二维薄膜讲课手册.docx
《二维薄膜讲课手册.docx》由会员分享,可在线阅读,更多相关《二维薄膜讲课手册.docx(13页珍藏版)》请在冰豆网上搜索。
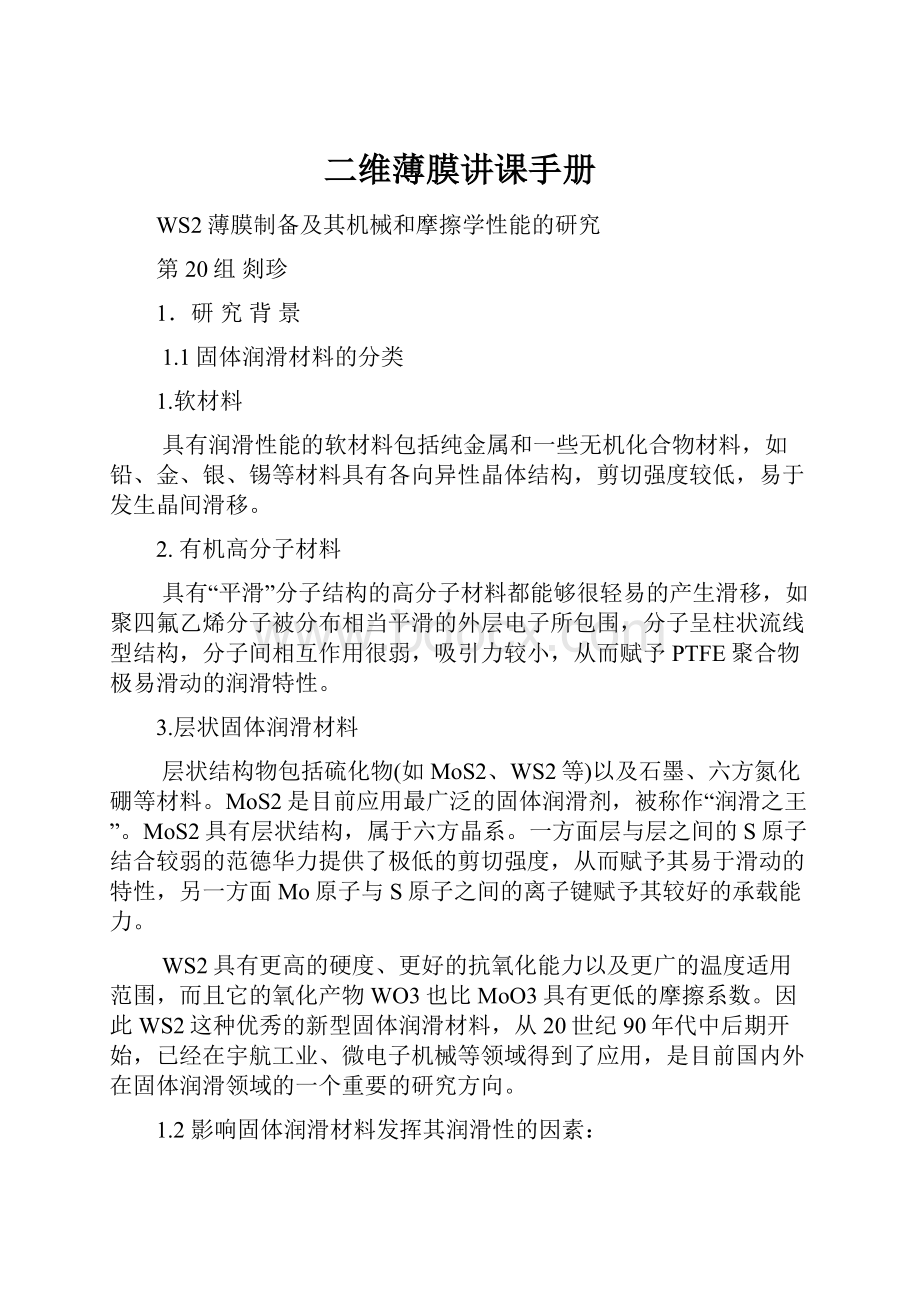
二维薄膜讲课手册
WS2薄膜制备及其机械和摩擦学性能的研究
第20组剡珍
1.研究背景
1.1固体润滑材料的分类
1.软材料
具有润滑性能的软材料包括纯金属和一些无机化合物材料,如铅、金、银、锡等材料具有各向异性晶体结构,剪切强度较低,易于发生晶间滑移。
2.有机高分子材料
具有“平滑”分子结构的高分子材料都能够很轻易的产生滑移,如聚四氟乙烯分子被分布相当平滑的外层电子所包围,分子呈柱状流线型结构,分子间相互作用很弱,吸引力较小,从而赋予PTFE聚合物极易滑动的润滑特性。
3.层状固体润滑材料
层状结构物包括硫化物(如MoS2、WS2等)以及石墨、六方氮化硼等材料。
MoS2是目前应用最广泛的固体润滑剂,被称作“润滑之王”。
MoS2具有层状结构,属于六方晶系。
一方面层与层之间的S原子结合较弱的范德华力提供了极低的剪切强度,从而赋予其易于滑动的特性,另一方面Mo原子与S原子之间的离子键赋予其较好的承载能力。
WS2具有更高的硬度、更好的抗氧化能力以及更广的温度适用范围,而且它的氧化产物WO3也比MoO3具有更低的摩擦系数。
因此WS2这种优秀的新型固体润滑材料,从20世纪90年代中后期开始,已经在宇航工业、微电子机械等领域得到了应用,是目前国内外在固体润滑领域的一个重要的研究方向。
1.2影响固体润滑材料发挥其润滑性的因素:
与基体材料、摩擦对偶件等材料本身的物理性能和表面状态有关;
