纺织病疵分析经验分享Word文档下载推荐.docx
《纺织病疵分析经验分享Word文档下载推荐.docx》由会员分享,可在线阅读,更多相关《纺织病疵分析经验分享Word文档下载推荐.docx(58页珍藏版)》请在冰豆网上搜索。
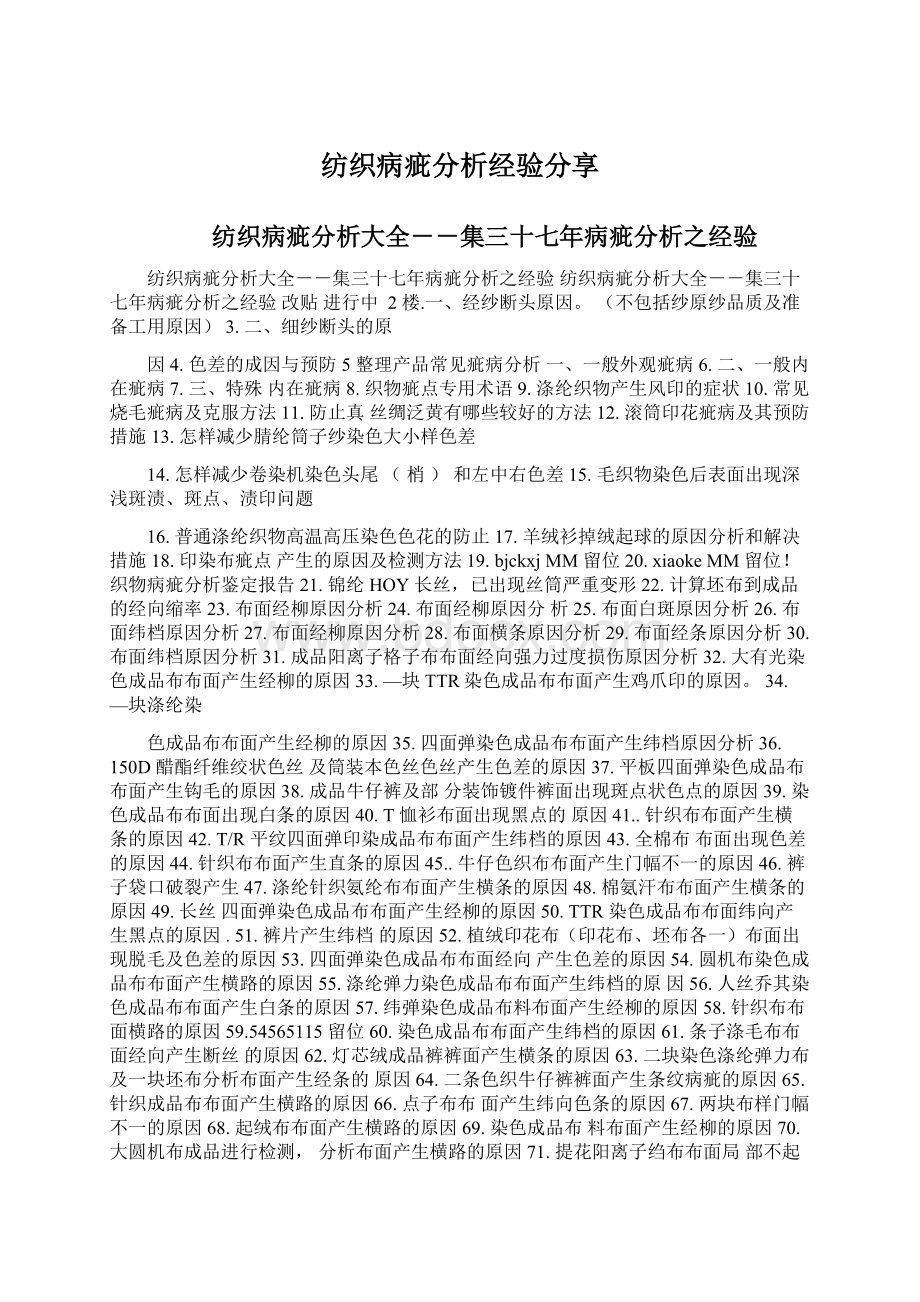
4.后梁及停经架位置赤字高,上下层经不张力悬殊太大。
5.停经架与综框距离过远过低。
6.空气调节、湿度过高过低。
(尤其麻纱反应最大)
7.剑颈、钢筘、综丝、停经片、剑带等毛糙。
8.过撑位置过高,应距最低位置1mm。
9.结头纱尾、飞花杂物搅入经纱。
10.值车对经纱倒断头、搅头处理不良,断经后接纱结头不良;
如纱尾长。
二、断纬原因
1.纬纱强力过低、松捻纱、大结头、棉籽屑、飞花回丝夹附。
2.络筒时强力过太、张力太大、成形不良。
3.边撑太前撞筘,距离钢筘到少要有1mml的间隙。
三、双纬
1.纬纱断头为主要原因,首先须减少断纬线。
2.值车工不注意在断头后,未将织口内断纬拉清。
3.值车工在断纬后未将开开口顺序较主合适时开车。
4.纬纱断头后断纬运动未立即作用停车,而中间缺少数根或一根纬纱
四、缩纬
1.纬纱捻度过大。
2.纬纱太干或太湿。
3.开口不清。
4.开口时间过早或过迟。
5.纬纱引出张力太小。
6.经纱张力不足。
7.纬纱筒子有大结头、飞花、杂物附着、粗节纱造成部分开口不清。
五、小稀路
1.筘座及卷取刺毛辊松动或腐蚀。
2.经纱张力过大或过小。
3.经纱上下两层纱张力相差悬殊。
4.停车过久后开车时梭口未较正。
5.停车后开车起动太缓慢影响打纬力。
(主电机皮带松驰无力)
六、纬纱尾织入
1.右测经纱距离顺风管太远,废边纱未能很好夹持纱尾。
2、纬纱张力太小,剑头开启时间太晚。
七、稀路
1.起因均为断纬、首先须减少断纬。
2.断纬卷取退卷绕装置不良。
八、跳花
1、综框松动、不平或过低。
2、经纱张力上下两层相差悬殊。
3、浆纱过毛、开口粘滞、上浆不良引起绒球或毛羽。
4、经纱有飞毛、纱尾及大结头。
5、综丝头尾损断或综丝搅乱。
6、部分经纱松弛或张力过低。
7、开口时间不对。
(开口过小)
8、边撑高低不规范。
9、钢筘筘号过密,请核对筘号及工艺单。
10、每筘纱根数过多,核对工艺单。
九、蛛网
1、停经片密度大,断经后不立即停车。
2、停经片间积聚飞花,运动失灵。
3、开口内有飞花,纱尾,杂物。
4、综丝损断。
5、纬纱张力突然过大,边撑将纬纱勾断成边蛛网。
6、停经片残缺、弯曲、过轻(重量)
7、一根停经片内有两根以上经纱。
8、其它断经原因。
十、密路
1、值车工断纬时退出布面过多或折坏布时退出布面过多
2、卷取部分扎着杂物、或不够润滑。
3、刺毛辊、刺毛皮伤残或磨损严重。
