连杆大小头双端面铣削组合机床及夹具设计docWord文件下载.docx
《连杆大小头双端面铣削组合机床及夹具设计docWord文件下载.docx》由会员分享,可在线阅读,更多相关《连杆大小头双端面铣削组合机床及夹具设计docWord文件下载.docx(21页珍藏版)》请在冰豆网上搜索。
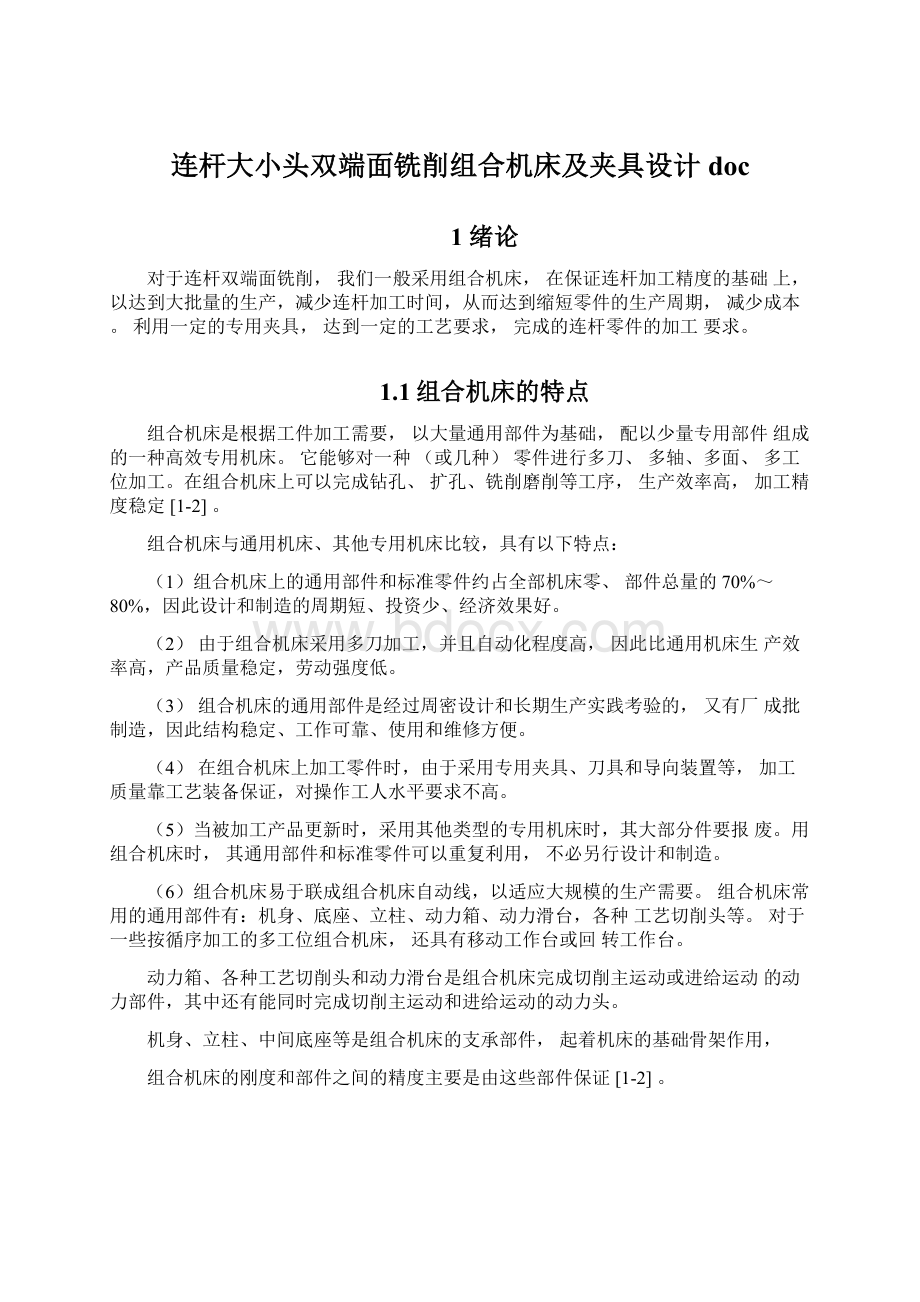
(1)制定工艺方案要深入现场了解被加工零件的加工特点、精度和技术要求、定位夹紧情况以及生产率的要求等,确定在组合机床上完成的工艺内容及其加工方法。
这里要确定加工工步数,决定刀具的种类和型式。
(2)机床结构方案的分析和确定根据工艺方案确定机床的型式和总体布
局。
在选择机床配置型式时,既要考虑实现工艺方案,保证加工精度,技术要求及生产效率;
又要考虑机床操作、维护、修理是否良好;
还要注意被加工零件的生产批量,以便使设计的组合机床符合多快好省的要求。
(3)组合机床总体方案这里要确定机床各部件间的相互关系,选择通用
部件的刀具的导向,计算切削用量及机床生产率。
给制机床的总联系尺寸图及加工示意图等。
(4)组合机床的部分方案和施工方案制定组合机床流水线的方案时,与
一般单个的组合机床方案有所不同。
流水线上由于工序的组合不同,机床的型式和数量都会有较大的变化。
因此,这时应按流水线进行全面考虑,而不应将某一台或几台机床分裂开来设计。
即使暂时不能全面地进行流水线设计,制定方案时也应综合研究,才能将工序组合得更为合理,更可靠地满足工件的加工要求,用较多的工作,也为进一步发展创造了有利条件[3-4]
2组合机床总体描述
目前,组合机床主要用于平面加工和孔加工两类工序。
平面加工包括铣平面、刮平面,车平面;
孔加工包括钻、扩、铰、镗孔以及倒角、切槽、攻螺纹、磨削、等。
随着综合自动化的发展,其工艺范围正扩大到车外圆、行星铣削、拉削、推削、磨削、及抛光、冲压等工序。
此外,还可以完成焊接、热处理、自动装配和检测、清洗和零件分类及打印等非切削工作【1】
2.1组合铣床工艺方案的制定工艺方案的制定是设计组合铣床最重要的步骤之一。
其制定过程应从以下的几个方面考虑:
1、被加工零件的特点。
2、加工的工序和加工精度的要求。
3、工件的生产方式等诸多方面综合考虑。
2.1.1被加工零件的特点
连杆是汽车发动机中的主要传动部件之一,它在柴油机中,把作用于活塞顶面的膨胀的压力传递给曲轴,又受曲轴的驱动而带动活塞压缩气缸中的气体。
连杆在工作中承受着急剧变化的动载荷。
连杆由连杆体及连杆盖两部分组成。
连杆体及连杆盖上的大头孔用螺栓和螺母与曲轴装在一起。
为了减少磨损和便于维修,连杆的大头孔内装有薄壁金属轴瓦。
轴瓦有钢质的底,底的内表面浇有一层耐磨巴氏合金轴瓦金属。
在连杆体大头和连杆盖之间有一组垫片,可以用来补偿轴瓦的磨损。
连杆小头用活塞销与活塞连接。
小头孔内压入青铜衬套,以减少小头孔与活塞销的磨损,同时便于在磨损后进行修理和更换。
在发动机工作过程中,连杆受膨胀气体交变压力的作用和惯性力的作用,连杆除应具有足够的强度和刚度外,还应尽量减小连杆自身的质量,以减小惯性力的作用。
连杆杆身一般都采用从大头到小头逐步变小的工字型截面形状。
