电镀工艺 挂镀与滚镀Word格式.docx
《电镀工艺 挂镀与滚镀Word格式.docx》由会员分享,可在线阅读,更多相关《电镀工艺 挂镀与滚镀Word格式.docx(10页珍藏版)》请在冰豆网上搜索。
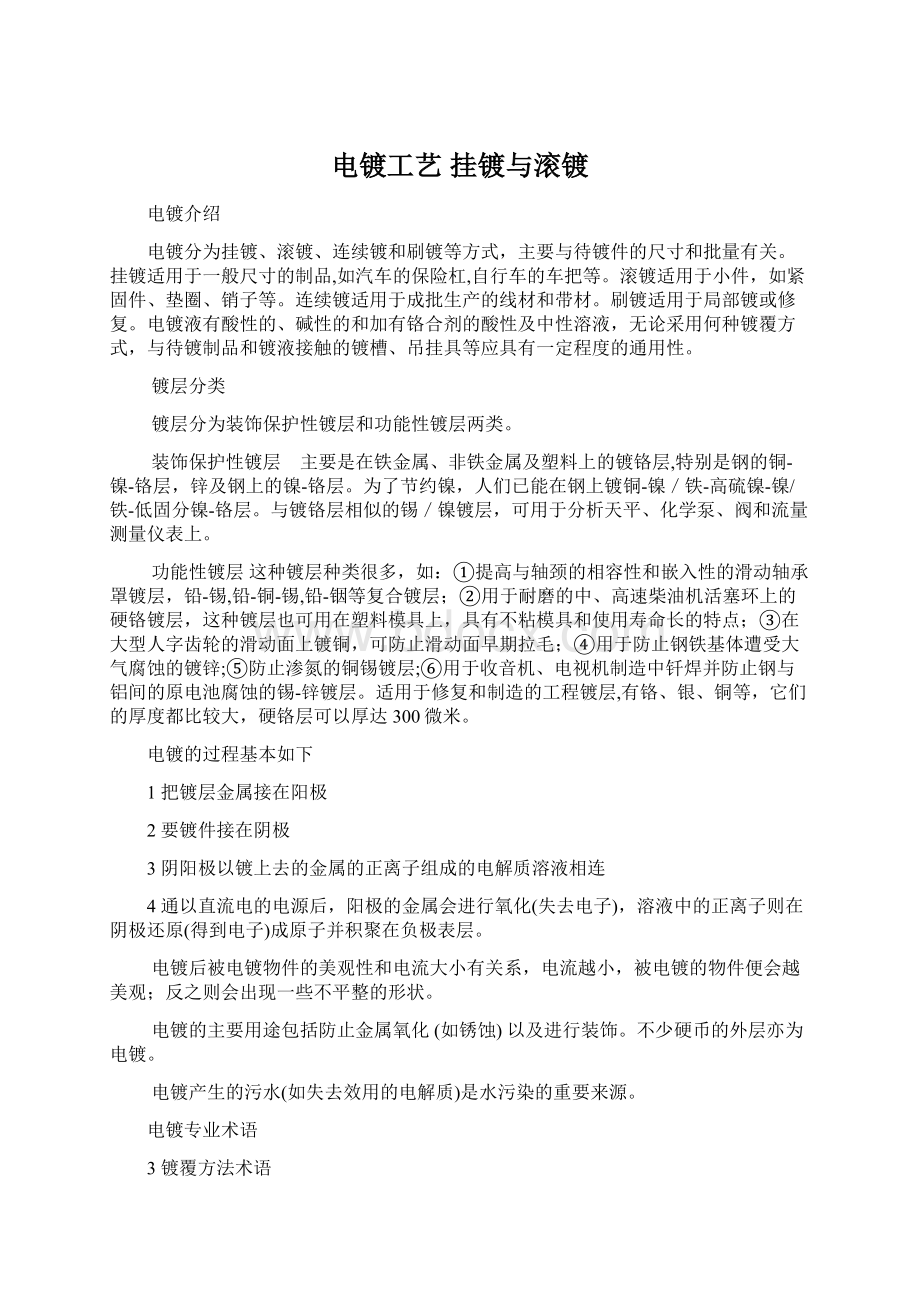
反之则会出现一些不平整的形状。
电镀的主要用途包括防止金属氧化(如锈蚀)以及进行装饰。
不少硬币的外层亦为电镀。
电镀产生的污水(如失去效用的电解质)是水污染的重要来源。
电镀专业术语
3镀覆方法术语
3.1化学钝化
将制件放在含有氧化剂的溶液中处理,使表面形成一层很薄的钝态保护膜的过程。
3.2化学氧化
通过化学处理使金属表面形成氧化膜的过程。
3.3电化学氧化
在一定电解液中以金属制件为阳极,经电解,于制件表面形成一层具有防护性,装饰性或其它功能氧化膜的过程。
3.4电镀
利用电解原理,使金属或合金沉积在制件表面,形成均匀、致密、结合力良好的金属层的过程。
3.5转化膜
对金属进行化学或电化学处理所形成的含有该金属之化合物的表面膜层。
3.6钢铁发蓝(钢铁化学氧化)
将钢铁制件在空气中加热或浸入氧化性的溶液中,使之于表面形成通常为蓝(黑)色的薄氧化膜的过程。
3.7冲击电流
电流过程中通过的瞬时大电流。
3.8光亮电镀
在适当条件下,从镀槽中直接得到具有光泽镀层的电镀。
3.9合金电镀
在电流作用下,使两种或两种以上金属(也包括非金属元素)共沉积的过程。
3.10多层电镀
在同一基体上先后沉积上几层性质或材料不同的金属层的电镀。
3.11冲击镀
在特定的溶液中以高的电流密度,短时间电沉积出金属薄层,以改善随后沉积镀层与基体间结合力的方法。
3.12磷化
在钢铁制件表面上形成一层不溶解的磷酸盐保护膜的处理过程。
3.13热抗散
加热处理镀件,使基体金属和沉积金属(一种或多种)扩散形成合金的过程。
4镀前处理和镀后处理术语
4.1化学除油
在碱性溶液中借助皂化作用和乳化作用清除制件表面油污的过程。
4.2电解除油
在含碱溶液中,以制件作为阳极或阴极,在电流作用下,清除制件表面油污的过程。
4.3出光
在溶液中短时间浸泡,使金属形成光亮表面的过程。
4.4机械抛光
借助于高速旋转的抹有抛光膏的抛光轮,以提高金属制件表面光亮度的机械加工过程。
4.5有机溶剂除油
利用有机溶剂清除制件表面油污的过程。
4.6除氢
将金属制件在一定温度下加热处理或采用其它方法,以驱除在电镀生产过程中金属内部吸收氢的过程。
4.7退镀
将制件表面镀层退除的过程。
4.8弱浸蚀
电镀前,在一定组成溶液中除去金属制件表面极薄的氧化膜,并使表面活化的过程。
