混炼车间操作与安全规程文档格式.docx
《混炼车间操作与安全规程文档格式.docx》由会员分享,可在线阅读,更多相关《混炼车间操作与安全规程文档格式.docx(13页珍藏版)》请在冰豆网上搜索。
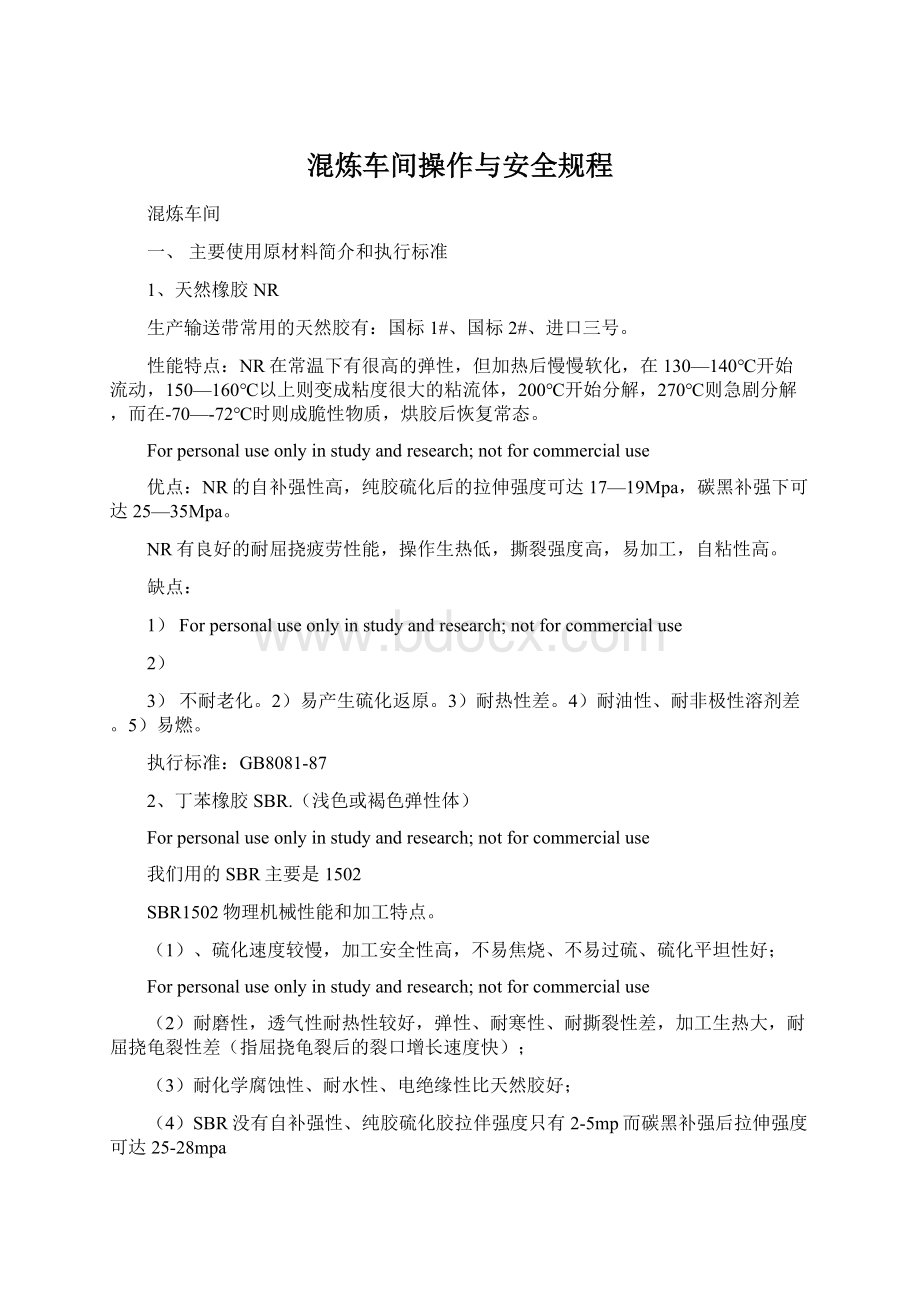
硬质橡胶30~50份。
在输送带中应用:
NR一般应用2.5份
SBR一般应用1.5~2.5份
GB/T2449-1992
8、促进剂M(浅黄色粉末,味极苦)
临界温度低(125℃),硫化速度快,焦烧时间中等。
配有碱性炉黑时有发生焦烧的危险,是天然橡胶的塑解剂。
混炼易分散。
作第一促进剂1~1.5份
作第二促进剂0.2~0.5份
HG11407-1989
9、促进剂DM(白色或浅黄色粉末味略苦)
临界温度130℃,硫速较M稍慢,焦烧时间较长,充模性好,易分散。
一般0.5~2份。
M和DM在配合的硫化胶中综合性能较好,有较高的拉伸强度和扯断伸长率,中等的定伸应力和硬度,良好的耐磨性和耐老化性及较小的压缩永久变型。
GB/T11408-1989
11、促进剂TMTD(白色粉末,飞扬时有呛鼻气味)
临界温度低100℃,
作促进剂时,易焦烧,硫速快,硫化平坦性差,用量大易发生过硫和早期硫化。
(硫化温度应在125~135℃之间)
作硫化剂时,具有焦烧倾向小,硫化平坦性好,硫化胶有极好的耐热老化性,生热小压缩永久变形小的特点。
但硫化胶拉伸强度高。
定伸应力偏低,抗屈挠疲劳性差,易喷霜。
在NR中作副促进剂时(0.05~0.1)
在合成胶中作副促进剂时(0.2~0.5)。
HG/T2334-1992
12、氧化锌ZnO(无毒、无味、白色细粉状的两性氧化物)
间接法ZnO纯度高,粒子细,活性高。
直接法ZnO纯度稍低,粒子较粗,重金属杂质含量较大,活性差。
氧化锌作活性剂外,还具有补强着色和增加胶料导热的作用。
一般用量2.5-5份
在耐热带中过10份。
GB3494-1983
13、硬脂酸stA.(白色或微黄色颗粒或块状物质稍有脂肪味,无
毒。
)
工业品纯度只有80-90%,其余成分为油酸或软脂酸,stA除作活化剂外,还有软化增塑的作用,有助于炭黑的分散。
用量过多会喷出制品表面并迟延胶料硫化。
0.5~2份
GB9103-1988
14、炭黑N330HAF
高补强型炭黑。
耐磨性比N220稍差,应用广泛对NR的补强效果较好。
在输送带中主要用于盖胶、擦贴胶。
GB/T3778-1994
15、炭黑N220ISAF
高补强型炉黑,耐磨性介于SAF和HAF之间,能赋予胶料以良好的拉伸强度。
对丁苯橡胶补强尤佳。
在输送带中为主要补强材料:
主用于一般用途和耐热带盖胶。
19、防老剂RD___抑制氧化,热老化及天候老化,对屈挠龟裂效果较差。
