小型铸造企业用熔化率为.docx
《小型铸造企业用熔化率为.docx》由会员分享,可在线阅读,更多相关《小型铸造企业用熔化率为.docx(25页珍藏版)》请在冰豆网上搜索。
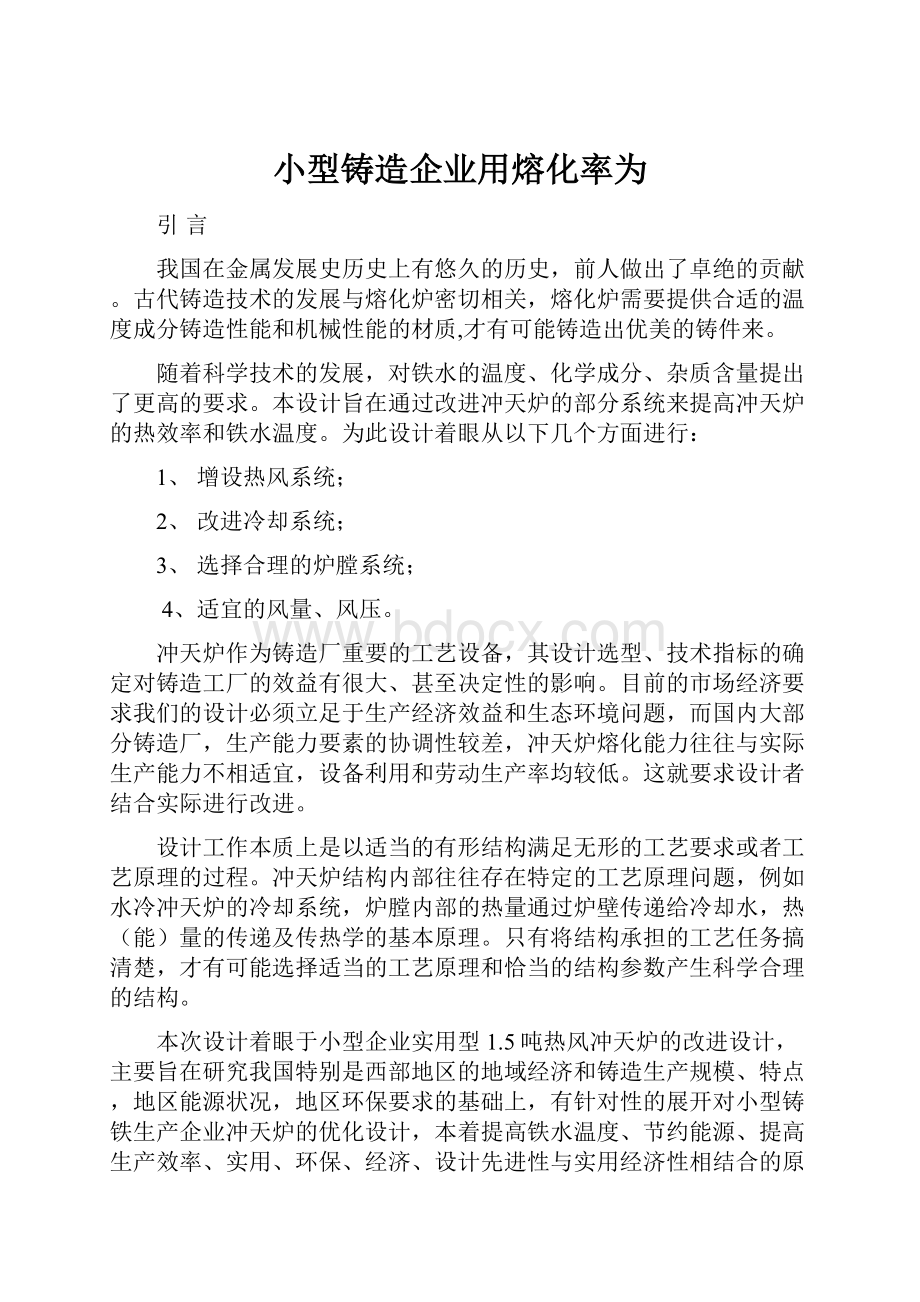
小型铸造企业用熔化率为
引言
我国在金属发展史历史上有悠久的历史,前人做出了卓绝的贡献。
古代铸造技术的发展与熔化炉密切相关,熔化炉需要提供合适的温度成分铸造性能和机械性能的材质,才有可能铸造出优美的铸件来。
随着科学技术的发展,对铁水的温度、化学成分、杂质含量提出了更高的要求。
本设计旨在通过改进冲天炉的部分系统来提高冲天炉的热效率和铁水温度。
为此设计着眼从以下几个方面进行:
1、增设热风系统;
2、改进冷却系统;
3、选择合理的炉膛系统;
4、适宜的风量、风压。
冲天炉作为铸造厂重要的工艺设备,其设计选型、技术指标的确定对铸造工厂的效益有很大、甚至决定性的影响。
目前的市场经济要求我们的设计必须立足于生产经济效益和生态环境问题,而国内大部分铸造厂,生产能力要素的协调性较差,冲天炉熔化能力往往与实际生产能力不相适宜,设备利用和劳动生产率均较低。
这就要求设计者结合实际进行改进。
设计工作本质上是以适当的有形结构满足无形的工艺要求或者工艺原理的过程。
冲天炉结构内部往往存在特定的工艺原理问题,例如水冷冲天炉的冷却系统,炉膛内部的热量通过炉壁传递给冷却水,热(能)量的传递及传热学的基本原理。
只有将结构承担的工艺任务搞清楚,才有可能选择适当的工艺原理和恰当的结构参数产生科学合理的结构。
本次设计着眼于小型企业实用型1.5吨热风冲天炉的改进设计,主要旨在研究我国特别是西部地区的地域经济和铸造生产规模、特点,地区能源状况,地区环保要求的基础上,有针对性的展开对小型铸铁生产企业冲天炉的优化设计,本着提高铁水温度、节约能源、提高生产效率、实用、环保、经济、设计先进性与实用经济性相结合的原则,面向小型、批量鋳件生产企业,在原有炉型的基础上改进炉体结构、技术参数,适当提高技术含量,以最优化的设计配置来满足社会的需要。
第一章炉体结构设计及参数确定
本章主要介绍冲天炉炉体结构的设计及其参数的确定,其它部分的设计将在后面的章节中进行叙述。
1.1概述
常用冲天炉主要由以下四部分:
①炉身部分;②炉底部分;③前炉;④烟囱组成。
但为了适应不同的原材料(炉料及燃料)、不同生产方式、不同生产规模和熔炼各种铸铁的需要,冲天炉又可分为很多种类。
这一部分主要是对冲天炉炉体的结构进行设计,并对主要参数进行确定。
由于工艺参数、结构参数和熔炼指标之间的关系非常复杂,所以在设计冲天炉时,一般都是以某些工艺参数为依据来计算和选择结构尺寸的范围,同时参考现有生产效果较好的冲天炉来确定具体结构和尺寸[5]。
1.2结构设计及参数确定
1.2.1炉身
1.炉壳结构
炉身外壳是一个锅炉钢板制成的圆筒,内彻耐火砖,外壳和耐火砖之间留有间隙,中间填入石棉制品作为绝热材料。