与服役环境有关,如工作气氛、使用温度、施加载荷以及转动速度等,固体润滑材料在不同工作气氛中使用,其润滑性能差异很大。
1.3WS2在一些行业的应用举例
WS2为深灰色带有金属光泽的细结晶粉末,美国率先将其应用到航天飞机、战斗机、军用机械的链条传动等军事领域,以及超高真空系统中的转动、滑动等部件上。
在发动机运转过程中,活塞工作时温度很高,顶部达600-700K,在气缸内以很高的速度(8~12m/s)往复运动,活塞在这种恶劣的条件下工作,会加速磨损,一般使用高强度铝合金,经过镀WS2膜后,则可降低磨损,延长寿命,说明WS2本身可在高温下保持润滑功能。
美国军用直升机的变速箱中各齿轮均采用WS2技术处理,膜层厚度0.5um;薄膜含极细微孔,与润滑油有亲和力;耐高温,化学惰性,低摩擦系数,使变速箱中产生的热减少,齿轮变换时力减少,操作快速平滑;延缓了齿轮表面微坑的出现。
1.4WS2晶体结构
WS2具有六方晶系层状结构,其中每一层是由两层六边形硫原子夹一层金属钨原子组成,硫原子与钨原子组成三角锥形。
每一层中硫原子与钨原子是由强共价键连接,而层与层之间是由相对较弱的范德瓦尔斯力相结合。
WS2极易从层与层之间辟开,所以具有良好的固体润滑性能,稳态的WS2即通常所说的2H-WS2,其中“H”代表六方晶系,“2”是指每个WS2分子包含两个S-W-S单元层结构。
WS2的两种典型取向分布I型织构和II型织构。
对于WS2薄膜来说,其润滑性能的好坏主要决定于II型织构的强度。
其II型织构的强度越大,理论上WS2固体润滑薄膜的润滑效果越好。
因此如何提高WS2固体润滑薄膜II型织构的强度是目前固体润滑领域的研究热点之一.