为了保证发动机运转均衡,同一发动机中各连杆的质量不能相差太大,因此,在连杆部件的大、小头两端设置了去不平衡质量的凸块,以便在称量后切除不平衡质量。
连杆大、小头两端对称分布在连杆中截面的两侧。
考虑到装夹、安放、搬运等要求,连杆大、小头的厚度相等(基本尺寸相同)。
在连杆小头的顶端设有油孔(或油槽),发动机工作时,依靠曲轴的高速转动,把气缸体下部的润滑油飞溅到小头顶端的油孔内,以润滑连杆小头衬套与活塞销之间的摆动运动副[5]
2.1.2加工的工序和加工精度的要求
连杆上需进行机械加工的主要表面为:
大、小头孔及其两端面,杆体与杆
盖的接合面及连杆螺栓定位孔等。
图2-1为汽车发动机连杆零件的主要技术要求。
图2-1发动机连杆主要技术要求
连杆总成的主要技术要求如下:
1.为了使大头孔与轴瓦及曲轴、小头孔与活塞销能密切配合,减少冲击的不良影响和便于传热。
大头孔公差等级为IT6,表面粗糙度Ra应不大于0.8μm,大头孔的圆柱度公差为0.012mm;
小头孔公差等级为IT8,表面粗糙度Ra应不大于1.6μm。
小头压衬套的底孔的圆柱度公差为0.005mm,素线平行度公差为0.04mm。
2.大小头孔的中心距影响到汽缸的压缩比,进而影响到发动机的效率,两孔中心距的尺寸公差等级应不低于IT9。
3.连杆大头孔两端面对大头孔中心线的垂直度误差过大,将加剧连杆大头两端面与曲轴连杆轴颈两端面之间的磨损,甚至引起烧伤,一般规定其垂直度公差等级应不低于IT9。
4.连杆大小头两端面间距离的基本尺寸相同,但其技术要求是不同的。
大头两端面间的尺寸公差等级为IT9,表面粗糙度Ra不大于3.2μm;
小头两端面间的尺寸公差等级为IT12,表面粗糙度Ra不大于6.3μm[6-7]。
2.1.3工件的生产方式
由于本次设计主要对连杆进行双端面铣削,尺寸精度,形状精度,位置精度需要达到一定的技术要求,且端面的表面粗糙对连杆的运动有一定的要求。
因此在设计本次工艺方案时,需进行粗铣、精铣、粗磨、精磨四道工序。
采用粗铣、精铣、粗磨、精磨四道工序,并将精磨工序安排在精加工大、小头孔之前,以便改善基面的平面度,提高孔的加工精度。
粗磨在转盘磨床上,使用砂轮端面磨削,这种方法的生产率较高。
精磨在M7130型平面磨床上用砂轮的周边磨削,这种办法的生产率低一些,但精度较高。
2.2确定切削用量、切削力和切削功率
2.2.1切削用量的选择原则正确地选择切削用量,对提高切削效率,保证必要的刀具耐用度和经济性,保证加工质量,具有重要的作用。
铣削切削用量的选择与要求的加工表面粗糙度及其效率有关系。
当铣削表面粗糙度数值要求时,铣削速度应高一些,每齿走刀量应小一些。
若生产率要求不高,可以取很小的每齿走刀量,一次铣削4mm~5m的m余量达到RA1.6μm的表面粗糙度。
这时每齿的进给量一般为0.02mm~0.03mm。
表2-1是用硬质合金端铣刀的铣削用量
查组合机床设计简明手册得知[1]。
表2-1用硬质合金端铣刀的铣削用量
加工材料
工序
铣削深度(mm)
铣削速度
V(m.min-1)
每齿走刀量
Fz(mm/z)
钢ab=520~720MPa
粗
2~4
80~120
