙二醇。
此过程虽然产物选择性较高,
但由于反应分两步进行,水解释出的乙酸需循环使用,且存在腐蚀及能耗问题,所以自1978年哈康公司建成年产360kt乙二醇装置后,未见推广。
(2)氯乙醇水解法1919年,德国巴登苯胺纯碱公司开发的氯乙醇水解法生产乙二醇是较早的工业方法。
此法副产物少,但生成的氯化钠难以分离,又未能解决腐蚀及能耗高等问题,迄今尚未得到推广。
综合上述各种生产工艺,以生物质发酵制备混合多元醇技术利用可再生的资源同时生产出多种重要化学品,如果有成功高效的分离技术配合,潜力诱人。
以乙烯(环氧乙烷)为原料的环氧乙烷水合法是目前乙二醇工业生产的唯一工艺,但能耗高,消耗大量石油资源,经济效益低。
环氧乙烷催化水合法可以大大降低水比,节省能耗,降低生成成本。
半石油路线的碳酸乙烯酯法可充分利用CO2资源,减少了环氧乙烷的消耗,在现有环氧乙烷生产装置内,只需增加生产碳酸乙烯酯的反应步骤就可以生产碳酸乙烯酯和碳酸二甲酯两种应用广泛的化工产品。
利用合成气的“CO催化合成草酸酯和乙二醇”技术,充分利用我国相对丰富的煤和天然气资源,生产我国目前供不应求的乙二醇,弥补我国石油资源的不足,将对我国的化工和能源产业产生巨大的影响,此技术被国际化工界认为是当今世界C1化工领域的一项重大新工艺、新技术。
2煤制乙二醇技术
以煤为原料生产乙二醇,主要有以下3条工艺路线。
(1)以煤气化制取合成气(CO+H2),再由合成气一步直接合成乙二醇。
其反应的化学方程式如下:
2CO+3H2→HOCH2CH2OH
此反应的反应条件苛刻,需要催化剂和高温高压条件。
该工艺技术的关键是催化剂的选择。
在1947年美国DuPont公司采用钴催化剂由合成气直接合成了乙二醇,但该催化剂要求的反应即使在高温、高压条件下乙二醇的收率也很低。
1971年,美国UCC公司首先公布用铑催化剂从合成气制乙二醇,其催化活性明显优于钴,但所需压力仍太高(340MPa),同时副产大量的甲酸酯。
Masuda等[5]以钴、铑为催化剂对该反应进行了研究,发现乙二醇的选择性随氢分压的增大而显著增大。
20世纪80年代以来,确定为合成气直接合成乙二醇的优良催化剂主要分为铑和钌催化剂两大类[8-9]。
UCC公司采用铑为催化活性组分,以烷基膦、胺等为配体,配制在四甘醇二甲醚溶剂中,反应压力可降至50MPa,反应温度降至230℃,不过合成气整体的转化率和选择性仍然很低。
钌类催化剂主要利用了咪唑的甲基和苯取代物,据认为咪唑类化合物的强配位作用和碱性作用对反应有利,1-甲基苯异咪唑(NMBI)在四甘醇醚(TGM)存在下,能够把乙二醇选择性提高到70%以上。
日本研究的铑和钌均相系催化剂[10-11]。
乙二醇选择性达57%,产率达259g/(L.h)。
日本工业技术院最近获得的一项专利则是以乙酰丙酮基二羰基铑为催化剂,合成气经液相反应制得乙二醇,乙二醇产率可达l7.08mol/molRh。
(2)以煤气化制取合成气(CO+H2),由合成气制甲醇,甲醇制乙烯,乙烯氧化得环氧乙烷,最后由环氧乙烷水合法制乙二醇。
煤制烯烃在中国已有多个示范装置在建设中,预计将于3年内走向成熟;
乙烯制乙二醇工艺和石油路线一样,是非常成熟的技术;
不足之处是流程较长,并且甲醇制取乙烯过程中还会生成丙烯。
(3)以煤气化制取合成气(CO+H2),CO催化偶联合成草酸酯再加氢生成乙二醇。
上述3种方法中,第一种方法是最简单、有效的途径,即使反应选择性和转化率较低,也具有很大的实际应用价值。
但因反应条件苛刻,时至今日,直接法取得的成果还不足以实现工业化,但它的进展还是很大的,如果能够有突破,使反应在较温和的条件下进行,将非常有竞争力[12]。
