单段煤气炉工艺流程及原理文档格式.docx
《单段煤气炉工艺流程及原理文档格式.docx》由会员分享,可在线阅读,更多相关《单段煤气炉工艺流程及原理文档格式.docx(10页珍藏版)》请在冰豆网上搜索。
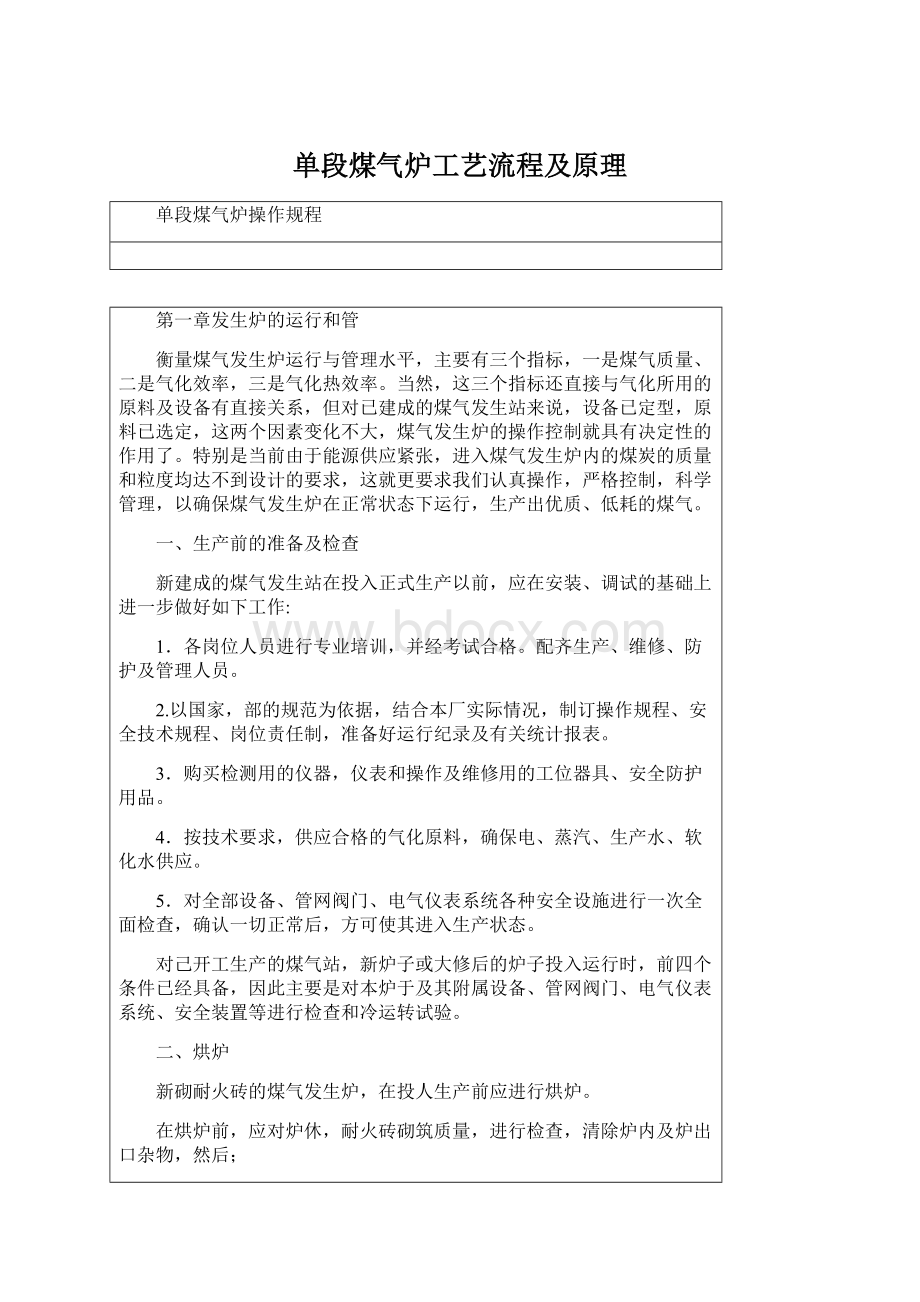
2.接通电源、仪表、供汽、供水管网,向水套注入软化水至规定水位,向各处水封注入生产水至规定水位或按要求保持溢流。
3.打开自然通风阀,拉开钟罩阀。
4.选择合理的烘炉时间及升温速度。
升温速度一般从室温到120℃时,取10℃/h120~340℃之间,取15℃/h,340~550℃之间,取20℃/h,但这并不是一成不变的,还要视气候条件及砌炉后自然干燥的时间长短而定。
其原则是在保证耐火砖及灰缝不致因急冷急热而产生裂纹和变形的前提下,为了节省烘炉时间和费用,可适当的加快升温速度和减少烘炉时间。
5.装入木柴,点火烘炉,并注意按烘炉曲线控制炉内温度变化,升到550℃后,停止加木柴,让其自然冷却下来。
6.待炉子冷下来后,经化验炉内一氧化碳含量少于0.03mg/L时,即可进入炉内检查。
三、点炉
烘炉后,如发现问题需出渣检修,则在检修完后重新装渣。
如一切正常,即可在原有的渣层上,装入300kg左右木柴,木柴上面再放些刨花等引燃物,准备好火种,从人孔投入。
炉中木柴点着后,即盖上人孔盖,关闭自然通风阀,逐渐开启供风阀供风·
炉底供风压力控制在30mmH2O左右。
待木柴均匀燃烧旺盛,炉出温度达250℃左右时,即可少量加煤,并加大供风,将炉底压力控制在50mmH2O左右.随后逐渐增加加煤量和供风量,提高炉底压力,炉出温度也逐渐升高。
当煤层厚度达200mm时,即可打开供调节饱和温度的蒸汽阀门供蒸汽,随着加煤量、供风量的增加,逐渐将饱和温度调节到规定值。
在上述过程中,要勤观察、勤操作。
前期要注意使整个炉膛内木柴均匀燃烧,后期则要注重炉内层次培养,并探炉检查。
当炉内层次达到工艺要求后,取样化验,煤气中氧含量少予0.4%~0.8%时,即可送气。
四、并网
并网是指煤气站已经在生产供气,新增加的炉于接通网路,而不是指全站送气。
当新点的炉子被确认可供气并入运行中的煤气网路时,视不同情况分别操作:
1.通知操作工注意煤气排送机前、后压力变化,并调到工艺要求。
2.如点炉时以最大阀放散管放散时,则应解除竖管水封以接通网路,同时放下最大阀的钟罩,以封闭放散管通路。
3.如点炉初期是从洗涤塔放散管放散时,则应在打开洗涤塔出口大阀门接通网路的同时,关闭放散管阀门,停止放散。
五、生产炉转热备用
在工厂企业中,煤气需用量并不是一个常数,而是不断变化的,因此煤气生产量也相应随之变化。
当变化量较少时,可以可用增加或减少单台炉气化强度的办法来调节;
当变化量较大时,单靠这种办法来调节就不够了,必须用增加或减少发生炉台数的办法来调节。
因此,各煤气发生站除了因检修需要而配置一定数量的冷状态备用发生炉外,还必须配置一定数量的热状态备用发生炉,以满足调节负荷及当运行中煤气发生炉临时出现故障时换炉的需要。
热状态备用发生炉简称热备用炉,与煤气生产网路断开,靠自然通风不熄火,产生的废气从放散管排空。
生产炉转热备用操作:
1.将自动改为手动,减少供风量,适当多加煤,降低炉出温度。
