非金属材料成形文档格式.docx
《非金属材料成形文档格式.docx》由会员分享,可在线阅读,更多相关《非金属材料成形文档格式.docx(18页珍藏版)》请在冰豆网上搜索。
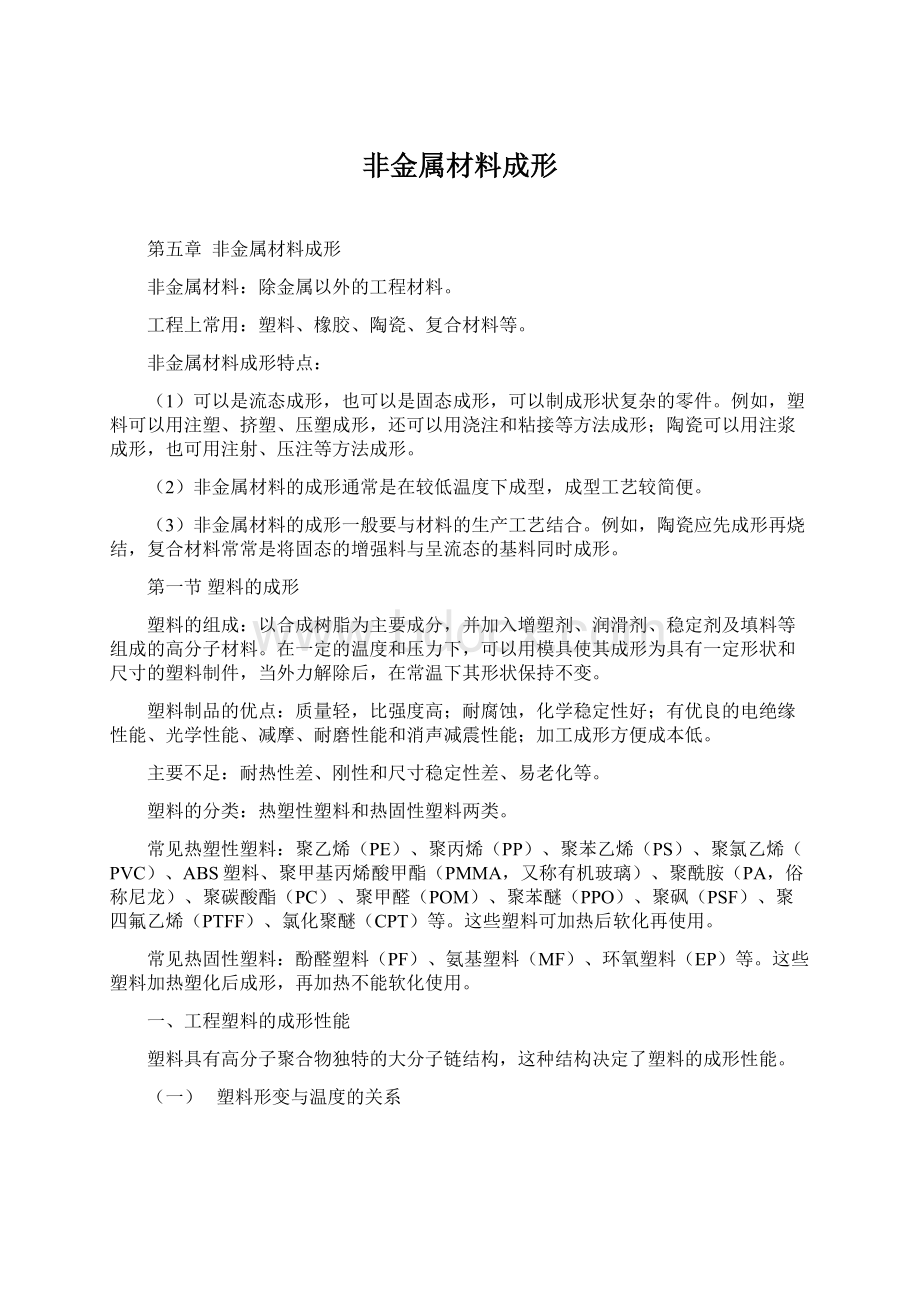
一、工程塑料的成形性能
塑料具有高分子聚合物独特的大分子链结构,这种结构决定了塑料的成形性能。
(一)
塑料形变与温度的关系
热塑性塑料形变特性(力学性能)如图5-1所示。
低于玻璃化温度Tg为玻璃态、高于粘流温度Tf(或结晶温度Tm)温度为粘流态、在玻璃化温度和粘流温度之间为高弹态,当温度高于热分解温度(Td)时,塑料会降解或气化分解。
图5-1塑料的形变与温度的关系
玻璃态,强度、刚性等力学性能较好,可作为结构材料使用。
高弹态,外力作用下,会产生很大的弹性形变(可达100%~1000%),此时的高聚物具有橡胶的特性。
粘流态,高聚物开始粘性流动,变形是不可逆变形,一般在此温度范围成形。
固化:
热固性塑料在成形过程中,由于高聚物发生交联反应,分子将由线型结构变为体型结构,这一过程称为固化。
热固性塑料受热后的状态变化曲线如图5-2所示。
图5-2热固性塑料受热后的状态变化曲线
(二)
塑料的流变性能
使用中:
正常使用中处于玻璃态。
成形时:
在成形过程中,一般要求塑料处于粘流态(或塑化态)成形。
粘流体:
塑料聚合物熔体是非牛顿流体(或称粘流体),其粘度随流动中的剪切速率、温度、压力的变化而有较大的变化。
对于一种塑料,通常其粘度随温度的升高而降低,塑料的粘度愈小流动性也愈好,图5-3是几种常用塑料的粘度与温度变化曲线,从图中可以看出,不同塑料由于其分子结构的差异,粘度对温度的敏感程度不同。
粘度也随流动时的剪切速率(或称为速度梯度)的变化而变化,剪切速率增加时粘度会随之降低,如图5-4所示。
当温度一定时,塑料熔体流动剪切速率愈高,其粘度愈低,也愈有利于塑料成形。
图5-3几种常用塑料的粘度与温度变化曲线
1—增塑聚乙烯2—硬聚乙烯3—聚甲基丙烯酸甲酯
4—聚丙烯5—聚甲醛6—低密度聚乙烯7—尼龙66
图5-4粘度随剪切速率(速度梯度)的变化
1—聚砜(350℃挤出)2—聚砜(350℃注射)3—低密度聚乙烯(350℃)
4—聚碳酸酯(315℃)5—聚苯乙烯(200℃)
(三)
塑料的成形工艺性
塑料的成形工艺性主要表现在以下几个方面:
1.流动性塑料在一定的温度与压力下填充模具型腔的能力称为塑料的流动性。
热塑性塑料的流动性用熔融指数(也可称熔融流动率)表示,熔融指数越大,流动性也越好,熔融指数与塑料的粘度有关,粘度愈小熔融指数愈大,塑料的流动性也愈好。
常用塑料的流动性大致可分为三类:
流动性好:
尼龙、聚乙烯、聚苯乙烯、聚丙烯、醋酸纤维素等;
流动性中:
改性聚苯乙烯、ABS、聚甲基丙烯酸甲酯、聚甲醛、氯化聚醚等;
流动性差:
聚碳酸酯、硬聚氯乙烯、聚苯醚、聚砜、聚芳砜、氟塑料等。
热固性塑料的流动性指标一般用拉西格流动性表示,不同的塑料流动性不同,对于同一种塑料,由于交联反应的分子量不同,填料的性质与多少不同,增塑剂和润滑剂的多少不同,拉西格流动性也不同,同一品种塑料的流动性可分为三个不同的等级。
