悬置系统设计计算Word下载.docx
《悬置系统设计计算Word下载.docx》由会员分享,可在线阅读,更多相关《悬置系统设计计算Word下载.docx(9页珍藏版)》请在冰豆网上搜索。
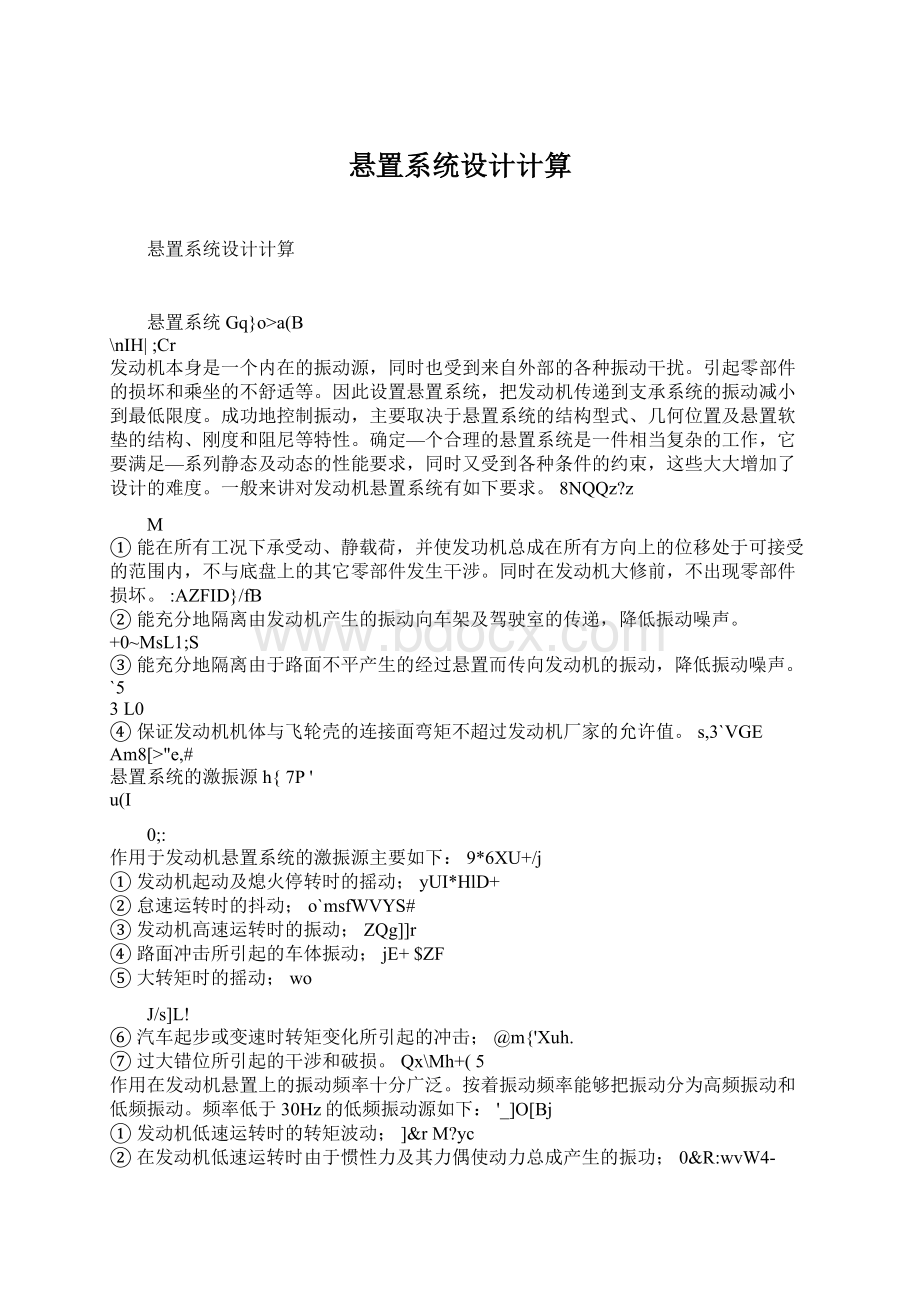
@m{'
Xuh.
