冷冲模毕业设计汇总文档格式.docx
《冷冲模毕业设计汇总文档格式.docx》由会员分享,可在线阅读,更多相关《冷冲模毕业设计汇总文档格式.docx(12页珍藏版)》请在冰豆网上搜索。
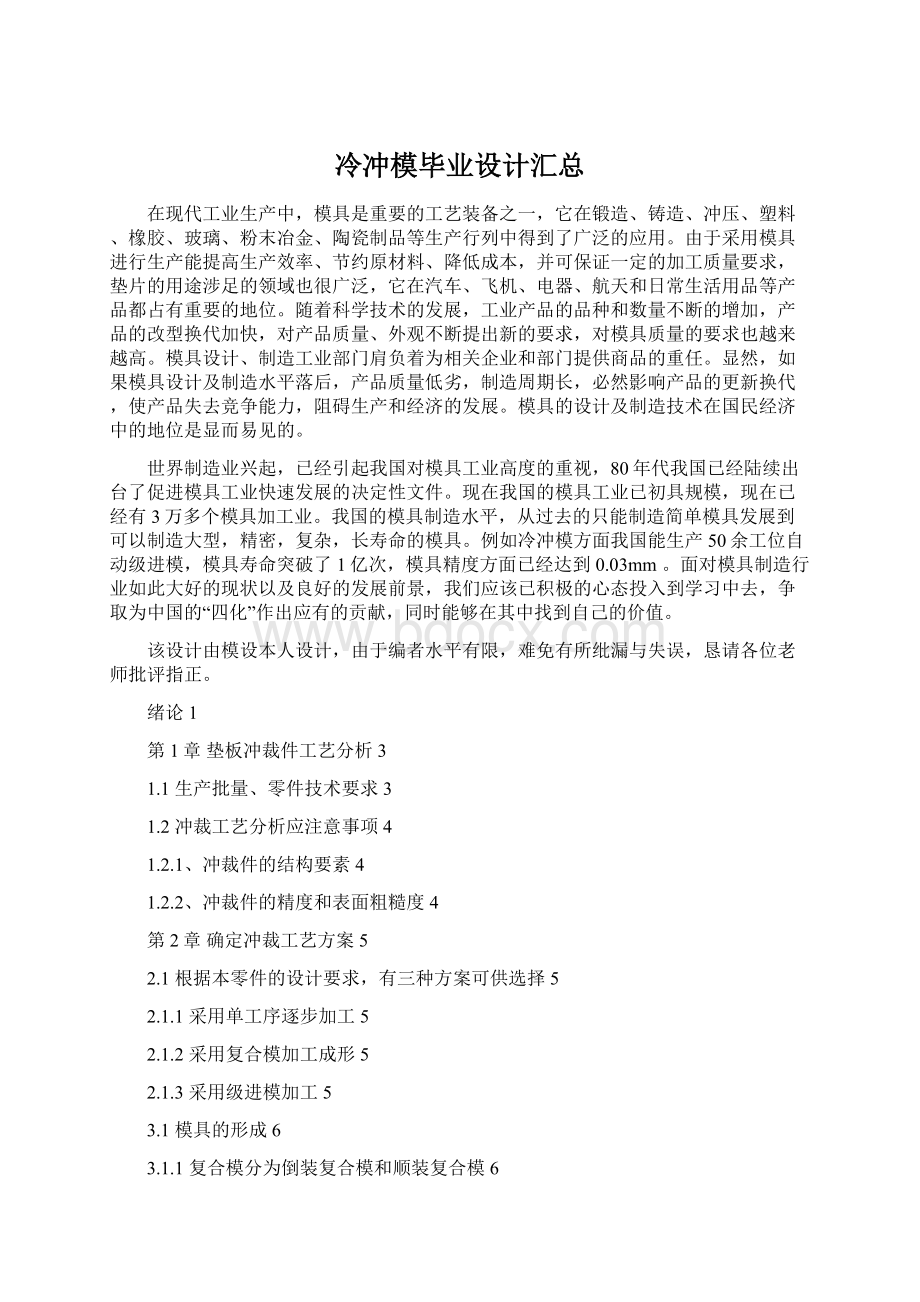
4.1.3步距的计算10
4.1.4材料利用率10
4.2冲压力的计算、初步选取压力机的吨位11
4.2.1冲压力的计算11
4.2.2初步选取压力机的吨位12
4.3计算模具压力中心13
4.4计算凸、凹模刃口尺寸,并确定其制造公差13
4.5估算凹模外形尺寸、以便选择标准组合14
4.6弹性元件的选取与计算15
4.6.1弹性元件的选取15
4.6.2卸料螺钉及装置16
4.6.3卸料螺钉的设置形式16
第5章模具的主要零部件设计18
5.1凸模结构设计18
5.2垫板的设计18
5.3紧固件19
5.4凸缘模柄19
第6章压力机校核20
6.1冲裁模模具闭合高度的校核20
6.2工作台面的校核20
总结21
参考文献22
绪论
第1章垫板冲裁件工艺分析
1.1生产批量、零件技术要求
材料Q235、厚度t=1mm;
设计要求:
精度等级IT14、大批量生产冲裁件。
图1.1
1.2冲裁工艺分析应注意事项
1.2.1、冲裁件的结构要素
冲裁件的形状应力求简单、规则,以便节省原材料,减少工序数目,提高模具寿命,降低工件成本。
(1)、冲裁件内、外形转角处应避免尖锐的转角,应当有适合的圆角。
(2)、冲裁件上应尽量避免窄长的悬臂和凹槽。
(3)、冲裁件上孔与控之间、控到零件边缘的距离,受模具强度和制件质量的限制,其值不能太小,一般要求≧2t。
(4)、冲裁件端部带圆弧时,当采用有搭边落料成形时,应取R=B/2。
(5)、因受凸模强度和稳定性的限制,冲裁件的孔不能太小。
用自由凸模和带护套的凸模所能冲制的最小孔径。
1.2.2、冲裁件的精度和表面粗糙度
(1)、普通冲裁件内外形尺寸的经济精度一般不高于IT11级,落料件精度最好低于IT10级,冲孔件最好低于IT9级,所以本设计精度选IT13级;
(2)、因为本次设计材料厚度为0.8㎜,所以根据课本表2-7,选表面粗糙度Ra为3.2。
第2章确定冲裁工艺方案
2.1根据本零件的设计要求,有三种方案可供选择
2.1.1采用单工序逐步加工
(1)、冲孔→落料单工序模,