2.打开放散管阀门,同时将发生炉与煤气网路断开。
3.停止加煤机和出灰机构运转。
4.缓慢关闭供风阀和供饱和温度蒸汽阀,打开自然通风阀。
5.关闭汽包补充蒸汽阀,打开放汽阀。
6.调小竖管及洗涤塔冷却水。
在操作过程中及热备用期间应注意的几个问题:
(1)放散管阀门及自然通风阀的开度要适当,不能过大或过少,否则不仅浪费煤炭,而且可能造成事故。
(2)发生炉在热备用期间,炉内呈负压状态,因此不能打开探炉孔,不得启动加煤机和出灰机构,以免吸人空气引起爆炸,同时应注意检查各处水位、水封。
(3)热备用时间超过48小时,则应启动炉子处理一次。
其步骤是关闭自然通风阀,打开供风阀供风,启动加煤机及出灰机构,经探炉确认处理达正常后,恢复热备用状态。
六、热备用炉投入运行
当煤气用量增加时,需要将热备用中的炉子投入运行,其操作是:
1.关闭自然通风阀,打开供风阀及饱和温度蒸汽阀。
2.启动加煤机及出灰机构。
3.调大竖管和洗涤塔冷却水阀门。
4.调整集汽包水位,关闭放汽阀,打开补充蒸汽阀。
5.打开探炉孔,检查炉内层次,调整加煤、出灰量及饱和温度。
6.取样化验,当煤气中含氧量小于规定值时,则按并网操作程序接人网路,投入运行状态。
七、停炉
生产中的发生炉停炉有以下三种情况:
1.按计划检修停炉。
2.煤气产量减少,且预计较长一段时间不会增加,为了减少热备用时的煤耗而停部分炉子。
3.临时出现故障,必须停炉才能修复时的被迫停炉。
其操作步骤如下:
(1)按生产炉转热备用炉操作程序先将炉于与生产网路断开。
(2)停止加煤和供风,加大蒸汽供给量进行灭炉。
(3)经探炉确认炉火全部熄灭后,即停止蒸汽供应,切断电源和水源。
(4)打开探炉孔、人孔,出渣,清炉。
(5)待炉温降低,取样化验合格后,方可进入炉内检查、修理。
八、正常操作与管理
为了确保安全和生产出优质煤气,使发生炉在正常状态下运行,司炉人员必须严格按照安全技术操作规程对运行中的煤气发生炉加强管理与操作:
1.密切注视各部位指示仪表、运转部位、水封、水位、安全设施是否正常,每小时如实将读数记录在运行日志上。
2.每小时探炉一次,其步骤及应注意的事项如下:
(1)先将探炉孔汽封的蒸汽阀打开,再打开探炉孔盖,并将汽封蒸汽调节到适当值。
蒸汽太小则封不住,煤气外溢;
蒸汽太大则使炉顶部分煤气含水蒸汽量增加,还会引起炉内压力波动。
(2)将检查钢钎放入探炉孔,测量出空层高度,将发生炉炉膛总高度减去空层高度即得出总层高度。
(3)将两根钢钎插入炉内。
其中一根斜插,测量炉子中间的层次,另一根直插,测量炉子边上的层次.烧钎两分钟取出,根据目测不同部位的颜色,来判断炉内的层次及温度。
正常情况下,中灰高度为:
100~200mm,边灰高度为400~500mm,火层高度为100~200mm。
(4)经过测量与探炉,如发现炉子不正常,则应及时处理,使其恢复到正常状态。
(5)探完炉后,应先盖上探炉孔盖,再关蒸汽阀门。
(6)由于汽封的蒸汽会在探炉孔口处形成抽力,将空气带人炉内,为了防止大量空气带入炉内,操作时最多只准同时打开两个探炉孔。
3.当汽包水位低于规定水位时,应及时补水。
但当水套严重缺水时,则应立即停炉,让炉子慢慢冷下来并经检查确认水套完好时,方可进水,重新投入生产;