炉身外壳分段制造,然后焊成一体。
为使耐火砖牢固,在炉壳内壁焊上支承法兰,安放承重环,承环避免放在风口附近,用锅炉钢板制成,宽度小于砌砖层厚度[2,8]。
主要参数:
①炉身外壳材料:
锅炉钢板厚度6m
②外壳与耐火砖间隙:
20mm
③炉身外壳每段长度不超过3500mm
④承重环:
材料:
锅炉钢板厚度:
10mm宽度:
120mm
第一承重环位置:
上排风口以上700mm
2.炉身下段结构
炉身下段即炉缸区,从砂床顶面至第一排风口中心线,起汇集铁水和炉渣的作用,并使铁水和炉渣通过过桥导入前炉,炉底砂床厚度设计要适宜,过低,易漏铁水且炉底温度低不利于铁液排出;过厚,打炉困难,且要有一定斜度。
主要参数:
炉底砂床厚度:
300mm斜度:
1:
20
3.炉身上段结构
炉身上段即一排风口中心线至加料口下缘的距离。
加料口下缘砌有空心铁砖,以承受加料时的撞击,顶层铁砖带有斜面,便于加料,有效高度影响炉料预热效果,热效率和铁水温度与炉膛内径有关,要根据实际生产能力和熔化率设计最佳的高度,过高易产生搁料,压碎焦炭增加供风阻力,但也不能过低。
主要参数:
顶层铁砖至加料口下缘距离:
180mm铁砖层数:
7
每层块数:
8铁砖材料:
铸铁
4.炉膛
目前炉膛种类包括:
直线炉膛、折线炉膛、曲线炉膛,在对比几种炉膛优缺点之后,我选择设计卡腰形曲线炉膛。
炉膛呈卡腰形,减少了炉壁效应的影响,改变炉膛内焦碳燃烧状况及炉气流向和流速,使气流分布更加均匀、合理、以提高冲天炉的热效率[2]。
①工作原理
由于二排风口处炉径明显变小,二排风口进风的冷却作用使卡腰在长时间的熔炼过程中保持下来,这使炉气对炉壁的冲刷作用较小,炉气分布比较均匀。
其原因在于卡腰炉型及二排主风口突入炉中央,不仅改善了底焦燃烧,而且使空气深入炉子中心,削弱了炉壁效应,促使炉气沿炉膛截面均匀分布。
另外一排风口进风气流向上流动过程中,由于炉壁效应而偏向炉壁,至卡腰处二排风口进风又把气流重新推向炉中心部位,并抑制二氧化碳还原反应的发生,从而保证底焦内炉气分布均匀,强化底焦燃烧。
②结构设计
卡腰是指把第二排风口处炉径缩小为平均直径的四分之三或将此处炉膛面积缩小为平均炉膛面积的45%~55%。
两排风口集中分布在卡腰处,送风强度大,大斜度风口可使风进入炉膛中心,在炉内形成底焦燃烧的集中高温区,而且由于卡腰冲天炉是两排小间距,熔化带炉气呈弱氧化性,抑制了熔化带铁、硅、锰等元素的烧损。
所以两排小间距卡腰冲天炉熔炼时硅锰元素烧损低,铁氧化少,能熔炼出高温优质铁水[17]。
如图ZSC-01-01。
③主要参数
平均直径:
D=1/2×(D3+1/2×(D1+D2))
=1/2×(580+1/2×(320+480))=490mm
式中:
D1为第一排风口处直径;
D2为第二排风口处直径;
D3为熔化带最大直径。
炉壳外径:
Dw=Dn+2S=810+2×6=822mm
