学位论文ys234001牵引杆的机械加工工艺及夹具设计Word文件下载.docx
《学位论文ys234001牵引杆的机械加工工艺及夹具设计Word文件下载.docx》由会员分享,可在线阅读,更多相关《学位论文ys234001牵引杆的机械加工工艺及夹具设计Word文件下载.docx(19页珍藏版)》请在冰豆网上搜索。
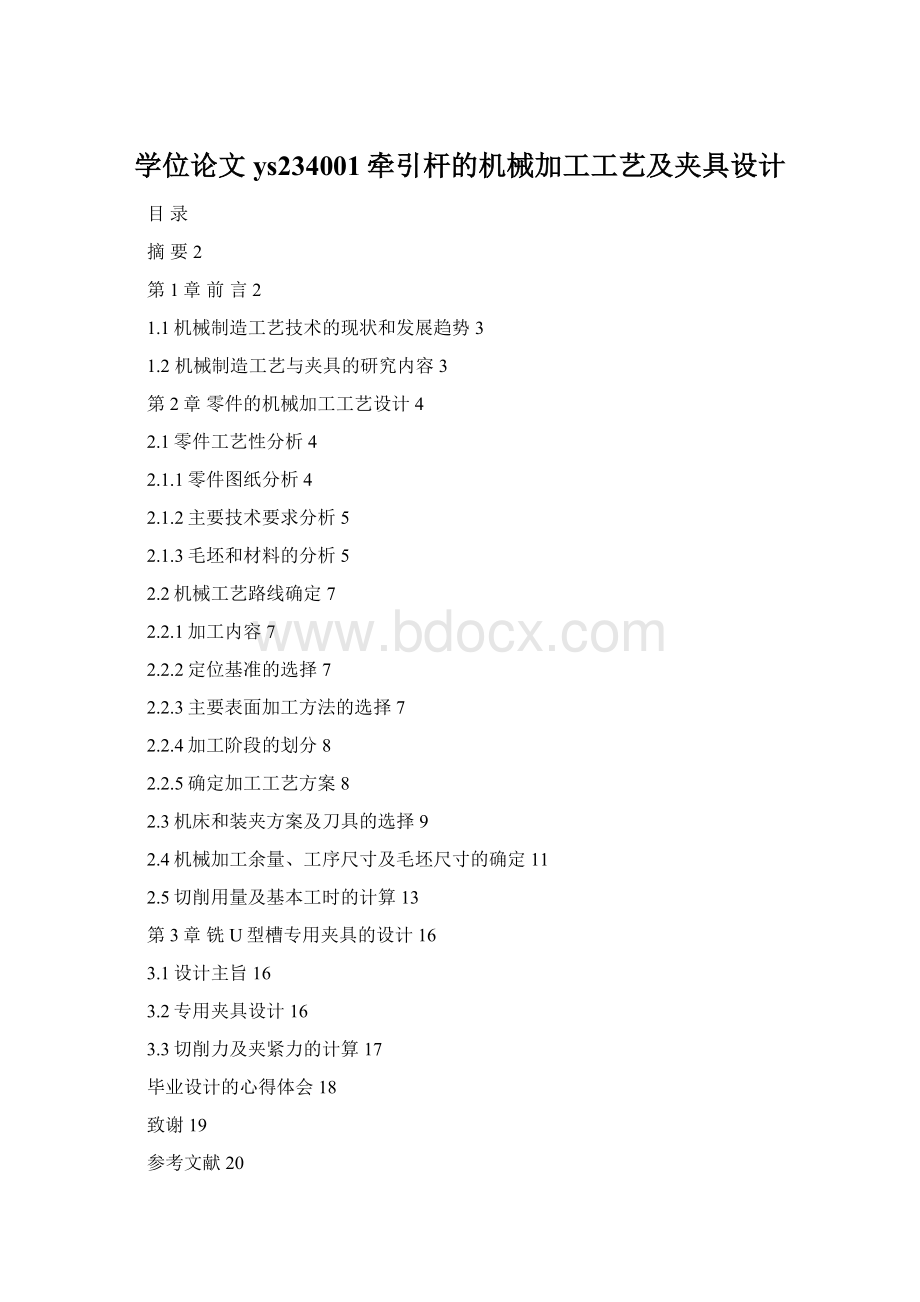
现代机械产品的特点是多品种、更新快、生产周期短。
这就要求整个机械加工系统及机械制造工艺向着柔性、高效、自动化方向发展。
由于成组技术理论的出现和计算机技术的发展,计算机辅助设计CAD,计算机辅助工艺设计CAPP、计算机辅助制造CAM、数控加工技术等在机械制造业中得到了广泛的应用,从而大大缩短了机电产品的生产周期,提高了效率,保证了产品的高精度、高质量。
1.2机械制造工艺与夹具的研究内容
机械制造的内容极其广泛,它包括零件的毛坯制造、机械加工及热处理和产品的装配等。
机械制造工艺及夹具研究的工艺问题可归纳为质量、生产率和经济性三类。
第一,要保证和提高产品的质量。
第二,要提高劳动生产率。
第三,要降低成本。
对这三类问题也要辩证的分析,要在满足质量要求的前提下,不断提高劳动生产率和降低成本。
以优质,高效,低耗的工艺去完成零件的加工和产品的装配,这样的工艺才是合理的和先进的工艺。
第2章零件的机械加工工艺设计
图一牵引杆零件图
2.1零件工艺性分析
2.1.1零件图纸分析
由零件图可知,该零件主要加工面为U型槽,加工时为防止两侧面变形,故铣U型槽时要设计专用夹具。
牵引杆整体精度要求并不是很高,采用铣削加工就可以达到要求,但是其形状位置精度要求较高,U型槽与基准面A的平行度要求为0.1,左端面与基准面B的垂直度要求为0.02,这些要求将影响到仪器的装配精度,是加工中主要要保证的精度要求。
零件的尺寸标注采用统一的基准即设计基准,无多余尺寸与封闭尺寸。
2.1.2主要技术要求分析
1.牵引杆的技术要求如下:
⑴锻造
⑵调制,220~270HB
⑶涂防锈油保护
2.牵引杆的位置要求如下
⑴U型槽与基准面A的平行度要求为0.1
⑵左端面与基准面B的垂直度要求为0.02
3.牵引杆的加工表面如下:
⑴主要加工表面
基准面B,U型槽,工件上下前后端面,Φ8,Φ4的孔
⑵次要加工便面
前后端面,M8螺纹孔
2.1.3毛坯和材料的分析
1.材料:
45钢
2.毛坯类型:
此零件为锻件
3.生产批量:
小批量
4.热处理
⑴因为牵引杆的毛坯制造方式是锻造,锻造后会出现组织缺陷,残余应力,还常出现硬度不均匀现象,为了细化晶粒,改善组织提高力学性能以利于切削加工,也为最终做好热处理,所以要在切削加工之前做退火或正火热处理。
⑵在切削加工后还要做淬火和低温回火处理,淬火+低温回火获得较好的强度,塑性,韧性和良好配合的力学性能。
⑶最终热处理发黑
5.确定机械加工余量
此零件最大的外形轮廓尺寸为400㎜左右,在《机械加工工艺设计手册》表2-9锻件最大边长尺寸250-400㎜中查出锻件的单边加工余量为3㎜。
6.零件尺寸公差
表2-1
尺寸
上偏差
下偏差
234
+0.15
-0.15
392.5
50
+0.3
-0
9(左端面)
+0.1
-0.1
9(U型槽)
+0
-0.2
16
--0.2