1.5润滑剂润滑机理
固体润滑是将具有低剪切强度的固体润滑剂用擦涂或溅射镀膜的方法附着在基底材料表面。
在摩擦的过程中,固体润滑材料可以在对偶件表面形成摩擦转移膜,使摩擦作用发生在易剪切形变的固体润滑剂中,从而起到润滑的作用,减少摩擦系数,降低磨损程度。
1.6实验室常见制备方法
1.硫化法
原理:
首先要在基片上沉积一层纯钨或者氧化钨薄膜,然后利用硫粉或硫化氢气裂解产生的硫离子将其硫化从而形成WS2薄膜。
在硫化过程中硫化时间、硫化温度等都是影响薄膜结构与性能的主要因素。
2.射频溅射法
原理:
利用射频激励放电,离化氩气产生Ar+轰击WS2靶材,溅射粒子在基片上沉积形成WS2薄膜。
所得薄膜一般为非晶态结构。
通过对工作气压、沉积温度、溅射功率等工艺参数的调节,可以得到结构致密、性能优异的WS2薄膜,是实验室中经常采用的一种方法
3.孪生靶中频磁控溅射法
原理:
将直流电源改为交流中频电源就衍生出了中频磁控溅射技术,当采用同时溅射两个并排放置的外形与尺寸完全相同靶材的形式,这样溅射效率高,溅射过程稳定。
2.WS2薄膜制备
2.1制备器材
多功能离子镀膜机镀制纯WS2薄膜;基体材料是单晶硅片和TC4钦合金;过渡层选用高纯Ti靶。
2.2具体制备工艺
1.基体材料装入真空镀膜机,抽真空;
(其中单晶硅片用于膜层的微观形貌及物相成分分析,TC4合金则用来测试薄膜的力学性能及摩擦磨损性能。
)
2.通入Ar气,打开离子源,轰击清洗基体材料;
3.直流磁控溅射Ti过渡层,10min
4.停止工件架的转动,使样品静置于WS2靶面正前方,36min
2.3对WS2薄膜制备工艺优化
主要研究了工作气压、沉积温度等工艺对薄膜形貌,物相结构,力学性能及摩擦磨损性能的影响。
工作气压,0.5Pa、0.8Pa、1.0Pa、1.5Pa,(50℃)
沉积温度,50℃、100℃、150℃、200℃
图1给出了单晶硅片在沉积温度100℃、工作气压1.0Pa时制备薄膜的表面SEM照片。
由于硅基底表面过于平整,且薄膜本身的导电性较差,从薄膜表面的SEM照片看不出明显的特征形貌。
仔细观察薄膜的表面,可以隐约看到一些白色的球形颗粒,由于溅射靶材是由粉末冶金方法而成,在薄膜的沉积过程中,溅射靶材上的MS2颗粒容易产生脱落现象,从而在薄膜表面形成一些粗大的溅射颗粒。
图2给出了纯WS2薄膜的能谱图(EDS分析)薄膜中O元素的存在,薄膜样品出炉后在空气中发生了氧化,也可能是由镀膜过程中真空系统中残留的氧成分所致。
三.薄膜的微观结构及形貌分析
1.优化工作气压
图3是在相同沉积温度(100℃)、不同工作气压下沉积WS2薄膜的截面形貌。
工作气压为0.5Pa时所制备的薄膜质地较为细腻、致密,但膜层很薄,沉积效率较低。
随着工作气压的升高,薄膜的致密性有所降低,膜层结构变得疏松,1.0Pa时最为明显,此时膜厚达到了最大值,薄膜开始出现柱状晶的生长趋势。
随后工作气压达到1.5Pa时,薄膜的柱状晶形貌更为明显,但是薄膜的生长速度却又降了下来。
说明工作气压是影响薄膜形貌的一个重要因素。
提高工作气压可以增加溅射时产生的二次电子数量,使辉光作用增强,从而使被溅射出来的粒子数量增加,提高溅射效率。
但是,工作气压太大,则会使粒子在到达基体表面前与气体分子的碰撞机会增多,从而降低到达基体表面时粒子的平均动能及数量。
所以初步选定0.8Pa为合适的工作气压,通过调节沉积温度来进一步优化工艺参数。
2.优化工作温度
如图5所示,沉积温度对WS2薄膜的截面形貌没有太大的影响。