式中:
S为炉壳钢板厚度
炉壳内径:
Dn=D+2(S1+S2)=490+2×(140+20)=810mm
式中:
S1为炉衬厚度;S2为绝热层厚度。
炉缸深度:
h=360mm
有效高度:
H=h+qt/rlF=3820mm
式中:
T:
为炉料在炉内停留时间(h);
rl:
炉料密度(t/m3);
F:
炉膛横截面积(m2)。
1.2.2风箱
风口设置在风箱内,一排风箱,双排风口。
结构较简单,制造维修方便。
主要参数:
风箱外径:
D1=(1.8~2.5)Dj=1840mm
风箱宽度:
a=320mm
风箱高度:
b=(0.35~0.5)D1=1140mm
材料:
锅炉钢板厚度:
5mm
1.2.3窥视孔与风口
1.风口结构
炉身上设置圆形风口,长度要比炉衬厚度短一些。
主要参数:
选用双排风口,每排4个。
风口总面积:
=F×i=0.19×4%=7540mm2
式中:
F为炉膛面积(㎡);
i为风口比。
每个风口面积:
f=
/8=7540/8=942mm2
风口直径:
d=
=35mm
排距:
hf=(0.8~1.1)df=300mm
风口斜度:
45º材料:
锅炉钢板厚度:
5mm
风口长度:
第一排:
240mm第二排:
360mm
2.窥视孔结构
窥视孔设置在风箱上风口所对的位置,通过它可用铁棒捅风口避免有燃烧不完全的焦碳存在,保持畅通,窥视孔装置密封性要好,结构简单,操作方便。
1.2.4炉气换热器
1.热风的作用[20]
①增加了氧和碳的反应速度,缩短了燃烧带的长度,使得燃烧带更为集中,最高温度区接近风口,提高了铁水温度并提高了熔化效率。
②提高送风温度,使得空气中的自由氧更为活跃,因而增加了氧和底焦中碳的反应速度。
③采用热风,使焦炭的消耗量相应地减少,因此,铁水的增碳、增硫都相应减少。
④增加了热收入,因热风使冲天炉内导入了补充热量,提高了炉气温度,这样就使铁水通过底焦的过热度提高。
⑤热风减少了硅、锰的烧损,同时也有利于脱硫。
2.换热器的选择
炉顶换热技术主要是利用炉气中的化学热来提高冲天炉的热效率的。
冲天炉炉气的物理热约占焦碳发热量发5%~8%,炉气中CO的化学热占26%~41%,利用此化学热的冲天炉就比冷风冲天炉热效率可提高约15%,换热效率可达40%~60%。
同时,炉顶热风换热器还具有热惯性小、占地面积小、管道路径短结构紧凑,有利于提高热效率、投资少等方面的优越性。
因此,我选择此种换热器。
3.炉气换热器的结构
安装在冲天炉加料口上方的炉气换热器,用于进行炉顶热风换热,它是通过炉气中CO的再燃烧即化学热来预热冲天炉的助燃空气,从而提高冲天炉的燃烧温度。
目前常用的有四种基本形式:
①蛇形换热器;②密筋烟囱换热器;③多管换热器;④多层多管换热器
本设计采用的是密筋烟囱换热器和多层多管换热器的组合。
密筋烟囱换热器的结构和冲天炉密筋炉胆基本相同,用于预热。
而多层多管换热器则是管式结构,其管内为冲天炉鼓风,管外为炉气,基本结构见附图。