不得在严重缺水时向水套进水。
水套内应使用软化水,未经软化处理的水硬度大,易结垢,不仅影响传热效果,而且可能导致水套损坏和事故。
4.根据煤气生产量的变化及炉内气化情况,及时调整加煤量、出渣量、供风量和饱和温度等工艺参数。
5.按润滑卡片规定,定期给各部位加油,以保证良好的润滑和密封。
九、气化条件和参数的调整
运行中的煤气发生炉要维持其正常气化,必需对一系列的参数进行调整和控制,但其中三个气化参数是关键:
(一)燃料层厚度
在发上炉中的还原反应与温度有关,温度越高,反应越快;
同时也与接触时间有关,在温度一定的条件下,接触时间越长,反应所得到的co和H2越多,煤气质量也越好。
根据生产实践,国内部分工厂倡导厚煤层操作法,如Φ3m的发生炉总层厚度由正常的900~1100mm增加到1600mm,并与此相适应地增加供风量,提高炉底压力和饱和温度,这样的结果是:
1.提高了煤气质量,增加了煤气产量;
2.煤气炉出温度降低;
3.烧穿冒火的现象减少;
4.缓和了由偏炉所造成的一系列矛盾。
但煤层的厚度增加,相应的供风阻力也增大,有造成灰盘、鼓风箱水封被冲破的可能;
同时,在操作管理上也必须更加谨慎。
(二)气化强度
为了提高发生炉的生产能力,以达到在不增加设备的前提下,最大限度地满足发展生产对增加煤气的需要,开展了大流量生产试验,并总结出不少宝贵的经验:
1.对燃料进行严格筛分,不仅要求筛去全部粉尘,而且要求燃料块度大小之比在2:
1范围以内。
2.采用前面所阐述的厚煤层操作。
3·
为了适应提高气化强度的需要,对原有设备进行适当改造,如提高灰盆的水封,将炉身改为全水套等。
4.对风量、风压、饱和温度等工艺参数作相应的调整。
5.对运行中的煤气发生炉加强管理,勤检查,严格按规程操作。
采取以上措施后,一般都能将发生炉的生产能力提高20%,甚至更高一些。
(三)饱和温度
饱和温度的选择是正确操作发生炉、制取优质煤气的关键所在,但是最佳的饱和温度值并非一个固定值。
而是随着炉子气化状况、燃料种类、煤气用途的不同而异,这就要靠司炉工凭借丰富的生产经验来探索、总结。
一般选择原则是:
1.燃料:
灰分熔点低,为了防止结渣,选择较高的饱和温度;
灰含量多,块度小,在炉内气化过程中结渣的可能性大,可适当提高饱和温度;
含水分多,降低了炉温,应选取较低的饱和温度。
2.气化强度:
提高气化强度,风量、风压相应增加,炉内燃烧与气化速度也增加,则应提高饱和温度。
3.煤气用途:
作工业燃料气用,要求一氧化碳高,氢低,就应选择较低的饱和温度。
4.根据探炉情况判断炉内气化正常与否。
当发现火层温度太高时,则应提高饱和温度;
当炉内火层温度太低时,则应降低饱和温度。
就发生炉煤气而言,气化无烟煤时饱和温度在50~60℃之间变化;
气化烟煤时饱和温度在45~55℃之间波动。
除了上述的三个关键参数外,为了确保安全生产和气化过程正常进行,还必须对一些工艺参数进行调整与控制。
(1)燃料:
进入发生炉的燃料量都必须计量。
供给量由所需煤气的生产量来确定,对单台炉于来说,允许在设计额定值的30%~120%范围内变动;
同时对燃料的成分、含水量、含灰量要进行定期化验,对燃料的块度也有严格的要求,如对我公司炉型来说,一般设计规定为20~50mm。
