短轴车削指导书Word文件下载.docx
《短轴车削指导书Word文件下载.docx》由会员分享,可在线阅读,更多相关《短轴车削指导书Word文件下载.docx(18页珍藏版)》请在冰豆网上搜索。
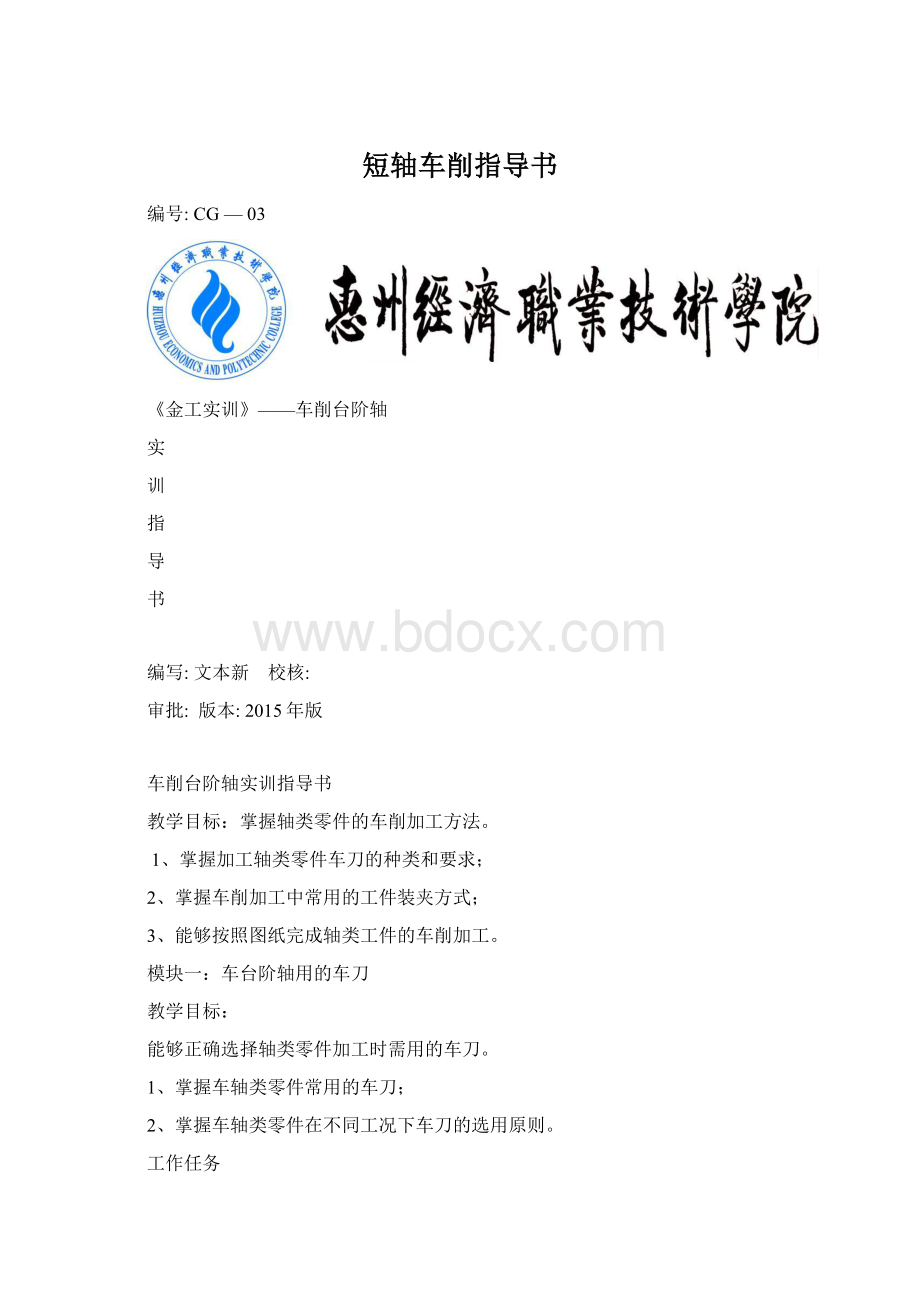
左右,因为这样刀尖角较大,能承受较大的切削力,而且有利于切削刃散热。
(3)一般粗车时采用0°
~3°
的刃倾角以增加刀头强度。
(4)为了增加切削刃强度,主切削刃上应磨有倒棱,其宽度br1=(0.5~0.8)f,倒棱前角
γ01=-(5°
~10°
)。
(5)为了增加刀尖强度,改善散热条件,使车刀耐用,刀尖处应磨有过渡刃。
(6)粗车塑性金属(如钢类)时,为了保证切削顺利进行,切屑能自行折断,应在前刀面上磨有断屑槽。
断屑槽常用的有直线型和圆弧型两种。
断屑槽的尺寸主要取决于进给量和切削深度。
2、精车刀
精车时要求达到工件的尺寸精度和较小的表面粗糙度,并且切去的金属较少,因此要求车刀锋利,切削刃平直光洁,刀尖处必要时还可磨修光刃。
切削时必须使切屑排向工件待加工表面。
选择精车刀几何参数的一般原则是:
(1)前角一般应大些,使车刀锋利,切削轻快。
(2)后角也应大些,以减少车刀和工件之间的摩擦。
精车时对车刀强度要求并不高,也允许取较大的后角。
(3)为了减小工件表面粗糙度,应取较小的副偏角或在刀尖处磨修光刃。
修光刃长度一般为(1.2~1.5)f。
(4)为了控制切削排向工件待加工表面,应选择正确的刃倾角(3°
~8°
(5)精车塑性金属时,前刀面应磨相应宽度的断屑槽。
相关实践知识
45º
和90º
外圆车刀的安装和使用
1、45º
外圆车刀的使用:
车刀又两个刀尖,前端一个刀尖通常用于车削工件的外圆。
左侧另一个刀尖通常用来车削平面。
主、副切削刃,在需要的时候可用来左右倒角。
(见下图)
车刀安装时,左侧的刀尖必须严格对准工件的旋转中心。
否则在车削平面至中心时会留有凸头或造成车刀刀尖碎裂,刀头伸出的长度约为刀杆厚度的1~1.5倍,伸出过长、刚性变差,车削时容易引起振动。
图3.145°
车刀的使用
2、90º
车刀又称偏刀,按进给方向分右偏刀和左偏刀,下面主要介绍常用的右偏刀。
右偏刀一般用来车削工件的外圆、端面和右向台阶,因为它的主偏角较大,车外圆时,用于工件的半径方向上的径向切削力较小,不易将工件顶弯。
车刀安装时,应使刀尖对准工件中心,主切削刃与工件中心线垂直。
如果主切削刃与工件中心线不垂直,将会导致车刀的工作角度发生变化,主要影响车刀主偏角和副偏角。
图3.2
右偏刀也可以用来车削平面,但因车削使用副切削刃切削,如果由工件外缘向工件中心进给。
当切削深度较大时,切削力会使车刀扎入工件,而形成凹面,为了防止产生凹面,可改由中心向外进给,用主切削刃切削,但切削深度较小。
模块二:
轴类工件的装夹
掌握轴类工件的装夹方法。
1、掌握使用三爪卡盘装夹工件;
2、掌握在三爪卡盘上找正工件的方法。
对工件在车床上运用一夹方法进行装夹。
一、三爪卡盘的拆装
