压力机与垫板间夹紧装置的设计.docx
《压力机与垫板间夹紧装置的设计.docx》由会员分享,可在线阅读,更多相关《压力机与垫板间夹紧装置的设计.docx(22页珍藏版)》请在冰豆网上搜索。
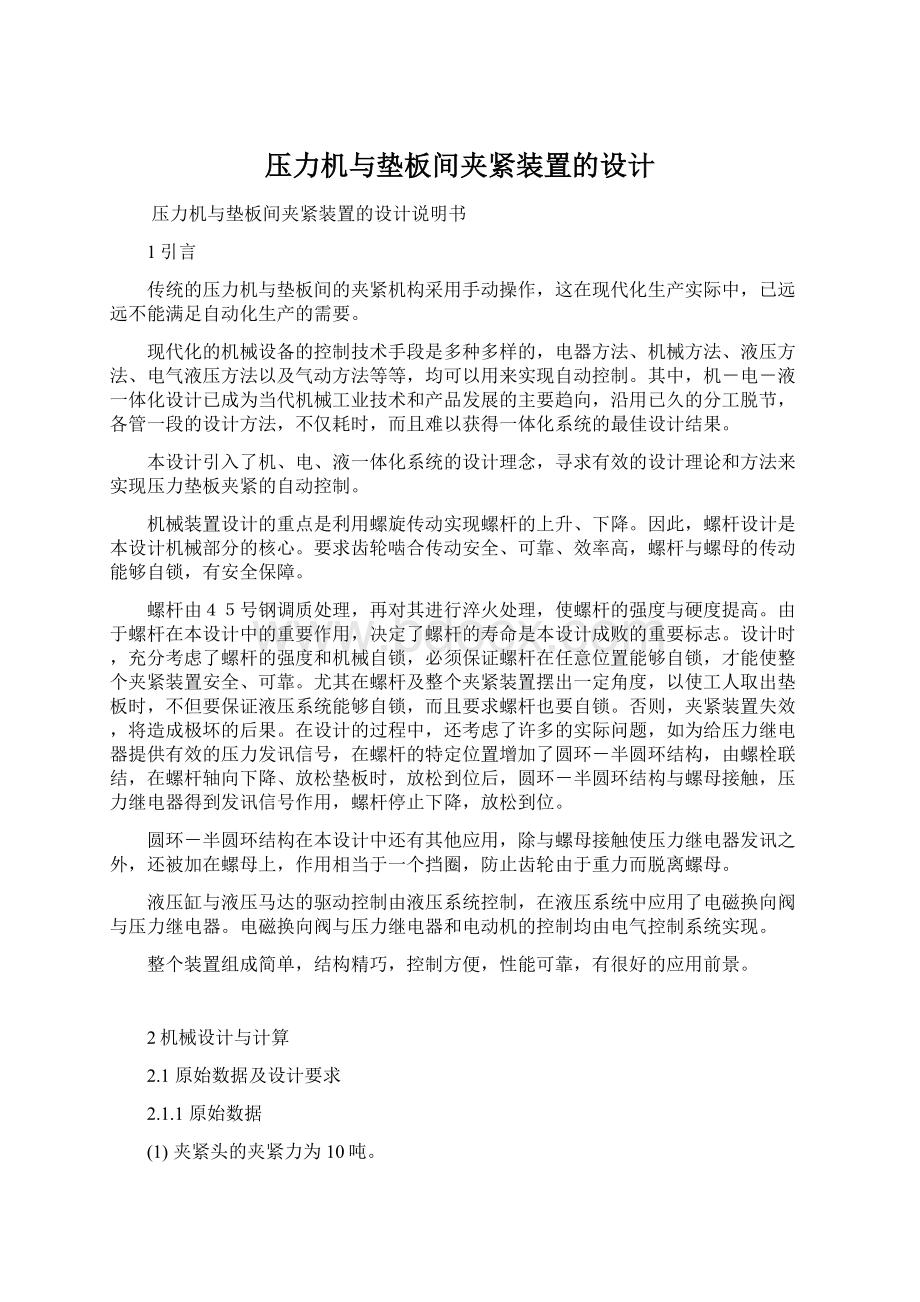
压力机与垫板间夹紧装置的设计
压力机与垫板间夹紧装置的设计说明书
1引言
传统的压力机与垫板间的夹紧机构采用手动操作,这在现代化生产实际中,已远远不能满足自动化生产的需要。
现代化的机械设备的控制技术手段是多种多样的,电器方法、机械方法、液压方法、电气液压方法以及气动方法等等,均可以用来实现自动控制。
其中,机-电-液一体化设计已成为当代机械工业技术和产品发展的主要趋向,沿用已久的分工脱节,各管一段的设计方法,不仅耗时,而且难以获得一体化系统的最佳设计结果。
本设计引入了机、电、液一体化系统的设计理念,寻求有效的设计理论和方法来实现压力垫板夹紧的自动控制。
机械装置设计的重点是利用螺旋传动实现螺杆的上升、下降。
因此,螺杆设计是本设计机械部分的核心。
要求齿轮啮合传动安全、可靠、效率高,螺杆与螺母的传动能够自锁,有安全保障。
螺杆由45号钢调质处理,再对其进行淬火处理,使螺杆的强度与硬度提高。
由于螺杆在本设计中的重要作用,决定了螺杆的寿命是本设计成败的重要标志。
设计时,充分考虑了螺杆的强度和机械自锁,必须保证螺杆在任意位置能够自锁,才能使整个夹紧装置安全、可靠。
尤其在螺杆及整个夹紧装置摆出一定角度,以使工人取出垫板时,不但要保证液压系统能够自锁,而且要求螺杆也要自锁。
否则,夹紧装置失效,将造成极坏的后果。
在设计的过程中,还考虑了许多的实际问题,如为给压力继电器提供有效的压力发讯信号,在螺杆的特定位置增加了圆环-半圆环结构,由螺栓联结,在螺杆轴向下降、放松垫板时,放松到位后,圆环-半圆环结构与螺母接触,压力继电器得到发讯信号作用,螺杆停止下降,放松到位。
圆环-半圆环结构在本设计中还有其他应用,除与螺母接触使压力继电器发讯之外,还被加在螺母上,作用相当于一个挡圈,防止齿轮由于重力而脱离螺母。
液压缸与液压马达的驱动控制由液压系统控制,在液压系统中应用了电磁换向阀与压力继电器。
电磁换向阀与压力继电器和电动机的控制均由电气控制系统实现。
整个装置组成简单,结构精巧,控制方便,性能可靠,有很好的应用前景。
2机械设计与计算
2.1原始数据及设计要求
2.1.1原始数据
(1)夹紧头的夹紧力为10吨。
(2)夹紧过程小于10秒钟。
(3)夹紧的行程为20mm。
(4)系统压力为16MP。
2.1.2 设计要求
(1)夹紧头夹紧后要求有自锁。
(2)整个夹紧装置中的八个夹紧头动作可以分别控制,以便于测试与检修。
(3)综合考虑机械、电气与液压控制的结合。