(2)、落料→冲孔单工序模;
方案优点:
由于采用单工序模,模具制造简单,维修方便,生产率低,工件精度低,不适合大批量生产。
2.1.2采用复合模加工成形
生产率高,工件精度高,但模具制造较复杂,调整维修较麻烦,使用寿命低。
因为本次设计的复合模能在压力机一次行程内,完成冲孔落料等工序,在完成这些工序的过程中无需进给移动。
2.1.3采用级进模加
工
方案的优缺点:
级进模具有操作安全的显著特点,模具强度较高,寿命较长。
使用级进模便于冲压生产自动化,可以采用高速压力机生产。
级进模较难保证内、外形相对位置的一致性。
但级进模轮廓尺寸较大,制造复杂,成本较高,一般适用于大批量生产小型零件。
根据本零件的设计要求,以及各方案的特点决定采用第2种方案比较合理。
第3章选择模具的结构形式
3.1模具的形成
3.1.1复合模分为倒装复合模和顺装复合模
(1)、落料凹模装在下模时称为顺装复合模。
特点是工件和冲孔废料都将落在凹模表面上,必须加以清除后才能进行下一次冲裁,因此操作不方便,也不安全,对多孔工件不宜采用,但冲出的工件表面比较平直。
(2)、落料凹模装在上模时称为倒装复合模,特点为冲孔废料由冲孔凸模冲入凹模洞口中,积聚到一定数量由下模漏料孔排出,不必清除废料,操作方便,应用广泛,但工件表面平直度较差,凹凸模承受的张力较大,因此凹凸模的壁厚应严格控制,以免强度不足。
经分析后,此工件有四个小孔一个大孔,若采用顺装式复合模,操作很不方便,另外,此工件无较高的平直度要求,工件精度要求也很低,所以从操作方便,模具制造简单等方面考虑,决定采用倒装式复合模。
倒装复合模的凹凸模型孔内积存冲孔废料对型壁形成较大的张力。
因此倒装复合模的凹凸模最小壁厚b值不能太小,查表2—28得值符合要求,所以采用倒装式复合模符合要求。
3.2出件装置及方式
复合模出件选用逆出件,冲出凹模内的工件需由出件装置反向推出或顶出,倒装复合模的出件装置在上模,也可以采用橡胶块作为弹性元件,结构比较简单,调整也方便,但此弹性卸料只适于板料厚度小于0.3mm的薄板冲裁。
由于橡胶块产生的压料、推件力有限。
既要采用推出或顶出装置。
此材料选用弹压卸料式模具,出件方式可选用逆出件式模具,弹压卸料式模具又称之为敞开式模具,封闭式模具比较安全。
3.3模架的选取
3.3.1标准模架
标准模架有如下特点
