75吨余热锅炉化学清洗方案Word格式.docx
《75吨余热锅炉化学清洗方案Word格式.docx》由会员分享,可在线阅读,更多相关《75吨余热锅炉化学清洗方案Word格式.docx(25页珍藏版)》请在冰豆网上搜索。
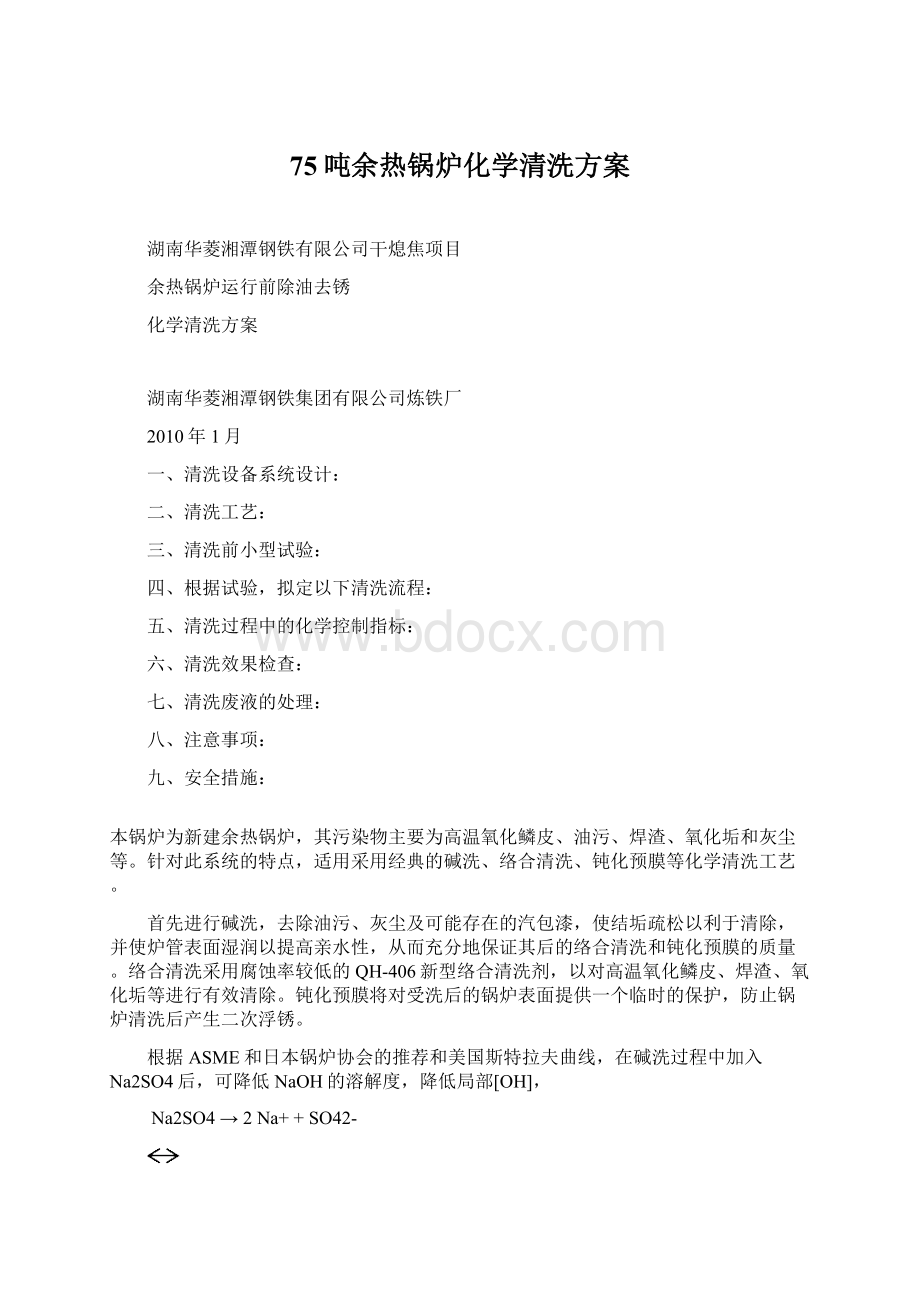
前水冷壁管
1
前联箱
64
后水冷壁管
2
后联箱
侧水冷壁管
3
侧联箱
74
(5)不同流量下各部分管内介质平均流速表:
管组名称
管径
(mm)
根数
截面积
(m2)
25t/h
流速(m/s)
51×
0.0929
0.0748
0.1074
0.0647
由于是锅炉投运前的除油去锈,过热器和省煤器等部位都为全新,清洗的部位是水冷壁管、下降管、汽包、系统管道等,为防止清洗过程中的酸气腐蚀,清洗前预先将除盐水(或清水)灌满过热器、省煤器等,加以保护。
为了了保证钝化预膜的效果,采用如下原则洗清工艺流程:
水冲洗→碱洗→水冲洗→络合清洗→中和水冲洗→漂洗钝化→废液处理。
贮、供水的质量和数量应能满足化学清洗和水冲洗的用水需要,清洗水用量参照《火力发电厂锅炉化学清洗导则》见表:
清洗过程
用水量为清洗系统水容积的倍数
汽包炉
直流炉
碱洗及随后的水冲洗
5-8倍
6-9倍
酸洗及随后的水冲洗
8-10倍
钝化用水
2-3倍
总用水量
15-21倍
16-22倍
清洗用水由甲方提供。
汽包容积13.5m3,水冷壁8.5m3,光管蒸发器5.7m3,鳍片管蒸发器4.4m3,吊挂管0.63m3,一次过热器1.5m3,二次过热器2.4m3,省煤器4.6m3,管道7.5m3。
共计48.73m3。
三、清洗施工工艺确定:
通过各种试验,确定清洗流程:
3.1施工前准备及临时清洗系统配置
(1)客供品
工厂提供的水、电、汽按客供品控制,接受时项目部须检查客供品的规格或技术参数(流量、压力、温度等)是否满足方案要求,清洗结束后须将其恢复原样。
(2)隔离、标记
将受洗锅炉、锅炉循环水、汽系统与其他系统隔离,各附件盲板封死或关闭,防止其它运行的锅炉蒸汽倒流和附件损坏,以保证清洗过程中无串线、无异常升温。
并在拆除的阀门和拆除部位以及盲板位置设置明显标记。
(3)拆除、盲板加封
拆除除氧器给水泵出口阀门,作清洗进口;
拆除除氧器进出口阀门,并短接;
拆除锅炉给水泵进出口阀门,并短接;
将一台循环泵进出口短接并在其上加阀门,另一进口与减温器注水管连接,入口作清洗进出口;
水冷壁集箱预置清洗口作为清洗进出口;
拆除减温器并作短接,以保证循环;
过热蒸汽放散管入口处阀门关闭;
拆除过热蒸汽出口阀门清洗接口。
所有安全阀拆除并加盲板;
所有远传二次仪表拆除;
汽包内件的拆除:
找开人孔,拆除汽包内所有非焊接的内件置于汽包外汽包污物清理完毕后,汽包内件装入汽包内或置于清洗槽内同时清洗。
(4)清洗系统安装、检漏
按余热锅炉化学清洗系统配管图(正循环+反循环)连接清洗系统,以清洗压力(4-6kgf/cm2)对受洗系统(含临时清洗系统)检漏,以30分钟系统无渗漏为合格。
3.2水冲洗及上水
(1)用除氧器给水泵注上水,用循环泵对锅炉进行水冲洗。
(2)使用介质:
工业水;
测定项目;
目测排出污物。