(4)在设计中要充分考虑使夹紧装置结构紧凑,美观,制造、维修成本低。
2.2 拟定设计方案
驱动机构包括液压马达,液压缸,单级齿轮传动1、2,螺旋-螺母传动。
齿轮用键与螺母联结。
具体用液压马达来带动齿轮1旋转,通过齿轮1、2的啮合传动将动力传递给自制螺母。
将螺杆即夹紧头径向固定,使其通过与螺母的螺旋传动能够沿轴向上升、下降,从而实现夹紧或放松垫板的目的。
通过液压缸活塞杆在垂直方向上的伸缩,实现夹紧装置的摆进、摆出。
即液压缸的活塞杆伸出时,在液压力的作用下,推动整个夹紧装置摆出,并锁紧。
反之,活塞杆缩回时,整个夹紧装置能够摆回,等待下一次的夹紧。
整个系统实现夹紧-放松-摆进-摆出四个动作。
液压缸与液压马达的驱动由液压控制系统来实现,通过液压系统元件来实现液压缸的调速和液压缸与液压马达的换向。
电动机与液压系统中的电磁换向阀和压力继电器的控制由电气部分实现,本设计引入了PLC来进行对电磁换向阀和压力继电器的控制,而电动机则用星-三角启动[1]。
2.3 确定系统的机械参数
滑动螺旋传动主要是承受转矩和轴向力。
因轴向力的作用,螺旋副旋和面间的压强很大,而且相对的滑动速度又大,所以,其主要的失效形式是螺纹的磨损[5]。
2.3.1确定螺杆参数
(1)计算螺杆中径
由给定参数:
夹紧力10吨夹紧时间t=15s 夹紧行程S=20mm
计算得V=20×10-3/15=1.33×10-3m/s
F=10×103×9.8=9.8×104N
螺杆采用碳钢或是合金钢制成,由于本系统是低速重载的一般传动,采用45号钢或50钢均可。
螺杆中径=ξ(2.1)
=×
=
根据圆整要求,取=36mm
查得P=3mm
式中参数:
ξ-梯形螺纹,ξ=0.8
φ-传动精度高和要求寿命长时取φ=4
[P]-滑动螺旋副材料的许用比压,16MPa
(2)确定扭转力矩
tgφ=S/π=/(2.2)
所以Ft =n·P·Fr/π·d2
=3×9.8×104/π×36
=2.5995×103N
计算得 T=Ft ·d2/2(2.3)
=2.5995×103×18
=4.679×104N·mm
(3)耐磨性计算
螺纹的磨损与很多因素有关,重要的有螺纹工作表面的压强、相对滑动速度、粗糙度和润滑状态等,其中最主要的是压强和滑动速度。
相对滑动速度一定时,压强越大磨损越大。
因此,滑动螺旋的耐磨性计算,就是限制螺纹工作面上在某一滑动速度下的压强P,使之小于相应滑动速度下材料的许用压强[P]。
因为(2.4)
=
=
所以=36mm合格
耐磨性条件为:
P=F/A=F/z·π·d2·h(2.5)
=9.8×104×π×3/83×π×36×0.5×3
=12.7416MPa[P]
(4)螺杆的强度校核
螺杆工作时受轴向力F和转矩T的作用,在螺杆危险剖面上同时存在拉应力σ和扭转剪应力τ,按第四强度理论,其危险剖面的强度条件为