(1)、标准模架是模具标准件中商品化程度最高的,有各种型号与规格可供选购。
(2)、出售的标准模架均由本专业厂成批制造,质量有保障,价格便宜。
(3)、虽然每个模具都是单件生产的,但是模架却可以批量生产。
为适应批量生产的需要,降低生产成本,提高模架质量,模座采用铸铁制造,普通模架的导柱与导套选用20号钢制造并经身碳淬火,硬度58~68HRC。
(4)、标准模架严格按冷冲模架技术条件GB2845—81制造与验收。
可见,标准模架质量要求很高的,设计模具时应尽量选用。
3.3.2非标准模架
下述两种情况下设计制造的模架属于非标准模架。
一种是标准模架的尺寸规格不能满足要求,企业需要自行设计制造的模架,例如多工位级进模所需要的特长模架。
设计折中模架时应掌握如下两条原则:
一是模座应采用低碳钢板制造而不用铸铁,因为单件生产,其外形不应采用铸铁模座的外形,应尽量简化,例如,采用矩形,但要求周边倒角。
二是导柱导套仍选购标准件,模具商店单独出售各种成套的导柱导套。
这种自制的非标准模架,当装配质量良好时,完全可以达到标准模架的质量标准。
另一种是导柱导套及模座等主要零件全由企业自行设计制造的模架,多为单件生产。
一般地讲,所生产的模架导向精度与使用寿命都不如标准模架。
有的企业设计模具时,模架要件件出图样,制造模具时,有要件件下料开始。
这是很落后的做法,不仅模具生产周期过长,而且模具质量也较差。
为了促使我国模具工业整体水平的
提高与兴旺发达,应当改变这种落后的作法,广泛应用专业厂生产的标准模架。
由于我国目前模具标准化与商品化还不尽完善,有些大型企业为了满足生产的需要,按企业标准或部门标准进行生产的小批量模架,供本企业使用,质量也可以保障,也能起到标准模架所起到的作用。
当属企业标准模架。
若采用中间导柱模架,则导柱对称分布,受力很均衡,滑动平稳,拔模简单、方便,但只可以一个方向送料。
若采用对角导柱模架,则受力不均衡、滑动不平稳,可纵向或横向送料。
若采用后侧导柱模架,则可三方向送料。
操作者视线被阻挡,结构比较紧凑,但模具受力不均衡,滑动不平稳。
根据相关资料决定跟设计采用中间导柱模架。
3.4定位装置
在落料模与复合模中,挡料的主要作用是保证纵向搭边值.活动挡料销通常安装在倒装落料模或倒装复合模的弹压卸料板上,凹模不开避让孔,因此不损害凹模强度,由此本次设计为倒装复合模且加工简单,所以可用活动挡料销来定位.