在冲天炉炉顶热风换热器的设计中,必须注意各部分在工作中的热膨胀问题.焊接结构、焊接工艺问题,同时应设置必要的热风控制仪器仪表,以增加热风系统的可靠性[16]。
如图ZSC-01-02。
主要参数:
密筋换热器:
内外筒间隙:
a=20mm炉胆高度:
H=780mm
筋片厚度:
S=4mm
多层多管换热器:
高:
1200mm风管间的距离:
1440mm
风管直径:
40mm总高度:
1880mm
1.2.5烟囱
烟囱在加料口上面,其外壳与炉身联成一体内壁砌耐火砖,烟囱内径应不小于炉膛内径,加料口以上部分适当缩小,以利于引导炉气向上流动并排出炉外。
主要参数:
内径:
dr=600mm外径:
(0.8~1)Dw=900mm
砌砖厚度:
150mm高度:
5000mm
加料口尺寸:
1560×800
1.2.6炉底部分
1.炉底板和基座
炉底板和基座是冲天炉的支撑部分,炉底板承受炉身移出部分全部重量,须有加强筋。
炉壳用螺栓紧固在炉底板上,炉底板中间的孔是熔炼终了后,排出和清理炉内残余炉料的出口。
基座用来紧固轨道上的支柱,并将载荷分配在基础上[2]。
主要参数:
炉底板:
材料:
铸铁厚度:
40mm筋高:
25mm孔径:
400mm
基座:
材料;铸铁埋入地下深度:
350mm尺寸:
450×450mm
3.基础及地脚螺钉
基础大小与承重及地基的承载能力有关,基础面积可根据地基承载能力和所需承载重量计算。
主要参数:
材料:
钢筋混凝土尺寸:
1600×3500mm厚度:
450mm
地脚螺钉:
M18个数:
24个
4.炉底门
炉底门用有加强筋的锅炉钢板制成,分为前后两半,用铰链与炉底板连结,能抵抗弯曲,在其上钻有若干通气眼,烘炉时炉底砂床中的水气易逸出,两半炉底门相互搭接,保证关闭后严密,采用拉钩式锁紧机构,并用摇臂固定[2]。
主要参数:
材料:
锅炉钢板厚度:
15mm筋高:
15mm
通气眼孔径:
12mm
1.2.7活动炉身
活动炉身即炉缸部分,对于小型冲天炉,为修炉方便,炉身应做成可移动式的,修炉时可把熔化区以下炉身移出,分段修搪,而活动部位移出位置及移动方式要根据实际情况进行合理设计。
活动炉身车轮在轨道上行走向后移出,前炉和炉身上部由加料平台固定。
活动部分与固定部分之间设有升降机构,用千斤顶抬升,楔入楔铁用以固定,便于装卸和保证接缝严密[3]。
①车轮
采用单轮缘,易于导向和防止脱落又不增加滚动阻力,安装在轨道外侧,为弥补轨道和车轮间安装误差,车轮工作表面宽度比轨顶稍宽,车轮的踏面做成圆柱形,装在固定的心轴上,用定轴件固定在机架上,车轮在轴上自由转动,轮毂与轴之间装入滚动轴承。
主要参数:
材料:
铸铁直径:
180mm个数:
4
②轨道和支柱
轨道用来承受车轮传来的集中压力,并引导车轮运行,轨道采用工字钢,钢轨架在用槽钢制成支柱上。
主要参数:
轨道:
材料:
工字钢长度:
2800m间距离:
600mm
支柱:
材料:
槽钢高:
80mm个数:
6
1.2.8过桥
过桥是前后炉的连接通道,容易损坏而造成漏铁水的事故,或使铁水冷却造成冻结。
因此,过桥长度应考虑装前炉盖活动方便和前后炉砌砖厚度的情况下适当选择。
过桥体是锅炉钢板制成的矩形箱体,内砌耐火砖,与壁之间有绝热层。
过桥孔为矩形,高大于宽,断面向前炉方向逐渐扩大,过桥口过小易冻结,堵塞,过大底焦易吹出,过桥口底部斜度与炉底砂床一致,过桥体尺寸主要取决于生产率及熔化延续时间。
主要参数:
过桥体宽:
380mm过桥体高:
360mm
过桥口高:
70mm过桥口宽:
40mm
绝热层厚:
30mm材料:
锅炉钢板
1.2.9固定式前炉的结构
1.前炉炉筒和炉盖
前炉炉筒的炉壳由锅炉钢板制成,上下两端都有法兰连接,炉壳上有出铁槽,出渣槽、工作门、过桥口及正对过桥处的观察孔,下部靠法兰用螺钉与地基固定,上部有前炉盖,并有专门的卡子使之紧固,炉壳内砌耐火砖。
炉壳与耐火砖之间有绝热材料层。
弓形的前炉盖是铸铁铸成,炉盖内部有小钩,使散料内衬附着牢固,顶部有两个吊环,对称分布,二者有紧固结构固定,采用楔销式[4]。
主要参数:
炉筒:
材料:
铸铁厚度:
10mm
炉盖:
材料:
锅炉钢板厚度:
6mm
前炉容量根据铸件情况确定取0.75t
炉底厚度:
h1=340mm斜度:
1:
20
前炉直径:
dq=(0.8~1.2)dj=400mm
前炉炉壳直径:
Dq=dq+2(δ1+δ2+δ3)=400+2(130+30+6)=732mm
式中:
δ1为前炉炉衬厚度;
δ2为炉壳与炉衬间绝热层厚度;
δ3为炉壳钢板厚度。
前炉有效高度:
Hy=h2+h3=560mm前炉高度:
Hq=1020mm
2.出铁槽与出渣槽
出铁槽与出渣槽用锅炉钢板焊成,内砌耐火材料,都有一定斜度,出铁槽不宜过长,宽度及高度应保证铁水流出不飞溅出去。
出铁槽末端的宽度和高度可适当减小。
出铁槽出渣槽的耐火材料层表面离出铁口出渣口下缘有一定距离,以便能用堵口机构。
主要参数:
材料:
锅炉钢板耐火材料厚:
60mm
出铁槽宽275mm高:
280mm斜度:
1:
20
出渣槽:
长:
400mm斜度:
40º
耐火材料层表面距离出铁口、出渣口下缘:
40mm
3.过桥观察孔
观察孔设在前炉上正对过桥处,通过它观察和清理过桥,确保过桥畅通。
4.工作门
前炉下部开有工作门,打炉时清除前炉炉渣,烘炉时点火用。
工作门关闭后,在前炉内把门缝堵严,保证不漏铁水,工作门上开有小工作门,供打炉时清理前炉炉渣。
主要参数:
材料:
锅炉钢板尺寸:
400×400mm
5.出铁口及出渣口
位于前炉底最低处的是出铁口,出铁口直径根据铁水柱压头为转移的铁水流速度计算,铁水柱的压头数值取决于铁水柱、炉渣柱的高度及炉内压力。
出铁口直线部分不宜过长,否则铁水易冻结,打开出铁口困难,其余部分要有斜度,出渣口用于排除刚中的渣滓。
第二章冲天炉配套设备