(3)判定标准:
放气口水溢流出为满水
排出口水清洁无污物
3.3升温
(1)起动循环
起动循环泵将锅炉及清洗系统中的纯水进行循环运行,开启蒸汽加热阀门,边循环,边加热。
(2)操作程序
循环泵使清洗系统中的工业水进行循环;
循环同时,注入蒸汽加热。
(3)测定项目
温度,每30分钟测一次。
3.4碱洗
(1)使用化学药品浓度
碱洗主剂1.5%
碱脆防止剂0.2%
促进剂包抑浸润剂渗透剂0.1%
(2)药品溶解
边循环边缓慢加入化学药品,混合均匀。
(3)清洗液注入清洗循环系统
清洗按正循环运行,按升温流程逐步升温至50~60℃左右,流量控制在50~80m3/h。
(4)操作程序
碱洗液加入以后,流量控制适当,温度为80±
10℃左右,正循环3-4h,反循环3-4h,碱洗总时间24h。
化学分析:
每4小时测定一次温度和PH值。
(5)测定项目:
温度、PH
(6)判定基准:
PH值9~13,温度55~80℃
时间满24小时。
(7)碱洗液排出
废液用HCI中和处理达标后排放;
排液完毕后,系统上满水再冲洗。
3.5水洗升温
通过水洗,使经过碱洗后锅炉内循环水PH值为7~9,温度升至80±
10℃。
(1)操作程序:
向清洗槽内加水,边循环边上水,使回流口出水。
水洗至循环水PH值为7~9。
以升温流程将温度升为80±
10℃左右。
(2)测定项目:
PH值,温度。
PH值7~9,温度80±
3.6络合清洗
络合清洗为去除受洗部件内部氧化物及焊渣的主要步骤。
(1)用药品浓度
名称浓度
QH-406络合清洗剂3-4%
QH-402缓蚀剂0.4%
点蚀抑制剂0.3%
(2)药品溶解及加入
将计量的QH-402缓蚀剂和点蚀抵制剂逐步加入循环槽中循环1小时。
溶液循环混合均匀后,加入QH-406络合清洗剂,边加热边循环分步完成,加完后用氨水将清洗剂PH值调至3~4。
(注:
在QH-406络合清洗剂加入循环槽之前,应将各试片挂在清洗槽中相对流速小的部位,并自此时计时。
)
(3)操作程序
清洗剂加入后,即开始正循环清洗,流量50~80m3/h,温度控制在80±
10℃左右,循环1小时,切换成反向循环。
每隔半小时测一次清洗液浓度,[Fe2+]、[Fe3+]、PH值、温度;
清洗时间6~8小时;
络合清洗后水冲洗时每2h打开排污阀排污5min。
(4)测定项目
清洗剂浓度、[Fe2+]、[Fe3+]、PH值、温度。
(5)判定标准
清洗液浓度稳定
[Fe3+]稳定
试样管段已清洗干净
(6)清洗液排出
清洗液用NaOH中和至排放标准后排入与现场所确认的地方。
3.7水冲洗
待清洗废液排尽,在清洗槽内上水,边上水边循环进行水冲洗,直至出水口无污物。
(1)测定项目
PH值
(2)判定标准
PH值4~7
目测无污物
3.8漂洗
除二次浮锈,为钝化作准备
柠檬酸0.5%
(2)药品加入
系统循环加温,温度在50~60℃开始加药;
加入除锈液(计量),边循环边加药。
除锈液加入后,加入计量的氨水将PH值调至3~4,保证总循环净时间2小时,温度为80±
10℃,流量为50~80m3h。
(4)测定项目:
PH值、温度
(5)判定基准
温度80±
10℃,PH值3~4。
3.9钝化预膜