只是随着温度的升高,200℃沉积的薄膜中出现了一定程度的纤维状结构,使得膜层的致密性有所降低。
提高沉积温度会增大膜层沉积速率的同时,还会增加真空腔体内气体离子的动能,提高靶材溅射粒子与气体粒子之间的碰撞几率,这在一定程度上会降低薄膜的致密性。
3.WS2薄膜的物相结构分析
图6是WS2薄膜的XRD图谱。
对沉积温度分别为50℃、150℃和200℃条件下制备的WS2薄膜进行了X射线衍射分析,发现三组样品都在2e角14附近出现了明显的衍射峰,此角度对应于WS2的(002)晶面。
并且50℃沉积wS2薄膜的(002)峰值最强,150℃次之,200℃最弱。
这表明,较低温度沉积WS2薄膜的结晶性比较好。
另外,三种薄膜在32-36之还出现了不太明显的(100)、(101)和(102)衍射峰。
由此可以说明本实验通过中频磁控溅射所制得的WS2薄膜均具有不同程度的(002)基面择优取向,并随着沉积温度的升高,基面取向的程度逐渐减弱。
由图6可知,WS2薄膜主要是以(002)晶面生长的,属于II型织构,这将有利于提高薄膜的润滑性能。
4.薄膜的力学摩擦性能分析
4.1纯薄膜的力学性能
1.硬度测量
利用MH一SD型显微硬度仪所测得的硬度值反映的是膜层和基体的综合硬度,试验条件为0.098N的载荷,保载15s。
图7为沉积温度对WS2薄膜维氏硬度及努氏硬度的影响。
薄膜的维氏硬度与努氏硬度均是随着温度的升高而有所降低,50℃时薄膜的硬度最大。
前面提到,沉积温度升高可以增加薄膜的厚度,同时还会会降低薄膜的致密性,进而引起薄膜硬度的下降。
另外薄膜的努氏硬度数值要略低于维氏硬度值,这一现象可能与两种硬度表征方法的作用机理有关。
2.附着力测量
WS2薄膜本身是一种具有润滑性质的软质膜。
在进行划痕试验时极易在划痕处形成一层润滑转移膜,因此很难仅从声发射曲线来准确判断出薄膜与基体之间的结合强度,这就需要结合薄膜的划痕形貌进行观察。
图8是不同沉积温度条件下沉积WS2薄膜的划痕形貌,划痕试验时加载力自左向右逐渐从ON增加至100N,划痕长度为5rnrn,之后卸载时划痕会因惯性延长一段距离。
如图8所示,在较小的载荷时(约20N以内)四种薄膜均出现了崩边现象,表明薄膜内部己经发生了轻微的内聚失效(对应于Lc1),但是膜层并没有完全划破,而是顺着压头的前进方向形成了一层连续的具有自润滑性能的转移膜粘附在划痕表面。
随着载荷的增加,转移的膜层会不断地产生损耗,当载荷达到一定程度时,膜层不再能够连续的铺展在划痕表面(即被划破)。
此时划痕逐渐变宽,划痕两侧开始出现明显的亮边,进而导致薄膜开始从基体上发生大面积的剥离。
即薄膜完全被压头划破并从基体上连续剥离所需的最小载荷,将临界载荷表示为Lc2,以区别于之前薄膜内聚失效时的Lcl。
表5给出了四种沉积温度条件下沉积WS2薄膜的膜/基结合强度Lc2(临界载荷)。
4.2.纯薄膜的摩擦学性能
摩擦磨损试验仪对纯WS2薄膜的摩擦学性能进行了测试。
摩擦副选用中4cm的GGr15钢球,载荷为0.98N-14.7N,转动速度为120rpm和40rpm,测试环境为室温大气(相对湿度RH为40%一80%)
如图9,纯WS2薄膜的摩擦系数较低,基本都在0.1左右,随着沉积温度的升高,摩擦系数有上升的趋势。
是因为较低沉积温度的WS2薄膜具有较强的(002)基面取向,而基面膜又是其产生润滑效果的根本所在。
如图10,对于50℃沉积的WS2薄膜,在高载荷、较高转速(9.8N、240rpm)条件下,经过14min的摩擦过程,在GCr15钢球接触点周围黏附了大量的磨屑。
