导热油炉操作规程Word格式文档下载.docx
《导热油炉操作规程Word格式文档下载.docx》由会员分享,可在线阅读,更多相关《导热油炉操作规程Word格式文档下载.docx(19页珍藏版)》请在冰豆网上搜索。
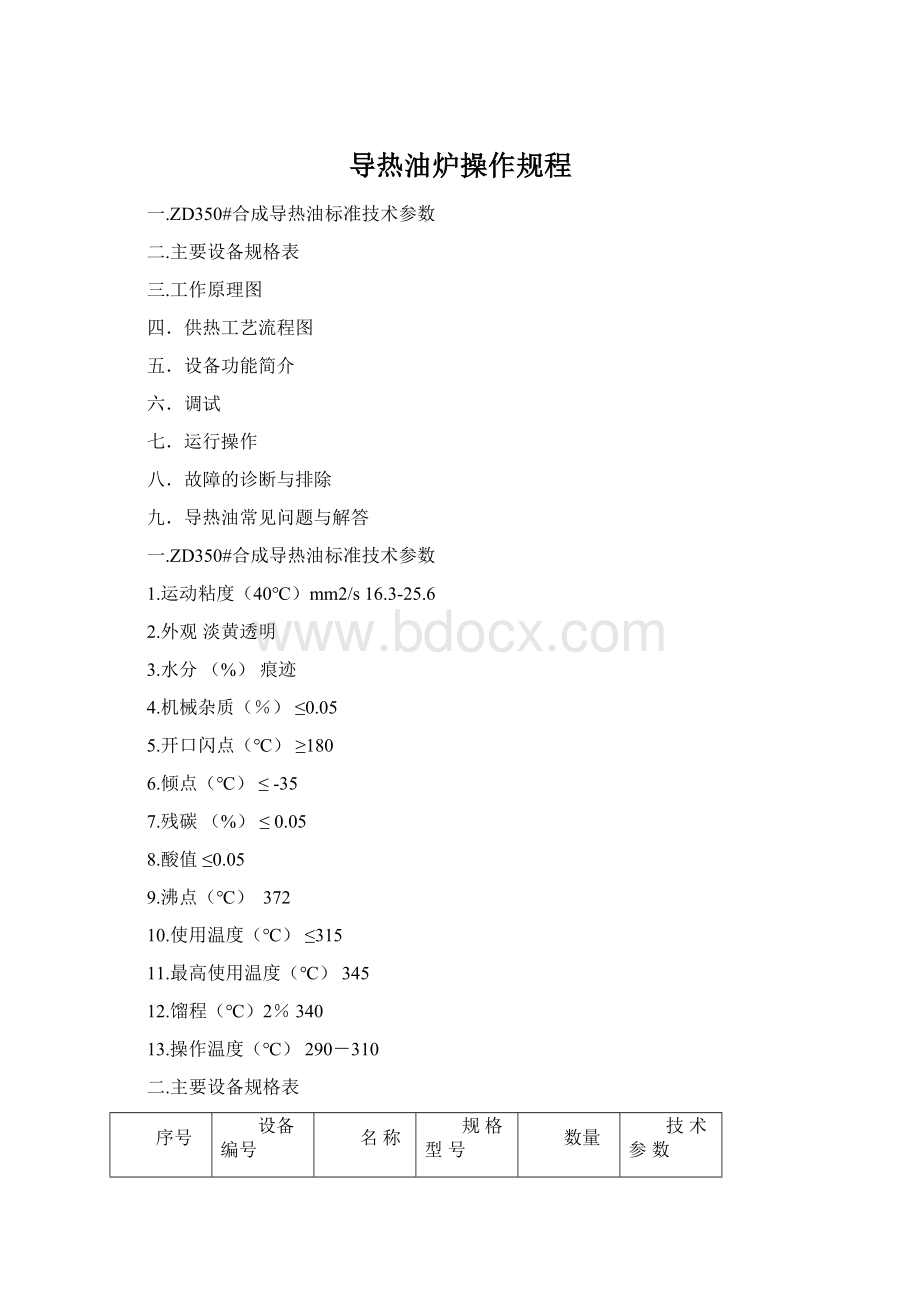
162℃;
烟气进口温度:
360℃;
烟气出口温度:
245℃;
空气流速:
6.5m/s;
烟气流速:
11m/s;
受热面积:
25m2
3
MC-1/2
陶瓷多管除尘器
XTD-4
进口流速:
<
20m/s;
阻力:
900pa;
除尘效率:
>
95%;
处理烟气量:
12800m3/h
4
V-1
储油槽
10m3
1台
设计温度:
200℃;
工作介质:
导热油;
容器类别;
常压;
主体材质:
Q235AF;
公称容积;
10m3;
5
V-2
膨胀槽
8m3
8m3;
6
X-1/2
调速箱及电机
ZW700-A
7
X-3/4
提升式上煤机
STM-200
8
X-5/6
螺旋除渣机
CZX6-3.1右旋
9
P-1/2/3
热媒循环泵
WRY125-100-250
3台
操作流量:
200m3/h;
操作温度:
280℃,最高320℃;
操作压力:
扬程:
60m;
电机:
Y250M-2/55,55KW;
防暴防护等级IP44;
填料密封或机械密封;
10
P-4/5
注油泵
2CY-3.3/3.3-1
3.3m3/h;
60℃;
0.32MPa;
32m;
Y100L1-4,2.2KW;
填料密封;
11
F-1/2
鼓风机
T4-72NO4A右0度
鼓风量:
4040-7460m3/h,风压:
2000-1265Pa;
工作温度:
45℃;
联轴转动,电机:
Y132S1-2,5.5KW
12
F-3
引风机
YX9-35-12NO8C右0度
引风量:
17245-19342m3/h,风压:
2854-2903Pa;
皮带转动,电机:
Y180L-4,22KW
13
F-4
YX9-35-12NO8C左0度
三.工作原理图(图一:
注入式工作原理图)
四.供热工艺流程图、轴测图〔详见附图〕
①加热炉
加热炉是加热炉系统的主机部分,有机载热体由此获得热源。
主机分为炉本体与燃烧室两大部分。
炉本体又分为圆型和箱型。
中小型炉本体采用阀筒型结构,大型炉本体采用箱型结构。
燃烧室下部设有落灰装置。
燃烧室的炉排部分采用链条炉排型式,并设有四档速度调速箱,另有上煤、出渣、除尘、鼓风、引风等辅助设备。
②热油循环泵
热油循环泵是导热油闭路强制循环的动力,要求每台加热炉配置两台泵,其中一台为备用。
我公司热油循环泵根据实际运行情况进行开备。
③膨胀槽(高位槽)
膨胀槽用作导热油因温度变化而产生体积变化的补偿,从而稳定系统载热体的压头,同时还可以帮助系统脱水排气,因此膨胀槽应设置在比系统其他设备或管道高出1.5~2m标高处。
正常工作时应保持高液位状态,当突然停电或热油循环泵发生故障而需紧急停炉时,可以将冷油置换阀打开,此时高位槽的冷油利用其位能流经炉管而入贮油槽,从而防止炉管内导热油超温过热。