自定心卡盘是车床上的常用工具,它的结构和形状见下图。
当卡盘扳手插入小锥齿轮2的方孔中转动时,就带动大锥齿轮3旋转。
大锥齿轮3背面是平面螺纹,平面螺纹又和卡爪4的端面螺纹啮合,因此就能带动三个卡爪同时作向心或离心移动。
1.定心卡盘的规格
常用的公制自定心卡盘规格有:
150、200、250。
2.自定心卡盘的拆装步骤
(1)拆自定心卡盘零部件的步骤和方法:
图3.5三爪卡盘的结构
松去三个定位螺钉6,取出三个小锥齿轮2;
松去三个紧固螺钉7取出防尘盖板5和带有平面螺纹的大锥齿轮3。
(2)装三个卡爪的方法装卡盘时,用卡盘扳手的方榫插入小锥齿轮的方孔中旋转、带动大锥齿轮的平面螺纹转动。
当平面螺纹的螺口转到将要接近壳体槽时,将1号卡爪装入壳体槽内。
其余两个卡爪按2号3号顺序装入,装的方法与前相同。
3.卡盘在主轴上装卸练习
(1)装卡盘时,首先将连接部分擦净,加油确保卡盘安装的准确性。
(2)卡盘旋上主轴后,应使卡盘法兰的平面和主轴平面贴紧。
(3)卸卡盘时,在操作者对面的卡爪与导轨面之间放置一定高度的硬木块或软金属,然后将卡爪转至近水平位置,慢速倒车冲撞。
当卡盘松动后,必须立即停车,然后用双手把卡盘旋下。
二、用三爪卡盘装夹
自定心卡盘的三个卡爪是同步运动的,能自动定心,工件装夹后一般不需找正。
但较长的工件离卡盘远端的旋转中心不一定与车床主轴的旋转中心重合,这时必须找正,如卡盘使用时间较长而精度下降后,工件加工部位的精度要求较高时,也必须找正。
自定心卡盘装夹工件方便、省时,但夹紧力没有单动卡盘大,所以适用于装夹外形规则的中、小型工件。
三、用四爪卡盘装夹
由于单动卡盘的四个卡爪各自独立运动,所以工件装夹时必须将加工部分的旋转中心找正到与车床主轴旋转中心重合才可以车削。
单动卡盘找正比较费时,但夹紧力较大,所以适合用于装夹大型或形状不规则的工件。
单动卡盘可以装成正爪或反爪两种形式,反爪用来装夹直径比较大饿工件。
四、用一夹一顶装夹
用两顶尖装夹工件虽然精度很高,但刚性较差,影响切削用量的提高。
因此,车削一般轴类工件,尤其是较重的工件,不能用两顶尖装夹,而用一夹一顶装夹用顶尖装夹工件,必须先在工件的端面钻出中心孔。
五、用两顶尖装夹
对于较长的或必须经过多次装夹才能加工好的工件、如长轴、长丝杆等的车削,或工序较多,在车削后还要铣削或磨削加工,为了保证每次装夹时的装夹精度(如同轴度要求),可用两顶尖装夹。
两顶尖装夹工件方便,不需找正,装夹精度高。
中心孔的形状和作用
国家标准GB145-85规定中心孔有A型(不带护锥)、B型(带护锥)、C型(带螺孔)和R型(弧型)四种。
精度要求一般的工件采用A型。
A型中心孔由圆锥孔和圆柱孔两部分组成。
圆锥孔的圆锥角一般为60°
(重型工件用90°
),它与顶尖锥面配合,起定心作用并承受工件的重量和切削力;
圆柱孔可储存润滑油,并可防止顶尖头触及工件,保证顶尖锥面配合贴切,以达到正确定中心。
设备、工具、材料配置表
项目三
车床
工具/量具
刀具
材料
模块二
型号
数量
名称
C6135
15
顶尖钻
注意事项