后两种方法可望在近期实现商业化,鉴于第二种方法中的煤制烯烃还需要过几年才能走向成熟,而第三种方法已完成20万吨/年的工业装置的建设并试车成功,是最先实现工业化的煤制乙二醇路线。
下面将重点介绍第三种方法(下文提到的煤制乙二醇路线特指第三种方法)。
2.1国内外相关技术现状与趋势
2.1.1国外相关技术发展情况
1965年,Fenton等[13]发现了醇类氧化羰化合成草酸酯技术,奠定了当今煤制乙二醇的技术基础。
四十多年来,各技术发达国家十分重视煤制乙二醇新技术的研发。
日本的Ube公司[7,14]于1978年建成6000t/a草酸二丁酯水解生产草酸工厂,该工艺是在硝酸的存在下,以活性炭为载体的Pd为催化剂,用CO、O2和正丁醇反应,反应温度90℃,压力9.8MPa,生成草酸二丁酯。
2C4H9OH+2CO+1/2O2→(COOC4H9)2+H2O
草酸二丁酯再采用液相加氢合成乙二醇。
此工艺催化剂体系单一,回收容易,催化剂活性较高,产品纯度高,生产实现连续化。
但是反应中草酸二丁酯的生成速率低,副产物多,且加氢反应要在20MPa以上进行,液相体系易腐蚀设备,且反应过程中催化剂易流失,至今没有推广。
继液相法成功之后,针对液相法合成中条件比较苛刻,如高温、高压及反应过程中催化剂流失等工艺缺点,日本宇部兴产公司和意大利蒙特爱迪生公司于1978年相继开展了气相法的研究[15]。
气相法反应过程分为两步:
第一步为一氧化碳在负载型Pd/α-Al2O3催化剂的作用下,常压与亚硝酸甲酯偶联反应生成草酸二甲酯和一氧化氮,反应方程式为
2CH3ONO+2CO→(COOCH3)2+2NO
第二步为偶联反应生成的一氧化氮与产品分离后进入填料塔,在那里常温条件下与甲醇和氧气反应生成亚硝酸甲酯,反应方程式为
2NO+2CH3OH+1/2O2→2CH3ONO+H2O
生成的亚硝酸乙酯返回偶联过程循环使用。
总反应式为
2CH3OH+2CO+1/2O2→(COOCH3)2+H2O
目前,日本宇部兴产公司对该方法进行了中试试验,已基本具备工业化生产的条件,并先后发表了一些专利,但尚未见到建厂生产的报道[16-17]。
2.1.2国内相关技术发展情况
随着国际CO气相偶联制草酸酯、草酸工艺路线的提出,大大促进了国内研究者对气相法的研究开发。
根据我国资源分布特点,以CO为原料制备有机含氧化物,对于缓解石油产品的紧张状况、合理利用天然气和煤气资源具有重要战略意义,由CO气相催化偶联制草酸酯已成为国内C1化学及有机化工领域中的重要课题[18]。
我国西南化工研究院,曾于1981—1982年采用液相法合成草酸二乙酯,草酸二乙酯和碳酸二乙酯的总收率达79.63%;
中科院成都有机所[19-20]于1985—1989年开展了纯CO气相催化合成草酸二乙酯的研究,曾对5种催化剂进行了试验;
浙江大学化工系[21]也于1989年开展过纯CO气相催化合成草酸二乙酯的研究,并在浙江江山化工厂进200t/a合成草酸二乙酯的中试。
天津大学[22]、华东理工大学[23]、南开大学[24]也开展了这方面的研究,比较有代表性的研究有:
王保伟等[25]对CO气相偶联制草酸进行了模拟放大研究,已完成中试,还对Cu-Ag/SiO2催化剂上草酸二甲酯的加氢反应进行了初步研究;
李振花等[26]对草酸二乙酯气相催化加氢制乙二醇进行了初步研究;
Xu等[27]从催化动力学方面对这一反应进行了初步探索;
李竹霞等[28-29]采用Cu/SiO2化剂以草酸二甲酯为原料,加氢制备乙二醇,对催化剂前体和反应特性进行了研究。
