论文燃煤电厂烟气除尘脱硫工程设计毕业论文Word文件下载.docx
《论文燃煤电厂烟气除尘脱硫工程设计毕业论文Word文件下载.docx》由会员分享,可在线阅读,更多相关《论文燃煤电厂烟气除尘脱硫工程设计毕业论文Word文件下载.docx(34页珍藏版)》请在冰豆网上搜索。
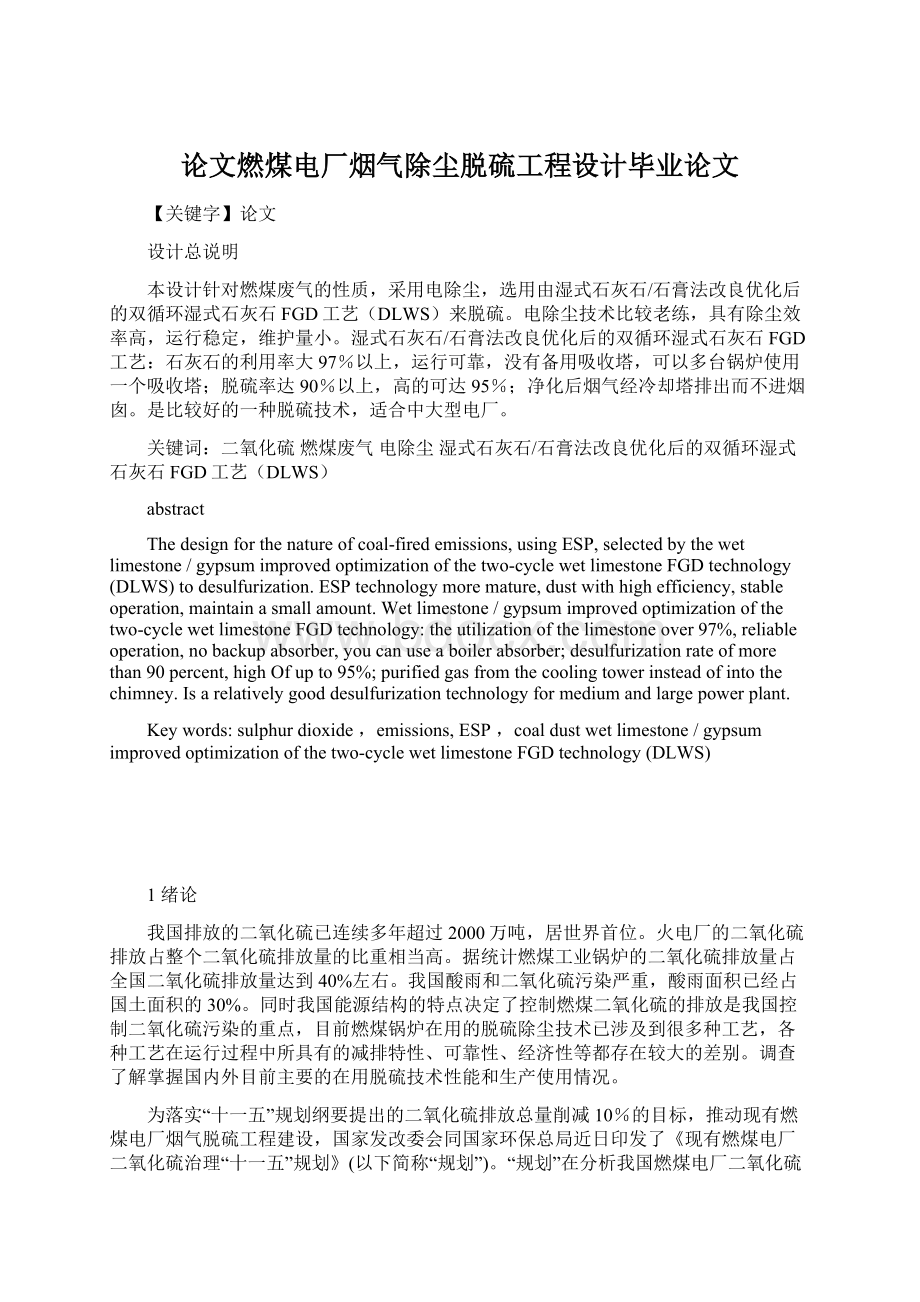
二是强化政策引导,完善电价形成机制,研究和逐步实施根据燃煤机组脱硫改造的实际投资和运行成本核定脱硫电价。
鼓励安装烟气脱硫装置的机组优先上网,优先保障上网电量。
二氧化硫排污费优先用于现有燃煤电厂二氧化硫治理。
对脱硫关键设备和脱硫副产品综合利用继续给予减免税优惠;
三是加快脱硫产业化发展,加大对拥有自主知识产权烟气脱硫技术和设备产业化的扶持力度,加快烟气脱硫新技术、新工艺的研发和示范试点,推动烟气脱硫副产品综合利用,继续整顿烟气脱硫市场;
四是充分发挥政府、行业组织和企业的作用。
国家发改委、国家环保总局根据“规划”,将每年公布需安装烟气脱硫设施的电厂名单、重点项目及完成情况,接受社会监督。
同时,将加快制订烟气脱硫设施建设、运行和维护技术规范,开展烟气脱硫特许经营试点,加大对已投运烟气脱硫设施运行的监管,对非正常停运烟气脱硫设施的将加大处罚力度。
本设计是介绍450WM燃煤电厂的烟气除尘脱硫方案及工程设计。
本设计主要对650t/h燃煤锅炉烟气除尘脱硫技术作了详尽的说明。
介绍和论证了各种除尘和脱硫的方法及工艺流程,通过对烟气脱硫工艺进行综合评价,选定工艺系统简单,运行可靠,占地面积小投资和运行费用低的工艺。
同时,也对所选工艺的主要设备和附件作了详细介绍。
2烟气除尘脱硫的工艺及技术的介绍
2.1废气脱硫的工艺方法
近年来,我国的脱硫工作有了很大进展,在自主研究、自我开发的同时,引进了几套较成熟的脱硫设备,主要有湿式石灰石/石膏法、旋转喷雾干燥法、LIFAC法、简易湿法、海水脱硫、电子束脱硫及循环流化床燃媒技术等。
湿式石灰石/石膏法是将石灰石粉制成浆液,在吸收装置中将烟气中的SO2脱除而副产石膏的方法。
该方法是目前应用最广的一种烟气脱硫(FGD)方法,占湿法烟气脱硫的70%以上。
其脱硫率高,可达95%以上,运行可靠,技术最为成熟,可适用于高、中、低硫煤。
但它最大的缺点是设备庞大,占地面积大,投资和运行费用高。
石灰、石灰石的粉料被直接喷入锅炉炉膛内的高温区,被煅烧成氧化钙,烟气中的二氧化硫即二氧化硫反应而被吸收。
由于烟气中氧的存在,在吸收进行的同时,还会有氧化反应发生。
由于喷射的石灰石在炉膛内停留时间很短,因此在这段时间内因完成煅烧、吸附、氧化的反应,主要包含如下的反应:
CaCO3CaO+CO2
CaO+SO2+1/2O2CaSO4
采用白云石(CaCO3.MgCO3)或当石灰石中含有MgCO3时,还会发生如下反应:
CaCO3CaO+CO2
SO2+1/2O2+MgOMgSO4
2.1.2旋转喷雾干燥法烟气脱硫
此工艺称半干法FGD工艺,其基本工艺路线是将石灰制成一定浓度的浆液供给脱硫塔,在脱硫塔中由高速旋转的喷雾装置将浆液雾化成100μm以下的微滴,同时与含SO2的热烟气接触,在雾滴干燥的同时,完成对SO2的吸收。