⑦过大错位所引起的干涉和破损。
Qx\Mh+(5
作用在发动机悬置上的振动频率十分广泛。
按着振动频率能够把振动分为高频振动和低频振动。
频率低于30Hz的低频振动源如下:
'
_]O[Bj
①发动机低速运转时的转矩波动;
]&
rM?
yc
②在发动机低速运转时由于惯性力及其力偶使动力总成产生的振功;
0&
R:
wvW4-
③轮胎旋转时由于轮胎动平衡不好使车身产生的振动;
]c1@8Z4N8W
④路面不平使车身产生的振动;
2Ex=*P
6
⑤由于传动系的联轴器工作不佳产生附加力偶和推力,使动力装置产生的振动。
ac|]buj)
p@WY
;
频率高于30Hz的高频振动源如下:
MC-]{ZH
①在发动机高速运转时,由于惯性力及其力偶使动力总成产生的振动;
C
0M=_!
②变速时产生的振动;
=+:
n2}!
O_
③燃烧压力脉动使机体产生的振动;
YgzC`[YN
④发动机配气机构产生的振动;
S|R71=0.
⑤曲轴的弯曲振动和扭振;
pw~,1HB
⑥动力总成的弯曲振动和扭振;
/cMmNBx
⑦传动轴不平衡产生的振动。
\i^#f[
总之,使发动机总成产生振动的主要振源概括起来有两类:
一为内振源,主要是由于燃烧脉动、活塞和连杆的运动产生的不平衡力和力矩。
二为外振源,主要来源于不平的道路或传动系。
这两种振源几乎总是同时作用,使发动机处于复杂的振动状态。
Aa6@^<
(1)燃烧激振频率`Qxd,4MnRp
这是由发动机气缸内混合气燃烧,曲轴输出脉冲转矩,由于转矩周期性地发生变化,导致发动机上反作用转矩(又称倾覆力矩)的波动。
这种波动使发动机产生周期性的扭转振动,其振动频率实际上就是发动机的发火频率,计算公式为:
nwy6JX@
f1=2×
i×
n/60/τ99u$"
G@d-D
式中:
f1-点火干扰频率;
Hzs-M$EOn(
τ-发动机冲程数;
(2或4)Wj{~D2,
i-发动机气缸数;
-oEA=A
n-曲轴转速,r/minPqG0{'
*^
(2)惯性力激振频率FKKhLf
由不平衡的旋转质量和往复运动的质量所引起的惯性激振力和力矩的激振频率为:
3:
eApv[
f2=Q×
n/60!
.~{Z9
f2-惯性力激振频率;
twmsm
Q-比例系数(一级不平衡力或力矩Q=1,二级不平衡力或力矩Q=2)。
"
aP,L,z
不平衡惯性力的激振频率与发动机的缸数无关,但惯性力的不平衡量与发动机缸数和结构特征有着密切的关系。
8hmY;
=
关于外振源,归根结底是路面的激励,经过车轮、驱动系统、转向系统及车架等而传递到动力总成,因此在选择悬置系统的固有频率时,需要考虑到车辆与发动机连接部分的共振频率。
BnB?
=EK!