4.9强浸蚀
将金属制件浸在较高浓度和一定温度的浸蚀溶液中,以除去金属制件表面上氧化物和锈蚀物的过程。
4.10镀前处理
为使制件材质暴露出真实表面,消除内应力及其它特殊目的所需,除去油污、氧化物及内应力等种种前置技术处理。
4.11镀后处理
为使镀件增强防护性能,提高装饰性能及其它特殊目的而进行的(诸如钝化、热熔、封闭和除氢等)处理。
5材料和设备术语
5.1阳极袋
用棉布或化纤织物制成的套在阳极上,以防止阳极泥渣进入溶液用的袋子。
5.2光亮剂
为获得光亮镀层在电解液中所使用的添加剂。
5.3阻化剂
能够减缓化学反应或电化学反应速度的物质。
5.4表面活性剂
在添加量很低的情况下也能显著降低界面张力的物质。
5.5乳化剂
能降低互不相溶的液体间的界面张力,使之形成乳浊液的物质。
5.6络合剂
能与金属离子或含有金属离子的化合物结合而形成络合物的物质。
5.7绝缘层
涂于电极或挂具的某一部分,使该部位表面不导电的材料层。
5.8挂具(夹具)
用来悬挂零件,以便于将零件放于槽中进行电镀或其他处理的工具。
5.9润湿剂
能降低制件与溶液间的界面张力,使制件表面容易被润湿的物质。
5.10添加剂
在溶液中含有的能改进溶液电化学性能或改善镀层质量的少量添加物。
5.11缓冲剂
能够使溶液PH值在一定范围内维持基本恒定的物质。
5.12移动阴极
采用机械装置使被镀制件与极杠一起作周期性往复运动的阴极。
6测试和检验相关术语
6.1不连续水膜
通常用于表面被污染所引起的不均匀润湿性,使表面上的水膜变的不连续。
6.2孔隙率
单位面积上针kong的个数。
6.3针kong
从镀层表面直至底层覆盖层或基体金属的微小孔道,它是由于阴极表面上的某些点的电沉积过程受到障碍,使该处不能沉积镀层,而周围的镀层却不断加厚所造成。
6.4变色
由于腐蚀而引起的金属或镀层表面色泽的变化(如发暗、失色等)。
6.5结合力
镀层与基体材料结合的强度。
6.6起皮
镀层成片状脱离基体材料的现象。
6.7剥离
某些原因(例如不均匀的热膨胀或收缩)引起的表面镀层的破碎或脱落。
6.8桔皮
类似于桔皮波纹状的表面处理层。
6.9海绵状镀层
在电镀过程中形成的与基体材料结合不牢固的疏松多孔的沉积物。
6.10烧焦镀层
在过高电流下形成的颜色黑暗、粗糙、松散等质量不佳的沉积物,其中常含有氧化物或其他杂质。
6.11麻点
在电镀或腐蚀中,与金属表面上形成的小坑或小孔。
6.12粗糙
在电镀过程中,由于种种原因造成的镀层粗糙不光滑的现象。
6.13镀层钎焊性
镀层表面被熔融焊料润湿的能力。
滚镀介绍
一、概述