1、在主轴上安装卡盘时,应在主轴孔内插一铁棒,并垫好床面护板,防止砸坏床面。
2、安装三个卡爪时,应按逆时针方向顺序进行,并防止平面螺纹转过头。
3、装卡盘时,不准开车,以防危险。
模块三:
车削加工台阶轴
掌握轴类工件的车削加工方法。
1、掌握车床的操作方法;
2、理解不同加工面的刀具选择原理;
3、能正确控制粗车余量;
4、能正确控制精车的尺寸精度;
5、掌握轴类零件的测量方法。
按照图纸要求加工台阶轴,并对工件尺寸进行测量。
一、粗车
在车床动力条件允许的情况下,通常采用进刀深、进给量大、低转速的做法,以合理的时间尽快的把工件的余量去掉,因为粗车对切削表面没有严格的要求,只需留出一定的精车余量即可。
由于粗车切削力较大,工件必须装夹牢靠。
粗车的另一作用是:
可以及时的发现毛坯材料内部的缺陷、如夹渣、砂眼、裂纹等。
也能消除毛坯工件内部残存的应力和防止热变形。
二、精车
精车是车削的末道工序,为了使工件获得准确的尺寸和规定的表面粗糙度、操作者在精车时、通常把车刀修磨的锋利些,车床的转速高一些,进给量选的小一些。
三、刻度盘的计算和应用
在车削工件时,为了正确和迅速的掌握进刀深度,通常利用中滑板或小滑板上刻度盘进行操作。
中滑板的刻度盘装在横向进给的丝杠上,当摇动横向进给丝杠转一圈时,刻度盘也转了一周,这时固定在中滑板上的螺母就带动中滑板车刀移动一个导程、如果横向进给丝杠导程为4mm,刻度盘分80格,当摇动进给丝杠转动一周时,中滑板就移动5mm,当刻度盘转过一格时,中滑板移动量为4/80=0.05mm。
使用刻度盘时,由于螺杆和螺母之间配合往往存在间隙,因此会产生空行程(即刻度盘转动而滑板未移动)。
所以使用刻度盘进给过深时,必须向相反方向退回全部空行程,然后再转到需要的格数,而不能直接退回到需要的格数。
但必须注意,由于工件是旋转的,用中滑板刻度指示的切削深度,实现横向进刀后,直径上被切除的金属层是切削深度的两倍。
消除刻度盘空行程的方法见下图。
如果多转动了几格,绝不能简单地退回,而必须向相反方向退回全部空行程,再转到所需的刻度位置。
图3.6刻度盘的操作
四、轴类工件的测量
轴类工件的尺寸常用游标卡尺或千分尺测量。
1.游标卡尺
游标卡尺的式样很多,常用的有两用游标卡尺和双面游标卡尺。
以测量精度上分又有0.1㎜(1/10)精度游标卡尺,0.05(1/2)精度游标卡尺和0.02(1/50)精度游标卡尺。
(1)0.1㎜(1/10)精度游标卡尺刻线原理
尺身每小格为1㎜,游标刻线总长为9㎜,并等分为10格,因此每格为9/10=0.9㎜,则尺身和游标相对一格之差为1-0.9=0.1㎜,所以它的测量精度为0.1㎜。
(2)0.05㎜(1/20)精度游标卡尺刻线原理
尺身每小格为1㎜,游标刻线总长为39㎜,并等分为20格,因此每格为39/20=1.95㎜,则尺身和游标相对一格之差为2-1.95=0.05㎜,所以它的测量精度为0.05㎜。
(3)0.02㎜(1/50)精度游标卡尺刻线原理
尺身每小格为1㎜,游标刻线总长为49㎜,并等分为50格,因此每格为49/50=0.98㎜,则尺身和游标相对之差为1-0.98=0.02㎜,所以它的测量精度为0.02㎜。