磨屑在挤压力及摩擦力的作用下,形成了沿摩擦方向分布的转移膜。
对摩擦副表面大片状的转移膜进行EDS能谱分析,见表6。
发现转移膜中含有大量的S、O、W元素,说明在摩擦的过程中薄膜黏附在了GCr15钢球表面。
与膜层成份相比,转移膜中的S元素含量明显降低,并伴随有O元素的明显升高,这说明WS2薄膜在摩擦转移的过程中发生了一定程度的氧化反应。
另外,转移膜中还含有少量的铁元素,这是因为钢球在摩擦过程中会不可避免的发生磨损,产生的磨屑积累在了转移膜中。
5.文献二
研究思路和前面讲的很相似,所以具体内容只作简单介绍,不再赘述。
本文主要采用射频共溅射沉积法制备了纯WS2膜和WS2-Ag复合膜,膜厚约为1um,少量Ag以晶态散布在非晶态WS2中,膜的力学性能和摩擦学性能会随着Ag含量的多少而变化,且均好于纯WS2膜,并研究了Ag含量在5.5%,9.0%,13.6%,16.9%,20.3%时膜的形貌、元素组成、相结构、力学、摩擦学性能。
作为固体润滑WS2薄膜可以是非晶态的,也可以是具有不同取向的晶态结构薄膜,对于非晶态WS2薄膜来说,影响其摩擦学性能的不确定因素很多,制备过程中的一些工艺参数如溅射气压、溅射功率、沉积时间等对薄膜的润滑作用是影响。
对于晶态的WS2薄膜目前被普遍认可的润滑机理为WS2具有六方晶系层状结构,其中每一层是由两层六边形硫原子夹一层金属钨原子组成,硫原子与钨原子组成三角锥形。
每一层中硫原子与钨原子是由强共价键连接,而层与层之间是由相对较弱的范德瓦尔斯力相结合。
WS2极易从层与层之间辟开,所以具有良好的固体润滑性能,稳态的WS2即通常所说的2H-WS2,其中“H”代表六方晶系,“2”是指每个WS2分子包含两个S-W-S单元层结构。
(目前制备的方法主要集中在射频磁控溅射和反应磁控溅射两种方法上,通过这两种方法制备的WS2薄膜多为非晶态,因此对于非晶态WS2薄膜的摩擦性能和润滑机理仍有待进一步的探讨和研究)
多功能离子镀膜机镀制纯WS2薄膜,其中WS2膜层由孪生靶中频磁控溅射方法沉积,过渡层选用纯度为99.99%的高纯Ti靶通过直流磁控溅射方法获得,工作气体为高纯氢气。
具体制备工艺如下:
(为了解决并提高溅射薄膜的膜/基结合力,沉积过程中常用金属与合金作为过渡层。
过渡层可以缓解或降低薄膜与基底材料之间因膨胀系数差别过大而造成的膜层内应力,从而对提高膜/基结合力起到至关重要的作用。
)
5.基体材料装入真空镀膜机,抽真空;
(其中单晶硅片用于膜层的微观形貌及物相成分分析,TC4合金则用来测试薄膜的力学性能及摩擦磨损性能。
)
6.通入Ar气,打开离子源,轰击清洗基体材料;
7..直流磁控溅射Ti过渡层,10min
8.停止工件架的转动,使样品静置于WS2靶面正前方,36min
对工艺的优化过程
通过对比不同工作气压条件下沉积薄膜的形貌、S/W原子比等特性,选定一个合适的工作气压:
然后就是对沉积温度的调节,分别为50℃、100℃、150℃、200℃。
图1给出了单晶硅片在沉积温度100℃、工作气压1.0Pa时制备薄膜的表面SEM照片。
由于硅基底表面过于平整,且薄膜本身的导电性较差,从薄膜表面的SEM照片看
不出明显的特征形貌。
仔细观察薄膜的表面,可以隐约看到一些白色的球形颗粒,由于溅射靶材是由粉末冶金方法而成,在薄膜的沉积过程中,溅射靶材上的MS2颗粒容易产生脱落现象,从而在薄膜表面形成一些粗大的溅射颗粒,其数量会随着膜厚的增加而逐渐增多.