15.7
18
8.5
5.5
7.零件的毛坯图如下:
图二牵引杆的毛坯图
2.2机械工艺路线确定
2.2.1加工内容
基准面ARa6.3,基准面BRa6.3,两侧面Ra6.3,上表面Ra3.2,U型槽Ra3.2,Ф8通孔Ra1.6,左端面与底面平行度要求0.02,尺寸16的中心线与U型槽的同轴度要求0.1,尺寸16与M8螺纹的同轴度要求0.15。
2.2.2定位基准的选择
1.粗基准的选择。
粗基准的作用主要是决定不加工面与加工面的位置关系,以及保证加工面的余量均匀。
根据粗基准选择原则:
(1)选择重要表面为粗基准
(2)选择不加工表面为粗基准
(3)选择加工余量最小的表面为粗基准
(4)选择较为平整光洁、加工面积较大的表面为粗基准
(5)粗基准在同一尺寸方向上只能使用一次
因为粗基准本身都是未经机械加工的毛坯面,其表面粗糙且精度低,若重复使用将产生较大的误差。
根据以上原则可选基准面A面和基准面B为粗基准,加工其他表面。
2.精基准的选择原则:
⑴“基准重合”原则
⑵“基准统一”原则
⑶“自为基准”原则
⑷“互为基准”原则
⑸精基准选择应保证工件定位准确、夹紧可靠、操作方便。
根据“基准重合”“基准统一”原则,以尺寸160-0.2的中心线为精基准。
2.2.3主要表面加工方法的选择
表2-2
加工表面
尺寸精度
表面粗糙度
加工方案
基准面A
IT8~IT11
6.3
粗铣—半精铣
基准面B
粗铣—粗磨
两侧面
上表面
IT7~IT8
3.2
U型槽
粗铣—精铣
左端斜面右端倒角
粗铣
Φ8的通孔
IT6~IT8
1.6
钻—粗铰—精铰
Φ4的孔
钻
M8-6H的螺纹孔
IT7-IT8
钻—攻
2.2.4加工阶段的划分
⑴粗加工阶段
粗加工的目的是切去绝大部分多余的金属,为以后的精加工创造较好的条件,并为精加工提供定位基准,粗加工能及时发现毛坯的缺陷,予以报废或修
补,以免浪费工时。
牵引杆的粗加工是加工牵引杆的各个表面。
⑵辅助加工阶段
攻牵引杆左端上的螺纹。
⑶精加工阶段
精加工阶段切除剩余的少量加工余量,主要目的是保证零件的形状位置精度、尺寸精度及表面粗糙度,使各主要表面达到图纸要求。
精加工的加工精度一般为IT6~IT8,表面粗糙度为Ra3.2~1.6μm,牵引杆的精加工包括牵引杆的各个表面。
2.2.5确定加工工艺方案
工序一:
工步1铣四方
工序二:
工步1热处理
工序三:
工步1铣四面,去锐边
工步2铣两端
工序四:
工步1磨四面,去锐倒角
工序五:
工步1粗铣槽
工步2精铣槽
工步3按图铣30°
×
50+0.30
工序六:
工步1铣倒角,铣左端斜边,钻铣孔Ф8(通孔),钻孔Ф4(通孔),扩铣孔Ф8(螺纹孔)
工序七:
工步1钻攻左端螺纹孔M8,孔口倒角
工步2铰孔Ф8(通孔)
工步3去所有锐角,检查,调整B面平行度,上防锈油
2.3机床和装夹方案及刀具的选择
铣四方
(1)加工设备的选择
本工序选择X6142万能升降台铣床,主要技术参数如下:
工作台尺寸(mm):
425X2000定位精度0.02/150
最大工作行程(mm):
X1210、Y370、Z370主轴转速:
18—1400m/s
重复定位精度:
0.02mm
(2)定位、夹紧方式和对刀点的确定
铣四方时,直接加紧工件两侧固定即可。