4、压布辊压力不够或弯曲。
5、落布时卷布未卷紧。
6、卷布辊过于光滑。
十一、筘痕、方眼、布面毛糙
1、上下层经纱张力相差过大。
2、综框不平,过高过低。
3、经纱张力太大太小。
4、后梁太低,停经架太低。
5、开口太大或开口不清。
6、开口时间太迟或过早。
7、浆纱过硬。
8、每筘经纱根数过多。
9、浆纱太毛、开口粘滞。
10、筘齿太厚或分布不均匀。
11、工场太干燥。
12、纬纱张力引出不均匀。
十二、边撑疵
1、边撑针号太粗或太细。
2、边撑针尖弯曲或损断。
3、边撑刺毛圈转动不灵活或磨损。
4、边撑位置不对。
5、布面张力过高或过低(经纱张力)
6、纬纱张力过大。
7、边撑内夹有飞花、杂物、纱尾等。
十三、断边纱
1、边撑转动不灵活或刺毛辊磨损。
2、边撑位置过高过低过前过后。
3、筘齿挤逼弯曲或松动或毛糙。
4、开口时间不合。
5、罗纹织边、开口过大过低过高过早过迟。
6、经纱筘幅过阔过窄。
7、织轴经纱过阔过窄。
8、纬纱引出张力过大。
9、边纱穿法及边纱根数不合。
10、经纱张力过大或过小。
11、织轴卷绕时边纱下陷。
十四、毛边、毛巾边
1、纬纱引出张力过小。
2、边纱穿法不合规定。
3、织边开口过高过低过早过迟或开口不清。
3、钢筘、筘齿松动或挤逼。
4、边撑位置太高、太低、太后。
十五、紧边、袋形布、硬边
1、边纱每筘根数过多、减少后能改善。
2、纬纱张力过大。
3、边纱张力过大。
4、平纹改为2/2罗纹纱,多数能改善
5、边纱穿法错误。
6、边撑太短或未用足,伸张力不足。
7、边撑太后。
8、织轴宽度与布幅宽相差过大十六、松经、紧经
1、经纱倒断头(并轴时)
2、经纱两根以上有并粘、在织造时分开时紧时松
3、经纱与停经片缠绕。
4、经纱飞纱时经过线路不良时紧时松。
5、坏综丝。
6、经纱络筒时纽结伸展松弛。
7、废经纱绕于织轴上压住邻纱。
8、经纱上有飞花球,纱尾绕在综丝和停经片处。
9、织轴卷绕太松而织造时经纱张力较高形成下陷。
10、织轴浆纱时长短不一,了机时松紧不一。
11、停经架距综框过远(用速度慢)
12、停经片过轻、弯曲。
十七、簇织
1、经纱开口内夹尾纱或经纱断头飞花杂物移去后形成一簇经纱被拉长。
2、经纱上有纽结将一簇经纱拉长。
3、经纱一簇减受外力被拉长。
十八、布边不平齐
1、纬纱引出张力过小或过大不均匀。
2、织轴经纱过阔。
3、边织开口过大、过低或边织综框过后。
4、梭眼内有飞毛纱尾杂物。
十九、边蛛网
1、综丝内有纱尾、飞花等。
2、纬纱张力过大、同时经纱边纱张力特别小。
3、边撑位置太后。
4、边纱穿法不合、边纱并绞。
二十、狭窄边
1、边纱根数过小。
2、纬纱张力过强。
二十一、脱边
1、边纱开口内夹有尾纱等。
2、边织开口时间不合。