ca==[σ](2.6)
所以ca=
=[σ]
=
(5)螺纹牙强度校核
螺纹牙根部剖面的剪切强度条件为
τ=F/z·A=F/π·d,·b·z[τ](2.7)
b=0.65P=0.65×3=1.93mm
所以螺杆的剪切强度τ=17.98N/mm2[τ]=63N/mm2
因为螺纹牙根的弯曲强度条件为σb=M/W=3Fh/zπd,b2[σb](2.8)
计算得到σb=94N/mm2[σb]=105N/mm2
2.3.2确定齿轮传动的参数
(1)轮的转速n1=P·60/V(2.9)
=3×60/1.33=135r/min
初选传动比为1,所以齿轮2的转速n2=135r/min
(2)轮的材料,确定精度等级及许用压力。
两齿轮均选用45号钢,调质处理,由机械设计手册查得HB=217-255,取HB=245。
选取齿轮的精度等级为8级(GB10095-88)查得σHlim=590N/mm2σFlim=230N/mm2计算应力循环次数N:
N=60·n·j·Lh(2.10)
=60×1×(10×300×8)
=1.44×106得ZN1=1.25
YN1=1取ZW=1(HB1<350HB2<350);YX=1(估m≤5)YST=2
SHmin=1 SFmin=1.4
接触疲劳许用压力公式得:
[σH1]12=σHlim/ShminZN1ZW=1.25=737.5N/mm2(2.11)
弯曲疲劳许用应力公式,得:
[σF]12=(σFlim/SFmin)YSTYN1YX=211=328.6N/mm2(2.12)
(3)接触疲劳强度设计:
a≥(u+1)(2.13)
T1=46790N=1.0Φa=0.4
由机械设计手册,查得
查得
初定中心距
at≥(u+1)=(1+1)(2.14)
=68.1
取at=100一般取m=(0.01~0.02)at选取标准模数m=2mm齿数(2.15)
所以,Z2=Z1=50
中心距(2.16)
圆周速度为:
(2.17)
选取齿轮的精度等级为8级可以由机械设计手册,马达驱动,载荷平稳取
按
8级精度,得
按(2.18)
考虑低速级轴的刚度较大
由机械设计手册得
按齿轮等级8级,(未经表面硬化的齿轮)
所以,(2.19)
因为
所以
由机械设计手册得
所以
校核中心距
(2.20)
所以,中心距
合适分度圆直径:
(2.21)
齿轮宽度 (2.22)
取
由疲劳公式得
(2.23)
所以,(2.24)
=
= 故安全
齿轮的几何尺寸:
(2.25)
(2.26)
(2.27)
所以,采用锻造齿轮
齿轮1的尺寸
齿轮2的尺寸
PROE天空论坛提供
3液压系统设计
液压系统作为液压主机设计的重要部分,设计时必须满足主机工作循环所需的全部技术要求,且静动态性能好,效率高,结构简单,工作安全可靠、寿命长,经济性好,使用维护方便。
