物料输送线plc控制系统设计说明文档格式.docx
《物料输送线plc控制系统设计说明文档格式.docx》由会员分享,可在线阅读,更多相关《物料输送线plc控制系统设计说明文档格式.docx(11页珍藏版)》请在冰豆网上搜索。
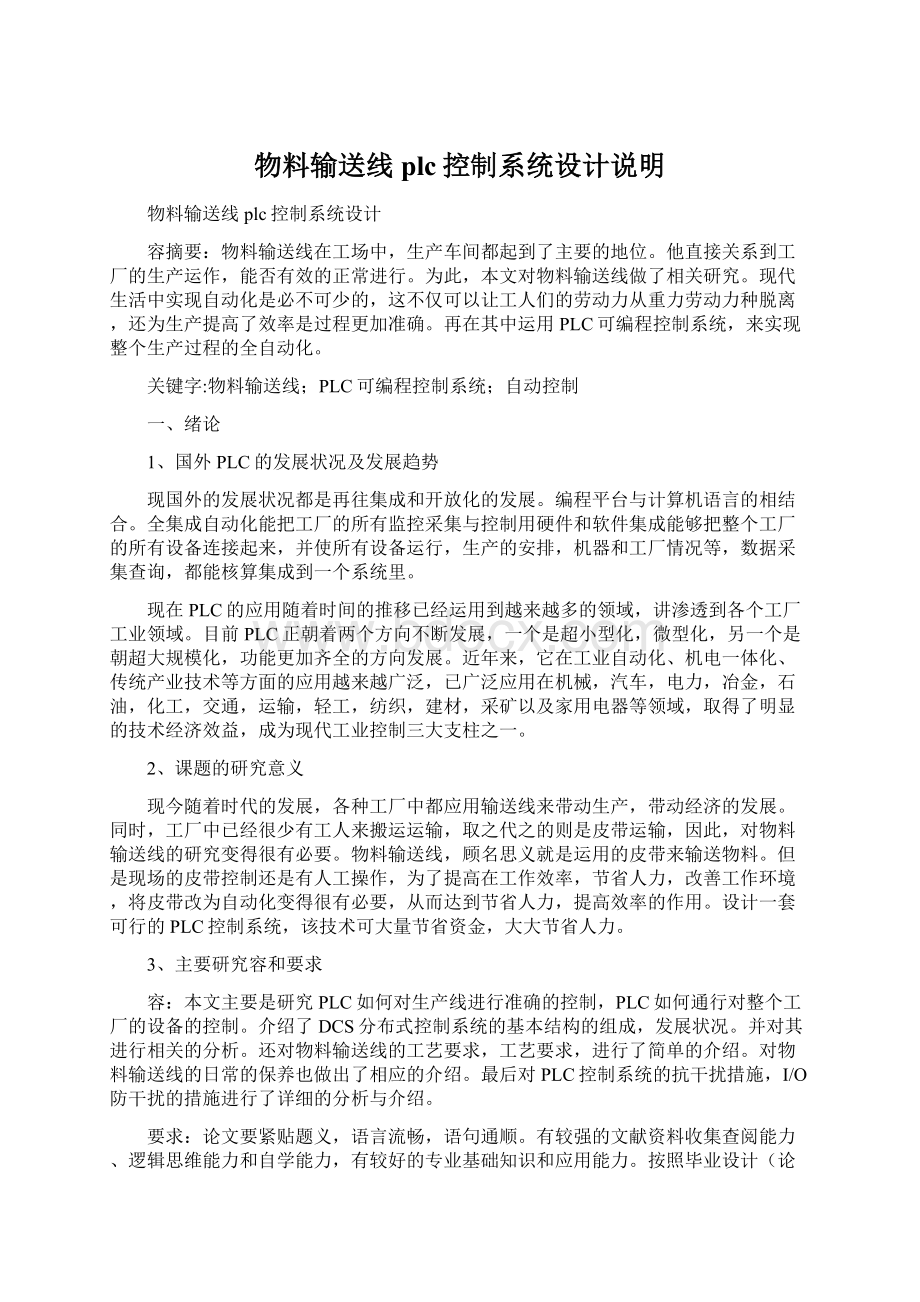
但是现场的皮带控制还是有人工操作,为了提高在工作效率,节省人力,改善工作环境,将皮带改为自动化变得很有必要,从而达到节省人力,提高效率的作用。
设计一套可行的PLC控制系统,该技术可大量节省资金,大大节省人力。
3、主要研究容和要求
容:
本文主要是研究PLC如何对生产线进行准确的控制,PLC如何通行对整个工厂的设备的控制。
介绍了DCS分布式控制系统的基本结构的组成,发展状况。
并对其进行相关的分析。
还对物料输送线的工艺要求,工艺要求,进行了简单的介绍。
对物料输送线的日常的保养也做出了相应的介绍。
最后对PLC控制系统的抗干扰措施,I/O防干扰的措施进行了详细的分析与介绍。
要求:
论文要紧贴题义,语言流畅,语句通顺。
有较强的文献资料收集查阅能力、逻辑思维能力和自学能力,有较好的专业基础知识和应用能力。
按照毕业设计(论文)时间安排,不抄袭、剽窃他人成果,保质保量完成各阶段任务,并主动按时提交相应的成果给助教老师。
二、系统整体设计
1、控制系统的分析与确定
DCS为集散控制系统的英文(DISTRIBUTEDCONTROLSYSTEM)简称,如图2.1所示。
指的是控制危险分散、管理和显示集中。
它是基于计算机技术,控制技术,通讯技术图形显示技术,通过某种通讯网络将分布在工业现场附近的现场控制站、检测站、操作管理站、控制管理站及工程师站连接起来完成分散控制集中操作的综合控制系统。
图2.1DCS系统基本结构
上世纪七十年代中期问世的DCS系统的基本结构,由控制站、显示操作工作站(或称人机接口)、以及将控制站、显示操作站点连成一个总体的通信总线共3个部分组成。
随着微电子、计算机、通信尤其是工业网络等高新技术及产品的迅速发展以及工业应用需求的变迁。
使现DCS这三个组成部分的职责与相互关系在设计理念上有较大的变化。
设计DCS的初衷是“危险分散、信息集中”。
危险分散体现于早期的一个控制站或控制单元仅仅包含8至16个控制回路。
往往要配置多个控制单元才能满足现场一个机组或一套生产装置整体控制要求。
现代化的工业生产,由于采取能量回收措施以及配套的公用工程使工艺流程上、下游各单元设备之间存在物流与能量流之间的勾连而形成的一套生产装置或机组是一个有机的整体,该整体的安全平稳生产并非能由各控制单元分别实施局部分割控制所能确保的.因此,工业应用要求扩大控制站的I/O容量与控制回路数,使之能覆盖一套生产装置(或机组)的控制需求而实现局部集中控制。
FCS为现场总线控制系统的英文(FIELDBUSCONTROLSYSTEM)简称,如图2.2所示。
现场的总线是连接智能化的设备和自动化的数字式,双向传输,多分支结构的通信网络。
它的关键在于能够支持双向,多节点,总线式,的全数字式通讯。
图2.2FCS系统基本结构
现场总线用于过程自动化、制造自动化、楼宇自动化等领域的现场智能设备互连通讯网络。
它作为通信网络的基础,现场总线技术是控制、计算机、通讯技术的交叉与集成,涉及的容十分广泛,现场总线是在80年代末、90年代初国际上发展形成的,现在自动化系统的网络化是发展的大趋势,现场总线技术受计算机网络技术的影响是十分深刻的。