2.1除尘设备
冲天炉作为小型铸造企业重要的熔炼设备,在熔炼过程中,由于焦炭燃烧,金属炉料的预热、熔化及过热,炉气的运动,炉料的加入及下降,耐火材料的损坏等过程的进行,因化学作用、热作用及机械作用使冲天炉排放的烟气中含有大量的气体及固体有害物质,这些物质不仅对人类有害,而且对自然环境造成危害,所以必须高度重视,对排出的烟气进行除尘处理,使之达到国家规定的排放标准[12]。
冲天炉烟气除尘净化装置的主要设备是除尘器,按其工作原理可分为两大类:
一为干法除尘器,一为湿法除尘器,这次设计中我选择了干法除尘器。
2.1.1冲天炉烟气的组成
冲天炉烟气中,主要是二氧化碳、氮、氟化氢、二氧化硫、一氧化碳、氧、水蒸汽等组成,气体有害物质在烟气中所占比例不多,但危害不容忽视,必须予以处理,还存在固体有害物质如:
冶金粉尘、碳素烟尘、灰尘。
2.1.2干法除尘器
该法结构简单,维修方便。
这类除尘器是利用烟尘重力、惯性力、离心力或借助外电场产生静电引力或经过滤物的作用,将烟尘捕集达到除尘净化烟尘的目的[2]。
主要有以下几种:
1.火花捕集器;2.集尘室式除尘器;3.旋风除尘器;4.旋风颗粒层除尘器;5.布袋除尘器;6.静电除尘器。
2.2单轨加料机
根据不同炉子容量、车间布置和机械化要求,冲天炉加料设备大致可分为翻斗加料机、单轨加料机和爬式加料机三种形式。
本次设计选用固定式单轨加料机。
单轨加料机用卷扬机构、料桶、小车、单轨主梁和限位装置组成,固定式单轨加料机单轨主梁是直接装在建筑物或专用构架上的一根工字钢,该加料机结构简单、料省价低,卷扬机构装在梁上,节省平台上占用面积[3]。
主要参数选择:
(1)料桶起升机构
起重量:
1000kg起升速度:
16m/min
最大起升高度:
12m电动机型号:
JPE3-31-4
功率:
30kw转速:
1380r/min
减速器速比:
i=60.5卷筒直径:
220mm
钢丝绳:
GB359D-6×37+1-8.7-160-I-b
(2)小车运行机构
运行速度:
20m/min最大行程:
4.6m
电动机型号:
AE-7114P功率:
0.4kw
转速:
1420r/min减速器速比:
i=28.2
车轮工作直径:
130mm运行轨道:
GB706I#28a
(3)料桶
料桶容积:
0.15m3内部尺寸:
D×H=φ520×700
最大装载量:
300kg桶壁钢板厚:
B=6mm
底盖张开尺寸:
C=400mm张开时压杆行程:
E=180mm
料桶外径:
A=658mm
料桶装置总高:
L=1022mmF=180mmG=250mm
J=590mmK=620mmM=564mm
2.3送风设备
冲天炉的供风设备包括鼓风机,送风管道调节控制装置等。
2.3.1鼓风机的选择
本次设计采用冲天炉专用离心式鼓风机,它是根据我国冲天炉的特点和要求而设计的配套风机,它具有风压高,风量适中,结构简单耗电少及噪声低等特点。