滚镀适用于受形状、大小等因素影响无法或不宜装挂的小零件的电镀,它与早期小零件电镀采用挂镀或篮筐镀的方式相比,节省了劳动力,提高了劳动生产效率,而且镀件表面质量也大大提高。
所以,滚镀的发明与应用在小零件电镀领域无疑有着非常积极的意义。
滚镀早在20世纪20年代就已经在工业上得到应用。
国内滚镀最早于20世纪50年代中后期出现在上海,机械化连续滚镀设备在20世纪60年代左右开始使用,但当时的设备仅仅能够手动控制,而大型全自动滚镀生产线大概从20世纪90年代开始才有较为广泛的应用。
目前,滚镀的产量约占整个电镀加工的50%左右,并涉及到镀锌、铜、镍、锡、铬、金、银及合金等几十个镀种。
滚镀已成为应用非常普遍且几乎与挂镀并驾齐驱的一种电镀加工方式。
2滚镀的概念
滚镀严格意义上讲叫做滚筒电镀。
它是将一定数量的小零件置于专用滚筒内、在滚动状态下以间接导电的方式使零件表面沉积上各种金属或合金镀层、以达到表面防护装饰及各种功能性目的的一种电镀加工方式。
典型的滚镀过程是这样的:
将经过镀前处理的小零件装进滚筒内,零件靠自身的重力作用将滚筒内的阴极导电装置紧紧压住,以保证零件受镀时所需的电流能够顺利地传输。
然后,滚筒以一定的速度按一定的方向旋转,零件在滚筒内受到旋转作用后不停地翻滚、跌落。
同时,主金属离子受到电场作用后在零件表面还原为金属镀层,滚筒外新鲜溶液连续不断地通过滚筒壁板上无数的小孔补充到滚筒内,而滚筒内的旧液及电镀过程中产生的氢气也通过这些小孔排出筒外。
二、滚镀的几个基本特征
1.滚镀是在滚筒内进行的
滚镀与小零件挂镀最大的不同在于它使用了滚筒,滚筒是承载着小零件在不停地翻滚的过程中受镀的一个盛料装置。
典型的滚筒呈六棱柱状,水平卧式放置。
滚筒壁板的一面开口,电镀时一定数量的小零件从开口处装进滚筒内,然后盖上滚筒门将开口封闭。
滚筒壁板上布满了许多小孔,电镀时零件与阳极间电流的导通、筒内外溶液的更新及废气的排出等都需要通过这些小孔。
滚筒内的阴极导电装置通过铜线或棒从滚筒两侧的中心轴孔内穿出,然后分别固定在滚筒左右墙板的导电搁脚上。
零件在滚筒内靠自身的重力作用与阴极导电装置自然连接。
小零件的滚镀就是在这样的装置内进行的。
滚筒的结构、尺寸、大小、转速、导电方式及开孔率等诸多因素均与滚镀的生产效率、镀层质量等有关。
所以,滚筒是整个滚镀技术研究的重点之一。
2.滚镀是小零件在不停地翻滚的过程中进行的
滚镀时,小零件在滚筒内并非静止不动的,而是要随着滚筒的旋转不停地翻滚。
这种翻滚具体到某一个零件的情况是:
一会儿被埋进整个堆积零件的内部,一会儿又翻到外表面。
这样周而复始,直到整个滚镀过程结束。
那么,为什么要使小零件在滚筒内不停地翻滚呢?