jx
因此,悬置系统特性的选择首先要隔离发动机自身的振动,即不让发动机不平衡力造成的振动过分地传向车体。
这就要求悬置系统的固有频率低于发动机怠速工况下激振频率的0.7倍。
车体结构振动的降低,十分有利于降低结构振动造成的噪声。
当前汽车发动机的悬置软垫都相当软,发动机的固有频率大多处在6-20Hz的范围内。
如此低的频率,当汽车以正常车速行驶时,刚好处于不平道路的低频激励阶段,这就带来了路面激励下发动机的晃动问题。
在低频段内,发动机的固有频率与整车特性匹配不当时,路面激励所造成的发动机晃动可能引起汽车乘坐舒适性下降,也可能影响到汽车的操作性。
3U1gx"
@h
75iw.i6P>
k
悬置系统的布置/a@(2yi6
u|xr
c
1)悬置点的数量
k^6_u,>
X
悬置点的数量根据动力总成的长度、质量、用途和安装方式等决定。
悬置系统能够有3、4、5点悬置,典型的布置见图3-16-1。
5kl3l$,
一般在汽车上采用三点及四点悬置系统。
因为在振动比较大时,如果悬置点的数目增多,当车架变形时,有的悬置点会发生错位,使发动机或悬置支架受力过大而造成损坏。
w3Azd~go
三点式悬置与车架的顺从性最好,因为三点决定一个平面,不受车架变形的影响,而且固有频率低,抗扭转振动的效果好。
值得推荐的是前悬置采用两点左、右斜置、后端一点紧靠主惯性轴的布置方案,这种布置具有较好的隔振功能。
在四缸机上得到广泛应用。
而前一点、后两点的三点式多用于六缸机。
#],{VX7w
四点式悬置的稳定性好、能克服较大的转矩反作用力,不过扭转刚度较大,不利于隔离低频振动。
但经过合理设计,仍可满足四缸机、更能满足六缸机的要求。
四点式悬置在六缸机上的使用最为普遍。
图3-16-2是典型的三点式和四点式悬置。
?
3E%:
*-K
在重型汽车上,因为其动力总成质量和长度大,为了避免发动机机体后端面与飞轮壳接合面上产生过大的弯矩,一般在变速器上增加一个辅助支点,从而形成五点式悬置。
由于该支点距动力总成的质心最远,又是过定位点,因此辅助支点刚度不能太大,以避免因车架变形而损坏变速器或悬置支架。
zu)gh
Kh%ao(Mrl
2)悬置系统的解耦7LQ5<
RK
(1)悬置系统的解耦目的A<
e_o6
当弹性支承的刚体在一个自由度上的自由振动独立于另一个自由度上的自由振动时,我们说这两个自由度的振动是解耦的。
发动机悬置系统实际上具有六个自由度,而且是互为耦合的。
耦合的作用使发动机振动互相激励而加大,振动频率范围变宽。
这样要想达到同解耦时相同的隔振效果,就需要更软的悬置软垫,这就使得动力总成与周围零件之间有较大的相对位移,造成风扇与护风罩相碰或其它部件之间产生振动干扰,给整车布置造成困难。
由于软垫的较大位移,使橡胶内应变增大而影响其使用寿命。
1$-*yXG
另外,由于各自由度振动的互为耦合,很难对某个产生共振的自由度上的频率进行个别改进而不影响其它自由度上的隔振性能。
/L2[+a
(2)悬置系统弹性中心LnG2N
作用于被支承物体上的一个任意方向的外力,如果经过弹性支承系统的弹性中心,则被支承物只会发生平移运动,而不会产生转动。
反之,被支承物体在产生平移运功的同时,还会产生转功,即两个自由度上产生运动耦合。
hk:
E\4--
同样,如果一个外力矩绕弹性中心主轴线作用于被支承物体上,该物体只会产生转动而不会产生平移运动。
反之,物体在产生转动的同时,还会产生平移运动,同样出现两个自由度上的运动耦合。
#cfp
弹性中心是由弹性元件的刚度和几何布置决定的,与被支承物体的质量无关。
它对弹性系统而言,犹如质心之于刚体。
如果刚体质心与支承系统的弹性中心重合,则振动将大为简化。
lz.m
理论上,如果使发动机悬置系统的弹性中心同发动机总成的质心重合(图3-16-3),就可获得所有六个自由度上的振动解隅。
实际上完全解耦在悬置设计中是难以实现的,因为发动机的主要激振力只有垂直和扭转两种,而悬置设计中存在较多的约束。
因此只要在几个主要方向上获得近似解耦就行了。
V
Vv$=W0
3)悬置系统的布置|+?