(2)煤气:
一般的煤气站从炉出口至低压总管中间一段都布置得较紧凑,不具备计量装置所必需的直管段长度。
1)每两时进行一次半分析,化验煤气中的氧、一氧化碳、二氧化碳含量,据此来分析炉内气化正常与否,为司炉工提供操作依据;
一班进行一次全分析,通过化验得出煤气的全部成分,并计算出热值。
2)煤气炉出压力主要是用来克服净化系统和管道的阻力,一般控制在60~80mmH2o之间,在其他条件不变的情况下,如炉出压力增加,说明净化系统或管道被带出物堵塞,则应及时予以消除;
如供风量、风压、生产量增加,炉出压力相应增加则是正常现象。
3)煤气炉出温度直接影响到煤气站出温度,而煤气站出温度是煤气质量的重要指标之一,为了提高煤气的热值和燃烧温度,人们采取了许多措施来降低煤气站出温度,严格控制炉出温度或是其中之一。
同时,煤气炉出温度又是炉内气化情况特别是炉内层次正常与否的重要标志。
对于煤气发生炉来说,炉出温度在400~600℃之间属正常。
如炉出温度太高,说明炉内料层太薄或有烧穿、冒火等现象,煤气质量也要下降。
(3)供风,风量是由所需要的煤气产量来确定的,供风压力除随煤气产量、供风量增加而增高外,还要由料层的阻力和所要求的炉出压力来决定,因此它既是发生炉生产能力的一个间接标志,又能从另一侧面反映炉内气化情况正常与否。
对煤气发生炉来说控制在100~400mmH2O之间。
煤气负荷量是在不断变化的。
这种变化首先反映到煤气低压总管压力上,我们利用这个压力信号,通过自控系统来操作发生炉供风管上的蝶阀,当煤气负荷增加或减小时,低压总管上的压力相应地减少或增加信号,使蝶阀开大或关小,从而达到增加或减少供风的目的。
(4)炉渣含碳量:
是指灰渣中含碳量的百分比,每班取样化验一次,平时可用肉眼观察估测。
炉渣含碳量太高,说明炉内气化不正常,同时也标志着气化效率降低,不少工厂把它作为煤气站技术经济考核指标之一。
十、发主炉不正常炉况及处理
运行中的煤气发主炉,有时会出现异常现象,如煤气炉出温度过高或过低,炉渣含碳量增高,炉内出现结渣、冒火等现象,均称之为不正常炉况。
造成这种现象的主要原因有以下三个方面:
1.供应的气化原料不符合要求,如煤的质量降低,含灰分、煤矸石增多;
煤的块度不均匀,含煤粉多,恶化了炉内正常气化条件。
2.发生炉本身存在缺陷,如加煤系统或出灰系统出现故障或零件损坏,致使加煤、出灰不均匀等。
3,司炉工操作失误,如饱和温度未控制好,对加煤、出灰、炉内层次变化情况未及时监测和调整等。
当然这些原因并不是孤立的,而是互相牵连的,有时还是其共同作用的结果。
因此,炉况不正常情况的表现也是多种多样的,互相交错的,我们在这里将常见的不正常炉况归纳为三个问题予以分析说明。
鉴于在正常生产条件下前二个因素已基本固定。
既使出现,也显而易见,故在分析时着重说明操作因素及处理办法。
(一)煤气发生炉的热运行
1.煤气发生炉热运行的特征及判断
(1)首先可从炉出温度表上看出,煤气炉出温度超过工艺规定值。
(2)打开透炉孔观察,可见炉面呈红亮或黄亮色,有时有局部冒火现象。
(3)探炉可发现炉内有结渣现象,钎子插不下去,火层温度高,钎子拿出来时火层区呈黄亮色,有时甚至将钎子烧断。
(4)煤气取样化验,co2超过规定值,煤气发热值降低。