(1)使用药品浓度
氨水、QH-302金属钝化剂10%
停止加热,利用余热保温。
漂洗液中徐徐加入计量氨水,正循环0.5小时,调PH值至9~11。
加入计量的钝化剂。
总时间为6小时
PH值
PH值9~11,循环6小时
(6)钝化剂排出
钝化液经现场确认后排入指定点(PH6~9)。
3.10废液处理
锅炉化学业清洗废液的排放根据现场受纳水域功能的要求按GB8978-1996《污水综合排放标准》的规定控制排放浓度。
其中主要的有关指标和最高允许排放浓度如下:
受纳水域
污水排放执行标准
PH值
悬浮物SS(mg/L)
化学耗氧量(mg/L)
氟化物
磷酸盐(以P计)(mg/L)
Ⅳ、Ⅴ类水域或三类海域
二级
6~9
150
10
1.0
清洗废液的处理:
锅炉清洗废液中的主要成分,按水中所含杂质对水体卫生标准的影响将杂质可分为三组。
a)无机物:
主要是钙、镁和钠的硫酸盐和氯化物。
b)有毒物:
主要是铁、铜和锌的盐类,含氟化合物和联氨。
c)有机物、铵盐、亚硝酸盐、硫化物:
这些物质能被细菌氧化或直接氧化,其排放量应按水体的生物需氧量计算。
清洗废液的处理,使第二组的物质分离出来,使第三组物质氧化到允许的生物需氧量值,从而减少公害,达到废水排放二级标准。
锅炉清洗废液的处理方法
清洗废液的处理方法详见废液处理系统D1、D2。
石灰浆硫化钠
漂白粉酸碱
酸
空气
待处理水排放
1
图D2设备化学清洗后的废水处理系统
1—水箱;
2—中和箱;
3—泥渣沉淀箱;
4—pH值调节箱
四、清洗过程中的化学控制指标:
清洗各阶段中的化学监督是保证清洗质量的重要环节,必须要做到准确及时,尽量减少误差,以利于判断清洗终点。
清洗前应仔细检查各种清洗药品的质量,核对数量做好记录。
4.1试片和监视管段
准备试片和监视管段,重量和表面状态经现场确认后,在清洗前分别挂于汽包及循环槽中,用于腐蚀性监测。
化学清洗过程中腐蚀率以试片为准,数量及设置部位见下表。
试片/监视管段
材质
清洗槽
备注
试片1#
20g
请现场提供原材料
试片2#
12CriMoV
试片3#
19Mn6
监视管段以现场提供的样管为准,接在临时系统循环回路上,清洗后观察清洗效果。
4.2测定项目
按测定要求及测定项目认真做好清洗化学监督工作,做到及时准确。
4.3络合清洗和钝化
络合清洗时定期(2次/h)观察清洗槽中试片的表面状况,并记录于《化学分析与化学监督报告》。
4.4记录
如实填写《化学分析与化学监督报告》和《工艺流转卡》
五、清洗效果检查:
由于是新锅炉的清洗,重点是将各系统带的油、锈除掉,因此清洗效果主要看监视管段清洗情况。
5.1对监视管段的检查:
考虑检查和安装方便,监视管段装于清洗泵出口处2米,可随时拆装观察,当清洗8小时即可拆开观察,清洗的确定以此为据。
漂洗效果检查与此相同。
5.2对锅炉设备内部的检查:
(1)汽包内的检查:
由于是新炉,因此在酸洗时液位应高于运行正常水位以上(150mm),原则上即以观察汽包壁油、锈,清洗结束主要是检查汽包壁上油、锈是否除去,钝化膜是否形成,检查是否留有氧化铁渣等,若有应清除。
(2)水冷壁管下的联箱检查,对下联箱检查是否形成钝化膜,铁渣等是否排放干净。