第4章工艺计算
4.1排样设计与计算
4.1.1排样方案
选用有搭边,为了补偿剪板误差与定位误差,增加条料的刚度,方便送料选用直排,因为这样既简便又不会浪费材料。
因为本次设计采用单工序的冲裁方案,即冲孔落料两道工序完成,落料的排样图采用有搭边的直排。
查表2-10a=1.5a1=1.8;
步距S=51.5,取B=54mm。
图4.1
4.1.2条料宽度的计算
选用有横搭边的排样,用挡料销定距,导料销导向,在一侧导板装有侧压装置的模具,虽无侧压,送料使条料始终接触基准导料板送料。
按其公式2-7:
△——查表2-12可得△=0.5
料宽B=[D+2a1+△]0-Δ
=[50+2×
1.8+0.5]0-0.4
=54.10-0.5mm
a1-横搭边,其值见表2-10;
D-工件横向最大尺寸(㎜);
C1-条料入端导料间隙,见表2-13;
△-剪板公差。
4.1.3步距的计算
S=L+a=50+1.5=51.5mm
4.1.4材料利用率
试中:
A-一个步距内工件的有效面积;
S-送料步距;
B-料宽。
A=50×
50-(10×
10-3.14×
5²
-π6²
-4π2²
=2315.22mm
为了验算利用率,,差指导书表4-1选用规格为1000×
1500的板料。
计算其利用率
A=(19*50+20*1.5-(29*50-30*1.8
=1473920mm
4.2冲压力的计算、初步选取压力机的吨位
4.2.1冲压力的计算
查附录表1Mpa
取k=1.3t=0.8mm
L=30×
4+2×
10π+12π+16π
=270.72mm
冲裁力:
F=KLt
=1.3×
270.72×
0.8×
250
=70387.2N
查公式1-12:
卸料力:
FQ1=K1F
=0.07×
70387.2
=4927.104N
顶件力:
FQ3=K3F
=0.14×
=9854.208N
弹压卸料逆出件时的总冲压力F0为:
F0=F+FQ1+FQ3
=70387.2+4927.104+9854.208
=85168.512N
≈85KN
4.2.2初步选取压力机的吨位
根据总冲压力所以查模具设计指导表4-33初选压力机J23-16型。
根据冲裁工艺和冲裁结构计算,压力机的公称压力Fg必须大于冲压计算的总压力,即Fg>
F0,所以取(J23—16)型号的压力机。
其主要参数:
公称压力/KN160KN
滑块行程/㎜80㎜
滑块行程次数/(次/min)100次/min
最大封闭高度/㎜220㎜
封闭高度调节量/㎜60㎜
滑块中心线至床身距离/㎜160㎜
立柱距离/㎜220㎜
工作尺寸/㎜前后300㎜
左右450㎜
工作台孔尺寸/㎜前后110㎜
左右220㎜
直径160㎜
工作台板厚度/㎜厚度60㎜
模柄孔尺寸/㎜直径30㎜
深度50㎜
可倾角(可倾式工作台压力机)/(°
30°
4.3计算模具压力中心
因为本次所设计加工的零件为对称矩形件,其加工方式为冲孔落料一步完成,且精度为IT13级,为了模具设计和模具制造方便,压力中心就设计与制件中心即:
凹模板中心
4.4计算凸、凹模刃口尺寸,并确定其制造公差
查中表1—4,Zmin=0.072mm,Zmax=0.104mm
查中表2—21,x=0.4
按刃口尺寸的计算原则可得:
A类——落料B类——冲孔C类——孔中心距
(1)落料件刃口尺寸
以凹模为基准:
(2)冲孔件刃口尺寸
凸模为基准:
3)工件孔中心距离
4.5估算凹模外形尺寸、以便选择标准组合
在凹模板的类型中,可分为圆型凹模板和矩形凹模板,圆型凹模板一般从圆棒料上直接截取,因圆棒料还处于供应状态下,存在晶粒粗大碳化物分布不均等严重缺陷,用这种材料制作凹模将严重影响模具寿命,因此,选用圆型凹模板不合理,而矩形凹模板一般是有圆棒料按照工艺锻造而成,且不方便锻成圆毛坯,所以凹模板取矩形比较合理。