2.热运行形成原因及处理方法
造成热运行的原因常见的有两种,针对不同的原因,采取不同的处理方法
(1)饱和温度太低,即向炉底供风管中加入的蒸汽量少了,送入炉内的风中含水蒸气量不足,使炉内温度特别是氧化层温度增高,当温度超过灰渣熔点时,灰渣熔化,结成块状.这样不仅是沿炉截面的均匀供风遭到了破坏,恶化了炉内气化条件,而且由于大块熔渣的存在,使气流与碳的接触面减少,二氧化碳和水蒸气未能与碳充分反应就通过了还原层。
结果煤气炉出温度高,煤气中C02多,发热值低。
出现这种情况时,应减少该台炉子的负荷,适当提高饱和温度,使炉内温度降低到规定值,然后视具体情况作如下处理:
当结渣不严重时,用探炉的钎子穿插,破碎渣块,并适当调整加煤量和比灰量,使炉子逐渐恢复正常。
当炉子恶化情况严重,炉内结成一片片大块时,为了确保供煤气质量和便于处理,将该台炉于与网路断开,用直径30~40mm的大钢钎和铁锤进行敲打破渣,待基本上处理正常后再接人网路。
当炉子结成整块无法下料时,只得停炉打渣,处理好后再点炉生产。
(2)生产过程中,当煤气产量发生变化时,未及时调整加煤量和出灰量,造成灰层过高(大于500~600mm),总层过低(小于600~700mm),这样不仅是炉内的干燥干馏层没有,还原层也交薄,使二氧化碳、水蒸气等组成的气流没有足够的时间与碳接触完成还原反应,结果煤气中二氧化碳成分增加,煤气炉出温度增高。
出现这种情况时,应适当加快出灰和加煤,使灰层降至规定值,总层增加至规定值,炉子即可恢复正常状况。
(二)煤气发生炉冷运行
1.煤气发生炉冷运行特征及判断
(1)从炉出温度可看出,煤气炉出口温度低于规定值(对3M炉为400℃)。
(2)打开探炉孔观察,炉面呈暗红色或黑色。
(3)插钎检查时,按规定烧钎2分钟拿出来后,钎子上所示氧化层区域呈现暗红色,甚至有时看不出火层区域(此时可用湿布擦钎于,根据产生水蒸气的多少未判定火层区域)。
(4)煤气取样化验,一氧化碳和氢都较低;
炉渣取样分析,含碳量高。
2.冷运行形成原因及处理方法
(1)饱和温度太高,向炉中供风的水蒸气含量高,使炉内及火层温度低,这样不仅是碳不能充分氧化,炉渣含碳量高,而且由于炉温低,不能充分供应二氧化碳还原和水蒸气分解所需的热量,使煤气中一氧化碳和氢都很低。
出现这种情况时,应降低饱和温度,待炉内和氧化层温度恢复正常后,再将饱和温度调到正常值。
(2)在运行过程中,未能根据煤气产量调整加煤、出灰量,造成煤层太厚(>1200mm)、灰层太薄,有时甚至没有灰层。
送人炉内的风未能充分预热,炉内温度下降,煤气质量恶化,炉渣含碳量增高。
此时应停止出灰,把灰层培养起来,停止或减少加煤,使炉内层次逐渐恢复正常。
对湿式出灰的炉子,此时应严格控制灰盘水位,防止因灰盘水位大高而导致炉蓖因遇水急冷而炸裂。
(3)煤气发生炉生产量太低,炉内气化速度慢,炉温低。
遇到这种情况,多台炉子同时生产时,可将部分生产炉转为热备用,逐渐增加生产炉子的鼓风量,使其恢复正常。
单台炉生产时就无法调整,有时为了维持生产,不得不被迫放散,这样既浪费宝贵的能源,又污染了环境,这是应该尽量避免的,为了从根本上解决这个问题,一是加强计划调度,做到均衡生产;
另一是建立储气柜,予以调节负荷。