近年来,华东理工大学在工业化试验方面取得了突破性进展,该研究组于2003年在实验室打通流程,制备出乙二醇产品;
2005年,华东理工大学与上海焦化达成合作协议,并与2006年完成了30t/a的工业化模拟试验,成功制备出乙二醇;
2009年,华东理工与上海浦景化工技术有限公司、安徽淮化集团达成合作协议,在安徽淮化集团建设1000t/a煤制乙二醇的中试装置,项目将于2010年内建成。
此外,上海华谊投资近一亿元,在上海焦化区内采用华谊集团自主开发的煤制乙二醇工艺技术,建设1500t/a乙二醇和10000t/a草酸中试装置,目前项目正在建设中,预计将于2011年试运行。
中国五环工程有限公司、湖北省化学研究院、鹤壁宝马集团三方合作的煤制乙二醇中试基地项目于2010年1月开工建设,投资980万元进行300t/a中试。
日本宇部兴产与国内一家化工设计研究院合作正在进行草酸酯加氢制乙二醇的中试。
但目前都还没有成功中试或者工业化的报道。
2.2中国科学院福建物质结构研究所煤制乙二醇项目的技术优势和产业化进展
2.2.1实验室小试、模试技术积累及优势
中国科学院福建物质结构研究所是国内开展
CO气相催化合成草酸二酯研究的最早单位之一。
从1982年开始,小试研究开发出的CO气相催化合成草酸二酯催化剂,其活性达到了891g(CH3OCO)2/(L.h)(SV=3000h-1)和1411g(CH3OCO)2/(L.h)(SV=5025h-1),并完成了1004h的连续寿命试验。
1993年,成功通过了国家“八五”攻关项目200mL催化剂规模、1000多小时催化剂寿命考察的模试工作,打通了新工艺路线全过程,催化剂寿命达标。
为了更切合工业生产实际,考察了列管反应器的管径大小、催化剂装填方法、反应物料配比和加料方式对反应温度的影响、反应温度的控制技术、产物的回收分离、尾气的再生、回收、循环等工艺流程。
接着,在合成氨厂利用合成氨铜洗回收的工业CO气体(经脱硫、除氨、脱氢、除氧、除水等净化过程后)作为反应原料,进行2L催化剂的气相催化合成草酸二酯和草酸工艺条件的实验,取得了初步成功。
经过该研究所长达二十多年的研究开发,完成了具有自主知识产权的小试和模试技术[30],其中包括:
①第一次在国内外全部采用工业CO、工业NO、工业H2、工业O2和工业醇类为原料研究“煤制乙二醇”技术,更贴近工业生产实际;
②拥有自主创新的多项国家发明专利[31-35]、3种自主创新的性能处于国内外先进水平的催化剂技术;
③拥有全套工艺技术的核心技术。
2.2.2技术放大和产业化进展
2004年,在总结、梳理以往科研成果的基础上,福建物质结构研究所清楚地认识到煤制乙二醇项目的重大科学意义和对国家需求的重要贡献,重新组织了煤制乙二醇项目攻关组,集中全所的人力、物力和技术力量协同攻关,推进煤制乙二醇技术的工业化进程。
2005年攻关组与上海金煤化工新技术有限公司展开合作,对3种关键催化剂技术进行了技术集成和催化性能提升,取得了突破性进展,2006年完成了“CO气相催化合成草酸酯(300t/a)和乙二醇(100t/a)”项目的中试,达到日产900kg草酸甲酯的能力;
2006年12月,完成100t/a加氢生产乙二醇中试;
2007年8月,由金煤投资1.5亿元,在江苏丹阳组织万吨/年乙二醇的工业实验装置,并在2008年6月,完成了全部的试验工作,实现了预期各项技术指标,生产出的乙二醇产品质量完全达到国际国内同等水平,乙二醇产品各项理化指标均达到GB4649—1993优级品标准。
万吨级/年乙二醇工业实验装置包括如下自主创新的核心工艺技术。