二十二、绒球
1、上浆率过低。
2、浆液配合不适宜
3、上腊过多。
4、经纱受潮或霉烂。
5、经纱烘干不够。
6、钢筘筘齿生锈或毛糙。
7、停经架歪斜、或停经片过重。
8、经纱张力过强
二十三、弯纬、弓形纬
1、边撑位置过高或太后。
2、边撑长度不够。
3、边撑针号太细。
4、边纱张力过大过小。
5、边纱穿筘过密。
二十四、油污
1、前工序精纺、络纱、浆纱时沾上。
2、运输中沾上。
3、修机工、挡车工手不洁。
4、其他情况下沾上。
二十六、破洞、撕破
1、硬物或尖锐物碰撞布面或卷取刺毛辊。
2、刺毛辊及布边破损。
3、满布辊及布边搬运中摩擦。
4、边撑刺毛圈针号过粗过细。
5、布面张力过紧
二十七、染色不匀
1.用纱混棉不一律或混合错种类纱支。
2.用纱捻度差异大。
3.用纱稳定处理条件不一律。
4.用纱发霉或染油污。
5.浆纱时渗上腊过多。
6.浆纱浆料不易褪清。
7.部分经纱受意外磨蹭。
二十八、错纬
1、引纬错误
2、纬管色泽用错
3、络纱时混入错纱支
4、车工用其他机台不同纬纱二十九、异纤、飞花、杂物织入1、前段工序精纺、络纱、浆纱时沾上。
2、筒子纱不清洁。
3、布机清洁不良。
4、扦纬工作法不良。
5、值车工作法不良。
三十、阔幅、狭幅
1、筘号不适合。
2、筘号错误或不准确。
3、工场湿度过高或过低。
4、经纱张力过小或过大。
5、头份过多或过少。
6、边纱每筘根数过少或筘数不足或过大
7、用错细支或粗支纬纱或纬密过疏过密。
二、织造品质风险及成因2:
细纱断头的原因
细纱断头是细纱生产中的主要危害:
影响细纱机的产量,降低生产效率。
增加挡车人劳动强度。
易造成布面疵点增多,引起大幅度的质量波动。
增加回花、回丝、机物料消耗。
所以说断头是如今细纱高产、优质、低耗、大卷装生产发展的障碍。
细纱断头概括地可分为两类:
成纱前断头和成纱后断头。
1、成纱前断头的分析指前罗拉纺出纱条前的断头,其原因主要有以下几点:
1.1、粗纱断裂:
若粗纱总是在上部换向附近断裂,可能因为粗纱捻度小所致。
若粗纱总是于下部换向附近断裂,可能是细纱导纱杆位置偏高所致。
前纺机械原因形成的粗纱细节,也会导致细纱断头的增加。
1.2、挡车工责任心差,清洁不净,巡回不勤所造成的喇叭口积花、空粗纱,以及车间温湿度不好造成的绕胶辊、绕皮圈、绕罗拉等形成细纱断头。
2、成纱后断头的分析指从前罗拉至筒管间这段纱条在加捻卷绕过程中发生的断头。
其原因主要与以下几点有关:
2.1、锭速的影响锭速增加,则成纱后的断头增加。
其原因是:
锭速提高后,钢丝圈回转所产生的离心力增加,纱线的张力也随之增加,从而导致断头增加。
锭子在恒速转动时,落纱断头的分布是:
小纱最多,大纱次少,中纱最小,其比例为5:
2:
3。