22、石蜡___主要能防止制品的臭氧龟裂。
用多影响粘合。
23、松焦油___有力于配合剂的分散增加粘性,可提高制品耐寒性,用多迟延硫化。
24、古马隆__软化增塑,有助于炭黑分散,增加粘合具有一定的补强性,用多屈挠性下降。
二、生产用主要设备及原理
A、密炼机工作原理:
胶料在密炼室内两个相对回转的转子间隙中和转子与密炼室壁之间的间隙中,受到转子和上项栓不断变化的剪切和挤压作用。
促使胶料产生剪切变形而进行捏炼。
转子比速一般在:
1.1-1.18之间
上项栓压力范围:
2-7kg/cm
工作容量:
G=p.v.a
G容量kgp胶料比重kg./升
V密炼机容量升a设备利用系数,一般取值0.8-0.9
XHM/XSNX代表橡胶,H代表混炼,M代表密炼机,S代表塑料,N代表捏炼机。
B.开炼机工作原理。
胶料在与辊筒磨擦力的作用下被拉入两辊筒之间的间隙,胶料受到强烈的挤压和剪切,从而达到加工胶料的目的。
两辊筒的速比一般为:
1.2-1.3
X(S)K-400X代表橡胶类,K代表开放式。
400表示辊筒直径400mm。
三、生产中重要术语和名词解释
1、塑炼------借肋机械功或热能使橡胶软化为具有一定可塑性的均匀的工艺过程称之为塑炼。
2、混炼------在密炼机或开炼机将各种配合剂均匀地加入具有一定塑性的生胶中的工艺过程称为混炼;
(经混炼制成的胶料称为混炼胶)
3、结合橡胶-------混炼时,橡胶分子能与活性填料(主要是炭黑)粒子相结合生成一种不溶液于橡胶良溶剂的产物,称为结合橡胶。
结合橡胶的多少可用胶料的拉伸强度测量。
4、硫化活性剂-------凡能增加促进剂活性,提高硫化速度和硫化效率,改善硫化胶性能的化学物质都称为硫化活性剂。
5、防老剂------凡能延缓或抑制橡胶老化过程,延长橡胶及其制品的贮存期及使用寿命的物质称为防老剂。
6、补强剂------凡与橡胶混合能提高制品的机械强度、硬度、耐磨性、耐撕裂、定伸、拉伸强度的物质称为补强剂。
7、软化剂------在橡胶工业中将那些来源于天然物质常用来改善非极性橡胶加工性能的操作助剂称为软化剂。
8、增塑剂------将那些极性较大多用来改善极性橡胶的加工性能和耐寒性能的合成物质称为增塑剂。
9、硫化剂------在一定条件下能使橡胶发生硫化(交联)的化学物质称为硫化剂。
10、填充剂------在配合中起增加胶料容积,节省橡胶、降低成本的
作用的称为填充剂。
11、促进剂------凡能缩短硫化时间,降低硫化速度,减少硫化剂用量,提高和改善硫化胶物理机械性能和化学稳定性的化学物质,统称为硫化促进剂。
12热可塑性------是指生胶随温度升高而变软,随温度降低而变硬的特性,通常也称作假可塑性(如此塑炼就是假塑炼)