④贮油槽(低位槽)
贮油槽主要用来贮存高位槽、炉管及系统排出的导热油。
正常工作时应处于低液位状态,随时准备接受外来导热油。
排气口(呼吸口)应接至安全区,且不得设置阀门(用氮气保护的系统除外)。
⑤注油泵(齿轮泵)
2CY齿轮注油泵,用来向系统补充或抽出导热油。
泵体上箭头方向应是主轴旋转方向,也是介质的流动方向。
⑥滤油槽(Y型滤油器)
滤油器用来过滤并清除供热系统中的异物。
⑦油气分离器
油气分离器用来分离并排除供热系统中的空气、水蒸气及其他气体,从而确保导热油在液相无汽水的状态下稳定运行。
⑧安全阀
安全阀应设置在加热炉主管线上,且与炉本体之间不得设置阀门,安全阀主要用来防止阀门的误操作而引起的导热油升温超压。
⑨燃烧系统辅机
燃烧系统辅机的使用请参照相应的使用说明书,在此不怍说明。
⑩其它仪表、电器控制系统
调试是进一步考证安装质量、系统工作性能和熟悉操作要领、保证正常运行的重要工作,应由管理人员、技术人员、操作人员共同参加,在设备初次启动后的运行中,应对设备工况进行测定和记录,以保证今后系统的正常运行。
调试工作分冷态和热态两个步骤进行。
6.1冷态调试
⑴目的
●检查各单元设备的运转正常与否。
●检查冷态条件下的系统运行正常与否。
●使操作工熟悉和掌握操作要领。
⑵要求
●炉排冷态运行4~8小时,无异常,操作机构调节灵活。
●所有电机转向正确,设备负荷正常,动作正常,连续运行2小时以上。
●循环油泵在水压试验前应进行冷态调试。
●做好调试运行记录,及时排除可能出现的故障。
●做好调试前的一切准备工作。
⑶冷态调试步骤
●检查所有设备及管线安装是否符合图纸要求。
●检查系统试压冲扫是否符合要求。
●检查电器系统及控制仪表是否接妥。
●将减速机、热油循环泵轴承箱及其它转动机构根据要求注入润滑油或润滑脂。
●用手转动电机主轴、检查有无机械故障。
●将各运动机构单机试运行,检查设备运转方向是否正确,声音是否正常。
●炉排调速箱安全离合器的压力弹簧松紧调整适当。
●调节系统各个阀门,为注油、试车做好准备。
●注油泵向高位槽注油。
●启动热油循环泵。
●观察热油循环泵进出口压力、炉本体压降及进出口油温,排烟温度等仪表的工作显示是否正常。
●冷态运行连续四小时以上,如无异常现象,主可进行热态调试。
注意事项:
(1)开启注油泵向高位槽注油,直至高位槽低液位不报警,关闭注油泵,启动热油循环泵开始冷油循环,打开高位槽放空阀,经常开启管道放空阀,不断排出空气,及时补充高位槽内导热油,保持一定液位。
(2)冷油循环时间不少于4小时,观察油循环泵进出口压力及系统压力表、温度表等仪表显示是否正常,直至压差波动转向平稳,检查系统内无泄漏和阻塞现象,清理过滤器2-3次后方可进行热态调试。
6.2热态调试
热态调试应包括用热设备在内的运行操作,请按下表内容循序渐进。
方法
要领
判据
注
油
接通电源,启动注油泵,向膨胀槽注油,直到低液位不报警,关闭注油泵,启动循环油泵