(3)割管检查,割水冷壁管进行内部检查,油、锈是否清洗干净,钝化膜是否形成(清洗前割管作为监视管段时可免掉此项)
5.3腐蚀指示片的检查:
酸洗开始时,必须在清洗系统中挂放腐蚀指示片,经酸洗后立即取出检查,用碱中和表面酸液,再用乙醇溶液清洗,干燥后称重,计算腐蚀速率和检查外观是否有腐蚀坑点。
酸洗失重(g)
试片表面积(m2)×
酸洗时间(h)
腐蚀速率(g/m2h)=
用腐蚀指示片测量的金属腐蚀速度的平均值应小于6g/(m2·
h),且腐蚀总量不大于60g/m2
。
5.4系统清洗后钝化质量检查与监督
酸性CuSO4点滴试验方法
1、在钝化后的试样表面,选择若干点(其他处用石蜡封盖),然后逐点滴上CuSO4溶液(该溶液破坏钝化膜后将产生如下反应:
Fe+CuSO4=FeSO4+Cu),并用秒表记录CuSO4点滴液由蓝变红的时间,根据滴入试片表面Cu2+颜色的消失(由蓝转红)快慢来评定钝化膜的质量。
同一个试片上各点转色时间的长短可评定钝化膜形成的均匀程度。
2、酸性CuSO4点滴液的组成为:
0.4mol/l的CuSO4溶液40ml,10%NaCl溶液20ml和0.1mol/lHCl1.5ml,并用除盐水稀释至100mL。
3、酸性CuSO4点滴钝化膜,耐蚀性的检验标准见表B1。
表B1耐蚀性的检验标准
检验标准
优良
合格
不合格
CuSO4点滴变色时间
(s)
>10
5~10
<5
六、注意事项:
6.1清洗过程中,为防止酸气腐蚀,预先将除盐水(或清水)灌满过热器,省煤器等,加以保护。
6.2汽包内旋风分离器,在清洗过程中全部拆除,清洗完毕后在安装恢复。
6.3酸洗时,应维持酸液液位在清洗系统液位以上,水冲洗时,应维持液位在比酸洗时的液位略高一些。
钝化时的液位应比水冲洗的液位更高。
6.4清洗液的循环方式与锅炉的结构和受热面结垢的程度等因素有关。
对锈蚀严重的回路应先进行循环清洗,其余回路静置浸泡。
待该回路循环一定时间后,再依次倒换。
必要时对锈蚀严重的回路重复进行循环清洗(此项目根据现场情况决定)。
6.5为了提高清洗效果,每一回路都应进行正反循环清洗,(取决于炉管和汽包连接的情况)。
如通过汽包的某些导汽管位置很高,只能进行单向循环时,酸液应由高位管进入,由低位管排出。
6.6在整个清洗过程中,应有钳工、电焊工、值班员随时处理出现的故障。
6.7管路系统焊接工作必须由合格的焊工施焊,系统并经水压试验合格,系统不漏水,试验压力为所用清洗泵最高压力。
七、安全、环保措施:
7.1安全措施
(1)遵守建设单位的规章制度,做好安全生产三级教育;
(2)清洗前,所有人员必须学习清洗安全和操作规程,熟悉清洗用药的性能和灼伤急救方法;
(3)现场应挂上安全字样及清洗区域标志,禁止无关人员进入;
(4)清洗现场严禁吸烟,动火办理动火证,动火完毕清理现场,消灭火种;
(5)用水、电、汽(气)必须经厂方同意后,在指定的地点使用;
(6)高空作业或危险作业时,必须佩带安全带,施工中严禁高空坠物;
(7)清洗中,禁止在清洗系统上进行其它工作,尤其不准明火作业;
(8)清洗中必须有检修人员,随时检修清洗设备;
(9)所有清洗人员必须穿戴好安全劳动保护用品;
进入厂区必须戴安全帽;