第一级:
拉西格流动值为100~130mm,用于压制无嵌件、形状简单的一般厚度塑件。
第二级:
拉西格流动值为131~150mm,用于压制中等复杂程度的塑件。
第三级:
拉西格流动值为151~180mm,用于压制结构复杂、型腔很深、嵌件较多的薄壁塑件,或用于传递(压注)成形。
2.收缩性塑料制品从模具中取出冷却到室温后,发生尺寸收缩的特性称为收缩性。
由于塑料的热膨胀系数较钢大3~10倍,塑料件从模具中成型后冷却到室温的收缩相应也比模具的收缩大,故塑料件的尺寸较型腔小。
塑料制件的成形收缩值可用收缩率表示:
式中:
k——塑料收缩率;
Lm——模具在室温时的尺寸,单位为mm;
L1——塑件在室温时的尺寸,单位为mm。
塑料的收缩率是塑料成形加工和塑料模具设计的重要工艺参数,它影响塑料件尺寸精度及质量。
3.结晶性按照聚集态结构的不同,塑料可以分为结晶型塑料和无定形塑料两类。
如果高聚物的分子呈规则紧密排列则称为结晶型塑料,否则为无定型塑料。
一般高聚物的结晶是不完全的,高聚物固体中晶相所占质量分数称为结晶度。
结晶型高聚物完全熔融的温度Tm为熔点。
塑料的结晶度与成形时的冷却速度有很大关系,塑料熔体的冷却速度愈慢,塑件的结晶度也愈大。
塑料的结晶度大,则密度也大,分子间作用力增强,因而塑料的硬度和刚度提高,力学性能和耐磨性增高,耐热性、电性能及化学稳定性亦有所提高;
反之,结晶度低、或无定形塑料,其与分子链运动有关的性能,如柔韧性、耐折性,伸长率及冲击强度等则较大,透明度也较高。
4.热敏性和水敏性热敏性是指塑料对热降解的敏感性。
有些塑料对温度比较敏感,如果成形时温度过高容易变色、降解,如聚氯乙烯、聚甲醛等。
水敏性是指塑料对水降解的敏感性,也称吸湿性。
水敏性高的塑料,在成形过程中由于高温高压,使塑料产生水解或使塑件产生气泡、银丝等缺陷。
所以塑料在成形前要干燥除湿,并严格控制水分。
5.毒性、刺激性和腐蚀性有些塑料在加工时会分解出有毒性、刺激性和腐蚀性的气体。
例如,聚甲醛会分解产生刺激性气体甲醛,聚氯乙烯及其衍生物或共聚物分解出既有刺激性又有腐蚀性的氯化氢气体。
成形加工上述塑料时,必须严格掌握工艺规程,防止有害气体危害人体和腐蚀模具及加工设备。
除上述工艺性能外,还有吸气性、粘模性、可塑性、压缩性、均匀性和交联倾向等。
二、注射成形
塑料注射成形:
又称注塑成形,是热塑性塑料成形的主要加工方法,近年来,也用于部分热固性塑料的成形加工。
特点:
生产效率高、易于实现机械化和自动化、并能制造外形复杂,尺寸精确的塑料制品,大约60%~70%的塑料制件用注射成形方法生产。
注射成形工艺过程
注射过程:
包括加料、塑化、注射、保压、冷却定型和脱模等几个步骤。
塑化是塑料在注射机料筒中经过加热达到塑化状态(粘流态或塑化态);
注射是将塑化后的塑料流体,在螺杆(或柱塞)的推动下经喷嘴压入模具型腔;
塑料充满型腔后,需要保压一定时间,使塑件在型腔中冷却、硬化、定型;
压力撤消后开模,并利用注射机的顶出机构使塑件脱模,取出塑件。
注射成形的工艺条件:
温度、压力和时间等。
(1)温度在注射成形时需控制的温度有料筒温度、喷嘴温度、模具温度等。