图2给出了纯WS2薄膜的能谱图(EDS分析)薄膜中O元素的存在,一方面这可能是因为制备的薄膜样品出炉后在空气中发生了氧化,一方面也可能是由镀膜过程中真空系统中残留的氧成分所致。
表2与传统的射频溅射法制备的WS2薄膜相似,孪生靶中频磁控溅射方法所获得的WS2薄膜也有明显的S元素损失现象。
在O.5Pa的工作气压下,薄膜的S/W原子比只有0.78,0.8Pa时达到最大值1.32,然后随着工作气压的升高,S/W比呈现下降的趋势,到1.5Pa时S/W比为1.03。
是随着工作气压的升高S/W比先增加后减少。
薄膜的厚度是通过用扫描电镜观察硅片拌断后的新鲜截面来测量的。
图3是在相同沉积温度(100℃)、不同工作气压下沉积WS2薄膜的截面形貌。
通过对比我们不难发现,工作气压为0.5Pa时所制备的薄膜质地较为细腻、致密,但膜层很薄,沉积效率较低。
随着工作气压的升高,薄膜的致密性有所降
低,膜层结构变得疏松,1.0Pa时最为明显,此时膜厚达到了最大值,薄膜开始出现柱状晶的生长趋势。
随后工作气压达到1.5Pa时,薄膜的柱状晶形貌更为明显,但是薄膜的生长速度却又降了下来。
工作气压是影响薄膜形貌的一个重要因素。
提高工作气压可以增加溅射时产生的二次电子数量,使辉光作用增强,从而使被溅射出来的粒子数量增加,提高溅射效率。
但是,工作气压太大,则会使粒子在到达基体表面前与气体分子的碰撞机会增多,从而降低到达基体表面时粒子的平均动能及数量。
所以初步选定0.8Pa为合适的工作气压,通过调节沉积温度来进一步优化工艺参数。
表3给出了在0.8Pa的工作气压,50℃、100℃、150℃和200℃四种不同沉积温度条件下,ws2薄膜的S/W原子比及薄膜厚度。
其中在基体不加热的情况下,经过镀膜前高能粒子轰击以及过渡层Ti的制备,真空室内的温度已经自动上升至50℃。
在沉积WS2薄膜的的过程中,沉积温度一直维持在50℃-60℃间。
从表中可以发现,沉积温度对S/W原子比的影响没有工作气压对其作用效果明显,基本都在1.2-1.52之间。
沉积温度为50C时S/W原子比最高,可达1.52;沉积温度为200℃时S/W原子比最低,约为1.21。
这可能是由于温度升高,S原子的活性增加,更易与真空腔体内残余的H结合生成H2S气体而被抽出真空系统,导致了高温沉积WS2薄膜中的S元素缺失现象更为明显。
随着沉积温度的升高,气体离子溅射靶材形成的溅射粒子数量增多,从而提高溅射效率,导致溅射沉积WS2薄膜的生长速率加快,增加薄膜的厚度,如表3所示。
经过相同的镀制时间,200℃沉积WS2薄膜的厚度要比较低温度时高
约0.2um.