(4)游标卡尺读数方法:
首先读出游标零线,在尺身上多少毫米的后面,其次看游标上哪一条刻线与尺身上的刻线相对齐,把尺身上的整毫米数和游标上的小数加起来,即为测量的尺寸读数。
(5)游标卡尺的使用方法和测量范围:
游标卡尺的测量范围很广,可以测量工件外径、孔径、长度、深度以及沟槽宽度等,测量工件的姿势和方法见图3.7。
2.千分尺
千分尺(或百分尺)是生产中最常用的精密量具之一,它的测量精度一般为0.01㎜,但由于测微螺杆的精度和结构上的限制,因此其移动量通常为25㎜,所以常用的千分尺测量范围分别为0~25㎜,25~50㎜,50~75㎜,75~100㎜…每隔25㎜为一档规格。
根据用途的不同,千分尺的种类很多,有外径千分尺、内径千分尺、内测千分尺、游标千分尺、螺纹千分尺和壁厚千分尺等等,它们虽然用途不同,但都是利用测微螺杆移动的基本原理。
这里主要介绍外径千分尺。
千分尺有尺架、踮座、测微螺杆、锁紧装置、固定套管、微分筒和测力装置等组成。
千分尺在测量前,必须校正零位,如果零位不准,可用专用扳手调整。
(1)千分尺的工作原理:
千分尺测微螺杆的螺距为0.5㎜,固定套筒上刻线距离,每格为0.5㎜(分上下刻线),当微分筒转一周时,测微螺杆就移动0.5㎜,微分筒上的圆周上共刻50格,因此当微分筒转一格时(1/50转),测微螺杆移动0.5/50=0.01㎜,所以常用的千分尺的测量精度为0.01㎜。
(2)千分尺的读数方法:
1先读出固定套管上露出刻线的整毫米数和半毫米数;
2看准微分筒上哪一格与固定套管基准线对齐;
3把两个数加起来,即为被测工件的尺寸。
图3.7游标卡尺的测量使用
一、用手动进给车削外圆、平面和倒角
1、车平面的方法:
开动车床使工件旋转,移动小滑板或床鞍控制进刀深度,然后锁紧床鞍,摇动中滑板丝杠进给、由工件外向中心或由工件中心向外进给车削。
见图3.8。
图3.8车外圆、平面和倒角
2、车外圆的方法:
移动床鞍至工件的右端、用中滑板控制进刀深度、摇动小滑板丝杠或床鞍纵向移动车削外圆,一次进给完毕,横向退刀,再纵向移动刀架或床鞍至工件右端,进行第二、第三次进给车削,直至符合图样要求为止。
再在车削外圆时,通常要进行试切削和时测量。
其具体方法是:
根据工件直径余量的二分之一作横向进刀,当车刀在纵向外圆上进给2毫米左右时,纵向快速退刀,然后停车测量,(注意横向不要退刀)。
然后停车测量,如果已经符合尺寸要求,就可以直接纵向进给进行车削,否则可按上述方法继续进行试切削和试测量,直至达到要求为止。
为了确保外圆的车削长度,通常先采用刻线痕法,后采用测量法进行,即在车削前根据需要的长度,用钢直尺、样板或卡尺及车刀刀尖在工件的表面刻一条线痕。
然后根据线痕进行车削,当车削完毕,再用钢直尺或其他工具复测。
3、倒角、当平面、外圆车削完毕,然后移动刀架、使车刀的切削刃与工件的外圆成45º
夹角,移动床鞍至工件的外圆和平面的相交处进行倒角,所谓1×
是指倒角在外圆上的轴向距离为1mm.