2、总体结构的确定
在一般的情况下,监控系统都是由现场控制级设备、过程控制级设备、监控管理级设备组成多级体系,它们通过网络互相连接。
过程及设备从过程对象采集实时数据,按预先组态好的控制策略,接受操作人员的控制指示,从而实现对过程对象实时控制;
操作人员通过监控级设备,监视过程对象及控制装置的运行情况,并通过网络,向过程及设备发出指令,干预过程对象的控制,同时可进行数据分析和报表打印;
管理级设备可以接受监控管理级按规定的格式远传过来的数据,提供统一调度。
本文的设计中,整个系统主要由就地控制箱、PLC集中控制柜及上位远程监控终端3部分组成。
三、输送线的工艺研究及保养
1、输送线的工艺要求
引入PLC可编程控制器可解决很多问题。
具有的保护容有:
胶带跑偏,胶带车控制回路故障,胶带控制凹路故障,位置信号丢失,堆料,满仓信号提示等。
该系统的特点是:
性能稳定,扩展能力强,技术含量高,维修,维护,系统改造方便灵活,遇到紧急事故能及时停车,发出声光报警信号,能及时适应生产现场需要,确保了输送机的安全正常进行,具有广泛地适应性和推广价值。
系统在运行中要实现连续不断还必须要求输送的可靠工作,输送可靠工作的条件是:
(1)拖动皮带机的电机要安全可靠的运行
1)电机的功率要满足输送负荷的要求;
2)电机的工作是否正常应有检测装置。
(2)皮带机上的皮带是否工作正常
1)皮带机上的皮带是否打滑;
2)皮带机上的皮带是否跑偏。
2、输送线的工艺设计
物料输送线控制系统的工艺流程图如图3.1所示。
图3.1工艺流程图
在物料的输送过程中有3部分需要检测,物料上皮带时要经过一个平的皮带,然后物料经过一段爬坡的皮带进入第三个皮带,该皮带也是一个平坦的皮带,经过这三段皮带就可以进入仓库了。
爬坡的皮带和第一条皮带有一些区别,因为爬坡所以电机的功率要相对大一些。
在爬坡时掉包的可能性最大,因此在爬坡时对产品进行计数是最合适的,在这条皮带的中间安装一个传感器用来对产品进行计数。
3、输送线的日常保养
第一是输送线的输送带负荷过大出现打滑。
超出了自身的负荷能力,此时应当减轻输送物料的运输量或者增加输送机的本身的承重力,来防止打滑的现象。
第二是输送线的启动速度太快而造成打滑。
此时应当慢速启动或再次点动两下后再重新启动,也可以克服打滑的现象
第三是初力太小。
原因是输送带在离开滚筒时的力不够,所造成输送带的打滑。
此时处理的方法是调整拉紧装置,加大初力。
第四是滚筒的轴承的损坏而不运转。
原因可能是轴承部灰尘积聚的太多或是没有及时检修和更换已被严重磨损而转动不灵活的部件,造成阻力增大而打滑。
第五是输送机传动的滚筒与输送带之间的摩擦力不够所造成打滑现象。
原因一般就是输送带上有水滴没有擦拭干净或作业环境潮湿。
此时应当在滚筒加入些许松香末。
来防止打滑现象的出现。
四、PLC控制系统的抗干扰设计
1、抗电源干扰的措施
很多情况证明,由电源引起的干扰造成PLC控制系统的故障的情况发生很多。
PLC日常的供电都是由电网来供电。
由于电网的覆盖面很广,所以他将受到空间中电磁的干扰在线路上电压和电流。
特别是电网部的变化尤其明显,造成大型电力设备起停、交直流传动装置引起的谐波、电网短路暂态冲击等,都通过输电线路传到电源。
所以可以采取一下的措施来减少因为电源的干扰造成PLC控制系统的故障。
(1)采用性能优良的,抑制电网引入的干扰,在PLC控制系统中,电源占有很重要的地位。