经除尘分离烟气排放,脱硫渣循环适用。
发生如下化学反应:
SO2+H2OH++HSO3-
HSO3H++SO3
Ca2++SO32-CaSO3
旋转喷雾干燥法烟气脱硫,工艺过程简单,设备少,占地少,不许对脱硫产品进行二次处理,没有废水排放,脱硫后的烟气不需要二次加热,因而运行费用低。
该法适用于燃用中、低硫煤锅炉的烟气脱硫。
炉内喷钙尾部增湿脱硫(LIFCA)技术:
由芬兰Tampella公司和IVO公司联合开发的LIFAC脱硫工艺是炉内喷钙脱硫技术的基础上,在尾部烟道加装了增湿活化器,在活化器中,喷入的水雾与烟气中的末反应的氧化钙颗粒反应,生成活性更高的氢氧化钙,对SO2进一步吸收,总脱硫率可达70%~80%。
工艺原理:
第一阶段:
CaCO3CaO+CO2
锅炉烟气中SO3和部分SO2与CAO反应生成硫酸钙
CaO+SO2+1/2O2CaSO4
CaO+SO3CaSO4
第二阶段:
CaO+H2OCa(OH)2
Ca(OH)2+SO2CaSO3+H2O
CaSO3+1/2O2CaSO4
LIFAC工艺适用于燃用中、低硫煤锅炉的烟气脱硫,投资比湿法FGD少,占地面积小,特别适合于老厂改造。
由于属干法FGD技术,因此没有废水排放,烟气也不需要二次加热,因此运行费用低。
但脱硫率较低,钙硫比高,吸收剂利用率低,这是该法的主要缺点。
2.1.3简易湿式石灰石/石膏法烟气脱硫
简易湿式石灰石/石膏法烟气脱硫的原理与湿式石灰石石膏法脱硫原理相同,只是吸收塔为水平放置,空塔气速较高,烟气与吸收剂浆液垂直接触完成脱硫。
之所以称之为简易法式因为它处理的烟气量只占全部烟气量的80%以下,处理后的烟气与未处理的热烟气在进入烟囱前混合,使烟气温度升至露点以上在排放,省去了烟气再加热系统,节省了投资水平塔本身脱硫率可达95%以上,但由此混入未处理的热烟气后排放,使总的脱硫率超过80%。
2.1.4海水烟气脱硫
海水烟气脱硫是利用海水中固有的碱度吸收中和烟气中的SO2,吸收过SO2的海水,经海水恢复系统处理之后排入大海。
海水脱硫投资省、运行费用低。
缺点是占地面积大,系统存在腐蚀问题。
2.1.5电子束法烟气脱硫技术
电子束法烟气脱硫技术最早由日本荏原制作所于1971年开始研究,倒了20世纪80年代逐步工业化。
该法是利用电子加速器产生的等离子体氧化烟气中的SO2和NOx,同时与喷入的水和氨反应,生成硫铵和硝铵、脱氮的目的。
该技术的优点是反应速率快,在一个装置内同时脱硫、脱氮、副产肥料,实现了废物资源化,没有废水排放。
该工艺适应性强。
缺点是控制系统复杂,要求严格,能耗高。
2.1.6烟气循环流化床脱硫技术
烟气循环流化床脱硫技术是把固体流态化技术引入到FGD工艺中的一项新技术,在20世纪80年代以后有了很大发展。
烟气循环流化床是采用含湿量为3%~5%的石灰粉作为脱硫剂,在流化床中与高速流动的烟气接触完成脱硫。
在流化床尾部除下来的吸收剂经增湿后循环适用,以提高吸收剂的利用率。