二、机动进给车削外圆和平面
机动进给比手动进给又很多的优点,如操作力,进给均匀,加工后工件表面粗糙度小等。
但机动进给是机械传动,操作者对车床手柄位置必须相当熟悉,否则在紧急情况下容易损坏工件或机床,使用机动进给的过程如下:
纵向车外圆过程如下:
启动机床工件旋转à
试切削à
机动进给à
纵向车外圆à
车至接近需要长度时停止进给à
改用手动进给à
车至长度尺寸à
退刀à
停车。
横向车平面过程如下:
横向车平面à
车至工件中心时停止进给à
车至工件中心à
工件材料长度余量较少或一次装夹不能完成切削的光轴,通常采用调头装夹。
再用接刀法车削,掉头接刀撤消的工件,一般表面有接刀痕迹,有损表面质量和美观。
但由于找正工件是车工的基本功,因此必须认真学习。
1、接刀工件的装夹找正和车削方法:
装夹接刀工件时,找正必须从严要求,否则会造成表面接刀偏差,直接影响工件质量,为保证接刀质量,通常要求车削工件的第一头时,车的长一些,调头装夹时,两点间的找正距离应大些。
工件的第一头精车至最后一刀时,车刀不能直接碰到台阶,应稍离台阶处停刀,以防车刀碰到台阶后突然增加切削量,产生扎刀现象。
调头精车时,车刀要锋利,最后一刀精车余量要小,否则工件上容易产生凹痕。
2、控制两端平行度的方法:
以工件先车削的一端外圆和台阶平面为基准,用划线盘找正,找正的正确与否,可在车削过程中用外径千分尺检查,如发现偏差,应从工件最薄处敲击,逐次找正。
三、车削台阶的方法
在同一工件上有几个直径大小不同的圆柱体连接在一起象台阶一样,就称它为台阶工件,轴类工件俗称台阶为“轴肩”。
台阶工件的车削,实际上就是外圆和平面车削的组合,因此在车削时必须注意兼顾外圆的尺寸精度和台阶长度的要求。
1、台阶工件的技术要求
台阶工件通常和其他零件结合使用,因此它的技术要求一般有以下几点:
(1)各档外圆之间的同轴度;
(2)外圆和台阶平面的垂直度;
(3)台阶平面的平面度;
(4)外圆和台阶平面相交处的清角。
2、车刀的选择和装夹
车削台阶工件,通常使用90º
外圆车刀。
车刀的装夹应根据粗、精车和余量的多少来区别,如粗车时余量多,为了增加切削深度,减少刀尖压力,车刀装夹可取主偏角小于90º
为宜。
精车时为了保证台阶平面和轴心线的垂直,应取主偏角大于90º
。
3、车削台阶工件的方法
车削台阶工件时,一般分粗、精车进行,粗车时的台阶长度除第一档台阶长度略短些外(留精车余量)其余各档可车至长度,精车台阶工件时,通常在机动进给精车至近台阶处时,以手动进给代替机动进给,当车至平面时,然后变纵向进给为横向进给,移动中滑板由里向外慢慢精车台阶平面。
以确保台阶平面和轴心线的垂直。
4、台阶长度的测量和控制方法
车削前根据台阶的长度先用刀尖在工件表面刻线痕,然后根据线痕进行粗车。
当粗车完毕后,台阶长度已经基本符合要求,在精车外圆的同时,一起控制台阶长度,其测量方法通常用钢直尺检查,如精度较高时,可用样板,游标深度尺等测量。
5、工件的调头找正和车削
根据习惯的找正方法,应先找正近卡爪处工件外圆,后找正台阶处反平面,这样反复多次找正才能进行切削,当粗车完毕时,宜再进行一次复查,以防粗车时发生移位。
四、轴类零件车削工艺
为了进行科学的管理,在生产过程中,常把合理的工艺过程中的各项内容,编写成文件来指导生产。
这类规定产品或零部件制造工艺过程和操作方法等的工艺文件叫工艺规程。