目前广泛应用于中小型密筋炉胆热风冲天炉上,效果良好[3]。
参数确定
(1)型号:
HTD35-11
(2)风量:
35m3/min(12kpa)
(3)风压:
1300mmH2O
(4)轴功率:
10.4kw
(5)主轴转速:
5600r/min
(6)配套电机:
型号JO252-2功率:
13kw
(7)重量:
0.7t
(8)数量:
2台
2.3.2送风管道
送风管道是指从风机出口到冲天炉炉体之间的管道,控制调节装置和安全装置等的设计。
1.管道的设计
冲天炉风管为圆形断面,用3mm钢板制成,直径D=250mm
设计要求:
①风管中应留有3750mm的平直段,为了安装测量装置并保证其精度。
②风速控制在12~15m/s范围内,尽量减少转弯,断面变化和分支,鼓风机出口处风管应有750~1250mm直管段,以减少出风阻力,结构简单、牢固,尽量减少漏风损失,安装维修方便,要设有控制风量的装置。
2.控制调节装置
离心式鼓风机在进风管上设置一阀门,通过改变阀门开闭程度,使风机进风阻力变化,从而使风机输出的P-Q曲线改变,达到调节风量的目的,此法称为进口调节。
设计要求结构简单、操作灵便、调节性能好,漏风损失少。
2.4炉渣分离及处理设备
在冲天炉熔炼过程中必然产生一部分炉渣,它在炉内熔炼过程中是有用的物质。
然而当它到达炉底之后,我们要求将它与铁水分离开来,完成冲天炉熔炼的最后阶段,即炉渣分离。
炉渣分离后,必须将高温的炉渣进行出理,以简化操作,改善劳动条件,并综合利用炉渣。
这就是炉渣分离处理装置的作用和目的。
2.4.1炉渣分离装置
冲天炉的炉渣与熔炼工艺,炉子结构以及炉料情况有关,其渣量多少一般是以占铁水数量百分数表示,通常为:
一般酸性冲天炉5~10%
大型水冷冲天炉1~3%
碱性冲天炉15~30%
渣铁分离装置可以分为间断出渣和连续出渣装置两大类。
间断出渣时,炉渣是在前炉或炉缸内分离,通过渣口间断排出[1]。
本次设计的1.5t/h小型冲天炉就是使用这种出渣方式。
2.4.2炉渣粒化装置
炉渣粒化装置的目的是将从出渣口流出的炉渣立即用水将其冷却,在激冷和冲击的作用下,炉渣被碎为0.5cm的颗粒,随水流至沉淀池。
这样既改善了劳动条件又降低了劳动强度,确保安全生产,而且还为进一步综合利用炉渣创造了条件。
因此炉渣粒化装置是现代冲天炉不可缺少的一个组成部分。
1.炉渣量的计算
(1)每昼夜的炉渣量计算:
W=QPtN(t/天)
式中:
Q—冲天炉熔化率(t/h);
P—冲天炉炉渣量占铁水重量的百分率;
t—每昼夜冲天炉的实际熔炼时间(h);
N—同时开炉的冲天炉数(台)。
(2)炉渣量排出率的计算:
W=K×(PQN/γ渣)×(1000/3600)(L/s)
式中:
W—炉渣量排出量(L/s);
K—排渣量不平衡的修正系数;
γ渣—-炉渣的重度(kgf/L)。
2.简易炉渣粒化装置
(1)渣池