料筒温度应控制在塑料的粘流温度Tf(对结晶型塑料为熔点Tm)以上,提高料筒温度可使塑料熔体的粘度下降,对充模有利,但必须低于塑料的热分解温度Td。
喷嘴处温度通常略低于料筒的最高温度,以防止塑料流经喷嘴处因升温产生“流涎”。
模具温度根据不同塑料的成形条件,通过模具的冷却(或加热)系统控制。
对于要求模具温度较低的塑料,如聚乙烯、聚苯乙烯、聚丙烯、ABS塑料、聚氯乙烯等应在模具上设冷却装置;
对模具温度要求较高的塑料,如聚碳酸脂、聚砜、聚甲醛、聚苯醚等应在模具上设加热系统。
(2)压力注射成形过程中的压力包括塑化压力和注射压力两种。
塑化压力又称背压,是注射机螺杆顶部熔体在螺杆转动后退时受到的压力。
增加塑化压力能提高熔体温度,并使温度分布均匀。
注射压力是指柱塞或螺杆头部注射时对塑料熔体施加的压力。
它用于克服熔体从料筒流向型腔时的阻力、保证一定充模速率和对熔体压实。
注射压力的大小,取决于塑料品种、注射机类型、模具的浇注系统结构尺寸、模具温度、塑件的壁厚及流程大小等多种因素,近年来,采用注塑流动模拟计算机软件,可对注射压力进行优化设计。
在注射机上常用表压指示注射压力的大小,一般在40~130MPa之间。
常用塑料的注射成形工艺条件见表5-1。
(3)时间注射时间是一次注射成形所需的时间,又称成形时间,它影响注射机的利用率和生产效率。
注射时间一般在0.5~2min,厚大件可达5~10min。
表5-1常用塑料的工艺条件
塑料品种
注射温度/℃
注射压力/MPa
成形收缩率(%)
备注
聚乙烯
180~280
49~98.1
1.5~3.5
硬聚氯乙烯
150~200
78.5~196.1
0.1~0.5
聚丙烯
200~260
68.7~117.7
1.0~2.0
聚苯乙烯
160~215
49.0~98.1
0.4~0.7
聚甲醛
180~250
58.8~137.3
聚酰胺(尼龙66)
240~350
1.5~2.2
聚碳酸酯
250~300
78.5~137.3
0.5~0.8
ABS
236~260
54.9~172.6
0.3~0.8
聚苯醚
320
0.7~1.0
氯化聚醚
180~240
58.8~98.1
0.4~0.6
聚砜
345~400
0.7~0.8
氟塑料F-3
260~310
137.3~392
1~2.5
氟塑料F-4
冷压烧结370
模压1~5
压塑成形
注射机与模具
图5-5卧式注射机
1—锁模液压缸2—锁模机构3—移动板4—顶杆5—固定板6—控制台
7—料筒及加料器8—料斗9—定量供料装置10—注射缸
注射机按其外形可分为立式、卧式、角式三种,应用较多的卧式注射机如图5-5所示。
各种注射机尽管外形不同,但基本都由下列三部分组成。
(1)注射系统由加料装置(料斗)、定量供料装置、料筒及加热器、注射缸等组成,其作用是使塑料塑化和均匀化,并提供一定的注射压力,通过柱塞或螺杆将塑料注射到模具型腔内。
(2)合模、锁模系统由固定模板、移动模板、顶杆、锁模机构和锁模油缸等组成,其作用是将模具的定模部分固定在固定模板上,模具的动模部分固定在移动模板上,通过合模锁模机构提供足够的锁模力使模具闭合。