13停放的目的------主要是有利配合剂在胶料中的继续扩散,提高分散的均匀性,使橡胶和碳黑间进一步相互作用,生成更多的结合橡胶,提高补强效果。
14冷却的目的------防止胶料发生焦烧现象和停放中的粘连。
15压延效应-----胶片压延后出现纵横方向物理机械性能的各向异性现象叫压延效应。
(产生压延效应后,明显的出现顺压延方向胶料的拉伸强度大、扯断伸长率小、收缩率大;
而垂直于压延方向胶料的拉伸强度小、扯断伸长率大、收缩率小橡胶分子定向排序的结果。
16临界温度-------是指促进剂对硫化过程起开始迅速起作用的温度(临界温度并非固定不变,它随加热时间及其它条件的变化而变化)
17老化------橡胶及其制品在加工制造,长期贮存和使用过程中,逐渐产生度软发粘,变硬发脆或龟表裂,使物理机械性能变坏以致失去弹性而丧失使用价值,这种现象称为橡胶老化。
四、炼胶车间设备异常情况判断
1)密炼机齿轮箱有噪音
a、应检查润滑油液面低于标准;
b、检查或细听是否有轴承损坏的迹象。
2)密炼机翻斗翻不出或外翻时中途停止
应查看翻斗涡轮箱
3)皮带处噪音大或设备在正常时间不能运转
检查皮带是否伸长过大松动;
4)密炼机有电源但不能启动
应检查气泵是否启动或压砣是否升起
5)开炼机噪音大
a、检查大小齿轮油箱是否缺油;
b、检查电机、变速箱、主机地脚螺丝是否松动。
6)开炼机瓦胎处手背试温度
a、比体温略高些属于正常;
b、烫手,不能承受,已经断油,须立即停车。
查看轴瓦、油路、油泵或其他润滑油。
7)提升斗上行时跳动,则链条异常。
8)18寸开炼机启动时,电机连续导相几次,应检查磁力闸是否吸牢。
9)各轴承部位如有噪音或温度异常高,应停机检查;
10)电机声音细而响亮,应立即停机检查是否缺相电
11)电机温度过高
a、应检查是否风扇正常工作;
b、电压是否太低;
c、是否缺相电。
12)车间内有烧焦的气味
所有机车全部停机,检查电箱和电机电线
13)倒胶架来回运转不正常
槽内缺油或滑动铜块磨损严重。
五、炼胶工上岗资格技能要求
A应知:
1)炼胶工序各岗位工艺规程、作业指导书要求、岗位责任及安全操作制度,尤其安全制被设施。
2)日常生产的各型号半成品物理机械性能指标;
3)各型号半成品混炼胶质量对下工序内在、外观质量的影响和实际使用关系;
4)塑炼、混炼的基本理论知识;
5)本岗位密炼机容量计算方法;
6)输送带用主要原材料基本性能和应用知识;
7)本岗位炼胶设备构造基本原理及维护保养方法。
8)本工序的用电常识,防火重点,主要岗位。
9)各型号规格的擦贴胶、盖胶标识的重要性
B、应会:
1)能熟练按作业指导书操作,快检质量符合技术指标;
2)能掌握不同生胶品秤单用式并用炼胶操作要领及特殊加料顺序的执行方法。