为此,液压系统要与主机的总体设计(包括机械、电气设计)综合考虑,做到机、电、液的相互配合,保证整个装置的性能最高[2]。
3.1 液压系统的方案设计
3.1.1回路方式的选择
本设计中选用了开式回路,即执行元件的排油回油箱,油液经过沉淀、冷却后再进入液压泵的进口。
3.1.2执行元件的选择
(1)选用了液压马达用于实现连续地回转运动。
(2)活塞液压缸实现直线运动,因为只要求液压缸一个方向工作,反向退回,应选用单伸出活塞缸。
3.1.3调速方式的选择
采用单向节流阀实现速度的调节,这样能保证系统的刚性良好。
在本设计中选用了叠加式单向节流阀。
3.1.4调压方式的选择
(1)在先导型溢流阀的遥控口上远接一个三位四通电磁换向阀。
当电磁换向阀的左位或是右位通电时,系统的压力可由远程调压阀调节控制。
主溢流阀的调定压力大于两个远程调压阀的调定压力。
(2)通往液压缸的油路中,为实现二次压力油的调定选用了减压阀的减压回路。
本设计选用了叠加式减压阀。
3.1.5换向回路的选择
本设计的液压设备要求的自动化程度较高,因此应该选用电动换向,即小流量时应选择电磁换向,所以选用了三位四通的电磁换向阀。
基于叠加式阀的许多特点,在设计中除了选用了普通的电磁换向阀,还选用了叠加式电磁换向阀。
3.1.6动作转换控制方式
在本液压系统的动作控制中,均采用了压力继电器来控制液压缸或是液压马达的动作。
当某一油路的压力达到一定值后,其油路中的压力继电器就会发出讯号,使油路中的执行元件的动作停止。
3.2 液压阀的选取
3.2.1 叠加阀
叠加阀是指可直接利用阀体本身的叠加而无需另外的油道连接元件而组成液压系统的特定结构的液压阀的总称。
叠加阀安装在板式换向阀和底板之间,每个叠加阀除了具有某种控制阀的功能外,还起着油道作用。
叠加阀的工作原理与一般阀的工作原理基本相同,但在结构和连接方式上有其特点故而自成体系。
按控制功能叠加阀可分为压力流量、流量、方向三类,其中方向控制阀中只有叠加式单液控单向阀。
同一通径的各种叠加阀的油口和螺钉孔的大小位置、数量都与相匹配的板式主换向阀相同,因此,针对一个板式换向阀,可以按一定次序和数目叠加而组成各种典型的液压系统,通常控制一个执行元件的系统的叠加阀叠加成一叠。
(1)叠加阀的特点
由叠加阀组成的液压系统,结构紧凑,体积小,重量轻,占地面积小;叠加阀安装简便,装配周期短,系统有变动需增减元件时,重新安装较为方便,使用叠加阀,元件间无管件连接,消除了因管接头等引起的漏油、震动和噪声;使用叠加阀系统配置简单,元件规格统一,外形整齐美观,维修保养容易;采用我国叠加阀组成的集中供油系统,节电效果显著。
但由于规定尺寸的限制,由叠加阀组成的回路形式较少,通经较小,一般适用于工作压力小于120MPa,流量小于200L/min的机床、轻工机械、工程机械、煤炭机械、船舶、冶金设备等行