6+8@
动力总成一般有三个弯曲模态,如果把前悬置点布置在节点上,使得弯曲模态在节点上不能被激发,则可将车架与发功机引起的弯曲振动激振力相隔离,发动机的垂直振动不致传到车架上。
一般应尽可能将前悬置点布置在动力总成一弯模态的一个节点上,以减小振动传递。
Yn{dqH^
出于解耦的考虑,应根据撞击中心理论将后悬置布置在前悬置点的共轭点上,使前、后悬置点的冲击不至于相互影响,从而达到良好的隔振效果。
5j`U!
PE!
Lf•LR=Jy/mmhKxiM9Xg
Lf-前悬置点离动力总成质心G的纵向距离;
OC78XEa-
LR-后悬置点离动力总成质心G的纵向距离;
i,g<
s(:
JY-动力总成绕Y轴的转动惯量;
9i]]~5
M-发动机-变速器动力总成的质量。
gE!
mAQ,
前、后悬置的刚度还要根据承载量及到质心的距离合理地匹配,达到垂直及俯仰方向上的解耦。
*e>
IN;
n?
z+
KFV•LF=KRV•LR|$aKjl
KFV、KRV-分别为前后悬置的垂直刚度N/cm。
M>
p9YM90
悬置点如为一点,则尽可能靠近动力总成的最小惯性轴。
如为两点,出于解耦的目的,最好是呈V形布置,一般倾斜角度θ:
40o~45o,如图3-16-4所示。
zkVhuS`>
V型布置的悬置系统的弹性中心较低,在设计中经过倾角及位置的调整容易使其弹性中心落在或接近动力总成的主惯性型轴上。
如果假设悬置软垫在两个剪切方向上的刚度近似相等,有下列公式。
s/K)_"
e+[
垂直刚度:
KV=2(kpsin2θ+kscos2θ)bj%fqS5BB
侧向刚度:
KL=2(kpcos2θ+kssin2θ)U*q$DIkY
扭转刚度:
Kθ=2B2kpks/(kpcos2θ+kssin2θ)e!
ZQvJYm
θ-α=arctan(tanθ/k0){4dJ'
uT^oh
式中k0—悬置软垫的压缩刚度与剪切刚度之比,即k0=kp/ks;
h:
}1Dj5(
A—弹性中心高度;
3T~X
qR\
B—软垫支点到半水平距;
JV,rG]s
α—弹性中心到支点的连线的仰角;
$aVdg+6V
θ—悬置软垫的安装倾斜角;
xoJ+)vW
在实际设计中还有许多其它的布置形式。
如非对称的V形布置、平置、吊挂式等。
^r>
18p{U)
4)轿车发功机的悬置布置特点kuM&
>
Pty
轿车发动机一般采用四缸四冲程发动机.发动机前置、横置、前轮驱动,即FF式布置。
FF驱动方式下驱功反力矩直接作用于动力总成上,使发动机悬置受到较大的力。
因此,为限制发动机及排气系统等的位移,发动机悬置要有必要的刚度。
另一方面,为了减小怠速及中高速区域的振动噪声,要求发动悬置具有具有较好的柔件,达到良好的隔振性能。
作用于发动机悬置上的驱动反力矩,在FR式场合,就是动力总成输出最人转矩时所产生的最大反作用力矩,即倾覆力矩,它等于发动机最大转矩乘变速器最大减速比。
这—倾覆力矩主要由后悬置来承担,力矩方向与发动机旋转方向相反。
因此在后悬置一侧的软垫上将产牛很大的额外压缩负荷。
但在FF式的车辆上,则为差速器(驱动轴)的输出转矩。
因此FF式的驱动反力矩为阳式的3~4倍。
WRsn=O
另外,在主要采用横置发动机的轿车上,差速器的驱动反力矩与发动机转矩波功的激振方向一致,并和车身弯曲的方向相同,因此在横置发动机的悬置布置中,有以下特点:
T9!