细纱断头的原因在排除空调、机械操作及清洁工作不良、筒管不良、粗纱不良等因素后,采用变频器调速,细纱断头可降30个百分点左右。
2.2、纲丝圈重量的影响钢丝圈的重量影响纺纱张力的大小。
钢丝圈太重,纺纱张力大,使钢丝圈对纱线的摩擦增加,纱线断头增加;
钢丝圈太轻,纺纱张力小,气圈过大,造成纱线碰隔纱板,使相邻两锭间相互干扰,导致断头增加。
在选钢丝圈的重量时,要考虑以下因素:
2.2.1、纱线品种纱线愈粗,单纱强力增大,钢丝圈的重量应愈重;
在纺化纤时,由于化纤的弹性较好,易伸长,在同样重量的钢丝圈条件下,化纤纱线与钢丝圈的摩擦系数大,气圈张力小,故气圈成形大,易断头;
所以纺化纤时钢丝圈重量应比棉重2-3号,纺中长纤维时,重6-8号。
2.2.2、锭速锭速高时,纱线的离心力和纱线张力均增加,故应适当减轻钢丝圈的重量才能减少断头率。
2.2.3、钢领的使用时间的影响同等条件下,钢丝圈的号数随钢领运转时间的不同而不尽相同。
新钢领或修复后的钢领上车,钢丝圈与钢领的摩擦系数大,钢丝圈必须偏轻掌握;
随着钢领使用时间的增加,钢丝圈与钢领的摩擦系数减小,钢丝圈应适当加重;
钢领衰退到后期时,跑道磨损变形,出现拎头重,飞圈多,断头会剧增,这时应适当减轻钢丝圈重量。
钢领的使
用周期与纱线的品种结构、锭速的高低有关。
纱线号数越小,钢领的使用周期越长;
随锭速的加快,钢领的使用周期要缩短。
平面钢领的使用周期为12个月,6个月修复1次;
锥面钢领的使用周期为16个月。
但随着产品的
小批量,多样化,改号次数的增多,钢领的使用周期缩短为:
平面钢领4个月修复1次,8个月报废;
锥面钢领
13个月报废;
这样才能减少断头,保证成纱质量。
2.2.4、钢领的直径与筒管的长度钢领直径增加时,主要是卷绕小直径时,张力增加较多,若采用较重钢丝圈,在大纱卷绕小直径的部位,气圈形态更为平直,更易造成大纱断头。
故钢领直径增加时,应减轻钢丝圈的重量;
筒管高度的增加会引起纱线张力增加和气圈最大半径的增加,造成断头增加,所以应加重钢丝圈来加以解决。
2.2.4、钢领型号在实践中发现,钢丝圈重量的选择还要根据钢领的型号。
在其他相同条件下,使用锥面钢领纺纱比使用平面钢领纺纱所用的钢丝圈偏重掌握,可增大卷装容量,减少落纱次数,又可减少断头。
2.3、钢领、钢丝圈型号的选择及配合对断头的影响钢领、钢丝圈的型号及其配合,影响钢丝圈纱线通道大小及钢丝圈运行的平衡状态,从而影响纱线的断头。
在实践中发现:
平面钢领类适纺的纱号比较广泛,但在目前小批量、多品种生产、改号频繁的情况下断头增加;
而锥面钢领能适应频繁改号,但在适纺中、粗号纱时,在纺细号纱时断头特别多。
在实际生产中,钢领的型号一般是确定的,需要选择的是钢丝圈的型号。