烟气循环流化床脱硫技术发展很快,已出现了多种结构形式的装置,在钙硫比为1.1~1.5的情况下脱硫率可达80%~90%。
烟气循环流化床工艺系统简单,运行可靠,占地面积小,投资和运行费用低,无废水排放,是一种较好的干法脱硫工艺。
2.2废气除尘方法
2.2.1除尘器的分类
按除尘器分离捕集粉尘的主要机制,可将其分为如下四类。
1、机械式除尘器它是利用质量力(重力、惯性力、离心力)的作用使粉尘与气流分离沉降的装置,包括重力沉降室、惯性除尘器和旋风除尘器等。
2、电除尘器它是利用高压电场使尘粒荷电,在电场力的作用下使粉尘与气流分离的装置。
3、过滤式除尘器它是使含尘气体通过织物或多孔填料曾进行过滤分离的装置,包括袋式过滤器、颗粒层过滤层等。
4、湿式洗涤器它是利用液滴或液膜洗涤含尘气流,使粉尘与气流分离沉降的装置,它可用于除尘,也可用于气体吸收。
当专用于气体除尘时,也称湿式除尘器。
上述四类六种除尘器示于表2-1,表中分离区指除尘器内粉尘最后从含尘气体中分离出来的空间,简图中的虚线指示出分离界面。
表2-1四大类六种除尘齐的除尘过程
项目
机械力除尘器
电除尘器
过滤式除尘器
洗涤除尘器
捕
集
分
离
过
程
捕集阶段作用(力)
重力
惯性力
离心力
电力
惯性碰撞拦截
扩散
电力沉降
惯性碰撞
拦截
分离区与作用力
流动呆滞区重力
边壁上超极限负荷
外筒内壁超极限负荷
沉降极附着力
滤料层附着力
液体表面表面张力
按除尘效率的高低,可把除尘器分为高效除尘器(电除尘器、过滤式除尘器和高能文丘里洗涤器)、中效除尘器(旋风除尘器和其他湿式除尘器)和低效除尘器(重力沉降室、惯性除尘器)三类。
此外,还按除尘器是否用水分为干式除尘器与湿式除尘器两类。
近年来,各国十分重视研究新的高效微粒控制装置。
现代除尘装置的发展趋势是将多种捕集机制巧妙、综合应用于同一除尘过程,使其效率大为提高。
例如,童志权等开发的XP系列湿式除尘装置就综合利用了离心力、惯性力及液滴、液膜、气泡捕集的多种机理,使工业装置的除尘效率均能达到99%以上,达到了电除尘器的效果。
2.2.2除尘器的性能指标
表示除尘器性能的指标有下列六项:
1、处理含尘气体的量,是代表除尘器处理含尘气体能力大小的指标,一般用通过除尘器体的体积流量(m3/h或m3/s)表示;
2、除尘效率;
3、压力损失;
4、设备投资及运行管理费用;
5、占地面积或占用空间体积;
6、设备可靠性及使用寿命。
前三项属于技术指标,后三项属于经济指标。
2.2.3除尘器的压力损失
除尘器的压力损失△p(又称阻力)是气体流经除尘器时所消耗的总机械能。
流体的总机械能包括势能与动能,而势能又由位能和压能两项组成。
在除尘器内,由于高度变化不大,气体的重度较小,位能一般可忽略不计。
因此,总机械能e可用压能p和动能ρυ2/2之和表示,即
e=p+ρυ2/2
在除尘技术中,习惯以静压代表压能,以动压代表动能,两者之和称为全压,代表总机械能。
因此,除尘器的压力损失一般用除尘器进,出口断面上齐鲁平均全压之差△p(Pa)表示。
除尘装置的阻力主要和流速、流动状态、流体性质、流道大小及形状等因素有关。