<
G:
Dd
①因降低发动机的扭转刚度应有一定的难度,很难确保对发动机转矩波动激振的隔离。
Uu5sp%"
②因为车身弯曲共振频率接近于发动机扭转振动频率域,且振动方向一致,因此容易发生低速时的振动。
rh6,
③发动机、变速器及差速器成为—体,因此瞬态变化剧烈。
aV8^I'
hCA
根据上述特点,在悬置设计上大致分为低速区域的转短波动激振及中高速区的惯性激振两部分。
悬置系统一般采用四点支承,其中一点为辅助点。
在设计上尽时能减小振动的耦合度。
采用非线性、变刚度的悬置软垫,提高低转矩时的隔振效率、减小大转矩时的振动位移。
f1D*+U\VR
图3—16—5,给出的前置发动机前轮驱动汽车发动机的悬置布置方案中,利用A、B、C三个悬置支承发动机装置的质量。
其中驱动转矩反力主要被C、D两个悬置所承受,这二个悬置的弹性和距离,也决定了动力装置的横滚共扼频率。
在这种汽车上,由于最终减速机构布置在变速器内,驱动转矩的反力较大,为了限制动力装置的位移,必须把动力装置的横滚共振频率设定的较低。
为此,C、D俩点大都采用非线性刚度系数的悬置软垫。
rv
8
Y0o
XUdefmn
悬置软垫的设计lJI!
au!
nUsm,DcVAz
1)悬置软垫的负荷h&
(5swr
一般前悬置位于发功饥机体前端或机体前部两侧,与后悬置相比、远离动力总成的质心,因此动力总成的垂直静负荷主要由后悬置承担,而前悬货主要承受扭转负荷。
对后悬置来说.距离动力总成的主惯性轴较近,承受较小的扭转负荷及振幅。
同时,由于它处于发动机动力输出端,受传动系不平衡力的严重干扰和外部轴向推力的冲击,当发动机输出最大转矩时.支承点出现的最大反作用力也应由后悬挂来承担。
因此后悬置的垂直刚度较大,也起着限制动力总成前后位移的作用。
悬置系统同样还承受了汽车行驶在平平道路上的颠簸、冲击、汽车制动及转向时所产生的动负荷(表3-6-1)。
@t>
FQzX
2)悬置软垫的机构形式rCt8=1
在设计发动机悬置时。
必须充分的考虑悬置的使用日的,例如支承的质量和限制的位移等,选择合理的形状。
悬置的基本形式有三中,即压缩式、剪切式和倾斜式,见图3-16-6。
表3-16-2,给出了这二种悬置的基本特性及用途。
一般采用倾斜式的悬置结构,利用这种悬置的弹性特性,支点设定能够获得较大的自由度。
&
{:
E3d~Ms
表3-16-1不同使用工况下可能出现的冲击加速度值1xEM>
#^b\
应用形式垂直加速度(g)cus$jJW
公路用车辆±
4mGO4(Kp
越野车辆±
6mD$G
n,f
发电机组±
6$C5_2|
船用(包括辅助设备)±
6]um"
g|
叉车±
3!
7G@v=CTE
X--p@5GZ@
表3-16-2悬置软垫的基本特性及用途h)Cekq4C2Z
]in]HS(
悬置形式压缩式倾斜式剪切式k(,SWDE(|G
弹性!
N4CYVC
特性压缩刚度大>
op@A"
-CC
剪切刚度小压缩、剪切x48H
特性均好压缩刚度小BUAm
$N
剪切刚度大sx}kKdFS
主要U0"
dVAY
用途用于振动输入小、支承质量大的场合用于振动输入大、支承质量大的场合用于振动输入小、支承质量小的场合/_1WU-5G
XH(lu{eY3O
3)悬置软垫的限位、2sqW
~K
如果动力总成的位移过大,使动力总成本身,或它进排气系、操纵机构管路、接线等和周围的机件相碰,产生损伤。
同时悬置软垫也容易损坏。
为此,必须从悬置结构上限制过大位移。
~N5jx554
①增加位移较大的方向上的悬置刚度。
例如,在汽车加速行驶或转弯行驶时,动力装置产生的惯性力,可能使动力装置产生较大的位移。
为了限制动力装置的位移,应该在前后、左右方向上设置较硬的悬置.防止动力装置出现过大的位移。
Oa.\pz|)[(
②采用非线形、变刚度的悬置结构,以同时减小小激振力引发的振动和限制大激振力时大的振动位移。
例如.在汽车停驶发动机怠速运转,或汽车等速行驶时,发功机的输出转矩较小。
这时,悬置软垫的刚度较低,能有效地隔离振动。
在快速起步时,驱动转矩的反力十分大,可能使动力装置产生左右横滚的振动。
另外,汽车在不平整路面上行驶时,随着整车的大幅度上下颠动,动力总成也产业很大的上下惯性力。
由于这时悬置软垫的刚度变大,也能有效地限制动力装置的振动和位移。
悬置软垫限位结构的实例如图3-16-7所示。
IUZTkKa
4)悬置软垫的可靠性lrr|l2iJ-
(1)疲劳破坏8V|U!