在选择钢丝圈的型号时,必须考虑适纺品种,纱线粗细及锭速高低等因素。
2.4、合理确定钢丝圈使用周期
随着钢丝圈的高速运行,磨损到一定程度,钢丝圈与钢领间的配合状况差,运行的平稳性差,纱线张力波动大,使断头增加;
所以,必须合理确定钢丝圈的使用周期。
钢丝圈的使用周期与原料、纱号、锭速、卷绕都密切相关。
正常情况下纱号越粗,锭速越高,卷装越大,都会使钢丝圈的调换周期相应缩短。
在实践中发现:
锥面钢领在新上车纺中、细号纱时,钢丝圈在纺一落后就换掉,否则会产生大面积断头。
2.5、捻度对断头的影响纱线捻度在一定范围内增加,纱线的强力增加,有利于减少断头。
在原棉品质较差、短绒较多、成熟度差、纤维细时,采用增加捻度2%左右,可有效地减少断头,但会增加成纱毛羽
色差的成因与预防
一、色差
1.疵病特征:
染色制品所得色泽深浅不一,色光有差别。
(1)同批色差:
同批产品中.一个色号的产品箱与箱之间、件与件
之间、包与包之间、匹与匹之间有色差。
(2)同匹色差:
同匹产品中的左中有有色差或前后有色差或正
反面有色差。
色差是染整厂常见疵病和多发性疵病之一,严重影响染色成品的质量。
2.产生原因各类织物的纤维组成不同,染色时采用的染料种
类及工艺设备不同、加上染色加工中有不同的要求和特点,产生疵病的原因及表现就不一样。
色差在外观表现上多种多样,但究其原因,主要有以下几种。
(1)染料在织物上先期分布不均匀:
染料在固着之前,如果在织物各部位上分布不匀,固色后必然形成色差。
造成这种现象的主要原因为:
1织物因素:
由于纤维性能不同或前处理退、煮、漂、丝不够匀透,使染前半制品渗透性不匀而引起对染料吸收程度的差异。
2吸液因素;
由于机械结构上的原因或操作不当,使织物各部位的带液率不一致,因而造成色差。
轧辊压力不匀、加入染化料不匀等都会使织物吸收染料不匀。
2预烘因素:
在浸轧染液后预烘时,由于烘燥的速率和程度不一致,引起染料发生不同程度的泳移,使染料在织物上分布不匀。
(2)染料在织物上固着程度不同:
尽管染料在织物上先期分布是
均匀的,但在固着过程中.如条件控制不当(如温度、时间、染化料浓
度等),使织物上某些部位的染料没有得到充分固色,在后处理皂洗时即被去除.从而产生色差。
例如,分散染料热溶温度两边或前后不一致、还原染料部分还原或氧化不充分、活性染料汽蒸条件不良等都会造成织物的前后或左右有色差。
(3)染料色光发生变异:
这种差异不是由于织物上染料分布不均匀造成的.而是由于某些原因引起织物上的部分染料的色光发生变化,一般有以下3种原因:
1染前因素:
半制品的白度不匀或pH值有较大差异,在染色后
往往造成色光差异。
2染色因素:
例如分散染料热溶温度过高,使某些染料的色光变得萎暗;
还原染料的过度还原,也会使色光有差异。
2染后因素:
在后整理过程中.如树脂整理、高温拉幅以及织物
上PH值的不同等,都会引起染料色光有不同程度的变化。
④皂洗:
如皂洗不充分,会使发色不充足.色光不准。
3.克服办法
(1)改善轧辊的均匀性。
采用普通轧车染色者,应将轧辊表面车磨成中间直径略微大、两端直径略小的橄榄形辊筒;
合理选择橡胶轧辊的硬度。
(2)采用均匀轧车。
生产单一品种、单一色泽的产品时、用橄榄形辊筒解决边中色差或左中有色差是一个可行的办法。
然而在生产小批量、多品种、多色位品种时.则因为要考虑的因素较多,常需频繁调换辊简.故给使用过程带来麻烦。
采用均匀轧车是解决边中色差、左中右色差的好办法。
(3)选用合适设备,改善设备状态,使被染物在整个染色过程中
能均匀上色。
(4)改善织物干燥的均匀性。
织物进入热风烘燥机后,喷风口风速的大小和温度的高低对水分蒸发快慢的影响不同。
凡风速大、温度高的区域,水分蒸发就快,从而使染液向蒸发快的区域泳移,造成色差。
加工厚类织物时,温度相差10C以内对色差影响不大,
而加工薄织物时,温差大于5C就会有明显色差。
风速左中右相差
4m/s之内,对厚织物影响很小.而风速相差2m/s时,薄织物就会有
明显的色差。
所以必须认真对待,严格调整好风速,并使布面温度及升温速度一致,使织物一致干燥,不致于造成色差。
热风部分采用横导辊穿布方式,对防止正反面色差比较有利。
因为吹到织物两面的热风来自相同的风道。
如果采用垂直穿布的热风烘干机,设备要改装,使上下风口的风量成风速可作适当的调节,有利于纠正色差。
烘筒烘燥机属接触性烘燥,与烘筒接触部位升温快,干燥快,也易造成泳移问题。
所以,使织物先接触的供筒温度适当低一些,再逐步进入高温烘筒.这有利于减少产生色差的可能。
采用红外线予烘、微波烘干等方式,染制品内外能一致烘干.有利于避免泳移产生的色差。
用红外线烘燥织物时,正反两面的红外线辐射必须力求均匀,红外线辐射器与织物的距离不能太近,以防烘燥过急,产生正反面色差。
另外,染前半制品的烘干要均匀一致,使半制品染色时吸液量一致,不能因半制品含水分不均匀造成吸收染化料不均匀而形成色差。
(5)染色时要合理选用染料。
应尽量选择上染曲线相似的染料,以利于减少色差。
染色所用染料要按产地、批号分开存放。
要认真做好测试化验工作,对每批染料的色光做到心中有效,分批使用,防止产生色差。
(6)染色时加入匀染性助剂,如棉针织品投染时加入棉用匀染剂,有利于色差减少。
涤/棉织物轧染时要在染液中加入适当的防泳移剂(例如在染液中添加海藻酸钠、聚丙烯酸衍生物等).这对防止泳移造成的色差具有一定效果。
(7)加强练原经管,为染色提供合格半制品。
1坯布的纤维种类、质量、配比以及上浆情况对染色均有较大的影响。
不同纺织厂的坯布,在相同染色工艺