不同类型除尘器的阻力计算式是不同的,后面将分别介绍。
由于通风机所耗功率与除尘器的阻力成正比,所以总希望其值小些。
2.2.4各种除尘器的介绍
1重力沉降室
结构如图2-2所示,含尘气流进入后,粉尘借本身重力作用向底部自然沉降。
要使具有沉降速度为vs的尘粒在沉降室内全部沉降下来,必须使气流通过沉降室的时间L/v大于或等于尘粒从顶部沉降到底部灰斗所需的时间H/v,即
式中L——除尘室长度,m;
H——沉降室高度,m;
v——沉降室内气流的水平运动速度,m/s。
当沉降室的实际高度H大于粉尘的沉降高度h(=vsτ)时,可用h/H表示沉降室的分级效率
重力沉降室结构简单,投资少,性能稳定可靠,维修管理容易,压力损失小(50~150Pa),但设备庞大,效率低。
适用于净化密度大]颗粒粗、磨损强的粉尘。
设计好时能捕集40~50μm以上尘粒,不宜于捕集20μm以下尘粒。
常用作多级净化系统的第一级粗净化。
㈡惯性除尘器
惯性除尘器是使含尘气流冲击在挡板上,或让气流方向急剧转变,使尘粒受惯性力作用而从气流中分离出来的一种除尘装置。
起除尘机制示于图2-3。
冲击到挡板B1上的尘粒当中,惯性力大的粗尘d1首先被分离下来,而被气流带走的尘粒(如d2,d2<d1)由于挡板B2使气流方向转变,借离心力作用又被分离下来,烟气中带走的尘粒d3<
d2。
假设气流的旋转半径为R2,切线速度为v0,则根据下式,尘粒d2所具有的离心分离速度为
可见,这类除尘器实际上同时利用了惯性力、离心力和重力的作用。
惯性除尘器宜用于净化密度和粒径较大的金属或矿物粉尘,不宜用来净化粘性和纤维性粉尘。
由于气流方向转变次数有限,净化效率不高,也常用作多级除尘中的第一级,用以捕集10~20μm以上的粗尘粒。
压力损失依形式而定,一般为300~700Pa。
㈢旋风除尘器
旋风除尘器是利用含尘气流旋转运动产生的离心力从气体中分离尘粒的装置,又称离心式除尘器,它结构简单,体积小,不需特殊的附属设备(洗涤器要求供水及污水处理装置,过滤式和电力除尘器要振打清灰装置,电力除尘器还要高压整流电源等),因而造价低,除尘效率高,适应粉尘负荷变化性能好,可用于高温干尘烟气的净化,无运动部件,运行管理简便,广泛应用于个工业部门,已有近100年的历史和100种以上的形式。
但是,旋风除尘器难以捕集5μm以下的粉尘粒子,其阻力也比重力沉降室和惯性除尘器高。
㈣湿式除尘器
湿式除尘器是用水或其他液体与含尘气体互相接触使粉尘粒子被捕集的装置,也能用于气体吸收及气体的降温、加湿、除雾(脱水)等操作中,这是其他类型的除尘器所起不到的作用。
湿式除尘器简单、造价低、效率高,适宜净化非纤维性和不与水发生化学反应的各种粉尘,尤其适宜净化高温、易燃和易爆的含尘气体。
但存在设备及管道的腐蚀、污水和污泥的处理、因烟温降低而导致的烟气抬升减少及冬季排气产生冷凝水雾等问题。
湿式除尘器有时又称为湿式气体洗涤器。
图2-4为湿式除尘器的工作机理。
㈤电力除尘器
电力除尘器是利用静电力实现粒子(固体或液体粒子)与气流分离沉降的一种除尘装置。
电除尘器的除尘过程可分为以下四个阶段:
(1)、电晕放电在电晕极(又称放电极,若为负电晕则接电源负极)与集尘极(又称收尘极,接地为正极)之间施加直流高电压,使放电极发生电晕放电,气体电离,生成大量自由电子和正离子。
正离子被电晕极吸收而失去电荷,与自由电子一起被气流中的负电性气体分子俘获后形成的气体负离子,在电场力的作用下向集尘极(正极)移动便形成了空间电荷。
(2)、粒子荷电通过电场空间的气溶胶粒子与自由电子、负离子碰撞附着,边实现了粒子荷电。
(3)、粒子沉降在电场力的作用下,荷电粒子被驱往集尘极,在集尘极表面放出电荷而沉集其上。
在电晕区内,由电晕放电产生的气体正离子向电晕极运动的路程极短,只能与极少数的尘粒相遇,使其荷正电,它们也将沉集在截面很小的电晕极上。
(4)、粒子清除用适当方式(振打或水膜等)清除电极上沉集的粒子。
为保证电除尘器在高效率下运行,必需使以上四个过程十分有效地进行。
图2-5为电除尘器的除尘过程的示意图。
㈥过滤式除尘器
过滤式除尘器有内部过滤和表面过滤两种方式。
所谓内部过滤是把松散的滤料(如玻璃纤、金属绒、硅砂和煤粒等)以一定体积填充在框架或容器内作为过滤层,对含尘气体进行净化,尘粒是在过滤材料内部进行捕集的。
颗粒层过滤器和作为空调用的纤维填充床过滤器属内部过滤式。
表面过滤是采用织物等薄层滤料,将最初粘附在织物表面的粉尘初层作为过滤层,进行威力的捕集。
由于织物一般作成袋形,固又称袋式过滤器。
袋式除尘器的除尘过程:
织物滤料本身的网孔一般为10~505μm,表面起绒滤料的网孔也有5~105μm,因而新鲜滤料开始使用时滤尘效率很低。
但由于粒径大于滤料网孔的少量尘粒被筛滤阻留,并在网孔之间产生“架桥”现象;
同时由于碰撞、拦截、扩散、经典吸收和重力沉降等作用,一批粉尘很快被纤维捕集。
随着捕尘量不断增加,一部分粉尘嵌入滤料内部,一部分覆盖在滤料表面上形成粉尘初层(见图2-6)。
由于粉尘初层及随后在其上继续沉积的粉尘层的捕集作用,过滤效率剧增,阻力也相应增大。
袋式除尘器之所以效率高,主要是靠粉尘层的过滤作用,滤布只起形成粉尘层和支撑它的骨架作用。
随着集尘层不断加厚,阻力愈来愈大,这时不仅处理风量将按所用风机和系统的压力-风量特性下降,能耗急增,而且由于粉尘堆积使空隙率变小,齐鲁通过的速度增加,增加到一定程度后,会使粉尘层的薄弱部分发生“穿孔”,以致造成所谓的“漏气”现象,使除尘效率降低;
阻力太大时,滤布也容易损坏。
因此,当阻力增大到一定值时,必须清除滤料上的集尘。
但由于部分尘粒进入织物内部和纤维对粉尘的粘附及静电吸引等原因,滤料上仍有部分剩余粉尘,所以清灰后的剩余阻力(一般为700~1000Pa)比新鲜滤料的阻力大,效率也比新鲜滤料的高。
为保证清灰后的效率不致过低,清灰时不应破坏粉尘初层。
清灰以后,有开始下一周期的过滤
3烟气除尘脱硫工艺综合评价与推荐方案
在选择脱硫工艺时应考虑以下主要因素:
①设备投资;
②环保要求;
③系统所占场地面积;
④吸收剂来源;
⑤水源问题;
⑥脱硫系统的电耗;
⑦燃煤含硫量;
⑧脱硫渣的处理与利用。
3.1计算锅炉的蒸发量、烟气量、组成和物料衡算