掌握各阀门的正确操作方法,及时补充膨胀槽导热油,经常开启管道放空阀门排出空气。
待预算的导热油量全部进入系统后,膨胀槽低液位不报警,储油槽内液位显示为少量油液。
冷
循
环
循环油泵不断运转,初步排出系统内空气时间为6~8小时,清除过滤器内杂物2~3次。
检查压差波动情况,经常开启系统放空阀门。
检查过滤器有无阻塞。
出现循环油泵吸空时,可停运2~3分钟然后再启动。
压差波动转向平稳。
放空阀排出的油液中无气体。
系统无漏点和阻塞现象。
点
火
用不带铁钉等金属的木柴,均匀铺在炉排上引燃,并控制燃料量。
循环油泵保持不吸空,温升控制在10℃/h且不超过50℃。
从观火门观察开始正常燃烧。
上
煤
用手工向炉内均匀铺撒干煤。
逐步过渡用煤斗饲煤。
煤质粒度<
40mm,但<
6mm粉煤不超过50%,含水控制在8~10%,上煤不得使用自动控制。
烘
炉
按升温曲线要求进行,油温控制在100℃以下,运转72小时左右(或根据实际情况规定运行时间)
炉膛的烘干情况。
注视压差波动情况和循环泵不吸空。
逐步排除油液中的气和汽。
炉墙保温层含水量<
7%
压差由波动转向平稳排气明显减少。
煮油
〔脱水排气〕
按升温曲线要求进行。
油温控制在125~150℃连续运转48小时(或根据实际情况确定运行时间
检查系统泄漏点和阻塞现象,以及热膨胀情况。
油中水份在此间汽化,重点去除油中水份和低挥发成份。
压差波动由剧烈转向平稳,经过重新紧固的法兰密封面已不产生泄漏,各部机械运转正常(热油循环泵吸空时可停运0.5~1分钟)。
升
温
按升温曲线升至额定工作温度。
控制在10℃/h的温升速率
全面检查各控制仪表计的正确显示。
各项指标达到满足生产要求。
6.3升温曲线(见图2首次开炉升温曲线图)
说明:
(1)点火:
用不带铁钉等金属的木柴,均匀铺在炉排上引燃,并控制燃烧量,使油循环泵保持不抽空,油升温速率控制在10℃/h左右。
(2)上煤:
用手工向炉内均匀铺撒干煤,逐步过渡用煤斗上煤,从观火门观察炉内燃烧情况。
确保炉火燃烧平稳、均匀,无断火现象。
(3)烘炉:
按升温曲线要求进行,油温控制在105℃以下注意观察循环油泵进出口压差波动情况,如出现循环油泵吸空,可停运2-3分钟,再重新启动,观察炉膛烘干情况,以上三点指燃煤锅炉(新炉),燃油锅炉可参照第3点(烘炉),要严格控制进油量与时渐进按升温曲线控制热油温度。
(4)脱水排气:
按升温曲线进行,油温控制在120℃-150℃,在此期间重点除去油中水分和低挥发成分,随着温度升高至200℃以上时,系统法兰连接处可进行热紧固,热油泵吸空可停运0、5-1分钟,再重新启动。
低位槽、高位槽放空阀全部开启,直至压差由波动转向平稳,排气明显减少(其间脱水应严格注意压力表的摆动情况,如有摆动应停止加温当恢复正常后方可继续加温)。
。
以确保导热油中产生的水蒸气不重新凝结成水,系统中水份多少,一般决定于冲扫程度,水份积存越多煮油时间越长。
如未将油中气、水脱尽,则加热炉不可能正常供热,此为导热油液相强制循环供热的最基本要求,应特别重视脱尽油中水、气这一工作。