3)能对自己生产的混炼胶质量作出分析判断,发生焦烧或有杂质、配合剂颗粒的原因,并能及时采取纠正预防措施;
4)能识别本岗位常用原料的品种牌号、执行标准、外观质量的好坏。
5)能鉴别机械的运转是否正常,及时发现事故隐患。
6)能对混炼胶质量问题因机械的原因、原料工艺的完因作出正确分析估计。
六、混炼车间安全生产管理规定
A烘胶安全操作规程
1)检查搬运车辆的完好,搬运时注意脚下和通道有无障碍物。
2)生胶垛高不得超过十层,胶块码放整齐。
3)搬运时不得超载、过高运送。
4)烘胶温度控制在工艺规定范围内,不准烘干其它物品。
5)严禁将火柴、打火机等火种带入烘胶室。
6)烘胶室内蒸汽管道要有护罩,防止烫伤或橡胶烫流。
7)车间无人时,照明灯必须关闭。
灯下不准站人。
8)烘胶室旁必须有相应的防火器材。
B切胶安全操作规程
1)操作前认真检查油箱油位、行程开关及液压系统、切刀。
2)切胶时精力集中,严防胶块弹出伤人。
3)禁止切冻、硬生胶。
4)不准切含大量钢丝的胶料或杂物。
5)严禁手臂伸过切刀拉取生胶或用脚踩踏胶块。
6)切小块天然或合成胶时严禁面对面操作。
7)限位开关故障或油顶漏油时,不准使用。
8)停用时,切刀应放到底,切断电源,整理现场。
9)切胶前生胶码放整齐,不准堵住通道。
C配大料工安全操作规程
1)割开带子时防止划伤自己。
2)倒取粉剂时轻拿轻放,以免飞扬伤眼或呛鼻子。
3)开松焦油阀门时,倒北边去开,防止烫伤。
4)衣服穿着达三紧,以免被大料簸箕挂住。
5)各种标准件料只能逐件卸车码放,严禁倒歪。
6)秤上放料要轻放,以免砸坏磅秤。
7)配料处保持道路畅通,严禁铺摊一地。
8)切好生胶上架码放,不用的整件,下班退库
9)合成擦胶时,胶条运输不可落满地,用袋子或少抱。
10)配料中发现异物应及时向主任报告(尤其回轧)。
11)出库取料,严格执行《搬运作业指导书》
D捣胶工安全操作规程
1)启动提升机倒料时,必须等捏炼机卸料斗回位后才能启动。
2)卸料前,开炼机必须已运转正常。
3)料斗内胶料如不能卸下,严禁抓、扯,以免被胶压住手臂,应将提升斗复位,调整处理后重新卸料。
4)料斗内胶料倒完后,必须将料斗下放复位,严禁提升机料斗长时间在空中停放,以免发生危险。
5)严禁在卸料处通过或传递物品。
6)严禁在开炼下用手去扒卸料斗内胶料。
7)启动前检查两侧急停开关的完好和灵敏性。
8)22寸开炼机启动工作时,严禁单人操作
9)割出小卷应拿住一端纵放入捣胶机内,严禁横放。
10)加硫磺和T后严禁割刀,以免伤眼。
11)捣胶工上岗必须先检查三紧(两手腕、腰),合格方可上岗。
12)捣胶时防止胶料坠落后将料盘顶出碰脚。
13)在胶料入捣胶架时,身体应尽力往后倾斜。
14)捣胶完毕后下胶卷时,严禁身体靠仍抱着胶的辊筒,应两手全力抓胶,然后抱下。
E出片、冷却、卷取、架起安全操作规程