现从设计蒸发量为650t/h的燃煤锅炉的现场取得的燃煤组成(质量比)如下:
C=65.7%;
灰分=18.1%;
S=1.7%;
H=3.2%水分=9.0%;
O=2.3%(含N量不计)。
从《大气污染控制工程》查得锅炉热效率=75%,空气过剩系数为1.2,低位发热量=20939kj/kg,水的蒸发热2570.8kj/kg,烟尘的排放因子为30%[2]。
解:
锅炉燃煤量、烟气排放量及组成
3.1.1锅炉燃煤量
已知煤的低位发热量为20939kj/kg,水的蒸发热为2570.8kj/kg,则蒸发量为650t/h的锅炉所需热量为2570.8×
650×
10³
=16.7×
108kJ/h,需煤量为
表3-1烟气排放量及组成(以燃烧1kg煤为基础)
各组分
C
S
H
O
水分
灰分
重量/g
657
17
32
23
90
181
质量/mol
54.75
0.53
16(分子)
0.72(分子)
5
需氧/mol
8
-0.72
理论需氧量:
54.75+0.53+8-0.72=62.56mol/kg(煤)
理论空气量:
62.56×
(3.76+1)=297.79
=297.79×
2.24×
10-3
=6.67m³
/kg(煤)(标志)
理论空气量下烟气组成(单位:
mol)
CO2:
54.75SO2:
0.53H20:
16+5N2:
3.76
理论空气量
54.75+0.53+16+5+62.56×
3.76=311.51mol/kg=6.98m³
/kg
实际烟气量(标志)6.98+6.67×
(1.2-1)=8.31m³
106.3t/h煤的烟气量(标志)106.3×
103×
8.31=8.83×
105m³
/h
烟气组成(标志):
Cso2=0.53×
64×
103/8.31=4082mg/m³
C烟尘=(181/8.31)×
30%=6534mg/m³
3.1.2确定烟气除尘脱硫工艺并进行物料衡算
锅炉烟气除尘脱硫工艺与脱硫方法有关,对于干法(吸附法)脱硫,粉尘须在脱硫除SO2之前除去,以防吸附剂中毒;
湿法(液体吸收法)脱硫,可采用先除尘后脱硫、先脱硫后除尘或除尘脱硫同时进行工艺,应根据实际情况选择。
可行的途径有:
①利用现有除尘设备,设计SO2脱除装置。
②取消现有除尘设备,设计脱硫、除尘新系统。
本设计拟采用现有除尘设施、后加脱硫装置的工艺,其流程为:
锅炉烟气锅炉烟气除尘设施脱硫设施烟囱。
物料衡算:
GB16297-1996中规定二类区:
TSP≤250mg/m³
SO2≤700mg/m³
据此得:
250mg/m³
(标志)
出口粉尘
粉尘入口η≥96.2%
6534mg/m³
图3-1
除尘量(6534-250)×
8.83×
105×
10-6=5548.8(kg/h)
η≥82.8%
脱硫系统
除尘系统
入口SO2浓度出口SO2浓度700mg/m³
图3-2脱硫计算示意图
4082mg/m³
(标态)脱硫量(以SO2计)(4082-700)×
105×
10-6=2986.3(kg/h)
计算结果示下图(标态)
脱硫
除尘
Q=88300m³
锅炉Cso2=4082mg/m³
排气