(5)升温:
升温速率控制在10℃/h左右,使油温度逐步升至260℃左右,并全面检查各控制仪表的正常显示。
(如有辅助排气阀,正常使用后必需关闭)
6.4注意事项
⑴压差不稳定时,不得投入使用。
⑵停炉时,油温应降至80℃以下时,热油循环泵方可停运。
⑶高温状态时要确保导热油循环良好。
⑷正常工作时,高位槽内导热油应保持高液位,贮油槽内导热油应处于低液位。
⑸应按规定对各机械润滑点注油。
⑹出油温度不得超过导热油的允许工作温度。
⑺紧急停炉时,不得用水重浇炉膛。
⑻保证出渣机水密封良好。
⑼不符合要求的煤块不得加入煤斗,同时注意出渣口煤渣结块,而影响出渣。
⑽不同品种导热油一般不得混用。
⑾贮油槽的放空接口应引至安全区。
⑿首次升温速度必须按升温曲线进行。
⒀启动鼓风机前应先开引风机,停止引风机前应停止鼓风机。
⒁应建立设备运行台帐。
⒂锅炉房应配备电器、油类消防器材。
经过专业培训已取得了操作证和参加过调试运行的司炉工,基本已掌握了操作技能,但还必须在实践中定期总结经验,不断提高运行水平。
(可参照《JX-GR-L(G)(10~700)图供热工艺流程图》说明)
7.1燃烧正常工况标志
火床平整、火焰均匀,呈亮黄色,无空冷风口、无焦块,着火处距煤闸门200~400mm,燃烧段整齐一致,在老膺铁(或出渣口前)500mm处烧尽,排烟呈显黄色,排烟温度在规定范围内,炉膛负压保持在19.6~29.4Pa(2~3mmH2O水柱)。
7.2上煤与出渣
⑴煤质要求
低位发热量>
18.8MJ/kg(4500Kcal/kg)的烟煤,粒度≤40mm,且<
6mm的煤粉不超过50%;
含水控制在<
10%;
灰份为10~25%,不得>
30%;
挥发物≥20%;
灰熔点1000℃。
⑵煤层厚度
控制在90~120mm,视煤质和供热要求调整煤闸门进行控制,煤量不得超过额定供量(折成标准煤计算)。
⑶炉排运行速度
以煤燃烧尽和不在煤闸处着火为准,通过带动炉排运转的调速器进行调节,一般为四档速度。
大型炉可采用无级调速器。
⑷出渣
开车时应先开动出渣机,后开动炉排;
先停炉排,后停出渣机顺序操作,保证出渣完全。
操作时必须保证水密封良好。
7.3风量调节
应按先开引风机,后开鼓风机,先停鼓风机,后停引风机顺序操作。
风量调节,必须与供热量匹配,是通过调节风门或停、开鼓、引风机实现的。
7.4热能输送的调节
⑴出口油温的调节
将电控柜上出口油温显示控制表调至所需工艺温度范围,步骤如下:
此表具有上、下限设定,预调时先将设定开关拨至“下限”,旋转下限设定旋钮至所需工艺温度的下限值,再将设定开关拨至“上限”位,旋转上限设定旋钮至工艺所需温度的上限值,最后把测量/设定开关拨至“测量位”,即显示出口油温。
当鼓、引风机置“自动”位,出口油温低于下限温度(t1≤t2)绿灯亮,鼓、引风机自动投运;
当出口油温处于上、下限温度之间(t2L≤t2≤t2H)灯不亮,鼓、引风机仍继续运行。