0.2~0.4
精
0.5~1
100~180
0.05~0.20
钢ab=700~900MPa
60~100
90~150
0.05~0.15
钢ab=1000~1100MPa
40~70
0.1~0.3
0.05~0.10
铸铁
2~5
50~80
80~130
0.05~0.2
铝及其合金
300~700
0.10~0.4
500~1000
0.051~0.3
由上表可知,对于本次设计,我们应该选用加工材料为钢ab=520MPa~720MPa,粗铣:
铣削深度2mm~4m,m铣削速度80m.min-1~120m.min-1,每齿走刀量0.2mm/z~0.4mm/z;
精铣:
铣削深度0.5mm~1m,m铣削速度100m.min-1~180m.min-1,每齿走刀量0.05mm/z~0.20mm/z。
组合机床常用铣削方法加工平面,精铣的平面度可达003mm~0.05/1000mm,表面粗糙度可达Ra0.8μm~1.6μm。
对基面的平行度可保证在0.05mm以内,基面间距的尺寸精度可保证在0.05mm以内。
2.2.1.1粗加工时切削用量的选择原则
粗加工时加工精度与表面粗糙度要求不高,毛坯余量较大。
因此,选择粗加工的切削用量时,要尽可能保证较高的单位时间金属切削量(金属切削率)和必要的刀具耐用度,以提高生产效率和降低加工成本[8-12]。
金属切削率可以用下式计算:
Zw≈V.f.ap.1000
式中:
Zw单位时间内的金属切除量(mm3/s)
V切削速度(m/s)
f进给量(mm/r)
ap切削深度(mm)提高切削速度、增大进给量和切削深度,都能提高金属切除率。
但是,在这三个因素中,影响刀具耐用度最大的是切削速度,其次是进给量,影响最小的是切削深度。
所以粗加工切削用量的选择原则是:
首先考虑选择一个尽可能大的吃刀深度ap,其次选择一个较大的进给量度f,最后确定一个合适的切削速度V。
选用较大的ap和f以后,刀具耐用度t显然也会下降,但要比V对t的影响小得多,只要稍微降低一下V便可以使t回升到规定的合理数值,因此,能使V、f、ap的乘积较大,从而保证较高的金属切除率。
此外,增大ap可使走刀次数减少,增大f又有利于断屑。
因此,根据以上原则选择粗加工切削用量对提高生产效率,减少刀具消耗,降低加工成本是比较有利的。
1)切削深度的选择:
粗加工时切削深度应根据工件的加工余量和由机床、夹具、刀具和工件组成的工艺系统的刚性来确定。
在保留半精加工、精加工必要余量的前提下,应当尽量将粗加工余量一次切除。
只有当总加工余量太大,一次切不完时,才考虑分几次走刀。
本次设计选用铣削深度为2mm~4m。
m
2)进给量的选择:
粗加工时限制进给量提高的因素主要是切削力。
因此,进给量应根据工艺系统的刚性和强度来确定。
选择进给量时应考虑到机床进给机构的强度、刀杆尺寸、刀片厚度、工件的直径和长度等。
在工艺系统的刚性和强度好的情况下,可选用大一些的进给量;
在刚性和强度较差的情况下,应适当减小进给量。
本次设计选用每齿走刀量0.2mm/z~0.4mm/z。
3)切削速度的选择:
粗加工时,切削速度主要受刀具耐用度和机床功率的限制。