沉积温度对WS2薄膜的截面形貌没有太大的影响。
只是随着温度的升高,200℃沉积的薄膜中出现了一定程度的纤维状结构,使得膜层的致密性有所降低,如图5所示。
提高沉积温度会增大膜层沉积速率的同时,还会增加真空腔体内气体离子的动能,提高靶材溅射粒子与气体粒子之间的碰撞几率,这在一定程度上会降低薄膜的致密性。
WS2薄膜的物相结构分析
图6是WS2薄膜的XRD图谱。
对沉积温度分别为50℃、150℃和200℃条件下制备的WS2薄膜进行了X射线衍射分析,发现三组样品都在2e角14附近出现了明显的衍射峰,此角度对应于WS2的(002)晶面。
并且50℃沉积wS2薄膜的(002)峰值最强,150℃次之,200℃最弱。
这表明,较低温度沉积WS2薄膜的结晶性比较好。
另外,三种薄膜在32-36之还出现了不太明显的(100)、(101)和(102)衍射峰。
由此可以说明本实验通过中频磁控溅射所制得的WS2薄膜均具有不同程度的(002)基面择优取向,并随着沉积温度的升高,基面取向的程度逐渐减弱。
具有ii型织构的的薄膜具有很强的滑动性,具有良好的润滑效果。
由图6可知,WS2薄膜主要是以(002)晶面生长的,属于ii型织构,这将有利于提高薄膜的润滑性能。
WS2薄膜的力学性能
利用MH一SD型显微硬度仪所测得的硬度值反映的是膜层和基体的综合硬度,试验条件为0.098N的载荷,保载15s。
图7为沉积温度对WS2薄膜维氏硬度及努氏硬度的影响。
从图中可以看出,薄膜的维氏硬度与努氏硬度均是随着温度的升高而有所降低,50℃时薄膜的硬度最大。
前面提到,沉积温度升高可以增加薄膜的厚度,同时还会会降低薄膜的致密性,进而引起薄膜硬度的下降。
另外薄膜的努氏硬度数值要略低于维氏硬度值,这一现象可能与两种硬度表征方法的作用机理有关。
据相关数据表明,相同载荷的条件下努氏压痕的深度要小于维氏压痕。
后面会详细介绍这两种显微硬度表征方法的压头形状、硬度及压痕深度的计算方法,并考察其对软基体(TC4合金)上沉积WS2薄膜硬度的影响。
对比表3和4,我们可以发现,几种不同沉积温度薄膜对应的维氏压痕都比较深,大约有1.1-1.2um;而努氏压痕的深度相对较浅,约0.7-0.8um。
一般认为,若要客观真实的反应较薄膜层本身的硬度,压头压入膜层的深度应尽量小于整个膜厚的1/10-1/7。
显然以上两种硬度测试方法对于膜厚只有1.5um左右的软质WS2膜来说不太适用。
但由于基体材料相同,同为TC4合金,而膜层的厚度相差又不是很大,基材对薄膜硬度产生的作用效果可视为一致,用显微硬度仪测得的硬度结果也可以在一定程度上反应出沉积温度对WSZ薄膜硬度产生的影响。
温度较低时由于薄膜的结构比较致密,对应的硬度值也较高,而温度较高时,膜层中出现了一定程度的纤维结构,导致其硬度会偏低。
另外,薄膜的
努氏压痕深度要明显小于维氏压痕,若考虑基体对薄膜硬度的影响,则努氏硬度更能反映出WS2薄膜的实际硬度(即本征硬度)。
这在某种程度上也对工件实际应用过程中的性能评估具有一定的参考价值。
沉积温度对WS2薄膜附着力的影响
薄膜与基体之间的结合问题是影响薄膜使用性能的关键因数之一。
本实验采用划痕法对WS2薄膜的膜/基结合强度进行评价。
WS2薄膜本身是一种具有润滑性质的软质膜。
一方面其声信号不太明显,另一方面进行划痕试验时极易在划痕处形成一层润滑转移膜,因此很难仅从声发射曲线来准确判断出薄膜与基体之间的结合强度,这就需要结合薄膜的划痕形貌进行观察。