当出口油温超过上限温度(t2≤t2H)红灯亮,并发出报警信号。
此时鼓、引风机停运。
排调速机经断电延时继电器,延时一段时间后停转,炉膛内煤的燃烧程度降低。
当出口油温回到上、下限温度之间,鼓、引风机继续停运,降到低于下限温度时,鼓、引风机再自动投运,使出口油温保持在设定范围内,又免使鼓、引风机运、停频繁。
⑵导热油进出炉压力表的调节
一定的循环油流量,对应一定的压差(△P),压差是为检测导热油循环量而设。
当循环流量下降时,压差也相应减少,故在使用前先在压差表上设定一压差值(一般在40~80Kpa范围内),预调时先将测量/设定开关拨到“设定”位置,旋转设定旋钮到正常工况值,再将开关拨到“测量”位置,即指示进、出油炉的压力差,此值应大致与进、出油炉压力表值相一致(△P≈P1-P2),如发现相差较大,可在循环泵停运时,调速仪表背面的调另电位器,使其在测量位时显示导热油进出口之间的静压值。
当导热油流量因某种原因下降,压差表显示低于设定值,为防止导热油局部过热、结焦,应降低燃烧程度,故当鼓、引风机置于“自动”位时,鼓、引风机自动受控停运,红灯亮,并发出报警信号。
7.5突然停电、冷油置换
当循环油泵因停电不能运转时,炉管内油温由于炉膛余热作用,在1~2分钟内炉内导热油就会超过允许值,这时应迅速打开冷油置换阀门,把膨胀槽的冷油,经过炉内,自流至储油槽内,同时进行湿煤压火或紧急停炉处理。
此过程应在5分钟内完成。
务必注意:
勿将膨胀槽内的油放尽,以免系统吸入空气,可以预先将膨胀槽内的油液放至储油槽,当膨胀槽内的油液即将放完而未放尽时,在贮油槽液位计上作一油液液位标记,进行冷油置换操作时,当贮油槽油位趋于标记时,关闭冷油置换阀。
7.6停炉
(1)紧急停炉:
热油循环泵必须继续运行,此时停止送煤和鼓风,炉排快速将红煤送出,若停电用湿煤压火或蒸汽压火。
(2)计划停炉:
热油循环泵必须继续运行,停止送煤和鼓风,炉排继续运转,烧尽余煤送出后停引风,待油温低于80℃时停止循环油泵。
7.7导热油的补充与更换
当低液位报警时,应及时补充导热油。
7.8电气控制
(1)循环油泵
始终保持单机运行,由开、停按钮操作,运行时指示灯亮,进、出炉的循环压力由压力表监视、工作电流由电流表监视,泵机出现故障时由压差表报警。
(2)鼓、引风机
手动位置由开、停机按钮操作,运行时指示灯亮
受出口油温控制,温度超过上限自动停运,温度低于下限自动投运,且引风机先于鼓风机投运(0.7MW/h以下炉无此功能)
自动位置受压差表控制当压差低于设定值时自动停运;
当压差高于设定值时自动投运。
(3)上煤机
由煤斗上升、下降按钮分别操作,在上、下极限位置串由自停开关,用颜色不同的升、降指示与按钮配合。
(4)炉排调速机
采用两档机械变速,再配双速电机,共四档变速,由炉排快运和炉排慢运分别操作,用不同的颜色信号指示。
(5)出渣机
由开、停按钮操作,运行时指示灯亮
(6)注油泵
(7)液位开关
装设在膨胀槽上,当其油位呈低液位时,低液位指示灯亮,发出报警信号,此时应开启注油泵向膨胀槽注油,直至“低液位”消除