(1)、保证每个零件都能够均匀地受镀。
小零件在滚筒内是堆积在一起的,其中一部分零件分布在堆积体的内部,称为内层零件;
另一部分零件则分布在堆积体的外表面,称为表层零件(如图1所示)。
滚镀时,主金属离子实际只在表层零件的表面还原形成金属镀层,而内层零件由于受到表层零件的屏蔽、遮挡等影响只有电流通过,却几乎没有电化学反应发生。
所以,为了能够有机会受镀,内层零件就需要从堆积体的内部翻出变为表层零件。
而表层零件也不能长时间停留,电镀进行一会儿后,受到滚筒的旋转作用又变成了内层零件。
这样,小零件只有不停地翻滚,才能促使内层零件与表层零件不断地变化、转换,并最终保证每个零件都有均匀受镀的机会。
1-内层零件;
2-表层零件
图1内层零件与表层零件示意图
(2)、避免表层零件“烧黑”或“烧焦”。
小零件在滚筒内如果不翻滚而处于静止状态,那么使用很小的电流密度,就可能使表层零件附近的金属离子匮乏而产生“烧焦”现象。
尤其贴近滚筒壁板的表层零件,会使从孔眼处进入滚筒的电流受到阻碍,从而集中停留在零件上紧挨孔眼部位的狭小表面,造成该处镀层烧焦留下黑色眼点,即所谓的“滚筒眼子印”。
这时,小零件在滚筒内翻滚的作用,类似于挂镀的溶液搅拌或阴极移动。
挂镀时如果没有溶液搅拌或阴极移动的作用,则电流密度上限不易提高,镀层沉积速度也难于加快。
2.3滚镀时小零件所需的电流是以间接的方式进行传输的。
挂镀时,零件所需的电流由挂具直接传输,零件与挂具紧密接触,中间没有任何介质。
因此,挂镀的电流传输平稳,接触电阻小,各零件所获得的电流基本不因传输问题而有所不同。
但滚镀时,零件是整体压在滚筒内的阴极导电装置上的,与阴极导电装置直接相连的零件只有极少部分,而绝大部分只能通过堆积重叠的零件与阴极导通。
所以,滚筒内的阴极导电装置只能首先将电流输送给与自己直接接触的零件,然后才能由这些零件输送给其它零件,并在其它零件与零件之间一个一个地传输下去,这就是滚镀的间接导电方式。
这种间接导电方式无疑是滚镀的又一重要特征。
它由于主要靠零件与零件之间间接导电,而不是零件直接与阴极接触导电,所以,滚镀时零件的接触电阻较之挂镀相应增大。
三、滚镀的分类
1.概述
科学地划分滚镀的种类,应以滚镀所使用的滚筒的形状和轴向为主要依据。
滚筒形状是指滚筒的外形类似于何种器物,滚筒轴向是指滚筒旋转时转动轴方向与水平面呈现什么关系。
根据滚筒这两个方面的不同,将电镀生产中常见的滚镀方式划分为卧式滚镀、倾斜式滚镀和振动电镀等三大类。
2.卧式滚镀
卧式滚镀的滚筒形状为“竹筒”或“柱”状,使用时卧式放置。
滚筒轴向为水平方向,所以卧式滚镀也叫水平卧式滚镀。
生产中常见的六角形滚筒、镀铬滚筒、杆状(或辐条)滚筒、缝衣针滚筒等都属于卧式滚镀的范畴。
其中以六角形滚筒应用最广泛。
典型的卧式滚筒结构如图1所示。
2.1滚筒横截面形状
卧式滚筒的横截面形状有六角形、八角形和圆形等。
采用六角形滚筒,零件在翻动时跌落的幅度大,零件的混合较充分,所以镀层厚度波动性优于其它形状的滚筒。
这种优势在装载量不超过滚筒容积的二分之一时更为明显。