1)上岗前检查三紧(手腕处、腰),合格方可上岗。
2)严禁在冷却机风扇处停留、倚靠,以免将衣服吸入,发生危险。
3)盖胶进入冷却带网中,发生褶皱,可用木棒展开,或停机处理,严禁用手去展,以免挂伤手臂。
4)卷取前必须先将布轴垫布布置好,缓慢卷取,严禁“”作业。
5)卸下盖胶卷时,小车必须有专人扶按,防止翻车伤人。
6)架盖胶卷时,二人要相互呼应,防止挤手或碰伤腿脚。
7)卷取前穿架布轴时,二人要配合小心,防止碰伤或挤手。
8)从22寸开炼倒移至出片机时,胶卷不少于4卷,严禁大卷上胶
9)上胶前,18寸开炼机必须已运转正常
10)割刀时,出片人员应注意割刀方向是否有人。
11)出片后,刀架位置在支架上,以防砸伤或碰脚。
12)出片时如出现架胶现象,严禁用手直接按胶。
13)出片时,严禁一手投胶,一手在辊下按胶。
F投料工安全操作规程
1)端起大簸箕时防止碰到其它物品。
2)上捏炼机台时,要站稳慢慢来,防止滑倒或撒落粉剂。
3)倒料时,注意手臂防止碰伤。
4)投生胶时,不能连续投入,等第一块捣碎,再投第二块。
5)严禁投、手伸进密炼室。
6)关闭投料门是,防止挤手或笤帚。
7)投入粉剂后下降压砣时,关上投料门,防止粉料溢出伤眼、呛鼻子。
8)合成擦胶时,严禁将袋子同胶倒入开炼机。
G开炼安全操作规程
1)不准到卸料斗下站立等卸料。
2)卸料斗回翻时严禁抢拿未卸净胶料。
3)卸料斗归位后方可抬料。
4)衣服达到三紧才可上岗。
5)衣服严禁倚靠辊筒或坐在料盘上休息。
6)打包过薄时,注意调节冷却水,防止胶料温度过高烫伤。
7)回轧盖胶发现异物应停机处理,严禁运转中撕扯、抢拿
8)合成擦胶中的长线头或钢丝应提前捡出,不要在开炼中强拉硬扯,以免勒伤手臂。
9)擦贴胶下片冷却时,轻轻放入隔离水池。
七、本工序质量缺陷、原因及纠正预防措施
密
炼
不
均
1、密炼机浮砣,压力表定的额定压力小或气路不通畅;
2、单车容量大,超过密炼室允许容量;
3、密炼温度低。
4、混炼时间短。
1、检查电磁伐和气路或调整压力开关;
2、从新核算配方容量按标准公式计算投料;
3、提高密炼室温度;
4、增加密炼时间。
熟
胶
1、密炼室温度过高。
2、密炼时间过长。
3、帘线胶用量比例过大
4、误加入硫磺或双T等硫化剂。
1、降温至工艺要求。
2、缩短密炼时间。
3、与技术人员联系,调整配方。
4、加强管理,强调工艺。
密炼
出现
粉胶
1、车容量小。
2、密炼时间不足。
3、密炼温度过低
4、上顶栓压力小。
1、与技术人员联系调整配方。
2、增加密炼时间。
3、增加密炼温度。
4、检查、调整压力。
混
时
脱
辊
1、包辊胶含胶量低;
2、胶料粘性太差
3、填充剂量太大;
4、松放辊距太快过大;
5、填充剂投料时一次加入导致;