图7是不同沉积温度条件下沉积WS2薄膜的划痕形貌,划痕试验时加载力自左向右逐渐从ON增加至100N,划痕长度为5rnrn,之后卸载时划痕会因惯性延长一段距离。
如图7所示,在较小的载荷时(约20N以内)四种薄膜均出现了崩边现象,表明薄膜内部己经发生了轻微的内聚失效(对应于Lc1),但是膜层并没有完全划破,而是顺着压头的前进方向形成了一层连续的具有自润滑性能的转移膜粘附在划痕表面。
随着载荷的增加,转移的膜层会不断地产生损耗,当载荷达到一定程度时,膜层不再能够连续的铺展在划痕表面(即被划破)。
此时划痕逐渐变宽,划痕两侧开始出现明显的亮边,进而导致薄膜开始从基体上发生大面积的剥离。
即薄膜完全被压头划破并从基体上连续剥离所需的最小载荷,将临界载荷表示为Lc2,以区别于之前薄膜内聚失效时的Lcl。
表5给出了四种沉积温度条件下沉积WS2薄膜的膜/基结合强度Lc2(临界载荷)。
从表5中我们发现,随着沉积温度的升高,WS2薄膜的临界载荷Lc2有减小的趋势。
50℃和100℃薄膜在60N左右产生了膜层与基体的分离,而150℃和200℃薄膜的临界载荷Lc2约有50N。
薄膜的沉积温度对膜/基结合强度的影响,
可能与不同沉积温度下薄膜的微观结构及其硬度有关。
前面提到沉积温度较高时,薄膜的硬度较低,结构较为疏松,这可能会导致薄膜在受到外加载荷时被压入的深度较深且更易被撕裂。
WS2薄膜的摩擦学性能
WS2薄膜是一种减摩性能优异的固体润滑材料。
本实验采用兰州化物所研制的MS一T3000型摩擦磨损试验仪对纯WS2薄膜的摩擦学性能进行了测试。
摩擦副选用中4cm的GGr15钢球,载荷为0.98N-14.7N,转动速度为120rpm和
240rpm,测试环境为室温大气(相对湿度RH为40%一80%)
在120rpm、1.96N的测试条件下,对不同沉积温度制备的wS2薄膜进行了摩擦系数的测试,测试时间为10min。
不同温度沉积ws:
薄膜的平均摩擦系数值见图8,从图中可以看出,纯WS2薄膜的摩擦系数较低,基本都在0.1左右,随着沉积温度的升高,摩擦系数有上升的趋势。
结合不同沉积温度WS2薄膜的XRD图谱,可以发现,较低沉积温度的ws2薄膜具有较强的(002)基面取向,而基面膜又是其产生润滑效果的根本所在。
与之相对应的是,较低温度沉积的WS2薄膜也具有较低的摩擦系数(即更好的润滑效果)。
随着沉积温度的升高,WS2薄膜的(002)基面取向程度逐渐减弱,薄膜的减摩效果也随之减弱。
对于50℃沉积的WS2薄膜,我们进一步考察了其在高载荷、较高转速(9.8N、240rpm)条件下,摩擦副接触表面形成摩擦转移膜的能力。
经过14min的摩擦过程,在GCr15钢球接触点周围黏附了大量的磨屑。
磨屑在挤压力及摩擦力的
作用下,形成了沿摩擦方向分布的转移膜,如图8所示。
对摩擦副表面大片状的转移膜进行EDS能谱分析,见表6。
发现转移膜中含有大量的S、O、W元素,说明在摩擦的过程中薄膜黏附在了GCr15钢球表面。
与膜层成份相比,转移膜中的S元素含量明显降低,并伴随有O元素的明显升高,这说明WS2薄膜在摩擦转移的过程中发生了一定程度的氧化反应。
另外,转移膜中还含有少量的铁元素,这是因为钢球在摩擦过程中会不可避免的发生磨损,产生的磨屑积累在了转移膜中。
摩擦副表面转移膜的成份分析