切削深度、进给量和切削速度三者决定了切削功率,在确定切削速度时必须考虑到机床的许用功率。
如超过了机床的许用功率,则应适当降低切削速度。
本次设计选用铣削速度
-1-1
为80m.min-1~120m.min-1。
2.2.1.2精加工时切削用量的选择原则
精加工时加工精度和表面质量要求较高,加工余量要小且均匀。
因此,选择
率[12]
精加工时的切削深度应根据粗加工留下的余量确定。
通常希望精加工余量不要留得太大,否则,当吃刀深度较大时,切削力增加较显著,影响加工质量。
本次设计选用铣削深度为0.5mm~1mm。
精加工时限制进给量提高的主要因素是表面粗糙度。
进给量增大时,虽有利于断屑,但残留面积高度增大,切削力上升,表面质量下降。
本次设计选用每齿走刀量0.05mm/z~0.20mm/z。
切削速度提高时,切削变形减小,切削力有所下降,而且不会产生积屑瘤和鳞刺。
一般选用切削性能高的刀具材料和合理的几何参数,尽可能提高切削速度。
只有当切削速度受到工艺条件限制而不能提高时,才选用低速,以避开积屑瘤产生的范围。
由此可见,精加工时选用较小的吃刀深度ap和进给量f,并在保证合理刀具耐用度的前提下,选取尽可能高的切削速度V,以保证加工精度和表面质量,同时满足生产率的要求。
本次设计选用铣削速度为100m.min-1~180m.min-1。
2.2.2
连杆工艺方案确定
图2-2发动机连杆零件简图
连杆由大、小头和杆身等部分组成。
大头为开式结构(系直剖式连杆)。
连杆和连杆盖用螺栓,螺母连接。
为减少磨损和便于修理,大头孔和小头孔内分别安装轴瓦和铜套。
连杆身的截面为工字形,可减少重量和减少惯性力又使连杆具有足够的强度和刚度。
连杆头两端面有落差且杆身对称。
大小头侧面设计有定位凸台作为机械加工时的辅助定位基准,便于定位基准的统一[1-5]。
连杆总的工艺特点是:
外形复杂,不易定位;
大、小头有细长的杆身连接,所以弯曲刚性差,易变形;
尺寸精度,形状精度和位置精度及表面粗糙度要求很
连杆所选的材料为45钢(精选含碳量为0.42%~0.47%),并经调质处理以提高其强度及其抗冲击能力,其硬度为217HBS~287HB。
S其锻件重量为7.5kg。
根据以上的工艺特点下面初步拟订工艺方案[1]
1、工艺基面的分析及选择
采用以V形铁为主要定位元件的方法。
为提高其定位精度,要把V形铁的角度做大一些。
如图2-3所示:
图2-3工艺基面的选择
2、工序间余量的确定
3、刀具结构的选择按相关的资料选取端铣刀的形式。
在铣削过程中,端铣刀的直径要大于加工工件的最大宽度,由给定的加工零件图可知最大为Bmax=135m,m故端铣刀的直径选取150mm为宜,其齿数按标准选7。
即D=150
Z=7
2.2.3铣削用量的选择为使组合铣床更好的提高生产效率,便于人工操作,最少的停车损失和使刀具的寿命更长、加工质量更好,合理的选择铣削用量是非常必要的。
下表为硬质合金端铣刀的铣削用量[8-12]。
表2-2
铣削深度
钢b52~70
(公斤/毫米2)
2~4mm
80~120米/分
0.5~1mm
100~180米/分
0.05~0.02
加工工件为45号钢,所以选如下的铣削用量
铣削深度T=3mm
铣削速度V=120m/min