(1)氨氧化技术在进行CO气相催化合成草酸酯的反应过程中,一般都采用NaNO2与H2SO4反应生成的氮氧化物作为循环的NO气体消耗的补充。
但这种方法只能在小规模的研究工作中使用,不适合大工业生产的需要。
因此,为了适应大规模工业生产的实际需要,福建物质结构研究所在国内外首先成功开发了用氨在空气中高温氧化产生的氮氧化物或硝酸工业尾气中的氮氧化物作为合成草酸酯的NO补充气源的工艺技术,既降低了NO气体的生产成本,又为全套煤制乙二醇技术的大规模生产推广创造了有利条件。
(2)高浓度CO气体脱氢催化剂及脱氢净化的工艺技术成功开发了高浓度CO气体脱氢净化催化剂及其全套净化工艺,使含氢的工业CO气体经过脱氢净化后可以直接用做合成草酸酯的CO气源;
把高浓度CO(CO≥98%,含氢1%~2%)气体中的H2净化到H2≤100μL/L;
脱氢催化剂的对氢气的氧化选择性≥70%,氢气的转化率≥99%。
(3)高活性CO气相催化合成草酸酯催化剂和工艺技术成功开发了高活性CO气相催化合成草酸酯催化剂及其合成工艺,并有效地解决了高活性草酸酯合成催化剂的超温问题,催化剂活性和选择性达到国内外的领先水平,催化剂时空产率≥750g(CH3OCO)2/(L.h)(SV=3000h-1),草酸酯的选择性≥99.5%。
(4)高活性草酸酯催化加氢合成乙二醇催化剂和工艺技术成功开发了高活性草酸酯催化剂加氢合成乙二醇催化剂及其工艺,经过分离和精馏得到的乙二醇产品各项理化指标符合GB4649—1993优级品的标准,所开发的加氢催化剂在草酸二甲酯液时空速0.2~0.5g/(mL.h)、反应压力为0.8~3.0MPa、反应温度为200~250℃、氢气空速为4000~8000h-1的条件下,草酸酯转化率≥98%,乙二醇选择性≥90%,时空产率≥110g(CH2OH)2/(L.h),在连续运行1000h后性能仍保持稳定。
(5)NO氧化酯化技术成功开发了直接用工业O2和含醇量≥20%的醇水溶液对尾(NO)进行循环利用的氧化酯化工艺技术。
NO的回收率≥95%(体积分数),从而大大减少NO气体的补充量,并且整个工艺技术操作过程简单,投资少,能耗低,有效降低了生产成本。
(6)排放气体中消除NO污染由于直接使用空气、工业CO、NO和O2作为反应气体,这些原料气中都含有大量的N2、Ar、CO2、CH4等非反应气体,随着反应的不断进行,既要不断补充工业CO、工业NO气体,又要不断从反应系统排出非反应气体。
这就必然会同时从反应系统排出NO、CH3ONO和甲醇等有用的反应气体。
为了减少反应原料的消耗,反应尾气达标排放,福建物质结构研究所开发成功了既能把NO作为反应原料回收循环使用、又能达标排放的独特的消除排放气体NO污染环境的工艺技术,使排放尾气中的氮氧化物的含量小于200μL/L,达到国家环保允许排放的标准,使整个工艺技术达到无污染的绿色环保工程
的标准。
2009年3月18日,万吨级煤制乙二醇成套工艺技术通过了由中国科学院主持的成果鉴定。
鉴定委员会一致认为:
该成套技术符合循环经济三原则,完全拥有自主知识产权,全部采用工业CO、NO、H2、O2和醇类为原料,反应条件温和,技术指标达到了设计要求,万吨级工业试验装置运行稳定,具备了进一步建设大规模工业化生产装置的条件。
2007年8月,在内蒙古自治区通辽市启动了120万吨/年规模(首期20万吨工业示范)的乙二醇工业大装置。
2009年12月,内蒙古自治区通辽市高新技术开发区的20万吨工业示范装置全部建设完成,并于12月7日试车成功,打通了全套工艺流程,生产出合格的乙二醇产品。
随后,通过对原有设计进行调整,使整套装置具备联产10万吨/年草酸的能力,经过联动试车,于2010年5月3日试产出合格的草酸产品。