Q)
橡胶材料的循环变应力的作用下可能出现疲劳破坏,设计时应注意橡胶的许用应力和许用变形,表3-16-6,给出了一般悬置橡胶材料的许用应力和许用变形。
xX7]iu/p
(2)老化.5*QD_5t
悬置软垫在使用中,不可避免的会受到热、臭氧和紫外线等的作用、造成悬置软垫的抗拉强度、力学性能下降,并产生裂纹。
因此在悬置设计中应使悬置软垫远离热源或加以隔离。
]cz|XeQJ
表3-16-3悬置软垫许用应力和变形+:
&
XM/
*}YU$8/
变形形式允许应力允许变形P}:
iJ
ds
压缩1~1.515~20{^WK_+]i
剪切0.1~0.220~30dtVj]^hr?
`'
12B'
(3)永久变形bB}TmoQ;
BD
悬置软垫在使用中重复地变形,或受热等因素影响下,橡胶将产生永久变形,使橡胶的尺寸发生变化。
anq=H
(4)粘接面的剥离vE-f$/pkq
一般设计中要求橡胶与金属骨架的粘接强度高于3MPa,但由于产品质量问题或软垫在高温环境下长期使用后,粘接面的粘接强度下降并引起剥离而导致损坏。
;
M=*YA
5)悬置软垫橡胶的材料cv_;
l)uc5}
在设计中应根据使用要求选择符合要求的橡胶材料。
当前主要采用混合橡胶,它以天然橡胶为主料,添加了部分丁苯橡胶.有的悬置也采用了丁腈橡胶。
当前采用的减振橡胶材料有一般的加硫橡胶,如NR(天然橡胶),SBR(丁苯橡胶),BR(丁二烯橡胶),IR(异戊橡胶);
特殊的耐油加硫橡胶,如NBR(丁腈橡胶);
特殊耐候(轻度耐油)橡胶,如CR(氯丁二烯橡胶);
阻尼力教大的橡胶,如IIR(丁基橡胶);
特别耐热的加硫橡胶,如EPDM(乙丙烯橡胶)。
lUO)H1hm>
6)悬置软垫的阻尼`e+L.PT@x
根据悬置系统的幅频响应特性,当动力总成在低频振动时,为了减小振动的振幅,应采用阻尼因数较大的软垫,此时阻尼越大,振动响应越小。
其中,最典型的例子是冲击。
而当动力总成作30Hz以上的高频振动时,由于激振力的频率较高,能够不必考虑动力总成悬置系统的共振问题。
为了降低动力总成的振动对整车的影响,切断高频振动的传递。
应该使振动系的阻尼越小越好,此时阻尼越小,振动响应越小。
oTF/25aC
+
fpka
液压悬置Qij"
-4?