本设计在渣口前设置一水池,让炉渣直接流到水池中,利用池中的水将炉渣冷却,停炉后用人工清理水池中的炉渣。
(2)水泵
采用3BA型水泵。
2.5冲天炉水冷装置
2.5.1分类
冲天炉的水冷装置按其工作原理可分:
(1)内冷式;
(2)外冷式。
本次设计采用的雨淋式水冷系统属于外冷式。
2.5.2雨淋式水冷系统
该系采用壁厚为6mm的钢管作为管道,制成环行固定于冲天炉熔化区以上的炉壳外,管道上安装有喷嘴。
经冷却后的水流经管道,从喷嘴喷出,水流沿炉身外壳流下,将热量带走,从而达到冷却的目的。
由于水冷时的给热系数很大,炉衬表面的温度下降很多,使得内壁形成一个渣壳以保护炉壳[9]。
如图ZSC-01-03。
使用该系统的优点是:
(1)结构简单;
(2)安装方便;(3)节省能源;(4)使用简易;(5)清理容易。
主要参数:
水管直径:
100mm壁厚:
6mm材料:
钢管
冷却高度:
1290mm喷嘴个数:
20间距:
130mm喷嘴直径:
30mm
第三章冲天炉的耐火材料
3.1耐火材料
就耐火材料系统而言,所有冲天炉可分为加料区、熔化带、炉缸、出铁口、分渣器、炉外流槽。
而不同部位要求不同性能的耐火材料。
因此,要通过对冲天炉的熔炼状况的分析,炉渣化学成分的控制,来选择适当炉衬材料,以使水冷冲天炉达到长龄、连续熔炼的目的,从而提高熔化效率和铁液温度,尽而提高生产效率[19]。
3.1.1对耐火材料的要求
1.耐火度2.高温结构强度3.耐急冷急热性
4.化学稳定性5.高温体积稳定性6.耐压强度
7.一定的体积密度和气孔率8.性质和尺寸要准确
3.1.2耐火材料的分类
1.酸性耐火材料2.碱性耐火材料3.中性耐火材料
3.1.3耐火材料的使用
在本次设计中耐火材料的具体使用为:
在风口区及以下位置使用粘土砖;在熔化带区域使用红硅石;在加料口以下部位使用铁砖[18]。
3.2隔热材料
在过热区使用轻质硅砖,其他地方使用轻质粘土砖。
第四章冲天炉说明与操作
4.1工艺参数的选择
4.1.1底焦高度的确定
1.底焦高度
底焦高度指第一排风口中心线到底焦顶面之间的高度。
这是影响铁液温度和化学成分的一个十分重要的操作参数。
理论上,冲天炉底焦的正常高度应处于炉内燃烧区还原带上平面,运行时底焦高度波动范围为一批层焦高度(约200mm)。
另外,在开炉初期加入的炉料及后炉过桥前炉皆未得到良好预热,为了补充这部分“额外”损耗,确保初期铁水良好过热,尽量缩短底焦高度,料柱及炉体吸热达到平衡状态的时间[1]。
2.选择与确定
底焦高度与供风强度、风口排距、焦碳块度、层焦焦耗有关,装料时底焦高度由于考虑到焖炉时的消耗和装料后压实的作用,所以要比实际运行时底焦上顶面高250mm左右。
具体的数据要根据不同结构的炉子,查阅手册确定[2]。
H=Dmax+500-700mm
式中:
H----底焦高度;
DmaX----最大炉膛直径。
4.1.2风量与风压
冲天炉风量常用标准压力管或流量孔板,并配备比较精确的压差计,在总风