并且,六角形滚筒零件间相互抛磨的作用强,更利于提高镀层的光亮度。
2.2滚筒轴向
卧式滚筒的轴向为水平方向。
所以,卧式滚筒在带动零件翻滚时,零件运行方向与水平面垂直,这样有利于各零件间充分混合及提高镀层的光亮度。
并且,零件的垂直运行还为卧式滚筒的装载量赢得了优势。
例如,生产中装载150kg左右零件的卧式滚筒并不少见,这对其它滚镀方式来说是不可思议的。
尤其近些年,卧式滚筒的长度和直径有了较大的发展,适合滚镀的零件尺寸和重量也有所增加,许多原有的挂镀零件也可以滚镀。
所有这些,都使滚镀劳动生产效率高的优越性得到较好的体现。
卧式滚镀以劳动生产效率高、镀件表面质量好、适用的零件范围广等诸多优越性在滚镀生产中应用最广泛。
卧式滚镀的应用范围涵盖了五金、家电、汽摩、自行车、电子、仪器、手表、制笔、磁性材料等行业小零件电镀加工的绝大部分,是名副其实的小零件电镀加工的主力军。
所以,多年来滚镀技术的研究重点总是围绕着卧式滚镀在开展。
但是,由于卧式滚筒的封闭式结构,造成了卧式滚镀电镀时间长、镀层厚度不均匀、零件低电流区镀层质量不佳等缺陷,使其在生产中的应用受到影响。
3.倾斜式滚镀
倾斜式滚镀的滚筒形状为“钟”或“碗”形,所以,倾斜式滚筒也被称作钟形滚筒。
滚筒轴向与水平面约成40&
ordm;
~45&
角,则零件的运行方向倾斜于水平面,倾斜式滚镀的名字即由此而来。
1-电机;
2-滚筒;
3-阴极;
4-镀槽;
5-阳极;
6-导料槽;
7-升降手柄.
图2倾斜潜浸式滚镀机
目前使用的倾斜式滚镀设备叫做倾斜潜浸式滚镀机(如图2所示)。
倾斜潜浸式滚镀机于20世纪60年代开始在上海地区使用,由于其操作轻便灵活、易于维护而广受欢迎。
另外,使用倾斜式滚镀机镀件受损较轻,比较适合易损或尺寸精度要求较高的零件。
但是,倾斜式滚镀机滚筒装载量小、零件翻滚强度不够,在劳动生产效率和镀件表面质量等方面逊色于卧式滚镀机。
所以,多年来倾斜式滚镀的应用与发展始终落后于卧式滚镀。
4.振动电镀
振动电镀是国外20世纪70年代末发展起来80年代初大量应用的一项小零件电镀新技术。
它比常规的滚镀技术具有更加突出的优越性,因此一经问世即得到快速的应用与发展。
国内振动电镀出现于20世纪80年代末,并从90年代后期开始在小零件电镀领域应用逐渐广泛。
1-振荡器;
2-振杆;
3-传振轴;
4-料筐
图3振筛示意图
振动电镀的滚筒形状为“圆筛”或“圆盘”状,滚筒内零件的运动靠来自振荡器的振动力来实现。
所以,振动电镀的滚筒一般被形象地称作“振筛”(如图3所示)。
振筛的振动轴向与水平面垂直,则振筛内零件的运动方向为水平方向。
振动电镀的振筛结构和振动轴向与传统卧式滚筒有着本质的区别,所以会产生与传统卧式滚镀迥然不同的效果:
①振筛的料筐上部敞开后,彻底打破了传统卧式滚筒的封
闭式结构,消除了滚筒内外的离子浓度差。
所以,由滚筒封闭式结构带来的滚镀的缺陷得到最大程度的改善。
例如,镀层沉积速度快、厚度均匀及零件低电流区镀层质量好等。