B
只使用橡胶软垫,很难产生很大的振功阻尼。
为了改进冲击等过大的振动,悬置必须具有很大的阻尼力,这就是液压式悬置,它同样可降低高频时的悬置刚废,提高减振、降噪效果。
Brv1+btL
1)液压悬置的构造j+94@d[G
液压悬置的基本结构见图3-16-8。
用一个中心螺栓将一个普通的锥形橡胶悬置垫固定在顶部,与隔板一起构成上腔,下腔由一个弹性皱皮膜和隔板构成,皱皮膜由—个固定盖保护,固定盖与皱皮膜构成与大气相通的气室,隔板上开有一个活动板。
同时隔板上开有小孔,阻尼缓冲液可由隔板上的小孔经上腔流到下腔。
5m>
ss@;
YxGJ=-9K
2)液压悬置的工作原理}QQr}HZ#
当发动机高频小幅振动时,上腔内压没有上升,这样可得到较小的悬置刚度以减小振动(图3-16-8a)。
当发动机低频大幅振动时,活动板的动作爱到限制、上腔压力升高,流体经过阻尼孔流人下腔,利用流体的流动阻力,产生很大的阻尼力,从而使振功得到很大的衰减(图3-6-8b)。
在设计液压式悬置时,能够改变某些参数,自由地设定共振频率,例如改变液压悬置的动态参数,节流孔的口径和孔长等,这样,利用液体的共振现象,就能实现任意的动态弹性特性。
有的液压式悬置还设有高频节流孔等附加机件,能改进240Hz以下的动态弹性特性。
液压悬置的动态特性见图3-16-9。
O*vZA2tPC
M~7,M#>
悬置系统的设计程序Vy`Uj
①确定动力总成的总质量,包括内部注满的机油和冷却液。
|.;
3%~rS!
②确定动力总成的质心位置。
s2#&
Q!
③确定动力总成主惯性轴的位置。
5(uhta
④测出或估算出动力总成绕三个主惯性轴的转动惯量。
3tuxmTk
⑤设定动力总成前、后悬置支承点的数目,布置形式,各支承点离质心和主惯性轴的位置及相应的几何尺寸,并结合解耦原理作必要的分析计算。
D!
=q3"
[
⑥分别计算前、后悬置支承点上承受的静态负荷。
p"
$`q
⑦计算发动机机体后端面与飞轮壳接合面上的静态弯矩,该弯短值必须在发动机制造商规定的范围内;
否则,应调整前、后悬置支承点的位置或增加尾部辅助支承点,使该处的弯矩值控制在限值内。
I_VEVXT;
⑧计算发动机、变速器总成在悬置软垫上可能引起的最大转矩反作用力。
可用两种计算标准,一是发动机输出最大转矩时,另一是发动机在额定功率点时(包括最大变速比)。
然后根据软垫制造商提供的软垫“负荷——变形”曲线,核对所选样的软垫是否能承受这一作用力及软垫的最大变形量是否在合理的范围内。
^Km0z2V
⑨按实际应用情况,确定动态负荷冲击加速度的数值。
ToczM
M:
H
⑩设计悬置支架,按动态负荷计算进行强度校核。
若发动机制造商没有提出机体后端面与飞轮壳接合部位的静念弯矩限值,则应按动态负荷计算该部位的弯矩和工作应力,保证该薄弱环节安全可靠。
L)B&
8#_v
⑾选择合适的悬置软垫,应能承受上述动态负荷,并满足隔振要求,确定软垫的刚度。
Gotc8~~E
⑿根据所选择的软垫的压缩和剪切刚度及系统布置形式,分别计算前、后悬置的垂直综合刚度,侧向综合刚度和扭转综合刚度及相应的固有频率(如果是平置式布置,则系统的垂直方向固有频率和隔振效率可从软垫制造商提供的坐标图上根据静态变形量确定)。
oKLxXl=
⒀确定发功机的外激振频率。
bS$J|95
⒁经过软垫制造商提供的坐标图,按照软垫的静态压缩量以及外激振额率,确定悬置系统的隔振效率。
O;
gG]O@
⒂检查悬置系统是否具备克服其它外力和惯性力的能力,必要时应设置限位装置。
8pOce=
⒃选择能满足工作环境条件的需要的悬置软垫的材料。
n>
g`yw
⒄校核悬置系统的结构布置能否适应整车提供的空间,确保不与周围零部件发生干涉。
M/z$=~
⒅试验。