电网干扰串入PLC控制系统主要是通过PLC系统的供电电源(有CPU电源,I/O电源等),变送器供电的电源与PLC系统具有直接电气连接的仪表耦合进入的。
现在一般对PLC系统的供电电源,一般采用隔离性能较好的电源,而对变送器的供电的电源和PLC系统有直接的电气连接的仪表的供电电源,并没有受到足够的重视。
虽然有采取了一定的措施,但普遍还是不够的,主要使用的隔离变压器分布参数大,抑制能力差,经电源耦合串入共模干扰。
所以对变送器的和共用信号仪表供电应选择分布电容量小,一直带大的配电器,以减少PLC系统的干扰。
此外,为保障电网供电不中断,可采用不间断供电电源,提高供电安全可靠性。
并且还具有较强的
干扰隔离的功能,是一种PLC控制系统的理想电源。
(2)硬件的滤波措施,在干扰较强或者可靠性要求较高的场合,应该使用带屏蔽层的隔离变压器对PLC系统供电。
还可以在隔离变压器一次侧串接滤波器,如图所示。
(3)正确选择地点,完善接地系统。
滤波器和隔离变压器同时使用
2、防I/O干扰的措施
由信号引入干扰会引起I/O信号工作异常和测量精度大大降低,严重时将引起元器件损伤。
对于隔离性能差的系统,还将导致信号间互相干扰,引起共地系统总线回流,造成逻辑数据变化、误动作或死机。
可采取以下措施以减小I/O干扰对PLC系统的影响。
(1)从抗干扰角度选择I/O模块
(2)安装与布线时注意:
①动力线、控制线以及PLC的电源线和I/O线应分别配线,隔离变压器与PLC和I/O之间应采用双绞线连接。
将PLC的I/O线和大功率线分开走线,如必须在同一线槽,可加隔板,分槽的走线最好,这不仅能使其有尽可能大的空间距离,并能将干扰降到最低限度。
②PLC应远离强干扰源。
如电焊机、大功率硅整流装置和大型动力设备,不能与高压电器安装在同一个开关柜。
在柜PLC应远离动力线(二者之间距离应大于200mm)。
与PLC装在同一个柜子的电感性负载,如功率较大的继电器、接触器的线圈,应并联RC电路。
③PLC的输入与输出最好分开走线,开关量与模拟量也要分开敷设。
模拟量信号的传送应采用屏蔽线,屏蔽层应一端接地,接地电阻应小于屏蔽层电阻的1/10。
④交流输出线和直流输出线不要用同一根电缆,输出线应尽量远离高压线和动力线,避免并行。
(3)考虑I/O端的接线:
输入接线一般不要太长,但如果环境干扰较小,电压降不大时,输入接线可适当长些。
输入/输出线要分开。
尽可能采用常开触点形式连接到输入端,使编制的梯形图与继电器原理图一致,便于阅读。
但急停、限位保护等情况例外。
输出端接线分为独立输出和公共输出,在不同组中,可采用不同类型和电压等级的输出电压。
但在同一组中的输出只能用同一类型、同一电压等级的电源。
由于PLC的输出元件被封装在印制电路板上并且连接至端子板,若将连接输出元件的负载短路,将烧毁印制电路板。
采用继电器输出时,所承受的电感性负载的大小,会影响到继电器的使用寿命,因此,使用电感性负载时应合理选择,或加隔离继电器。
(4)正确选择接地点,完善接地系统(5)对变频器干扰的抑制
五、输送线系统的软件设计
1、S7-200PLC软件系统与STEP编程软件
(1)数据类型
S7-200PLC指令的参数所用的基本数据类型有1位布尔型(BOOL)、8位字节型(BYTE)、16位无符号整数(WORD)、16位有符号整数(INT)、32位无符号双字整数(DWORD)、32位,有符号双字整数(DINT)、32位实数(REAL)。
S7-200的CPU中存放数据类型为BOOL、BYTE、WORD、INT、DWORD、DINT和REAL。