预计20万吨工业示范装置在2010年年底能正常达产,实现大于70%设计负荷的运行(即第一年年产14万吨乙二醇),通辽金煤公司今年还将完成二期40万吨/年乙二醇项目立项审批工作,并于年内适时启动二期项目建设。
2.3煤制乙二醇技术的原理与路线
煤制乙二醇工业化技术和新型催化剂的应用研究以及采用工业CO、工业NO、工业氢气、工业氧气和工业醇类作为原料制备乙二醇的具体工艺技术及原理如下所述。
(1)具体工艺技术
图1煤制乙二醇技术原理
工业气体CO脱氢处理→纯净的CO原料气体(脱氢催化剂)合成草酸酯过程
2RONO+2CO→(COOR)2+2NO(合成催化剂)
2NO+1/2O2→N2O3
N2O3+2ROH→2RONO+H2O
总反应
2ROH+2CO+1/2O2→(COOR)2+H2O
生成草酸
(COOR)2+4H2O→(COOH)2·
2H2O+2ROH
加氢制乙二醇过程
(COOR)2+4H2→(CH2OH)2+2ROH(加氢催化剂)
烷基R可为甲基、乙基、丙基、丁基等,RONO可由甲醇、乙醇、丙醇、丁醇等为原料制得。
生产草酸的总反应方程式
2CO+1/2O2+3H2O→(COOH)2_2H2O
生产乙二醇的总反应方程式
2CO+1/2O2+4H2→(CH2OH)2+H2O
上述反应过程显示出:
煤炭+空气+水→乙二醇。
(2)煤制乙二醇技术原理(图1)
这条完整的煤制乙二醇技术路线是由中国科学院福建物质结构研究所首先提出并顺利实施的,其对整套工艺技术路线及工艺技术路线中的3种关键催化剂拥有独立自主知识产权。
3个关键催化剂包含在3个催化反应过程中:
工业CO的催化脱氢、羰基催化合成反应和草酸酯催化加氢制备乙二醇。
技术路线是绿色、原子经济的反应过程。
2.4经济效益分析
煤制乙二醇技术路线是以煤、水、氧气为反应原料的原子经济反应,CO和H2中的C、O、H元素全部利用转化成乙二醇。
在江苏丹化集团以优质块煤(以1200元/t计算)为原料在万吨级工业示范装置上每生产1t乙二醇的成本市6444元,与石油路线的成本(7000元/t)不相上下。
考虑到丹化集团用优质块煤的固定床技术造气,相应的成本会高一些,所以放大规模后成本会进一步下降。
第一套20万吨煤制乙二醇装置建在内蒙古自治区通辽市,利用当地丰富的褐煤资源(150元/t),采用恩德炉造气技术,气头、电力、蒸汽等项费用将有大幅下降,1t乙二醇的生产成本大约2625元,与石油路线的成本(7000元/t、石油价格为90美元/桶)相比,有了大幅度的下降。
甲醇制烯烃路线煤制乙二醇工艺尚没有工业化的示范装置,中国科学院大连化学物理研究所和亚化咨询公司对其成本进行了估算,当煤价为185元/t时,对应乙二醇生产成本为5000元/t左右。
因而可以预测,此项技术与石油乙烯生产乙二醇的技术相比,具有明显优势的经济效益;
与即将工业化的甲醇制烯烃路线煤制乙二醇技术相比,也有明显的价格优势。
2.5技术影响力
煤制乙二醇技术发展过程中,受到国内外企业的普遍青睐。
在2007年中国科学院党组冬季扩大会议和2008年中国科学院工作会议上,作为“源头创新,点石成金”典型案例向全院介绍。
2009年5月7日,技术鉴定后,中国科学院在北京人民大会堂组织了“世界首创万吨级煤制乙二醇技术”新闻发布会,科技部、工信部、国土部、基金委、中国石化协会、福建省政府、江苏省政府、内蒙古自治区等部门领导和国内三十多家主流媒体共同出席了发布会。
全国人大常委会副委员长中国科学院院长路甬祥院士在会上作了重要讲话,充分肯定了技术的先进性,高度评价了技术创新机制。
煤制