②通过控制振筛的振动频率或振幅等条件,可以达到控制零件在振筛内混合条件的目的,从而可将各零件的镀层厚度波动性控制到最小。
③电镀时使用大的电流密度并同时进行着机械光整作用,镀层结晶细致,表面光亮度高。
④对零件的擦伤、磨损等均小于其它滚镀方式。
另外,振动电镀时阴极导电平稳,夹、卡零件现象较轻,并且可以随时对零件进行质量抽检。
但是,由于受到振筛结构和振动轴向的限制,振筛的装载量比较小,并且振动电镀设备的造价也比较高,所以目前振动电镀还不适于单件体积稍大且数量较多的小零件的电镀。
但对不宜或不能采用常规滚镀或品质要求较高的小零件,如针状、细小、薄壁、易擦伤、易变形、高精度等零件,振动电镀有着其它滚镀方式不可比拟的优越性。
所以,振动电镀是对常规滚镀的一个有力的补充。
四、滚镀的注意事项
1.电流密度差异大
滚镀的阴极电流密度虽然较大,然而由于电流密度差异悬殊,多数电流消耗在高电流密度的工件上,平均电流密度却很小,结果是阴极电流效率低,如操作中稍有疏忽,镀层厚度就难以保证。
2.滚镀过程中同时存在化学溶解
当工件翻滚时会使电流时断时续,要求加厚镀层需要延长滚镀时间,然而在局部处的镀层仍难以增厚。
3.及时调整主盐浓度
滚镀溶液中主盐消耗较快,这主要是阳极面积常常不足,工件出槽时损耗较多等原因引起的。
主盐含量过低时会引起电流效率下降,镀层难以镀厚,为此需根据化验分析数据及时予以调整。
4.滚镀件预处理难度大
滚镀件只能在篮筐里预处理,难免有重叠,故难以彻底除尽污物。
因而滚镀溶液易受污染,由于滚镀溶液对杂质较敏感,故溶液的净化处理工作量较大,往往容易因此而耽误生产。
5.滚镀溶液的pH值变化大
pH值的变化尤其在滚镀镍时更为明显。
这是因为滚镀镍过程中局部部位析氢激烈。
为维护生产,pH值需要勤调。
五、总结
滚镀的三种方式各有其不同的特征、优缺点及适用范围等,生产中应根据镀件的形状、大小、批量及质量要求等具体情况,选择准确合理的滚镀方式,以达到为企业节约增效、提高产品质量的目的。
例如,对于常规小零件,应首选卧式滚镀的方式。
而对于不宜或不能采用卧式滚镀或品质要求较高的小零件,则一般考虑振动电镀的方式。
但振动电镀不是一种“万灵药”,有时对于振动电镀也解决不了的小零件,可以采用一些比较特殊的电镀方式,如篮筐镀、筛网镀或布兜镀等。
化学镀与电镀从原理上的区别就是电镀需要外加的电流和阳极,而化学镀是依靠在金属表面所发生的自催化反应。
化学镀镍层是极为均匀的,只要镀液能浸泡得到,溶质交换充分,镀层就会非常均匀,几乎可以达到仿形的效果。
电镀无法对一些形状复杂的工件进行全表面施镀,但化学镀过以对任何形状工件施镀。
高磷的化学镀镍层为非晶态,镀层表面没有任何晶体间隙,而电镀层为典型的晶态镀层。
电镀因为有外加的电流,所以镀速要比化学镀快得我,同等厚度的镀层电镀要比化学镀提前完成。
化学镀层的结合力要普遍高于电镀层。
化学镀由于大部分使用食品级的添加剂,不使用诸如氰化物等有害物质,所以化学镀比电镀要环保一些。
化学镀目前市场上只有纯镍磷合金的一种颜色,而电镀可以实现很多色彩。