进入施工区工作服,乳胶手套,防酸胶鞋必须穿戴整齐;
加注清洗剂时,必须戴好防护眼镜,以防药液飞溅伤人;
(10)搬运清洗剂,严禁肩扛、手抱;
(11)在夜间施工行走时,注意扶梯、孔洞地面盖板等是否可靠,防止滑倒、坠落;
(12)清洗中,应注意用电、用汽安全;
(13)清洗现场配置急救水源、毛巾、药棉及其它医药用品,以备急救时使用;
(14)按照厂家ISO9001规定的作业程序程序文件实施各施工步骤;
(15)遵守厂家《化学清洗安全操作规程》。
7.2环保措施
余热清洗废液经处理并达标后排放,严禁采用渗坑、渗井和漫流的计划调节排放废液。
7.2.1废液排放标准
锅炉化学业清洗废液的排放根据现场受纳水域功能的要求按GB8978-1996《污水综合排放标准》的规定二级标准控制排放浓度。
注:
Ⅲ、Ⅳ、Ⅴ类水域按GB3838-88《地面水环境质量标准》划分。
二、三类海域按GB3097-82《海水水质标准》
排入未设置二级污水处理厂的城镇排水系统的污水。
应根据受纳水域的功能要求,分别执行一级或二级标准。
声明:
处理清洗废液根据现场的实际情况,在废液处理排放时遵循二级标准。
八、附件
附件1:
余热锅炉清洗系统原则流程图
附件2:
余热锅炉清洗工艺和监测项目
附件3:
余热锅炉化学清洗工程工时工序表
附件4:
余热化学清洗工程用设备一览表
附件5:
余热锅炉化学清洗工程化学分析监督用试剂、仪器一览表
图1余热锅炉循环清洗系统示意图
G—流量表;
P—压力表;
T—温度计;
U—取样点;
Y—腐蚀指示片安装处;
F—转子流量计
1—省煤器;
2—汽包;
3—水冷壁下联箱;
4—清洗箱;
5—清洗泵;
6—浓药泵;
7—浓碱箱;
8—浓酸箱;
9—光管蒸发器;
10—鳍片蒸发器;
11—低温过热器;
12—高温过热器;
余热锅炉清洗工艺和监视项目
序号
工序
清洗介质
工艺参数
备注
温度(℃)
流量(m3/)
时间
(h)
项目
取样
位置
频次
(次/h)
终点
水冲洗
除盐水或工业水
------
常温
50~80
2-4
目测无污物
大循环
碱煮
碱洗主剂阴离子活性剂碱脆抑制剂
-------
80±
24
温度时间
各溢流口
满24h
--------
络合
清洗
QH-406络合清洗剂3~4%
局部腐蚀抑制剂QH-402
3~4
6~8
清洗液浓度
[Fe3+]
[Fe2+]
温度
进出口
相隔30分钟清洗液%≤0.2%
[Fe3+]稳定
5
中和水冲洗
6
漂洗
柠檬酸0.5%氨水
温度PH值
满2小时
7
钝化
钝化剂10%
9~11
保温
6-8
满6小时
大循环+浸泡
8
废液
处理
工业盐酸、片碱
—
——
PH
9
11
12
13
14
15
16
17
运输进场
安全教育
系统隔离
配管
升温、水冲洗
酸洗
漂洗、钝化
系统恢复
交工验收
型号及规格
数量
1)
循环泵
“+”后为备用
2)
水冲泵
3)
压力表
4)
温度计
5)
止回阀
清洗循环泵出口用
6)
闸阀
循环清洗用
试压、流量控制用
7)
截止阀
蒸汽入口
8)
配电箱
9)
无缝钢管
10)
11)
黑胶管
开裂老化者禁用
12)
循环槽
13)
临时配电盘
14)
法兰