装夹工件时要校正工件,方法是用百分表拉直侧边直线,然后用深度百分表打毛坯上表面,调整可调支撑使毛坯表面误差在0.5以内。
(3)刀具和量具的选择
选择高速钢圆柱铣刀,选用分度值为0.05mm的游标卡尺进行测量
铣四面及两端,去锐边
铣四面及两端时,直接加紧两侧固定即可。
(在磨四面时,均已相邻两面定位,保持四面垂直)
去锐边
在装夹工件时要校正工件,方法是用百分表拉直侧边直线,然后用深度百分表打毛坯上表面,调整可调支撑使毛坯表面误差在0.5以内。
选择高速钢立铣刀,选用分度值为0.05mm的游标卡尺进行测量
磨四面
(1)加工设备的选择
本工序选择M1432B万能外圆磨床,主要技术参数如下:
320X2000定位精度0.003/150
X5700、Y1800、Z1515
磨轮最大外径×
厚度(㎜):
400×
磨四面时,直接加紧两侧,固定。
(在磨某一表面时,均已相邻的两表面定位,保持四面垂直)。
(3)刀具的选择
选择砂轮进行磨削。
工序五﹕粗铣精铣槽及按图铣30°
(2)定位、夹紧方式和对刀点的确定
铣槽时,将工件装于特定的夹具中。
在装夹夹具时要校正工件,方法是用百分表拉直侧边直线,然后用深度百分表打毛坯上表面,调整可调支撑使毛坯表面误差在0.5以内。
(3)刀具和量具的选择
选择高速钢圆柱铣刀,高速钢立铣刀,T形槽铣刀,选用分度值为0.05mm的游标卡尺进行测量
铣右端倒角及左端斜面
铣左端斜面时,将工件装于特定的夹具中即可。
铣右端倒角时,将工件调头装夹于特定的夹具中即可。
钻通孔Ф4,钻铰通孔Ф8
本工序选择T617A卧式铣镗床,主要技术参数如下:
工作台行程(mm):
纵向900横向750定位精度0.01/150
镗床外形尺寸(mm):
X3773、Y2425、Z1848
铣通孔时,将工件直接装夹于工作台上,夹紧。
(夹紧时,可在工件两侧面垫铜片以防止工件表面磨损)在装夹工件时要校正工件,方法是用百分表拉直侧边直线,然后用深度百分表打毛坯上表面,调整可调支撑使毛坯表面误差在0.5以内。
选择刀具中心钻,扩孔钻,丝锥。
量具选用内径千分尺。
左端M8螺纹孔的加工
四爪卡盘夹紧。
(夹紧时,可在工件表面垫铜片以防止工件表面磨损)在装夹工件时要校正工件,方法是用百分表拉直侧边直线,然后用深度百分表打毛坯上表面,调整可调支撑使毛坯表面误差在0.5以内。
选择刀具中心钻,丝锥。
量具选用内径千分尺
2.4机械加工余量、工序尺寸及毛坯尺寸的确定
1.平面的加工
⑴基准面B和上表面的加工,要求粗铣—粗磨,跟据《金属机械加工工艺设计手册》表4-28及表4-11,得粗铣1mm,粗磨0.5mm。
表2-3
工序名称
工序间余量
经济精度等级
工序尺寸
粗磨
0.5
IT8
Ra6.3
1
IT9
18+0.5×
2=19
毛坯
19+1×
2=21
Ra12.5
⑵两侧面的加工,要求粗铣—粗磨,跟据《金属机械加工工艺设计手册》表4-28及表4-11,得粗铣1mm,粗磨0.5mm。
表2-4
16+0.5×
2=17
17+1×
⑶基准面A和后端面的加工,要求粗铣—半精铣,跟据《金属机械加工工艺设计手册》表4-28,得粗铣1.5mm,半精铣1mm。
表2-5
半精铣
400
1.5
400+1×
2=402
402+1.5×
2=405
⑷U型槽的加工,要求粗铣—精铣,跟据《金属机械加工工艺设计手册》表4-28,得精铣1.5mm。
表2-6