每齿走刀量sz=0.3毫米/齿
铣削用量的选择应该使选择的刀具充分发挥其性能。
所以就不能选择太低。
考虑到批量生产时也没必要把切削用量选太高,以免增加刀具损耗。
总之要根据加工精度和加工材料,工作条件和技术要求进行分析。
所以以上的选择是可行的。
2.2.4确定切削力、切削功率
根据选定的切削用量(组要指切削速度v及进给量f),确定切削力,作为选择动力部件(滑台)及夹具设计的依据;
确定切削扭矩,用以确定主轴及其他传动件(齿轮、传动轴等)的尺寸;
确定切削功率,用以选择主传动电机功率。
一銑削力和主切削功率计算
1主切削力Fc
因选取硬质合金端面銑削45,钢工件,由<机床设计手册>得:
Fc1150ae1.06af0.88dt(0.13)ap0.9.nt(0.18)Z
ac——系数
af——铣削接触深度
af——每齿的进给量
dt——铣刀的深度
ap——铣削深度
Z——铣刀齿数
故由上则有:
Fc553.86N
2切削功率:
N切
612001.086KW
2.3铣端面组合机床配置型式的选择
对于加工发动机连杆这样的工件,特别适合大、中箱体件的加工。
为尽可能地提高生产率,最理想的是将工件一次性全部加工。
经过和指导老师商量后,我们决定设计四根主轴两端同时进行铣削。
在满足条件的情况下,采用卧式双面铣床是可行的。
在配置铣削头固定的卧式组合机床时,其传动装置的电机通常是采用顶置式,即电动机放在铣削头上方。
在配置铣削头移动的卧式组合机床时,其传动装置的电机通常是采用侧置式,即电动机放在铣削头侧面。
本次设计采用的铣削头是安装在滑台上的,可随滑台一起移动,但是是铣削头调整到适当位置后边不再移动,所以采用电动机安装在铣削头上方的配置型式。
在加工连杆过程中,还必须考虑到加工零件特点对结构方案的影响。
在加工精度要求影响方面,不仅提高原始精度,提高工件的定位基准和减少夹紧变形等措施,还要采用如下措施[3]。
1、采用定位块定位,保证连杆能够安装稳定,便于操作,提高加工过程精度要求。
2、采用刚性主轴方案,由于机床导轨间隙及导轨磨损的影响。
在加工过程中就不易产生振动,并且有足够的刚性保证其径向切削力。
2.4影响总体布置的因素
1、加工精度的影响
当工件的加工精度要求较高时,应采用具有固定夹具的单工位组合机床,加工精度要求较低时,可采用具有移动夹具的多工位组合机床。
此外,还要考虑到不同布置形式的机床所能达到的加工精度。
例如,对于同轴度要求较高的各孔,应采用从同一面对工件进行加工机床布置形式。
2、工件大小、形状和加工部位特点的影响对于较大的工件,宜采用单工位机床,反之,宜采用多工位机床;
对于大直径深孔的工件,宜采用具有刚性主轴结构的立式机床;
对于小直径深孔的工件,通常采用专门的深孔加工机床;
对于被加工孔的中心线与定位基准垂直的工件,一般采用立式机床。
本原则也可根据机床的使用条件综合考虑。
根据上述原则,对于本章实例,可采用立式机床。
但考虑工件排屑方便,机床空间的高度可矮些,故可采用卧式组合钻床。
3、生产率的影响
零件的生产批量大小是决定采用单工位、多工位或自动线,还是按中小批量生产特点来设计组合机床的重要因素。