因为压力中心O沿矩形L×
B宽度方向处于对称线上,而沿长方向不在对称线上。
可取O点沿厂度方向到短边的最大距离为L′的一半,则L′×
b即为修正后的凹模有效面积。
自矩形L′×
b向四周扩大一个允许的凹模壁厚C值,可得凹模外形尺寸L×
B,就能保证压力中心与凹模及模柄中心线重合。
查中表2-17得28~36mm
由于这些零件长宽相等,即压力中心可放在凹模中心,再者此工件料较薄,所以应取较小值C=28mm
L=50+2c=50+228=106mm=B
由于本次设计的工件是四边都相等的对称矩形,为了选用书上的标准模架。
所以根据本次设计的实际情况凹模板的周界尺寸应选用125100㎜。
因为采用逆出件式模具,可选用全直壁型孔。
4.6弹性元件的选取与计算
4.6.1弹性元件的选取
(1)、假设考虑了模具结构,决定用4个厚壁筒形的聚氯酯弹性体。
(2)、计算每个弹性体的预压力FY:
Fy=4927.104N/4=1231.776N
(3)、考虑橡胶块的工作压缩量较小,取预压缩率ξY=10%。
由表2-27查得单位压力Fq=1.1Mpa。
(4)、按式2-49计算弹性体的截面面积A:
A=FY/Fq=(1232/1.1)=1120mm²
(5)、卸料螺钉的选取
如果选用直径为10mm的卸料螺钉,选取弹性体穿卸料螺钉孔的直径d=Φ10.5mm,则弹性体的外径b可按下式求得:
为了保证足够的卸料力,以获得更平整的工件,需要加大压料力,可适当增大外径D。
(6)、橡胶高度的校核
当橡胶块用作较大压缩量的弹性元件时,如压料装置中的橡胶块需按下式进行相对高度的校核:
5H/D1.5
式中D——橡胶块的直径;
的H高度为20校验符合要求。
经查8——47。
4.6.2卸料螺钉及装置
卸料螺钉的特点:
模具国标规定了两种卸料螺钉,即圆柱头卸料螺钉
(GB2867.5——81)与圆柱头内六角卸料螺钉(GB2867.6——81)均具有如下特点:
(1)、螺纹长度虽短但与光杆段有台阶,可保证旋入弹压卸料板后不易松动。
(2)、螺纹长度是指光杆段长度且有公差要求,便于保证弹压卸料板工作平面与凹模面平行。
(3)、螺钉材料为45钢且要求热处理硬度为35~40HRC,以便保证螺钉有足够的强度,能承受卸料过程中反复作用的拉应力。
普通螺钉具备上述特点,因此应选用标准卸料螺钉。
因凸模经刃磨后,在重新安装弹压卸料时,在螺钉头部应加垫圈,其厚度为刃磨量,特别是橡胶喀为弹压卸料元件时更应注意这一点,以免预压量过大损害压力机。
4.6.3卸料螺钉的设置形式
根据设计的要求及其采用一般形式为沉孔形。
(1)、卸料螺钉长度的确定:
L=h1+h2+h3+h0(㎜)
=16+6+35+21
=78
H1——凸凹模固定板的厚度
H2——垫板的厚度
H3——下模座的厚度
H0——预压后弹性元件的高度;
(2)、卸料螺钉在下模座深度的计算
h1=h2+1+1+0.8
=8+2.8
=10.8mm
H2——卸料螺钉头部的高度
第5章模具的主要零部件设计5.1凸模结构设计鉴于此模具结构,根据零件形状确定凸模结构如下:
因为材料厚度t=0.8㎜,取1㎜;
打杆运动距离取5所以凸模长度为50㎜。
冲孔Φ12凸模:
图5.1冲孔Φ4凸模:
图5.25.2垫板的设计在凸模固定板与上模座之间加一块淬硬的垫板,可避免硬度较低的模座因局部受凸模较大的冲击压力而出现凹陷;
致使凸模松动。
有些模具在凹模与下模座之间也加垫板,目的为了提高模具的使用寿命。
垫板的平面形状尺寸与固定板相同,其厚度一般取6~10㎜,如果结构学要,例如在用螺钉吊装凸模时,为在垫板上加工吊装螺钉的沉孔,可适当增大垫板的厚度。
在垫板上穿过连接螺钉、卸料螺钉和定位销处要钻通孔,其直径比相应件的直径增大0.5~1㎜,应注意,穿销孔是在预装模具时调整好冲裁间隙后,连同模座和固定板一起经钻孔,铰孔加工出来的,垫板淬火变形后难以打入销钉。