精铣
6+1.5×
2=9
Ra3.2
6
2.孔的加工
⑴Φ8通孔的加工要求钻—粗铰—精铰,根据《金属机械加工工艺设计手册》表4-15,得钻加工到的尺寸为7.8mm,粗铰加工到的尺寸为7.96mm,铰加工到的尺寸为8mm。
表2-7
工序间余量
精铰
0.04
IT7
8
Ra1.6
粗铰
0.08
8-0.04=7.96
7.8
IT11
7.96-0.08=7.8
⑵M8-6H螺纹孔的加工要求钻—攻,根据《金属机械加工工艺设计手册》表4-41,得钻加工的尺寸为6.8mm。
攻螺纹:
螺距P=1.25
牙深=0.6495×
1.25=0.812
H=0.866×
1.25=1.0825
螺纹底径=螺纹外径-2×
牙深=7.73-2×
0.812=6.106
2.5切削用量及基本工时的计算
铣四面
1.加工条件
工件材料:
45钢调制处理,σb=550~670MPa,锻造。
加工要求:
粗铣粗磨牵引杆四面,粗铣精铣U型槽
机床:
X6142卧式(万能)铣床。
刀具:
高速钢立铣刀,铣刀直径D=22mm,L=72mm
2.计算切削用量
⑴粗铣牵引杆的四面
确定粗铣两侧面的加工余量为1.5mm,可以两次加工完成,按ap=0.5确定进给量f:
根据《机械加工工艺师手册》表30-13得af=0.06~0.10mm/z可取0.48mm/r,根据《机械加工工艺师手册》表30-23得立铣刀的铣削速度为55~115m/min,可取55m/min
确定机床主轴转速
现选用X6142卧式铣床,根据机床使用说明书取nw=800r/min
则实际切削速度
当nw=800r/min时工作台每分钟进给量fm应为:
Fm=f×
nw=0.48×
800=384mm/min
按机床说明书取fm=390mm/min
计算切削工时:
按工艺手册得
被切削层长度L=400mm
刀具切入长度
刀具切出长度L2=2~5mm,取L2=4mm
行程次数i=2
机动时间
铣槽
⑴粗铣U型槽,重新选用Φ6的立铣刀
确定粗铣U型槽的加工余量为6mm,可以一次加工完成,按ap=3确定进给量f:
根据《机械加工工艺师手册》表30-13得af=0.06~0.10mm/z可取0.5mm/r,根据《机械加工工艺师手册》表30-23得立铣刀的铣削速度为15~35m/min,可取15m/min
按机床说明书取发fm=400mm/min
被切削层长度L=375mm
行程次数i=1
⑵精铣U型槽
确定精铣U型槽的最大加工余量Zmax=1.5mm,可以一次加工完成,ap=0.75mm
确定进给量f:
根据《机械加工工艺师手册》表30-13得af=0.06~0.10mm/z可取0.80mm/r,根据《机械加工工艺师手册》表30-23得立铣刀的铣削速度为15~25m/s可取15m/min。
按机床说明书取fm=400mm/min
刀具切出长度L2=2~5mm,取L2=3mm
基本工时为:
第3章铣U型槽专用夹具的设计
为了提高劳动生产率,保证加工质量,降低劳动强度,通常需要设计专用夹具。
经过与指导老师协商,决定设计第六道工序钻铣U型槽的夹具。
3.1设计主旨
本夹具主要用来铣槽,加工到本工序的时候,上表面已经加工,以此面定位来铣槽,在这道工序加工时,主要应考虑如何提高劳动生产率,降低劳动强度,而精度则不是主要问题。