(8)压差表
压差值按不同系统预调至设定值,小于设定值时能使处于“自动”位的鼓、引风机停运,同时报警
(9)出口油温表
显示出口油温预先根据工艺温度设定上、下限温度值,超过上限温度值时红灯亮,低于下限温度值时,绿灯亮,正常时灯不亮,控制鼓、引风机运、停见
(2)
(10)回油温度
显示释放热量后回到加热炉的油温
(11)炉本体回烟温度,预热空气温度、排烟温度
由显示温度表进行显示,并与其余各点温度共用一表,用转换开关人工切除
(12)报警
凡膨胀槽液位低于规定、压差低于设定值,出口油温超过设定值上限,均发出声、光报警信号,为避免噪音,在按下“消除报警”按钮后,声音报警信号消除,但报警信号保持,直至参数恢复正常。
(13)为防止因未及时消警,致使警铃通电时间较长而烧坏,故警铃的安装位置必须在工作人员听得到的位置,以免发生不必要的事故。
(14)总电源
由空气自动开关进行,总电源的启闭由红灯指示。
1.炉本体及循环系统
故障现象
故障原因
排除方法
加热炉进出口油温差超过给定值(由试验和运行确定)
循环泵供油量下降
超负荷运行
导热油变质
加热炉与供热设备不匹配
保温不良
油中含有气、汽
消除油泵及管路故障
降至正常负荷运行
换新油
合理选用燃煤加热炉
重新保温
继续脱气、汽
输送油管内发现气锤声,进出口压力表指针摆动
补充新油时混入空气未脱尽
膨胀槽低液位报警
管路系统(包括油炉)漏油或脱气后未及时补充油液
消除系统缺陷
补充新油
压差低于给定值
循环油泵吸空
导热油中含汽
过滤器阻力大
加热炉管漏油
消除油泵及管路缺陷
进行煮炉脱气
清洗过滤器
检查炉内加热盘管
管路油循环不畅通
过滤器堵塞
导热油粘度增加
阀门未全打开
管内留有余物
补充或更换导热油
打开阀门
清除管内杂物
2.燃烧系统
可能原因
炉膛向外冒烟
烟道堵塞
鼓、引风机风量调节不当
疏通烟道,清除除尘器积灰及炉内灰槽积灰
调整风压、风量保持炉膛19.6~29.4pa负压(2~3mmH2O)
炉排卡住
炉排跑偏
炉排在链轮外拱起与侧密封角钢卡住
炉排断裂
铁器进入炉排
严重结焦
调节左右螺母,使炉排松紧一致
调节炉排松紧合适,或抽掉一列炉排片,均匀间隙
更换断裂排片清除铁器
设法排除铁器
打焦或换煤种
炉排过烧、烧坏两侧炉排、两侧板过热发生弯曲
压火时间过长
两侧负量过长
避免长时间压火
调整密封块,均匀风量
炉排长销与炉排侧板卡住,导致长销弯曲
长销两端与两侧板间距不相等
两侧间距调至相等
烟囱冒黑烟
燃煤不完全
煤粉比例过大
调整风量适当
控制煤粒细度、并加适量水份
炉尾前煤未燃尽
尾窗风量不足
煤质特性与炉排速度不适应
打开尾窗风口,加强拨火
调整炉排速度
炉排漏煤严重
炉排损坏
炉排间隙大
燃煤粉粒比例过大
更换炉排片
调整炉排间隙
燃煤需经筛选
排烟温度过高出力降低、耗煤增
炉管积灰严重
炉内反射烘顶损坏,烟气短路
导热油失效
采用清洗剂,清除炉管积灰
清除烟气短路缺陷
更换导热油
九.热传导液常见问题与解答
9.1传导液的报废指标有哪些?