6、胶料过硬(包括再生胶硬度伸长率小;
7、生胶自身特性(如顺丁、三元已丙)
8、油脂软化剂放的太晚
9、胶温过高。
1、调整含胶率和生胶总量;
2、适当增加古马龙、沥青的用量;
3、调整大料配比份数;
4、松放辊距不易过急;
5、填料如炭黑钙粉要分批缓慢加入;
6、增加软化剂的量,调整使用再生胶或塑炼生胶;
7、用其它生胶改善包辊性;
8、软化剂必须同填充剂同时加入;
9、控制密炼温度,降低室温。
针孔、气泡
1、胶温、过高过低
2、配合剂含水太多
3、供胶卷过松、窝藏空气
4、出片时积胶量过多
5、古马龙没化开
6、含胶率高,透气性差
1、严格控制胶温、辊温
2、对含水过多的配合剂进行干燥处理
3、下片厚度不能太薄
4、按工艺要求调节积胶量
5、提高温度并在配料前粉碎古马龙
6、粗炼排气
杂质、色斑、污点
1、原材料不纯
2、设备打扫不干净
加强原材质量管理,清洗设备
厚度、宽度
规格不
符合要求
1、热炼温度波动或热炼不充分
2、胶料温度波动
3、胶料可塑度不一致
4、卷取松紧不一致
5、调距未调准
6、开炼振动或轴承不良
7、出片时积胶调节不当
1、改进热炼条件
2、控制好辊温
3、加强胶料可塑度控制,固定反回胶掺用比例
4、调整盖胶卷取速度
5、调节辊距,力求恒定
6、改进设备防振性能
7、调节好积胶量
表面粗糙
1、热炼不足,胶料或辊温过低
2、热炼不均
3、胶料自硫
1、注意胶料保温,提高辊温
2、改进热炼。
控制好辊温
3、降低热炼温度及压延机辊温
混炼
熟胶
1、密炼室或开炼机温度过高;
2、配合剂用量不当;
3、在密炼室加了硫化剂;
4、多次回炼导致。
1、调节冷却水,降低温度;
2、调整配方;
3、严格执行工艺,必须在开炼上加硫化剂。
4、注意混炼胶停放时间,回轧时降低密炼或开炼温度。
九、本工序产品或半成品指标
D炼胶车间产品或半成品性能指标。
1天然橡胶塑炼胶要求:
塑炼段数
一段塑炼胶
二段塑炼胶
三段塑炼胶
可塑度
0.35±
0.03
0.45±
0.52±
仅供个人用于学习、研究;
不得用于商业用途。
notforcommercialuse.
Nurfü
rdenpersö
nlichenfü
rStudien,Forschung,zukommerziellenZweckenverwendetwerden.
Pourl'
é
tudeetlarechercheuniquementà
desfinspersonnelles;
pasà
desfinscommerciales.
толькодлялюдей,которыеиспользуютсядляобучения,исследованийинедолжныиспользоватьсявкоммерческихцелях.
以下无正文