由于考虑到装夹时会影响两侧面的精度要求的问题,故铣U型槽时要设置专用夹具。
3.2专用夹具设计
1.定位基准的选择
由零件图可知,以底面作为精基准。
把零件直接插进专用夹具中,尾端设置一顶点,限制六个自由度。
在上表面上设置三个夹紧点,用钩形压板来夹紧,可防止零件移动,采用完全定位的方式。
2.夹紧装置的设计
夹紧机构的三要素是夹紧力方向、作用点、大小的确定。
设计的时候有如下要求:
⑴在夹紧过程中工件应能保持在既定位置,即在夹紧力的作用下,工件不应离开定位支撑。
⑵夹紧力的大小要适当、可靠。
既要使工件在加工过程中不产生移动和震动,又不使工件产生不允许的变形和损伤。
⑶加紧装置应操作安全、方便、省力。
⑷夹紧装置的自动化程度和复杂程度应与工件的产量和批量相适应。
3.定位误差分析
⑴定位元件尺寸及公差的确定。
该夹具以底面定位,要求保证槽的尺寸公差以及槽的轴线与底座上槽16+0.1+0.05的同轴度公差,为了满足工序的加工要求,必须使工序中误差总和小于或等于该工序所规定的工序公差。
槽90-0.2与底座上槽16+0.1+0.05的同轴度公差为0.1
⑵计算槽90-0.2与底座上槽16+0.1+0.05的同轴度公差。
其最大间隙
此即为槽90-0.2与底座上槽16+0.1+0.05的最大同轴度误差,满足上述要求,故上述同轴度误差允许。
4.夹具体设计
铣U型槽时,为了防止装夹过程中使两侧面变形,影响表面精度,所以设计夹具时应减少对两侧面的装夹。
夹具体要有足够的精度、强度和刚度,结构工艺性要好,排屑方便,和在机床上安装稳定可靠的要求。
本夹具用于在铣床上加工U型槽,夹紧机构操作简单、夹紧可靠。
本次设计中还按老师的要求画出了夹具图,具体结构可参见附图
3.3切削力及夹紧力的计算
切削刀具:
Φ6高速钢立铣刀,Z=3
本加工按铣削估算夹紧力,实际效果可以保证可靠的夹紧。
1.实际所需夹紧力:
查《机械加工工艺师手册》表30-20得
表20-21得
表20-22得
,
2.螺旋夹紧力
所以
毕业设计的心得体会
紧张而又辛苦的毕业设计结束了。
当我拿到的任务的时候,我仿佛经过一次翻山越岭,登上了高山之巅,顿感眼前豁然开朗。
毕业设计是我们专业课程知识综合应用的实践训练,这是我们迈向社会,从事职业工作前一个必不可少的过程。
“千里之行始于足下”,通过这次毕业设计,我深深体会到这句千古名言真正的含义。
我今天认真地进行毕业设计,学会脚踏实地迈开这一步,就是为明天能稳健地在社会大潮中奔跑打下坚实的基础。
说实话,毕业设计非常累。
然而,当我一着手理清自己的设计成果,仔细回味这几周的心路历程,一种少有的成功喜悦即刻使我倦意顿消。
虽然这是我刚学会走完的第一步,是我人生中的一点小小的胜利,然而它令我感到自己成熟了许多。
通过毕业设计,使我深深体会到,干任何事都必须耐心细致。
毕业设计过程中,许多计算时不免令我感到心烦意乱;
有两次因为不小心我计算出错,只能毫不情愿地重来。
但一想起老师对我们的耐心教导,想到今后自己应承担的社会责任,想到世界上因为某些细小的失误而出现难以控制的事故,我不禁时刻提醒自己,一定要养成一种高度负责,一丝不苟的良好习惯。
这次毕业设计是我在工作作风上,得到了一次难得的磨练。
短短几周的毕业设计,使我发现自己所掌握的知识是真正的如此贫乏,自己综合应用所学专业知识的能力是如此不足,几年来学习那么多课程