答:
一般使用半年后,每隔2-3个月化验一次。
粘度变化大于15%,闪点低于130℃,酸值大于0.5mgkoH/g,残碳达到1.5%以上应引起注意,其中有一项指标超标应考虑更换。
9.2热传导液可否混用?
从热传导液的使用性能看,纯度越高,馏程范围越窄,其热稳定性越好。
一个混合物的热稳定性是由其中热稳定性较差的组分决定的。
因此热传导液可否混用必须遵循科学的方法。
即采用SH/T0680-1999热传导液热稳定性测定法试验方法进行评价。
根据实验分析数据做出判断。
9.3如何通过日操作和管理延长热传导液的使用寿命?
如果整套系统设计合理,配套适当,热传导液产品质量符合SH/T0677-1999,热传导液标准,延长使用寿命的关键在于日常的操作管理提供以下几点可供参考。
℃左右,不要超过80℃。
℃以下方可停泵,防止导热油局部过热。
9.4在加热系当中为什么要设膨胀槽,有何意义;
惰性气体密封有何意义?
因加热系统中被加热介质受热膨胀体积发生变化,因此需容纳介质受热的膨胀量,新装入的产品中轻组分和运行中产生的低沸物的排空、补充蒸发及操作损耗,惰性气体密封(以氮气为主)及液相密封等,在实际使用中,当使用温度超过最高设计温度,膨胀槽必须氮封。
其主要作用是防止导热油因接触空气而氧化,致使导热油提前报废。
一般来说热传导液的氧化可通过系统的设置操作及加入高温抗氧剂加以控制,如升高高位槽的位置(但最高温不能超过六米左右),采用小口径膨胀管以及冷热油置换、控制膨胀槽温度低于70℃(一般情况下,在投入正常使用后关闭辅助排气阀门就能解决)。
如热传导液的初馏点低于系统的最高使用温度,有可能造成泵的气蚀和较大的损耗,这种情况下须采用惰性气体密封。
9.5何谓导热油的再生?
所谓再生,是将使用到一定程度,但尚未报废的热传导液经适当处理,使之基本达到原产品的指标。
处理方法一般使用减压蒸馏,除掉高沸物和低沸物,然后精制、脱色。
还有一种方法是化学分离法,其处理方法一般是经化工助剂分离、沉降、高目数过滤、中和、再次加入部分功能剂调和而成。
应该注意的是:
部分再生或部分更换应根据日常检验,掌握好时机,如果热传导液已严重老化,可能造成设备结焦,必须彻底更换。
9.6何种原因可造成传热系统发生事故,如何避免?
热传导液为可燃性有机物,具有着火和爆炸的潜在危险,分析事故原因,主要以下几种可能:
9.7为什么要安装旁路过滤器?
热传导液在运行中由于热裂解和热聚合会产生胶质、沥青和细小炭粒,这些物质数量逐渐增加会导致设备结焦和一系列操作问题。
通常在泵前设置以金属丝网过滤器只能除掉机械杂质和污物,如在系统中安装一旁路过滤器,则可在不停车的情况下随时将胶质、沥青质和炭粒滤除。
从延长热传导液使用寿命的角度考虑,最好在开车前就设置合适的旁路过滤器,并连续使用,如果油品已经变质。
可及时加设旁路过滤器采用不同孔径的滤芯从粗滤到细滤逐渐更换。
9.8哪些检验项目可说明运行中热传导液的变质情况?
运行中定期检验的目的