有时从工件的外形及轮廓尺寸上看,可采用单工位固定夹具的机床布置形式,但是由于生产率要求很高,就不得不采用多工位的机床布置方案,以便使装卸工件时间与机动时间重合。
被加工的零件的生产批量越大,工序安排一般就越趋于分散,且粗、半精、精加工应分别在不同的机床上完成
对于中小批量生产的情况,则要力求减少机床的台数,并应将所有工序尽量集中在一台或少数几台机床上完成,以提高机床的利用率【13】
2.5组合铣床的总体分析——三图一卡
2.5.1被加工零件的工序图
被加工零件工序图是指根据已确定的工艺方案,表示一台组合机床或自动线对加工零件应完成的工艺内容的示意图,它包括加工部位尺寸、精度、表面粗糙度及技术要求等内容。
它不能用产品的零件图代替,而须在原零件图的基础上,突出本机床或自动线的加工内容及必要的说明进行重新绘制。
它是进行组合机床设计的主要依据,也是制造、使用、检验和调整机床的重要技术文件。
其内容应包括以下几个方面:
(1)表示出被加工零件的形状和轮廓尺寸及与本机床设计有关的部位的结构形状和尺寸。
尤其是当需要中间导向套时,应表示出零件内部的筋、壁布置及有关结构的形状和尺寸,以便检查工件、夹具、刀具是否发生干涉。
(2)表示出加工用定位基准、夹紧部位及夹紧方向,以便依此进行夹具的定位支承(包括辅助定位支承)、限位、夹紧及导向系统的设计。
(3)表示出本道工序加工部位的尺寸、尺寸精度、表面粗糙度、形状位置精度及技术要求,另外还应表示出本道工序对前道工序提出的要求(主要指定位基准)。
(4)表示出必要的文字说明,如被加工零件的编号、名称、材料、硬度、重量及加工部位的余量等。
(5)绘制时,按一定的比例,细实线表示与本道工序加工无关的部分,粗实线表示被加工部位精度、粗糙度、位置精度、定位面及夹压方向。
(6)凡本道工序保证的尺寸、角度等,应在基尺寸数值上打上方框,并在下面加一横线(粗实线)。
以下为被加工零件图,其材料为45钢并经调质处理,其硬度为217HBS~287HB。
S
图2-4连杆工序图
2.5.2被加工零件的加工示意图零件加工的工艺方案要通过加工意图才能反映出来。
加工示意图表示:
被加工零件在机床上的加工过程,刀具、辅具的布置状况,工件与夹具、刀具等机床各部件间的相对位置关系,以及机床的工作行程和工作循环等。
因此,它是刀具、辅具、夹具、主轴箱、液压和电气装置设计及通用部件选择的主要原始资料,也是对整台机床布置和技术性能的原始要求,同时还是调整机床、刀具及试车的依据。
其内容包括以下几方面:
(1)应反映机床的加工方法、加工条件及加工过程。
(2)根据加工部位的特点及加工要求,决定刀具的类型、数量、结构、尺寸(直径和长度)。
(3)决定主轴的结构类型、规格尺寸及外伸长度。
(4)选择标准或设计专用的接杆、浮动卡头、导向装置、攻丝靠模装置、刀杆托架等,并决定它们的结构参数及尺寸。
(5)标明主轴、接杆、夹具(导向装置)与工件之间的联系尺寸、配合及精度等。
(6)根据机床的生产率及刀具和工件的材料等,合理确定并标注各主轴的切削用量
(7)加工示意图的绘制顺序是:
先按比例用细实线绘出工件加工部位和局部结构的展开图,然后用粗实线绘出加工表面。
为了简化,对同一主轴箱上结构尺寸完全相同的主轴,