如果模座是用钢板制造的,当凸模截面卖弄地不太小时,可以省去垫板。
5.3紧固件冲模上的紧固件包括连接螺钉和定位销钉,受力较大的连接螺钉一般都采用内六角螺钉,其特点是用45钢制造,并淬火达35~40HRC,因此可承受较大的拉应力,受力不大的小螺钉可以采用普通圆柱头螺钉,但一般不用半球头或沉头螺钉,前者一字槽容易拧坏,后者装配时不便调整,定位销采用普通圆柱销,可以承受一定的切应力。
5.4凸缘模柄在上模座加工出容纳模柄大凸缘的沉孔,与凸缘为H7/h6配合,并用3个或4个内六角螺钉进行固定。
由于沉孔底面的表面粗糙度较差;
与上模座的平行度也较差,所以装配后模柄的垂直度远不如压入式模柄。
因此在能应用压入式模柄时,不应采用凸缘模柄。
折中木笔国内的优点在于凸缘的厚度一般不到模座厚度的一半,模座凸缘以下部分仍可加工出型孔,以便容纳推件装置的顶板,采用螺纹模柄的小型模具也可以这样应用,但螺纹连接的长度要比上模座厚度小一些。
第6章压力机校核6.1冲裁模模具闭合高度的校核压力机的装模高度必须符合模具闭合高度的要求,即Hmax-5㎜≥Hm≥Hmin+10㎜190-5㎜≥Hm≥160+10㎜185㎜≥Hm≥170㎜式中:
Hmax、Hmin—分别为压力机的最大、最小装模高度(㎜);
Hm—模具闭合高度
所选用的压力机闭合高度为185符合其闭合高度的要求。
6.2工作台面的校核由于我们所选用的压力机的长宽为200×
160mm,其工作台面的工作尺寸为前后300㎜,左右450㎜,符合其工作台面的要求。
总结通过本次设计使我受益匪浅,我不但认识到自己专业知识严重缺乏,而且还认识到自己缺乏实际工作经验和设计经验。
在当今工业生产中模具是最重要的工艺装备之一,它在锻造、铸造、冲压、塑料等各行各业的生产生产中得到了广泛的应用。
由于采用模具进行生产能提高生产效率、节约原材料,降低成本,并可保证一定的加工质量、要求和精度等重要方面。
尽管我国的模具制造行业这些年来发展较快,模具的设计和制造水平也越来越高,但和国外发达国家相比,仍存在着很大的差距。
由于制造、技术落后,造成了模具供不应求的状况,还不能适应国民经济发展的需要,严重影响工业产品品种的发展和质量的提高。
通过设计过程中,我不但更深一层次掌握了模具设计的步骤、方法,更进一步掌握了一些关于模具设计的相关资料,在翻阅了很多资料的过程中,使自己深深认识到模具设计是一门高精密化、高效益的技术,但自己在设计过程中由于没有从事相关工作的经验和设计经验。
所以存在着很多问题,但通过在指导老师耐心地指导和讲述自己错误的过程中,使自己的错误得到了及时的纠正,本人再次感谢自己的指导老师,因为她使自己更清楚认识到自己的不足和知识的严重缺乏,还有她对待自己的学生一丝不苟的敬业精神,深深得感动了自己,她将深深地影响了我以后的
职业生涯。
我会在以后的工作中、生活中更好地发挥自己的所长来回报自己的母校和栽培我的老师,也要虚心的向他人学习,来弥补自己的欠缺,我坚信自己一定会成功。
参考文献[1][2][3][4][5][6][7][8][9]钟毓斌主编.冲压工艺与模具设计.北京:
机械工业出版社,2006史铁梁主编.模具设计指导.北京:
机械工业出版社,2006郝滨海主编.冲压模具简明设计手册.北京:
化学工业出版社,2004许发樾主编.冲模设计应用实例.北京:
机械工业出版社,1999孙凤勤主编.冲压与塑压设备.北京:
机械工业出版社,2005周玲主编.冲模设计实例详解.北京:
化学工业出版社,2000王芳主编.冷冲压模具设计指导.北京:
机械工业出版社,1999马正元主编.几何量精度设计与检测.北京:
机械工业出版社,2005杨占尧主编.冲压模具图册.北京:
高等教育出版社,2008