完成注射后,打开模具顶出塑件。
(3)操作控制系统安装在注射机上的各种动力及传动装置都是通过电气系统和各种仪表控制的,操作者通过控制系统来控制各种工艺量(注射量、注射压力、温度、合模力、时间等)完成注射工作,较先进的注射机可用计算机控制,实现自动化操作。
注射机还设有电加热和水冷却系统用于调节模具温度,并有过载保护及安全门等附属装置。
注射成形模具是注射成形工艺的主要工艺装备,称为注射模。
注射模一般由定模部分和动模部分组成,如图5-6所示。
图5-6注射模
1—定位环2—主流道衬套3—定模底板4—定模板5—动模板6—动模垫板7—模脚8—推杆固定板
9—推杆固定底板10—拉料杆11—推杆12—导柱13—凸模14—凹模15—冷却水道
根据模具上各种零部件的作用,塑料注射模一般有以下几部分。
(1)成形部分组成模具型腔的零件。
主要由凸模、凹模、型芯、嵌件和镶块等组成。
(2)浇注系统熔融塑料从喷嘴进入模具型腔流经的通道称为浇注系统。
它一般由主流道、分流道、浇口和冷料井等组成。
其作用是使塑料熔体稳定而顺利地进入型腔,并将注射压力传递到型腔的各个部位,冷却时浇口适时凝固以控制补料时间。
(3)导向机构为了使动模与定模在合模时能准确对中,以及防止推件板歪斜而设置的机构,主要有导柱、导套等。
(4)侧向抽芯机构塑件的侧向有凹凸形状的孔或凸台时,在塑件被推出前必须先拔出侧向凸模或抽出侧向型芯。
侧向抽芯机构一般由活动型芯、锁紧楔、斜导柱等组成。
(5)推出机构又称脱模机构,它是在开模时将塑件推出的零部件。
主要有推板、推杆、主流道拉料杆等组成。
在注射模上还有加热、冷却系统和排气系统等。
注射模模架的国家标准有《塑料注射模中小型模架及技术条件》(GB/T12556—90)和《塑料注射模大型模架》(GB/T12555—90)前者适用于尺寸为B×
L≤560×
900的模板;
后者适用于尺寸为B×
L=(630×
630)~(1250×
2000)的模板。
三、压塑成形
压塑成形又称压缩成形、模压成型,是塑料成形加工中较传统的工艺方法,目前主要用于热固性塑料的加工。
压塑成形工艺过程
压塑成形原理:
将经过预制的热固性塑料原料(也可以是热塑性塑料),直接加入敞开的模具加料室,然后合模,并对模具加热加压,塑料在热和压力的作用下呈熔融流动状态充满型腔,随后由于塑料分子发生交联反应逐渐硬化成形。
成形工艺过程:
预先对塑料原料进行预压成形和预热处理,然后将塑料原料加入到模具加料室闭模后加热加压,使塑料原料塑化,经过排气和保压硬化后,脱模取出塑件。
然后清理模具和对塑件后期处理。
影响成形因素:
应控制好成形温度和压力。
压塑成形温度高低,对塑料顺利充型及塑件质量有较大影响。
在一定范围内,提高温度可以缩短成形周期,减小成形压力,但是如果温度过高会加快塑料的硬化,影响物料的流动,造成塑件内应力大,易出现变形、开裂、翘曲等缺陷,温度过低会使硬化不足,塑件表面无光,物理性能和力学性能下降。
通常压缩比大的塑料需要较大的压力,生产中常将松散的塑料原料预压成块状,既方便加料又可以降低成形所需压力。
表5-2是常用热固性塑料的压塑成形温度和压力。
表5-2常用热固性塑料的压塑成形温度和压力