一个零件可以用几种不同的加工方法制造,但在一定条件下只有某一种方法是比较合理的。
台阶轴如图3.9。
图3.9
表1-1台阶轴加工工艺过程
工
序
号
工种
加工简图
工步内容
工装
装夹
方法
1
来
料
认真阅读图样,读懂、读熟,主要结构形状、尺寸位置、表面质量、技术要求必须牢记。
毛坯:
Φ40×
106
仔细检查毛坯尺寸,注意加工余量,做到心中有数。
2
车
1、夹持Φ40外圆,伸长70mm;
2、车端面见平;
3、粗、精车Φ38×
65,达到表面结构要求;
4、粗车Φ32×
40。
右偏刀
三爪自定心卡盘装夹
3
1、调头夹持Φ32外圆;
2、车另一端面,保证长62mm;
3、粗车Φ32×
40;
4、粗车Φ22×
30;
三爪自定心卡盘
4
1、调头装夹Φ22或Φ32处、找正;
2、精车端面,保证平面度;
3、精车Φ30×
40,Φ20(h8)×
20;
4、精车时须控制表面质量,并注意形位误差;
5、倒角,去毛剌、锐边。
右偏刀、
45度车刀
5
1、调头装夹Φ30处,找正,不能损坏已加工表面;
2、精车端面,保证平面度,控制长度60mm;
40mm,Φ20(h9)×
30mm;
三爪卡盘
6
检
测
评
分
1、自检;
2、互检;
3、总检、评分。
游标卡尺、千分尺、杠杆表、V型铁、平板等。
7
体
图
模块三
游标卡尺、千分尺、百分表
各15
90°
车刀
30
Q235φ40×
105棒料
45°
五、容易产生的问题和注意事项
1、工件平面中心留有凸头,原因是刀尖没有对准工件中心,偏高或偏低。
2、平面不平有凹凸,产生原因是进刀量过深、车刀磨损,滑板移动、刀架和车刀紧固力不足,产生扎刀或让刀。
3、车外圆产生锥度,原因有以下几种:
(1)用小滑板手动进给车外圆时,小滑板导轨与主轴轴线不平行。
(2)车速过高,在切削过程中车刀磨损。
(3)摇动中滑板进给时,没有消除空行程。
(4)车削表面痕迹粗细不一。
主要是手动进给不均匀。
(5)变换转速时应先停车,否则容易打坏主轴箱内的齿轮。
(6)切削时应先开车,后进刀。
切削完毕时先退刀后停车,否则车刀容易损坏。
4、测量过程中的注意事项:
(1)使用游标卡尺测量时,测量平面要垂直于工件中心线,不许敲打卡尺或拿游标卡尺勾铁屑。
(2)工件转动中禁止测量。
(3)使用千分尺要和游标卡尺配合测量,即:
卡尺量大数,千分尺量小数。
(4)测量时左右移动找最小尺寸,前后移动找最大尺寸,当测量头接触工件时可使用棘轮,以免造成测量误差。
(5)用前须校对“零”位,用后擦净涂油放入盒内。
(6)不要把卡尺、千分尺与其它工具,刀具混放,更不要把卡尺、千分尺当卡规使用,以免降低精度。
(7)千分尺不允许测量粗糙表面。
六、台阶轴评分表
班级
(学号)
姓名
成绩
评分标准
技术要求
配分
评分标准
检测结果
车床起动、操作正确
不合格扣5分
工件装夹正确
车刀安装正确
加工过程正确
10
Φ38±
0.10mm(1处)
超差扣5分
Φ35±
0.10mm(2处)
Φ20h8Φ20h9(2处)
8
长度尺寸±
0.10mm(5处)
每超1处扣3分
9
同轴度
超差扣3分
平面度及清角
11
Rα≤3.2μm、6.3μm
12
倒角、去毛剌、锐边、
13
整体外观
14
安全与文明生产
违者全扣
16