不同的数据类型具有不同的数据长度和数据围。
在上述数据类型中,用字节(B)、字(W)型、双字(D)型、分别表示8位、16位、32位的数据长度。
数据类型如表5.1所示。
表5.1数据位数与取值围
数据的位数
无符号数
有符号整数
十进制
十六进制
B(字节):
8位值
0-255
0-FF
-128-127
80-7F
W(字):
16位值
0-65355
0-FFFF
-32768-32767
8000-7FFF
D(双字):
32位值
0-4294967295
0-FFFFFFFF
-2147483647
80000000-7FFFFFFF
位存储单元的地址由字节地址和位地址组成,其中的区域标示符“1”表示输入(input),字节地址为3,位地址为2。
这种存取方式称为“字节.位”寻址方式。
(2)寻址方式
1)直接寻址
直接寻址指定了存储器的区域、长度和位置,例如VW790是V存储区中的字,其地址为790。
可以用字节(B)、字(W)、或双字(DW)方式存取V、I、Q、M、S和SM存储器区。
例如VB100表示以字节方式存取,VW100表示存取VB100、VB101组成的字,VD100表示存取VB100~VB103组成的双字。
2)间接寻址
指令给出了存放操作数地址的存储单元的地址称为间接寻址。
S7-200CPU允许使用指针对下述存储区域进行间接寻址:
I、Q、V、M、S、AI、AQ、T和C。
间接寻址不能用于位地址、HC或L存储区。
使用间接寻址之前,应创建一个指向该位置的指针。
指针为双双字值,用来存放;
另一个存储器的地址,只能用V、L或累加器做指针。
建立指针时必须用双字传送指令将需要间接寻址的存储器地址送到指针中。
指针也可以为子程序传递参数。
&
VB200表示VB200的地址,而不是VB200中的值。
2、PLC控制程序设计
(1)皮带电机的启动与停止
皮带的启停如图5.1所示。
图5.1电机的启停顺序流程图
在输送线上每条输送皮带上电机的启停顺序是不一样的,因为物料是向前输送的。
当启动时皮带需要从后向前逐个启动,如果从后向前启动时物料已经上了第一条皮带而第二条第三条皮带还没有启动,这样就会使物料都拥挤在第一条皮带的末端,最后造成物料无法传输。
当皮带停止运行时,为了让所有的物料都进入仓库必须先停掉第一条皮带,然后逐次停掉后续的皮带让后续皮带能把所有的物料都输送进仓库,如果先停第三条的话不仅无法将后面的物料送到仓库还会造成后面传输过来物料的拥堵。
启动程序
LDI1.2
JMP1
LDI1.5
OQ0.4
ANI2.0
=Q0.4
LDI2.1
OQ0.5
ANI2.2
=Q0.5
LDI2.3
ANI2.4
LBL1
LDNI1.2
JMP2
LDI1.3
OQ0.6
ANQ1.1
ANT98
=Q0.6
TONT33,3000
LDT33
ANQ0.7
ANQ1.0
ANT97
TONT34,+3000
TOFT98,+6000
LDT34
ANI1.4
TOFT97,+6000
LBL2
(2)产品的计数
产品的流程示意图如图5.2所示。
图5.2皮带运行过程中物料的计数
在本系统中加入了对物料的计数功能,可以在运输的过程中就统计出来产品的数量。
在第二条皮带上进行计数,当有物体通过传感器时输入PLC的电平发生变化,根据输入脉冲的变化次数来计数,通过输出口在显示器上显示产品的数量。
LDI0.3
LDC1
OSM0.1
CTUC1,+3000
LDSM0.1
CTUC2,+3000