塑料种类
成形温度/℃
成形压力/MPa
酚醛塑料(PF)
三聚氰胺甲醛塑料(MF)
脲甲醛塑料(UF)
聚酯塑料(UP)
邻苯二甲酸二丙烯酯(PDPO)
环氧树脂塑料(EP)
有机硅塑料(OSMC)
140~180
135~155
85~150
120~160
145~200
150~190
7~42
14~56
0.35~3.5
3.5~14
0.7~14
7~56
压塑设备及模具
压塑成形设备:
液压机,它由机架(包括上下横梁、立柱、机座等)、活动横梁、工作油缸、顶出机构、液压传动和电器控制系统等部分组成,如图5-7所示。
图5-7液压机
1—工作液压缸2—上横梁3—活动横梁4—立柱5—机座6—推出缸
压塑成形模具:
如图5-8所示,与注射模不同的是,压塑模没有浇注系统,只有一段加料室,这是型腔的延伸和扩展。
注射成形时模具处于闭合状态成形,而压塑模成形是靠凸模对凹模中的原料施加压力,使塑料在型腔内成形。
压塑模成形零件的强度要比注射模高。
图5-8压塑模结构
1—上加热板2—上模板3—承压块4—凸模5—加热器6—凹模
7—推杆8—弹簧9—导向柱10—推板11—支架12—下模底板
四、其它成形方法
传递成形
传递成形原理:
又称压注成形或挤胶成形,它是在压塑成形的基础上发展起来的热固性塑料成形方法,其工艺类似于注射成形工艺,所不同的是传递成形时塑料在模具的加料室内塑化,再经过浇注系统进入型腔,而注射成形是在注射机料筒内塑化。
将塑料原料经过预处理,闭模后将原料加入加料室加热软化(若是下加料室传递成形应先加料,后闭模加热),随即在柱塞的挤压下通过模具的浇注系统将熔融塑料挤入型腔,塑料在型腔内继续受热受压而固化成形,然后开模取出制品,并清理型腔、加料室和浇注系统。
传递成形优点:
成形周期短;
塑件飞边小,易于清理;
能成形薄壁多嵌件的复杂塑料制品;
塑件的精度和质量较压塑件高。
但传递成形加料室内总会留有余料,塑料损耗较大;
模具结构较压塑模复杂,制造成本较高。
传递成形模具:
如图5-9所示。
图5-9传递成形模具
1—压柱2—加料室3—上模板4—凹模
5—导柱6—下模垫板7—固定板8—型芯
挤出成形
挤出成形:
也称为挤塑成形,主要用于热塑性塑料生产棒、管等型材和薄膜等,也是中空成形的主要制坯方法。
挤出成形生产线:
由挤出机、挤出模具、牵引装置、冷却定型装置、切割或卷曲装置、控制系统组成,如图5-10所示。
挤出机相当于注射机的注射系统,它由料斗、料筒和螺杆组成。
工作时螺杆在传动系统驱动下转动,将塑料推向料筒中加热塑化,在挤出机的前端装有挤出模具(又称机头或口模),塑料在通过挤出模具时形成所需形状的制件,再经过冷却定型处理就可以得到等截面的塑料型材。
图5-10型材挤出生产线
1—冷却水入口2—料斗3—料筒4—加热器5—挤出螺杆6—分流滤网7—过滤板
8—机头9—喷冷却水装置10—冷却定型装置11—牵引装置12—卷料或裁切装置
如果挤出的中空管状塑料不经冷却,将热塑料管坯移入中空吹塑模具中向管内吹入压缩空气,在压缩空气作用下,管坯膨胀并贴附在型腔壁上成形,经过冷却后即可获得薄壁中空制品。
图5-11是挤出中空吹塑成形过程及挤出吹塑模具。
图5-11挤出中空吹塑成形过程及挤出吹塑模具
如果挤出的中空管状塑料不经冷却,在机头中心通入压缩空气,将管坯吹成管状薄膜冷却后可加工为各种薄膜制品。
图5-12是挤出吹塑薄膜加工工艺过程示意图。
图5-12挤出吹塑薄膜加工工艺过程示意图
1—吹气孔2—卷料辊3—挤出机头4—口模套5—冷却风环
6—调节器7—薄膜管8—导向辊9—人字板10—牵引辊
在挤出机头芯部穿入金属导线,挤出制品即为塑料包敷电线或电缆。
挤出工艺参数:
压力、温度和挤出速率等。
挤出加工时料筒的压力可以达到55MPa,工作温度根据塑料品种的不同,塑化温度一般在180~250℃。
挤出速率是单位时间内挤出机口模挤出的塑料质量(单位为kg/h)或长度(m/min)。
挤出速率大小表示挤出机生产率的高低,它与挤出口模的阻力、螺杆与料筒的结构、螺杆转速、加热系统及塑料特性等因素有关。
其中螺杆的结构与转速影响最大,螺杆结构如图5-13所示,它的工作部分由加料段、压缩段、均化段组成。
图5-13螺杆结构
H1—加料段螺槽深度H3—均化段螺槽深度D—螺杆直径
α—螺旋角L—螺杆长度e—螺棱宽度s—螺距
真空成形
真空成形:
也称为吸塑成形,它是将热塑性塑料板材、片材固定在模具上,用辐射加热器加热到软化温度,用真空泵(或空压机)抽取板材与模具之间的空气,借助大气压力使坯材吸附在模具表面,冷却后再用压缩空气脱模,形成所需塑件的加工方法。
成形特点:
生产设备简单,效率高,模具结构简单,能加工大尺寸的薄壁塑件,生产成本低。
真空成形方法:
凹模真空成形、凸模真空成形、凹凸模真空成形等。
凹模真空成形方法如图5-14所示,一般用于要求外表精度较高,成形深度不高的塑件。
图5-14凹模真空成形
凸模真空成形方法如图5-15所示,一般用于内表面精度要求较高,有凸起形状的薄壁塑件,凸模真空成形方法较凹模真空成形方法塑件壁厚稍均匀。
图5-15凸模真空成形
凹凸模真空成形方法如图5-16所示,它是先将塑料板材夹在凹模上加热,软化后将加热器移开,然后通过凸模吹入压缩空气,凹模稍微抽真空使塑料板贴附在凸模的外表面。
这种成形方法,由于将塑料板吹鼓延伸后再成形,因此壁厚均匀,可用于成形较深的制件。
图5-16凹凸模真空成形a)夹紧片材b)预压拉伸c)成形d)开模及顶出
真空成形产品类型:
塑料包装盒、餐具盒、罩壳类塑件、冰箱内胆、浴室镜盒等;
常用材料有聚乙烯、聚丙烯、聚氯乙烯、ABS、聚碳酸酯等材料。
(四)
反应注射成形
反应注射成形原理:
把两种发生反应的塑料原料分别加热软化后,由计量系统进入高压混合器经混合发生塑化反应,再注射到模具型腔中,它们在型腔中继续发生化学反应,并且伴有膨胀、固化的加工工艺。
反应注射成形工艺:
如图5-17所示。
它适合加工聚氨酯、环氧树脂等热固性塑料,也可以用于生产尼龙、ABS、聚酯等热塑性塑料。
例如,轿车仪表盘、方向盘、飞机和汽车的座椅及椅垫、家具和鞋类、仿大理石浴缸浴盆等。
图5-17反应注射成形工艺过程示意图
1—原料槽2—搅拌叶轮3—计量加压泵4—模具5—加热器6—锁模装置7—喷嘴
8—混合器9—清洗液10—真空泵11—电动机12—控制阀13—空压机